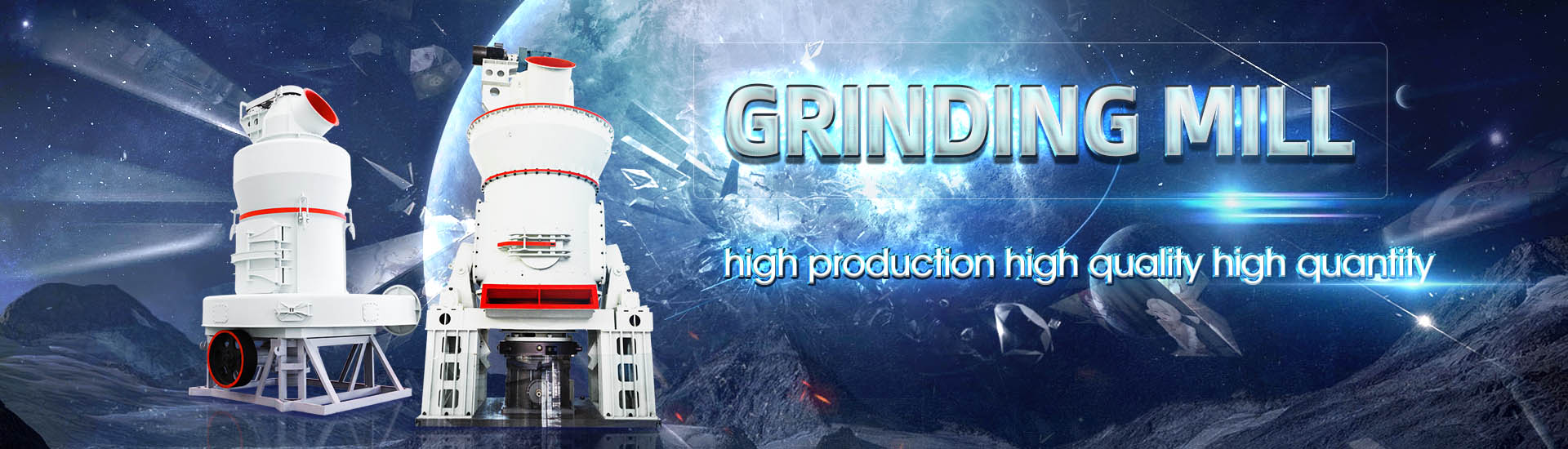
Powder pressing process flow
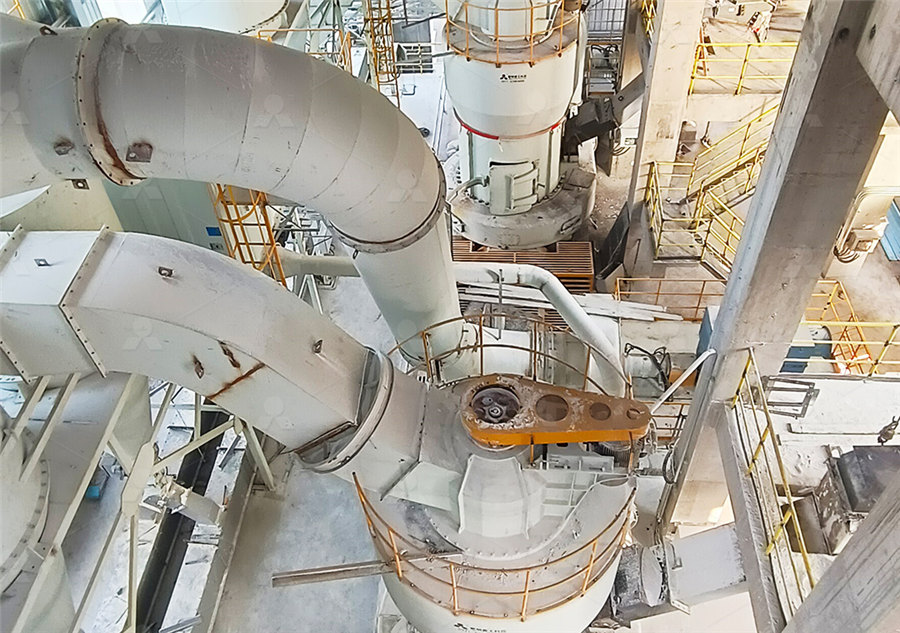
Powder Metallurgy PDF
•After the metallic powders have been produced, the conventional PM sequence consists of three steps: 1 Blending and mixing of the powders 2 Compaction pressing into desired part shape Figure 181 Simplified flow chart of the basic powder metallurgy process Figure 182 Two methods for producing metal powders: (a) melt atomization and (b) atomization from a rotating Chapter 18: Powder Metallurgy SUTPowder metallurgy – science of producing metal powders and making finished /semifinished objects from mixed or alloyed powders with or without the addition of nonmetallic constituentsPowder metallurgy – basics applications IIT Guwahati2014年1月1日 The powderforming process contains four basic steps: 1 Powder preparation 2 Powder mixing, blending, and/or slurry preparation (a powder–liquid suspension is known as a Powder Processing of Bulk Components in Manufacturing
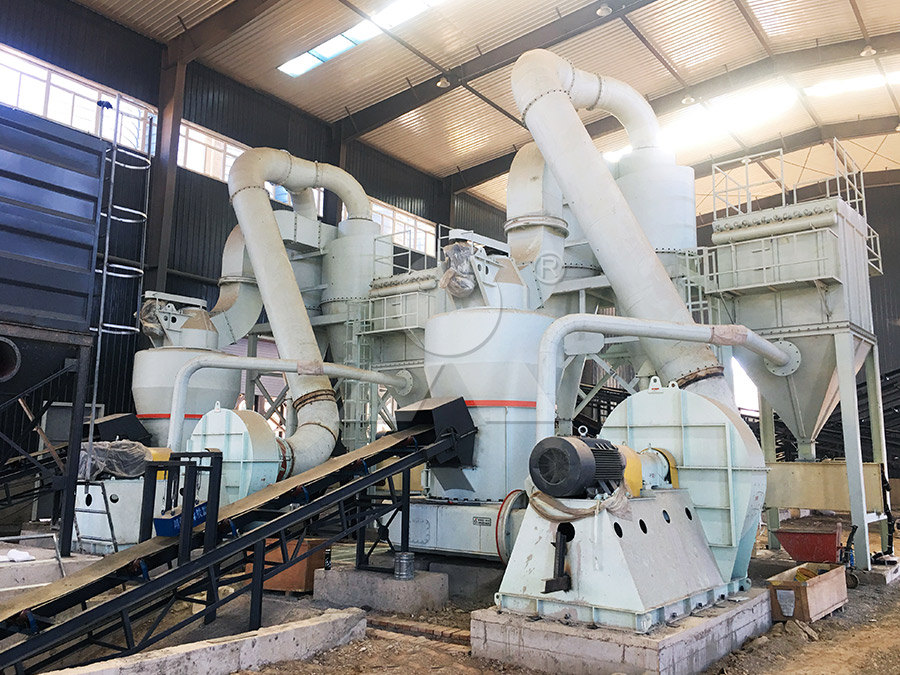
Characterization and flowability methods for metal powders
2020年12月3日 Metal powders can be processed, for example, by pressing, sintering, thermal spraying techniques or more modern additive manufacturing techniques, such as selective After the mass of powder is squeezed into a shape and ejected from the press, it is fed slowly through a special hightemperature controlled atmosphere furnace to bond the particles Powder Metallurgy Processes MPIF2022年11月25日 Press Sinter process compacts metal or ceramic powder into a shape and then sinters it at high temperatures to bond particles CIP applies uniform pressure to powder within a flexible mould submerged in a fluid, What is Powder metallurgy Powder metallurgy types In this review, we discuss powder flow and its measurement techniques and mainly focus on various approaches to improve the cohesive powder flow property As a solid state, powders have diverse applications in different A concise summary of powder processing
.jpg)
Pressure sintering of powder materials Powder Metallurgy and
2011年6月22日 In these processes, powder (porous) blanks are compacted, consolidated, and moulded under applied forces without form discontinuity Powder compaction in a die during 2023年6月1日 Since the sample size was drastically reduced, which introduced powder flow measurements into pharmaceutical preformulation stages, this method can be applied to process operations such as die and capsule filling, mixing, powder coating and conveying, and to applications such as dry powder inhalers, in which particlelevel behavior dominates over bulk A concise summary of powder processing methodologies for flow The powder metallurgy process, also known as pressandsinter consists of mixing elemental or alloy powders, compacting the mixture in a die, and then sintering, or heating, the resultant shapes in an atmospherecontrolled furnace Conventional Powder Metallurgy Process MPIF2024年2月2日 An atomization machine uses high velocity water flow to atomize molten metal into particles and is capable of producing 10 kg to 10,000 kg of powder in each batch There are few limitations to the types of metals that can be used in the powder metallurgy process Pressing And Sintering Of Powder Parts Porosity, Impregnation, And Powder Metallurgy: What Is It? Processes, Parts, Metals Used
.jpg)
Powder Metallurgy: What Is It? Processes, Parts, Metals Used
Powder metallurgy is a manufacturing process that produces precision and highly accurate parts by pressing powdered metals and alloys into a rigid die under extreme pressure With the development and implementation of technological advances, powder metallurgy has become the essential process for the production of bushings, bearings, gears, and an assortment of Powder Processes Lorraine F Francis, in Materials Processing, 2016 56 Summary Powder processes provide a means to create simple as well as complex shapes from powder starting materials The engineering of powder processing methods requires an understanding of how the characteristics of powders, including size, size distribution and shape, impact the flow and Powder Process an overview ScienceDirect TopicsDefinition and process of hot pressing Hot pressing is a highpressure, lowstrainrate powder metallurgy process used to form powder or powder compact at high temperatures to induce sintering and creep processesIt involves the simultaneous application of heat and pressure to fabricate hard and brittle materialsAn Indepth Analysis of Hot Pressing Technology and Its Since the sample size was drastically reduced, which introduced powder flow measurements into pharmaceutical preformulation stages, this method can be applied to process operations such as die and capsule filling, mixing, powder coating and conveying, and to applications such as dry powder inhalers, in which particlelevel behavior dominates over bulk behaviorA concise summary of powder processing methodologies for flow
.jpg)
Powder Processing an overview ScienceDirect Topics
Production equipment and tooling selection Peter Scallan, in Process Planning, 2003 Powder processing The steps involved in powder processing were previously described in Section 4103 and these are powder blending, compacting, sintering and finally secondary processing In terms of equipment, the compacting requires a press that can deliver forces in the region of 10–17 2014年1月1日 Pressure is applied to the two opposing pistons to consolidate the powder into a green body Die pressing metal powders is a simple process in most cases because the plastic deformation of the particles enables excellent powder flow, cold welding, and in some cases almost complete consolidation by cold weldingPowder Processing of Bulk Components in ManufacturingThis article provides an overview of the powder pressing process, providing information on the powder properties of bronze and brass and the roles of lubricant and compaction dies in the pressing process It discusses the structural defects that originate during the compaction processProcessing of Powder Metallurgy Bronze and Brassprocess grinds the powder materials by impact/collision attrition • Milling can be dry milling or wet milling In dry milling, about 25 vol% of powder is added along with about 1 wt% of a lubricant such as stearic or oleic acid For wet milling, 3040 vol% of powder with 1 wt% of dispersing agent such as water, alcohol or hexane is employedPowder metallurgy – basics applications IIT Guwahati
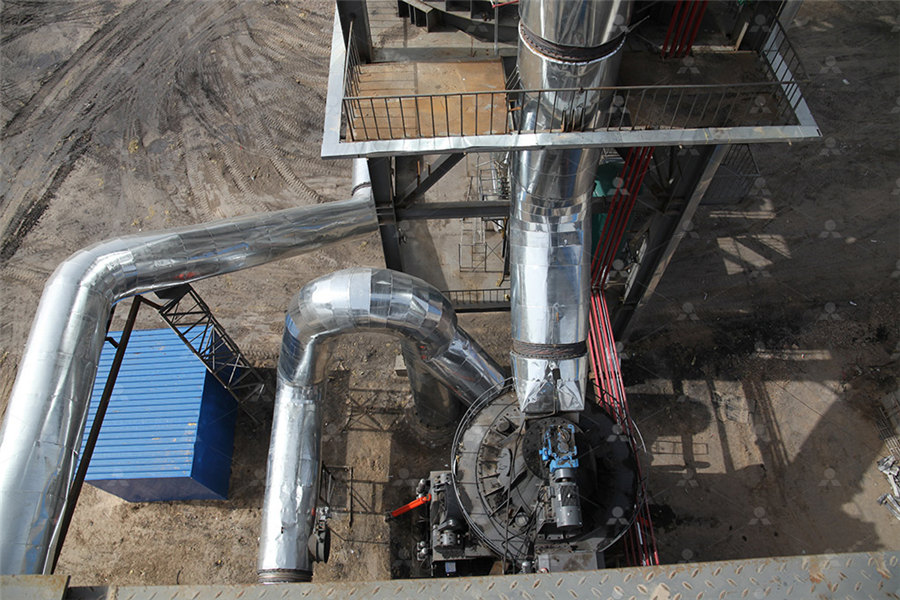
Advances in PowderFilled Mold Processes: A Comprehensive
2024年11月9日 Powder molding technology is a versatile process widely used in the pharmaceutical, ceramic, chemical, food, and powder metallurgy industries The powderfilling mold process is a key link in powder compression molding, and the uniformity and consistency of powder filling directly affect the final quality of powder products Powder filling of molds is a Cocoa Powder Manufacturing Process Flow: From Beans to Powder Ever wondered how that rich, velvety cocoa powder, made from the finest raw materials, makes its way into your favorite desserts? Brace yourself, because Cocoa Powder Manufacturing Process Flow: From Two major factors in the compacting operation influence design considerations with powder metallurgy: the flow behavior of metal powders and the pressing action Metal powders do not flow hydraulically because of the friction between particles and the dies The design, therefore, should ensure adequate powder distribution within the die cavity Design Considerations with Powder Metallurgy PickPM2022年11月12日 Cocoa beans are an important economic crop and are also divided into many varieties with different flavors There are four main products of cocoa beans after processing: cocoa nibs, cocoa liquor, cocoa butter, and cocoa powder Today, let us approach the cocoa factory and take a look at the cocoa processing flow chart Process Flow of Cocoa Beans:Cocoa Processing Flow Chart (From Bean To Powder)
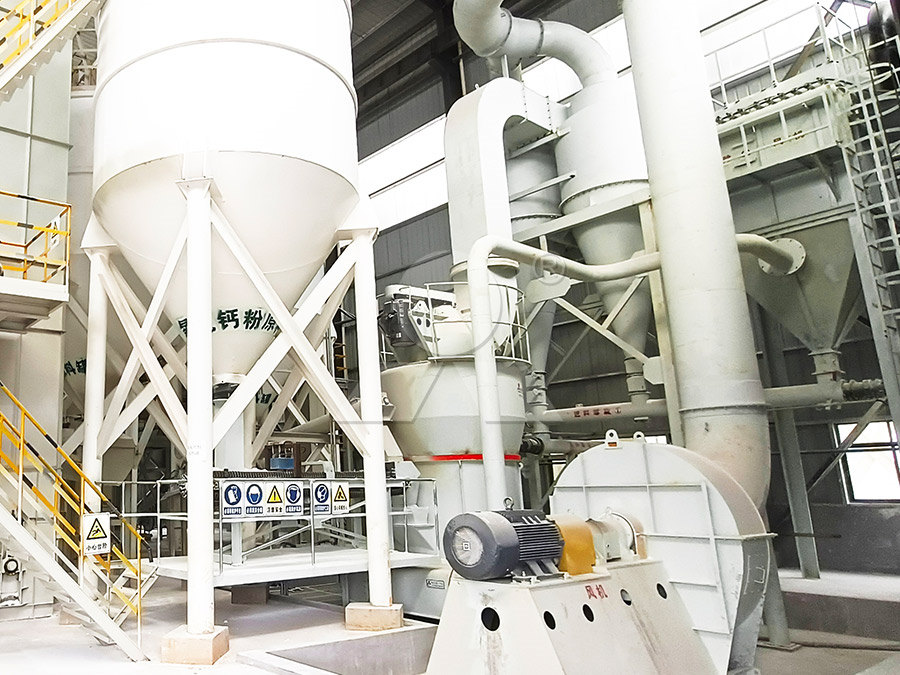
What is Powder metallurgy Powder metallurgy types application
2022年11月25日 Because of this uniaxial pressing, the powder particles do not flow well perpendicular to the forcing axis, limiting the part geometry design to one direction Isostatic Pressing Not like Press and Sintering process’s uniaxial pressure, in Isostatic pressing, hydraulic pressure is applied to the powder from all directions2020年12月3日 The AIFE parameter and flow index were determined from three commonly used rotary shear devices: The computercontrolled Ring Shear Tester RST01 pc, the Brookfield PFT Powder Flow Tester and the Characterization and flowability methods for metal powders2013年11月29日 The object of a pressing process is to form a netshaped, homogeneously dense powder compact that is nominally free of defects A typical pressing operation has three basic steps: (1) filling the mold or die with powder, (2) compacting the powder to a specific size and shape, and (3) ejecting the compact from the dieCeramic Powder Compaction MRS Bulletin Cambridge Core2016年11月16日 3 Introduction – Powder Process • Process of producing metal powders and making finished /semi finished objects from mixed or alloyed powders with or without the addition of nonmetallic constituents • Powder metallurgy (PM) is a metal working process for forming precision metal components from metal powders The metal powder is first pressed into Powder metallurgy PPT SlideShare
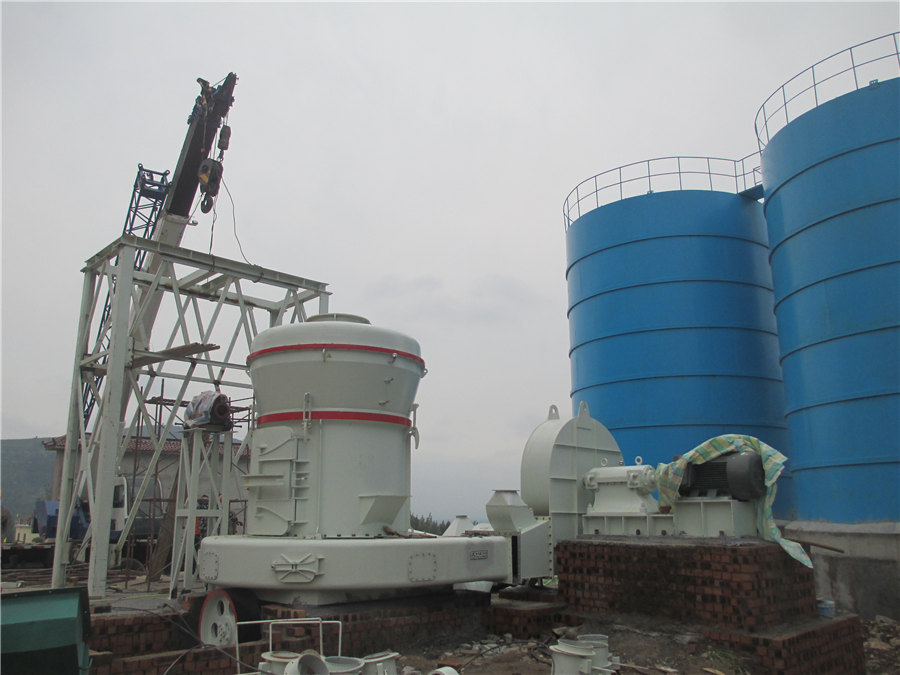
Chapter 18: Powder Metallurgy SUT
182 The Basic Process Four basic steps 1 Powder manufacture 2 Mixing or blending 3 Compacting 4 Sintering Figure 181 Simplified flow chart of the basic powder metallurgy processNevertheless, as with other powder metallurgy processes, manufacturers must carefully characterize the metal powder’s properties for the process to be successful Commonly characterized physical properties include powder flow, density, hardness, particle size, and particle shape of the respective powders Other key characteristics include Optimizing metal powders for Isostatic Pressing Malvern This case study has been focused on the intensification of the freeflowing powder preparation process involved in the very beginning of the ceramic tile manufacturing process Nowadays, the most widely used ceramic tile shaping method is uniaxial pressing of spraydried powder in hydraulic presses The base Case Study 2: Ceramic Powder Processing2017年3月14日 Powder Pressing Powder pressing is the compaction of powders into a geometric form Pressing is usually performed at room temperature This creates a solid part called a green compact The strength of Powder pressing PDF Free Download SlideShare
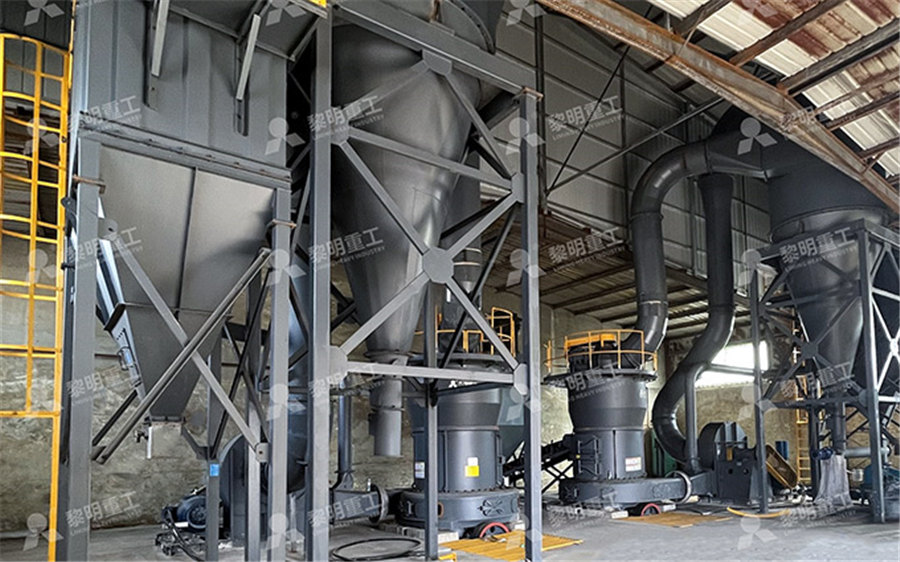
Material characterization solutions for pressing and sintering
For materials like ceramics and hard metals, the primary powder is often spraydried to form a feedstock with improved flow characteristics and compressibility In order to achieve consistent quality in the feedstock, ‘green body’, and final sintered component, the metal or ceramic powder’s characteristics must be carefully optimizedDownload scientific diagram Flow chart of powder metallurgy process from publication: Effect of Powder Metallurgy Process and its Parameters on the Mechanical and Electrical Properties of Copper Flow chart of powder metallurgy process ResearchGateFLOW CASTING PULVERIZATION DEGASSING FORGING Rapid Solidification / Powder Metallurgy 14010102 Manufacturing Process VACUUM HOT PRESSING INCOMING Al INGOT AND ALLOYING ADDITIONS CONTROL CASTING HEAD Most of the P/M alloys can be divided into three main application fields: low densityAluminium Powder MetallurgyTemperature control is an essential aspect of the pressing process in cocoa powder manufacturing The pressing process is usually done at specific temperatures ranging from 8085 degrees CelsiusCocoa Powder Manufacturing Process: From Bean to Powder
.jpg)
The Importance Of Powder Flow Characterization Granutools
The funnel or silo configuration is a common approach for powder feeding in food and pharma industries, where powder bridging and powder segregation must be avoided to ensure consistent flow rates Indeed, powder segregation during processing and storage may result in poor flow, a buildup of powder residue, and problems with stock handling and filling and packing operationDry pressing is an established process for shaping components using powder technology for many materials However, complex component shapes place high demands on the pressing technology and bring their own challenges, such as distortion due to green density gradients and cracks after ejection or firingPowder Pressing and Sintering Fraunhofer IWM2022年1月4日 A better dimensional control can be achieved by this dry powder pressing methodology 1411 Uniaxial Die Pressing In this process granulated powder is allowed to flow into a hardened steel die/mold followed by uniaxial pressing Powder inside the die is pressurized and kept at desired pressure for some time before releasing the pressureShape Forming and Sintering of Ceramics SpringerLink2023年6月13日 Let’s see what products different manufacturing industries are making by using the powder metallurgy process: 1 Industrial Tools The powder metallurgy process helps form several industrial tools, including gauges, wire guides, wire drawing dies, blanking and stamping tools, hammers, bits, stones, etcA StepByStep Guide To Powder Metallurgy Process JIAHUI BLOG
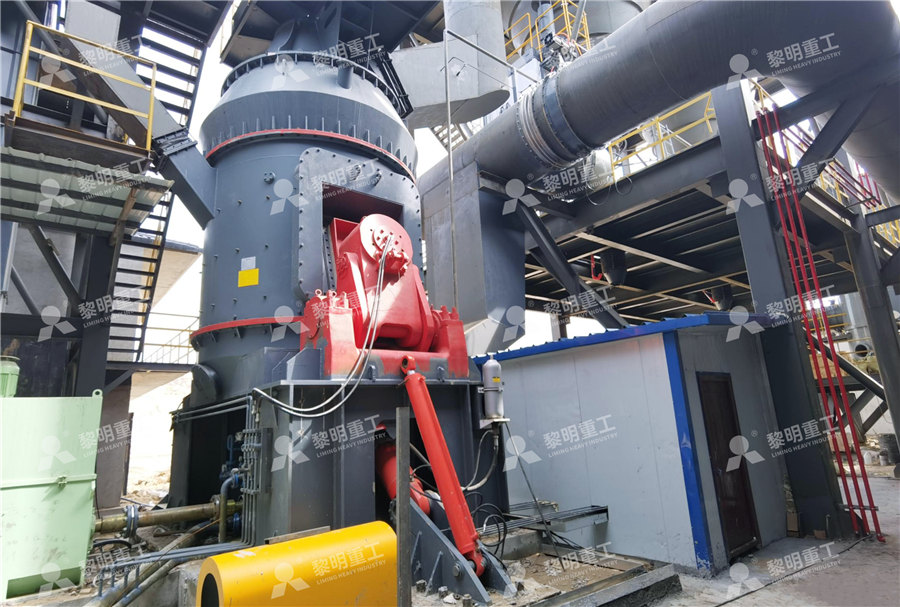
Forging and Hot Pressing
the development of the proper process parame ters and tooling for new applications and the solution of problems in existing processes The important process features are described here for both powder forging and hot pressing, along with specific applications and materials Fig 1 Preform Upsetting Repressing Forging (a) Preform Repressing Hot Results and perspectives on the collaboratory process are published in “Dense granular flow — a collaborative study,” Powder Technology 284 (2015) 571–584 Building from this, IFPRI has engaged in fundamental work linking powder flow with granular physics, and is now running an interactive RoundRobin exercise aimed at best practices in DEM modeling of dry flowsPowder Flow International Fine Particle Research InstituteThe caking of a powder can very weak, the powder being broken down in the subsequent process stages, which is not too problematic, or can be much harder, with the lumps being persistent and causing some operational problems in factories, or even consumer complaints if the material has been conditioned for being soldPowder caking or clumping review : causes and how to solve itThe Powder Metallurgy Process Powder Metallurgy comprises a family of production technologies, which process a feedstock Powder Metallurgy industry news, technical articles, magazine The dominant consolidation process involves pressing in a rigid toolset, comprising a die, punches and, possibly, mandrels or core rodsThe Powder Metallurgy Process
.jpg)
Parametric optimization of hot pressing powder metallurgy process
2024年5月7日 The current study aims to develop a multilayered B4C/AA7075 functionally graded material (FGM) with high impact toughness as well as hardness The FGM was fabricated through a hot compaction powder metallurgy process Taguchi's L9 orthogonal array coupled with grey relational analysis was utilized to optimize the critical process parameters such as MCE 313: Manufacturing Process I Powder Metallurgy Department of Mechanical Engineering Page 3 FIGURE 71: Several atomization methods for producing metallic powders: (a) and (b) two gas atomization methods; (c) water atomization; and MCE 313: Manufacturing Process I Powder Metallurgy 71 Powder Compact thin films are deposited via an optimized powder aerosol deposition (PAD) process Pressing at 120 °C further improves the morphology and the optoelectronic film properties Integrating the perovskite films in a solar cell configuration results in fully working devices, with champion power conversion efficiencies of >6%First of Their Kind: Solar Cells with a Dry‐Processed Perovskite 2021年11月1日 Additive manufacturing (AM) is one of the representatives of advanced manufacturing technology, and it has been developed rapidly in the industry due to its unique advantages which are difficult to be realized with traditional processing methods [1, 2]In the powderbed AM process, a thin layer of powder is spread on the powder bed by a roller or a Comprehensive evaluation of powder flowability for additive
.jpg)
Powder Technology and Particle Simulation Fraunhofer IWM
Powder pressing and sintering Most powder technology process routes include two basic process steps: shaping and subsequent heat treatment Pressing a powder into a mold is one of the most common shaping processes Determining the optimal process parameters for new or modified processes and materials is often timeconsuming