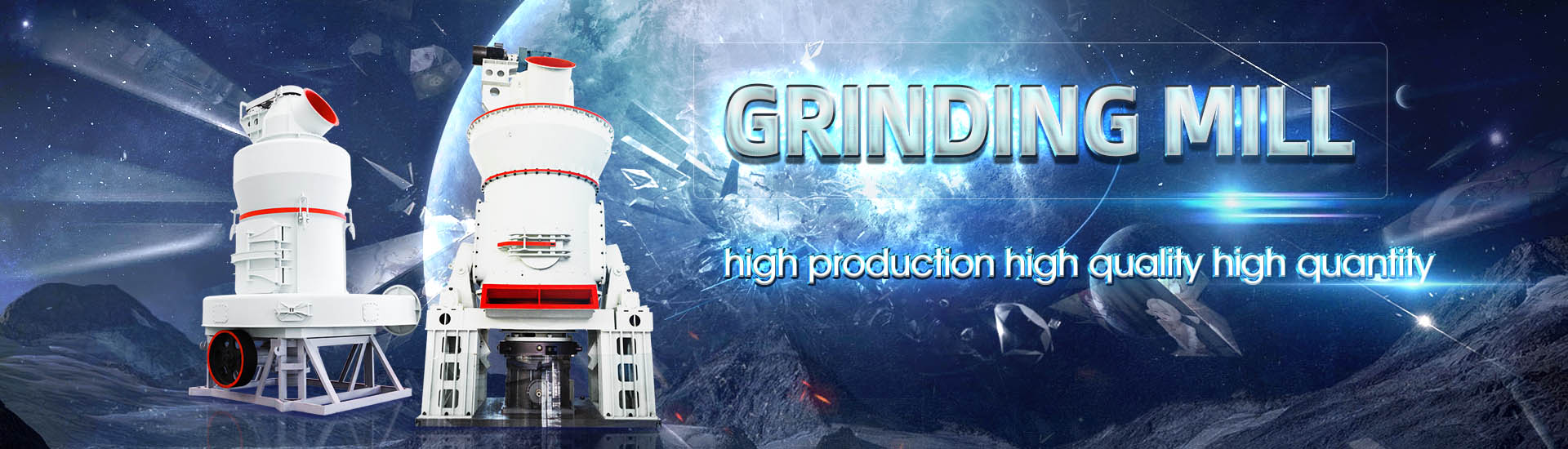
Raw coal vertical ore steel plant
.jpg)
Prospects for Coalbased Direct Reduction Process KOBELCO
Kobe Steel has developed coalbased direct reduction (DR) technologies, the FASTMET, FASTMELT and ITmk3 processes, which reduce carbon composite agglomerates (pellets or 2016年3月30日 Depleting resources of coking coal, the world over, is posing a threat to the conventional (blast furnace [BF]–basic oxygen furnace [BOF]) route of iron and steelmaking During the last four(PDF) i) Direct Reduced Iron: Production ResearchGate2024年8月5日 To compare green steel production, which will consume electrical energy, to the incumbent blast furnace method, which consumes carbon in the form of coked coal, we can Economics of Electrowinning Iron from Ore for Green Steel Making Steel Coking plant To make steel in a blast furnace, coal must first be turned into coke Coke has a dual role in the steelmaking process First, it provides the heat needed to melt the Raw materials Coking plant ArcelorMittal
.jpg)
TATA STEEL
Raw materials The making of steel depends on natural resources such as iron ore, coal and other minerals, which constitute our key raw materials Our steelmaking operations at Jamshedpur and Kalinganagar secure 100% of 2013年1月1日 This chapter discusses the role of coal in iron and steel metallurgy The chapter first gives information about routes for steel manufacture, current levels of steel production and Coal use in iron and steel metallurgy ScienceDirectsteel plants but also in the highly disaggregated sponge iron sector, which is dominated by smallsized coalbased direct reduction of iron (DRI)based plants India is one of the unique ENERGYEFFICIENT TECHNOLOGY OPTIONS FOR DIRECT Coal is a key raw material in steel production Coal is primarily used as a solid fuel to produce electricity and heat through combustion Coke, made by carburising coal (ie heating in the FACT SHEET Steel and raw materials
.jpg)
Global iron and steel plant CO2 emissions and carbonneutrality
2023年9月20日 Iron and steel plants are classified into 17 types by iron and steel processing routes and grouped according to size into three classes based on CO 2 emissions in 2019 The coke is a porous, hard black rock of concentrated carbon (contains 90 to 93 percent carbon), which has some ash and sulfur but compared to raw coal is very strong The strong pieces of coke with a high energy value provide Steel Production American Iron and Steel Institute2024年3月17日 Raw Materials and Their Role in Steel Production Raw materials are the cornerstone on which the steelmaking process is built They are pivotal in defining the quality and characteristics of the finished steel The A Visual Guide: Steel Making Process Chart Cabaro augmenting India’s future steel production to meet its growing demand Like its global compatriots, the steel industry in India is facing the challenges of reducing carbon emissions and improving energy as well as resource efficiency Both coal and gasbased DRI plants are operational in India However, the share of coalbasedENERGYEFFICIENT TECHNOLOGY OPTIONS FOR DIRECT
.jpg)
Vertical coal mills in steel plant casting: Efficient pulverization for
The Role of Vertical Coal Mills in Steel Plant Casting: Vertical coal mills are primarily used for pulverizing coal before it is injected into the blast furnace or used in other processes within the steel plant Here's how they function in the casting process: 1 Coal Pulverization: The mill takes raw coal and grinds it into a fine powder Vertical raw mill is one kind of raw mill, generally used to grind bulk, granular, and powder raw materials into required cement raw meal in the cement manufacturing plantVertical raw mill is an ideal grinding mill that crushing, drying, grinding, grading transfer set in one It can be widely used in cement, electric power, metallurgy, chemical industry, nonmetallic ore, and other industriesVertical raw mill Cement Plant2018年3月22日 Find Steel Plant Iron Ore Mine stock images in HD and millions of other royaltyfree stock photos, Part of the abandoned coal and steel production plant in Landschaftspark DuisburgNord The landscape park is a public park around a disused iron and steel works in Duisburg, Germany VerticalSteel Plant Iron Ore Mine royaltyfree images Shutterstock2024年4月26日 The ore is then extracted and transported to the processing plant b Underground Mining: Underground mining is employed when the iron ore deposit is located at significant depths Iron ore processing is a complex and vital process that transforms raw iron ore into usable steel From exploration and extraction to grinding, Iron Ore Processing: From Extraction to Manufacturing
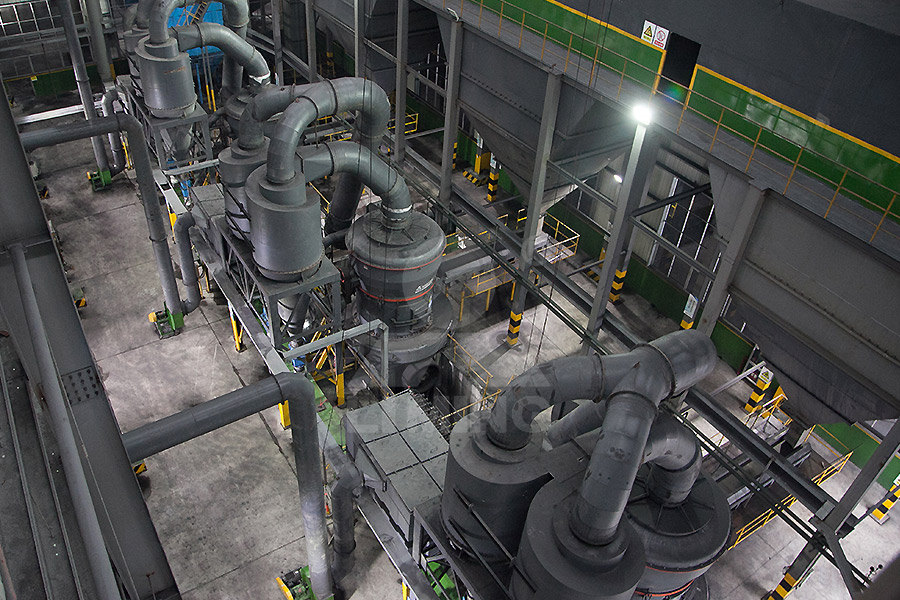
How we make steel
The starting point – refining the raw materials Raw materials are processed at Scunthorpe’s sinter plant, which forms an ironrich feedstock for the blast furnaces The ingredients – iron ore, coke and limestone fines – are carefully stacked and blended, then passed under an ignition hood at the sinter plantsubstantiated the applicability of various raw materials, such as ironore, dust and coal, but also yielded the various data necessary to design a commercial plant In 2001, Kobe Steel modified the demonstration plant into a commercial plant for processing steel mill dust generated at the Kakogawa Works Fig 3 shows the FASTMET process flowProspects for Coalbased Direct Reduction Process KOBELCO2024年2月4日 19 Major Departments: 1Coke ovens coal chemical plant: • Coal is converted into coke by heating the coal blend charge in the coke ovens in the absence of air at a temperature of 10000c 10500c for a period of 16/18 hours The volatile matter of coal liberated during carbonization is collected in gas collecting mains in the form of raw coke oven gas A presentation on Vizag Steel Plant ppt PPT Free Download2020年8月1日 process requires 137 t iron ore, 078 t coking coal, 01 t thermal coal, 0 16 t PCI coal, 027 t limestone an d 0125 t scrap steel The BFBOF p rocess accounts for about 9% of total global (PDF) COKING COAL THE STRATEGIC RAW
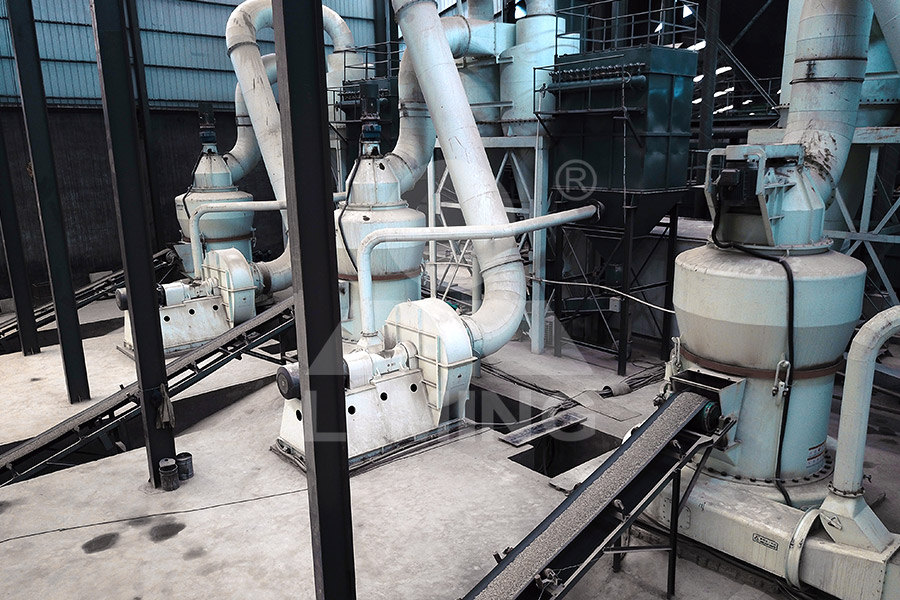
Steel Authority of India Limited Rourkela Steel Plant Rourkela
Rourkela Steel Plant Captive Power Plant#1 Environment Statement :: 201 920 M/s SAIL Rourkela Steel Plant :: Rourkela Page No 1 Steel Authority of India Limited Rourkela Steel Plant Rourkela – Fax : Ref No : 691/EE/1/356 Date : Raw Material Handling plant is meant for transporting materials from Raw material yard/Base mix yard to various process units of the plant The Major Raw materials required for Iron and Steel making are are Iron ore lump, Iron Ore fines, Sized iron ore, Flux limestone / dolomite, manganese, Quartzite coking coal, Noncoking coal ( for Boiler operation For Pulverized RMHP Vizag SteelJSW Steel manufacturing facilities in India are geographically diversified and include the Vijayanagar Plant in Karnataka (120 MTPA), Dolvi Works in Maharashtra (100 MTPA), Salem Works in Tamil Nadu (10 MTPA), Bhushan Power and Steel Limited (BPSL) Jharsuguda Plant in Odisha (35 MTPA), Raigarh and Raipur plants (JSW Ispat Special Steel Products Limited, a JSW Steel Integrated Report 2022年10月8日 The three main raw materials used to make pig iron (which is the raw material needed to make steel) for primary steel production in a blast furnace are the processed iron ore, coke (residue left after heating coal in the absence of air, generally containing up to 90% carbon) and limestone (CaCO 3) or burnt lime (CaO), How much investment needed to start a steel plant? (2024)
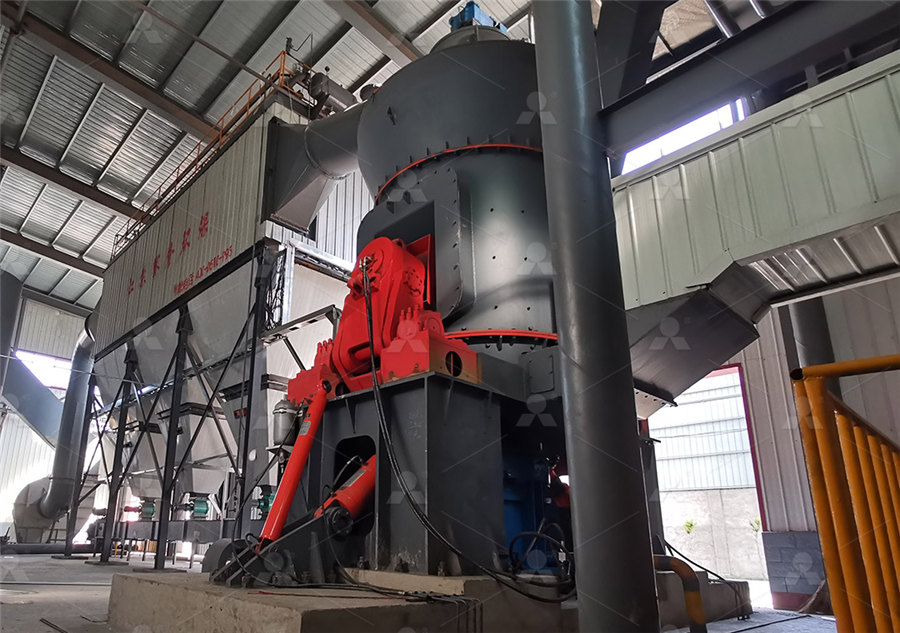
Augmentation of Ore Bedding and Blending Facilities
New Coal Handling Plant The new Coal Handling Plant can hold 15 days stock of Coking Coal for COB #6 (@ 3500 T/day) and CDI Coal of 10 days stock @ 1500 T/day) There are 24 Nos of RCC silos for stocking of Coking Coal and for CDI Coal, 6 Nos of RCC silos, each of capacity 2500 Tons New Coal Chemical DepartmentSuccessful inauguration of the New Steel Pilot Plant with a LOESCHE Ore Grinding Plant (OGPmobile) in Ouro Preto, MG, Brazil Ouro Preto – The company New Steel has developed a revolutionary new process for iron ore concentration for which New Steel has been awarded with the internationally highly esteemed Platts Global Metals Award for Innovation 2015Mills for minerals and ores Loesche2012年1月1日 Iron ore lump: The Fe content goes upto 630 %, and major quantity of ore is screened at raw material handling plant Coal : The coal ash varies in the range of 85 to 100 %, VM 25 – 30 %Coal dust injection in blast furnace : experience at Durgapur Steel PlantEquipment: 3 sets of HLM1900M coal vertical mill Auxiliary equipment: Jaw crusher, conveyor belt, quantitative feeder, dust collector; Vietnamese customers are very satisfied with this, and the coal is processed into highefficiency clean coal power for use in large steel mills, power plants, and coalfired plantsEnergysaving and Efficient Vertical Roller Mill Fote Machinery
.jpg)
Mineral Ore Coke Conveying in Steel Plant SKE Industries
In a steel plant, belt conveyors are crucial components of the material handling system, and they are widely used in conveying ore, coal, coke, sinter, pellets, slag, etc We offer inplant belt conveyors, tripper car, stacking conveyors, heatresistant belt CHAENG Vertical Roller Mills can be divided into GRMR Vertical Raw mill, GRMS Slag Vertical Mill, GRMK Vertical reliable performance, and good wear resistance Can grind Cement, slag, steel slag, nickel slag, coal and various mineral ore Rotary Kiln CHAENG has rich experience in the production of largescale Spare Parts for Steel PlantCHAENG Cement amp; Mining Equipment SupplierWe find that, in 2019, up to 745% (1,3891 Mt) of the total crude steel produced come from coalbased iron and steel plants Specifically, coalbased blast furnacebasic oxygen furnace (BFBOF Global iron and steel plant CO2 emissions and carbonneutrality 1 Iron ore, coal, coke and limestone are the major raw materials required for production of steel The inbound raw materials are received and unloaded at a Raw Material Unloading Yard (RMUY) The unloaded raw materials are processed at treatment plants (Coke, Sinter and Pellet Plants) from where they are sent to a blast furnace for iron makingAUGMENTING AN INBOUND RAW MATERIAL HANDLING SYSTEM OF A STEEL PLANT
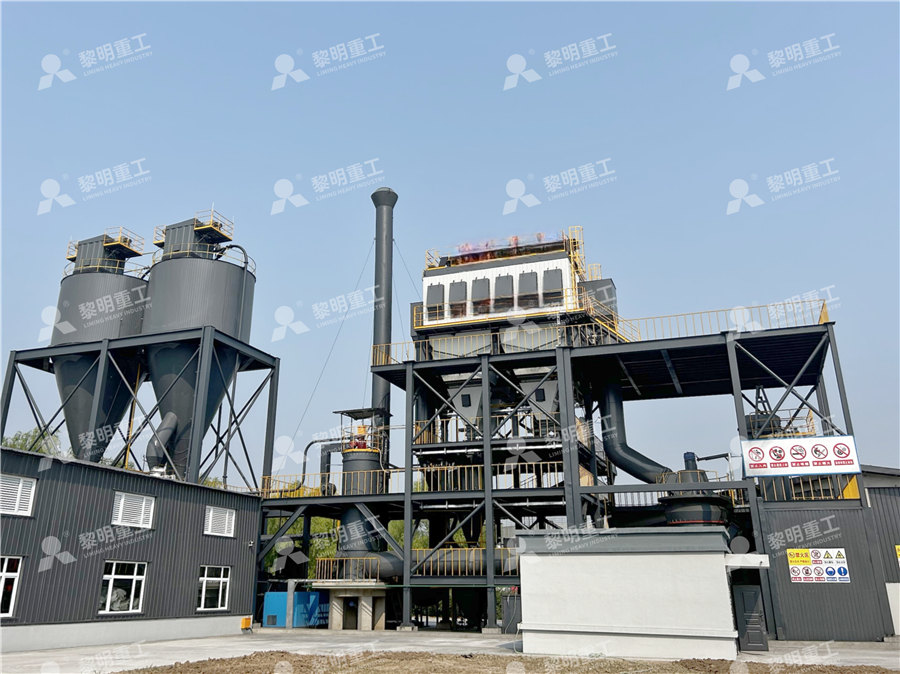
coal grinding machine CHAENG
Vertical Coal Mill is specially used for ultrafine grinding of raw coal and bituminous coal materials in cement, power plants, iron and steel plants and other fields The GRMC coal vertical mill produced by CHAENG adopts special structural design and production process, which is energysaving and environmentally friendly2014年10月1日 VRM has been widely researched in processing of cement (Ito et al 1997;Jorgensen 2005;Wang et al 2009, Ghalandari et al 2021), coal (Tontu 2020), iron ore (Reichert et al 2015), zinc ore (van Copper Ore Grinding in a Mobile Vertical Roller Mill Pilot PlantMaking steel Steel is made from iron ore, a compound of iron, oxygen and other minerals that occurs in nature The raw materials for steelmaking are mined and then transformed into steel using two different processes: the blast furnace/basic oxygen furnace route, and Making steel ArcelorMittalIn this there are designated bunkers for raw materials transported from mines / Sintering Plant (SP) / Raw Materials Handling Plant (RMHP) / Coke Ovens (CO) by wagons / conveyors v) Gas Cleaning Plant (GCP): RMH (Iron Ore Fluxes) Sinter Plant (Sinter) Coke Plant (Coke) SMS Hot Metal O2 Torpedo Steam Coal Injection Cold Air Stoves Hot Air RECOMMENDED GUIDELINE FOR IRON STEEL SECTOR MINISTRY OF STEEL
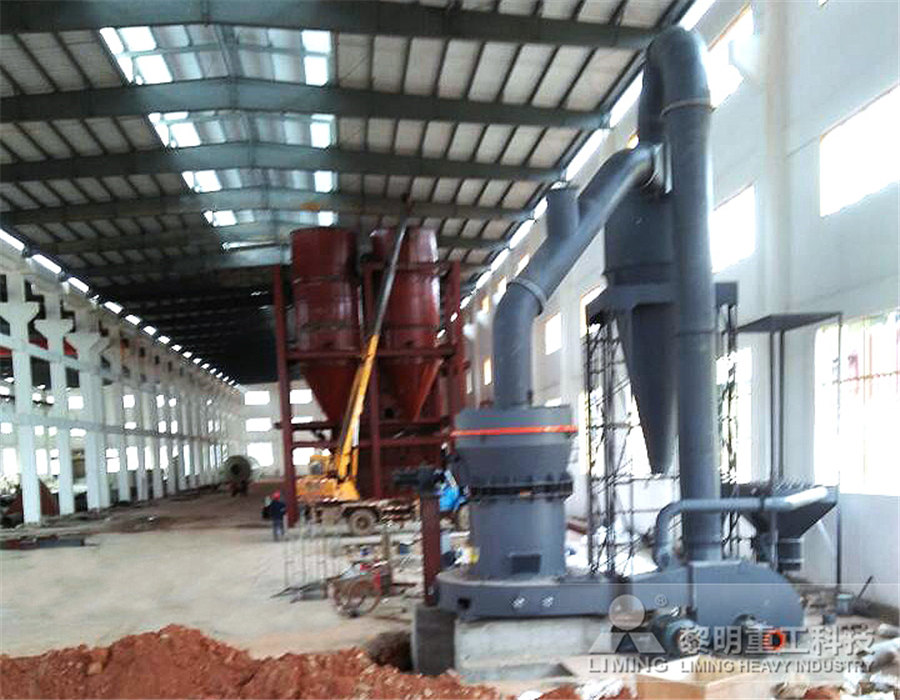
Fact sheet Energy use in the steel industry
Steel is produced via two main routes: the blast furnacebasic oxygen furnace (BFBOF) route and electric arc furnace (EAF) route Variations and combinations of production routes also exist The BFBOF route produces steel using raw materials such as iron ore, coal, limestone and steel scrap About 75% of steel is produced using the BFBOF routeApplication field: Coal vertical mills are widely used in cement production, calcium carbonate crushing processing, coal powder preparation stations, gypsum powder processing, power plant desulfurization, phosphate rock grinding, metallurgical industry and HighEfficiency Vertical Coal Mill Enhancing Coal PulverizationThe location of a pelletizing plant affects the method of receiving raw materials such as iron ore, additives and binders 221 Pretreatment process of Iron Ore Fines In the pretreatment process, iron ore fines are ground into finer size, suitable for green ball formation Dry or wet grinding process is adopted for grinding the iron ore finesPellet Plant produces Pellets using Iron ore and additives such as JSW Steel Dolvi Works is a 5 MnT steel plant that requires ~9 MnT of iron ore to meet its raw material needs The plant is undergoing a capacity expansion and within FY 202021, is expected to commence operations with an additional 5 JSW Steel Annual Report 20192020
.jpg)
JSW Steel Integrated Report 202021
Since July 2020, all mines have been operationalised and in FY 202021, they collectively produced around 1237 MnT of iron ore, which have been directed to our three integrated steel plants Currently, we are exploring ways in which the For the expansion of Bhushan Steel’s steel plant at Meramandali, india, Larsen and erection, testing and commissioning of the raw material handling system that included 43 kilometres of belt conveyors Newsletter RunofMine Largescale Raw Materials Handling at Bushan 2019年8月5日 iron ore nes or plant waste and coal nes, It is likely to increase 95 kg by 2020 and 150 kg by 2030 India’s goal is 300 million tonnes (Mt) steel production by 2030 Raw materials An Overview: Utilization of Iron Ore Fines and Steel Plant Wastes2020年12月30日 In the steel production industry, PM 25 is emitted during manufacturing as well as during the resuspension process at raw material storage sites The iron ore sintering process for steel plants requires several materials, including iron ore, coal, limestone, coke, and recycled steel (FernándezGonzález et al, 2017)Chemical Fingerprints for PM25 in the Ambient Air near a Raw
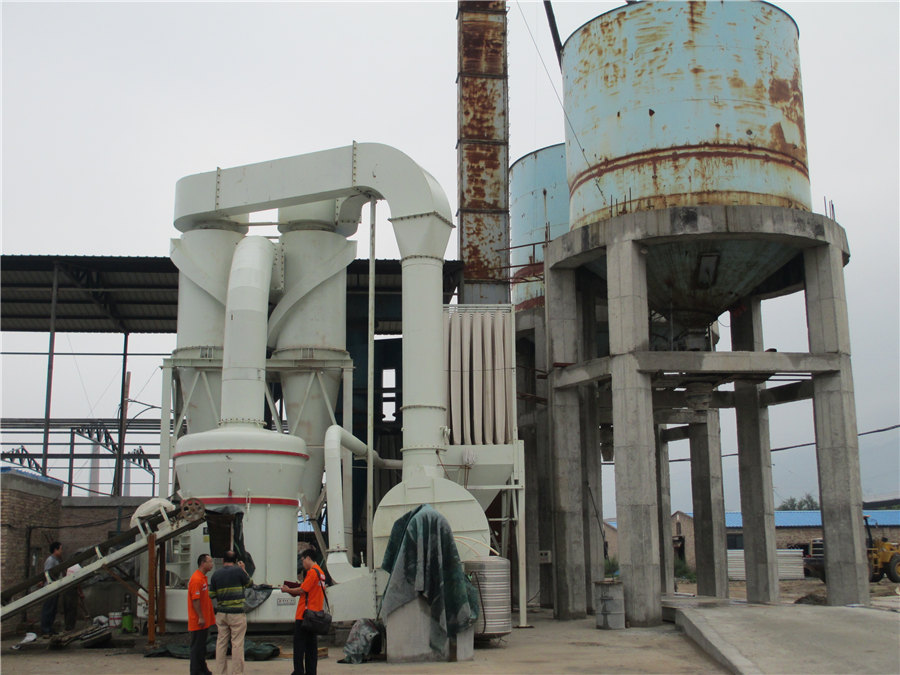
LOESCHE vertical roller mills for the comminution of ores and minerals
2001年10月1日 LOESCHE vertical roller mills are widely used for the comminution of raw materials in the cement industry, for the comminution of clinker and blast furnace slag and for the production of 2024年5月12日 Conclusion In conclusion, vertical integration was a key factor in the success of Carnegie Steel Company By owning and controlling multiple stages of production, the company was able to reduce How did vertical integration help the carnegie steel business?In 1979, Nigeria had initiated construction of the iron and steel projects which by 1985 were over 90% complete, including the National Iron ore Mining Company at Itakpe, two liquid steel Geological ReEvaluation of Nigeria's Iron Ore Deposits as Raw DRI process is a method to produce iron from iron ore without melting it The National Steel Policy, 2017 projects that by 2030, of the 80 million tonnes per annum (MTPA) of DRI The primary inputs for coalbased DRI plants include iron ore, coal, lump ore is produced directly by crushing and separating raw iron ore into fines and lumpsHow can India Decarbonise Coalbased DRI Plants in Steel Making?
.jpg)
Understanding Pellets and Pellet Plant Operations IspatGuru
2015年3月21日 Many pelletizing plants are located near iron ore mines This is because these plants are installed to pelletize the iron ores which are beneficiated at these mines Such plants receive the iron ore by rail and/or slurry pipelines Many other pelletizing plants are installed away from the iron ore mines These plants are independent of iron ore