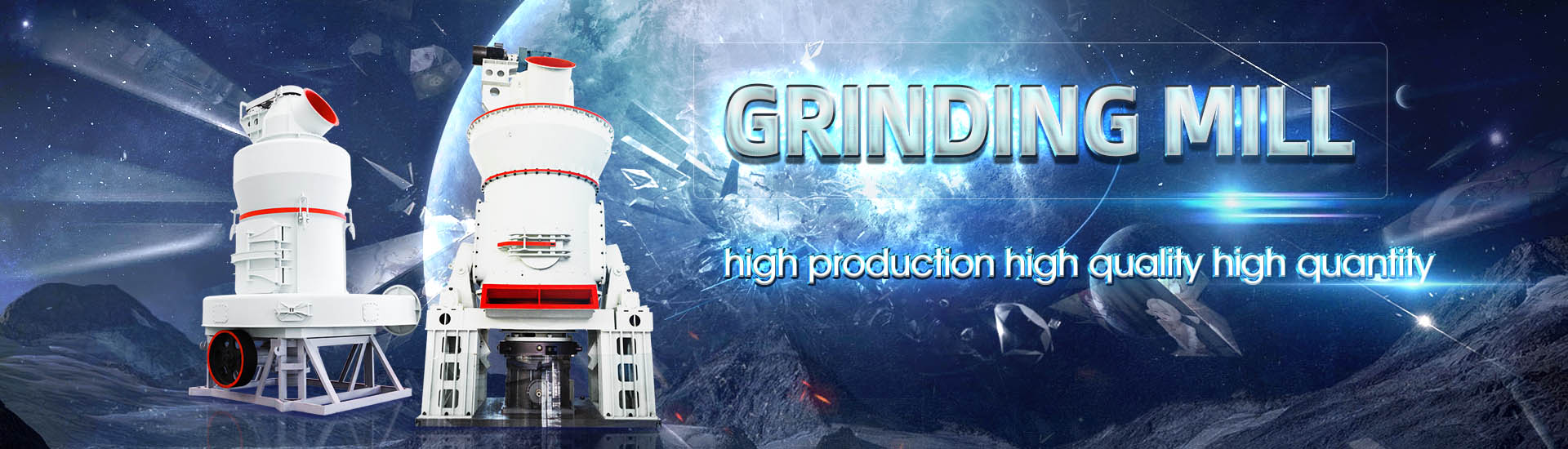
How to reduce material costs in iron ore powder processing plants
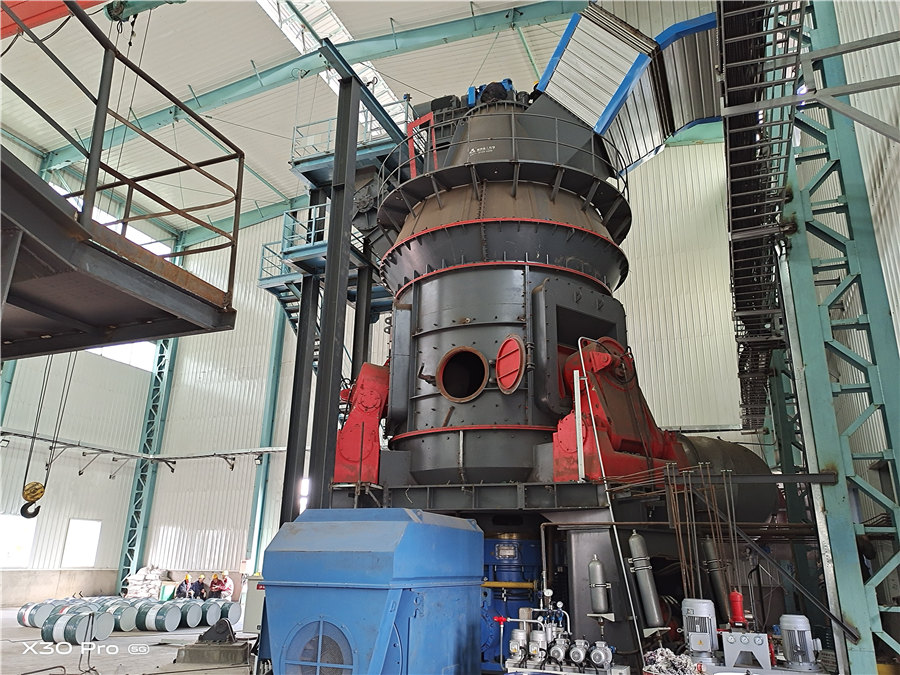
ENERGYEFFICIENT TECHNOLOGY OPTIONS FOR DIRECT
Direct reduction of iron (DRI) forms an important subsector of the Indian steel sector, accounting for about 33% of the total steel production, which is about 3415 million tonne of steel produced in2021年4月21日 From a technical perspective, the challenge of decarbonization involves two processes: chemical reduction for iron ore refining (process emission), commonly with Lowcarbon production of iron and steel: Technology options, 2022年10月26日 The results show that the optimization of ore proportioning according to the characteristics of the iron powder can effectively reduce the ore blending cost and process Optimizing Iron Ore Proportion Aimed for Low Cost by Linear Hatch‘s Mine to Process Optimization projects integrate mining and processing strategies, minimizing operating costs and maximizing overall profit Tlhe methodology involves ore Integrated mining and processing strategies reduce costs and
.jpg)
(PDF) Reducing Production and Transportation Costs for the
2021年3月1日 The article considers an integer model for transporting iron ore raw materials with minimal transportation costs An integer production and transport model allows you to Applying it to ironmaking production is not only conducive to energy conservation and emission reduction in the ironmaking process but also can achieve efficient utilization of crop wastePractical ways to reduce iron ores: process route for 2018年7月23日 The company uses highquality magnetite iron ores and reduces it through the proprietary Höganäs sponge iron process where a finely divided iron ore is being reduced with Raw materials management in iron and steelmaking firms2022年10月20日 Making iron and steel from iron ore requires a long process of mining, crushing, separating, concentrating, mixing, agglomeration (sintering and pelletizing), and Iron Ore Processing, General SpringerLink
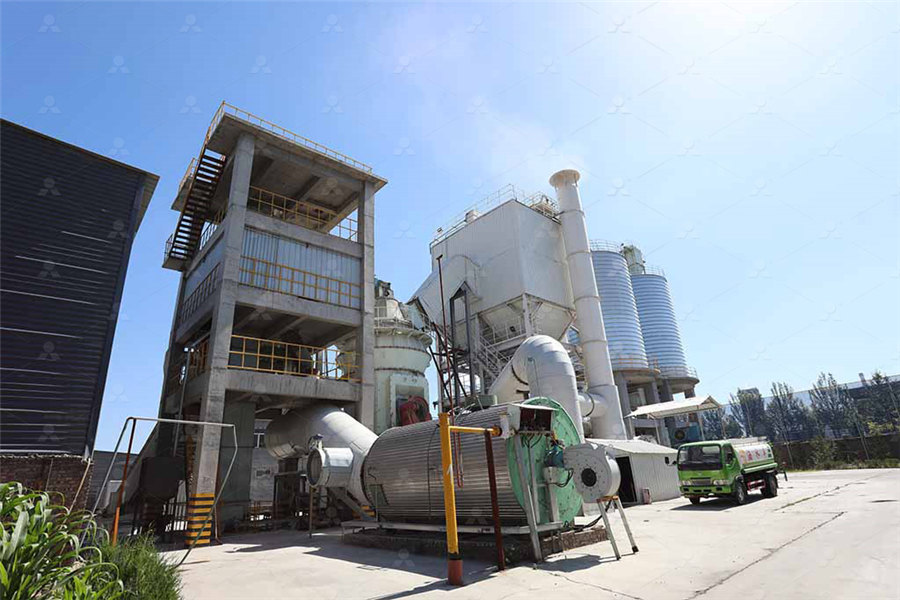
Iron Ore Reduction an overview ScienceDirect Topics
Iron ore reduction is an important process in the iron/steelmaking industry, where iron ore is reduced to metallic iron, usually with coal, coke, natural gas, CO, or hydrogen as the reducing 2020年10月26日 The depletion of highgrade ore minerals and the scarcity of fossil fuel reserves are challenging factors for metallurgical industries in the future Also, extensive mining for increased steel demand results in the Plasma Processing of Iron Ore IntechOpenThis processing works to transform raw, mined iron ore into a concentrated powder suitable for pelletizing In addition to mined iron ore, other sources of iron, such as flue dust collected from blast furnaces, or the dust produced at mine Iron Ore Pelletization FEECO International Inc2016年9月1日 Research aim is to study the material composition and sulfidemagnetite ore concentration of the ZapadnoPeschanskaya ore deposit and to develop a comprehensive technology for its processingREMOVING IMPURITIES FROM IRON ORES: METHODS
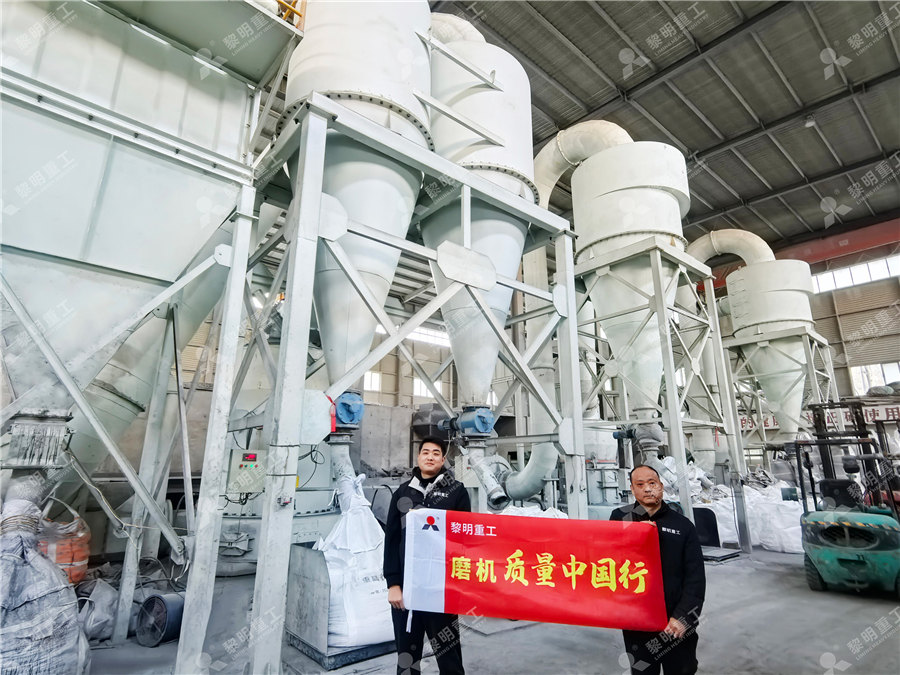
Iron Ore ScienceDirect
The estimated greenhouse gas emissions were 119 kg CO 2 e for mining and processing 1 tonne of iron ore The embodied energy values were 153 MJ/t ore for iron ore The results showed that loading and hauling made the largest contributions (approximately 50%) to the total greenhouse gas emissions from the mining and processing of iron ore2023年10月9日 The iron product has 6% carbon content The product is stable and free from spontaneous combustion In addition to the advantages of direct reduction iron, the product has high carbon content, and the smelting combustion releases heat that is used in the steelmaking process, which reduces electricity consumption during steelmakingDirect Reduction Ironmaking SpringerLink2021年5月20日 The pressure on the steel industry to reduce its carbon footprint has led to discussions to replace coke as the main reductant for iron ore and turn to natural gas, biosyngas or hydrogen Such a major transition from the blast furnacebasic oxygen furnace route, to the direct reductionelectric arc furnace route, for steel production would drastically increase the Driving investments in ore beneficiation and scrap upgrading 2019年11月30日 This paper explores possible strategies to meet iron ore customer requirements (reduce variability and keep Fe% and contaminants such as Al 2 O 3 % and P% within the acceptable tolerance) by optimizing the mine plan and scheduling strategy in the rehandling process The paper aims to obtain more homogenous iron ore grade by Effective Methods to Reduce Grade Variability in Iron Ore
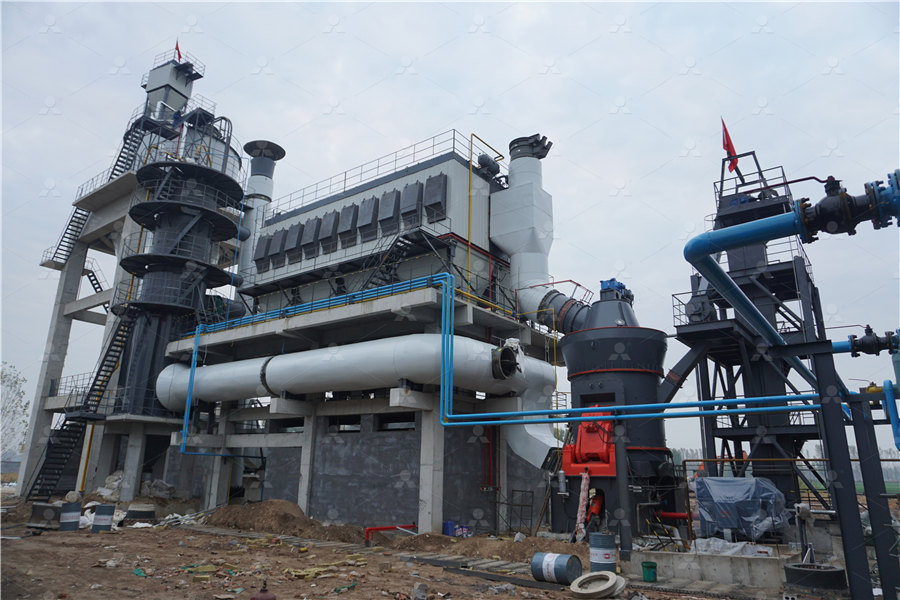
Dewatering and Drying in Mineral Processing Industry: Potential for
2010年6月30日 Wet beneficiation of minerals necessarily requires removal of large amounts of water—typically contaminated—before further processing of the concentrated ores can be carried outof oxygen from iron ore in its solid form The iron used in the steelmaking process is currently chemically reduced from iron ore through the use of fossil resources – natural gas or coal This process is known as Direct Reduced Ironmaking (DRI) Carbon combines with the oxygen in the iron ore, producing metallic iron and a carbonrich Fact sheet Hydrogen (H2)based ironmakingThe chronological distribution of the references cited in this paper is given in Fig 1 showing that the main reference material used in this review was published in the decade of the 1960s where there was significant research conducted in the United States on the processing of their iron ores The author is aware of significant publications in Portuguese (Brazilian iron ore industry), in Iron Ore Processing an overview ScienceDirect Topicslimited mining fleet available The process plant faced difficulties in maintaining grade and recovery as the ore mineralogy changed from predominantly hematite to a higher magnetite content Therefore, the focus of the project was to increase mine productivity, reduce costs in both mine and plant, and increase recovery as the oreINTEGRATED MINING AND PROCESSING STRATEGIES REDUCE COSTS
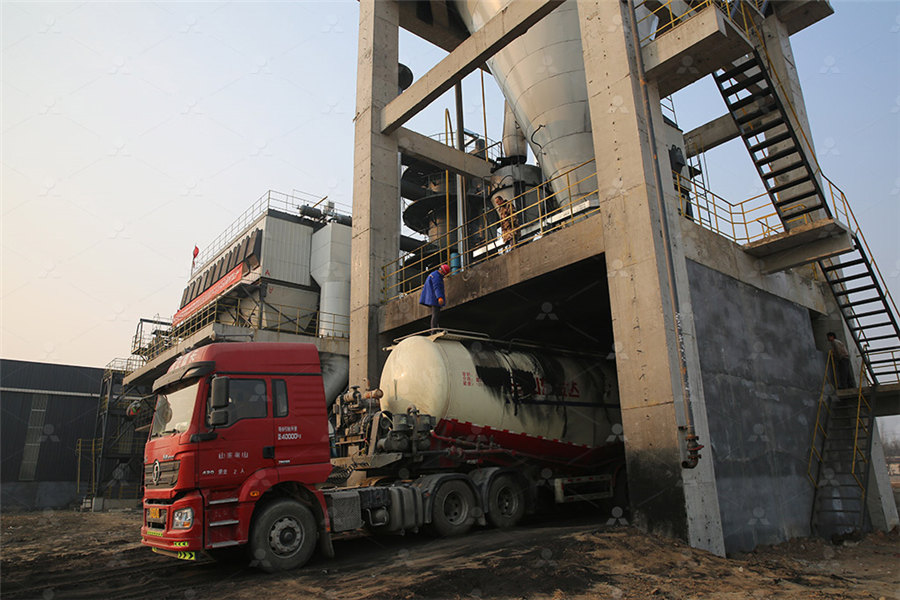
Ironmaking 101 – From Ore to Iron with Blast Furnaces
2017年10月10日 Roasting or calcination of the ore oxidizes some of the sulfur, phosphorus and arsenic impurities Sulfur oxide is volatile and evaporates off or is washed out Iron is mainly extracted from hematite (Fe 2 O 3) and magnetite 2023年2月15日 Hematite, also spelled haematite, is a weakly magnetic iron ore with better floatability than magnetite and wide distributionIt is one of the most important raw materials for the extraction of iron Its composition is complex How to Extract Iron from Hematite: Methods and Plants2022年10月4日 A notable fact is that the energy efficiency of conventional milling is only about 1%, as mentioned in Sect 1 An earlier experimental study indicated that about 80–90% of the energy input of a ball mill was used in heating the material (Schellinger 1951, 1952), and a recent study showed that over 75% of the electrical energy was used to heat the slurry (Bouchard et Reduction of Fragment Size from Mining to Mineral Processing: A 5 天之前 Copper industrial minerals include: natural copper, chalcopyrite, chalcocite, tetrahedrite, azurite, malachite, etc Chalcopyrite (a compound of copper, sulfur, and iron) is mined mainly, followed by chalcocite and bornite If copper ore wants to be fully utilized, it must be processed by flotation Flotation separation is an important copper ore beneficiation process in Copper Ore Processing Plants, Flow And Equipment
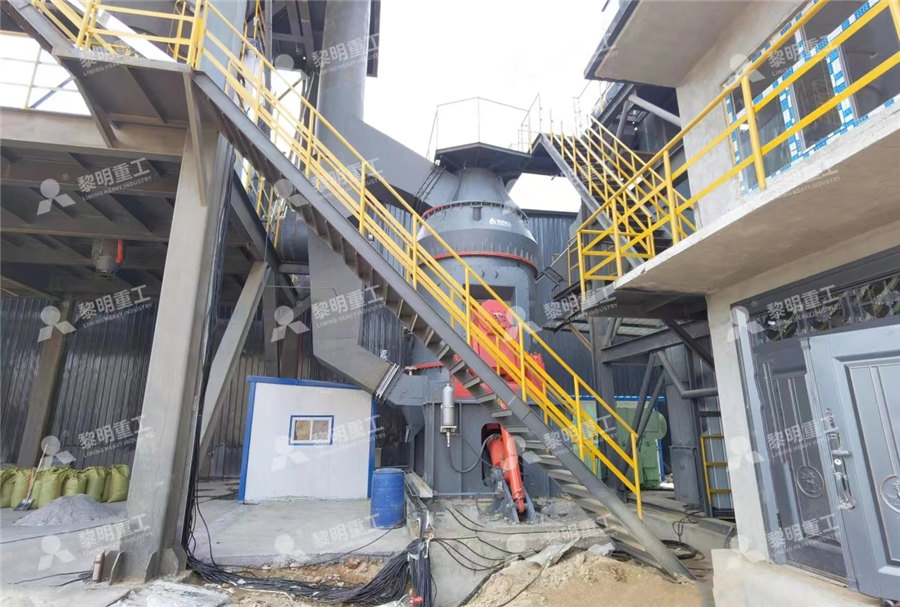
Introduction: Overview of the global iron ore industry
2022年1月1日 Turning to iron ore exports and imports, the tonnages are summarized in Table 11 for 2012 and 2018 (Australian Department of Industry, Science, Energy and Resources, 2021; US Geological Survey, 2020; United National Conference on Trade and Development (UNCTAD), 2021)As shown in Fig 13, China is the largest iron ore importing country and imported about 2023年10月25日 Iron ore is a crucial raw material for the global steel industry, and its supply chain is a complex network that involves multiple stakeholders and activities The iron ore supply chain begins with the mining of iron ore, which is then transported to processing plants for beneficiation and further refinement The refined iron ore is then transported to steel mills for Iron Ore Supply Chain: From Mining to Steel Production2023年4月5日 The blast furnace and direct reduction processes have been the major iron production routes for various iron ores (ie goethite, hematite, magnetite, maghemite, siderite, etc) in the past few decades, but the challenges of maintaining the iron and steelmaking processes are enormous The challenges, such as cumbersome production routes, scarcity of Recent Trends in the Technologies of the Direct Reduction and 2015年1月1日 Life cycle assessment (LCA) is a recognized method for assessing the environmental impacts of products, processes, and services It provides a scientifically sound method for comparing products and processes on common grounds and to identify socalled hot spots and provide opportunities for reducing environmental impactsLife cycle assessment of iron ore mining and processing
.jpg)
Essential Guide to Mineral Processing Equipment Flyability
The crude material is transferred to another offsite processing plant that smelts or refines the mineral ore into the final raw material Copper and gold concentrate Mineral Processing Equipment Below is a list of equipment used at each stage of mineral processing: Crushing and grinding equipment Cone crushers Gyratory crushers Jaw crushers2023年5月4日 Facilitylevel analysis of green H2 based steel production demonstrates colocation of highquality renewables and iron ore resources is imperative for cost minimisationGlobal green hydrogenbased steel opportunities surrounding When iron ore is extracted from a mine, it must undergo several processing stages Six steps to process iron ore 1 Screening We recommend that you begin by screening the iron ore to separate fine particles below the crusher’s CSS The six main steps of iron ore processing Multotec2017年10月17日 It is also the world's thirdlargest producer of LNG and is forecast to be the world leader by 2020 Reduction of iron ore to reduced iron form adds value and provides more compact products, which reduces From Ore to Iron with Smelting and Direct Iron
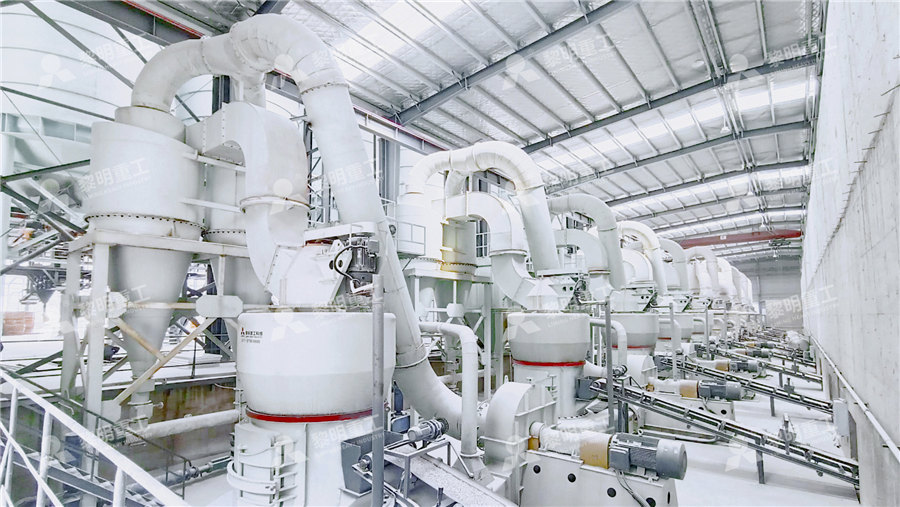
The Direct Reduction of Iron Ore with Hydrogen ResearchGate
2021年8月8日 The CO2lean direct reduction of iron ore with hydrogen is considered to offer a high potential to reduce CO2 emissions, and this direct reduction of Fe2O3 powder is investigated in this research2023年9月15日 Iron powder is a powdered form of elemental iron It is commonly used in many industrial and manufacturing applications due to its unique properties and versatility This comprehensive guide will provide an overview of iron powder, its types, characteristics, applications, design considerations, suppliers, installation, operation and maintenanceIron Powder: Characteristics,types,Specifications Additive 2014年3月1日 has significant advantages when processing lowgrade, finely grained iron ores containing ironbearing silicates The most common flotation route used for the beneficiation of iron ores is reverse (PDF) An overview of the beneficiation of iron ores via reverse 2018年3月15日 A 6500 TPD Gold Silver Processing Plant will cost millions of dollars where small mineral pilot plants may cost hundred of thousands and a portable pilot plant may cost only thousandsThe Basics of How Ore Processing and Recovery Plants Work
.jpg)
Traceability in iron ore processing and transports ResearchGate
2012年4月1日 At that point, a traceability system can lead to large costsavings if the residence times and mixing of the product in particle bins can be estimated with high accuracy2019年1月1日 ScienceDirect Available online at sciencedirect Procedia Manufacturing 35 (2019) 242–245 23519789 © 2019 The Authors Published by Elsevier BV Peerreview under responsibility of the organizing committee of SMPM 2019 101016/jpromfg201905034 101016/jpromfg201905034 23519789 © 2019 The AuthorsA review of ironmaking by direct reduction processes: Quality 2017年1月1日 Effective technology for a complex wasteless processing of the iron ores has been designed and includes three main components (plats): comminution plant, briquette plant, pigment plant(PDF) Effective Processing of the Iron Ores ResearchGate2021年4月21日 The BFBOF route employs BF to reduce the iron ore to molten iron and subsequently refined to steel in a BOF As the dominant technology for primary steelmaking, BFBOF route produced 71% of global crude steel production, over 1,279 million tons in 2018 4 Integrated BFBOF operations ( Figure 3 ) include pelleting, sintering, coking, and iron making Lowcarbon production of iron and steel: Technology options, economic
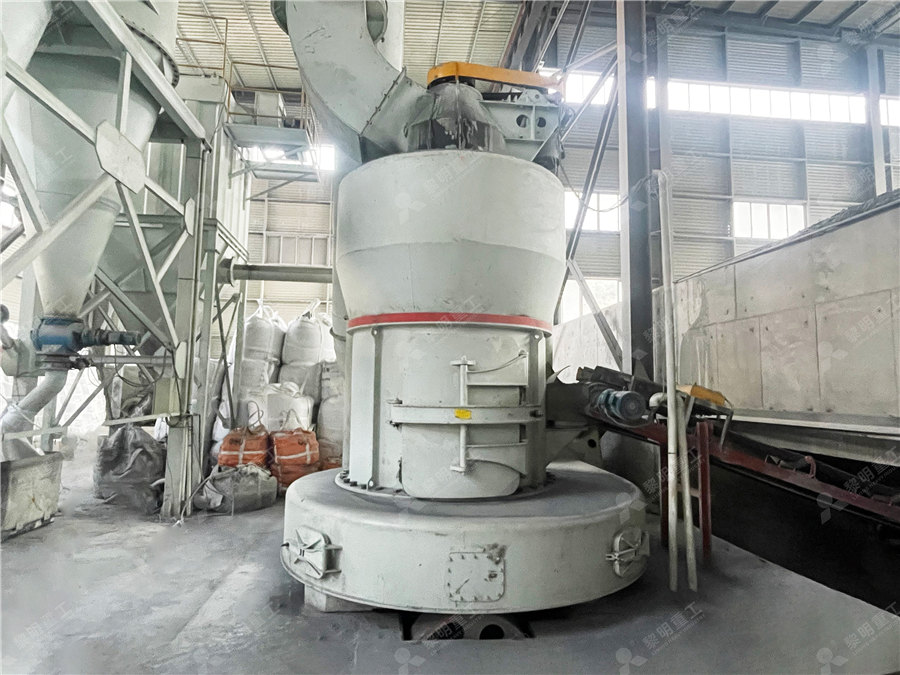
Iron Ore: From Mining to Processing to Dust Control
As of 2020, the largest global iron ore—producing companies were: Vale (Brazil, 300 million tons) The largest exporter of iron ore and the Americas’ largest mining company with a reserve of nearly four billion tons, Vale produces 80% 2023年1月1日 Hence, to meet the growing steel demand, the demand for iron ore is also increasing While, on one side reserves of good quality iron ore are depleting, on the other side the steel companies require better quality of iron ore with lower gangue content due to the addition of higher capacity blast furnaces for higher productivity, lower hot metal cost, and Iron ore beneficiation: an overview ScienceDirect2024年4月1日 Fig 2 illustrates the iron ore beneficiation process, particularly magnetic separation, resulting in the generation of inevitable tailings Due to the characteristics of iron ores and the conditions during beneficiation, it is inevitable that approximately 25–3 tons of IOTs are generated for every 1 ton of iron ore concentrate produced [7]A critical review on metallurgical recovery of iron from iron ore 2021年1月1日 Currently, approximately 14 billion tons per year of iron ore tailing wastes (IOT) are generated, mainly in Australia, Brazil, and China This work describes the characterization and application Iron Ore Tailings: Characterization and Applications
.jpg)
A Study on HighGrade Iron ore Beneficiation to Reduce
2020年5月21日 Iron ore pellets are largely characterized by inherent physical and chemical properties of the ore Alumina and silica play important roles in determining the productivity of a Blast Furnace On average, one percent increase in iron content improves productivity by 2% and reduces coke consumption by 1% Therefore higher iron ore feed content to blast furnace is Rio Tinto Iron Ore We are one of the world’s leading producers of iron ore Our iron ore operations in the Pilbara comprise a worldclass, integrated network of 17 iron ore mines, 4 independent port terminals, a 1,900kilometre rail network and related infrastructure We produce these mainstream iron ore products in Western Australia, including Pilbara Blend, the world's Iron Ore Rio Tinto2020年8月21日 Manganese is considered a relatively rare metal as concentrations of it in ore of commercial importance are geographically limited In nature, manganese is found in the form of oxides, carbonates, and silicates Manganese ores are complex in the sense that they not only consist of a complex oxide mineral assemblage but these minerals are also very finely inter From Ore Body to High Temperature Processing of Complex OresIron Ore Processing, General 1 Introduction Iron is the world’s most commonly used metal–steel, of which iron ore is the key ingredient, representing almost 95% of all metal used per year It is used primarily in structural engineering applications and in maritime purposes, automobiles, and general industrial applications (machinery)Iron Ore Processing, General
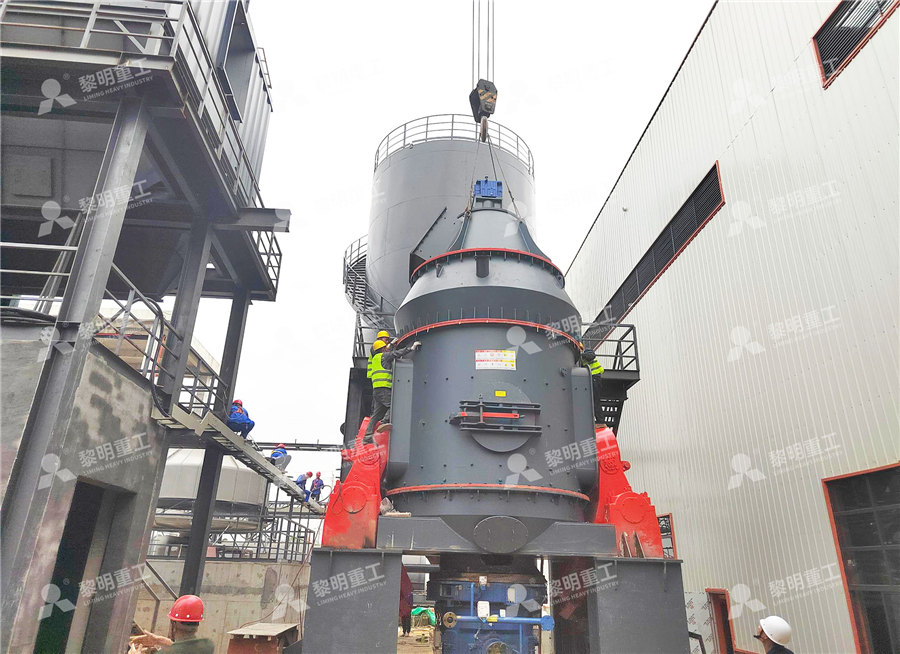
How Metal Powder Is Made: Step 1 of the Powder Metallurgy
Choose a powder metal material Solidstate reduction is an old process but can require up to 3 days in a kiln to fully reduce the iron ore to iron It requires ore of relatively high purity to get a desirable final product Our internal systems have been inspected for reliability and cost effectiveness, and received the seal of approval