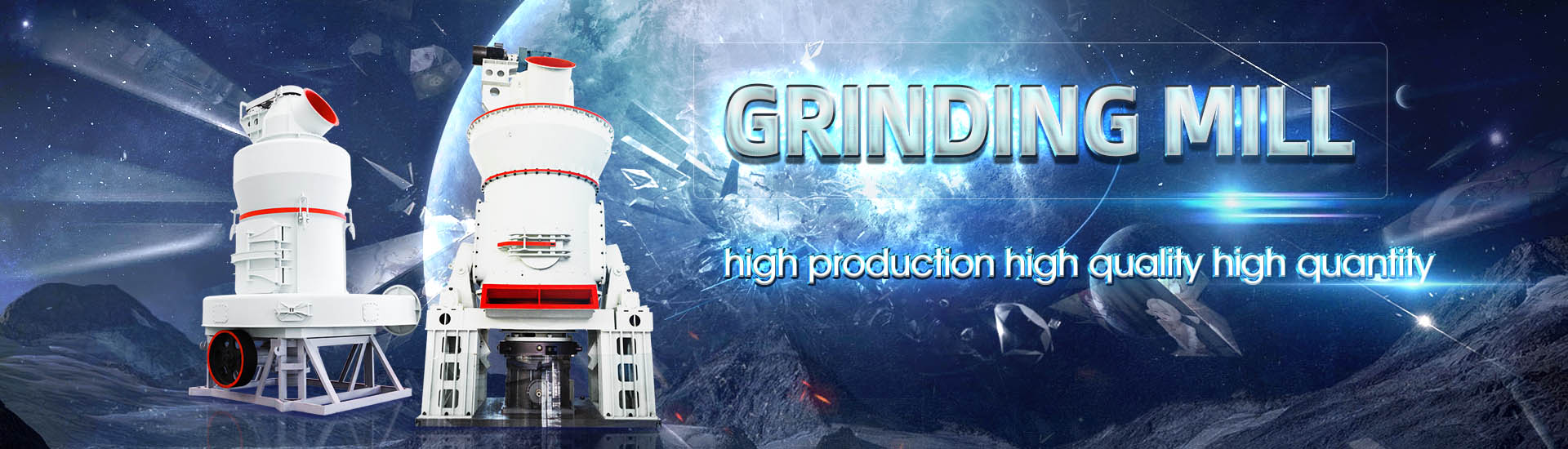
The grinding efficiency of the mill is high

Effect of different parameters on grinding efficiency
2016年11月22日 The grinding zone temperature elevation is dependent on the grinding efficiency and the proportion of grinding energy that enters the 2017年10月26日 The following are factors that have been investigated and applied in conventional ball milling in order to maximize grinding efficiency: a) Mill Geometry and Speed – Bond (1954) observed grinding efficiency to be a Factors Affecting Ball Mill Grinding Efficiency2018年1月1日 Specific energy consumption was determined as a function of material removal rate and compared to results of milling and turning processes The key influence factors on Energy efficiency of stateoftheart grinding processes2012年6月1日 maximize the grinding efficiency due to their high density and specific surface areaGrinding in Ball Mills: Modeling and Process Control ResearchGate
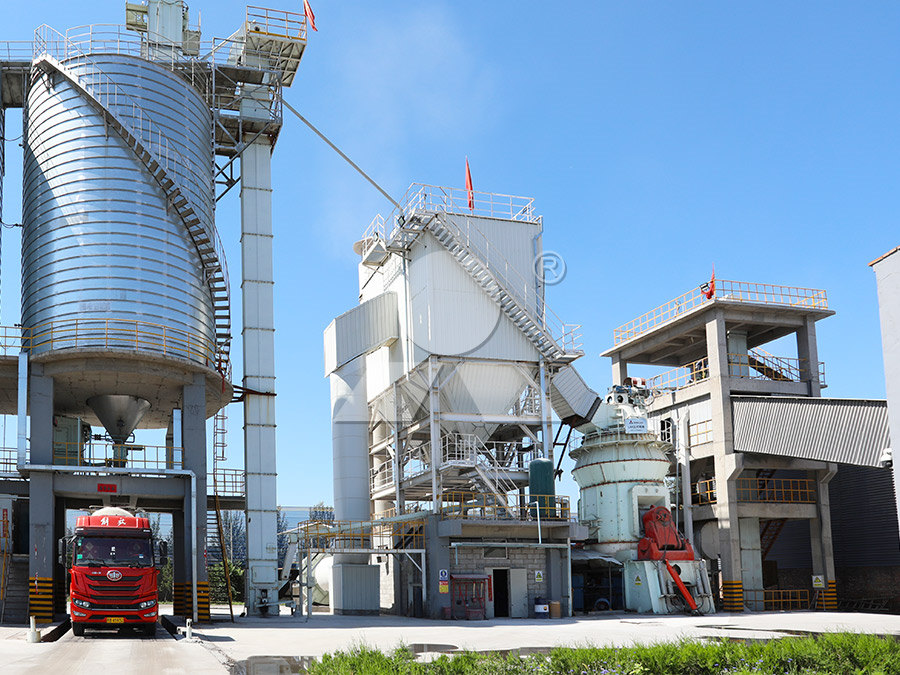
The Influence of the Grinding Media Diameter on
2024年6月14日 Therefore, optimizing the milling process, including correctly selecting grinding media, is essential to reduce energy consumption This article presents experimental studies of the grinding process of a model material 2022年1月1日 The results suggested that the highefficiency liberation of ore was obtained using the ceramicmedium stirred mill grinding technology, thus the efficient separation of iron and Highefficiency and energyconservation grinding technology 2018年9月29日 The article presents the results of laboratoryscale research on the determination of the impact of ball mill parameters and the feed directed to grinding on its Analysis of process of grinding efficiency in ball and rod mills with 2023年1月15日 In this paper, an innovative method for milling efficiency calculations based on the particle deformation process was proposed It depends on calculating the strain energy Novel methodology for mill efficiency determination based on
.jpg)
High efficiency ball mill grinding ResearchGate
2008年4月1日 Grinding efficiency can be increased by making some changes in operating practice, such as by using correct makeup media size, operating the mill in a charactering 2017年9月13日 Operating efficiency, based upon using operating work indices, is also a useful tool in comparing the variations in grinding mill operations such as: mill speed, mill size, size of grinding media, mill discharge arrangements, liner designs etcHow to Calculate Grinding Mill Operating Efficiency2023年4月23日 In order to increase the efficiency of the grinding mill, Stoimenov et al [38] suggested the increment of grinding media density Kelsall et al [17] investigated the influ ence of grinding media (PDF) Grinding Media in Ball MillsA Review2022年1月1日 A pilotscale grinding technology of ceramic medium stirred mill was proposed in this study Based on the specific productivity and grinding efficiency, the appropriate grinding parameters were ascertained as follows: material ball ratio of 07, ceramic ball medium size ratio (10 mm: 15 mm: 20 mm = 3:2:5), stirring speed of 110 rpm, grinding concentration of 50%, Highefficiency and energyconservation grinding technology using
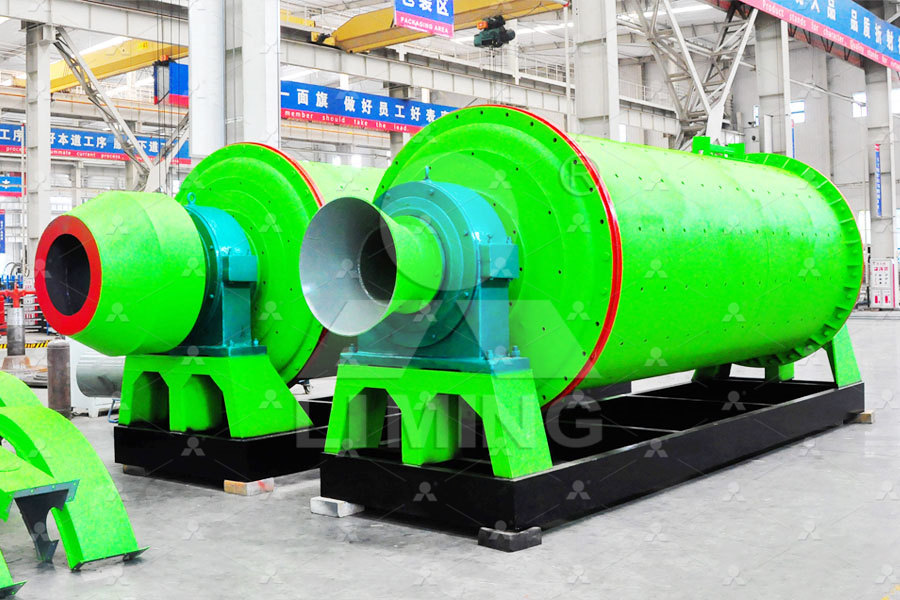
Four factors Affecting the Grinding Efficiency of Raymond Mill
There are mainly four factors that related to the grinding efficiency of Raymond mill which should be considered while using the mill Factor 1: The hardness of raw material The higher the hardness, the lower the output, the material with higher hardness will reduce the mill capacity, at the same time it will increase the wear of Raymond grinding parts2023年12月28日 In order to improve the grinding efficiency of the mill and reduce the phenomenon of overgrinding in the mill, the cycle load rate should be appropriately increased However, if the cycle load rate is increased very high, too much material will be in the mill, reducing the grinding efficiency 9 Add grinding aidsFactors Affect The Output and Quality of Ball Mills And How to 2023年11月1日 The ball mill on site, has problems such as uneven product particle size, low grinding efficiency, insufficient dissociation degree of useful mineral monomers, and high grinding energy consumption[[20], [21], [22], [33], [34]]The existing technological process of the first beneficiation workshop of Gongchangling Concentrator is as follows: two Energy conservation and consumption reduction in grinding 2020年3月21日 Ball mill's low grinding efficiency, low processing capacity, high production energy consumption, unstable product fineness, etc are problems that many customers will encounter How to effectively improve the grinding efficiency of the ball mill is an important issue Now, let's share 10 ways to improve the grinding efficiency of the ball mill!Top 10 tips to improve the grinding efficiency of ball mill
%3C1PGHL[2}HK_]YT.jpg)
Enhancing the Grinding Efficiency of a Magnetite SecondStage Mill
2024年1月31日 Ceramic ball milling has demonstrated remarkable energysaving efficiency in industrial applications However, there is a pressing need to enhance the grinding efficiency for coarse particles This paper introduces a novel method of combining media primarily using ceramic balls supplemented with an appropriate proportion of steel balls Three grinding media Classifying efficiency plays an important role in grinding efficiency High classifying efficiency means that those qualified grains can be discharged timely and efficiently, while low classifying efficiency means that most qualified grains are not discharged and sent to the ball mill for regrinding, which is easy to cause overgrinding and 10 Ways to Improve the Grinding Efficiency of Your Ball MillThe ball mill comminution process has a high electrical energy consumption, especially when those systems are in combination with first or secondgeneration classifiers It is also important to evaluate the grinding efficiency and ball charge efficiency for a Figure 5: first chamber grinding process evaluation Figure 4: BALL MILLS Ball mill optimisation Holzinger ConsultingHighenergy vibration ball mill is a small desktop laboratory grinding instrument It uses 1700r/min highfrequency threedimensional vibration to make the sample achieve the result of grinding or mixingMaximizing Grinding Efficiency: The Power of
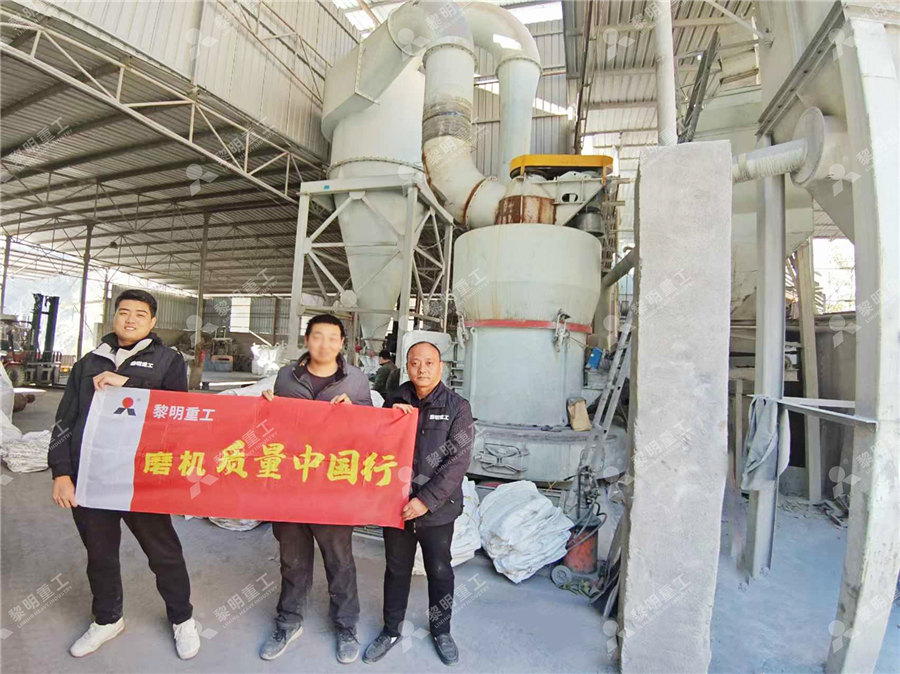
Experimental Study on the Influence of Rotational Speed on Grinding
6 天之前 There is an intersection point between grinding efficiency and energy consumption in Figure 9, which is the critical speed selection point, and the corresponding agitator speed is around 260 rpm If the speed is lower than this, the energy consumption of the mill is relatively small and the grinding efficiency is high2023年1月13日 The influence of materials on the grinding efficiency of ball mill is mainly reflected Thick slurry should be used for coarse ore feed and for handling hard and high specific gravity ores, and Three Major Factors Affecting the Grinding Efficiency of Ball Mill2012年12月1日 In this paper, The Copperbearing minerals Powder (≤2mm) in Dahongshan is used in conical ball grinding, the experimental study shows that the effect of ball material ratio on the grinding efficiency is obvious The critical value and the optimal value range of the ball material ratio are different on different grinding stages, the feasible ball material ratio of coarse Effect of Ball Material Ratio on the Grinding Efficiency of Copper 2021年8月31日 Ball Mill in Nigeria Grinding efficiency refers to the amount of ore processed for every 1kWh of electricity consumed It has the following representation methods: The raw ore Gongyi Forui Machinery Factory is a highquality enterprise specializing in the production of beneficiation equipment Over the years, Grinding Efficiency Henan Forui Machinery Technology Co, Ltd
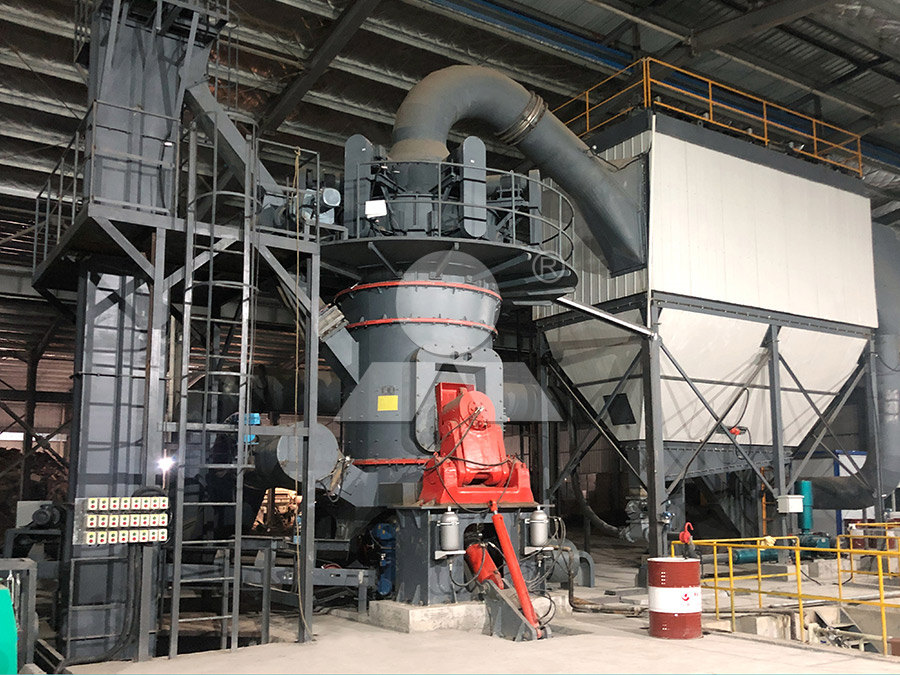
How to Measure Grinding Efficiency 911Metallurgist
2018年4月20日 The first two Grinding Efficiency Measurement examples are given to show how to calculate Wio and Wioc for single stage ball mills Figure 1 The first example is a comparison of two parallel mills from a daily operating report Mill The relative ‘efficiency’ of horizontal grinding mills compared to other comminution equipment is often debated, and efforts to improve the energy efficiency of these mills is an ongoing area of attention for process engineers The discharge arrangement design affects the material transport characteristics within a horizontal grinding millAchievement of High Energy Efficiency in Grinding Mills at 2015年10月23日 In this chapter an introduction of widely applied energyefficient grinding technologies in cement grinding and description of the operating principles of the related equipments and comparisons over each other in terms of grinding efficiency, specific energy consumption, production capacity and cement quality are given A case study performed on a EnergyEfficient Technologies in Cement Grinding IntechOpen2022年1月1日 The size of grinding media is the primary factor that affects the overall milling efficiency of a ball mill (eg power consumption and particle size breakage)Effect of grinding media on the milling efficiency of a ball mill
.jpg)
Effect of ball and feed particle size distribution on the milling
Effect of ball and feed particle size distribution on the milling efficiency of a ball mill: An attainable region approach N Hlabangana a, G Danha b, *, E Muzenda b a Department of Chemical Engineering, National University of Science and Technology, P O Box AC 939, Ascot Bulawayo, Zimbabwe b Department of Chemical, Materials and Metallurgical Engineering, College of 2024年2月29日 Sample Concentration at the Sampling Point As can be seen from Table 2, one section of grinding ball mill, that is, the moisture of the crushing final product is about 6%; the discharge concentration of 1# ball mill is 712%, in the normal range; the discharge concentration of 2# ball mill is 685%; and the discharge concentration of 3# ball mill is 691%, which Study on the Optimization of Grinding Efficiency in Gold Mine Combining impact and shearing actions enhances mill efficiency Proper selection of media milling equipment is vital for success in all three areas There are many different types of grinding mills (Table 1) Some devices, such as ball mills, Solids Choose the Right Grinding Mill Chemical 2022年4月19日 8 Improve classification efficiency The influence of classification efficiency on grinding efficiency is selfevident High classification efficiency means that qualified particles can be discharged in a timely and efficient manner, while low classification efficiency means that most of the qualified particles are not discharged and are returned to the mill for regrinding, which is 10 tips to improve the grinding efficiency of ball mill
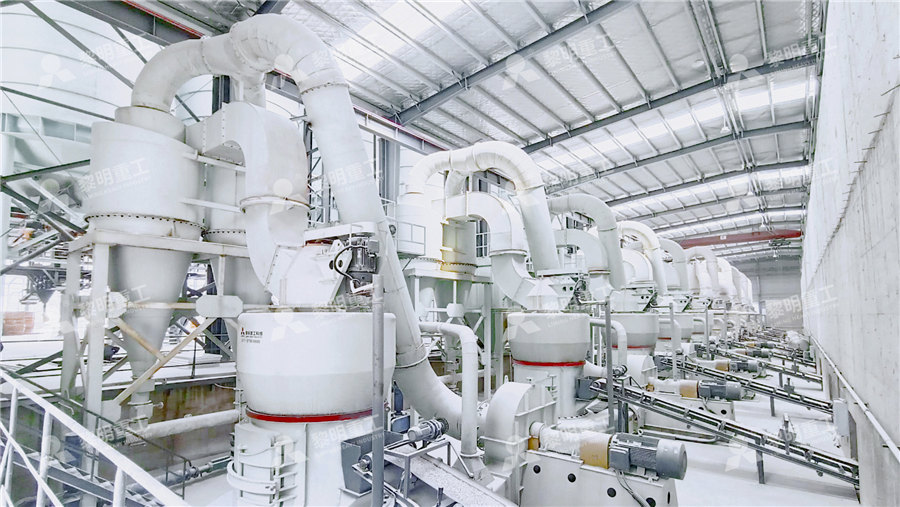
Effect of Moisture Content on the Grinding Process and Powder
2018年6月1日 The grinding process by friction at the microscale in a mill with stones is considered a variable combination of contacts: with twobody (the asperities of lower millstone in direct contact with Classification operation is carried out by high efficiency dynamic air classifiers inside the vertical roller mill shell Also, vertical roller mills combine drying, grinding andPerformance Evaluation of Vertical Roller Mill in Cement Grinding2021年4月1日 Owing to their high energy efficiency, stirred mills are commonly used in the fine or ultrafine grinding of lowgrade and fine disseminated ores to enhance liberation In this study, batch wet grinding studies were conducted in a stirred mill to evaluate the effect of the grinding media density, grinding media diameter, and stirrer tip speed on the ground products and Effect of grinding media properties and stirrer tip speed on the Table 2: Mill Comparison of Media Size, Power Intensity, number of grinding media The ability to use smaller media is probably the dominant impact on grinding efficiency It dramatically increases the grinding surface area and the number of grinding “events”, essential to efficiently grind fine particlesFine Grinding as Enabling Technology – The IsaMill
.jpg)
Energy efficiency of stateoftheart grinding processes
2018年1月1日 It enables a combination of high speed grinding and creepfeed grinding, typically referred to as high performance grinding [17] Especially when employed on highperformance alloys using high cutting velocities, the high costs of CBN are compensated by increased productivity and tool life compared to other abrasives [18]2023年7月20日 The grinding products of the former are directly processed in the next processing procedure without returning to the grinding mill After the grinding products of the rod mill – its efficiency is relatively high with the feeding particle size less than 30 mm and the product particle size around 3 mm, and the produced product Ore Grinding SpringerLink2020年1月11日 Working site of ball mill grinding media refilling In addition to the grinding media proportion and frequency, other factors such as the grinding media material, the shape and so on can improve the ball mill efficiency Consult a professional engineer for details The optimized grinding media can improve the ball mill efficiency by about 30%5 Ways to Improve the Ball Mill Efficiency FTMStudying the effect of different operation parameters on the grinding energy efficiency in laboratory stirred mill 30] Because of the high energy revealing in stirred mills for per unit volume and time, the energy consumptions is lower than that of the conventional tumbling mills The grinding efficiency is low for the particles Studying the effect of different operation parameters on the grinding
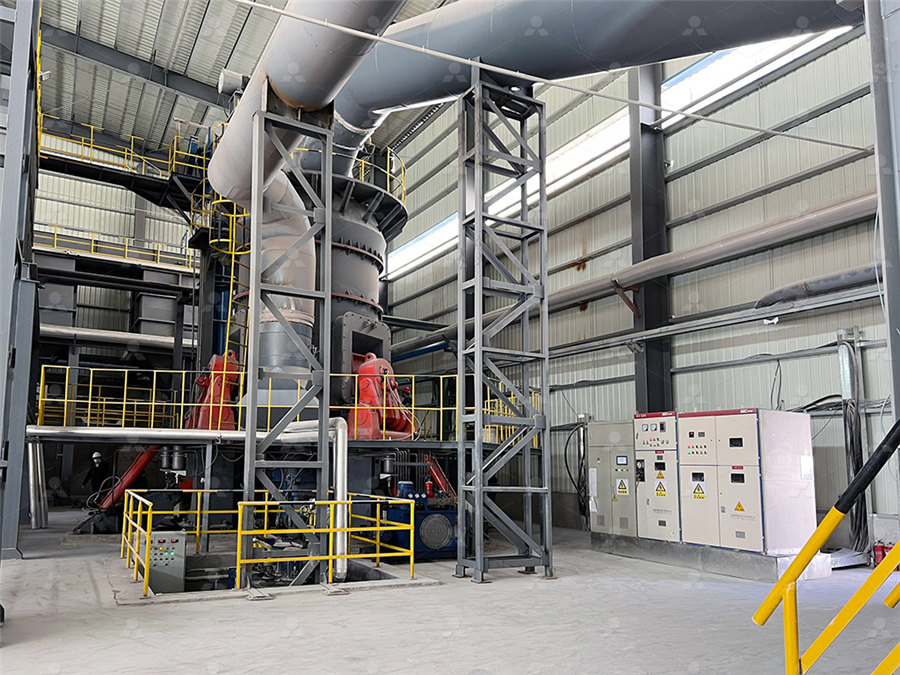
Ten Ways to Improve the Grinding Efficiency of Your
2019年4月22日 There are a lot of problems that most mineral processing plant meet when operating the ball mill, such as low grinding efficiency, low processing capacity, high energy consumption, unstable 2024年4月1日 The primary objective of this research is to examine the impact of various stirrer designs in different mill orientations on the efficiency of calcite grinding in a dry stirred mill In the context of the research, a series of batch grinding experiments were performed using a laboratoryscale stirred mill that could be oriented vertically or horizontallyThe impact of different stirrer designs and mill orientations on the 2008年4月1日 High efficiency ball mill grinding April 2008; Engineering and Mining Journal 209(3):62+ Authors: C Arentzen C Arentzen This person is not on ResearchGate, or hasn't claimed this research yetHigh efficiency ball mill grinding ResearchGate2022年3月29日 The increase in the grinding efficiency in the mill No 8 was achieved due to the presence of a large number of grinding media in the loading that have retained the ball shape This is the result of the fact that grinding media with high and evenly distributed hardness over volume retain their ball shape longer when wornEfficiency of the Use of HighQuality Grinding Balls from Chrome
.jpg)
Evaluating the performance of an industrialscale high pressure
2023年1月1日 To meet both energy efficiency and liberation requirements, one approach is to “crush more and grind less B, Nadolski, S, Bamber, A, 2011 A Pilotscale examination of a high pressure grinding roll/stirred mill comminution circuit In: Autogenous and Semiautogenous Grinding Technology Conference, Vancouver Google Scholar2024年7月17日 A steam jet mill (SJM), which employs industrial waste heat steam as a gas source, is a widely utilized apparatus for the pulverization of fly ash To achieve elevated singlemachine grinding capacity, efficiency improvement research based on structural optimization should be conducted In this study, numerical simulations and industrial experiments are Effect of Nozzle Quantity on the Flow Field Characteristics and % 98824 0489 0388 0100 0065 0052 0022 0025 0020 0015 Grinding tests were carried out in a dry stirred ball mill both vertical and horizontal orientations with varyingThe Effect of Stirred Mill Orientation on Calcite GrindingOne of the new grinding devices is an electromagnetic mill, which, due to its grinding capabilities has a high potential for efficient comminution of raw materials at low energy costs An important issue in application of electromagnetic mill is determination of the feed parameters which determines the efficiency of the mill’s operation [4]Analysis of a grinding efficiency in the electromagnetic mill for
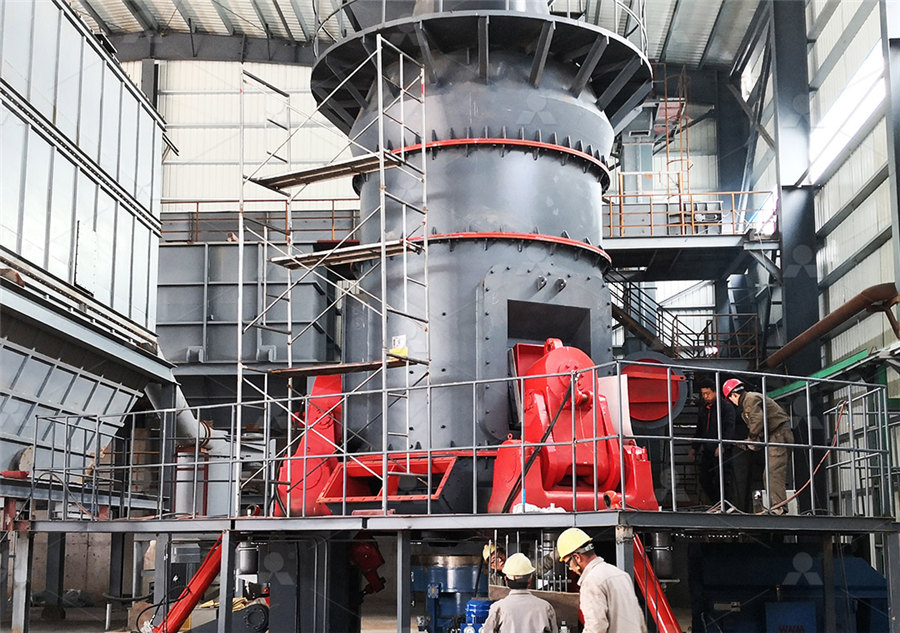
Efficiency Enhancement in Hammer Mills through Biomimetic
2024年6月3日 Hammer mill is widely used in the feed processing industry During its operation, the material is thrown against the inner wall of the sieve after being broken by the hammer Limited by the annular structure sieve, the grinded material tends to produce a “air material circulation layer” on the inner wall of the sieve, leading to problems such as low grinding