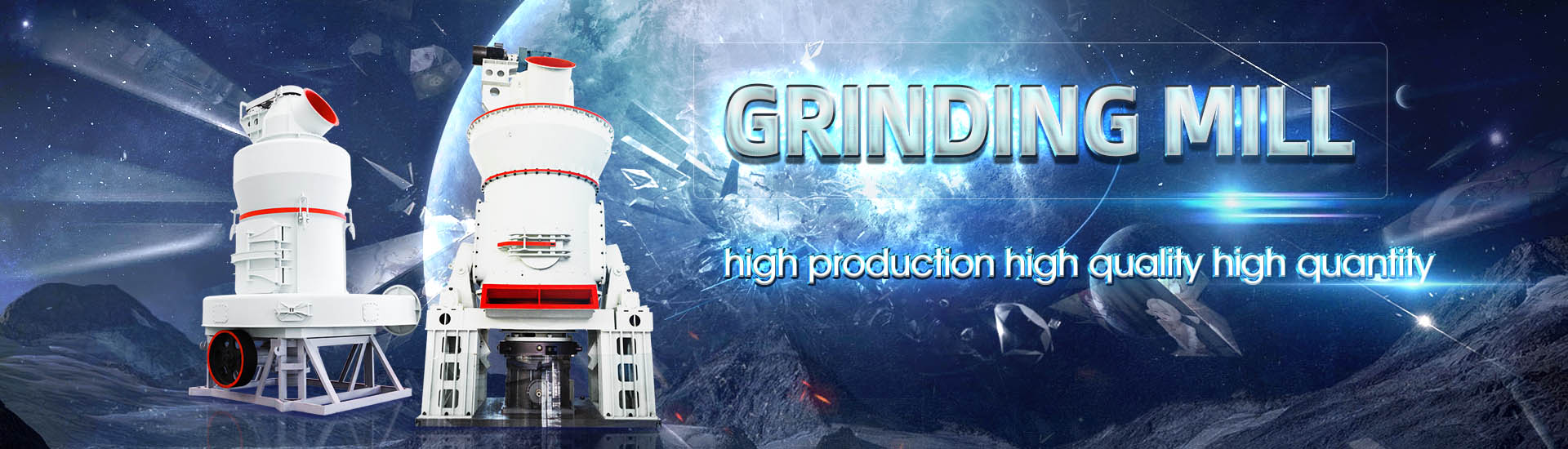
Ceramic ball mill grinding ratio
.jpg)
How to choose the size, filling amount and ratio of alumina
Generally speaking, the initial ball stone gradation of the ball mill is: 30% for large balls, 40% for medium balls, and 30% for small balls In practice, it mainly depends on the particle size of the material to be abrasive The diameter and speed of the ball mill should also be considered Fine grinding or milling reduces the particle size down to as low as 10 micrometer (μm) (4 x 105 in) in diameter Ball mills are the most commonly used piece of equipment for milling CERAMIC MATERIALS I2024年1月31日 Ceramic ball milling has demonstrated remarkable energysaving efficiency in industrial applications However, there is a pressing need to enhance the grinding efficiency for coarse particles This paper introduces a Enhancing the Grinding Efficiency of a Magnetite Since balls have a greater surface area per unit weight than rods, they are better suited for fine grinding The term ball mill is restricted to those having a length to diameter ratio of 2 to 1 and less Ball mills in which the length to diameter ratio is between 3 and 5 are designated tube millsBall Mill an overview ScienceDirect Topics
.jpg)
(PDF) Grinding Media in Ball MillsA Review
2023年4月23日 Despite various research conducted on ball mills, the grinding process mill speed, charge ratio, and grinding The laboratory tests done by Kayaci et al [92] in milling ceramic raw Stone loading amount = 314X the square radius of the ball mill X the specific gravity of the ball X the length of the ball mill X25%*1000 Regarding the gradation of the high alumina ceramic ball of the ball mill: Due to the different grinding aids added to How to choose the size, filling amount and ratio of alumina ceramic In the same way, ceramic grinding balls can be used for mixing: the operation is the same as for attrition, but this time several products are placed in the mixer rather than one The rolling motion of the balls will allow the different products to be perfectly mixed Ceramic ball mills are effective tools for attrition andBall mills and ceramic grinding balls // Umicore Ceramics2023年11月23日 Kaolin is one of the most important clay minerals that attracts attention due to its various application areas such as the ceramic industry In this study, the effects of solid/ball ratio and grinding time on the mechanical activation of kaolin were investigated Samples with 10 µm particle size were activated in The Fritsch Pulverisette 5 Ball Mill (Two Chamber Mill) at Effect of solid/ball ratio and grinding time on the mechanical
.jpg)
Ball Mills 911Metallurgist
2017年2月13日 Center peripheral discharge Rod Mill for minimal slimes in final product CERAMIC LINED BALL MILL Ball Mills can be supplied with either ceramic or rubber linings for wet or dry grinding, for continuous or batch type operation, in sizes from 15″ x 21″ to 8′ x 12′2023年10月27日 The ball mill is a rotating cylindrical vessel with grinding media inside, which is responsible for breaking the ore particles Grinding media play an important role in the comminution of mineral ores in these mills This work reviews the application of balls in mineral processing as a function of the materials used to manufacture them and the mass loss, as A Review of the Grinding Media in Ball Mills for Mineral A section cutthrough of ball mills A ball mill is a type of grinder filled with grinding balls, used to grind or blend materials for use in mineral dressing processes, paints, pyrotechnics, ceramics, and selective laser sinteringIt works on the principle of impact and attrition: size reduction is done by impact as the balls drop from near the top of the shellBall mill WikipediaThe initial grinding ball ratio of wet ceramic ball mill machine is generally 30% for large ceramic alumina balls, 40% for medium balls and 30% for small balls Performance Advantage of Ceramic Ball Mill The products of ceramic ball mill have uniform fineness, save power, Ceramic Ball Mill for Sale Buy Ceramic Ball Mill Machine with
.jpg)
types of ball mills Alpha Grinding Media
2024年5月8日 BALL MILL GRINDING MEDIA The ball mill grinding media typically consists of spherical or small cylindrical steel cylpebs, although materials such as steel, ceramic, glass, and even rubber can be used This variety allows the ball mill machine to grind raw materials with different properties and hardness levels2022年4月1日 Compared with steel ball medium, ceramic ball medium has characteristics of good wear resistance, high hardness and low density, and thus can significantly reduce the consumption of grinding power and grinding media when applied in stirred mills [2,3] Moreover, ceramic ball medium can improve the flotation performance of nonferrous and noble The first attempt of applying ceramic balls in industrial tumbling mill 2022年11月1日 It is also known that the ore processed by the plant is iron, with a Mohs hardness of between 8 and 85 and a specific gravity of 42 The P80 of 028 mm and the P50 of 010 mm, as depicted in Fig 1, represents the particle size distribution of the feed to the secondary millIt should be emphasised that the 30 mm refers to the diameter of the daily Can ceramic balls and steel balls be combined in an2022年1月1日 A pilotscale grinding technology of ceramic medium stirred mill was proposed in this study Based on the specific productivity and grinding efficiency, the appropriate grinding parameters were ascertained as follows: material ball ratio of 07, ceramic ball medium size ratio (10 mm: 15 mm: 20 mm = 3:2:5), stirring speed of 110 rpm, grinding concentration of 50%, Highefficiency and energyconservation grinding technology using
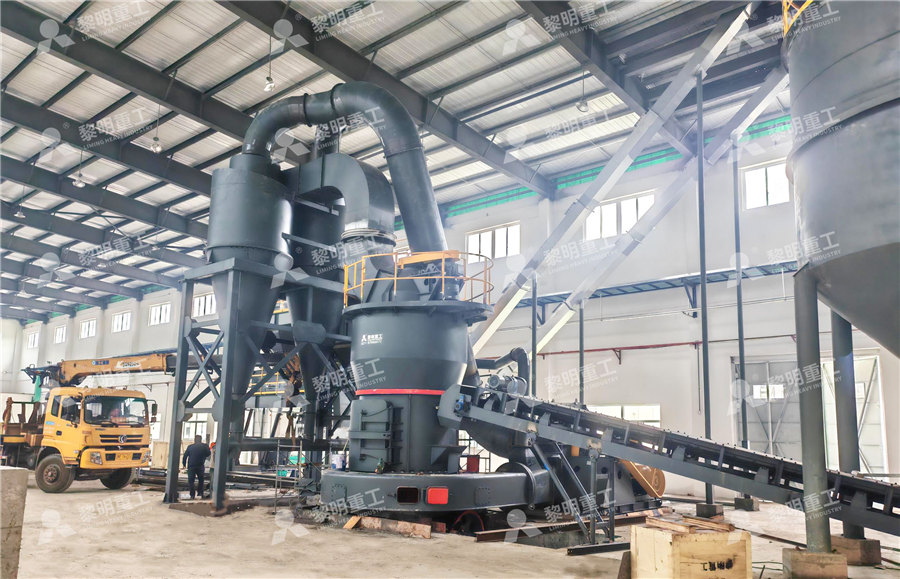
Grinding Media in Ball Mills for Mineral Processing
2023年11月24日 The performance of grinding media in a ball mill is measured in terms of wear rate, which is a function of the media composition, hardness, phase structure, and corrosive–abrasive characteristics of the slurry The wear mechanisms involved in a ball mill are impact, abrasion, corrosion, and erosionIn the same way, ceramic grinding balls can be used for mixing: the operation is the same as for attrition, but this time several products are placed in the mixer rather than one The rolling motion of the balls will allow the different products to be perfectly mixed Ceramic ball mills are effective tools for attrition andBall mills and ceramic grinding balls // Umicore CeramicsThe maximum power draw in ball mill is when ball bed is 3540 % by volume in whole empty mill volume Considering that ball bed has a porosity of 40 %, the actual ball volume is considered to be Best way to determine the balltopowder ratio in ballmilling?2013年8月3日 In Grinding, selecting (calculate) the correct or optimum ball size that allows for the best and optimum/ideal or target grind size to be achieved by your ball mill is an important thing for a Mineral Processing Engineer AKA Metallurgist to do Often, the ball used in ball mills is oversize “just in case” Well, this safety factor can cost you much in recovery and/or mill liner Calculate and Select Ball Mill Ball Size for Optimum Grinding
.jpg)
A Comparison of the FineGrinding Performance between
2024年1月18日 Moreover, two models were developed to use ceramic balls instead of cylpebs as finegrinding media in the wet tumbling mill based on the ball size and the ratio of the total mass of cylpebs Cylpebs can be replaced by ceramic balls with 116–175 times the diameter of cylpebs, taking up only 76%–83% of the total weight of cylpebsCeramic grinding media are also suited for use in processes where mixing and dispersing effects play an important role In the majority of these grinding processes, steatite and alumina are the most common ceramic materials used for grinding balls and linings CeramTec generally manufactures its grinding balls and linings with steatiteCeramic Grinding Beads, Balls and LiningsAdvantages and features of the ceramic ball mill The grinding fineness depends on the milling time The motor of the ceramic ball mill is started by the coupling reduce voltage which lowers the starting electricity and the ball mill’s structure is divided into integral type and freestanding type; advantages of the ceramic ball mill are lower investment, energy saving, structure novelty Ceramic Ball Mill For Grinding Materials FTM MachineryReview Grinding Media in Ball MillsA Review Nyasha Matsanga 1,*, Willie Nheta 1 and Ngonidzashe Chimwani 2 1 Mineral Processing and Technology Research Centre, Department of Metallurgy Grinding Media in Ball MillsA Review ResearchGate
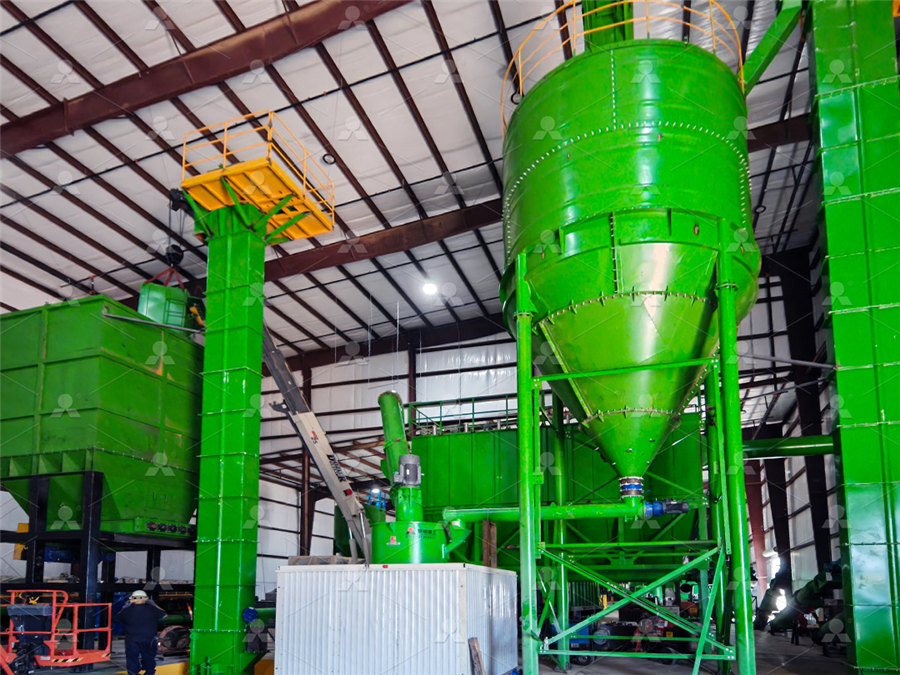
How to choose the size, filling amount and ratio of alumina ceramic
Stone loading amount = 314X the square radius of the ball mill X the specific gravity of the ball X the length of the ball mill X25%*1000 Regarding the gradation of the high alumina ceramic ball of the ball mill: Due to the different grinding aids added to PROCESSING OF CERAMIC POWDER USING HIGH ENERGY MILLING H Zoz, H Ren Zoz GmbH, Maltoz Strasse, D57482 Wenden, Germany Keywords: high energy milling, milling process, ceramic powder, fine powder, ball mill, grinding system, Simoloyer 1 Introduction High Energy Milling (HEM) is a well known and commercially used technique [13] Today thePROCEEDING OF CERAMIC POWDER USINGVBCC's HIGH ENERGY PLANETARY MILL Description: Planetary ball mills indeed sound like marvels of engineering! By leveraging the dynamic interplay of centrifugal and Coriolis forces, they achieve impressive feats of pulverization In VBCC's high energy planetary mill, the stationary jar filled with grinding balls becomes the center of attentionHigh Energy Planetary Mill VB CeramicsKeywords: Ball mills, grinding circuit, process control I Introduction Grinding in ball mills is an important technological process applied to reduce the size of particles which may have different nature and a wide diversity of physical, mechanical and chemical characteristics Typical examples are the various ores, minerals, limestone, etcGrinding in Ball Mills: Modeling and Process Control Sciendo
.jpg)
Ball Mill Grinding for Grinding Ceramic Raw Materials
Our ceramic ball mill has 35kg2t options and is used for grinding ceramic raw materials Factory direct sales and global distribution provide solutions to ensure optimal production efficiency for various applications2023年4月30日 According to the ratio of cylinder length (L) to diameter (D), the ball mill can be divided into short cylinder ball mill, L/D ≤ 1; long barrel ball mill, L/D ≥ 1–15 or even 2–3; and tube mill, L/D ≥ 3–5 According to the cylinder shape of the ball mill, it can be divided into cylindrical ball mill and cone ball millBall Mill SpringerLinkMagotteaux ceramic grinding beads are suitable for all existing and future types of stirred mills such as SMD, HIG, Isamill, VXP, Netzsch and others The beads have a diameter of 03 – 5 mm and the balls have a diameter of 8 – 60 mmCeramic grinding beads MagotteauxKeywords: Ball mills, grinding circuit, process control I Introduction Grinding in ball mills is an important technological process applied to reduce the size of particles which may have different nature and a wide diversity of physical, mechanical and chemical characteristics Typical examples are the various ores, minerals, limestone, etcGrinding in Ball Mills: Modeling and Process Control Sciendo
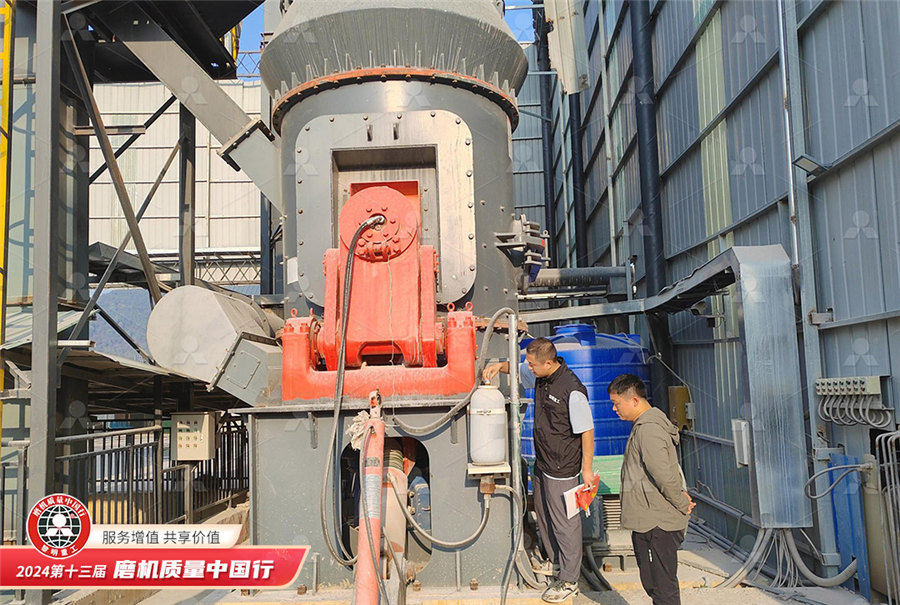
Ball Milling Glaze Mixing Preparation Glazy Ceramics Wiki
Glazy Ceramics Wiki Ball Milling Glazes Glaze Mixing Preparation ceramicswiki April 29, 2017, You need grinding media in a ballmill that has some tooth, like pebbles of are the largest, and two other sizes 50/50 Im not sure what ratio I use and I dont think you have to be that specific but it is most efficient if all the balls 2019年12月4日 steel balls Ceramic balls As the name implies, this grinding media are made of ceramic which is energysaving and environmentally friendly The ceramic ball has a Mohs hardness of 90, which is second only to 3 Types of Grinding Media for Ball Mills FTM 21 Effect of solid/ball ratio and grinding time on mechanical activation Unactivated kaolin samples obtained under 10lm particle size was ground in the Planetary Ball Mill (Planetary Ball Mill) at 400 rpm Dry grinding was carried out at different solid/ball ratios (1/10, 1/20, 1/30) and at different times (0, 15, 30, 45, 60 min)Effect of solid/ball ratio and grinding time on the mechanical 2023年11月1日 This paper presented an industrial validation test for reducing the energy consumption of grinding operations using a ceramic media stirring mill instead of a twostage ball mill According to the optimal grinding variable estimates, the medium filling rate reached 90%, the medium ratio (10 mm: 15 mm: 20 mm) was 3:2:5, while the material ball Energy conservation and consumption reduction in grinding
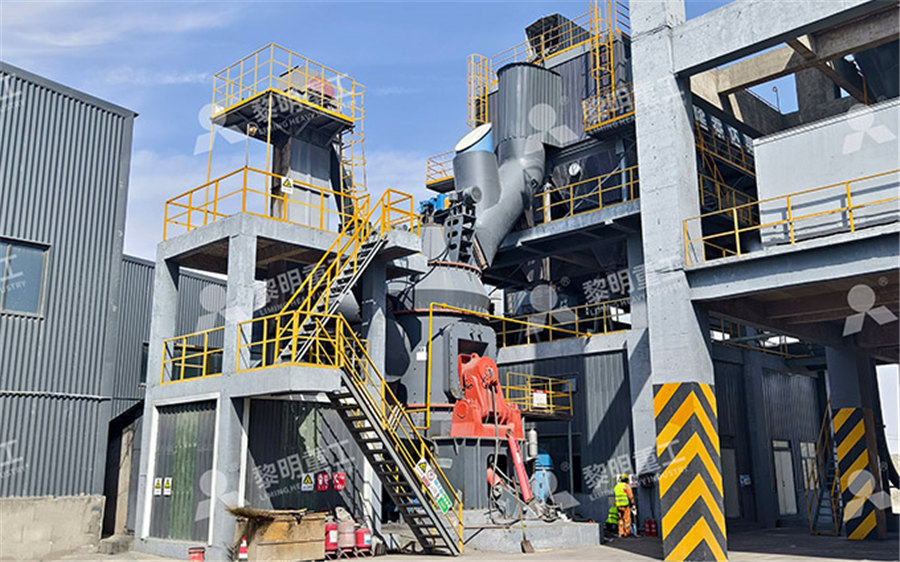
How to Determine the Ratio of Grinding Balls in a Ball Mill
2023年10月23日 Discover the best grinding ball materials for ball mills and their optimal combinations It's recommended to keep a record of the grinding ball size ratios that work best for a specific material during daily experiments to Ltd focus on producing and selling ceramic beads and parts such as grinding media, blasting beads • Speed ratio (speed sun wheel : grinding jar) Laarmann Group BV Op het Schoor 6 6041 AV The Netherlands info@laarmann laarmann webshoplaarmann +31 6 23 40 00 33 LM PBM PLANETARY BALL MILL Counter weight with 1 jar can be expanded for 14 positions PBM Planetary ball mill closed 1 Movement planetary millPLANETARY BALL MILL LaarmannThe ceramic ball mill is a kind of ball mill grinder that the liner plate is made of wearresistant ceramics It has a small capacity, suitable for small batch production, and it can realize a 24hour continuous work with dry grinding or wet grindingCeramic Ball Mill For Sale – Automatic Ceramic Ball Mill 2015年4月22日 In the present research work the mixture of boron carbide and graphite ceramic powders with a theoretical composition of 50% each by weight were mechanically alloyed in a laboratory ball mill with On the Use of Ball Milling for the Production of Ceramic Powders
.jpg)
Exploring Ball Mill Diagram: A Comprehensive Guide JXSC
2024年4月28日 Alongside the mining industry, ball mills are also used in different sectors, such as cement production, for grinding clinker and other raw materials; ceramic manufacturing, for grinding and mixing ceramic powders, and paint production, for dispersing and homogenizing pigments and other ingredientsPlanetary Ball Mill BM 1400+ (4 Grinding Stations) charcoal, hair, catalysts, chemicals, alloys, bones, metal oxides, iron ore, ceramics, polymers, bentonites, pigments etc Get Quote Digitally adjustable sun wheel speed 30400rpm with speed ratio 1: 22 / (Upgradable Versatile Planetary Ball Mill Upto 4 Grinding Stations