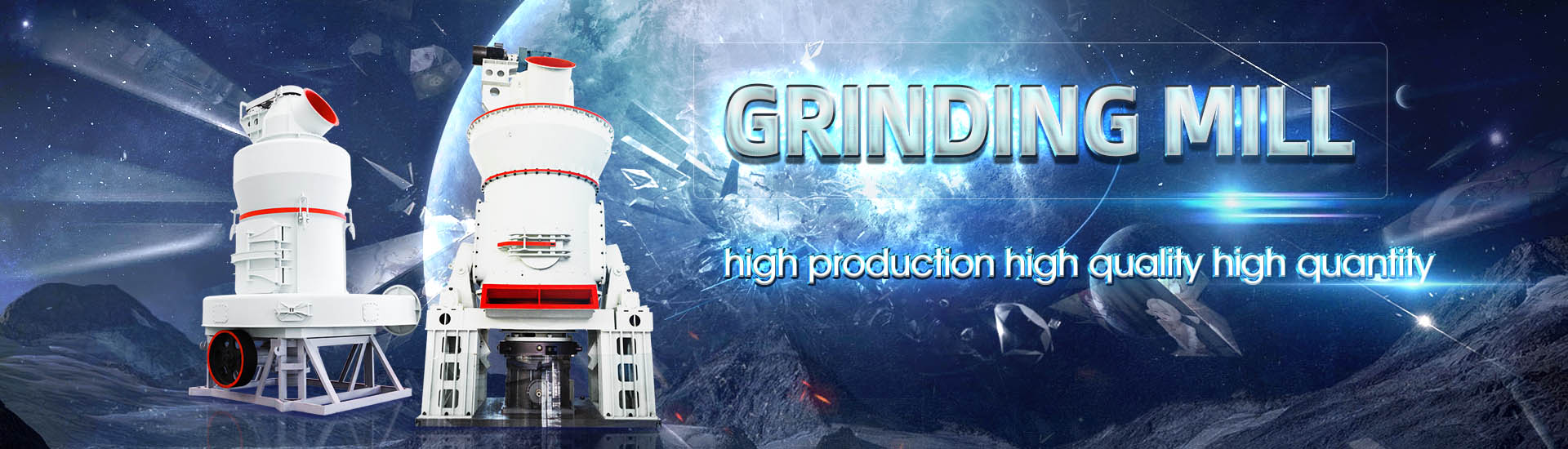
cement grinding enterprise quality management rules
.jpg)
Energy and cement quality optimization of a cement grinding circuit
2018年7月1日 This study aimed at improving both the energy efficiency and product quality of the end product for a given cement grinding circuit by applying an accurate sampling Grinding Optimization OptimizeIT Expert Optimizer benefits the cement mill operations in four ways: • More consistent quality (grade) The continual monitoring of the mill loading and the Industrial : Optimization for the Cement Industry ABBOptimization addresses the grinding process, maintenance and product quality The objective is to achieve a more efficient operation and increase the production rate as well as improve the run OPTIMIZATION OF CEMENT GRINDING OPERATION IN BALL MILLSNote for Cement Grinding and Cement Blending Plants: The client must provide CSC systemconform evidence that the clinker/cement suppliers meet the conditions set forth in P101 Concrete Sustainability Council
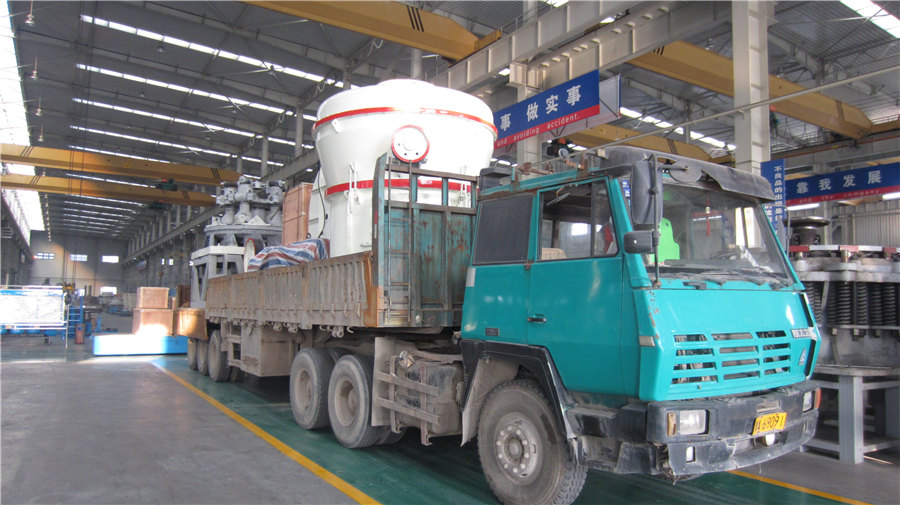
BALL MILLS Ball mill optimisation Holzinger Consulting
As grinding accounts for a sizeable share in a cement plant’s power consumption, optimisation of grinding equipment such as ball mills can provide significant cost and CO 2Cement grinding stations: Cement production in cement grinding plants is performed by cogrinding clinker and gypsum in dedicated mills (eg ball mills, vertical roller mills), and by Concrete Sustainability Councilraw materials, burning, grinding and quality control are supported by a range of chapters addressing critial topics such as maintenance and plant reporting, alongside a detailed The Cement Plant Operations Handbook International Cement All plants must have appropriate quality control systems in place to monitor and control the characteristics of raw materials and fuels In order to prevent critical environmental impacts, it Cement Environmental Directive Holcim
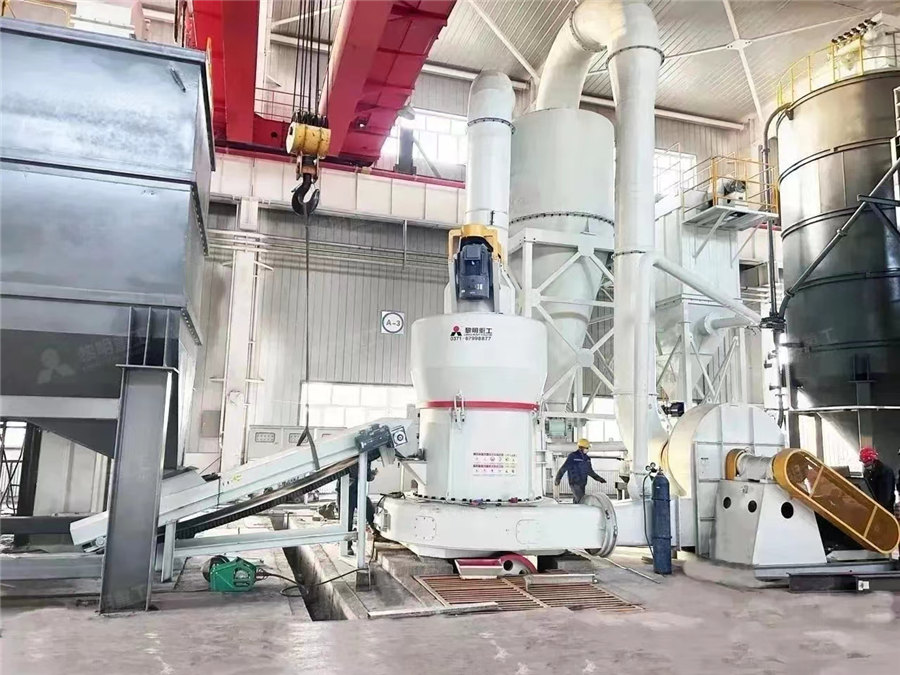
Case 1‐428‐925 November 2009 Madras Cements Ltd: to a Visible
brand enjoyed a strong recognition in southern India and was strongly associated with quality The company manufactured cement at five cement plants and two grinding plants in southern India (Exhibit 2 lists the manufacturing facilities of Madras Cements) Demand for cement is closely related to overall growth in the economy and particularly Enterprise Risk Eliminate Withdraw Approach Based Risk Management in Cement Industry Khaled M S Gad El Mola Assistant Professor, Mechanical Engineering Department, Industrial Engineering Program, Faculty of Engineering at Helwan, Helwan University, Helwan, Cairo, Egypt Email: kmsoli01@yahoo controlEnterprise Risk Eliminate Withdraw Approach Based Risk Management Condition in one of the grinding chambers of the mill Results of Optimization The graphical analysis presented in Figure 2 represents progress of grinding along the length of the mill after optimizing the grinding process rogress of grinding is clearly visible in Desired p the graphs Figure 2: Analysis of longitudinal samplesOPTIMIZATION OF CEMENT GRINDING OPERATION IN BALL MILLSThe addition of grinding aids and refined process strategies can improve the performance of vertical roller mills (VRM) The use of suitable grinding additives combined with effective management of total moisture in the mill circuit will significantly contribute to a better VRM operation and ultimately, to an improved final cement qualityGRINDING ADDITIVES VRM optimisation
.jpg)
Extended automation Integrated solutions for cement industries
Improve your cement production with collaborative production management Increase efficiency, reduce costs and document your performance Collaborative Production Management (CPM) solutions integrate manufacturing systems – providing visibility, execution, tracking, reporting and optimization of cement industriesWhen incorporated into an Industrial Information Technology architecture, full integration can comprise enterprisewide knowledge management for process, production, and maintenance management Accordingly, the cementspecific LIMS addresses two key areas in daily laboratory management: information management and laboratory task managementEverything you need to know about Automation and Optimization Dalmia Cement is a leading cement Dr Rajan is a PhD from IIT Delhi, in the area of Leadership, a postgraduate in business management from XLRI, Jamshedpur and an Bengal Cement Works (06 MnT) and at Belgaum Cement (09 MnT) Commissioning of a new Grinding Unit Meenakshi Cement Works at Tamil Nadu with 2 MnT Made a tectonic shift in About Us Dalmia Cement22 Environmental Management Systems (EMS) All plants must have an environmental management system in place to ensure that all environmental impacts and risks are effectively managed and mitigated Integrated cement plants (incl quarries and related captive power plants), grinding stations and AFR preCement Environmental Directive Holcim
.jpg)
Towards Sustainability: Slag Grinding Circuits Indian Cement
2022年2月1日 A detailed explanation of the joint approach of JSW Cement and the KHD Group helps in a better understanding on the acceptance of roller press in slag grinding and finish grinding and why it is well recognised throughout the cement industry JSW Cement has a strong commitment towards innovation in sustainability and technology to offer []2020年2月1日 They showed that the polymerbased grinding aid increases the specific surface, prevents agglomeration and ball coatings, and improves the roundness, fineness and fluidity of the ground cementEnergy and exergy analyses for a cement ball mill of a new 2018年7月1日 Among the industries, the nonmetallic industry was reported as the third largest energy user and accounted for about 12% of the global energy use [1]Within this portion, cement industry had the majority of the utilization with 85–12% [1], [2]US Energy Information Administration (EIA) [7] named cement industry as the most energy intensive among the Energy and cement quality optimization of a cement grinding circuitEnterprise Risk Eliminate Withdraw Approach Based Risk Management in Cement Industry Khaled M S Gad El Mola Assistant Professor, Mechanical Engineering Department, Industrial Engineering Program, Faculty of Engineering at Helwan, Helwan University, Helwan, Cairo, Egypt Email: kmsoli01@yahoo controlEnterprise Risk Eliminate Withdraw Approach Based Risk Management
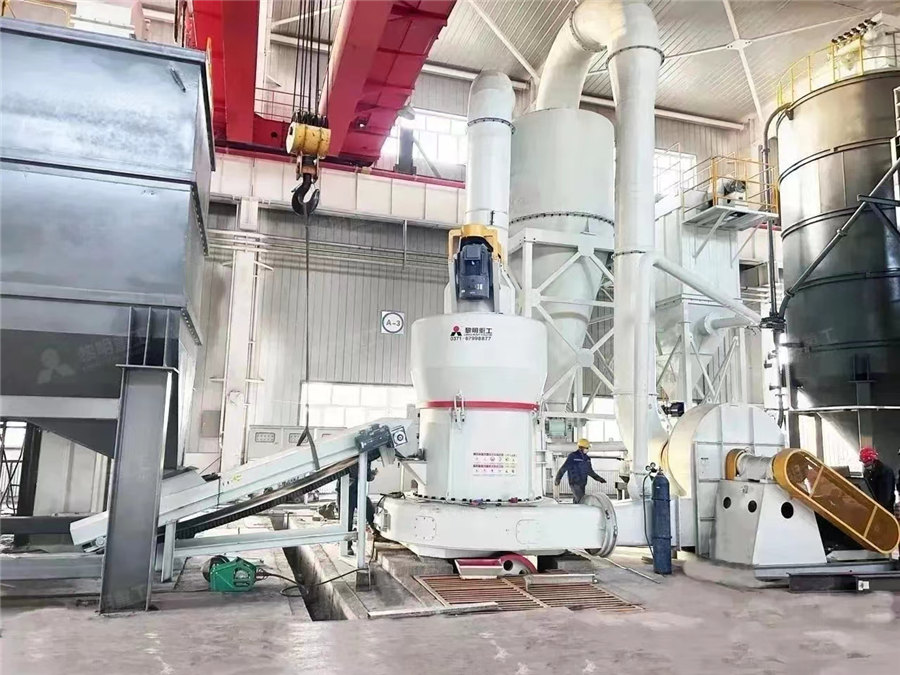
Thomas Holzinger, Holzinger Consulting, grinding system
For the cement quality of a roller press finish‑grinding system, studies show that for a standard type cement compared to VRM or ball mill, no differences could be observed Only for fine cement types (>4500 Blaine), requiring high early strengths, did the roller press finish‑grinding system achieve slightly lower strength performancesThis grinding ensures that all materials reach specific sizes required for the desired cement quality Quality Control: Postgrinding, the cement undergoes screening to ensure it meets the specified quality standards Any cement that does not meet the specifications is sent back for further processing Storage Preventing Moisture Contact StepbyStep Guide to the Manufacturing of Cement PRACTICAL VRM grinding bed This in turn reduces the amount of fossil fuels required to heat the mill and improves cement quality by reducing the negative impact of cement prehydration Below GCP presents two cement industry case studies from VRM systems located within the zones of high water stress shown in Figure 1 Case study 1: southern AfricaWATER MANAGEMENT Making VRM cement production greener2022年12月13日 I am delighted to share that one of our integrated cement plant at Muddapur in Karnataka is India’s only Integrated Cement Factory, which has been awarded this year FY2022 with most prestigious CII GreenCO Platinum Award for implementation of world’s best practices and best available technologies in decarbonisation, process optimisation, clean energy, waste Water management has recently undergone a paradigm shift
.jpg)
Grinding Solutions Indian Cement Review
2015年1月31日 From hubandspoke model to split grinding; from singlegrinding solution to a combination of system solutions; and from energyintensive traditional ball mill to upgraded versions and use of pregrinders, the cement industry is shifting towards more energyefficient grinding solutions ICR trains its spotlight on the current technology trends The cement 2023年9月26日 Maintenance Performance Optimization for Critical Subsystems in Cement PreGrinding Section: A Case Study ApproachMaintenance Performance Optimization for Critical Subsystems in Cement March, 2019 for Cement Grinding Unit M/S Shree Jharkhand Cement Plant (A unit of Shree Cement Limited) located near Village — Hansda, PO — Burudih, Dist — SeraikelaKharsawan, Jharkhand The plant has been commissioned in the month of May 2019 Submitted for your kind information please Thanking you, Yours faithfully,Automatically generated PDF from existing images Shree CementCement grinding is carried out in closed cement mill Dust extraction and pollution control system consisting of highly efficient bag filters and ID fan have been provide for cement mills, clinker silo, fly ash storage silo and cement silo Stack height of Cement mill of Bihar Cement Plant is 425 meter and Cement mill of NewPage 1 of 36 Shree Cement
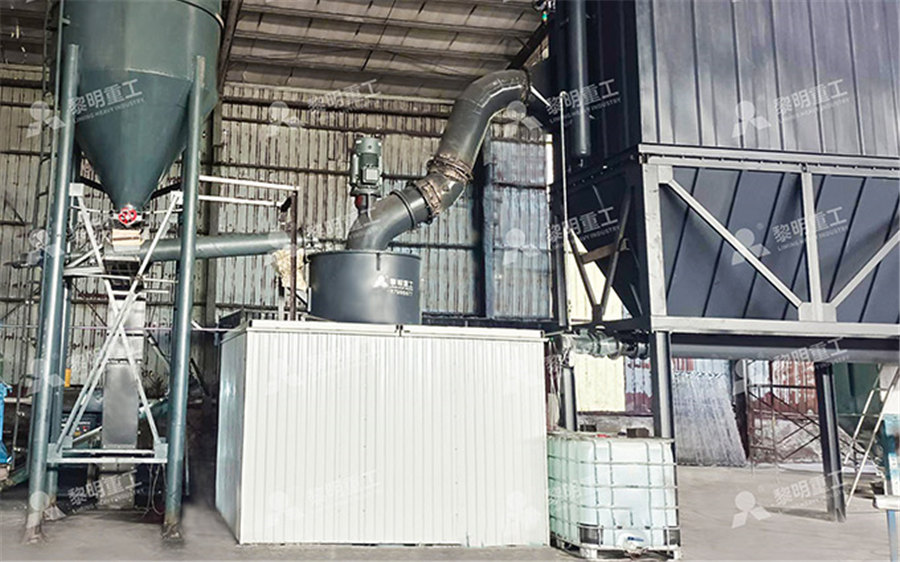
CRUSHING AND GRINDING SEMINAR The Cement
The purpose of the training is to Identify and understands necessary known and unknown information towards the completed cycle of the crushing and grinding system Throughout the course the lectures are supplemented with exercises Finish Grinding Quality specifications for portland cements are given in ASTM C 150 Test procedures are in ASTM C 114 Material proportioning and grinding circuit process control are very important to the quality of the finished product Everything you need to know about Operational 2012年12月31日 at evaluating the liquidity management of five leading Cement companies over a period of 10 years (200001 to 200910) More specif ically the emphasis w ill be on the follow ing issues:Liquidity Management of Indian Cement CompaniesStage 3: Grinding and Blending – Turning Clinker into Cement: 1 Clinker Grinding: Ball Mills: The cooled clinker is finely ground in ball mills, transforming into a powder known as cement Gypsum is added during this stage to control the setting time and improve the The Process of Manufacturing of Cement The Enterprise World
.jpg)
Effect of ester modified triethanolamine on the grinding quality
2024年9月13日 Enhancing the efficiency of grinding cement clinker can be approached from two key angles: the upgrading of grinding equipment and the introduction of cement grinding aids (GAs) Notably, GAs have been widely used due to the characteristics of minimal dosage, costeffectiveness, and remarkable enhancement [4], [5], [6]Zuari Cement is one of the leading cement producers in South India A owned subsidiary of the HeidelbergCement Group its, Commitment to customer satisfaction has seen Zuari Cement grow from a modest 05 million tonne capacity in 1995 to above 71 MnT in 2016 and has earned it amongst the leading innovative cement Brands in the countryZuari Cement Chennai Grinding UnitGrinding aids also serve to reduce coating problems in cement storage and enhances cement strengths GRINDING MILLS Mills will be selected according to type most suitable for required capacity and duty and for overall power consumption Cement grinding operation may be performed in one of the following mill setups Ball and tube millsCement Grinding Cement Plant OptimizationAt the Cement Grinding Stage, 90 – 95% of the clinker is mixed with gypsum and ground in a Cement Ball Mill to produce quality cement OPC 43 and OPC 53 In case of PPC Cement, there is an addition of Fly AshCement Grinding Unit Process High Quality Cement Grinding
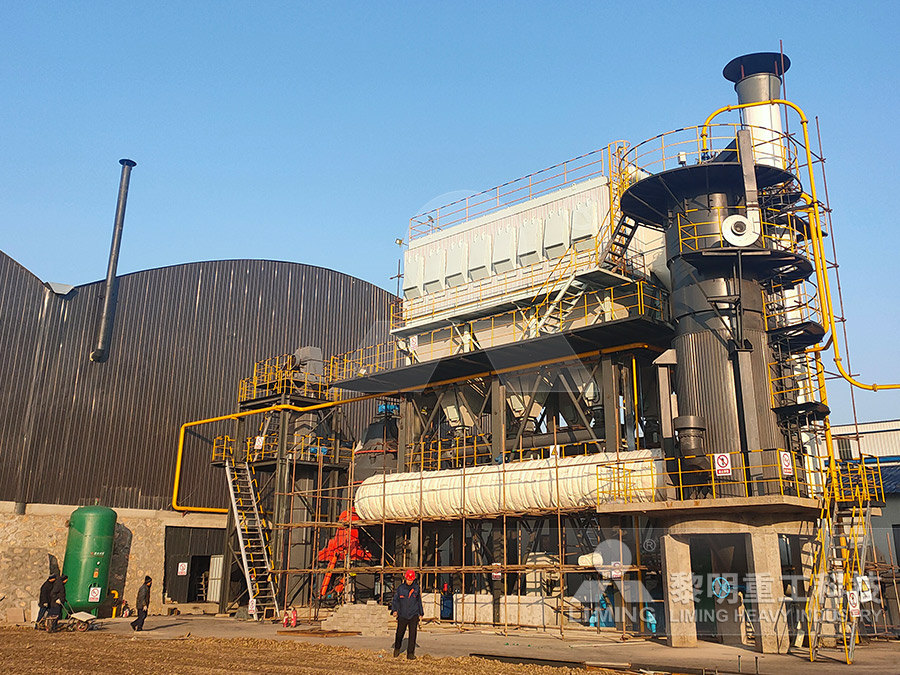
Grinding process is a critical stage in cement production
2023年8月21日 Tushar Khandhadia, General Manager – Production, Udaipur Cement Works, discusses the role of grinding in ensuring optimised cement production and a high quality end product How does the grinding process contribute to the production of highquality cement?The quality of cement depends on its reactive properties and particle size grinding helps to reduce Understand the fundamentals and gain insights on how to improve the performance and productivity, efficiency, and product quality of your grinding systems This 3day seminar covers ball and vertical mills with a focus oncomminution theory, design basis, operational principles, control and regulation, process troubleshooting, calculation methods, and optimizationCement Production Seminar: GrindingCEMENTS GROUND IN THE VERTICAL ROLLER MILL FULFIL THE QUALITY REQUIREMENTS OF THE MARKET DiplIng Th Fahrland, DrIng KH Zysk, Loesche GmbH, Duesseldorf, GermanyCEMENTS GROUND IN THE VERTICAL ROLLER MILL FULFIL THE QUALITY 2021年4月19日 Grinding of finished cement is performed in a single stage, intergrinding materials with very different grindabilities This intergrinding process has many different interactions among the different components of the finished cement In a context of developing more sustainable and less energy intensive processes, it is important to understand the Resistance to Grinding and Cement Paste Performance of Blends
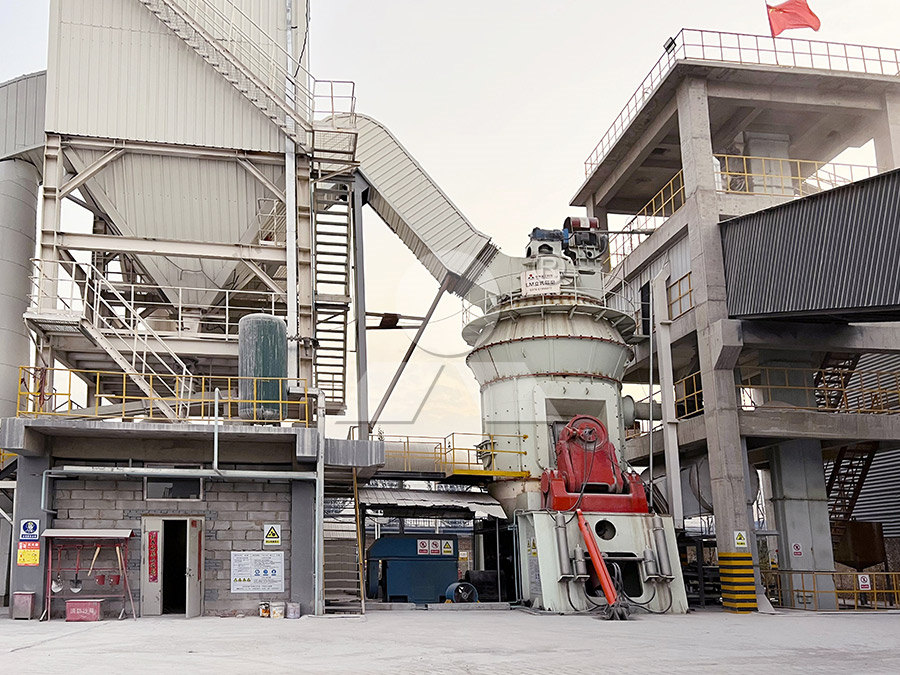
SUSTAINABLE WASTE MANAGEMENT: A CASE
2015年12月28日 Bapat (2013) mentions that there has been a considerable improvement in technology upgradation in the industry Pathak et al (2015) identify the waste management practices in this industry and The purpose of the training is to Identify and understands necessary known and unknown information towards the completed cycle of the grinding system, whether is a ball or vertical mill Throughout the course the lectures are supplemented with exercises and case studies, allowing the participants to relate the course material to their cement grinding facility and as a result CEMENT GRINDING COURSE The Cement InstituteHighcapacity cement grinding solutions are essential for meeting today’s production demands while optimizing energy use and maintaining product quality Technologies like vertical roller mills, highpressure grinding rolls, and horizontal roller mills offer robust solutions that enable cement plants to achieve higher output with lower operational costsHighCapacity Cement Grinding Solutions: Enhancing Efficiency Raw material and cement grinding are the first and the last major process steps during cement production The energy demand of these two processes amounts to up to ~70% of the electrical energy used in a cement plant For you as participant, this training will help to obtain a better understanding of the comminution processes as well as the equipment used for grindingGrinding Technology in Cement Production
.jpg)
CuttingEdge Grinding Solutions Indian Cement Review
2023年8月21日 ICR looks at the inner workings of grinding mills in the cement industry to understand the technological advancements that are reshaping the landscape against the foreground of sustainability Innovations to enhance the grinding processes are aimed at minimising their environmental footprint while increasing efficiency and performance In 2022年5月17日 Gebr Pfeiffer SE to supply MVR components, 5,810 kW gearbox Chettinad Cement has ordered an MVR 5600 R6 type mill and an MVR 5300 C6 type mill for raw meal grinding and grinding composite cement, respectively, from Germanybased Gebr Pfeiffer Private Limited for a new production line at its integrated Kallur plant in KarnatakaThe supplier []Chettinad Cement orders MVR mills for cement grindingThe cement quality control of cement plant is mainly based on specific technological process, which includes the quality control of various raw materials, semifinished products used in the production process, the sampling analysis of materials, to ensure the stability and uniformity of raw material composition The quality control of raw materials requires chemical composition How to improve cement plant process for better cement quality2024年1月27日 Dust monitoring in cement plants is more than just a legal necessity; it is an integrated approach for preserving human health, protecting the environment, and improving operational efficiency Two critical pillars underlie this complete approach: compliance, process optimization, and environmental stewardship Process OptimizationDust Monitor for Cement Plant: Improving Air Quality