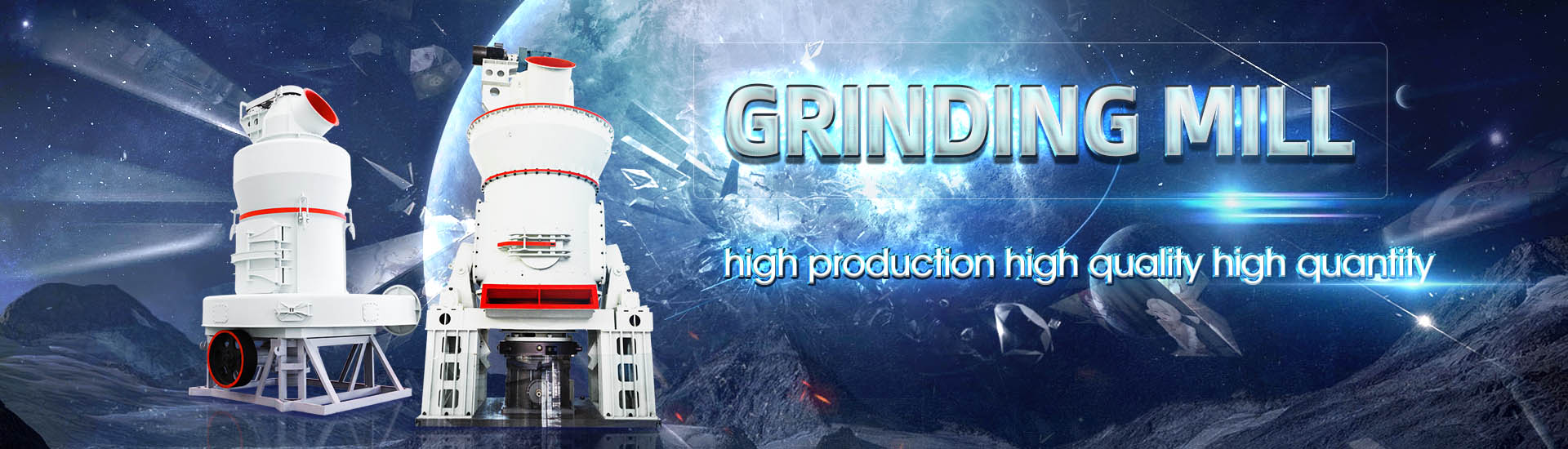
Cement kiln current
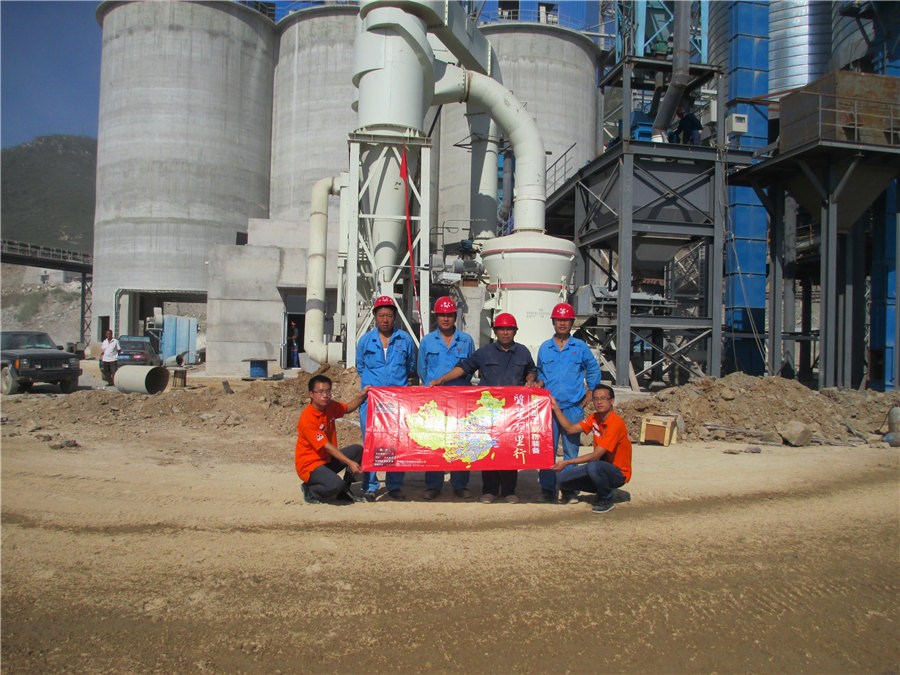
Modern Kiln Burner Technology in the Current Energy
The current manuscript presents a review on existing kiln burner technologies for the cement production process, in the context of the current climate of energy transition and environmental remediation2023年2月17日 The current manuscript presents a review on existing kiln burner technologies for the cement production process, in the context of the current climate of energy transition and environmental(PDF) Modern Kiln Burner Technology in the Current 2024年3月28日 Climate impacts per tonne of clinker produced today in European countries Paving the way for sustainable decarbonization of the European 2022年7月1日 Cement facilities currently use regionally available biomass: nutshells are used Current state of industrial heating and opportunities for
.jpg)
IMPROVING THERMAL AND ELECTRIC ENERGY EFFICIENCY AT
experience in the cement sector and focus on specific technical measures that could be homogenised, ground and finally fed into the cement kiln These natural materials chemically European Cement Research European Cement Research Academy2022年5月27日 Retrofitting the cement plants to oxyfuel reduces climate change impacts LCA and negative emission potential of retrofitted cement plants 2022年11月28日 Cement kiln coprocessing (CKC) is a promising technology for solid waste Technological opportunity identification of cement kiln co
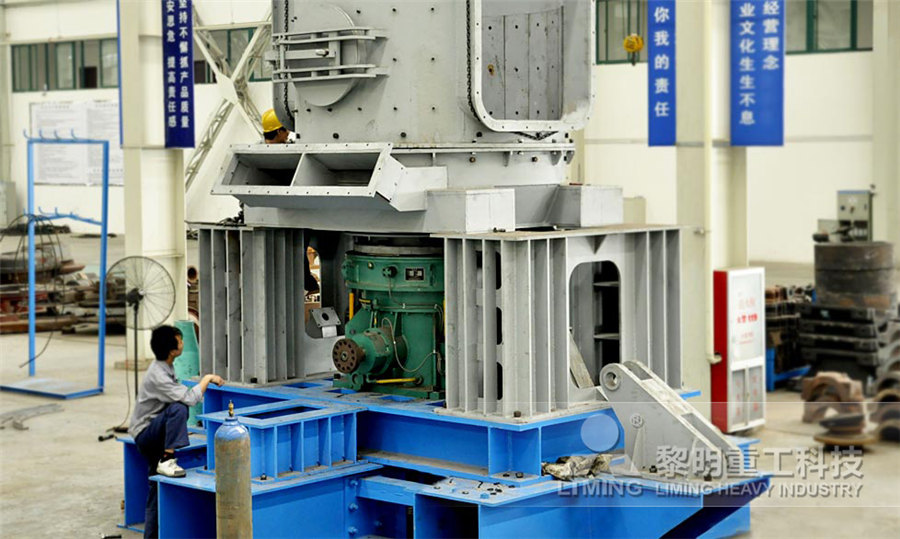
Recent Progress in Green Cement Technology Utilizing
2019年1月21日 With an estimation of over 35 billion tonnes of cement produced annually, approximately 900 kg of CO 2 is released per one tonne of cement produced [7] This estimation equates over 3 billion tonnes of CO 2 per year 2020年9月22日 Modern cement kilns are also extremely flexible in terms of fuel source and Environmental impacts and decarbonization strategies in the Temperatures of the air entering the kiln and leaving the kiln should be held as nearly constant as possible in order not to upset the heat profile in the kiln By weigh each unit of fuel burned (lb or kg) requires approximately units (lb or kg) The Air Circuit in a Rotary Kiln INFINITY FOR Clinker: reactions in the kiln The milled and blended raw materials go to a silo and then to the kiln Reactions which take place as the feed passes through the kiln are reviewed below They can be considered under three broad headings: Reactions in the cement kiln clinkering
.jpg)
Everything you need to know about Cement Kiln Dust
Everything you need to know about Cement Kiln Dust Generation and Management The cement industry prepared an enforceable agreement or contract for CKD management that would retain the current exclusion from Presented at 2008 IEEE/PCA 50th Cement Industry Technical Conf, Miami, FL, May 1922, 2008 1 BENEFICIAL USES OF CEMENT KILN DUST By: IEEEIAS Cement Industry Committee Wayne S Adaska, PE, Director, Public Works, Portland Cement Association Donald H Taubert, Director, Promotion Technical Service, Capitol Cement Abstract:BENEFICIAL USES OF CEMENT KILN DUST Alternative MaterialsFor more than 100 years, FLSmidth has been delivering cement kilns that are tested, reliable, and require minimal energy and space Our cement rotary kilns deliver high production capacity with long lifespans and low maintenance And now, with online condition monitoring services, we can optimise kiln performance even further and help you design a smarter, more effective kiln Kilns FLSmidth CementPicture: ©NERC: British Geological Survey Cat No P Front end of Ribblesdale Kiln 2 (constructed 1937): shell constructed mainly from staggered semicircular sections, with all joints riveted Picture: ©Rugby Archive: Cat No RC368 Back end of Southam Kiln 7 (constructed 1961): shell entirely welded The shell still consists of staggered halfcylindrical sectionsCement Kilns: Design features of rotary kilns

Modeling of Rotary Kiln in Cement Industry ResearchGate
2016年1月1日 Length, diameter and outdoor cement kiln 70, respectively, 41 and 45 meters Average thickness of 15 cm r efractory magnetite, which can be considere d to be uniform throughout t he cooking areaCement is manufactured from organic materials heated together at high temperatures to form a rocklike solid Chunks are then ground into a fine powder At the lower end of the kiln, a roaring flame heats the material to about 2,700 degrees Fahrenheit, making it partially moltenHow Cement is Made Portland Cement Association2023年10月26日 In the current study, the effect of cement kiln dust on the fresh and hardened cement mortar was investigated; chemical analysis of the binder was also included Cement kiln dust (CKD) content (% by dry weight of cement) was from 0 to 100% The fresh property of the cement was evaluated by flow table test, and the evaluation of hardened properties was based Soft computing techniques to estimate the uniaxial compressive 2022年5月27日 With the use of oxyfuel combustion, the cement kiln process itself must be modified considering current and future electricity mixes and intended climate targets to be achievedLCA and negative emission potential of retrofitted cement
.jpg)
Cracking the problem of cement, one of climate’s
2024年1月3日 Industrialscale cement is a multifaceted climate conundrum Making it is energy intensive: the inside of a traditional cement kiln is hotter than lava in an erupting volcano2022年11月28日 Cement kiln coprocessing (CKC) is a promising technology for solid waste treatment, which can achieve both goals of energy saving for cement production and environment protection for waste reduction, and further development of this technology is desired, so it is necessary to highlight its research gaps between science and technology In this study, a Technological opportunity identification of cement kiln co However, new cement kilns are of the 'dry process' type Dry process kilns In a modern works, the blended raw material enters the kiln via the preheater tower Here, hot gases from the kiln, and probably the cooled clinker at the far end of Manufacturing the cement kiln Understanding Cement rotary kiln A cement rotary kiln is a laterally set cement kiln that is inclined to a certain angle with the ground Raw meals in the kiln body will be calcinated in a lowspeed rotation In present cement plants, the new dry process cement rotary kiln is Cement Kiln Cement Rotary Kiln AGICO Cement Plant Supplier
.jpg)
Rotary kiln process: An overview of physical mechanisms, models
2023年2月25日 The rotary kiln is used in many solid processes, including drying, incineration, heating, cooling, humidification, calcination and reduction This widespread application can be attributed to factors such as the ability to handle varied loads, with large variations in particle size [1]The rotary kiln is a slightly inclined steel cylinder that rests on supports (bearing rollers) Cement particles react with water at their surface The outer layers of a cement particle react, and are replaced with a somewhat thicker layer of hydrate This is exemplified by the progress of reaction of a spherical particle of 14 μm diameter: The cement reacts with about 25% of its mass (or 79% of its volume) of waterCement Kilns: Size Reduction and Grinding2023年4月1日 Furthermore, during cement kiln combustion, the heavy metals could be solidified under hightemperature conditions, while hazardous gases such as furans and dioxins are decomposed (Zhao et al, 2017) However, the current longterm operation process of cement kiln coprocess of sludge has emerged as a problem that needs to be solved urgentlyReview on the use of sludge in cement kilns: Mechanism, 2023年2月17日 The current manuscript presents a review on existing kiln burner technologies for the cement production process, in the context of the current climate of energy transition and environmental remediation Environmental legislation has become ever stricter in response to global climate change, and cement plants need to adapt to this new reality in order to remain [PDF] Modern Kiln Burner Technology in the Current Energy
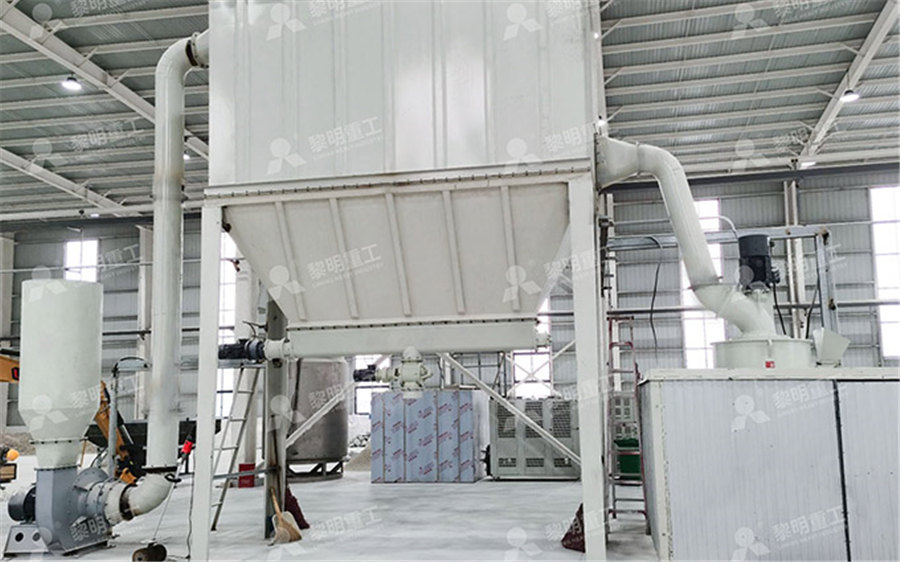
Chapter 10: Rotary Kiln Clinkerization and Thermal Zones
2022年7月2日 In the cement rotary kiln, the gas moves countercurrent (draft) the longitudinal movement of the material The different types of heat transfer in a rotary kiln are:During the complete repair, the kiln must be turned manually as necessary to help the convenient positioning of the weld (> 42m kiln = 8 spokes, 48m kiln = 10 spokes) The weight of the kiln must be supported by hydraulic jacks, mounted on wooden sleepers or steel support structures manufactured on each side of the replacement area and located under the spider reinforcementsSTEPS TO REPLACE KILN SHELL SECTIONS The Cement InstituteOn the raw material preparation page, there's a photo of an xrf bead that I took back in 2002, as part of a training programme I recently noticed that some of my bookshelves can be seen reflected in the bead In comparison with the exasperating difficulties involved in researching 100yearold cement plants, it was quite easy to identify many of the booksCement Kilns: Introduction2024年1月3日 A cement kiln provides an environment conducive to the use of many fuel substances, such as tires, not normally included in the fuel mix Specifically, coal fired; TDF planned In kiln with PH Current use Test use; Tire and TDF Use in Portland Cement Kilns Scrap Tires
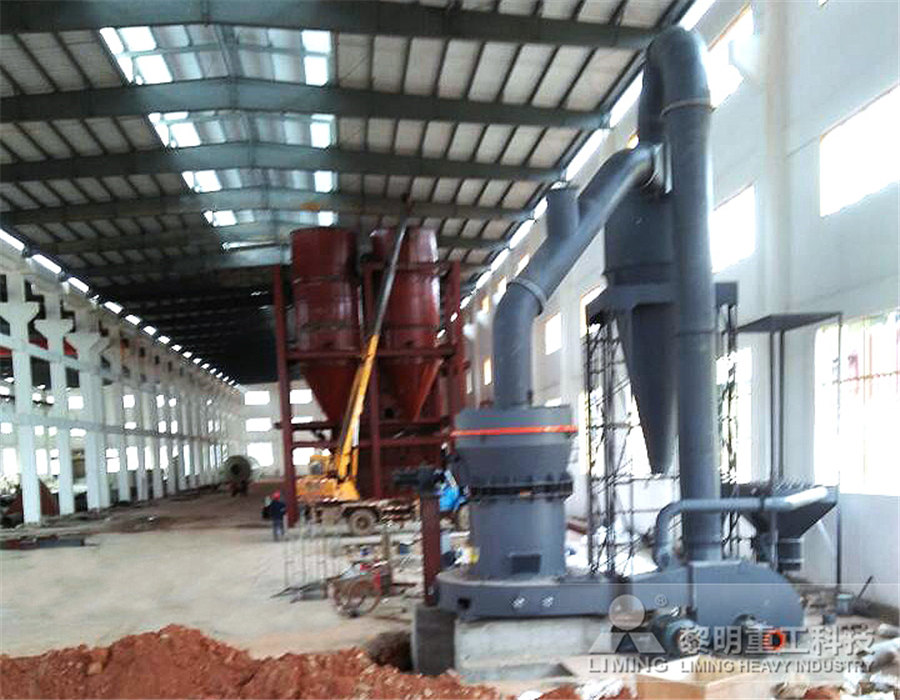
Burning alternative fuels in cement kilns Cement
1 Suitability of cement kilns for the combustion of secondary fuels Compared to other high energyintensive production processes of cement clinker burning process allows a relatively high potential to use secondary fuels [1]This is due Deep decarbonisation of industry: The cement sector Cement sector overview Cement is the binding agent of concrete, the most widely used construction material in the world The cement sector is a major greenhouse gas emitter, responsible for about 7% of CO 2 emissions globally (1), and about 4% in the EUDeep decarbonisation of industry: The cement sector Europa2008年5月18日 Cement manufacturing is a critically important industry in the United States and throughout the world In 2006, US cement plants produced 998 million metric tons of cement Worldwide production accounted for about 25 billion metric tons As with most large manufacturing industries, byproduct materials are generated These industrial byproduct and [PDF] Beneficial Uses of Cement Kiln Dust Semantic Scholar2022年12月21日 The current manuscript presents a review on existing kiln burner technologies for the cement production process, in the context of the current climate of energy transition and environmental (PDF) Modern Kiln Burner Technology in the Current Energy
.jpg)
Energy savings and operation improvement of rotating cement kiln
2016年2月1日 In cement kiln applications, Motor's 2 current flows back via the common DC link to motor 1 The motor's 1 torque constantly increases until its nominal limit imposed by the protection unit of the drive The usage of k f = 0002 improves the situation2024年3月28日 Here we assess 15 decarbonization options for the European cement industry under current and future conditions M Bakken, J Study of a full scale oxyfuel cement rotary kiln Int J GreenhPaving the way for sustainable decarbonization of the European cement 2024年1月10日 Request PDF Municipal solid waste (MSW) coprocessing in cement kiln to relieve China's Msw treatment capacity pressure In many countries, like China, the huge capacity of cement industry Municipal solid waste (MSW) coprocessing in cement kiln to The first rotary kiln was introduced to the cement industry by Frederik Ransome (1885) when he took out a patent in England titled “Improvements in Manufacture of Cement” The first of these rotary kilns were up to 20 m in diameter and 25 Everything you need to know about Kiln Burning
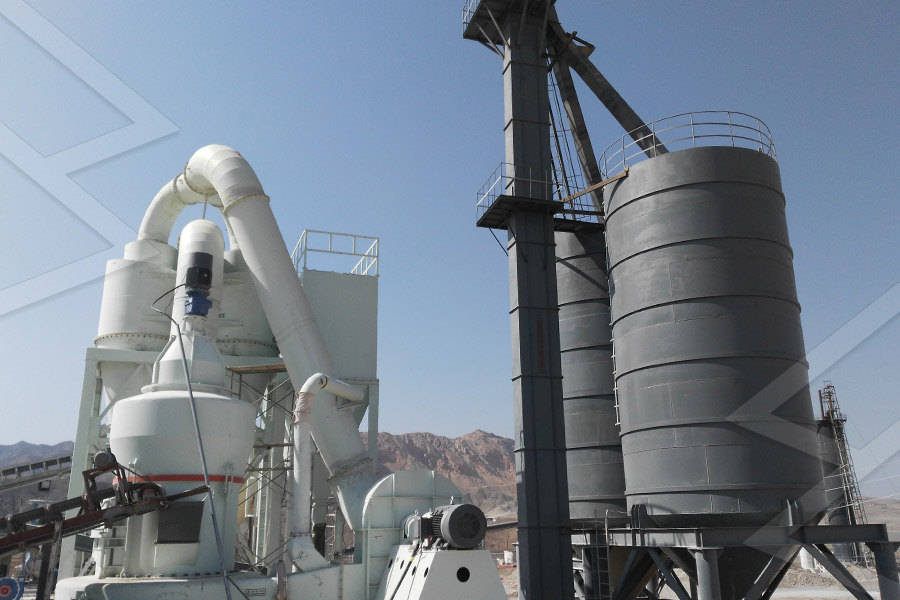
Projecting future carbon emissions from cement production in
2023年12月11日 Achieving lowcarbon development of the cement industry in the developing countries is fundamental to global emissions abatement, considering the local construction industry’s rapid growthCement kilns are used for the pyroprocessing stage of manufacture of Portland and other types of hydraulic cement, in which calcium carbonate reacts with silicabearing minerals to form a mixture of calcium silicatesOver a billion tonnes of cement are made per annum, and cement kilns are the heart of this production process: their capacity usually define the capacity of the cement plantCement kiln chemeuropeKiln performance and reliability is essential to profitable plant operations A rotary kiln shell has to withstand harsh conditions The steel and refractory lining structure is heated by a flame at 2000 °C while the outside surface temperature is around 450 °C, Infrared line scanner for rotary kiln shell temperature monitoring2024年11月23日 Cement Extraction, Processing, Manufacturing: Raw materials employed in the manufacture of cement are extracted by quarrying in the case of hard rocks such as limestones, slates, and some shales, with the aid of blasting when necessary Some deposits are mined by underground methods Softer rocks such as chalk and clay can be dug directly by Cement Extraction, Processing, Manufacturing Britannica

Cement kiln Wikiwand
Cement kilns are used for the pyroprocessing stage of manufacture of portland and other types of hydraulic cement, in which calcium carbonate reacts with silicabearing minerals to form a mixture of calcium silicatesOver a billion tonnes of cement are made per year, and cement kilns are the heart of this production process: their capacity usually defines the capacity of the cement plant2020年5月15日 Portland cement is produced by one of the highest energyconsumptive industrial processes Within the process, the rotary kiln represents one of the major sources of thermal energy loss Based on the lengthwise temperature profile of the kiln, an optimal placement for heat recovery is identified based on the highest surface temperaturesDesign Optimization of Waste Heat Recovery System around Cement Rotary KilnThe cement kiln is a vital component of the cement manufacturing process, playing a critical role in the production of highquality clinker Advances in kiln technology have significantly improved energy efficiency, reduced emissions, and enhanced the overall sustainability of Comprehensive Guide to Cement Kilns: Processes, Types, Such a kiln usually requires additional labor to attend the granulator plant DRYPROCESS KILNS As the term indicates, in this process the kiln feed enters the kiln in dry powder form Dryprocess kiln dimensions are similar to wet kilns in that they are long and typically show a lengthtodiameter ratio of approxi mately 30:1 to 35:1Types of Rotary Kilns INFINITY FOR CEMENT EQUIPMENT
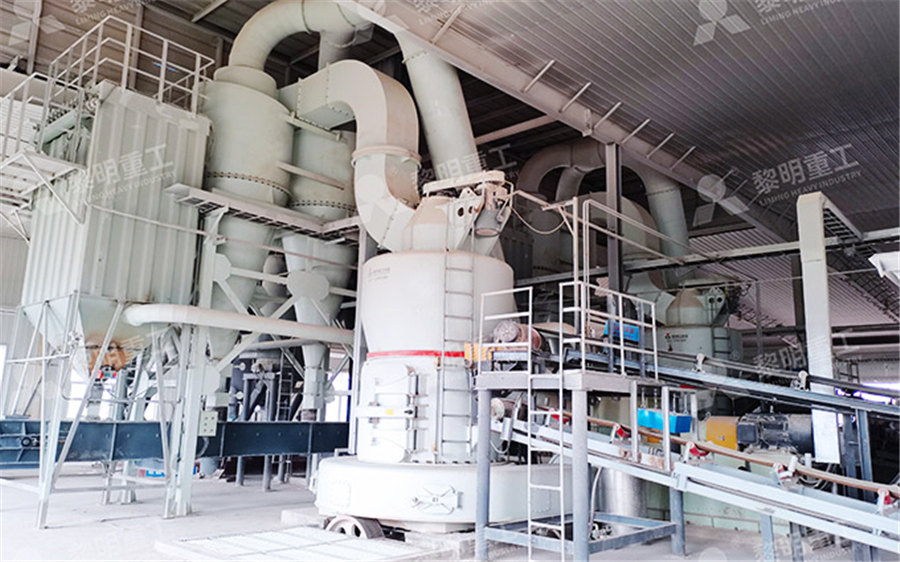
Cement Kiln an overview ScienceDirect Topics
Cement kiln is used for calcining cement clinker and it can be used widely for cement, metallurgical, chemical industries, etc As a result, the present average kiln efficiency level in a country is not representative of current worldwide best practices Kiln control is one of the most vital parts in the cement production