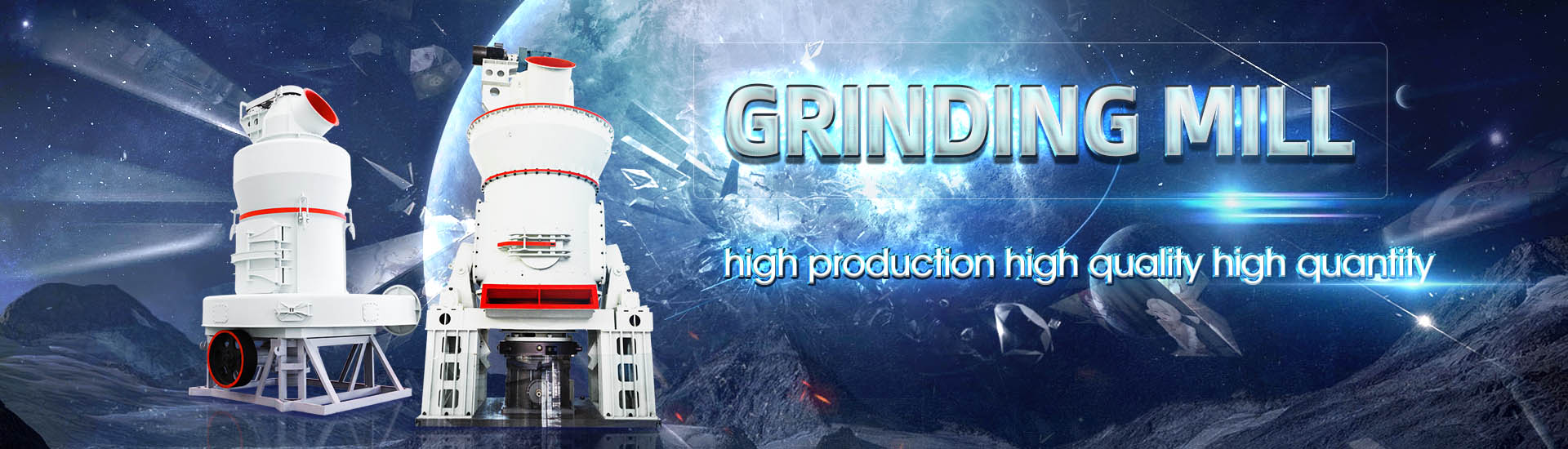
The function of Hantech grinding mill
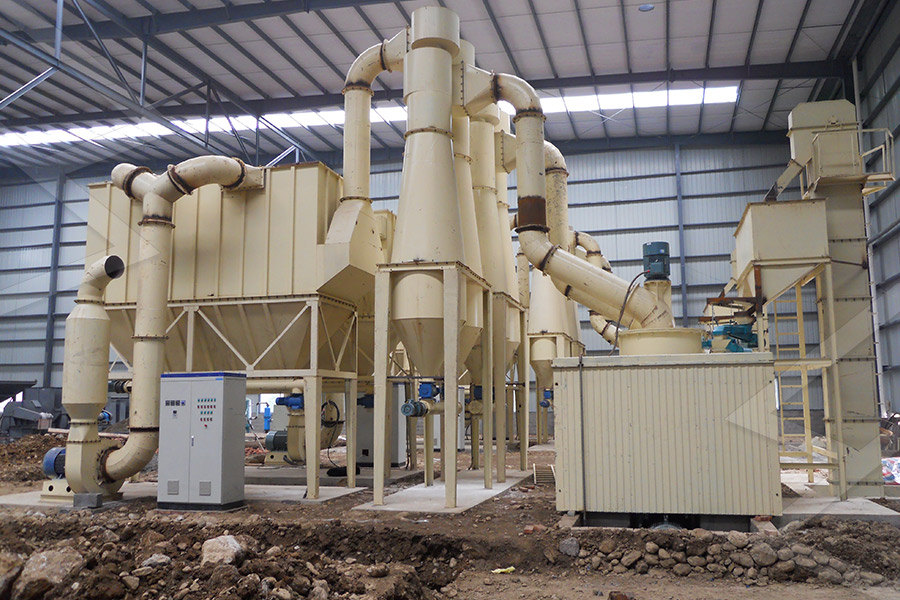
Technology Hantech Engineering
Our stateoftheart machinery allows us to produce in proverbial Swiss quality At our Wroclaw factory we mill, turn, grind, EDM and assemble components Obvously we produce automatically as well ul Spóldzielcza 37392020年6月15日 Grind curves give the steadystate values of the performance variables throughput, power draw, and grind in terms of the mill filling and critical mill speed The grind Steadystate and dynamic simulation of a grinding mill using grind 2015年4月9日 Grinding mills are size reductions machines that often follow crushers in the processes where finer products are desired after crushing Different grinding machines are usually named as mills, for example rod mills, Grinding Mills and Their Types IspatGuru2022年6月24日 Grinding is a manufacturing process which significantly contributes in producing high precision and durable components required in numerous applications such as aerospace, (PDF) A comprehensive review on the grinding process:
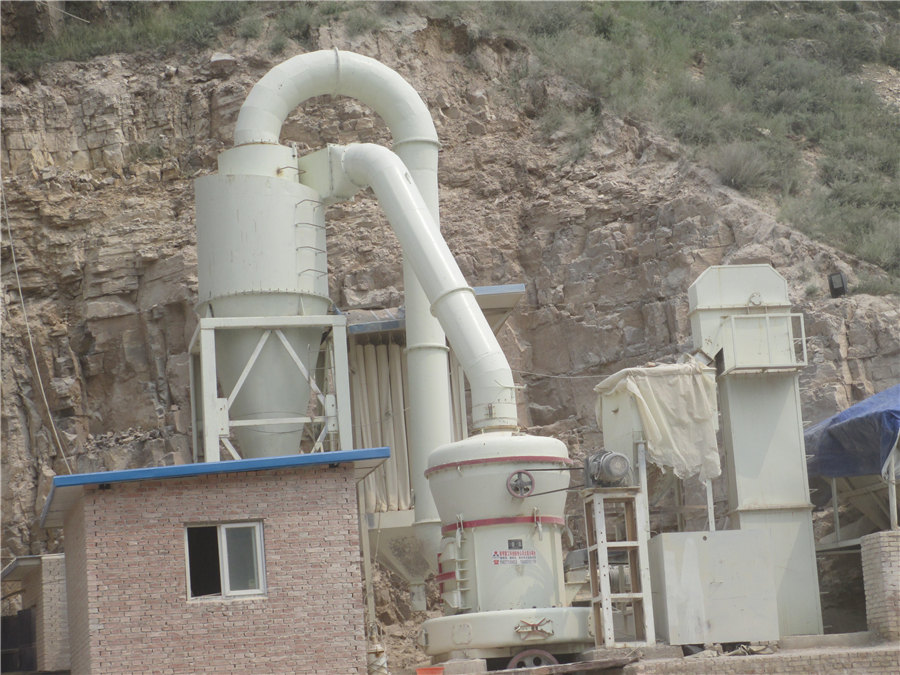
Grinding Mill an overview ScienceDirect Topics
Grinding can be achieved by several mechanisms, including: impact or compression due to sudden forces applied almost normally to the particle surface; chipping or attrition due to Grinding in ball mills is an important technological process applied to reduce the size of particles which may have different nature and a wide diversity of physical, mechanical and chemical Grinding in Ball Mills: Modeling and Process Control Sciendo2013年1月1日 Principles of Modern Grinding Technology explains the principles that led to rapid improvements in modern grinding technology over recent decades Removal rates and quality standards havePrinciples of Modern Grinding Technology2018年8月17日 Extreme temperatures, impact velocity, mill load, grinding media, ore types, and applications are some of the factors to be considered while installing new linersGrinding Mills — Types, Working Principle Applications
.jpg)
Intelligent technology in grinding process driven by data: A review
2020年10月1日 Datadriven construction of the grinding process data architecture is combined with data fusion, data processing, data storage, data analysis, and other technologies to Hantech Engineering Sp z o o ul Spóldzielcza 3739 55080 Katy Wroclawskie Poland Telephone +48 (0)71 363 56 50 Telefax +48 (0)71 363 49 70 production@ hantechengineeringGrinding Hantech Engineering2022年1月23日 VRM has the functions of grinding and powder selection, G A specific energybased size reduction model for batch grinding ball mill Miner Eng 2015, 70, 130–140 [CrossRef] 21Analysis and Optimization of Grinding Performance of 2 The innovative design of grinding chamber, the corn rough grinding (Ф30 sieve plate) efficiency improves 2030%, the corn grinding (Ф1012 sieve plate) efficiency improves 4070%, greatly reducing the grinder electricity The key functions and values of pellet mills and
.jpg)
Should the slurry density in a grinding mill be adjusted as a function
2007年7月1日 Adjustment to ball size could lead to significant improvement in grinding mill throughput (McIvor, 1997)The Bond’s equation for ball sizing (McIvor, 1997) can help in selecting the ball size for a given ore and grinding millBall mill simulations with ball wear modelling can also be used to identify the optimum ball size (Concha et al, 1992) for a given applicationThese machines function by using small grinding beads to disperse and reduce the size of particles in the substance being processed The main components of a bead mill machine include a grinding chamber, a rotor, a container to hold the material, and a motor to drive the rotorThe Role of Bead Mill Machines in Different IndustriesA mill is a device, often a structure, machine or kitchen appliance, that breaks solid materials into smaller pieces by grinding, crushing, or cutting Such comminution is an important unit operation in many processesThere are many different types of mills and many types of materials processed in them Historically mills were powered by hand or by animals (eg, via a hand crank), Mill (grinding) WikipediaA crushing plant delivered ore to a wet grinding mill for further size reduction The size of crushed ore (F 80) was 40 mm and the SG 28 t/m 3 The work index of the ore was determined as 122 kWh/t A wet ball mill 1 m × 1 m was chosen to grind the ore down to 200 micronsGrinding Mill an overview ScienceDirect Topics
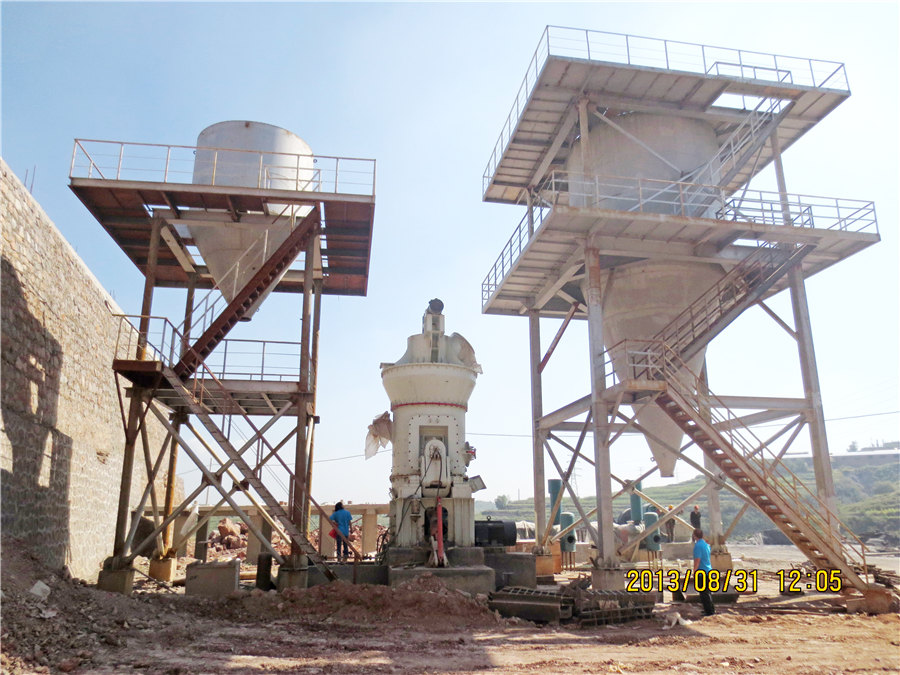
(PDF) Review of the Effect of Grinding Aids and Admixtures on the
2023年11月6日 PDF Grinding aids (GAs) are polar chemicals introduced in cement mills in either liquid or powder form to improve on mill grindability efficiency Find, read and cite all the research you 2007年7月1日 When the specifications and models of the ball mill are determined, the factors affecting the operation indexes of the grinding process include three facets [15–19]: one, the properties of the ore entering the grinding process, including the mechanical properties of the ore, the particle size distribution of the feed, and the required product fineness; second, the Should the slurry density in a grinding mill be adjusted as a function 2003年1月1日 An approach to quantifying the impact grinding performance of different materials is presented Based on a dimensional analysis and on fracture mechanical considerations, two material parameters (PDF) Modelling of Grinding in an Air Classifier Mill Based on a 2009年10月1日 Request PDF Batch Grinding in Laboratory Ball Mills: Selection Function The selection functions and the breakage distribution functions are based on the experimentallydetermined particle size Batch Grinding in Laboratory Ball Mills: Selection Function
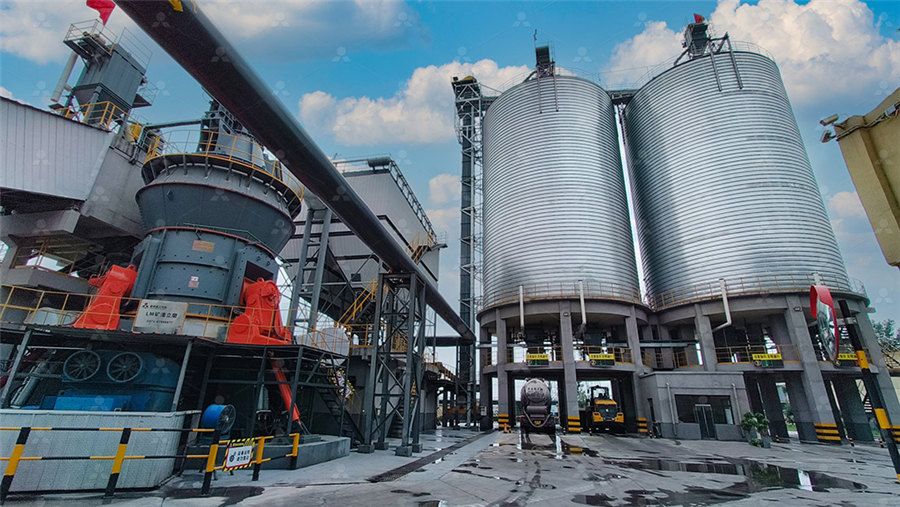
The wear detection of millgrinding tool based on acoustic
2022年4月7日 The monitoring of tool wear plays an important role in improving the processing efficiency and reducing the production cost of enterprises This paper is focused on the detection of electroplated diamond millgrinding tools by using the acoustic emission sensor The wear stages of millgrinding tools are divided into three parts, namely initial wear stage, normal wear Mill grinding efficiency is measured at the same time as CSE through circuit samplingFunctional performance analysis combines CSE and mill K M, McIvor, R E and Arafat, O, 2014 Functional performance of ball milling circuits a plant metallurgist's tool for process characterisation and optimisation, in Proceedings 12th AusIMM Functional Performance of Ball Milling Circuits AusIMMonline live calculators for grinding calculations, Ball mill, tube mill, critical speed, Degree of filling balls, Arm of gravity, mill net and gross power Optimization Online Trainingball mill calculations, grinding media filling degree, ball size, mill 2017年2月20日 Grinding Mill Specifications Data According to formula 423/√d, where d is equal to internal shell diameter within new liners In this case the thickness used was 60 mm for small mill sizes up to and including 2940 and 80 mm for larger millsGrinding Mill Design Ball Mill Manufacturer 911Metallurgist
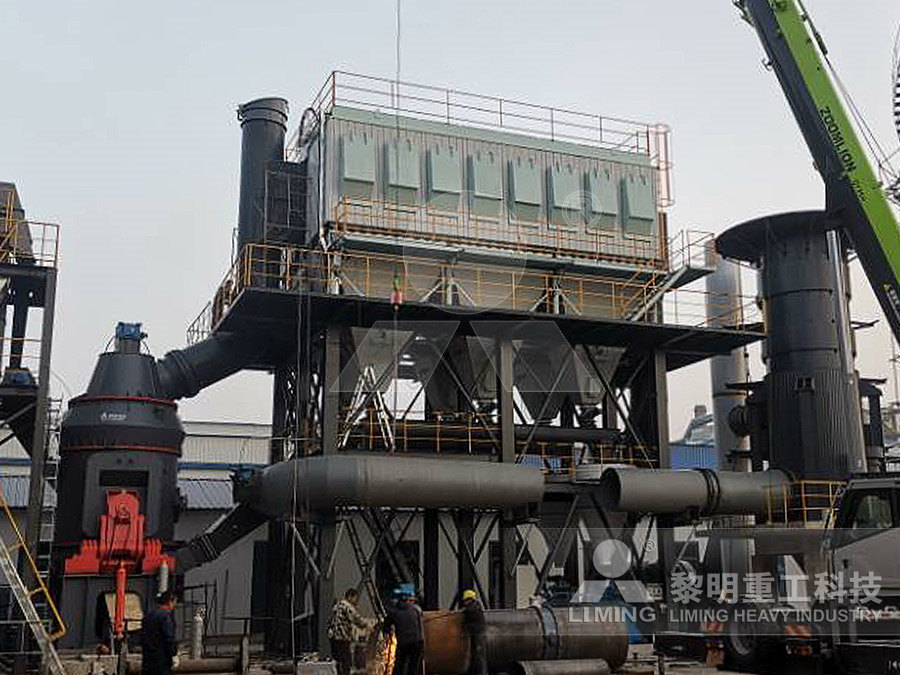
A Review of the Grinding Media in Ball Mills for Mineral
2023年10月27日 The ball mill is a rotating cylindrical vessel with grinding media inside, which is responsible for breaking the ore particles Grinding media play an important role in the comminution of mineral ores in these mills This work reviews the application of balls in mineral processing as a function of the materials used to manufacture them and the mass loss, as 2015年8月6日 The metal lifter bar design is generally a function of the grinding application and mill size The cross section however must retain two critical dimensions The first is that the lips or edges of the lifter that extend over the rubber plates must be kept at a minimum of 25 mm to provide adequate clamping of the liner plates by the lifterGrinding Mill Liners 911Metallurgistwhere T is the grinding time to reach a certain median particle size, K is a constant that depends upon the material being processed, the type of media and the particular mill being used, D is the diameter of the media, and N is the shaft rpm This equation shows that total grinding time is directly proportional to media or ball diameter and inversely proportional to the square root of Solids Choose the Right Grinding Mill Chemical Processing2019年1月30日 Mill power models have been used in a variety of ways in industrial practice since power directly equates to throughput and fineness of ground product We first start with HoggFuerstenau Power Model and show how this model successfully predicted the power draw of many grinding mills in several mining operations Then, we show how this model was on the The Evolution of Grinding Mill Power Models Mining,
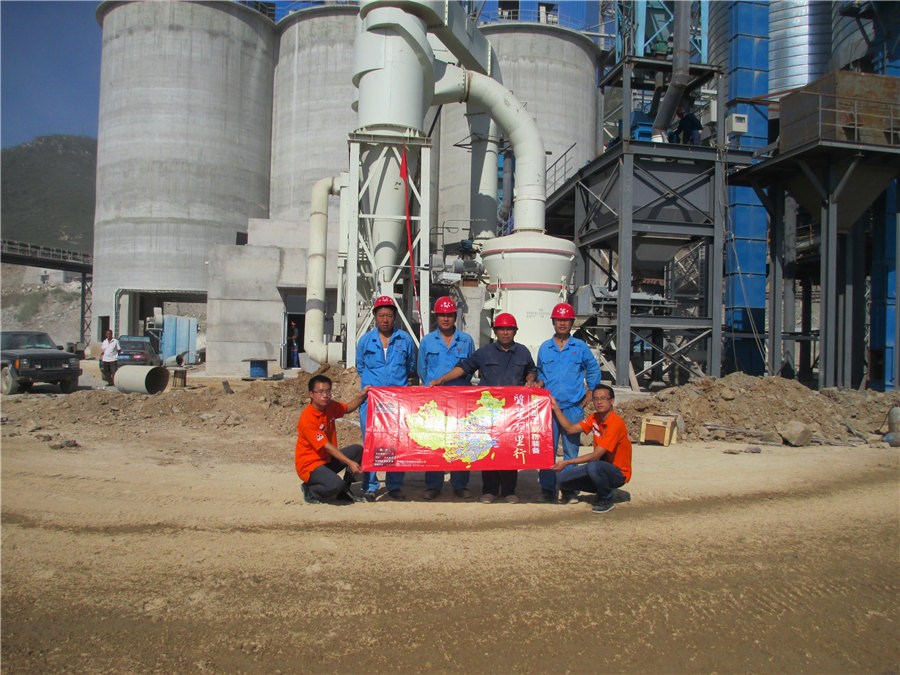
Study of the Grinding Process by Friction of Cereal Grains in
2023年12月6日 The grinding process via friction at the microscale in a mill with stones is considered a variable combination of contacts, with twobody (the asperities of lower millstone in direct contact with the asperities of upper millstone) and threebody (microparticles of ground seeds trapped between the asperities of lower and upper stones of the mill) contacts Three 2020年1月16日 Buzwagi Gold Mine (BGM) is operated by Acacia Mining and located in the Lake Victoria Goldfields of central Tanzania The mine commenced its operation since April 2009 and treats a sulphide copper (PDF) Optimization and performance of grinding circuits: the 2017年6月2日 Autogenous grinding (AG) and semiautogenous grinding (SAG) mills use the material to be ground as the grinding media Autogenous grinding mills use larger rocks to impact and break smaller rocks as the mill rotates How it Works: Crushers, Grinding Mills and PulverizersMetal Alloy Grinding Jar With Balls Grind and mill with ease using metal alloy grinding jars with balls Choose from 304/316L stainless steel or tungsten carbide and optional liner materials Compatible with various mills and features optional functionsWhat Is The Function Of Laboratory Grinding Mills? 4 Key Roles
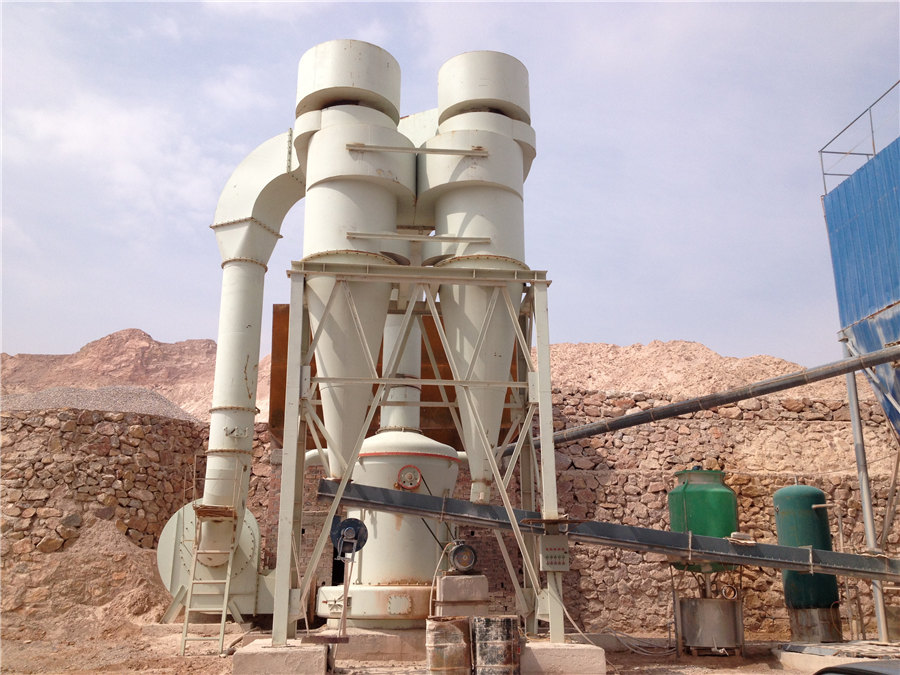
Analyzing the influence of lifter design and ball mill
2023年10月30日 Ball mills are the foremost equipment used for grinding in the mineral processing sector Lifters are placed on the internal walls of the mill and are designed to lift the grinding media (balls KINETICS OF GRINDING The progress of grinding as a function of time is described by the functions D(x, t) or R(x,t) with two variables Many theoretical papers investigated this problem but, however, no practicable formulae for industrial use has resulted For illustration we confine ourselves to mentioning an equation of batchKINETICS OF GRINDINGThe balls are 15 to 125 mm in diameter; the pebbles in a pebble mill are 50 to 175 mm in size A tube mill is a continuous mill contain a long cylindrical shell, excellent for grinding to very fine powders in a single pass The tube mill is converted into a Size Reduction1: Grinding – Unit Operations in Food Processing2017年5月8日 A lifter mill of 6 ft diameter, revolving at 187 rpm, is grinding coal The body of the mill is divided into two sections: one section, 75 ft long, being charged with 5 tons of steel balls, of 2 in average diameter, and the other section, 15 ft long, being charged with 6 tons of “Cylpebs” of 5/8 in average diameterGrinding Mill Power 911Metallurgist
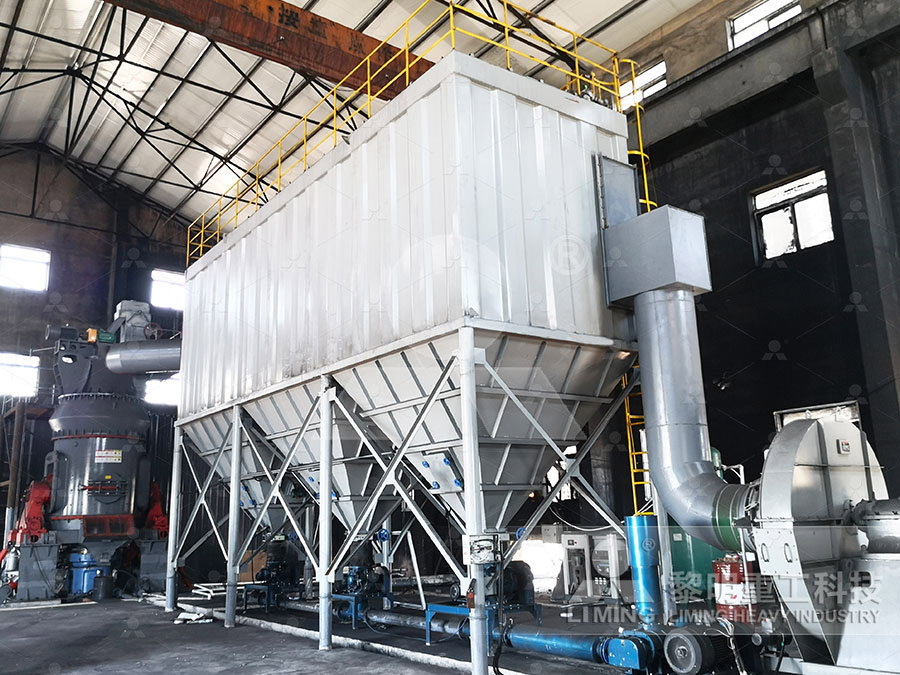
Determining Specific Grinding Rate of Coarse McGill University
Figure 1 Closed ball mill/cyclone circuit with example data at 105 µm (note amount is + or ) A Functional Performance Analysis Method (FPA) The defining equation from functional performance analysis is: Circuit Production Rate of Fines (CPRF, t/h) = Power Applied to Coarse Material (PAC, kW) × Specific Grinding Rate of Coarse (SGRC, t/KWh)The actual dispersion system in a bead mill consists of a milling chamber and an agitator; the milling chamber is filled with the grinding beads (material eg glass, zircon oxide, steel) and the product to be dispersed In the milling vessel, the grinding medium is kept moving by the agitator, which itself is driven by a motorIntroduction to the milling technology with the bead millGrinding Mills Barry A Wills, James A Finch FRSC, FCIM, PEng, in Wills' Mineral Processing Technology (Eighth Edition), 2016 71 Introduction Grinding is the last stage in the comminution process where particles are reduced in size by a combination of impact and abrasion, either dry, or more commonly, in suspension in waterGrinding Mill an overview ScienceDirect Topics2017年1月17日 Excessive mill speeds caused more power consumption but resulted in reduced grinding rate Based on the simulation data, two scaleup models were proposed to predict power draw and grinding rateBreaking down energy consumption in industrial grinding mills
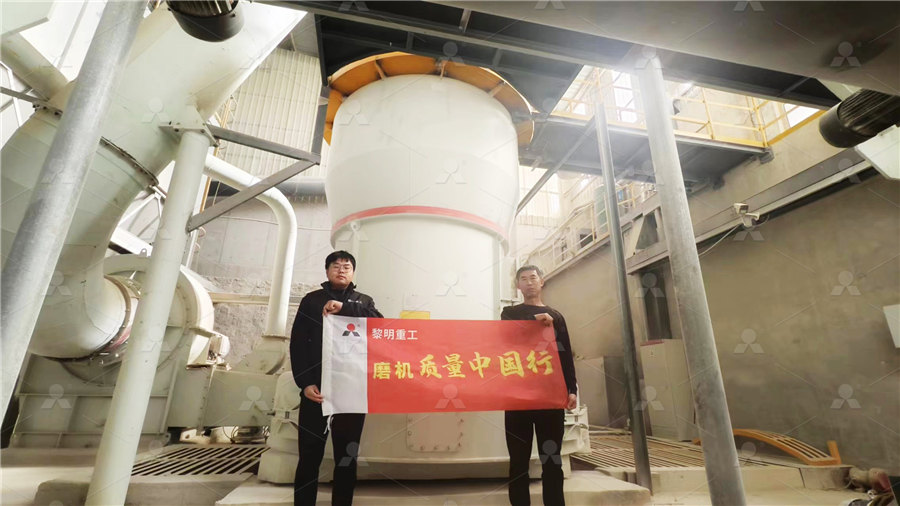
Analysis and Optimization of Grinding Performance of
2022年1月23日 VRM has the functions of grinding and powder selection, G A specific energybased size reduction model for batch grinding ball mill Miner Eng 2015, 70, 130–140 [CrossRef] 212 The innovative design of grinding chamber, the corn rough grinding (Ф30 sieve plate) efficiency improves 2030%, the corn grinding (Ф1012 sieve plate) efficiency improves 4070%, greatly reducing the grinder electricity The key functions and values of pellet mills and 2007年7月1日 Adjustment to ball size could lead to significant improvement in grinding mill throughput (McIvor, 1997)The Bond’s equation for ball sizing (McIvor, 1997) can help in selecting the ball size for a given ore and grinding millBall mill simulations with ball wear modelling can also be used to identify the optimum ball size (Concha et al, 1992) for a given applicationShould the slurry density in a grinding mill be adjusted as a function These machines function by using small grinding beads to disperse and reduce the size of particles in the substance being processed The main components of a bead mill machine include a grinding chamber, a rotor, a container to hold the material, and a motor to drive the rotorThe Role of Bead Mill Machines in Different Industries
.jpg)
Mill (grinding) Wikipedia
A mill is a device, often a structure, machine or kitchen appliance, that breaks solid materials into smaller pieces by grinding, crushing, or cutting Such comminution is an important unit operation in many processesThere are many different types of mills and many types of materials processed in them Historically mills were powered by hand or by animals (eg, via a hand crank), A crushing plant delivered ore to a wet grinding mill for further size reduction The size of crushed ore (F 80) was 40 mm and the SG 28 t/m 3 The work index of the ore was determined as 122 kWh/t A wet ball mill 1 m × 1 m was chosen to grind the ore down to 200 micronsGrinding Mill an overview ScienceDirect Topics2023年11月6日 PDF Grinding aids (GAs) are polar chemicals introduced in cement mills in either liquid or powder form to improve on mill grindability efficiency Find, read and cite all the research you (PDF) Review of the Effect of Grinding Aids and Admixtures on the 2007年7月1日 When the specifications and models of the ball mill are determined, the factors affecting the operation indexes of the grinding process include three facets [15–19]: one, the properties of the ore entering the grinding process, including the mechanical properties of the ore, the particle size distribution of the feed, and the required product fineness; second, the Should the slurry density in a grinding mill be adjusted as a function
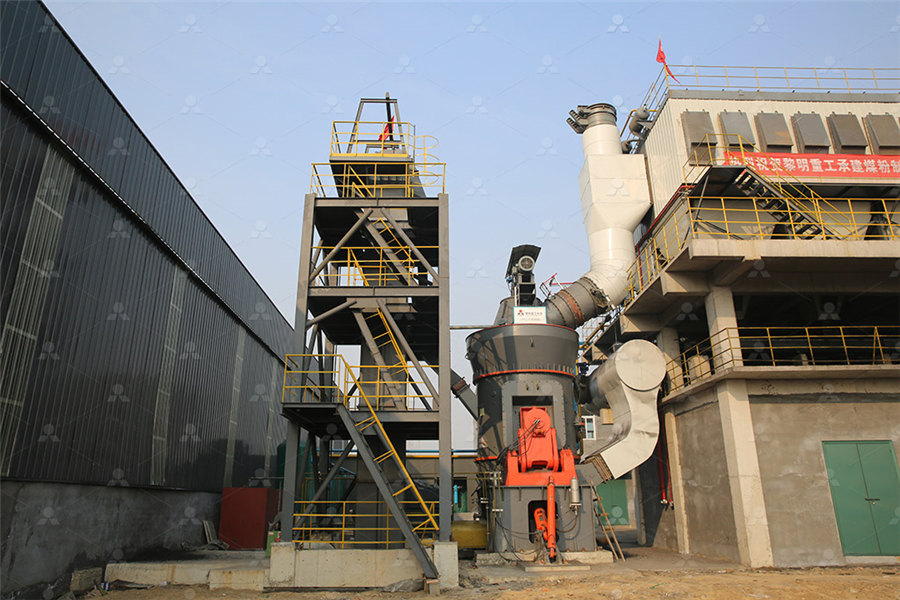
(PDF) Modelling of Grinding in an Air Classifier Mill Based on a
2003年1月1日 An approach to quantifying the impact grinding performance of different materials is presented Based on a dimensional analysis and on fracture mechanical considerations, two material parameters 2009年10月1日 Request PDF Batch Grinding in Laboratory Ball Mills: Selection Function The selection functions and the breakage distribution functions are based on the experimentallydetermined particle size Batch Grinding in Laboratory Ball Mills: Selection Function