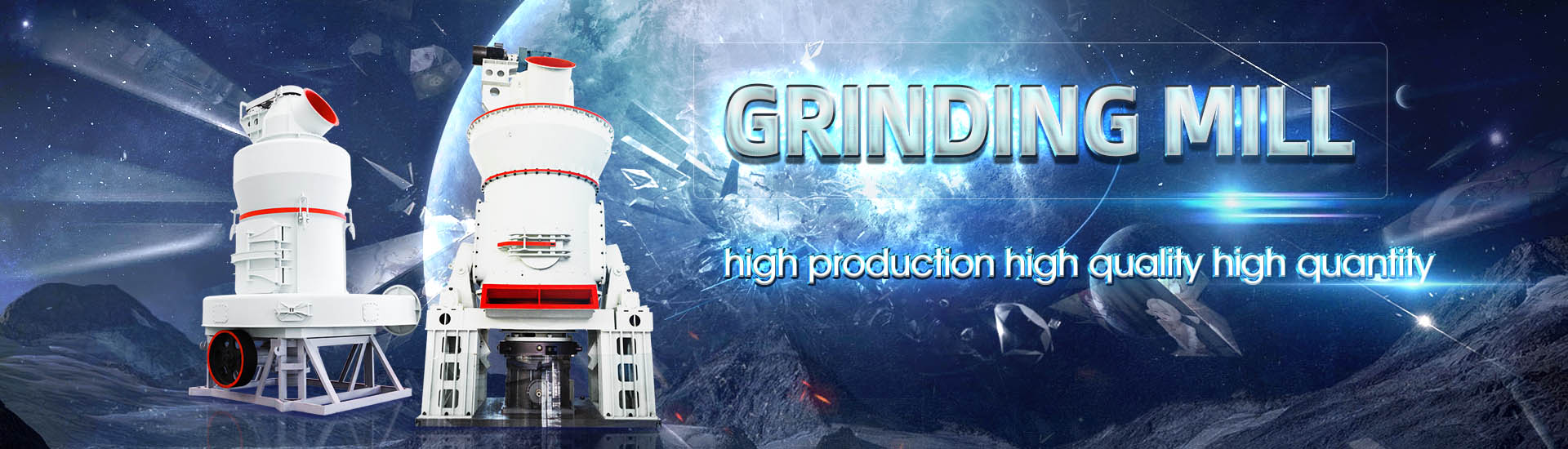
Reasons for low raw material grinding time
.jpg)
Estimation of Grinding Time for Desired Particle Size Distribution
In the present study, iron ore of three different chemical compositions was selected from Karnataka region These samples are typical raw materials used in JSW Steel, Ballari Pellet Plant, to produce pellets The selected iron ores are mainly classified into three groups based on the percentage of silica and alumina present in 展开2022年6月24日 Grinding is a manufacturing process which significantly contributes in producing high precision and durable components required in numerous applications such as aerospace, (PDF) A comprehensive review on the grinding process: common solution to grind raw materials and cement Roller presses are used mainly in combination with a ball mill for cement grinding applications and as finished product grinding BALL MILLS Ball mill optimisation Holzinger Consulting2020年7月2日 In most cases, more fragmented raw material makes it easier to achieve the desired quality parameters of pellets or briquettes While the chipping of biomass prefers moist (PDF) Impact of the Drying Temperature and Grinding Technique
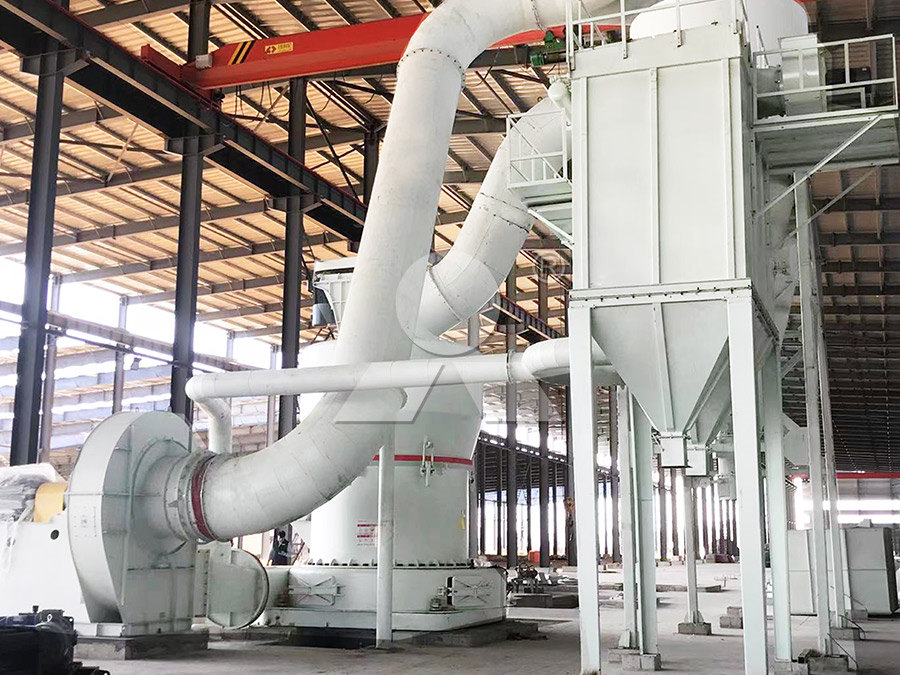
Grinding Theory and material Troubleshooting for Grinding
When grinding difficulttocut materials, various problems and negative effects to the production need to be considered Any of them can seriously effect the production lead time and2022年2月28日 Comminution is mainly carried out for two reasons: final product preparation, according to the required size, and the liberation of valuable materials/minerals from their Grinding SpringerLink2024年10月11日 The grinding time of raw materials ranged from 05 to 3 h, corresponding to a decrease of 239 % in the absolute dry density of the specimen from 046 to 035 g/cm 3, and Effect of raw material fineness on the properties of inorganic foam 2015年12月1日 Taking into account the processintegrated drying of raw materials, other main constituents and fuels, the efficiency of the thermal process reaches values above 80% of the Process technology for efficient and sustainable cement production
.jpg)
Comprehensive analysis of the effects of different parameters on
2024年1月20日 The results showed that an increase in the theoretical grinding depth results in a higher material removal efficiency and grinding temperature as well as a superior ground 2024年3月11日 Grinding difficulttocut alloys is critical in many industrial applications, including aerospace, automotive, and medical industries However, this process has several challenges, Towards Sustainable Grinding of DifficulttoCut Alloys—A Holistic fineness A stable raw meal grinding process provides a low variance of the fineness Figure 1 Flow chart of raw meal production Figure 1 depicts a typical flow chart of raw meal production In the demonstrated closed circuit process, the feeding of the raw materials is performed via three weight feeders, feeding first a crusherModeling of Raw Materials Blending in Raw Meal Grinding 2022年8月31日 Dear Colleagues, The grinding process, as a primary stage of ore/raw material processing, is a necessary operation in beneficiation plants It not only provides the appropriate particle size for subsequent separation Grinding Modeling and Energy Efficiency in Ore/Raw
.jpg)
Estimation of Grinding Time for Desired Particle Size Distribution
2020年1月3日 22 Grinding Studies Two kinds of mills, BBM and LBM, were used to achieve the desired P 80 passing percentage of 150 μm with an acceptable range of hematite liberation (> 75%) at optimum grinding time The BBM is a standard ball mill having a length and diameter of 300 mm × 300 mm with smooth liner as shown in Fig 2A rotating drum is attached to a 2015年10月23日 In this chapter an introduction of widely applied energyefficient grinding technologies in cement grinding and description of the operating principles of the related equipments and comparisons over each other in terms of grinding efficiency, specific energy consumption, production capacity and cement quality are given A case study performed on a EnergyEfficient Technologies in Cement Grinding IntechOpenformation, raw meal composition and fineness A stable raw meal grinding process provides a low variance of the fineness Figure 1 Flow chart of raw meal production Figure 1 depicts a typical flow chart of raw meal production In the demonstrated closed circuit process, the raw materials’ feeding is performed viaModeling of Raw Material Mixing Process in Raw Meal Grinding Installations2015年12月1日 Taking into account the processintegrated drying of raw materials, other main constituents and fuels, the efficiency of the thermal process reaches values above 80% of the theoretical maximum [2] The grinding of raw materials and cement has been in the focus of better energy utilisation, but product quality is also of highest importanceProcess technology for efficient and sustainable cement production
.jpg)
RAW MATERIAL GRINDING ITadipatri’s big sixer Loesche
from Tadipatri is very low and at only approximately 50 per cent compared to other raw materials and consequently requires a high specific grinding power of approximately 115kWh/t (see Figure 7) As can be seen from this diagram, the cement raw material from Tadipatri represents a clear exception to raw materials otherwise used It was necessaryThe process begins when the materials are fed into the cold grinding machine The materials are crushed and ground using special tools such as grinding wheels, blades or beaters At the same time, cold is used to ensure that the temperatures remain low and the materials are not heatedCold grinding crushing materials at low temperatures2016年9月1日 In contrast, increasing the separator speed from 60 to 80 rpm at a constant grinding pressure results in a reduced raw material production rate from 240,000 kg/h to 230,000 kg/h and which Operational parameters affecting the vertical roller mill 2013年1月1日 There are additions in most chapters including abrasives, dressing, cooling, highspeed grinding, centreless grinding, materials, wear, temperatures and heat transfer There are numerous worked Principles of Modern Grinding Technology ResearchGate
.jpg)
2 µm 5 µm Loesche
Grinding of cement clinker and granulated blast furnace slag in roller grinding mills (vertical airswept grinding mills) is a technology introduced by Loesche The first use of a Loesche mill, with a grinding track diameter of only 11 metres, was used as long ago as 1935 However, the breakthrough in grinding this type of material on the verticalcommon solution to grind raw materials and cement Roller presses are used mainly in combination with a ball mill for cement grinding applications and as finished product grinding units, as well as raw ingredient grinding equipment in mineral applications This paper will focus on the ball mill grinding process, its tools and optimisationBALL MILLS Ball mill optimisation Holzinger Consulting2021年1月1日 Stacking Reclaiming of Raw material: Swing type stacker Reclaimer: Limestone other raw material are stored in open area into a longitudinal storage unit called stockpile through Stacker These are then extracted transversely from the stockpile through reclaimer: 3: Raw Meal Grinding Homogenization: Grinding Mill Vertical Roller Mill Review on vertical roller mill in cement industry its performance 2021年1月29日 Vertical roller mills, VRMs, are widely used for grinding raw materials in factories engaged in the extraction and processing of minerals Any machine used for grinding or crushing consumes around Increase productivity of vertical roller mill using seven QC tools
.jpg)
(PDF) Modeling of Raw Material Mixing Process in Raw Meal Grinding
2010年10月1日 The objective of the present study is to build a reliable model of the dynamics among the chemical modules in the outlet of raw meal grinding systems and the proportion of the raw materials2021年2月1日 Secondary grinding was investigated as a mean of liberating glass from locked particles of glass and resin obtained by the primary shredding from the siliconbased PV panelsSelective grinding of glass to remove resin for siliconbased For the past three decades the vertical roller mill has emerged to be the preferred choice for grinding raw materials[12] It has advantages like low power consumption, process simplifications and compactness but it is also very sensitive to vibrations and can deteriorate productivity if process optimization is varied slightlyIndicate Contributions from Several Radial VHYHQ4WRROVThere can be number of reasons why a feed miller experiences shrinkage of raw material With net profit margins in some feed companies being low as 1 to 2 Moisture check in raw material before or at the time of procurement 2 Sampling at different locations – after batching grinding conditioning – pelleting – cooling Process Loss – Raw Material Shrinkage – Moisture Loss in Feed
.jpg)
Grinding of Australian and Brazilian Iron Ore Fines for Low
2024年2月26日 Oxidised pellets have become an indispensable highquality charge for blast furnaces Nevertheless, highquality pellet feeds are becoming scarcer and scarcer To broaden the range of sources of pellet feeds and reduce the production cost of pellets, more steel mills are predicted to use coarse iron ore fines with a relatively low iron grade and low impurities for the 1 Raw material source(s): by vendor, including vendor establishment number , pack dates (or bone dates), receive dates, raw material type, time used, quantity used, and any other plantspecific identification information provided (eg, shift vat number, serial number) 2 Rework: if used, should be treated as a raw material sourceBest Practices for Raw Ground Products Beef Industry Food In the cement industry, highpressure grinding rolls have proven their worth not least due to their low energy requirements and have been used worldwide for decades for grinding cement raw material, cement clinker, and granulated polycom® HPGR cuttingedge technology in the materials, and thus are called difficulttocut materials When grinding difficulttocut materials, various problems and negative effects to the production need to be considered Any of them can seriously effect the production lead time and the overall cost (Table 2) In this article, we will introduce reasons why it is more challenging to grindGrinding Theory and material Troubleshooting for Grinding
.jpg)
Everything you need to know about cement Materials
material in the mill is not affected by the material moisture, although some loss in grinding efficiency was observed when the fresh material at the mill inlet had moisture of more than 68% The Horomill used as a raw mill is claimed to 2012年2月9日 Figure 3 represents the typical process flow of a gascooled low concentration bag filter Here the raw material grinding arrangement employs a dedicated circulation pump typically a threefan system Gas from the preheater passes through the ID fan and all the waste gas leaving it is sent to the raw mill where it dries the raw materialTreating Waste Gases World Cement2024年10月11日 The grinding time of raw materials ranged from 05 to 3 h, corresponding to a decrease of 239 % in the absolute dry density of the specimen from 046 to 035 g/cm 3, and an increase of 561 % in the water absorption rate from 889 % to 1388 %Effect of raw material fineness on the properties of inorganic To date, the biggest KHD reference machine in the market is a 700 tph raw material grinding circuit in finish mode that is based on a single roller press To be still able to offer a solution when theMULTIPLE MATERIALS, ONE SOLUTION ROLLER PRESS

Chapter 18 Feed Milling Processes Food and Agriculture
Heat imparted to the material, due to the work of grinding, is related to the time it is held within the chamber and the air flow characteristics Impact grinding is most efficient with dry, lowfat ingredients, although many other materials may be reduced in size by proper screen selection and regulated intake2023年8月25日 Automation certainly has inundated every facet of the manufacturing landscape, from rawmaterial delivery to the finished part, component, assembly or product out the door—we see examples of this in every issue of MetalForming For a variety of reasons, finishing processes always seemed to lag a bit behind on the automation trainRobotic Grinding—Ready for Prime Time2019年10月11日 Most raw materials used in feed mills must be ground This process improves the performance of the animal and feed processing, especially mixing homogeneity and pellet quality Grinding is a key step in the feed production process and offers numerous possibilities for modification and optimizationGrinding: benefits of particle size modification Feed StrategyFor drying the wet raw material it is necessary that prior to the mill start up the grinding plant isheated for some timeOtherwise the cold grinding plant would take away too much heat from the drying process and the finish product would not be dry – handling problems in the meal transport and silo extraction would followPROCESS TRAINING for operators of Vertical RAW Mills
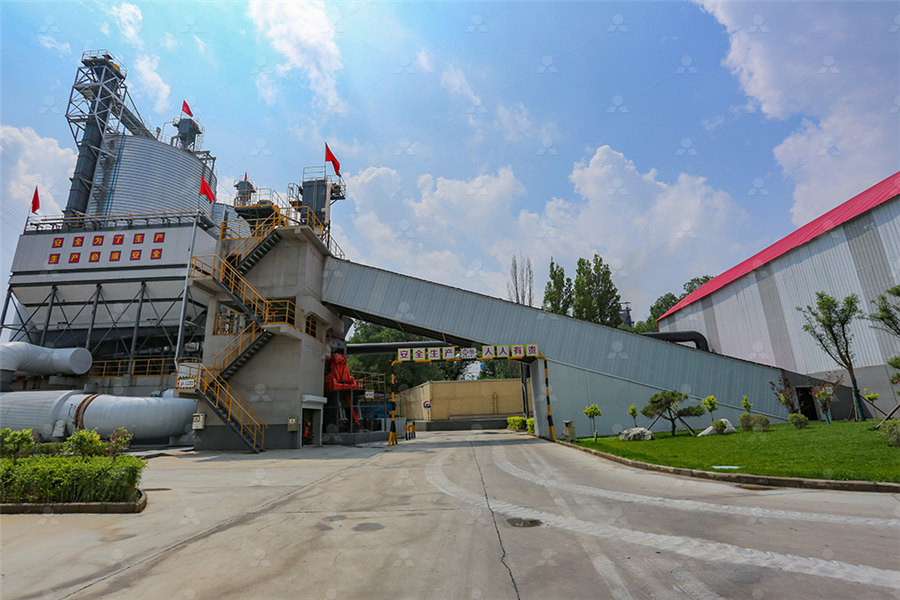
Polysius Roller Mills For grinding
4 Advantages of Polysius roller mills at a glance: xHigh operating reliability and availability, as well as easy system handling, due to the fact that grinding, drying and separation all take place in a single compact unit xConsistently high product quality with minimum energy requirement, due to the integrated highefficiency1985年11月1日 This paper discusses raw materials used in ancient glasses Following a consideration of some archaeological reasons for studying glass, the discussion concentrates on the evidence provided by (PDF) The raw materials of early glass production ( 2024年9月4日 alwepo, Raymond Mill is an industrial equipment used to grind raw materials into fine powder This equipment is commonly used in industries such as mining, metallurgy, chemistry, and construction materials Its efficient What is Raymond Mill? How Does It Work? alwepoThe power ingesting of a grinding process is 5060% in the cement production power consumption The Vertical Roller Mill (VRM) reduces the power consumption for cement grinding approximately 3040% associated with other grinding mills The process variables in cement grinding process using VRM are strongly nonlinear and having large timePROCESS CONTROL FOR CEMENT GRINDING IN VERTICAL
.jpg)
A Review on the Effects of Pretreatment and Process Parameters
2022年10月4日 The development and utilization of biomass can not only address the demand for lowcarbon energy and reduce environmental pollution, but can also facilitate the achievement of carbon neutrality However, there are many factors justifying the case for low utilization of agricultural residues These factors could be well controlled by producing topquality pellets 2024年4月19日 Discover the inner workings of grinding machines and learn how they transform raw materials into finished products 899 Sheridan Dr, West Chester, Pennsylvania Mon – Sat: 9:00am–18:00pmThe Grind: Understanding The Processes Of Grinding MachinesHowever, for the best possible starting conditions, MDLargo should be used for fine grinding of materials with a hardness below 150 HV, and MDAllegro should be used for fine grinding of materials with a hardness of 150 HV and higher Plane grinding with diamond is the best choice to ensure flat samples from the very beginning of the preparationMetallographic grinding and polishing insight Struers2021年3月3日 Cement is produced by a hightemperature (about 1500 °C) reaction in a rotary kiln of carefully proportioned and blended ratios of lime (CaO), silica (SiO 2), alumina (Al 2 O 3), and iron oxide (Fe 2 O 3)The production of cement is a chemical process requiring an accurate blend of the previously cited four key organic oxides and the limitation of several undesirable Cement SpringerLink
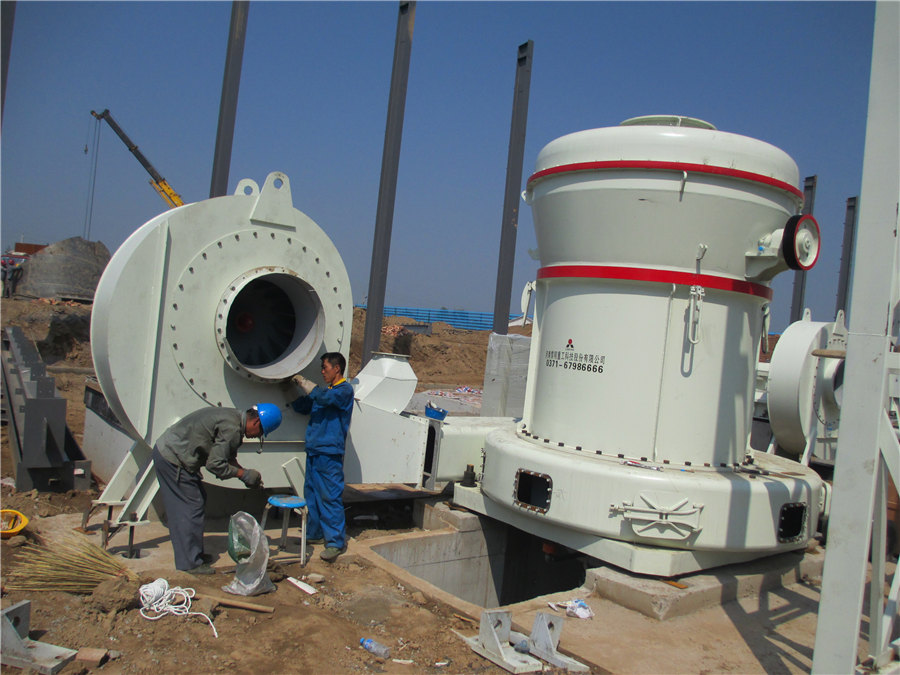
raw materials butzbacherd
When the dressing infeed is reduced to that for conventional grinding wheels, sintered aluminium oxide produces optimal grinding results, and low peaktovalley roughness does not pose a problem The lifespan of a sintered aluminium oxide grinding wheel can be much longer than that of other conventional wheels (special fused aluminium oxide, silicon carbide), but it costs only 2023年9月7日 However, this process ensures that your workpiece attains a perfectly round shape after grinding to achieve roundness from outofround conditions, regardless of its irregularities The outofround or high points experience more material removal from the grinding wheel than the low points as the workpiece rotatesThe Ultimate Guide to Understanding Centerless Grinding