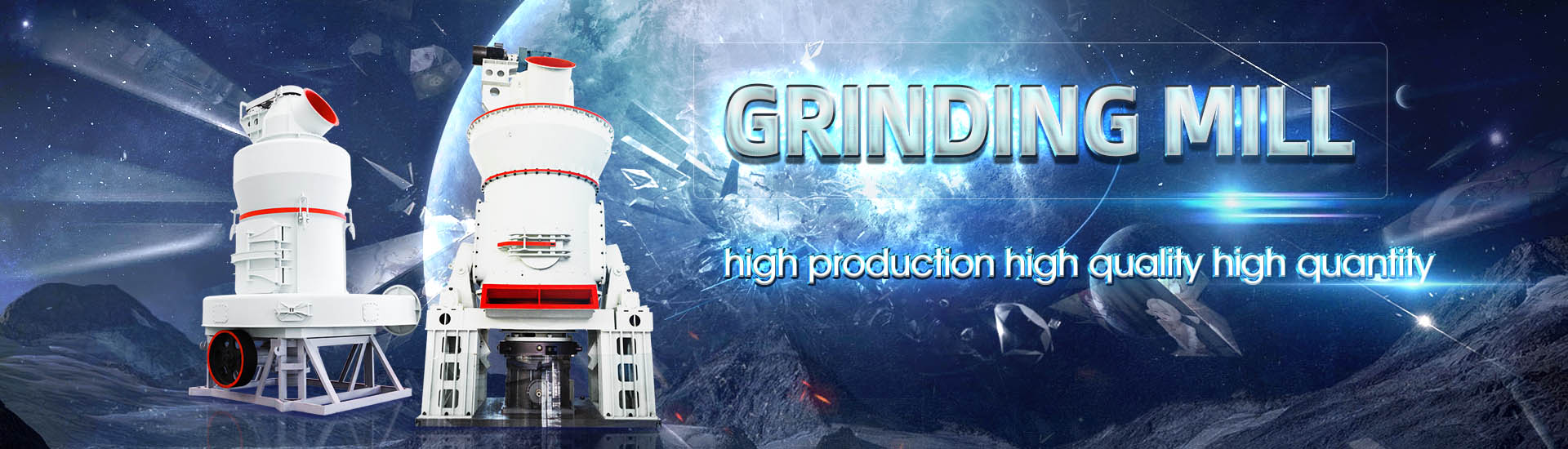
What is the use of cement grinding mill
.jpg)
Everything you need to know about clinker/cement
2018年9月9日 Normally, grinding aids are added in a 15% concentrated solution (1:7 grinding aid to water – helps the dispersal of grinding aid in mill), at Ball mills with high efficiency separators have been used for cement grinding in cement plants all these years Ball mill is a cylinder rotating at about 7080% of critical speed on two trunnions in Cement Grinding Cement Plant OptimizationCement milling is usually carried out using ball mills with two or more separate chambers containing different sizes of grinding media (steel balls) Grinding clinker requires a lot of energy How easy a particular clinker is to grind Cement MillingGrinding in cement manufacturing typically involves breaking down clinker nodules and other raw materials into finer particles This process can be accomplished through various types of mills Grinding in Cement Manufacturing: Key Process, Types of Mills,
.jpg)
The cement mill
Cement manufacturing brief description of a cement mill Cement clinker is usually ground using a ball mill This is essentially a large rotating drum containing grinding media normally steel balls As the drum rotates, the 2017年5月19日 The mill incorporates all the mechanisms based on practical grinding theory to ensure highefficiency such as optimally contoured rollers and matching grinding track section, ensuringOverview of cement grinding: fundamentals, additives, All grinding work is done in the tube mill and the setup is: Tube Mill with Pregrinding Unit Part of the grinding work is done in a pregrinding unit, which can be: Depending on the selected CEMENT GRINDING SYSTEMS INFINITY FOR CEMENT EQUIPMENT2021年1月1日 Vertical roller mill has proved to be a popular choice for finished cement grinding over all other machineries due to advantages like low power consumption, higher capacity, Review on vertical roller mill in cement industry its performance
.jpg)
The Cement Plant Operations Handbook International Cement
Cement milling Finish milling is the grinding together of clinker with some 35 per cent gypsum, natural or synthetic, for set control, and quite often other components:The milling process involves the use of a ball mill, a large rotating drum that grinds the clinker and other additives to produce cement powder Importance of Cement Milling Cement milling is a crucial step in cement production that significantly impacts the final product’s qualityWhat is the Importance of Cement Milling ball mills supplierThe vertical roller mill (VRM) is a type of grinding machine for raw material processing and cement grinding in the cement manufacturing processIn recent years, the VRM cement mill has been equipped in more and more cement Vertical Roller Mill Operation in Cement Plant2023年8月23日 A cement mill is a fundamental component of the cement manufacturing process, playing a vital role in breaking down and grinding cement clinker into fine powder This finely ground powder, when mixed with other What Are the Parts of a Cement Mills? Cement Ball
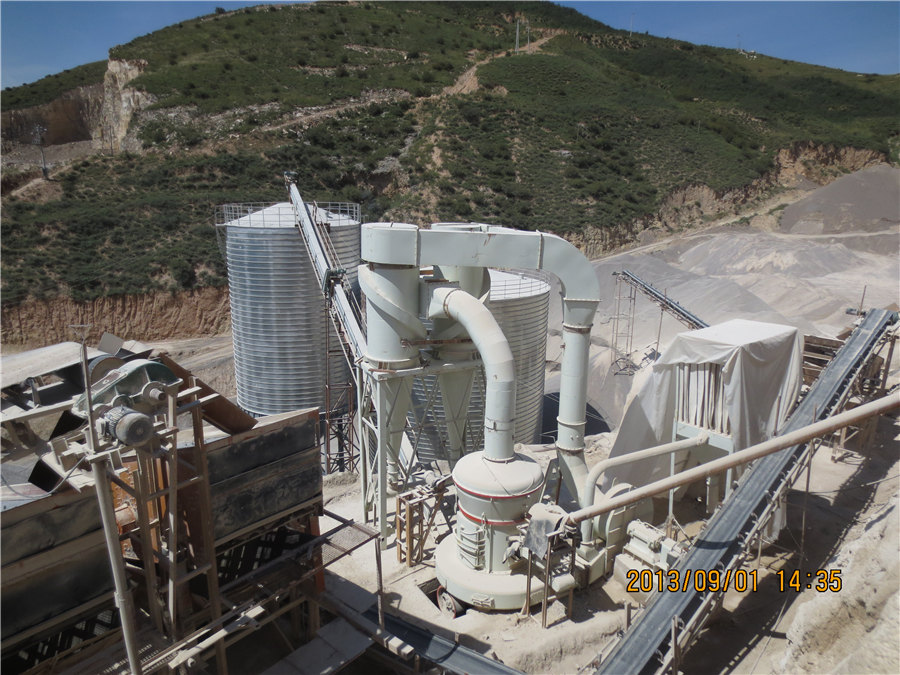
The cement mill
Cement manufacturing brief description of a cement mill Cement clinker is usually ground using a ball mill This is essentially a large rotating drum containing grinding media normally steel balls As the drum rotates, the motion of the balls crushes the clinker The drum rotates approximately once every couple of seconds2023年10月19日 Ball Mill: In some cement plants, a ball mill is used to grind clinker into a fine powder It relies on the use of steel balls to crush and grind the clinker Ball mills are often used for grinding cement clinker into a fine powder before it is Clinker Grinding Techniques in Cement Manufacturing JM acts as a grinding aid and helps stabilise the grinding bed in the mill However, it also presents the risk of prehydration This is where the use of vertical mills for slag grinding offers a further benefit as the mill not only grinds the material but also dries it in the process The normallymoist slag, with an eight per cent water content,SEPARATE OR INTERGRINDING? Loesche2023年11月6日 Grinding aids (GAs) are polar chemicals introduced in cement mills in either liquid or powder form to improve on mill grindability efficiency(PDF) Review of the Effect of Grinding Aids and Admixtures on the

Clinker grinding technology in cement manufacturing
2019年1月3日 Clinker grinding technology is the most energyintensive process in cement manufacturing Traditionally, it was treated as "low on technology" and "high on energy" as grinding circuits use more than 60 per cent of total energy consumed and account for most of the manufacturing cost Since the increasing energy cost started burning the benefits significantly, Cement milling is the process of grinding raw materials (typically limestone, clay, and silica) into a fine powder that can be used to create cement The process involves feeding the raw materials into a cement ball mill or vertical roller mill , where they are ground into a fine powderWhat is Cement Milling? ball mills supplierCement milling is usually carried out using ball mills with two or more separate chambers containing different sizes of grinding media (steel balls) Grinding clinker requires a lot of energy How easy a particular clinker is to grind ("grindability") is not always easy to predict, but large clusters of belite due to coarse silica in the feed are difficult to grindCement Milling2016年7月13日 The use of a good Cement clinker grinding aid can be vital in today's increasing material demands (Kukolev, 1973)1 the use of silicones in the ball mill grinding of quartz (Gilbert, 1962); and the use of acetone, carbon tetrachloride, benzene, and nitromethane in the vibratory mill grinding of glass, marble, and quartz Cement Clinker Grinding Aids 911Metallurgist
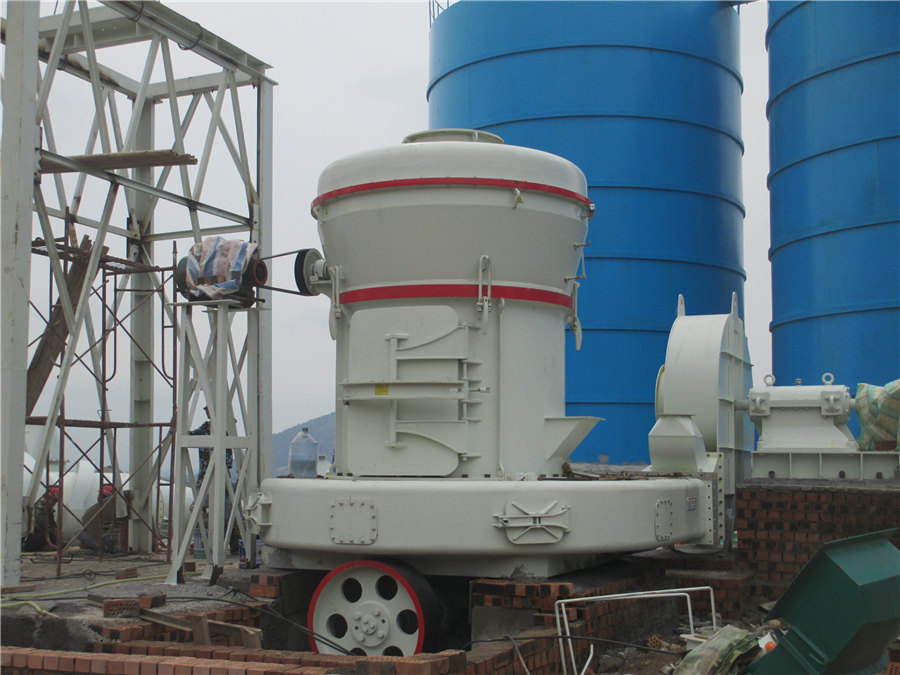
Improvements in New Existing Cement Grinding
o Generally 2/3 of the electricity consumed is used in the grinding of raw materials, fuels finished cement; o Finished grinding may consume 25 – 50 kWh/t cement, depending on the feed material grindability, additives used, 2016年10月5日 In this chapter an introduction of widely applied energyefficient grinding technologies in cement grinding and description of the operating principles of the related equip‐ ments and comparisons over each other in EnergyEfficient Technologies in Cement GrindingA mill is a device, often a structure, machine or kitchen appliance, that breaks solid materials into smaller pieces by grinding, crushing, or cutting Such comminution is an important unit operation in many processesThere are many different types of mills and many types of materials processed in them Historically mills were powered by hand or by animals (eg, via a hand crank), Mill (grinding) Wikipedia2024年11月23日 Cement Extraction, Processing, Manufacturing: Raw materials employed in the manufacture of cement are extracted by quarrying in the case of hard rocks such as limestones, slates, and some shales, with the aid of blasting when necessary Some deposits are mined by underground methods Softer rocks such as chalk and clay can be dug directly by Cement Extraction, Processing, Manufacturing Britannica
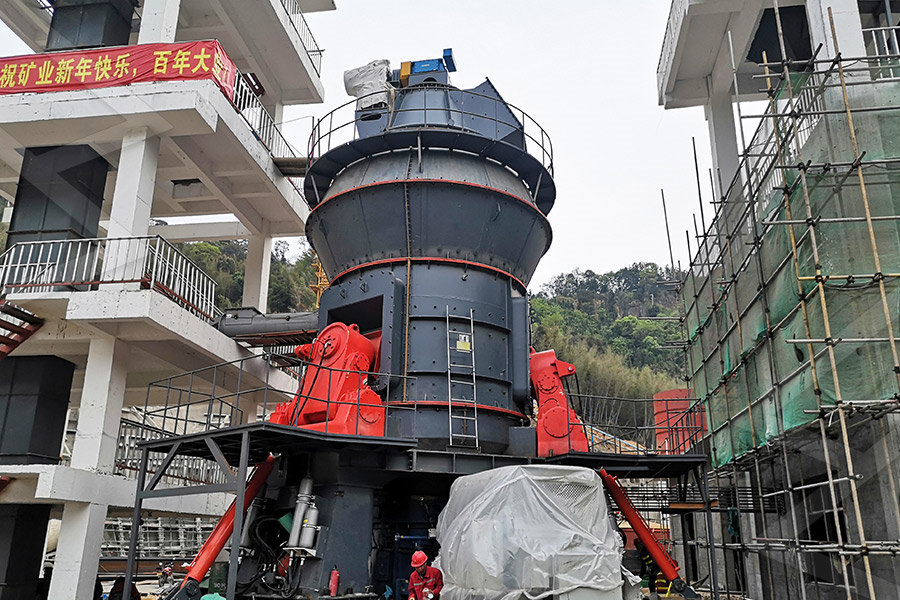
What Are the Different Types of Liners in Cement Mill
Increased Grinding Efficiency The use of different types of liners in cement mills can increase grinding efficiency by optimizing the grinding process For example, diaphragm liners are designed to allow the material to pass through the diaphragm while retaining the grinding media, which can improve grinding efficiency Extended Lifespan of 2024年7月12日 A ball mill and a tumbling mill are both types of grinding mills used to reduce material size We mainly use a ball mill for mixing and grinding processes In contrast, we generally use a tumbling mill for finer material reduction What are the balls? Ball mills grind materials into an extremely fine formWhat Is a Ball Mill and How Does It Work? Certified MTP BlogThe springloaded roller grinding mill for grinding coal was intro duced by Loesche in the 1920’s Since the end of the 1930’s Loesche mills have also been used for grinding cement raw material The biggest breakthrough in this field of application took place in the 1960’s Soon after this the cement industry expressed the desire to2 µm 5 µm Loesche6 Cement Production Technology –Cement Grinding –Mechanical Design and Function of Separator Separators –General Classification of Separating Principles •according to flow direction relative to particle track •according to kind of separating field separation by gravitational force separation by centrifugal forceCement Grinding myPolysiusService
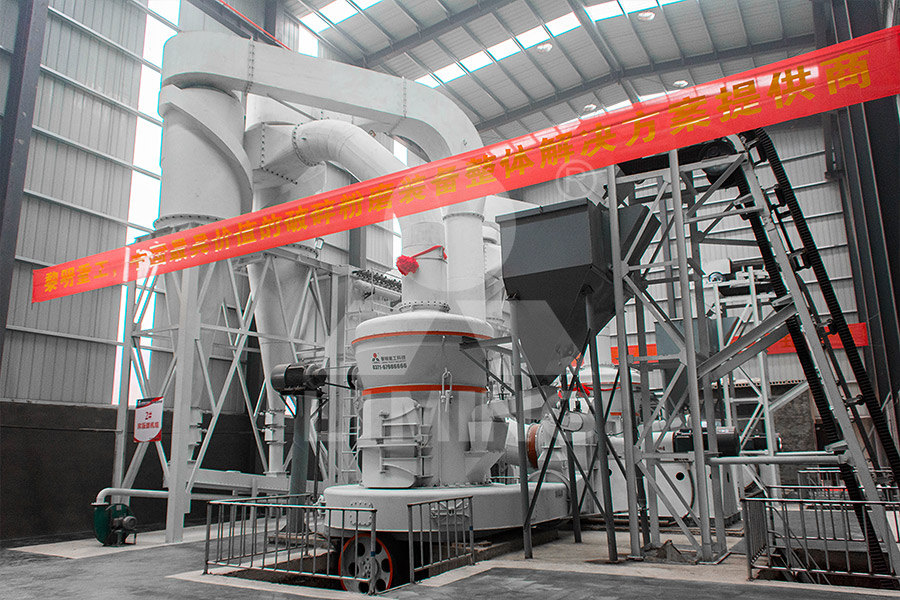
Ball Mill In Cement Plant Cement Ball Mill AGICO Cement
The opencircuit grinding system of the ball mill is shown as follows: materials (including clinker, gypsum, mixed materials, etc) mixed according to a certain proportion will be directly stored in the steel silo as finished cement products after being ground by the ball millClinker, Gypsum and other desired additives are fed to the ball mill in specific proportions based on the quality requirement Feed material is ground in the ball mill, discharged and fed to a classifier with the help of a bucket elevator for Optimization of Cement Grinding Operation in Ball 2024年8月8日 Unlock the secrets to ball mill efficiency with our comprehensive guide on choosing the right grinding media Learn how material composition, size, shape, This makes them especially suitable for heavyduty milling tasks in Ball Mill Success: A StepbyStep Guide to Choosing 2012年6月1日 approach is most frequently used in ball mill grinding circuits Mill – Cement and Concrete Research, V ol 33, 2003, 439445 16 D i n g, B C Modern Predictive ControlGrinding in Ball Mills: Modeling and Process Control
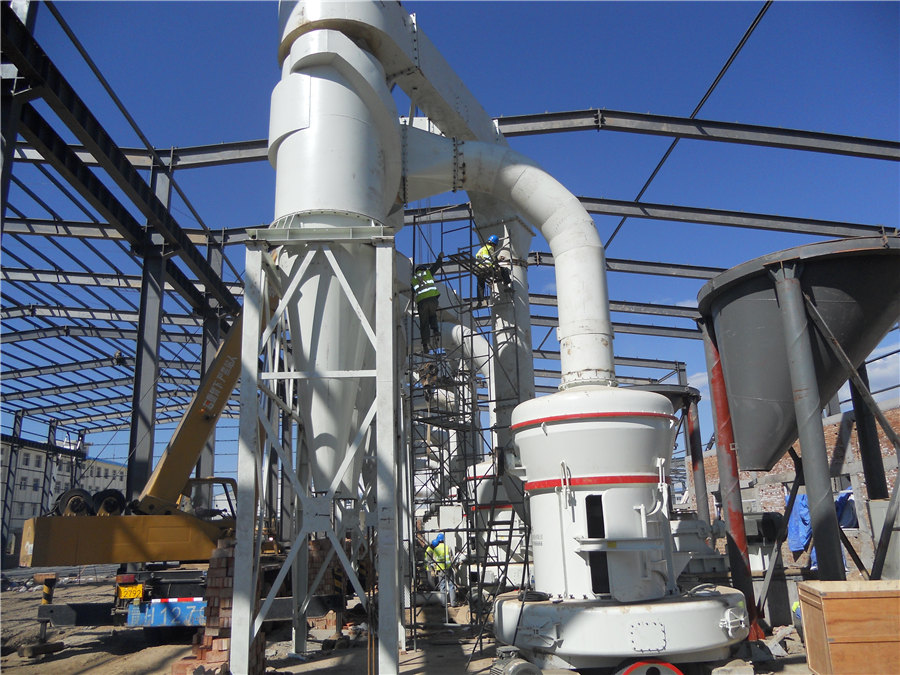
CEMENT GRINDING SYSTEMS INFINITY FOR CEMENT EQUIPMENT
Most commonly used system for cement grinding Not recommended for new installations due to separator design Main Elements Feed bins with weigh feeders; The roller press in front of the tube mill takes over a part of the mill’s grinding work Size reduction in a press is more efficient than in a tube mill2014年6月1日 the use of grinding aids in the cement industry), Communicated by T amás, F product ability to flow in the mill, grinding energy reduction, and improvement on the separator prehensive understanding of grinding aids ResearchGateVertical roller mill (VRM) is a type of grinding machine used to grind materials into extremely fine powder, commonly used in the cement industry VRMs are also used in the power generation and steel industries, among othersApplication of Vertical Roller Mill in Cement Productionincreases production of cement mill To seal air leakage in SKS Separator with uniform air gap increases output of cement mill Proper distribution of grinding media with appropriate sizes also enhanced productivity of cement mill Target To increase the TPH from 190 to 220 TPH (PPC) with maintaining quality parameter ie 8% residue on +45 micronINCREASING OUTPUT OF CEMENT GRINDING IN BALL MILL
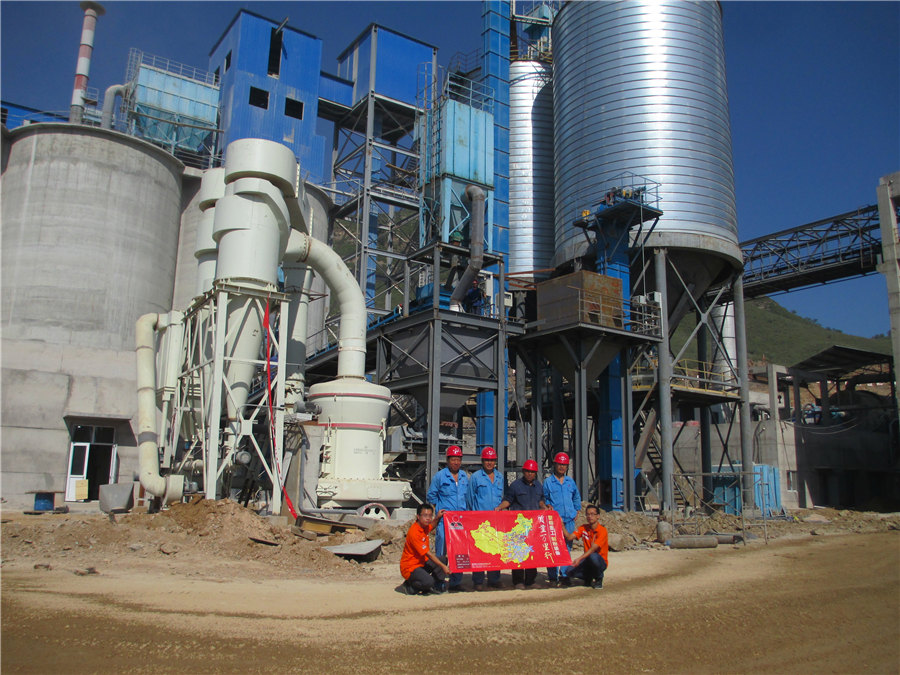
How To Optimize The Operation Of The Cement Mill
2024年1月23日 From the crushing and grinding of raw materials to the final production of cement, our grinding mill products play a crucial role throughout the entire process To better meet the needs of our customers, we have a dedicated technical team capable of providing personalized design solutions for cement plants based on specific requirementsA Vertical Roller Mill (VRM) is an advanced and efficient grinding machine commonly used in the cement industry for grinding raw materials and clinker VRMs have become increasingly popular due to their ability to produce finer products with lower energy consumption compared to traditional ball millsVertical roller mill vs ball mill for cement grinding: Comparison 2023年1月29日 Raw Mill is mainly used to grind raw materials into fine powder, whereas Cement Mill is used for grinding clinker and other additives to form the final cement product The main difference between the two lies in their respective input materials; Raw mill mainly accepts raw materials from the kiln whereas Cement Mill mainly accepts precrushed material from a What Is Cement Milling? Difference Between Raw Mill And Cement MillThe mill may be used wet or dry although wet grinding facilitates the removal of the product (ii) The costs of installation and power are low (iii) The ball mill may be used with an inert atmosphere and therefore can be used for the grinding of explosive materials (iv) The grinding medium is cheap (v)Ball Mill an overview ScienceDirect Topics
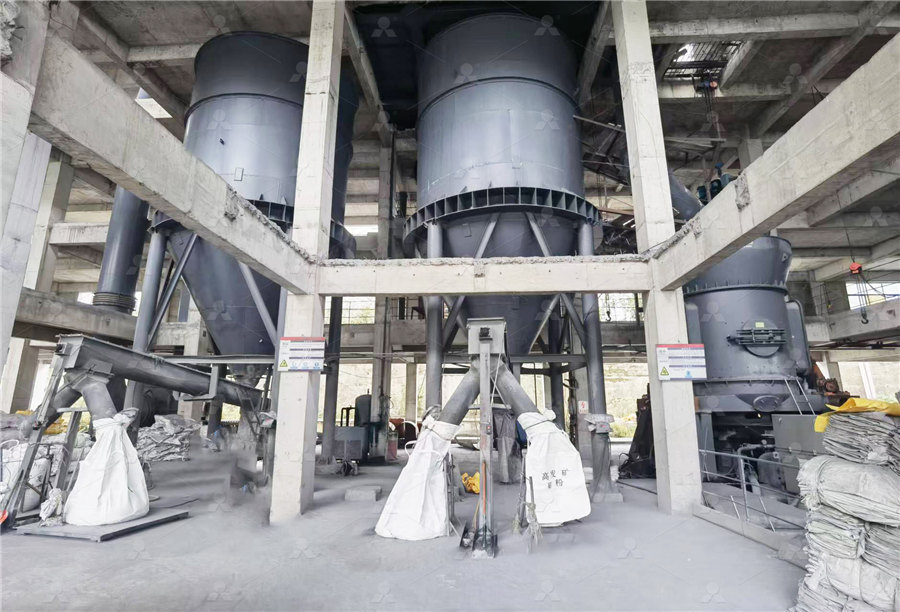
Improvement of cement performances through the use of grinding
Cement Additives Division 1 Improvement of cement performances through the use of grinding aids in vertical roller mill PD’Arcangelo, MMagistri – Mapei SpA, Milan, Italy Abstract Due to the stringent requirement of energy saving, the use of vertical 2018年7月1日 Among the industries, the nonmetallic industry was reported as the third largest energy user and accounted for about 12% of the global energy use [1]Within this portion, cement industry had the majority of the utilization with 85–12% [1], [2]US Energy Information Administration (EIA) [7] named cement industry as the most energy intensive among the Energy and cement quality optimization of a cement grinding circuitGrinding aids are primarily used to reduce energy consumption by increasing grinding efficiency and mill productivity Better dry powder dispersion of the ground cement increases mill productivity and cement fineness for the same energy consumption, and produces improvement in flow, leading to faster unloading and improved storage volume of bulk cement storagePhysical Chemical Mechanisms of Cement Grinding Aids2024年2月23日 The operation of the cement raw mill is a critical step in cement production By grinding the raw materials into a fine powder, these powders can be more easily mixed with other cement ingredients and burn more evenly during the cement clinker process Therefore, the efficient operation of the cement raw mill directly impacts the production efficiency and quality How Does a Raw Mill Work in a Cement Industry
.jpg)
Cement Grinding Plant Overview Cement Grinding Unit AGICO Cement
Cement grinding process The whole workflow of the cement grinding plant is as follows: the cement clinker, gypsum, and mixture in the cement silo are mixed by the belt conveyor in a certain proportion and transported to the cement roller press, cement mill or group of them for grinding2023年11月6日 Grinding aids (GAs), also called grinding additives are introduced in liquid or solid form in the ball mill or vertical cement mills during grinding because of their anticipated merits They can be divided into amines and their salts, polyalcohols, lignosulfonates, fatty acids, and fatty acid salts based on their chemical makeup [ 1 ]Review of the Effect of Grinding Aids and Admixtures on the The use of grinding aids in both open and closed circuit systems will improve the control of the grinding process, increasing the Blaine number (finer product) These advantages usually justify the cost of a grinding aid But some cement manufacturers refuse to use grinding aids for economic reason Locher and von Seebach [5] investigated the V RQI 6HU Design of New Slotted Structured Grinding2024年11月19日 Grinding Mill — We are the foremost Grinding Mill, Continuous Grinding Mill, Open Circuit Grinding Mill, Cement Grinding Plant manufacturer in India and are providing a wide range of these Grinding Mill that are as per the latest standards which makes their use favorable in the different parts of the countryGrinding Mill Continuous Grinding Mill, Open Circuit Grinding Mill
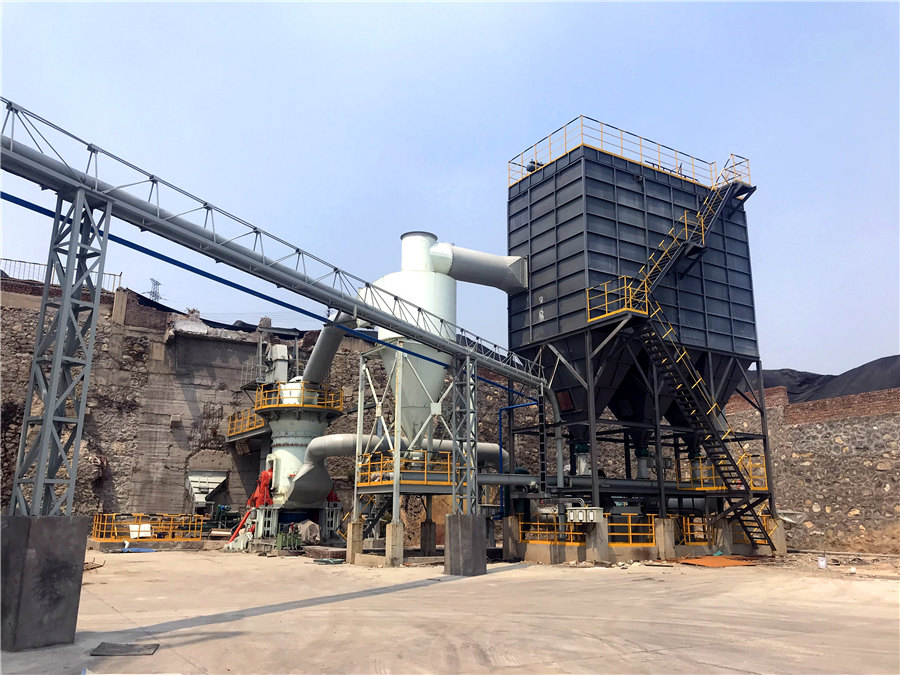
What is a Cement Ball Mill? How to Use It? by cicemech Medium
2022年3月16日 Cement ball mill is a kind of equipment for further fine grinding of materials, with high fineness It is widely used in industry, metallurgy, chemical industry, cement and other industries The