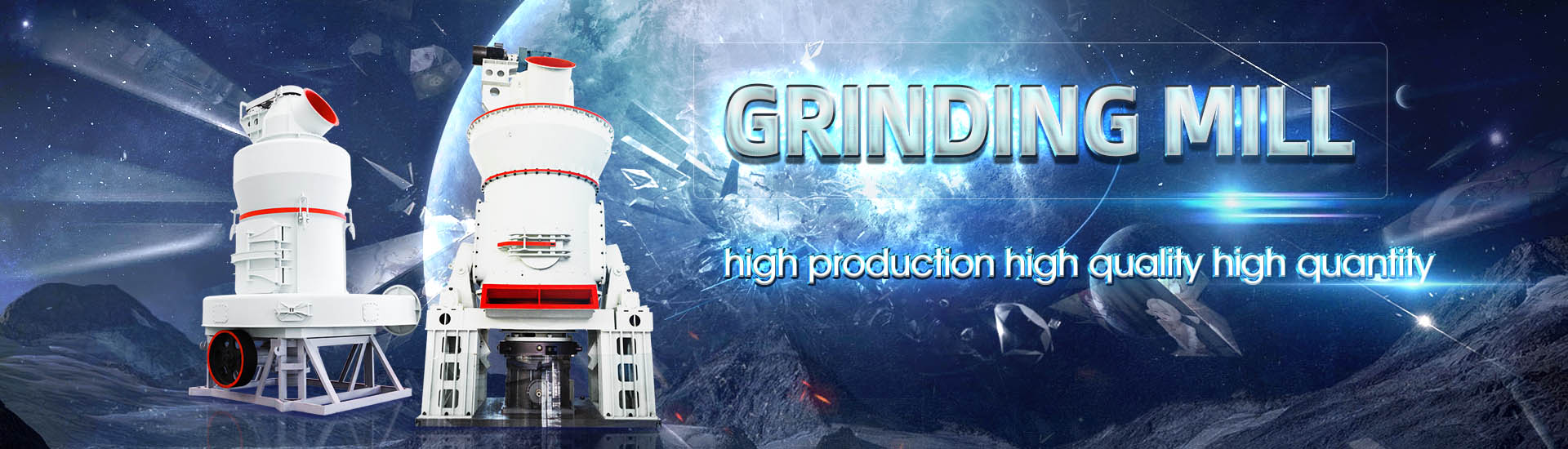
High fine vertical mill principle diagram
.jpg)
Schematic operation principle of a VRM [1]
This paper presents an experimental approach to measure and model the residence time distribution of vertical roller mill in cement clinker grinding circuitVertical roller mills are adopted in 20 cement plants (44 mills) in Japan In the vertical roller mill which is widely used in the raw material grinding process, raw materials input grinding table Vertical roller mill for raw Application p rocess materialsBy initiating a CL for an industrial cement vertical roller mill (VRM), this study conducted a novel strategy to explore relationships between VRM monitored operational variables and their Schematic operation principle of a verticalrollermillIt can be divided into vertical roller mill, horizontal cylinder roller mill, high pressure roller mill, Raymond mill, and column mill The basic structure of the vertical roller mill with vertical Roller Mill Springer
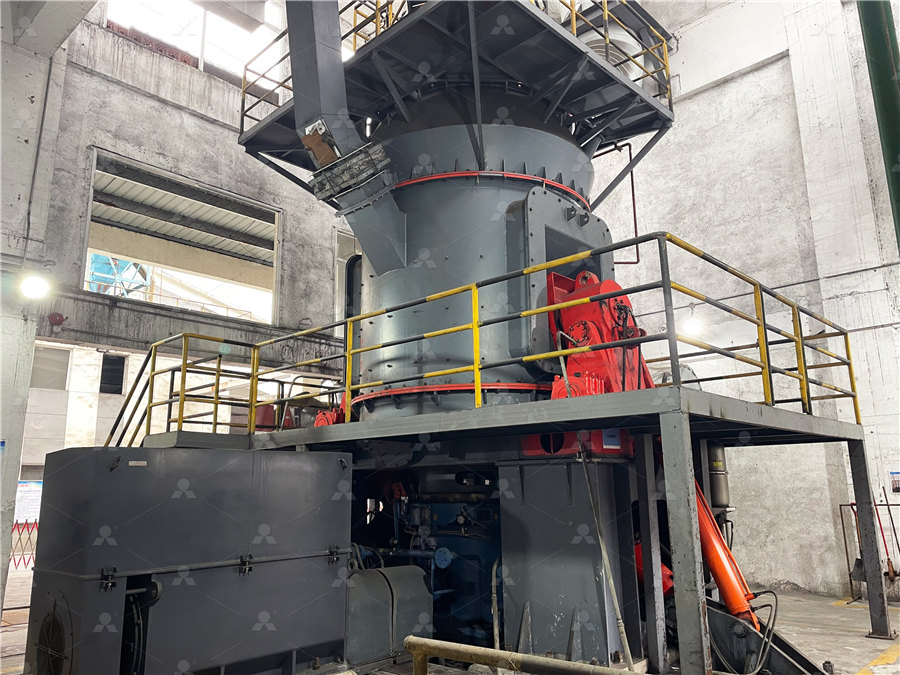
Analysis of vertical roller mill performance with changes in material
2022年5月31日 The vertical roller mill (VRM) is commonly used for secondary and tertiary crushing processes in numerous industries In this study, the discrete element method (DEM) a vertical roller mill (VRM) • Surpasses the classic methods if the controlled process demonstrates significant disturbances • A high degree of attention to the process states is required in order PROCESS OPTIMISATION FOR LOESCHE GRINDING PLANTSVertical stirred milling is a wellrecognized technology for the secondary, regrind and fine grinding applications and are increasingly replacing coarser ball mill applications in secondary and RECENT DEVELOPMENTS IN COARSE GRINDING USING VERTICAL MPS vertical mill from Pfeiffer is the ideal allrounder Grinding of coal, petcoke, clay, limestone, quicklime, gypsum, and many other materialsCoal mill, gypsum mill, clay mill, etc Pfeiffer MPS mills
.jpg)
Solid Edge’s Application in Vertical Mill Design Springer
A complete set of vertical mills mainly includes foundations, transmissions, roll plates, pressurizing devices, rocker arms, housings, three lock air valves, sealed blower systems, The principle of the attritionleaching carbonation process is to continuously refresh the surfaces of reactive particles so that leaching can proceed unimpeded, yielding enhanced carbonationSchematic of Tower and Verti mill Download NETZSCH laboratory vertical stirred mill along with its stirrer design used in the present study is shown in Figures 1 and 2(a) The stirrer design helps in fine grinding by properly dispersing Schematic diagram of the laboratory vertical stirred CLUM series ultrafine vertical roller millwas produced by Shanghai Clirik Machinery Co, Ltd Relying on 12 years of experience in the production of ultrafine powder and based on German and Taiwan ultrafine vertical mill Ultra fine vertical roller millUltra Fine Millultra
.jpg)
Ball Mill Grinding Machines: Working Principle, Types,
Ball Mill, Working Principle, Types, Parts, Applications and Advantages Ball Mill Grinding Machines: Exploring the Working Principle, Types, Parts, Applications, Advantages, and Recent Developments Ball mill grinding machines are 2024年1月1日 The vertical roller mill has the advantages of low energy consumption, high output, easy maintenance, etc, and has been widely applied in cement, steel and power industry, the preparation of nonmetallic ore ultrafine powder, manganese ore Roller Mill SpringerLinkof 80mm The raw materials are mixed in a certain proportion and fed into a vertical roller mill (LOESCHE mill) The vertical roller mill grinds the marital to D 85 of 90µm The ground product is calcined in a preheater to 850900℃ After calcination, the materials enter to a rotary kiln and heated to 1450℃ to become clinkerModeling and simulation of vertical roller mill using population Production of coarse powder and general fine powder above 45um, stable operation, high cost performance and high noise Ring roller mill: 2um content is about 20% or more, the highest fineness is 810um, middle and highend finished powder Produce 1015um powder, stable operation, short life of wearing parts, high noise and low output Ball millCLUM Ultrafine Vertical Grinding Mill
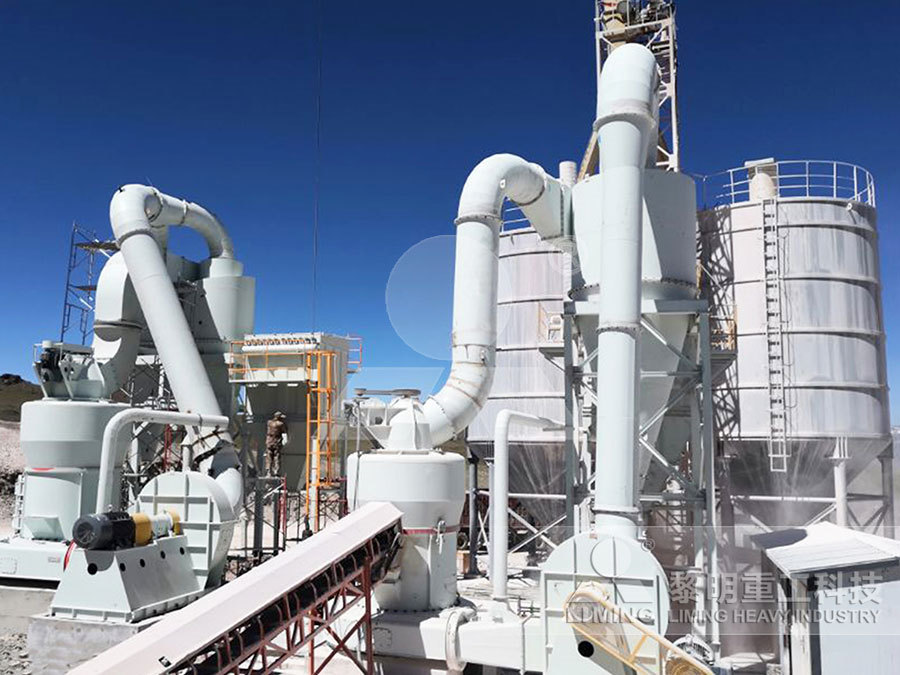
LM series vertical mill
LM series vertical mill is a new type of milling equipment WORKING PRINCIPLE The mill disk is driven by the gear box through electrical motor and the material will be fed to the center of the disk from the feeding port via an airlocking feeder and Fine powder vertical mill; Models: LM130K: LM150K: LM170K: LM190K: LM220K: LM280K: Plate The document provides installation and operation instructions for the HRM1700M Vertical Roller Coal Mill It describes the mill's technical parameters, components, structure, working principles, and installation process Key aspects include grinding rollers that can be removed for maintenance, a hydraulic system that controls grinding pressure, and a separator that Operation Manual: HRM1700M Vertical Roller Coal MillWorking Principle of Fluid Energy Mill Fluid energy mill is also known as jet mill It works on the principle of impact and interparticle attrition to achieve the desired particle size Construction of Fluid Energy Mill It consists of a grinding chamber which is an oval loop of pipe It has a diameter of about 25200 m and its height is 122 What is Fluid Energy Mill? Working Principle, Construction, Diagram 2024年4月28日 Through careful assessment of the mill’s working principles, construction, operation, and efficiency determinants, operators and engineers can make wellinformed decisions to ensure the maximum grinding efficiency and Exploring Ball Mill Diagram: A Comprehensive Guide

What is the Principle of Colloid mills? Inox mill
The operating principle of the colloid mill is that the fluid or semifluid material passes between the fixed teeth and the movable teeth that move relatively at high speed so that the material is subjected to a strong shearing force, friction It is characterized by its unique working principle, which involves a highspeed rotating shaft with agitator elements The attritor mill produces fine particles with a narrow size distribution, vertical mill, rod mill and AG/SAG mill for grinding in a variety of industries and materials Contact : info@ballmillssupplier; Tel What is The Working Principle of Attritor Mill? ball mills supplierCLUM ultrafine vertical mill is a new type of ultrafine grinding equipment integrating powder grinding, grading, conveying, secondary powder selection, and finished product packaging Capacity: 0245 t/h Max feeding size: 30mm Processing ability: 0245 t/h Application of CLUM ultrafine vertical mill:CLUM Ultrafine Vertical Mill2022年3月30日 Overview of Ball Mill Ball mill, also known as tumbling or pebble mill is milling equipment that encompasses cylindercontaining balls and is mounted on a metallic frame that can be rotated along with a longitudinal axis The large ball tends to break down coarse feed materials and the small ball mill to form fine products by reducing void spacesIntroduction to HighEnergy Ball Mill: Working Principle,
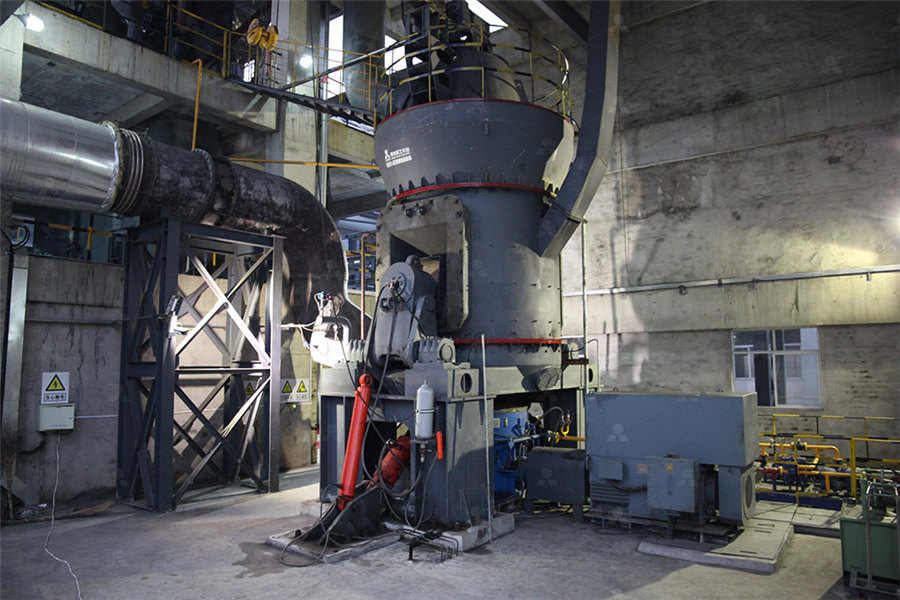
Ball Mill Principle, Application, Uses, Critical Speed, Diagram
For example, a small laboratory ball mill may cost around Rs 10,000 to Rs 50,000, while a highcapacity industrial ball mill can cost more than Rs 1,00,000 When choosing a ball mill, it is essential to consider both the price and the value for money2023年12月4日 The vertical orientation of the spindle allows for stability and minimizes vibrations during cutting, which contributes to achieving tight tolerances and fine finishes on workpieces Versatility in Machining: Vertical boring mills are versatile machines capable of performing a wide variety of machining tasks including boring, turning, facing, threading, and Vertical Boring Mills: A Comprehensive Guide Machine Tool 2023年3月15日 SBM has launched the LM Vertical Grinding Mill which integrates five functions of crushing material conveying It is characterized by centralized technological process, small occupational area, low investment, high efficiency, energy conservation and Vertical Finepowder Mill Series Models and parameters: LM130XGX: LM150XGX:LM Vertical Grinding Mill SBM Mill Crusherin combination with a ball mill for cement grinding applications and as finished product grinding units, as well as raw ingredient grinding equipment in mineral applications This paper will focus on the ball mill grinding process, its tools and optimisation possibilities (see Figure 1) The ball mill comminution process has a high electricalBALL MILLS Ball mill optimisation Holzinger Consulting
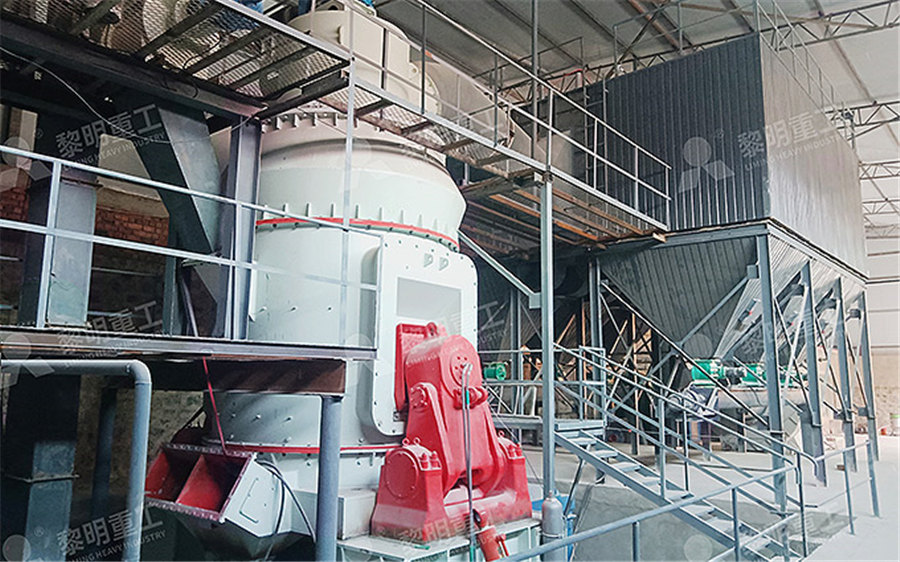
Industrial Vertical Grinding Mill
Air ring) The highspeed upward hot air is brought to the highefficiency separator integrated with the industrial vertical grinding mill The coarse powder is sorted by the separator and returned to the grinding plate for regrinding; the fine powder is discharged out of the mill with the air flow and is collected in the system2023年6月1日 This study aims to improve the output and production efficiency of a large vertical mill by optimizing its operational parameters This paper takes a large vertical mill in LGM as the object, a numerical calculation method of particle–fluid coupling system in large vertical mill based on CFDDPM theory, and a multiobjective optimization method of operating parameters of Operation parameters multiobjective optimization method of • Mill motor speed • Mill air flow/mill differential pressure • Temperature after the mill • Pressure before the mill • Grinding stock feed • Classifier speed • Mill fan speed • Water spraying • Hot gas • Fresh air Manipulated variables Disturbance variable Process measured value RelauchLMmaster 6 250814 11:47PROCESS OPTIMISATION FOR LOESCHE GRINDING PLANTSRoller Mill, Fig 1 Structure diagram of vertical roller mill 2 Roller Mill the hydraulic system After completing a grinding operation in the extrusion area, Fig 3 Working principle of highpressure roller mill 4 Roller Mill the fan and the host, and enters the Roller Mill Springer
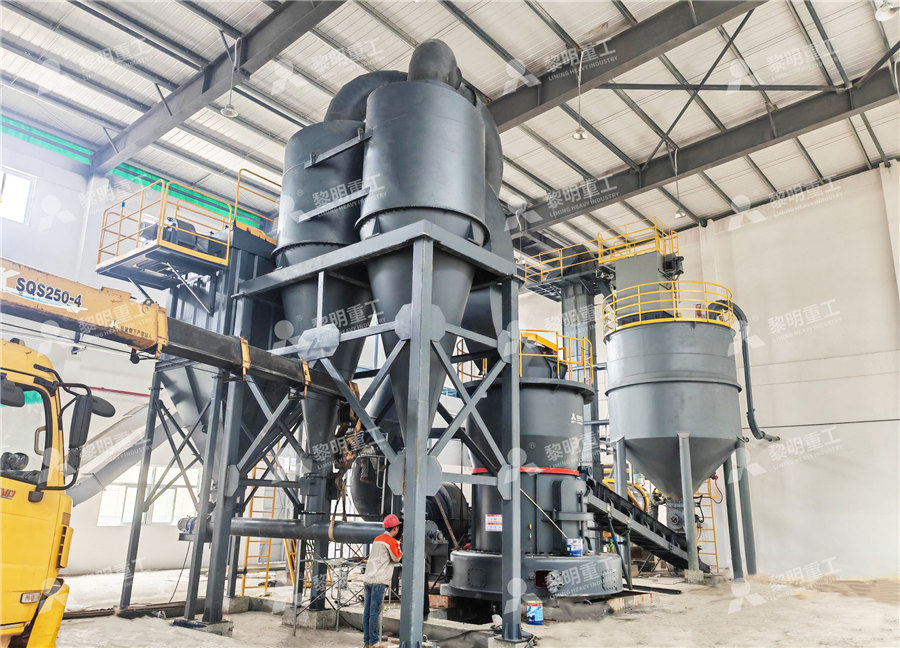
HIGmill high intensity grinding mill Metso
The process comprises just a scalping cyclone with no circulating load, feed tank and pump, and the mill itself The benefit of high power intensity and vertical installation is a very small footprint The head room over the mill is small and the flanged splitshell construction reduces the space needed for maintenanceBarite ultrafine vertical roller mill is an industrial vertical grinding mill that can grind nonmetallic ore into fine powder The mill has a high production capacity, high fine powder content, high degree of automation, convenient maintenance, long service life, environmental protection, and energysaving, and is an ideal equipment for largescale production of ultrafine powderBarite Ultrafine Vertical Roller MillDownload scientific diagram TowerMill Ò (Eirich courtesy) and Vertimill™ (Metso courtesy) from publication: Vertical Agitated Media Mill scaleup and simulation Vertical Agitated Media TowerMill Ò (Eirich courtesy) and Vertimill™ (Metso courtesy)I INTRODUCTION AND PRINCIPLES In this presentation we will discuss the principle of the Attritor and its applications The Attritor is a grinding mill containing internally agitated media It has been generically referred to as a “stirred ball mill” There are quite a few types of Attritors; we can categorize them as dry grindWe will discuss the principle of the Attritor and its applications
.jpg)
Bead Mill, Principle and Applications / Apex Mill series / Hiroshima
Basic flow for operating our bead mill (in case of UAM) The basic flow diagram for operating the Apex Mill series’ bead mills mainly consists of three pieces of equipment—a tank, a slurry pump, and a bead mill—which are connected with pipes The slurry is pumped from the mixing tank to Limestone ultrafine vertical mill is a high quality ores material powder grinding mill +17 [ protected] The limestone ultrafine vertical mill principle of vertical abrasive layer is adopted, HGM series Ultra Fine Powder Mill CLRM Series Enhanced Roller Grinding Mill YGM series Raymond Mill Hammer crusherLimestone Ultrafine Vertical MillThis article introduces the horizontalaxis wind turbine (HAWT), which is by far the most common type of wind turbine Horizontalaxis wind turbines may produce less than 100 kW for basic applications and residential use or as much as 6 HorizontalAxis Wind Turbine (HAWT) Working Principle of Ball Mill Operation The ball mill operates by rotating a cylinder horizontally and partially filled with balls The cylinder's rotation causes the balls to cascade and fall back into the mill, generating impact and friction against the material to be ground The following are the key components of a ball mill: 1Ball mill principle: An explanation of operation and importance in
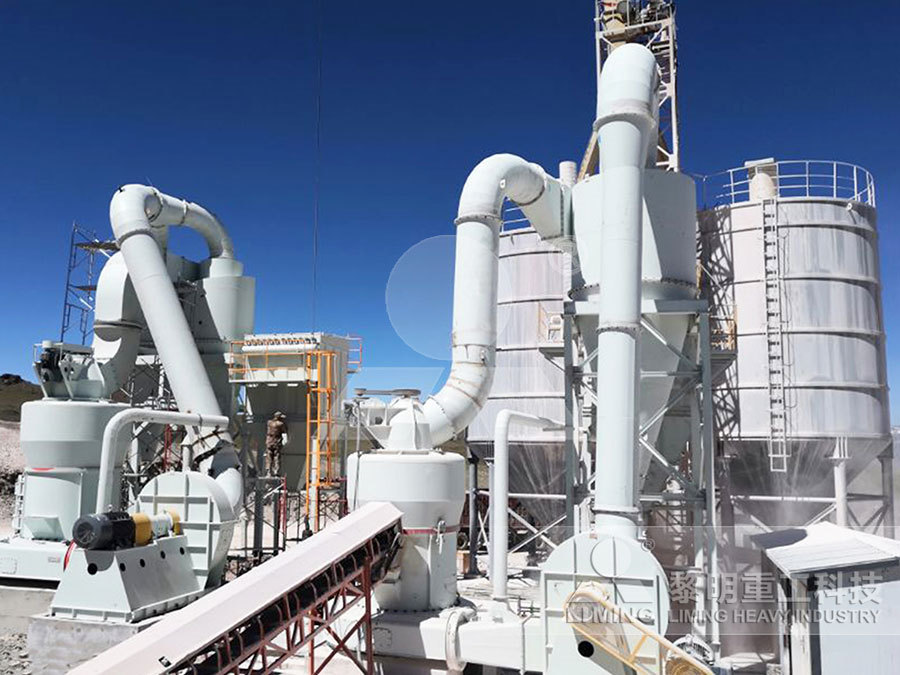
Working principle of jet mill
2023年9月28日 The principle of fluid energy milling, also known as jet milling, involves using highvelocity jets of compressed gas (typically air or nitrogen) to grind and disperse particles into fine powders In fluid energy milling, the Figure 3: Relationship between feed size (F80) and Bond efficiency factor (Huang et al, 2019) VERTICAL POWER MILL (VPM) – PRINCIPLE OF OPERATION Declining ore grades and more complex ore bodies, as well as waste management and global net zero initiatives, lead to a clear trend for high tonnage yet energy efficient grindingRECENT DEVELOPMENTS IN COARSE GRINDING USING VERTICAL the mill grinding chamber, in which the vertical agitator screw is located, together with a charge of grinding media and grinding material in slurry form Highgrowth markets in copper, ironore, gold, leadzinc ores, mineral sands and rareearth metals drive increasing demand for fine grinding to maximize recoveryEIRICH TowerMill Vertical agitated media millBall milling is a popular and versatile technique used for the fine grinding, mixing, and blending of materials Principles of Ball Milling Ball milling is a mechanical process that involves the rotation of a drum containing grinding media, typically steel balls, at a high speedExploring ball milling theory: A comprehensive guide
.jpg)
How to operate an air classifier mill to meet your fine grinding goals
vertical mill Combined drive In this classifier mill, as shown in Figure 2b, the classifier wheel and rotor disc are mounted on one shaft and rotate at the same speed As a result, the mill is smaller, has a lower purchase cost, and requires less installed horsepower than the vertical mill However, the apFigure 1 Vertical air classifier Limestone Powder Ultrafine Vertical Roller Mill Modle : CLUM Series Finished Size: 4003000 mesh Processing Ability: 3 – 45t/h Max Feeding Size: 10 mm M 1 Set Price: $ Range Of Application: Limestone, Calcium Carbonate, Talc, Limestone Powder Ultrafine Vertical Roller MillProduct advantage of talc powder ultrafine vertical roller mill 1 High quality powder size The fineness of the finished product is D97 545 microns Narrow particle size distribution, can produce 2 micron content of 20%70% products, greatly improving the added value of finished products and application areas 2Talc Powder Ultrafine Vertical Roller MillDownload scientific diagram The two principle parts of the colloidal mill system from publication: Application of ultra highpressure homogenization (UHPH) in the production of submicron / nano The two principle parts of the colloidal mill system Download