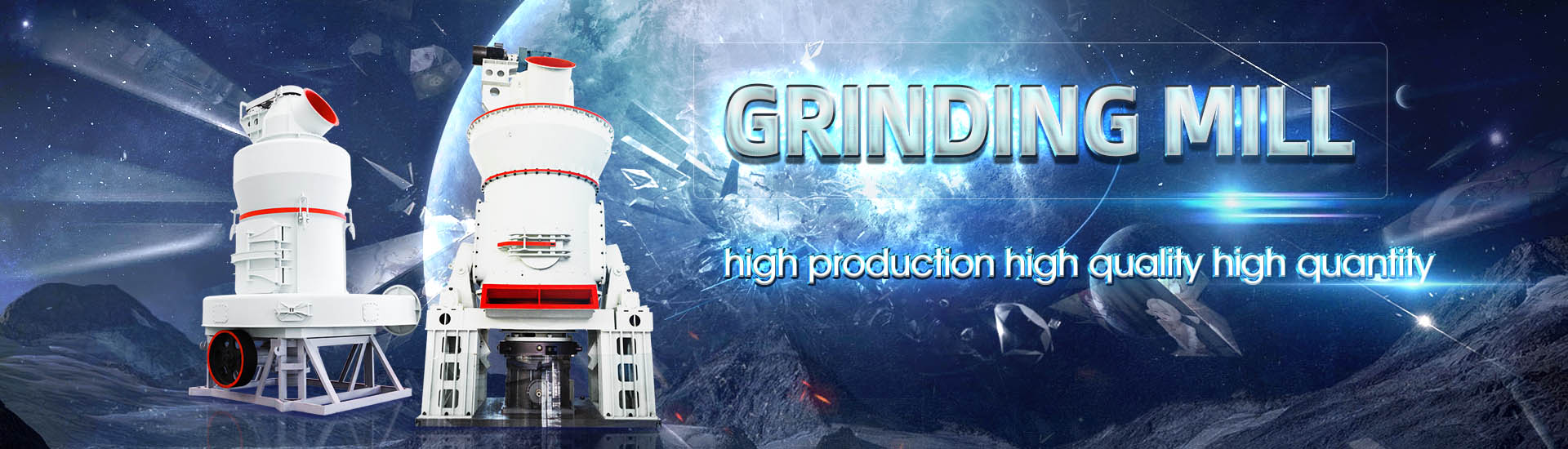
Cement ball mill and how to increase production
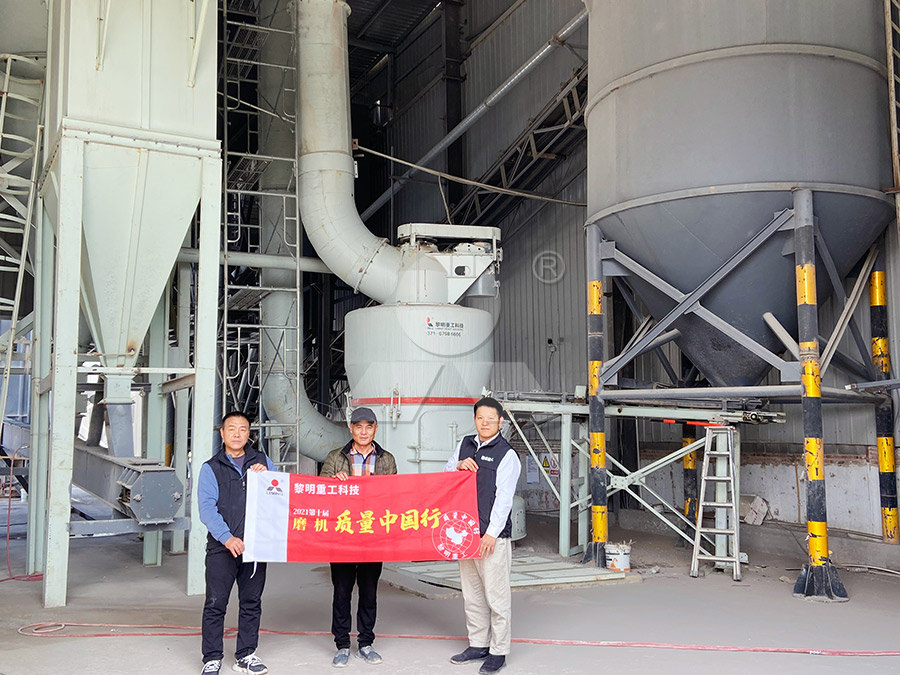
OPTIMIZATION OF CEMENT GRINDING OPERATION IN BALL MILLS
Optimization of the Cement Ball Mill Operation Optimization addresses the grinding process, maintenance and product quality The objective is to achieve a more efficient operation and increase the production rate as well as improve the run factor Consistent quality and Ball mill optimisation As grinding accounts for a sizeable share in a cement plant’s power consumption, optimisation of grinding equipment such as ball mills can provide significant cost BALL MILLS Ball mill optimisation Holzinger ConsultingOptimization of the Cement Ball Mill Operation Optimization addresses the grinding process, maintenance and product quality The objective is to achieve a more efficient operation and increase the production rate as well as improve Optimization of Cement Grinding Operation in Ball Optimizing the operation of cement mills is essential to maximize productivity, reduce energy consumption, and improve the quality of the final cement product In this article, we will delve into practical strategies for cement mill Cement Mill Optimization: Practical Strategies for
.jpg)
How to Improve Cement Ball Mill Performance
From Table 1 we can learn that if the particle size of the feed material is reduced from 25 mm to less than 2 mm, the mill output can be increased by at least 60%, which is relatively consistent with the actual production There are two 1987年8月1日 Cement manufacturing process is now operated with the aid of various control systems, such as raw meal composition control, kiln control and mill control Those systems Optimization of Cement Manufacturing Process ScienceDirect2020年2月1日 Nowadays, ball mills are used widely in cement plants to grind clinker and gypsum to produce cement In this work, the energy and exergy analyses of a cement ball mill Energy and exergy analyses for a cement ball mill of a new emission benefits to the cement producer Holzinger Consulting and partners provide solutions for the cement and minerals industry to improve plant performance, reduce production costs, increase productivity or implement new Ball Mill Optimisation Holzinger Consulting
.jpg)
Mike Sumner and Keith Marsay, Grace, examine ball mill
zes are beneficial to the efficiency in the fine particle size range in cement grinding In typical ball mill circuits the second chamber ill benefit from a reduction in mean size, so long as a Clinker Grinding: The main process in cement grinding units involves grinding the clinker into a fine powder using a cement ball mill or vertical roller mill This step is crucial as the fineness of the cement determines the rate of hydration and, StepbyStep Guide to the Manufacturing of Cement2023年8月23日 The production process of a cement ball mill involves raw material preparation, grinding, linearization, clinker grinding, and the eventual storage and distribution of the finished cement product This process is What Are the Parts of a Cement Mills? Cement Ball The ball mill discharge is feed to the top of the SKSSeparator Cement grinding capacity of Ball mill increases by adjustment of air gap in the V Separator with proper air distribution Maintaining uniform air gap between plates and steps in the VSeparator increases production of cement mill To seal air leakage in SKS Separator with uniform INCREASING OUTPUT OF CEMENT GRINDING IN BALL MILL
.jpg)
Cement ball mill Xinxiang Great Wall Machinery Co, Ltd PDF
The cement ball mill can perform dry process production and also wet process production, moreover it can do grinding and drying at the same time CHAENG cement ball mill has features of small investment, high rate of return, simple process and easy operation Advantages of CHAENG cement ball mill: 12019年10月18日 How to select a costeffective cement mill? AGICO Cement supplies highquality cement ball mill, vertical roller mill, cement roller press, any need? Skip to content +86 s To promote the productivity of the ball mill, you should consider of production increase and energy reduction In the real How To Select Cement Mill? Cement Ball Mill, Vertical Cement MillThe processing capacity of the ball mill increases with the increase of the filling rate of the steel ball AGICO Cement is specialized in design and supplies equipments for complete cement production lines of different scales, capacity from 300 to above 2500TPD; Main equipments include: rotary kiln, grinding equipment How to Improve Working Efficiency of Ball Mill2022年3月16日 Cement ball mill is a kind of equipment for further fine grinding of materials, with high fineness It is widely used in industry, metallurgy, chemical industry, cement and other industries TheWhat is a Cement Ball Mill? How to Use It? by cicemech Medium
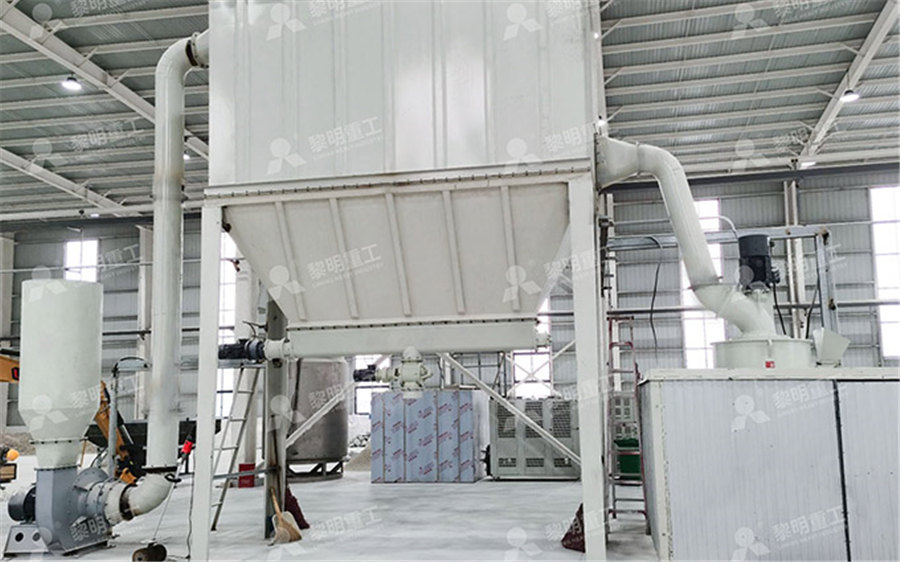
Cement mill Wikipedia
A 10 MW cement mill, output 270 tonnes per hour A cement mill (or finish mill in North American usage [1]) is the equipment used to grind the hard, nodular clinker from the cement kiln into the fine grey powder that is cementMost cement is currently ground in ball mills and also vertical roller mills which are more effective than ball mills2020年2月1日 They showed that the polymerbased grinding aid increases the specific surface, prevents agglomeration and ball coatings, and improves the roundness, fineness and fluidity of the ground cementEnergy and exergy analyses for a cement ball mill of a new Years of cement production practice shows that cement particle gradation should be distributed continuously within a certain size range Generally speaking, the cement particles smaller than 32 μm are beneficial to reduce bleeding and Ball Mill In Cement Plant Cement Ball Mill AGICO Excessive heat can actually impact your production in several ways For example, ball mills are often used for the creation of cement aggregate If the ball mill making the cement is running hot, it can cause issues during construction, Temperature Reduction for Ball Mill Optimization
.jpg)
Grinding in Ball Mills: Modeling and Process Control
2012年6月1日 The feed material is typically composed of the BFRs and the catalyst, both in powder form As the cylinder starts to rotate, the grinding balls inside the cylinder crush and grind the feed With the increase of cement mill specifications and the requirement of energy saving, high yield, and high quality of cement grinding plant, the closedcircuit grinding is an inevitable trend of cement grinding unitThe essential equipment of a closedcircuit grinding system is a cement classifier, also known as a cement separatorThe function of the cement classifier is to select How To Measure Your Cement Mill And Cement Classifier? AGICO CEMENTCommon problems in cement mill operations frequent issues encountered in cement mills and how to or operational issues can lead to significant production losses and increased costs Solution: Implement a comprehensive preventive maintenance program that includes regular “Ball Charge Management in Cement Mills” Available at: Common problems in cement mill operations frequent issues In another word, the cement grinding mill can increase the cement quality and guarantee the qualification rate of cement In general, cement mill can both apply for dry cement production and wet cement production Commonly, there are three hot types of cement mill in the cement industry: cement ball mill, Raymond mill, and vertical cement millCement Mill Cement Ball Mill Vertical Cement Mill Factory
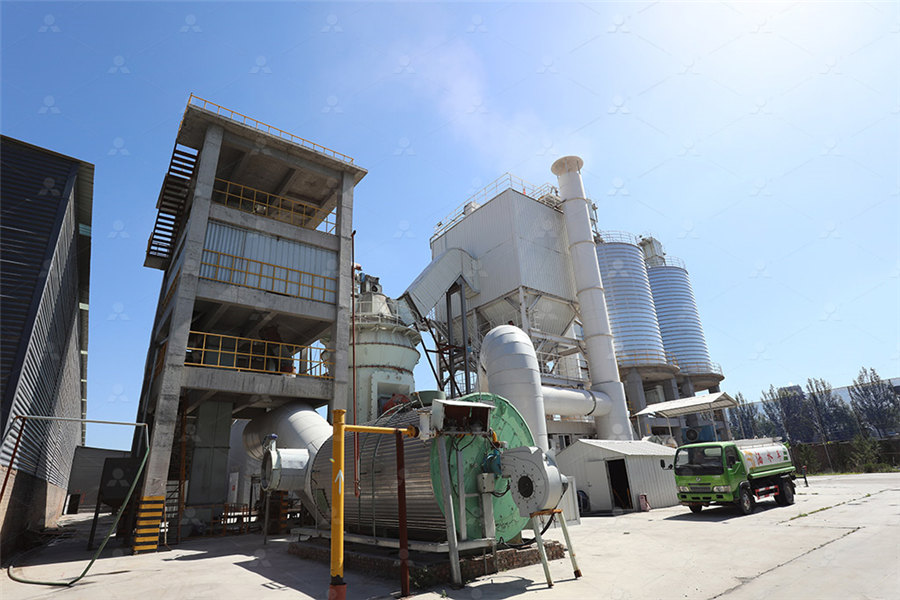
`Grinding Aid Effectiveness in Cement Ball Mill Academia
Conclusion Using Grinding Aid in Horizontal Cement Ball mill lead to increasing in the mill designed feeding and reduction in specific power consumption Narmak, Tehran, Iran and costeffectiveness of cement production A comprehensive experimental test program 3GRINDING AIDS: A STUDY ON THEIR and a variety of computer simulations Ball mill for cement grinding An inefficient ball mill is a major expense and could even cost you product quality The best ball mills enable you to achieve the desired fineness quickly and efficiently, We know that you strive to increase production while saving on CAPEX, operation and maintenance costsMilling and grinding FLSmidth Cement2023年12月28日 3 The ball mill is of good quality The better the quality of the ball mill, the more stable the performance of the ball mill will be during operation In addition, as for the lining plate of the ball mill’s wearing parts, the quality of the lining plate affects the overall production efficiency of the ball millFactors Affect The Output and Quality of Ball Mills And How to What is the difference between a ball mill and a coal pulverizer? A ball mill is a machine that grinds materials up to a consistent size using steel balls as the grinding medium A coal pulverizer is a machine that pulverizes coal to a fine powder for combustion in power generation, cement production, and other industries How does the ball How Is Coal Pulverized in a Ball Mill?
.jpg)
How To Optimize The Operation Of The Cement Mill
2024年1月23日 The efficient operation of a cement mill is vital for the overall productivity and quality of the cement production process Constant adaptation and optimization are essential in the dynamic environment of cement manufacturing to meet quality standards and In cement production, ball mill is one essential milling equipment in cement grinding, service life of ball mill is always concerned by cement plant owners good maintenance work can save manpower, material and equipment costs in How To Increase Wear Part Of Cement Ball Mill 2024年2月23日 The operation of the cement raw mill is a critical step in cement production By grinding the raw materials into a fine powder, these powders can be more easily mixed with other cement ingredients and burn more evenly How Does a Raw Mill Work in a Cement Industry2021年6月29日 Nowadays, ball mills are widely used in cement plants to grind clinker and gypsum to produce cement The research focuses on the mill speed as well as air classifier speed effect on the two Effects of Mill Speed and Air Classifier Speed on Performance of
.jpg)
Ball Mill Grinding Machines: Working Principle, Types, Parts
Ball mills find widespread applications in various industries due to their versatile grinding capabilities Some common applications include: Cement Industry: Ball mills are extensively used in the cement industry for grinding raw materials, clinker, and additives to produce cementRaw mill is generally called cement raw mill, raw mill in cement plant, it refers to a common type of cement equipment in the cement plantIn the cement manufacturing process, raw mill in cement plant grind cement raw materials into the raw mix, and the raw mix is sent to the cement kiln to make cement clinker, next, clinker and other admixtures will be ground into finished cement by Raw mill Cement PlantGrinding Aid Effectiveness in Cement Ball Mill Web: bulawali : bulawali@gmail, ali@bulawali LinkedIn: Ali Bulawali The introduction of the grinding aid (GA) has been started more than 50 year ago, to facilitate clinker grinding in cement mills improve mill output despite of the above features, the wear of mill interior parts well be increase`Grinding Aid Effectiveness in Cement Ball Mill Academia2023年10月23日 When blended by ball mill, the AluminaZirconia particles were changed into 977 μm, showing that the ball mill to refine powder particles while reducing the risk of agglomerationA study of different grinding aids for lowenergy cement clinker production
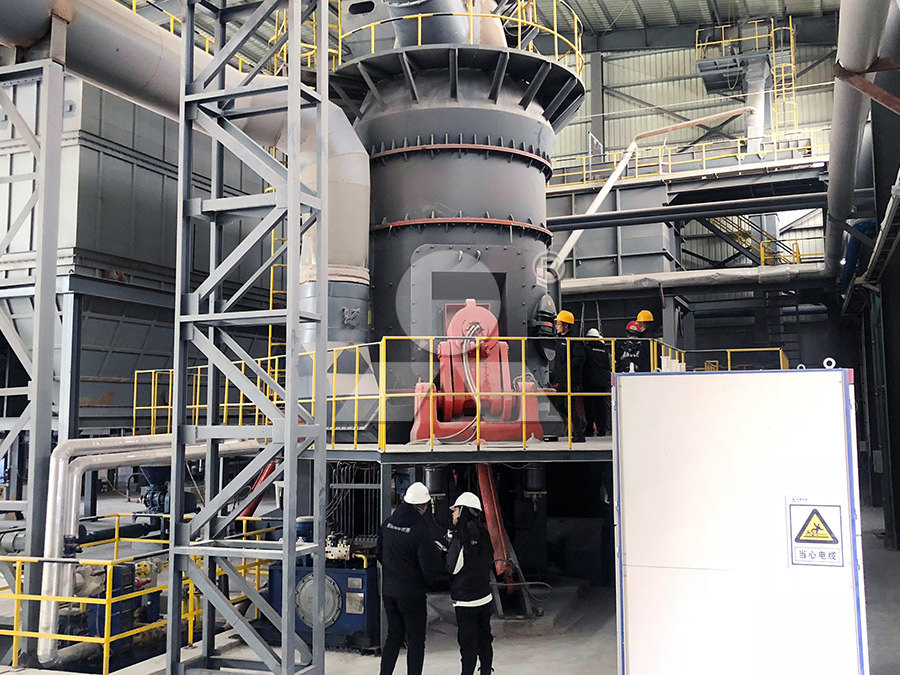
PROCESS DIAGNOSTIC STUDIES FOR CEMENT MILL
diagnostic study of Ball mill for cement grinding 2 METHODOLOGY FOR PROCESS DIAGNOSTIC STUDY : BALL MILL The process diagnostic study for ball mill optimisation is carried out in following steps depending on the type of problem of the grinding system • Production • Operation Philosophy • System Equipment • Size Reduction Pattern2021年6月10日 Also, the results demonstrated that cement production rate increases (185–224 t/h) and the electrical consumption decreases (411–331 kWh/t) when cement fineness decreases (3250 cm²/g–2820 Ventilation Prediction for an Industrial Cement Raw Ball Mill by Roll presses are also used; particularly in upgrading existing ball mill circuits either to increase production or reduce power consumption A press can accept material up to around 75mm in size and act as either a pregrinderfor a ball mill Raw milling and blending INFINITY FOR CEMENT Explore the intricacies of cement production, from quarry to packaging, and understand the environmental impact Learn stepbystep processes, a classifier to separate any oversized particles before being blended and heated to form cement The use of a ball mill is common in the cement production process, Cement Production Demystified: StepbyStep Process and
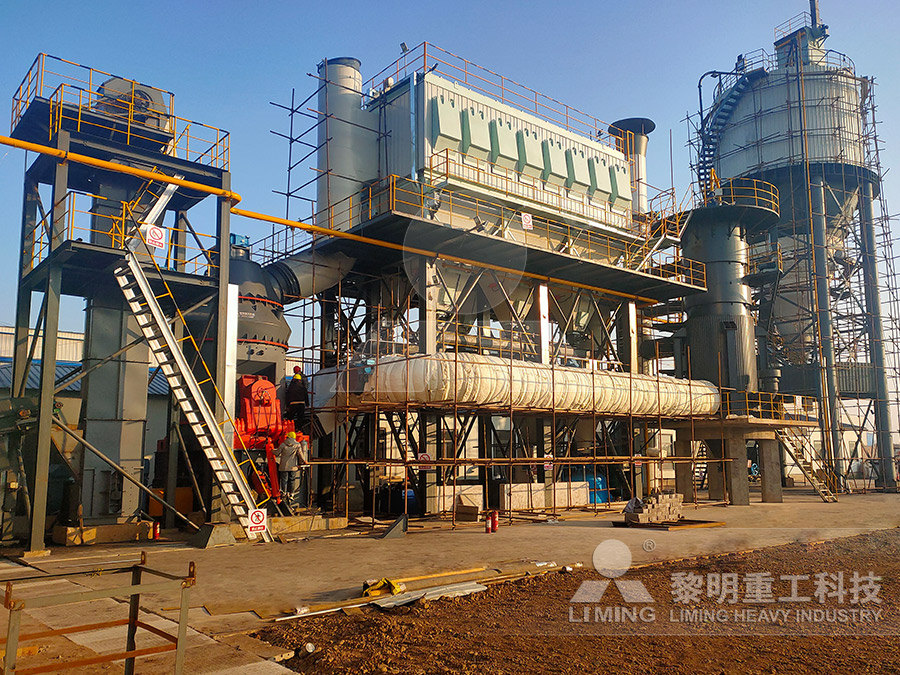
Important Operation Tips For Cement Vertical Mill
Regardless of Rotary kiln operation or grinding, it is necessary to clarify the inherent logical relationship of the system, which requires the operator to have a clear understanding of the characteristics of the system process and 2023年4月23日 One of the most used tumbling mills is the ball mill This paper reviews different types of grinding media that have been developed and improved over the years and their properties(PDF) Grinding Media in Ball MillsA Review ResearchGateThe installation of liners Length Diameter Ratio The lengthdiameter ratio of the cement ball mill is relatively large For mills of opencircuit grinding system, the lengthdiameter ratio is usually between 35 and 6 to ensure that the product fineness is qualified through single grinding; For ball mills in closedcircuit grind system, in order to increase the material flow rate, the length Cement Ball Mill Cost Effective Cement Grinding Mill from AGICOThe vertical roller mill (VRM) is a type of grinding machine for raw material processing and cement grinding in the cement manufacturing processIn recent years, the VRM cement mill has been equipped in more and more cement plants around the world because of its features like high energy efficiency, low pollutant generation, small floor area, etc The VRM cement mill has a Vertical Roller Mill Operation in Cement Plant

Process Training Ball Mill INFINITY FOR CEMENT EQUIPMENT
BALL MILL OPERATION Ball mills for finish grinding cement usually consist of two compartments An intermediate diaphragm separates both compartments from each other The 1 compartment is filled with coarser balls and lifting liners and is supposed to pre Choose the right cement manufacturing machine is an important influence factor to produce highquality cement The cement making machine frequently used in cement plants includes cement rotary kiln, shaft kiln, cement vertical mill, cement ball mill, cement roller press, etcCement Manufacturing Machine Cement Making Machine Cement 2020年5月1日 Cement industry consumes a huge amount of electrical energy that is about 100 kWh/t (kWh per ton (10 3 kg) of cement) [16]In a cement plant, about twothirds of the total electrical energy is used for particle size reduction of raw materials and clinker [17]There is a diverse range of options to decrease the production expenses as well as CO 2 emissions that Energy and exergy analyses for a cement ball mill of a new 2020年1月11日 Compared with other ball mills that used for the same period, his ball mill grinding efficiency is higher by about 25% At present, the capacity of the gold ball mill is 180TPH, the particle size of the feed is controlled at about 20mm, and the output easily reaches 200 mesh Gold ore working site5 Ways to Improve the Ball Mill Efficiency FTM