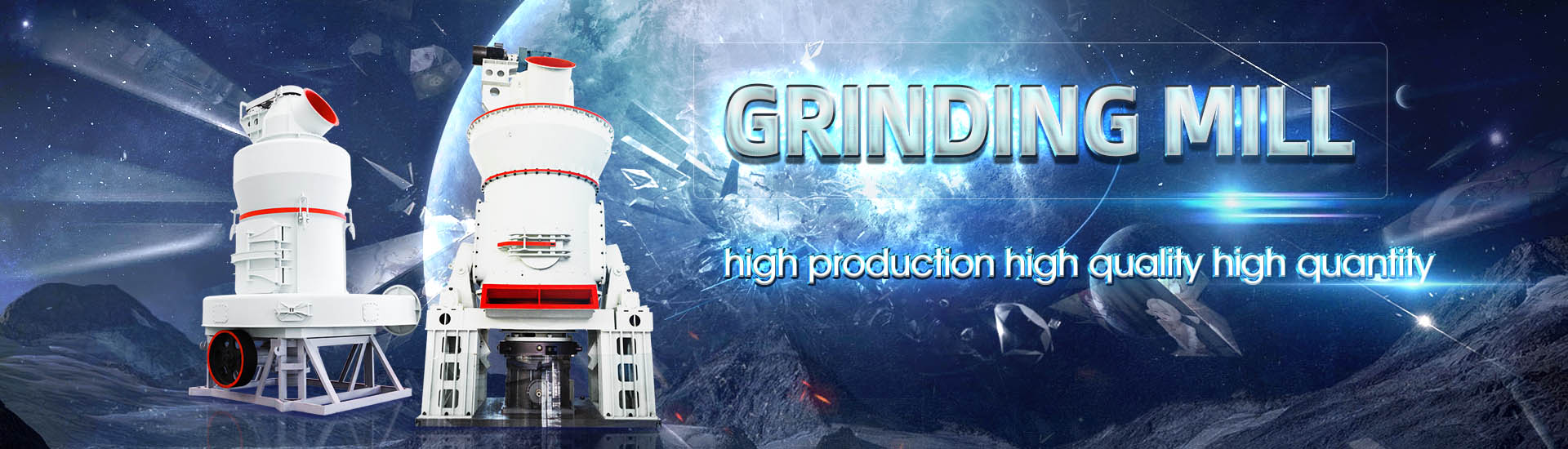
Relationship between ball mill processing capacity and discharge fineness
.jpg)
A comparative study on a newly designed ball mill and the
2020年1月1日 Mill with lifters has minimum recirculating load compared with mill without lifters The discharge end design of a ball mill plays an important role in discharging the desired 2018年6月1日 In this article the effect of grinding media size distribution and feed material particle size distribution (PSD) on the product fineness requirements were investigated A Effect of ball and feed particle size distribution on the milling The wellknown tradeoff when aiming to increasing ball mill throughput between capacity benefits from increasing circuit recirculating load, versus diminishing classification efficiency, is Digital Solutions to Evaluate Ball Mill Circuit Recirculating Load 2012年6月1日 Grinding in ball mills is an important technological process applied to reduce the size of particles which may have different nature and a wide diversity of physical, mechanical Grinding in Ball Mills: Modeling and Process Control ResearchGate
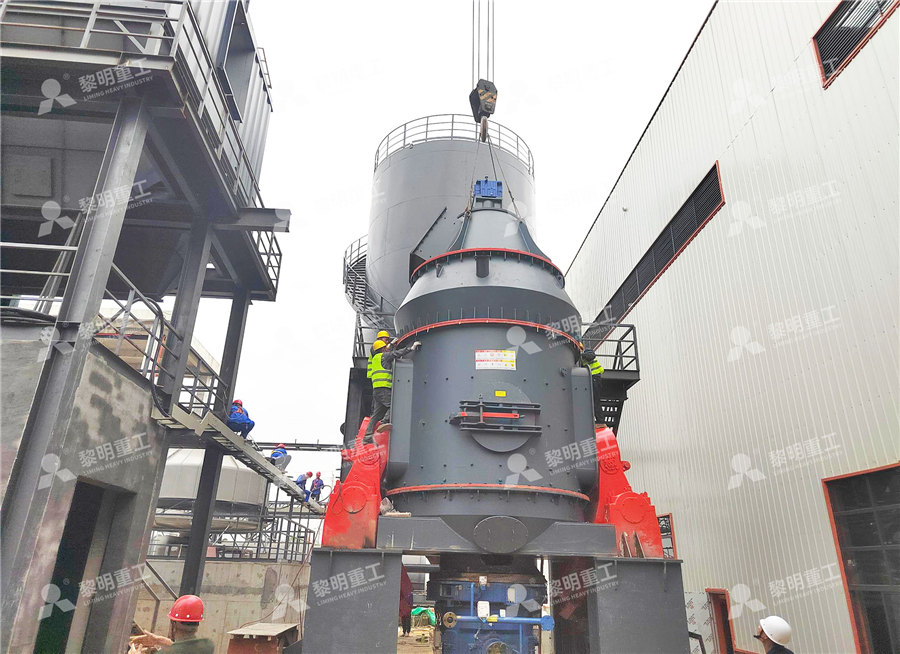
Effect of ball and feed particle size distribution on the milling
2018年2月1日 It was found that the ball mill consumed 5467 kWh/t energy to reduce the F 80 feed size of 7222 lm to P 80 product size of 2754 lm while stirred mill consumed 3245 kWh/t 2021年2月19日 Optimization results confirmed that the balls to powder weight ratio were the most influential process parameter The optimum process parameters setting concluded that Comparative Study on Improving the Ball Mill Process Parameters 2 BALL MILLS INTERNATIONAL CEMENT REVIEW FEBRUARY 2021 aim of delivering a target mill discharge size at the end of the chamber, with a maximum residue of five per cent >2mm BALL MILLS Ball mill optimisation Holzinger ConsultingAbstract: The particle size distribution of ball mill grinding products is an important production index of the grinding operation, and due to its multivariate strong coupling and nonlinearity in Reinforcement learning based ball mill discharge size distribution
.jpg)
(PDF) Optimization of mill performance by using online ball and
2010年3月10日 Ball mills are usually the largest consumers of energy within a mineral concentrator Comminution is responsible for 50% of the total mineral processing cost In 2018年6月1日 It was also observed that a binary mixture resulted in more material reporting to the required product fineness compared to having two mills in series with one having 20 mm and other 10 mm ball size For the finer feed material, it was also observed that a binary mixture again resulted in more material reporting to the required product specificationEffect of ball and feed particle size distribution on the milling or double helical scoop feeder Several types of ball mills are distinguished depending on the discharge system and these types are commonly known as overflow discharge mill, diaphragm or grate discharge mill and centreperiphery discharge mill, eg see [23] In industrial applications, the inner surface of the millGrinding in Ball Mills: Modeling and Process Control SciendoDimensionality in mill design Ball mill shape factors in the period prior to 1927 (Taggart, 1927) averaged ll/1 for 29 center discharge mills and 10/l 30 peripheral discharge mills With the resumption of new plant construction after the 1930s depression, Morenci concentra tor continued the l/1 ratio with its 31 x m (IDimensionality in ball mill dynamics Springer

Ball Mill an overview ScienceDirect Topics
Typical types of small ball mill known as pot mill (Fig 411) was introduced for grinding ceramic and cement raw materials in laboratories The larger balls and also coarser particles of the feed are supposed to segregate in the mill There is a definite relationship between the size of particles and the size of balls required for effective The application range of ball mill is wider, which can grind metal, nonmetal or stone 6 The discharge fineness is different The grinding fineness of ball mill is finer with 007404mm, while the output fineness of the rod mill is between 08330147mm 7 Different performance7 Differences Between Ball Mill and Rod Mill Knowledge The 2016年4月22日 The apparent difference in capacities between grinding mills (listed as being the same size) is due to the fact that there is no uniform method of designating the size of a mill, for example: a 5′ x 5′ Ball Mill has a working diameter of 5′ inside the liners and has 20 per cent more capacity than all other ball mills designated as 5′ x 5′ where the shell is 5′ inside diameter and Ball Mill Rod Mill Design 911Metallurgist1996年1月1日 The Mill Filling Inference Tool which has been implemented at several mine sites, compares SAG mill load cell and power draw measurements with outputs of a semimechanistic power model to estimate Power draw of wet tumbling mills and its relationship to charge
.jpg)
Closed circuit ball mill – Basics revisited ScienceDirect
2013年4月1日 Circulating load and classification efficiency effect on ball mill capacity revisited Relative capacity model introduced and validated Relationship between circulating load and classification efficiency verified by industrial data Existing fine screening technology could increase ball mill circuit capacity 15–25%2023年2月15日 Ball mill and rod mill Differences between ball mill and rod mill 1 Different capacity and granularity Ball mill The capacity of ball mills is 065 ~ 615t/h, and the discharge particle size of the ground material is 0074 ~ 04mm Rod mill The capacity of rod mills is 062 ~ 180t/h, and the discharge particle size is 0147 ~ 0833mm 2What Are the Differences between Ball Mill and Rod Mill?Discharge of pebbles, finer rock, ball scats and slurry from mills and its flow through trommels, and into other processing operations has strong impacts on ball mill performanceSIMULATION OF OVERFLOW BALL MILL DISCHARGE AND 2020年7月2日 The vibration of the ball mill foundation will seriously affect the operation stability of the ball mill According to the connection relationship between the ball mill and the foundation, the (PDF) Effects of Ball Size Distribution and Mill Speed and Their
.jpg)
Effect of ball and feed particle size distribution on
2018年2月1日 In another study to investigate ball size distribution on ball mill efficiency by Hlabangana et al [50] using the attainable region technique on a silica ore by dry milling, a threeball mix of 2007年12月1日 Request PDF Relationships between processing, morphology and discharge capacity of the composite electrode The cycled capacity of Li11V3O8 based positive electrodes varies between 100 and Relationships between processing, morphology and discharge capacity 2024年2月19日 The ratio of steel balls in the ball mill depends on the effective length of your mill, whether it has a roller press, the size of the feed particles, the lining and structure used, the expected sieve residue fineness and ratio, how many chromium balls to operate, and the rotation speed How much and other factors make a comprehensive judgmentBall Mill Steel Balls: Quality And Gradation JXSC Mineral2020年11月16日 where v = peripheral speed of the mill in feet per minute If the observed capacity of a mill at speed n1 is = T1 tph, the capacity T2 of the same mill at speed n2 should be The acceleration factor of the ball or rod mass is a function of the peripheral speed of the mill Thus P = f4(F) = f1(D²)f5(υ) Indicating that υ = πDn, andBall Mill Capacity and Power Consumption Relationship to Mill

Dynamic modelling, Ball mill, Mill control, Temperature, Energy
2019年9月1日 balance data is related to mill temperature where the latter is believed to be a primary indicator of inmill process dynamics [21, 12] It is a known fact that the biggest part of energy introduced in a ball mill is converted into heat, with only about 3 5% of this energy being used to grind the ore to the required finenessor double helical scoop feeder Several types of ball mills are distinguished depending on the discharge system and these types are commonly known as overflow discharge mill, diaphragm or grate discharge mill and centreperiphery discharge mill, eg see [23] In industrial applications, the inner surface of the millGrinding in Ball Mills: Modeling and Process Control Sciendo2014年1月1日 In this work the relation between the change in mill output and cement fineness caused in the ball mill grinding process of composite cement with respect to different operating input parameters Optimization of ball mill operating parameters for their effect on mill 2015年6月19日 The basic parameters used in ball mill design (power calculations), rod mill or any tumbling mill sizing are; material to be ground, characteristics, Bond Work Index, bulk density, specific density, desired mill tonnage capacity DTPH, operating % solids or pulp density, feed size as F80 and maximum ‘chunk size’, product size as P80 and maximum and finally the type of Ball Mill Design/Power Calculation 911Metallurgist
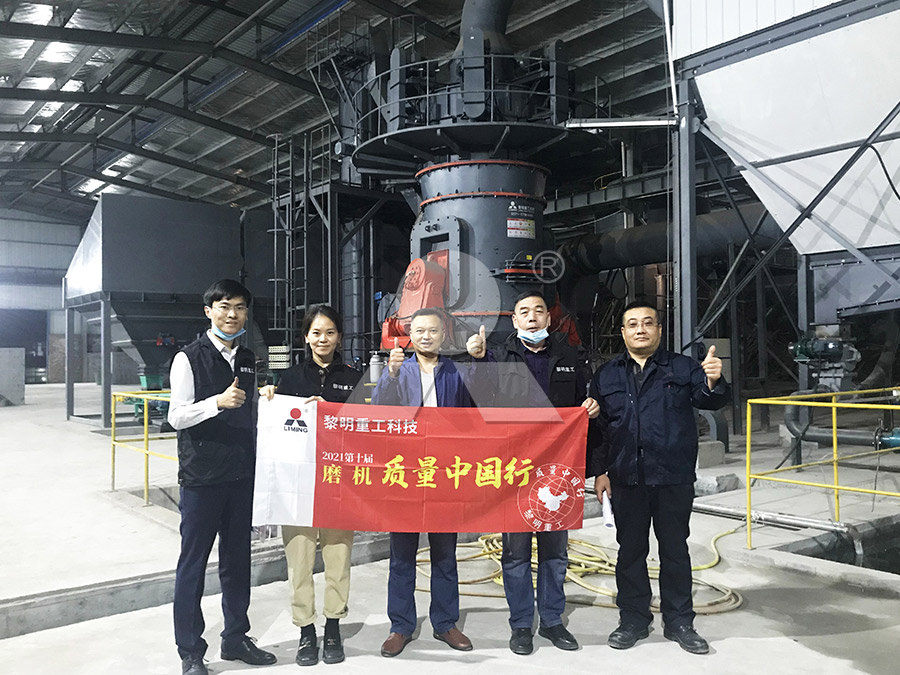
Influence of dry and wet grinding conditions on fineness and
2011年1月31日 The influence of grinding conditions on the production of fine particles and the width of the particle size distribution produced during ball mill grinding was investigatedGenerally, the filling rate of ball mill is 40% – 50%, and that of rod mill is 35% – 45% 5 Fineness of Product The discharging fineness of the material milled by ball mill is between 007404mm, and that of the material milled by rod mill is 9 Difference Between Ball Mill and Rod Mill How To 2019年11月26日 Difference Between SAG Mill and Ball Mill, from the working principle, application, Sometimes, in order to improve the processing capacity of the mill, a small amount of steel balls be added appropriately, usually What’s the Difference Between SAG Mill and Ball Mill2004年12月1日 The grinding parameters were adjusted over time to maximize mill productivity under stable conditions while achieving similar Blaine fineness as the control mix (ie, Blaine of 3850 ± 75 cm 2 /g)Optimization of continuous ball mills used for finishgrinding of
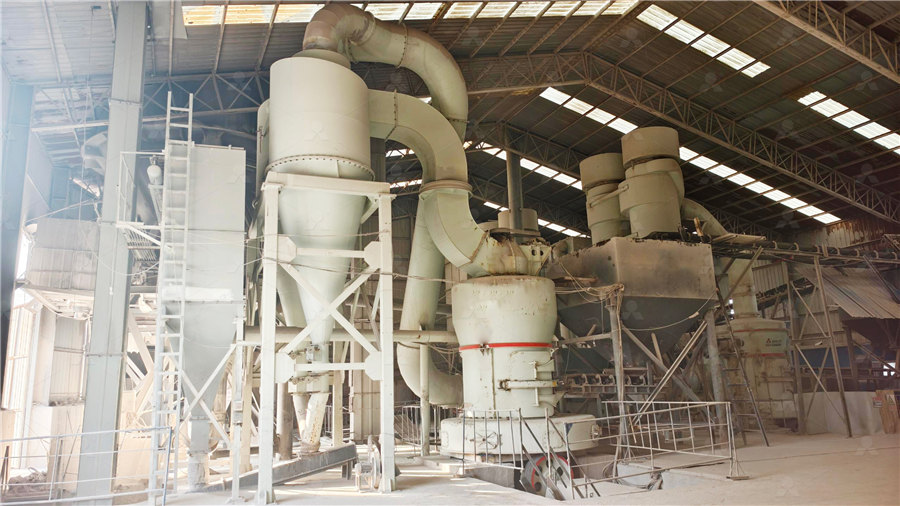
Ball Mill Circulating Load Formula 911Metallurgist
2015年10月9日 These volume constraints are not always readily apparent, leading to the assumption that the increased circulating load has limited the ball mill capacity Therefore, changes to the pump and cyclone may be required to handle the higher circulating load caused by an increased new feed rate Over Grinding The circulating loads generated in a 2023年10月27日 The ball mill is a rotating cylindrical vessel with grinding media inside, which is responsible for breaking the ore particles Grinding media play an important role in the comminution of mineral ores in these mills This work reviews the application of balls in mineral processing as a function of the materials used to manufacture them and the mass loss, as A Review of the Grinding Media in Ball Mills for Mineral Processing BARKHUYSEN, NJ Implementing strategies to improve mill capacity and efficiency, with platinum references and case studies The 4th International Platinum Conference, Platinum in transition ‘Boom or Bust’, The Southern African Institute of Mining and Metallurgy, 2010 Implementing strategies to improve mill capacity andImplementing strategies to improve mill capacity and efficiency, 2019年10月26日 Difference on applications between ball mill and grinding mill Grinding Fineness the discharge fineness of the grinding mill is adjusted by the fan air volume, Ball mill production capacity can be adjusted between 065615 tons In general, Difference and Choice of 2 Common Mills, Ball Mill and Grinding Mill FTM
.jpg)
(PDF) Power consumption management and simulation of
2022年3月15日 These mills consume enormous amounts of electrical energy (5060%); consequently, comminution costs roughly 60% of the overall investment in a beneficiation plant [2,3]2017年2月13日 where an approximate figure for the constant is 35 for rod mills, 40 for overflow ball or pebble mills and 45 for grate discharge ball or pebble mills ç is specific gravity of grinding media (for rods or balls normally 785) q is the charge volume in fraction of mill volume (40 % = 040) nc is the mill speed in fraction of critical speedBall Mills 911MetallurgistDownload scientific diagram – Relation between the grinding fineness and specific grinding work for several materials from publication: Empirical and scaleup modeling in stirred ball mills Relation between the grinding fineness and specific grinding 2024年9月20日 Ball mills operate on the principle of impact and attrition: in the operation of the mill, the grinding media in the mill throw itself against the material to be ground to produce fine particles This process is used to reduce the size of the ore to the necessary extent before proceeding, for instance, to flotation or magnetic separationThe Role of Ball Mills in Mineral Processing: A Comprehensive
.jpg)
Grinding SpringerLink
2022年2月28日 Some investigations demonstrate that stirred mills (compared to ball mills) have better performance when grinding occurs on a micronscale This improvement is because the mechanism of supplying energy during stirred milling is different from what happens in ball mills In ball mills, the abrasive and impact stress lead to particle breakage2020年5月1日 The main aim of this study is to improve the processing capacity of the largescale ball mill Taking a Φ549 × 883 m ball mill as the research object, the reason for the low processing capacity of the ball mill was explored via process mineralogy, physicochemical analysis, workshop process investigation, and the power consumption methodEnhancing the capacity of largescale ball mill through process 1996年4月1日 The discharge end design of a ball mill plays an important role in discharging the desired particle sizes (−150 + 10 µm) and the percentage of recirculating load from the discharge end of the Slurry discharge capacity of autogenous and semiautogenous mills 2017年7月1日 Combined DEM and SPH simulation of overflow ball mill discharge and trommel flow Author links open Due to the fineness of the feed material in such a ball mill, SPH method variant used here for fluids is a quasicompressible formulation with an equation of state specifying the relationship between particle density and Combined DEM and SPH simulation of overflow ball mill discharge
.jpg)
(PDF) Energy Efficient Ball Mill Circuit – Equipment Sizing
2013年7月15日 PDF The ball mill in closed circuit with hydrocyclones is an industry standard, and well known methodologies exist for equipment sizing, selection and Find, read and cite all the research 2021年6月29日 This article deals with the preparation and laboratory milling of βdicalcium silicate Dicalcium silicate is the second most important calcium silicate of Portland clinker βC 2 S is usually Effects of Mill Speed and Air Classifier Speed on Performance of 2023年11月24日 Matsanga, N; Nheta, W; Chimwani, N Grinding Media in Ball Mills for Mineral Processing Encyclopedia Available online: https media consumption In a grate discharge mill, the impact is a major player in the media there is a need to investigate the relationship between worn balls and mill speed, liner profiles Grinding Media in Ball Mills for Mineral Processing2020年3月1日 Taking a Φ549 × 883 m ball mill as the research object, the reason for the low processing capacity of the ball mill was explored via process mineralogy, physicochemical analysis, workshop Enhancing the capacity of largescale ball mill through process

Ball Mill VS Rod Mill: Difference Selection JXSC Machine
2024年1月10日 The Similarities Between Ball Mill And Rod Mill Appearance: and relatively high fineness of materials Usually, the discharge degree is between 0074~04mm, the discharge particle size is which has larger production capacity and higher efficiency A rod mill can be used instead of a shorthead cone crusher for fine crushing