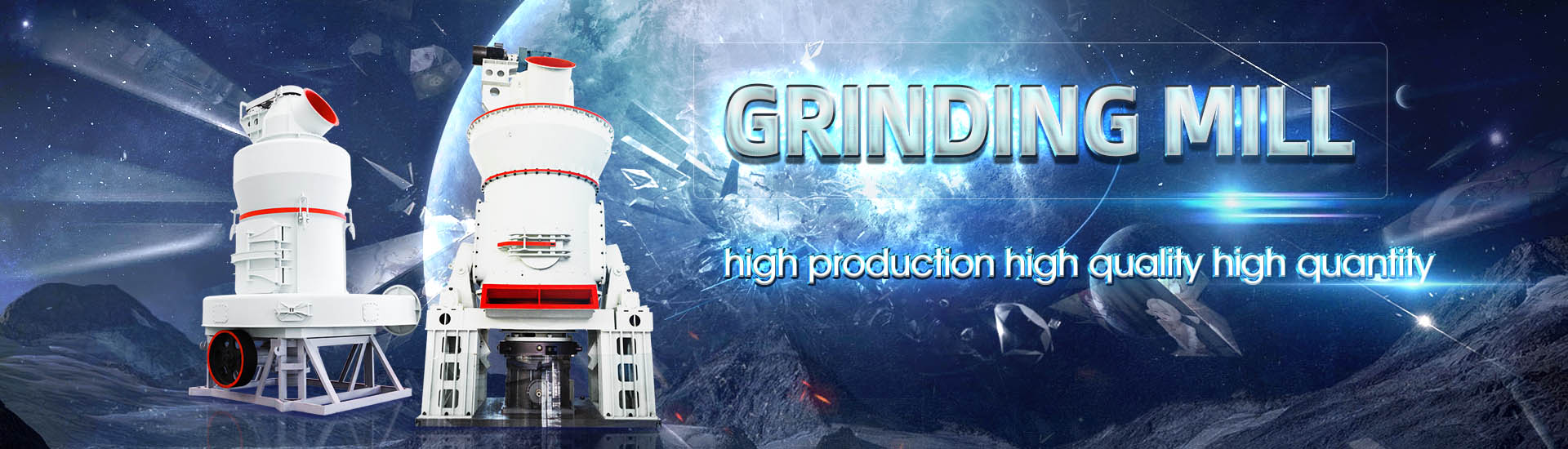
Xiaoma shear ore mill
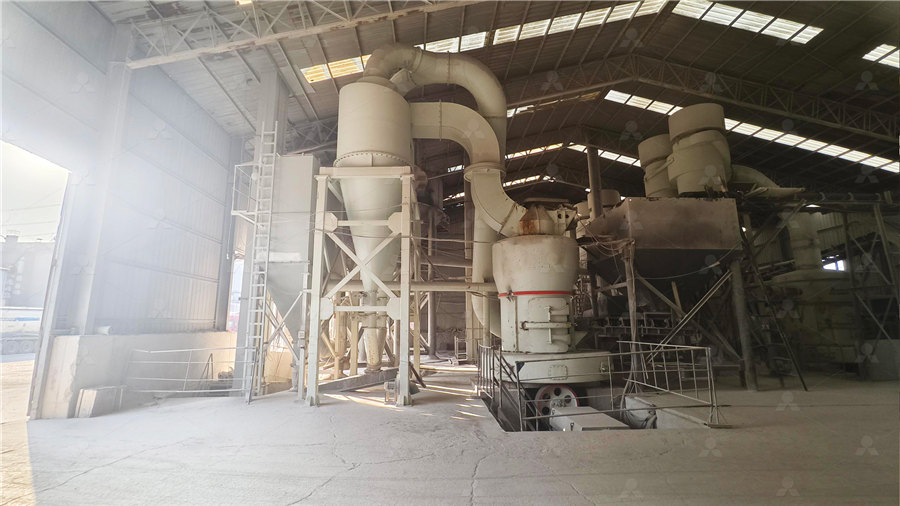
Original Research PaperBreakage process of mineral processing
2020年9月1日 Ore texture heterogeneity affects minerals breakage mode Shifting the particle breakage to nonrandom breakage mode improves liberation Microprocesses in breakage 2020年6月1日 Stirred media mills are used by the mining industry for ultrafine grinding to enhance liberation, and to decrease particle sizes of industrial minerals to tailor functional Stirred media mills in the mining industry: Material grindability The several types of crushers and mills available (Wills and Finch 2015) mainly differ by the stress mechanism and energy intensity they apply to ore particles, as summarised in Table 1 The All About Particles: Modelling Ore Behaviour in Mineral Elements2023年10月27日 Grinding media play an important role in the comminution of mineral ores in these mills This work reviews the application of balls in mineral processing as a function of the A Review of the Grinding Media in Ball Mills for Mineral Processing
.jpg)
Fine grinding: How mill type affects particle shape characteristics
2017年9月1日 The objective of this work is to assess the influence of fine grinding in ball mills and stirred mills on valuable mineral liberation and particle shape characteristics of UG2 ore, a 2020年5月1日 Stirred media mills are used by the mining industry for ultrafine grinding to enhance liberation, and to decrease particle sizes of industrial minerals to tailor functional Stirred media mills in the mining industry: Material grindability 2019年4月12日 高压辊磨机能量利用率高,目前已在水泥行业、金属矿山、冶金球团等领域广泛应用。 结合当前研究成果及工业现场数据,本文对比了高压辊磨机在金属矿山和球团预处理 高压辊磨机在金属矿选矿与球团预处理领域的工艺和 2024年1月1日 Stirred mill relies on highintensity stirring action to effectively drive small grinding medium, and forms multiple compressed rotating media layers, generating pressure and Stirred Mill SpringerLink
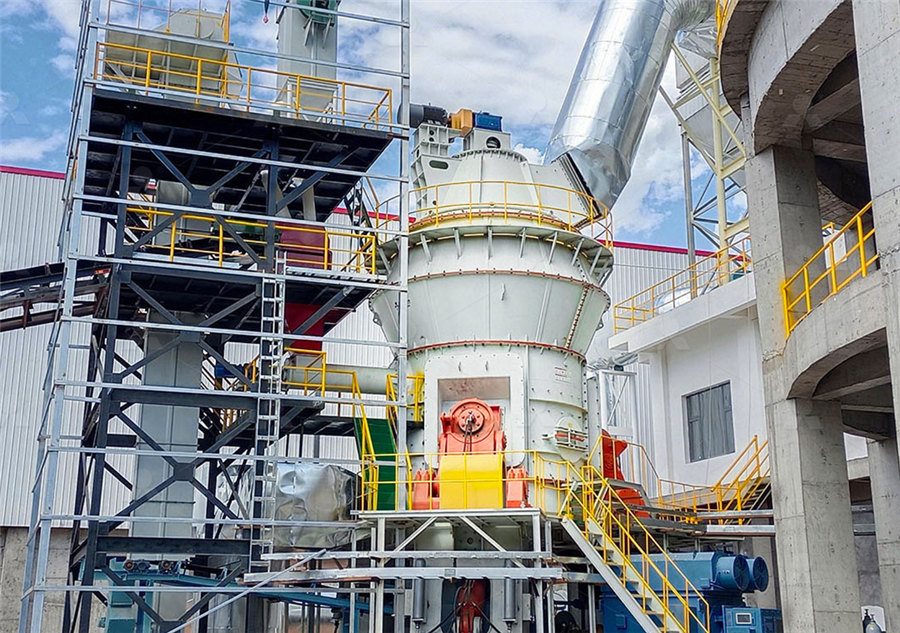
SBM Iron ore grinding plant for ores milling process
Ore grinding can be divided into grinding with media and without It can also be divided into dry grinding and wet grinding SBM can offer ball mill, raymond mill, roll mill used as iron ore Modes of size reduction: atwosided compression, bshearing, conesided impact [] Comparison of dry and wet grinding process in an electromagnetic mill is presented in this Modes of size reduction: atwosided compression, bshearing This also results in cost reduction and saving for the overall steel rolling mill By reducing waste, shearing machines assist in improving the total profitability of the steel rolling mill 5 Increased Safety Shearing machines operate with safety Everything You Need To Know About Shearing 2021年1月22日 To evaluate the net energy consumption of the stirred mill, the specific energy input [26,27] E m (kWh /t) was calculated as follows: E m = ∫ P t − P 0 dt m Where P(t) is the mean power of the stirred mill at each sampling time, kW; P 0 is the mean power of the stirred mill under no load (no water, grinding media and material), kW; t is grinding time,Impact of ball filling rate and stirrer tip speed on milling iron ore
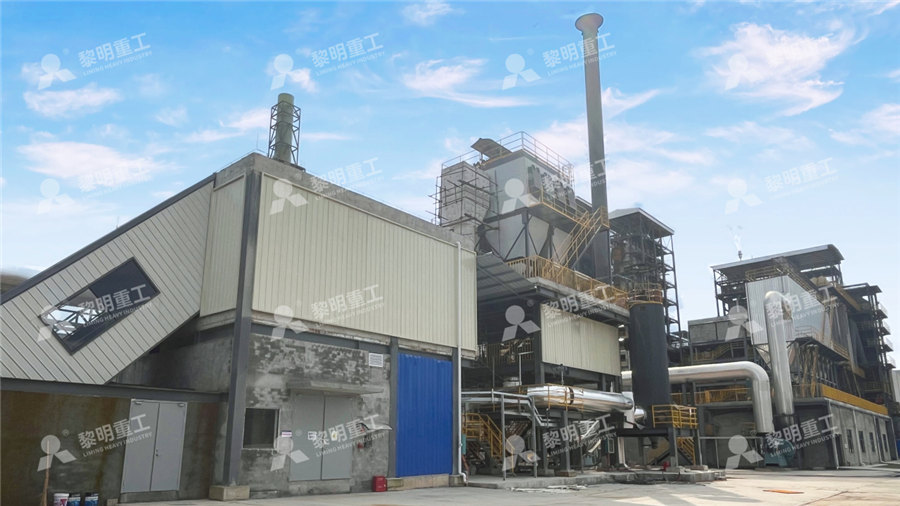
Three Roll Mill and The Potential Applications
Therefore, in comparison to the threeroll mill, it allows utilization of the larger agglomerates as the input material's part but it is more costly and complicated A ThreeRoll Mill’s Operation Rotation of the three roll mill’s three adjacent rolls 2022年1月1日 The wear volume of the material removed by a particle during an impact, V wear, can be given as: (22) V wear = E shear e c = E shear 40 p (23) E shear = − ∫ t 0 t 1 F c, t, i j v t, i j d t where E shear is the shear impact energy, e c is the cutting wear specific energy, and p is the plastic flow pressure of the target surface [58, 59]Investigation of the ball wear in a planetary mill by DEM simulation carried out on the cemented rodmill sand backfill (CRB) and oreCRB (OCRB) coupling specimens at various temperatures (20, 40 and 60 °C) The shear behavior and AE characteristic parameters of OCRB at different shear directions were compared and analyzed The results show that the temperature effect on the shear performance of CRBTemperature effect on shear behavior of orebackfill Springer2011年2月1日 Request PDF Understanding fine ore breakage in a laboratory scale ball mill using DEM DEM models of fine grinding in ball and stirred mills have to date almost entirely focused on the motion Understanding fine ore breakage in a laboratory scale ball mill using
.jpg)
Shear based stirred mill power model – An adimensional analysis
2015年3月15日 Riley et al investigated the stress frequency and stress energy in a stirredmedia mill using positron emission particle tracking [28] and defined the kinetic energy for a vertical stirredmedia mill at different tip speeds Shearbased power models compare the mill with a rheometer and predict the power draw and the wear behavior of the rotor It is almost impossible to describe, let alone do justice to, the variety of processes that have been used to mill ore The importance of mills cannot be understated since no money was made until the minerals were stripped of their metal values by the mill A good metallurgist or mill man was literally worth their weight in bullionWinning the Metal: Ore Mills of the West Western Mining History2021年10月1日 Understanding the temperature effect on shear behavior of the orebackfill coupling structure is critical for the safety and stability of backfill stope under the condition of high horizontal Temperature effect on shear behavior of orebackfill coupling The IsaMill™, as shown in Figure 815, is a horizontal stirred mill consisting of a series of 7–8 rotating grinding disks mounted on a cantilevered shaft that is driven through a motor and gearbox The disks operate at tip speeds of 21–23 m/s, resulting in energy intensities of up to 300 kW/m 3The mill is filled with suitable grinding media, and the space between each of the disks Stirred Mill an overview ScienceDirect Topics
.jpg)
Roller Mill SpringerLink
2023年7月4日 Roller mill is a type of grinding equipment for crushing materials by which is subjected to pressure and shear force It has the advantages of a large processing capacity, easy and has been widely applied in cement, steel and power industry, the preparation of nonmetallic ore ultrafine powder, manganese ore fine 2002年1月22日 For discussing the slip problem, the shear–pressure ratio τ/p has to be considered, which is plotted in Fig 4 for the same feed fraction stressed with the three specific milling forces of 25, 41 and 54 N/mm 2This ratio is smaller than 03 in the compression zone (α0)If the material would slip, then Shear stresses and material slip in high pressure roller millsHow It Works Boston Shearmills are constructed of a multislot rotor turning at high speeds in close proximity to a multiport stator Each shear head of the homogenizer consists of a rotor and stator, each with a double ring design This results in three distinct, high intensity work zones at each rotor / stator location where the mixture passes: Hygienic Boston Shearmill High Intensity Wet Mill Inline Admix2011年2月1日 In contrast, for SAG mills which were first modelled by Rajamani and Mishra (1996) and subsequently by others (Cleary, 2001a, Cleary, 2001c, Herbst and Nordell, 2001, Morrison et al, 2001, Morrison and Cleary, 2008) at least some fraction of the rock ore has been included Cleary (2004) showed that modelling the complete mill with 95% of the rock size Understanding fine ore breakage in a laboratory scale ball mill using
.jpg)
DEM investigation of SAG mill with spherical grinding media
2021年7月1日 Among the collisions happened in the mill, collisions on ore directly affect the breakage and abrasion of ore, including the oreore, oremedia, and oreliner collision The collision energy on ore is discussed from the relationship between collision energy and collision frequency and energy dissipation rate, as shown in Fig 11 a and Fig 11 b2019年4月16日 Conference: Applying a Successful Technology from the Cement Industry: Advantages of Grinding Ore in a VerticalRollerMill; At: Antalya, Türkey(PDF) LEARNING FROM OTHER INDUSTRIES; WHY THE VRMHowever, ore below the pay limit adds variation to the mill grade as increased mill throughput will be required to make up for the loss of gold, and that impacts on the recovery in the plant It is against these perspectives and findings of this study that the MCF should be seen as a method that identify the real problems underground and when these are addressed, the profitability of Monitoring ore loss and dilution for minetomill integration in Model HSP high shear pump The high capacity HSP model is ideal for inline blending, product smoothing, and deagglomerating poorly dispersed powders Wet milling of friable solids in suspension is even possible The selfpumping design of the rotor and stator elements eliminates the need for a separate process pump Model HSM high shear millHigh Shear Pump/High Shear Mill Ebara Mixers
.jpg)
Effect of Ball Mill Parameters’ Variation on the Particles of a
2021年10月21日 The economic and technical values of the hydrometallurgical or leaching processing are a function of its reaction rates and these reaction rates are enhanced by mechanical activation (MA) in hydrometallurgical processing This study presents a novel derived theoretical model for MAassisted leaching in investigating the effects of ball mill parameters 2022年5月23日 Grinding experiments were conducted in a laboratoryscale stirred mill on a lowgrade PGE bearing chromite ore HighPressure Grinding Rolls (HPGR) product of −1 mm was used as feed material to (PDF) Modeling and application of stirred mill for the coarse 2015年4月15日 Discharge from each mill Feed to each classification stage Oversize from each classification stage Fines from each classification stage, k Power drawn by each mill (motor input) Motor and drive efficiency of each What Ore Testing is Required For Mill SelectionThe rod mill is another type of grinding mill used in the copper ore mining process This machine uses steel rods as the grinding media instead of balls, which are commonly used in ball mills The rods grind the ore by tumbling Understanding the SAG Mill in Copper Ore Mining
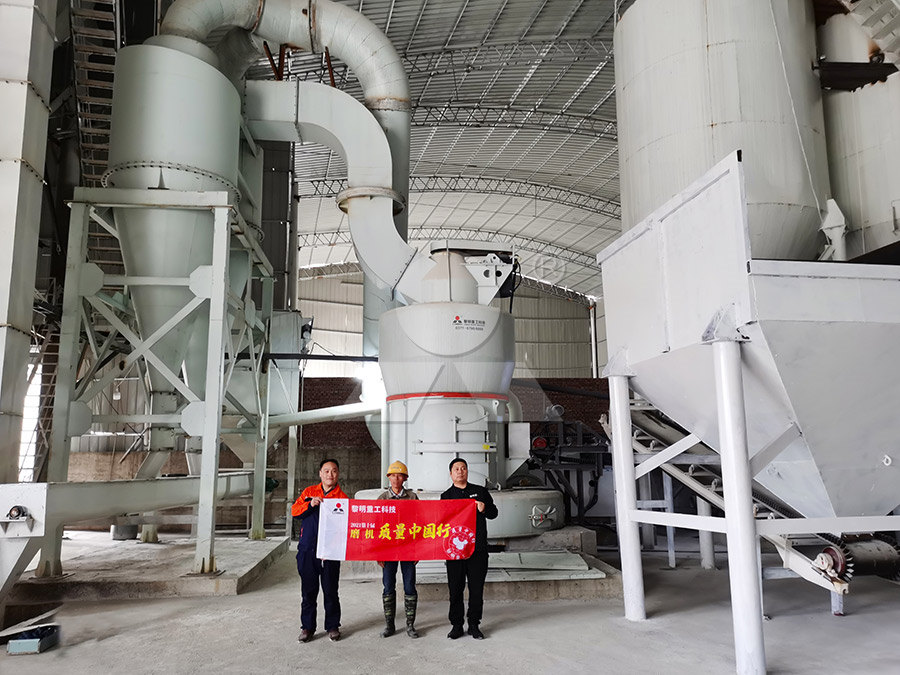
Ore Shoots and How to Trace Lode Veins Blogger
2013年3月28日 Ore shoots are areas in veins where valuable mineralization increases, often dramatically It has always been a subject of economic geology to try to understand where these rich shoots form and why, so miners can The vertical roller mill has the advantages of low energy consumption, high output, easy maintenance, etc, and has been widely applied in cement, steel and power industry, the preparation of nonmetallic ore ultrafine powder, manganese ore fine grinding, and other fields Horizontal Cylinder Roller MillRoller Mill SpringerDOI: 101016/JMINENG201502011 Corpus ID: ; Generalizing a shear–volume power model for stirred mill power prediction @article{Martins2015GeneralizingAS, title={Generalizing a shear–volume power model for stirred mill power prediction}, author={Sudarshan Martins and Peter H Radziszewski}, journal={Minerals Engineering}, Generalizing a shear–volume power model for stirred mill power 2017年11月1日 An iron ore mill relies on the grinding and impact of grinding balls to complete iron ore crushing The operating process of an iron ore mill is as follows: first, the ores are poured into the mill, and both the ores and the grinding balls are lifted by the lifting bar arranged on the wall of the cylinder body to a certain height, after which they fall onto the bottom of the mill to Friction and wear of liner and grinding ball in iron ore ball mill
.jpg)
Fine grinding: How mill type affects particle shape characteristics
2017年9月1日 The first stirred mill was installed in the platinum industry in 2002, and by the year 2010, forty stirred mills had been installed at various platinum operations in South Africa, and these led to a step change in flotation recoveries (Rule, 2011, Rule, 2010)Over the last decade, approximately 200 Automated Scanning Electron Microscopy (AutoSEMEDS) systems have 2017年6月15日 To this end, a laboratoryscale ball mill was used to evaluate the variation of wear process of the lifter in different milling conditions of mill speed, ball filling, grinding media size and shapeFriction and wear of liner and grinding ball in iron ore ball millTable 2 general SAG mill circuit and ore data Specification Data Operating circuit Closedcircuit Operating mill ball charge 15 percent by volume Operating mill total charge 32 percent by volume Mill speed 1008 RPM (76 percent of critical speed average) Ore specific gravity (sg) 277 Ore bulk density 164 tonnes/m3Paper # 25 Copper Mountain Overview on the Grinding Mills and In the mill, the mixture of medium, ore, and water, known as the mill charge, is intimately mixed, the medium comminuting the particles by any of the above methods Apart from laboratory testing, grinding in mineral processing is a continuous process, material being fed at a controlled rate into one end of the mill and discharging at the other end after a suitable dwell (residence) timeGrinding Mill an overview ScienceDirect Topics
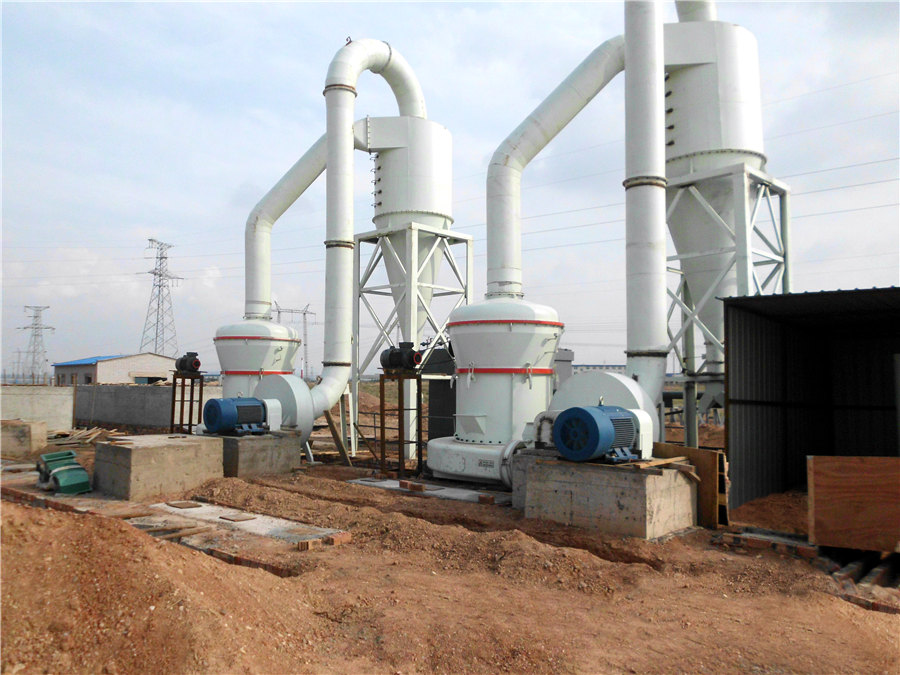
Everything You Need To Know About Shearing
This also results in cost reduction and saving for the overall steel rolling mill By reducing waste, shearing machines assist in improving the total profitability of the steel rolling mill 5 Increased Safety Shearing machines operate with safety 2021年1月22日 To evaluate the net energy consumption of the stirred mill, the specific energy input [26,27] E m (kWh /t) was calculated as follows: E m = ∫ P t − P 0 dt m Where P(t) is the mean power of the stirred mill at each sampling time, kW; P 0 is the mean power of the stirred mill under no load (no water, grinding media and material), kW; t is grinding time,Impact of ball filling rate and stirrer tip speed on milling iron ore Therefore, in comparison to the threeroll mill, it allows utilization of the larger agglomerates as the input material's part but it is more costly and complicated A ThreeRoll Mill’s Operation Rotation of the three roll mill’s three adjacent rolls Three Roll Mill and The Potential Applications2022年1月1日 The wear volume of the material removed by a particle during an impact, V wear, can be given as: (22) V wear = E shear e c = E shear 40 p (23) E shear = − ∫ t 0 t 1 F c, t, i j v t, i j d t where E shear is the shear impact energy, e c is the cutting wear specific energy, and p is the plastic flow pressure of the target surface [58, 59]Investigation of the ball wear in a planetary mill by DEM simulation
46.jpg)
Temperature effect on shear behavior of orebackfill Springer
carried out on the cemented rodmill sand backfill (CRB) and oreCRB (OCRB) coupling specimens at various temperatures (20, 40 and 60 °C) The shear behavior and AE characteristic parameters of OCRB at different shear directions were compared and analyzed The results show that the temperature effect on the shear performance of CRB2011年2月1日 Request PDF Understanding fine ore breakage in a laboratory scale ball mill using DEM DEM models of fine grinding in ball and stirred mills have to date almost entirely focused on the motion Understanding fine ore breakage in a laboratory scale ball mill using 2015年3月15日 Riley et al investigated the stress frequency and stress energy in a stirredmedia mill using positron emission particle tracking [28] and defined the kinetic energy for a vertical stirredmedia mill at different tip speeds Shearbased power models compare the mill with a rheometer and predict the power draw and the wear behavior of the rotor Shear based stirred mill power model – An adimensional analysisIt is almost impossible to describe, let alone do justice to, the variety of processes that have been used to mill ore The importance of mills cannot be understated since no money was made until the minerals were stripped of their metal values by the mill A good metallurgist or mill man was literally worth their weight in bullionWinning the Metal: Ore Mills of the West Western Mining History
.jpg)
Temperature effect on shear behavior of orebackfill coupling
2021年10月1日 Understanding the temperature effect on shear behavior of the orebackfill coupling structure is critical for the safety and stability of backfill stope under the condition of high horizontal The IsaMill™, as shown in Figure 815, is a horizontal stirred mill consisting of a series of 7–8 rotating grinding disks mounted on a cantilevered shaft that is driven through a motor and gearbox The disks operate at tip speeds of 21–23 m/s, resulting in energy intensities of up to 300 kW/m 3The mill is filled with suitable grinding media, and the space between each of the disks Stirred Mill an overview ScienceDirect Topics