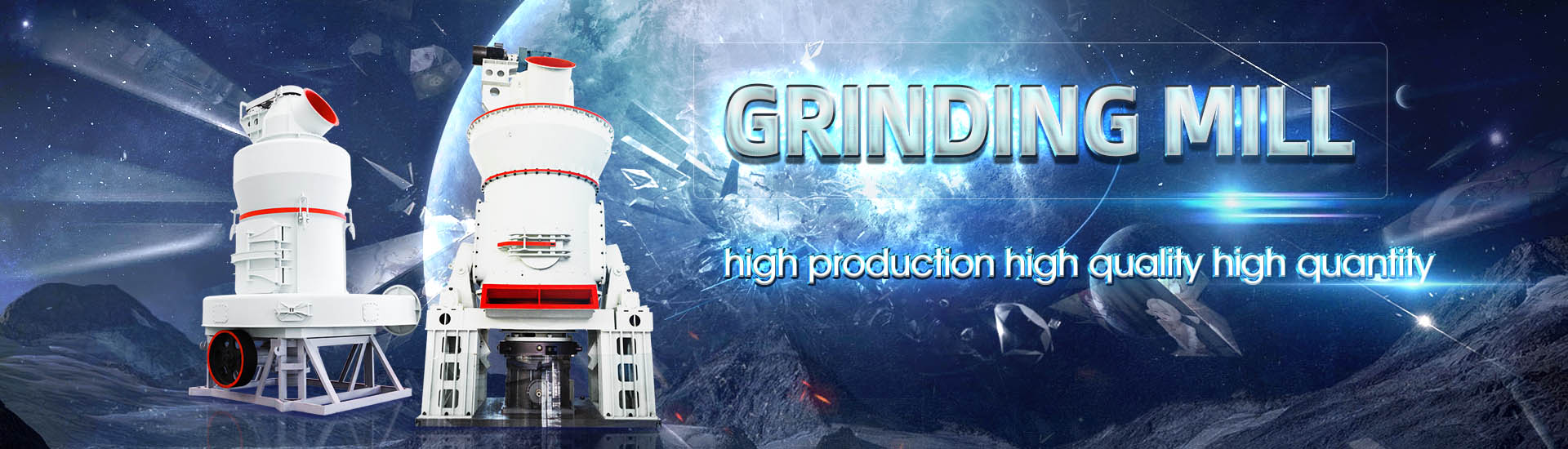
Some common problems in cement production process
制粉项目-2023.11.17.jpg)
Solving Cement's Massive Carbon Problem Scientific
2023年2月1日 Replacing fossil fuels with renewable energy sources and raising efficiency across production could reduce the carbon footprint by up to 40 percent Using different raw materials for clinker2024年6月1日 Decarbonising cement and concrete production face several challenges and barriers that hinder the transition to lowcarbon practices Technological challenges and Decarbonising cement and concrete production: Strategies, Cement plants aggravate the critical challenges of anthropogenic environmental pollution, global warming, climate change, and excessive fossil fuel use by emitting 15% of global Impacts of Cement Production on the Environment with Practical 2010年10月23日 Cement production releases 5–6% of all carbon dioxide generated by human activities, accounting for about 4% of global warming It can release huge amounts of Cement industry: sustainability, challenges and perspectives
CFB石灰石脱硫剂制备64.jpg)
Environmental Impacts of Cement Production: A
2020年11月19日 In the literature, several studies assessed the impacts of cement production considering its upstream processes (ie, production of commodities, raw materials, transport to the factory plant, production process) 2022年1月17日 NOx, SOx, CO, CO2, H2S, VOCs, dioxins, furans, and particulate matter are all common air pollutants from cement manufacturing Other sources of dust particles include A systematic review on the impact of cement industries on the 2020年9月22日 In addition to CO 2 and other greenhouse gas (GHG) emissions 16, dust, particulate matter 17 and mercury 18 are also associated with cement and concrete Environmental impacts and decarbonization strategies in the weighting 50 kg each Most cement is used in concrete as an essential material in the construction industry [38, 40] There are two types of processes used in cement production: the dry process and the wet process [38] • Dry process: In this process, the raw materials are dried using different types of dryers or air separators,Impacts of Cement Production on the Environment with Practical
.jpg)
Cement Production Demystified: StepbyStep Process and
The use of fossil fuels such as coal, natural gas, and oil is common in cement production, both as a fuel for the kiln and as a source of heat for other parts of the process which leads to CO2 emitted by combustionHowever chemical reactions happening in the kiln (calcination) are also responsible for up to 60% of the total of emissions of the cement production process [PCA]2020年1月1日 About half of the emissions are caused by process emissions during the clinker manufacture, 40% by the combustion of fuels to heat the cement kiln, and 10% by power consumption and transportation Assessment on Cement Production Practice and 2021年3月1日 This paper reviews the impact of cement industry towards the global environment and solutions to the problem The increasing harvesting of raw materials for mounting cement manufacturing causes Environmental impact of cement production and Solutions: A Understanding the role of the kiln in cement production is pivotal to grasping the entire manufacturing process of Portland cement Contrary to common belief, the kiln is not merely a large furnace but a sophisticated piece of equipment that plays a critical role in transforming raw materials into clinker, the precursor to cementWhat is the Manufacturing Process of Portland Cement?
.jpg)
Common Well Cementing Problems and Solutions
Pegasus Verte Inc Common Well Cementing Problems and Solutions 3 I Abstract Throughout the well’s life cycle, cement serves as the foundation There are several issues associated with well cementing that can impede the well construction process, reduce well production, and be costly to resolve2024年6月1日 The cement industry plays a critical role in global carbon emissions, primarily due to the release of CO 2 during the production of cement The process of cement production involves the transformation of raw materials, such as limestone and clay, into clinker, which is a powdered form of cementDecarbonising cement and concrete production: Strategies, 2010年6月1日 Cement is manufactured in the following way: a fuel is burned to provide heat for the process of converting CaCO 3 to CaO, generating CO 2 [32]Developing an optimization model for CO2 reduction in cement production Workers transport the crushed raw materials to the cement plant, with the process varying significantly based on the proximity of the quarry to the manufacturing site Common methods of transportation include conveyor belts, trucks, and, in some cases, railways For plants near water bodies, workers might also transport materials via bargesStepbyStep Guide to the Manufacturing of Cement PRACTICAL
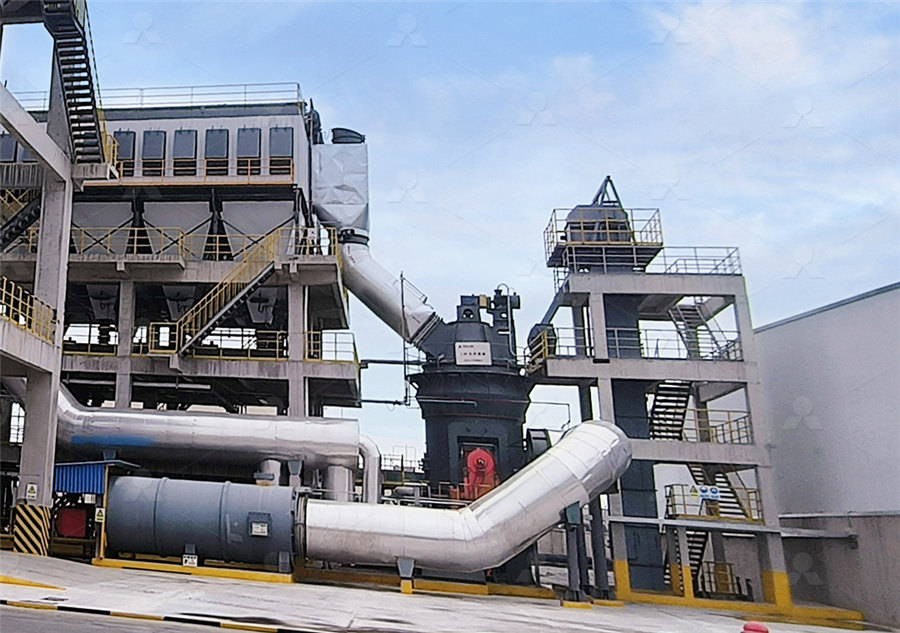
Cement Manufacturing Process and Its Environmental Impact
2023年7月10日 Cement manufacturing is a significant industrial activity that plays a vital role in the construction sector However, the process of cement production is associated with various environmental 2021年10月14日 The cement industry has excelled in areas which are within its control However, the constraints and limitations of the three main infrastructure support needed, which are mainly in the public sector and under the domain of The prospects and challenges of the Indian cement 2022年6月23日 Cement is one of the key essentials in the construction sector and forms the backbone of a nation’s economy The total world cement production is around 41 billion tonnes in 2019, with India being the secondlargest cement producer after China [1, 2]The current annual production of the Indian cement industry is 33448 million tonnes as of March 2020 [3, 4]Recent Progress in Refuse Derived Fuel (RDF) Coprocessing in Cement 2023年12月1日 This review paper explores the diverse range of cement additives and their significant impact on the properties of cementitious materials Cement additives play a crucial role in enhancing various (PDF) Advancements in Cement Technology: A
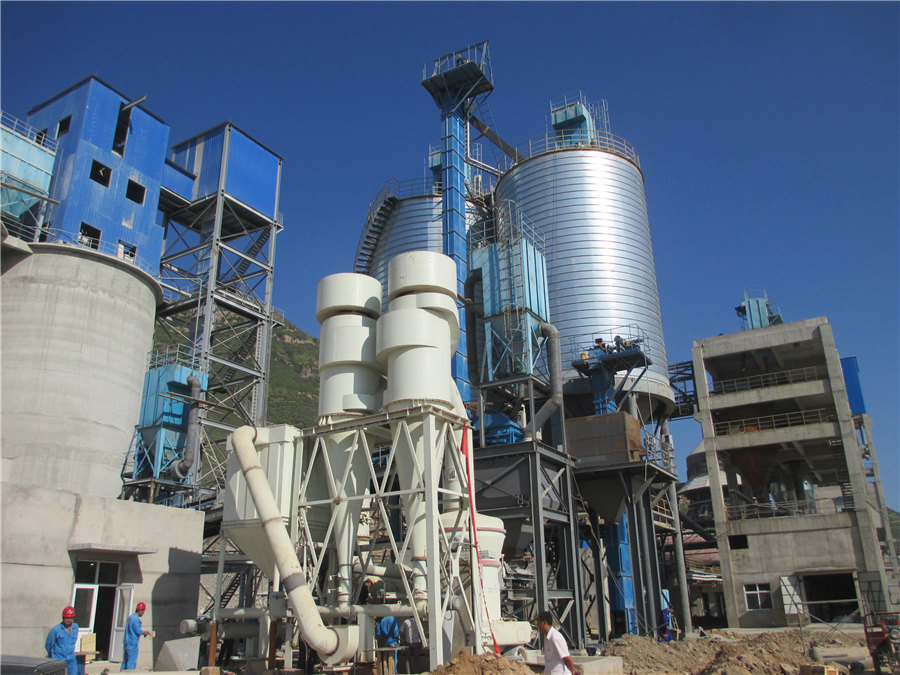
9 Environmental Impacts of Cement Production Environment Go!
Environmental Impacts of Cement Production Between 4 and 8% of the world’s total CO2 emissions come from concrete, which has a complicated environmental impact that is influenced by its manufacture, applications, and direct effects on infrastructure and buildingsCement, which has its own environmental and social effects in addition to substantially influencing those of 2022年1月1日 Studies have shown cement production releases roughly 08 tonnes of CO 2 per tonne of cement to the atmosphere [19] In the meantime, it is reported that a tonne of Portland cement production produces around a tonne of CO 2 greenhouse gas emissions and about 2% to 8% of global power consumption is due to the cement manufacturing process [20], [21]Environmental impact of cement production and Solutions: A The finer the grind, the more reactive is the finished cement Rapidsetting cements have smaller particle size than the less reactive low heat of hydration cements Cement is more reactive than clinker and can absorb moisture from the environment leading to some degree of prehydrationThe Cement Production ProcessPDF On Apr 22, 2018, Zeyad Hassan published Common Drilling well problems (Reasons, indications, mitigation and prevention) Find, read and cite all the research you need on ResearchGateCommon Drilling well problems (Reasons, indications, mitigation
.jpg)
Manufacture of Cement Materials and Manufacturing Process of
Cost of production: High: Low: Overall cost: Costly: Cheaper: Physical state: Raw mix (solid) Slurry (liquid) 2 Burning of Raw Materials Manufacture Process of Cement The manufacture procedures of Portland cement is described below Mixing of raw material; Burning; Grinding; Storage and packaging; 1The cement production process 1 The Quarry: The cement production process begins with the extraction of limestone and clay from the quarry 2 Crusher and PreBlending: The material is then crushed to reduce particle sizes and blended to reduce variability in composition 3 Raw Mill and Kiln: Raw materials and additives areA practical guide to improving cement manufacturing processes Stage of Cement Manufacture There are six main stages of the cement manufacturing process Stage 1: Raw Material Extraction/Quarry The raw cement ingredients needed for cement production are limestone (calcium), sand and clay (silicon, aluminum, iron), shale, fly ash, mill scale, and bauxite The ore rocks are quarried and crushed into smaller pieces of about 6 inchesHow Cement is Made Cement Manufacturing Process2020年10月30日 The reason for this is the serious difference in the cement manufacturing process compared to other common production processes Figure 2 Clinker bed in a petcoke and coalfired rotary kiln – a unique, complex Highlevel control in cement production World

Process of cement production in Nepal International Centre for
DMG 2008) The production capacity installed in two stateowned minebased industries and about 20 private clinkerbased factories are above 961, 000 MT, and the consumption of cement is about 102 Bulletin of the Department of Geology, Tribhuvan University, Kathmandu, Nepal, Vol 11, 2008, pp 71–78 Process of cement production in Nepal2021年11月1日 Despite the fact that there are several laws and regulations in place to oversee the cementproducing industries, environmental problems nevertheless still continue to persist [5]An Overview of EcoFriendly Alternatives as the 2011年8月9日 Cement production is an energyintensive process consuming thermal energy of the order of 33 GJ/tonne of clinker produced, which accounts for 30 – 40 percent of production costs (Giddings et al, 2000; EC, 2001)Alternative Fuels in Cement Manufacturing IntechOpen2020年9月14日 From there the clinker is conveyed to ball mills or roller presses, in which it is ground down to very fine cement, with the addition of gypsum and anhydrite, as well as other additives, depending on the use to which the cement is to be put Step #6 The finished cement is stored in separate silos, depending on type and strength classThe essentials of electrical systems in cement plants EEP
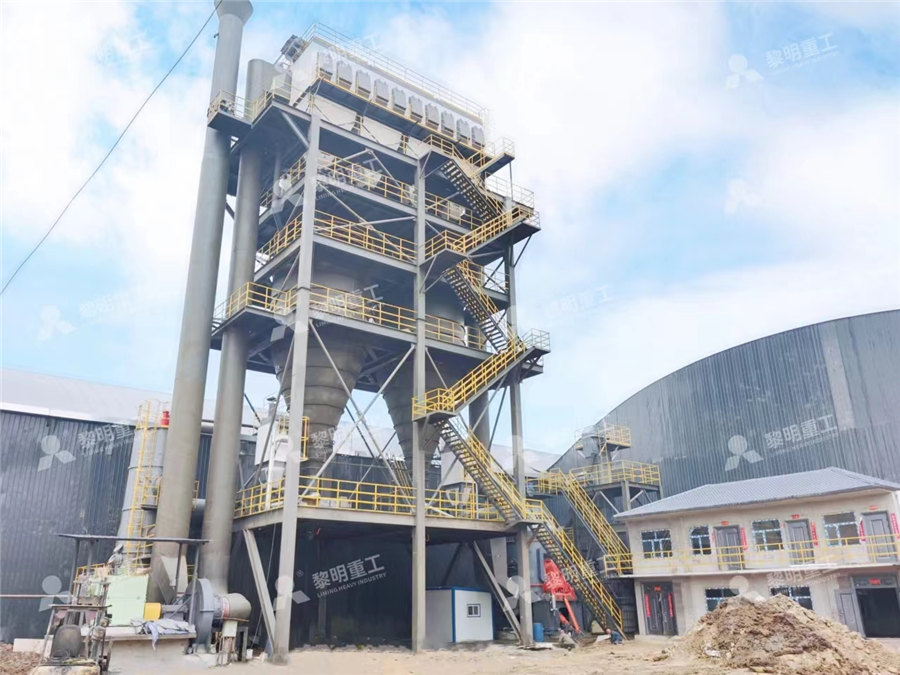
Cement and Clinker Production by Indirect Mechanosynthesis Process
2022年9月21日 Global cement production has reached 39 billion tons However, the clinkerization process, which is the basis of cement production, is responsible for an approximate annual global CO2 emission of can extend fossil fuel supplies and help resolve air pollution problems associated with the use of conventional fuels This chapter reviews in detail some of the main alternative fuels used in cement production It focuses on types of alternative fuels used, the environmental and socioeconomic benefitsAlternative Fuels in Cement Manufacturing IntechOpen2021年3月1日 This paper proposes an integrated approach where CO2 captured from cement plant will be utilized within the plant for producing nano calcium carbonate (CaCO 3) for use in cement manufacturing process(PDF) Environmental sustainability in cement industry: An Cement Silo Common Issue: Coating in cement Silo It happens due to storage of cement in silos at high temperature (>70 oC), and improper water spray system in cement mill Strategy to fix the issue: Use cement coolers if cement temperature is higher than specified Do not store cement for long time in mon Problems in Cement Plant
.jpg)
Cement Manufacturing Process INFINITY FOR CEMENT EQUIPMENT
Cement Manufacturing Process by TIZITA MOGES , SELAMU ABULE DEREJE ENDALAMAW IF YOU NEED THIS GUIDE AND ALL OTHER USEFUL EXCEL SHEETS WHICH WILL MAKE YOU MASTER THE PRODUCTION , PROCESS , Table 4, some of the problem their remedies in homogenizing silo Problem: Remedies: 12023年9月5日 Process control instrumentation is a complex system of sensors, transmitters, controllers, and other devices designed to measure and control physical quantities such as temperature, pressure, flow, and level in an Mastering Process Control Instrumentation in Cement Global cement production has reached 39 billion tons However, the clinkerization process, which is the basis of cement production, is responsible for an approximate annual global CO2 emission of 2 billion tons As part of Cement and Clinker Production by Indirect Approaches to cutting GHG emissions from the energy used in the cement production process include: Eliminating carbon emissions from limestone calcination during clinker production is more complicated Currently used approaches include: Based on the currently available and economically feasible technologies, carbon emissionsAND CEMENT PRODUCTION
.jpg)
China’s provincial process CO2 emissions from cement production
2022年4月12日 Carbon dioxide (CO2) emissions from China’s cement production process have increased rapidly in recent decades, comprising the secondlargest source of CO2 emissions in the country, next only to 2023年12月11日 Global cement emission patterns Global emissions from cement production reached 2059 Mt CO 2 in 2018, where energy and processrelated emissions account for 34% and 66% respectively Developed Projecting future carbon emissions from cement production in 2024年9月10日 Longer Production Time: The wet process generally takes longer for Cement production compared to the dry process, as it involves additional steps such as slurry formation and drying Conclusion This marks an end to the discussion on the wet and dry processes of Cement manufacture and has also enumerated on the major points of difference between dry Cement Manufacturing Process: Know Extraction, Processing 2021年3月3日 Cement is produced by a hightemperature (about 1500 °C) reaction in a rotary kiln of carefully proportioned and blended ratios of lime (CaO), silica (SiO 2), alumina (Al 2 O 3), and iron oxide (Fe 2 O 3)The production of cement is a chemical process requiring an accurate blend of the previously cited four key organic oxides and the limitation of several undesirable Cement SpringerLink
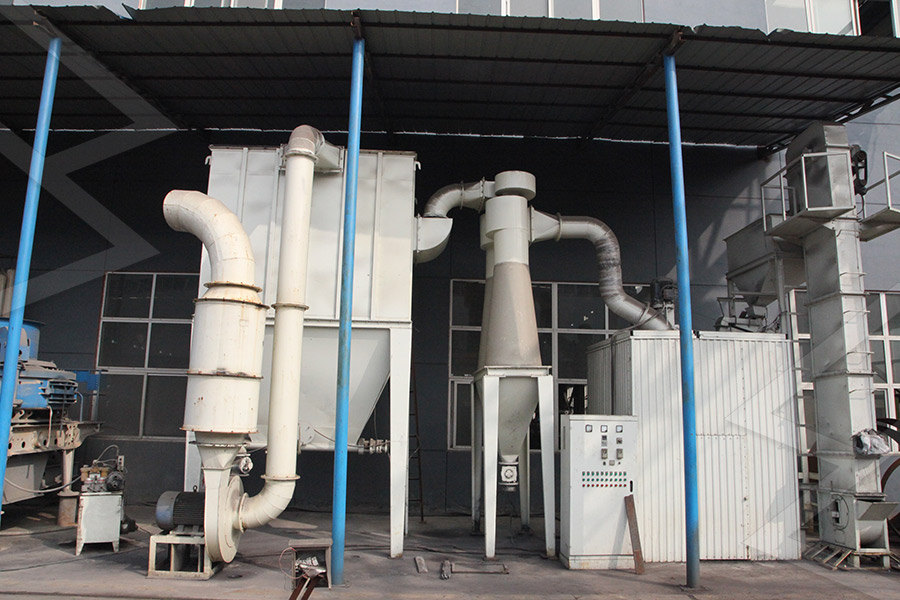
Cement Energy Environment
Cement manufacturing is a high energy intensive process and fuel consumed accounts for almost 3040% cost of production of cement To meet this energy requirement, the industry has mostly depended on fossil fuels like coal, petroleum, and natural gases since the beginning of cement production But due toPackaging is the most polluting process (in terms of dust) in cement production (Cumbane 2011) Nitrogen oxide (NOX) emissions are emitted from the high temperature combustion process of the cement kiln Carbon dioxide defined as greenhouse gas is mainly associated with fuel combustion and with the decarbonation of limestone (IFC 2007)OCCUPATIONAL HEALTH AND SAFETY IN CEMENT INDUSTRY2020年9月5日 (11) Brief history and today’s AM technology for infrastructure materials Historically, the very first application of AM for infrastructure materials can be attributed to the production of asbestos cement in the 1890’s with the development of the Hatschek method 29In this technology, which remains to date the most common processing method employed to Cements in the 21st Century: Challenges, Perspectives, and