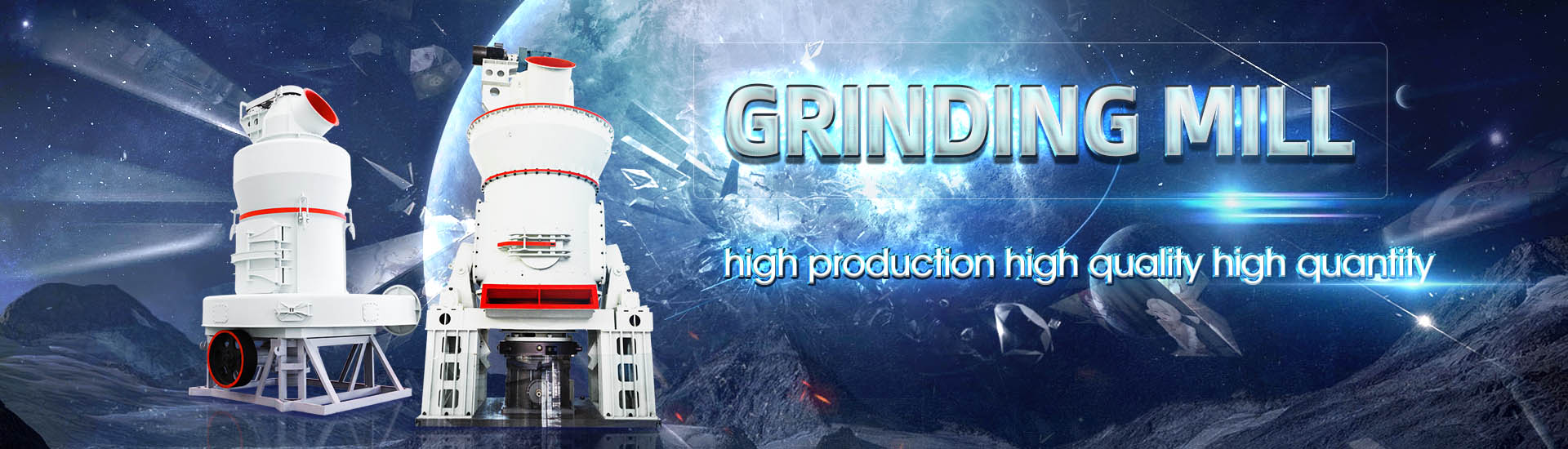
HOME→How much does Midas electrolytic aluminum waste slag grinding mill cost for calcium carbonate grinding mill
How much does Midas electrolytic aluminum waste slag grinding mill cost for calcium carbonate grinding mill
.jpg)
The recycling of carbonrich solid wastes from aluminum
2024年5月23日 16 Million metric tons of spent carbon electrodes modify carbonrich solid wastes from aluminum electrolysis are produced annually, threatening ecosystems by cyanide and fluoride pollution Here, we review carbonrich solid wastes with focus on sources and 2023年4月25日 This article analyzes and summarizes the composition and hazards of the overhaul slag and the current development status of domestic and international electrolytic Research Progress of Electrolytic Aluminum Overhaul Slag Disposal2012年5月30日 Aluminium salt slag is toxic/hazardous waste (production: 200–500 kg/Al tonne) Chemical and mineralogical characteristics are presented Various processes for Al metal Aluminium salt slag characterization and utilization – A review2023年4月13日 Aluminium is produced by electrolysis using alumina (Al2O3) as raw material and cryolite (Na3AlF6) as electrolyte In this HallHéroult process, the energy consumption is A comprehensive review of aluminium electrolysis and the waste
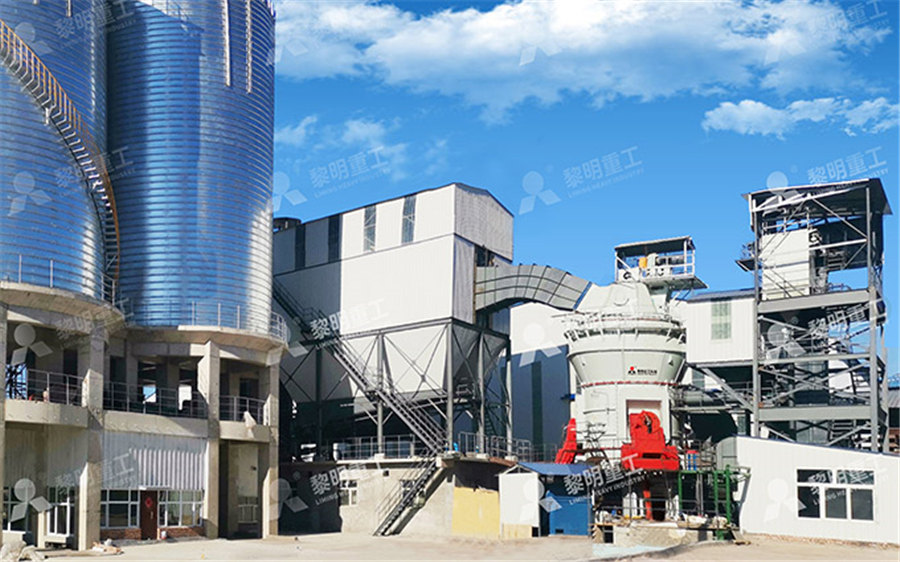
What kind of mill is best for grinding electrolytic aluminum slag
2023年9月22日 To extract lithium from electrolytic aluminum slag, the waste residue must first be dried to reduce its moisture content to less than 5% Then, it is pulverized by an aluminum 2024年2月1日 The electrolytic aluminum industry generates a large amount lithium (Li)containing electrolytic aluminum slag (EAS) annually, and this can result in severe Efficient lithium recovery from electrolytic aluminum slag via an 2021年10月31日 For every 5–15 kg of SCA (Liu et al, 2021) produced per ton of aluminum, its discharge amount exceeded 35,000 tons in 2020 SCA is composed of a large number of highquality carbon materials and highvalue Advances in the Safe Disposal and Comprehensive 2020年8月1日 The current efficiency of the electrolytic experiments is over 94% The purity of aluminum electrodeposited on the cathode is over 99% Large amounts of industrial waste Recovery of aluminum from waste aluminum alloy by low
.jpg)
A solidstate electrolysis process for upcycling aluminium scrap
2022年4月13日 Here we propose a solidstate electrolysis (SSE) process using molten salts for upcycling aluminium scrap The SSE produces aluminium with a purity comparable to that of 2min After which terpenic oil was added and the slurry was stirred for 05min Following this, the air was introduced, and after 05min of aeration, scraping of froth was startedRecovery of carbon and cryolite from spent carbon anode slag ofHCM’s HC1700 vertical pendulum Raymond mill, HLM series manganese carbonate vertical mill and other equipment have a high reputation in manganese ore enterprises all over the world market share, the following two types of electrolytic manganese powder grinding mill equipment will be introduced to youNews How to choose the electrolytic manganese powder grinding mill 2024年6月29日 The dual grinding system effortlessly handles everything from small With no trash service we had to freeze our food waste then take to the waste station $25 fee The Mill has been a life How often do I need to Mill Food Recycler
.jpg)
Recovery of carbon and cryolite from spent carbon anode slag of
2022年10月10日 The comprehensive recovery and utilization of electrolytic aluminum spent carbon anode slag (Hereinafter simplified as “carbon anode slag”) are therefore necessary Flotation is a physical separation method used to separate particles by using the difference in surface property of particles ( Chen et al, 2022 ; Ni et al, 2022 )Taking the slag powder production line with annual output of 200,000 tons as an example, the economic benefit of the grinding plant is analyzed for you:Slag Grinding Plant GGBS Plant Slag Mill, Slag Grinding Mill2023年3月12日 Aluminum has a variety of uses in the building, transportation, electric power, packaging, national security, and hightech industries due to its unique chemical and physical properties []Cryolitealumina molten salt electrolysis is mainly applied in modern industrial aluminum production [2,3]As the aluminum production process continues, a large amount of Recovery of Carbon and Cryolite from Spent Carbon Anode Slag Grinding Mills: Ball Mill Rod Mill Design PartsCommon types of grinding mills include Ball Mills and Rod Mills This includes all rotating mills with heavy grinding media loads This article focuses on ball and rod mills excluding SAG and AG mills Although their concepts are very similar, they are not discussed herePhotographs of a glass ended laboratory ball mill show Grinding Mills 911Metallurgist
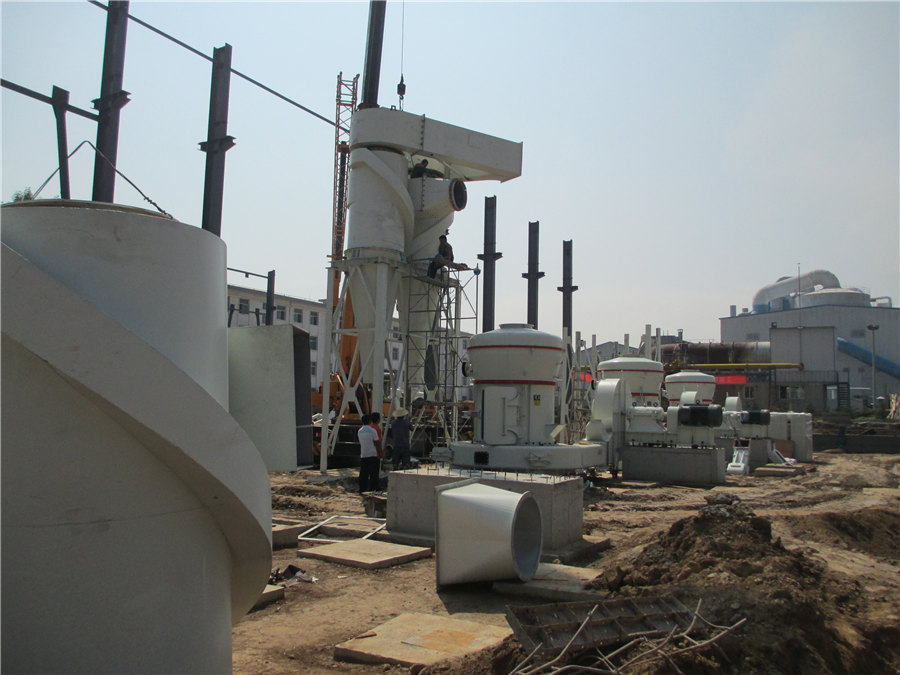
Aluminium dross processing/Brightstar Aluminum Machinery
The aluminum dross skimming from the smelting furnace is called primary aluminum dross, which is graywhite in appearance, mainly composed of a mixture of metallic aluminum and aluminum oxide, and the aluminum content can reach 15%~ 70%, also known as “white aluminum dross”; secondary aluminum dross is the waste after the primary aluminum dross is extracted from 2017年10月24日 Aluminum production is accompanied by production of fluorinecontaining solid waste Every year in the Bratsk Aluminum Plant 40000 tons of this waste is produced with a high fluorine and carbon content Technology for producing calcium fluoride is developed in order to regenerate fluorine Optimum conditions are studied and determined for leaching fluorine from Technology for Preparing Calcium Fluoride from Aluminum Production Waste2021年10月1日 Currently, the HallHeroult method is adopted for industrial aluminum smelting, with alumina as the raw material and cryolite as the solvent (Tarcy et al, 2011)According to statistics, China's primary aluminum output was 3708 million tons in 2020, of which the capacity of using domestic bauxite to produce alumina accounts for approximately 47% (National A novel approach for lithium recovery from waste lithium 2017年1月17日 Other process activities, such as spraying the ore with water for dust control or the fact that runofmine ore moisture is approximately 2%5% are not generally considered (Bleiwas, 2012a)Breaking down energy consumption in industrial
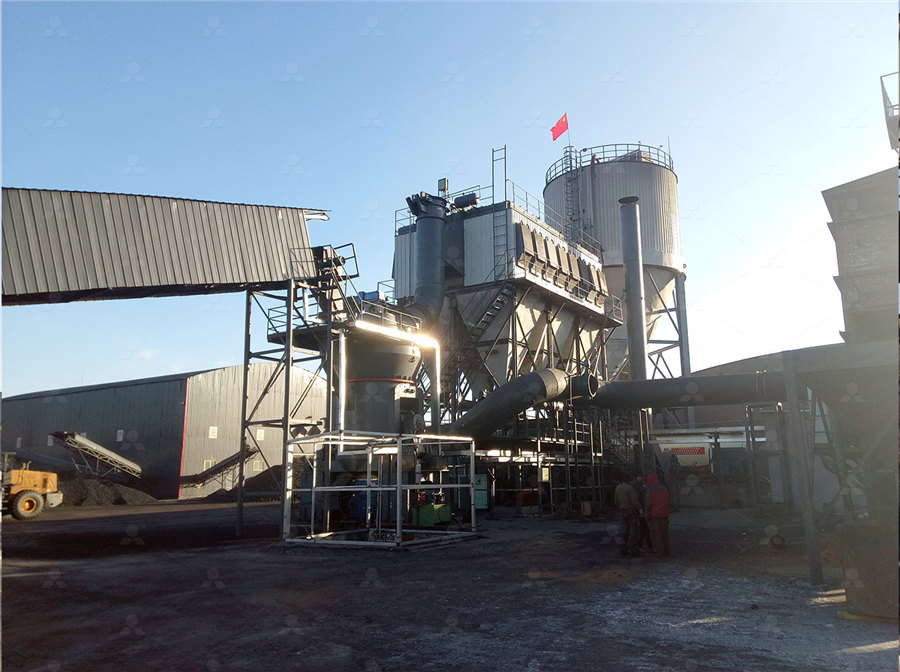
What is the grinding mill for grinding slag? – gkmill
2021年4月19日 It is an excellent equipment for grinding water slag, steel slag and other solid wasteWe have been deeply engaged in the grinding market for nearly 50 years, with sufficient experience, many cases, more mature team and high evaluation from customers2018年10月1日 For instance, the production of alumina with a purity of more than 97% from a solid waste cake produced at an aluminum factory in Egypt by dissolving the waste in sodium hydroxide solution, precipitating aluminum hydroxide from sodium aluminate solution by CO 2 injection, followed by heat treatment at 600–1000 °C to produce gamma and alphaalumina Hazardous aluminum dross characterization and recycling 2022年1月10日 Selective comminution and grinding mechanisms of spent carbon anode from aluminum electrolysis using ball and rod mills January 2022 Physicochemical Problems of Mineral Processing 58(3):Selective comminution and grinding mechanisms of spent carbon 2016年2月21日 Introduction Calcium carbonate is the most commonly used filler material in paper making (Naydowski et al, 2001)Ground calcium carbonate (GCC) is manufactured by grinding high quality limestone to very small sizes and is mostly used as a pigment, included as an externally applied coating in coated papersPerformance of Separation Processes for Precipitated Calcium Carbonate
.jpg)
HIGmill high intensity grinding mill Metso
The grinding chamber is filled up to 70% with inert ceramic grinding media beads Rotors stir the charge and grinding takes place between beads by attrition The number of rotors (grinding stages) depends on the application and can be as high as 2012年12月31日 The main mineral components of waste cathode carbon include sodium fluoride, cryolite, calcium fluoride, silicate minerals and so on, therein the fluorine content is about 986%, and the content Study on Harmless and Resources Recovery Treatment Technology of Waste Grinding of cement clinker and granulated blast furnace slag in roller grinding mills (vertical airswept grinding mills) is a technology introduced by Loesche The first use of a Loesche mill, with a grinding track diameter of only 11 metres, was used as long ago as 1935 However, the breakthrough in grinding this type of material on the vertical2 µm 5 µm Loesche2022年12月12日 Based on the research on bulk solid waste contact molding technology by our team [49], the comprehensive performance of pressed bricks with different ratios of aluminum ash and calcium carbide slag was investigated, the ratios of aluminum ash and calcium carbide slag are 9:1 ∼ 1:9 and pure aluminum ash and calcium carbide slag, the pressing pressure is 300 Comprehensive performance study of aluminum ash and calcium
.jpg)
Research on the Coprocessing of Mixed Electrolytic Aluminum Waste
This study collected electrolytic aluminum waste cathodes, anodes, limestone and other materials After grinding the materials with an electric mill, 50 grams of electrolytic aluminum waste samples were sieved to 0075 mm The sample was then dried for 2 hours at a temperature of 110 °C in the dryer, then stored in a2017年7月9日 Two hydrated phases of calcium carbonate, monohydrate (CaCO 3 ⋅H 2 O), and hexahydrate of calcium carbonates (CaCO 3 ⋅6H 2 O) are also possible forms of hydrated calcium carbonates Recently, it was revealed that Frontiers Calcium Carbonate Precipitation for CO2 This study collected electrolytic aluminum waste cathodes, anodes, limestone and other materials After grinding the materials with an electric mill, 50 grams of electrolytic aluminum waste samples were sieved to 0075 mm The sample was then dried for 2 hours at a temperature of 110 °C in the dryer, then stored in aResearch on the Coprocessing of Mixed Electrolytic Aluminum Waste 2016年3月21日 Pulp Densities Pulp densities indicate by means of a tabulation the percentages of solids (or liquidtosolid ratio) in a sample of pulp This figure is valuable in two ways—directly, because for each unit process and operation in Common Basic Formulas for Mineral Processing
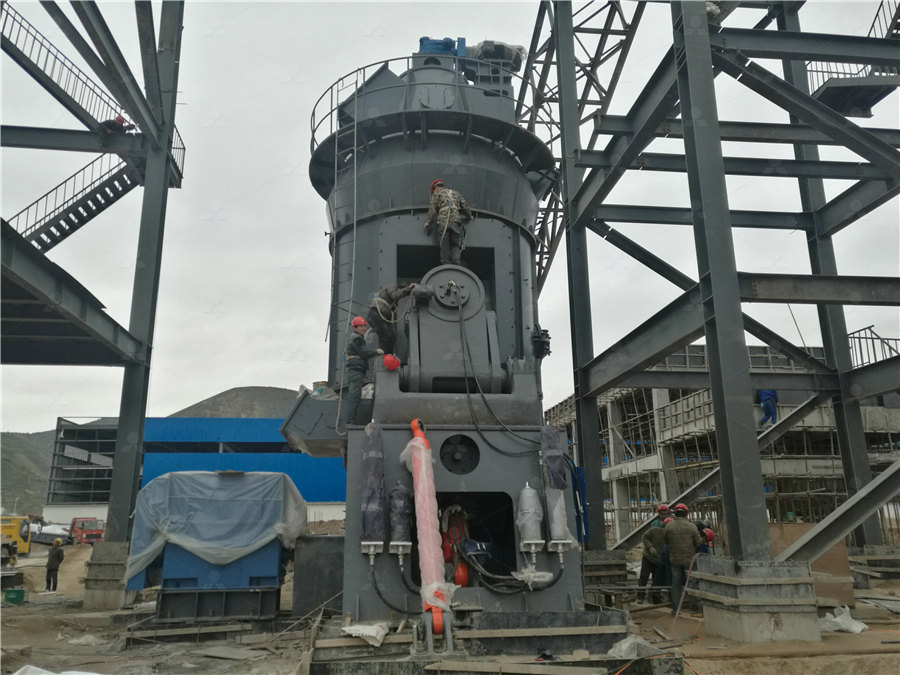
(PDF) Recovery of Carbon and Cryolite from Spent Carbon Anode Slag
2023年3月12日 3D response surface plot of γ −0074 mm as a function of the interaction: (a) grinding time × grinding concentration, 25 cm ball diameter; (b) grinding time × ball diameter, 60% grinding 2022年5月1日 Most widely used acidic agents could react with these carbonates and release CO2 before they were recarbonated After the leaching step, alkaline reagents (eg, NH4OH, NaOH) are introduced to Preparation of calcium carbonate nanoparticles from waste carbide slag 2012年5月30日 Aluminium salt slag is toxic/hazardous waste (production: 200–500 kg/Al tonne) Chemical and mineralogical characteristics are presented Various processes for Al metal recovery and recycling of KCl/NaCl to smelting process are reported Preparation of value added products from the final NMR is discussedAluminium salt slag characterization and utilization – A review2023年10月1日 Cryolitealumina (Na 3 AlF 6Al 2 O 3) molten salt electrolysis is the only modern method for the industrial production of metallic aluminum (Ishak et al, 2017)Under the influence of direct current, Al 2 O 3 dissolved in the molten salt is reduced to monolithic aluminum at the cathode (Haraldsson and Johansson, 2020)As the blood of the electrolytic cell, the electrolyte Efficient extraction and recovery of lithium from waste aluminum
.jpg)
How grinding mill design changed over the last 30 years
2020年6月3日 Effect of OEM mergers on grinding mill design A wave of grinding mill OEM mergers took place in the 70’s and 80’s During those years, only a handful of OEM’s were competing with one another, and no more than two or three could bid 2022年2月19日 Characterization of the Material The contents (wt%) of the main elements of rareearth molten salt slag were determined to be Nd 2 O 3 2827%, Pr 2 O 3 841%, SiO 2 1367%, Fe 2 O 3 1162%, MgO 894%, and F 1099% The Xray diffraction (XRD) pattern of rareearth molten salt slag shows neodymium fluoride (NdF 3) and neodymium oxyfluoride Recovery of RareEarth Elements from Molten Salt Electrolytic Slag 2023年12月1日 Tong et al (2023) mixed aluminum sulfate and calcium oxide to treat the rare earth molten salt electrolytic slag and achieved the expected effect, indicating that the reaction with fluoride in rare earth molten salt electrolytic slag after mixed roasting is feasible, which is consistent with the thermodynamic calculation results of the reaction of coroasting aluminum Review of efficient recycling and resource utilization for rare earth 2020年4月3日 Hcmilling (Guilin Hongcheng) New Environmentally Friendly MillHC Vertical Grinding Mill Max feeding size: ≤30mm Capacity: 625t/h Fineness: 0180038mmHow Much Is the Vertical Slag Grinding Mill
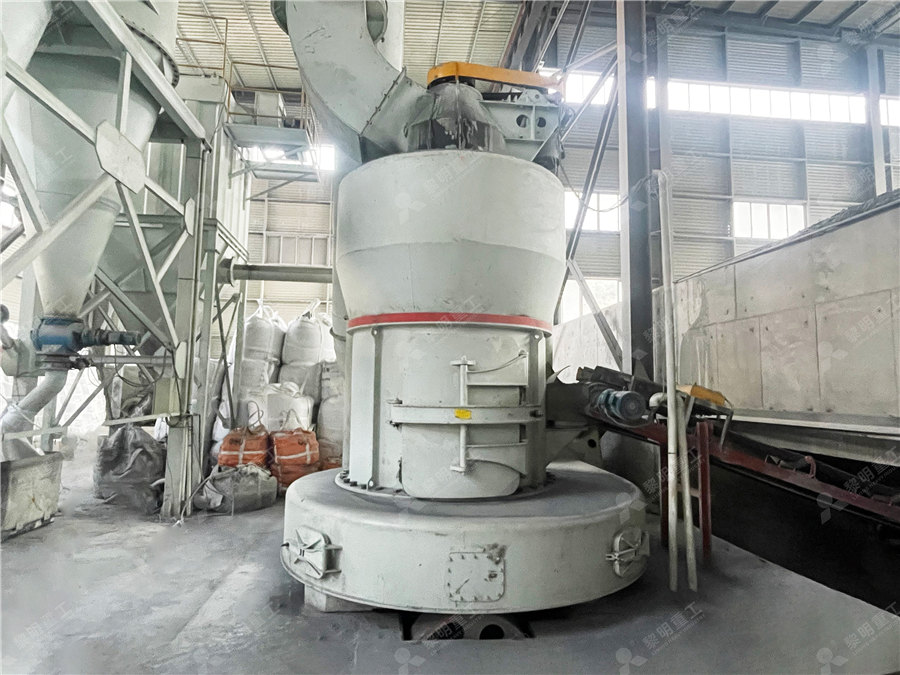
Clean Process for Selective Recovery of Lithium
2023年9月1日 Lithium (Li)bearing aluminum electrolyte slag is an inevitable byproduct of the aluminum industry, and improper disposal or stacking it may lead to potential environmental hazards This study employed hydrometallurgical 2016年5月16日 The average rate of generation of LD slag is approximately 150–180 kg per ton of crude steel in India []Researchers also found that this rate of production of LD slag somtimes reaches a high of 200 kg per ton of crude Sustainable Approaches for LD Slag Waste 2024年2月1日 Aluminum metal was produced using the cryolitealumina molten salt electrolysis method (Ishak et al, 2017) A large amount electrolytic aluminum slag (EAS) is generated during the electrolysis process, as the falling of carbon particles on the anode into the electrolysis cells and the accumulation of lithium fluorine result in energy consumption and electrolyte scrapping Efficient lithium recovery from electrolytic aluminum slag via an ECG combines abrasive grinding and electrochemical erosion producing a more efficient, costeffective, and burrfree part Be sure to read our latest electrochemical grinding solutions by visiting our Case Studies page Review frequently asked questions below, our electrochemical grinding machine offerings, as well as our Customer Care SolutionsFAQs About Electrochemical Grinding (ECG) Glebar
.jpg)
What’s The Use Of Aluminum Plant Waste? The Price Of Aluminum Waste
As a byproduct of production, aluminum plant waste residue is also increasing The total loss of aluminum content in the waste residue of aluminum plant in the production process is 112% HCMilling (Gulin Hong Cheng) can provide you with the best quality aluminum plant slag grinding mill machine and service2019年1月1日 All content in this area was uploaded by Somnath Kumar on Jan 29, 2019Recent trends in slag management utilization in the steel The iron oxides are reduced in the upper region of the furnace In the middle region, limestone (calcium carbonate) decomposes, and the resulting calcium oxide combines with silica and silicates in the ore to form slag The slag is mostly calcium silicate and contains most of the commercially unimportant components of the ore: \[\ce{CaO}(s)+\ce 233: Metallurgy of Iron and Steel Chemistry LibreTextsWANG Gongxun;LI Zhi;ZHU Mingqiao Preparation of Recycled Ceramic Tiles by Using Electrolytic Manganese SlagWaste Ceramic Grinding Fine Powder[J] BULLETIN OF THE CHINESE CERAMIC SOCIETY, 2013, 32(8): 14961501Preparation of Recycled Ceramic Tiles by Using Electrolytic