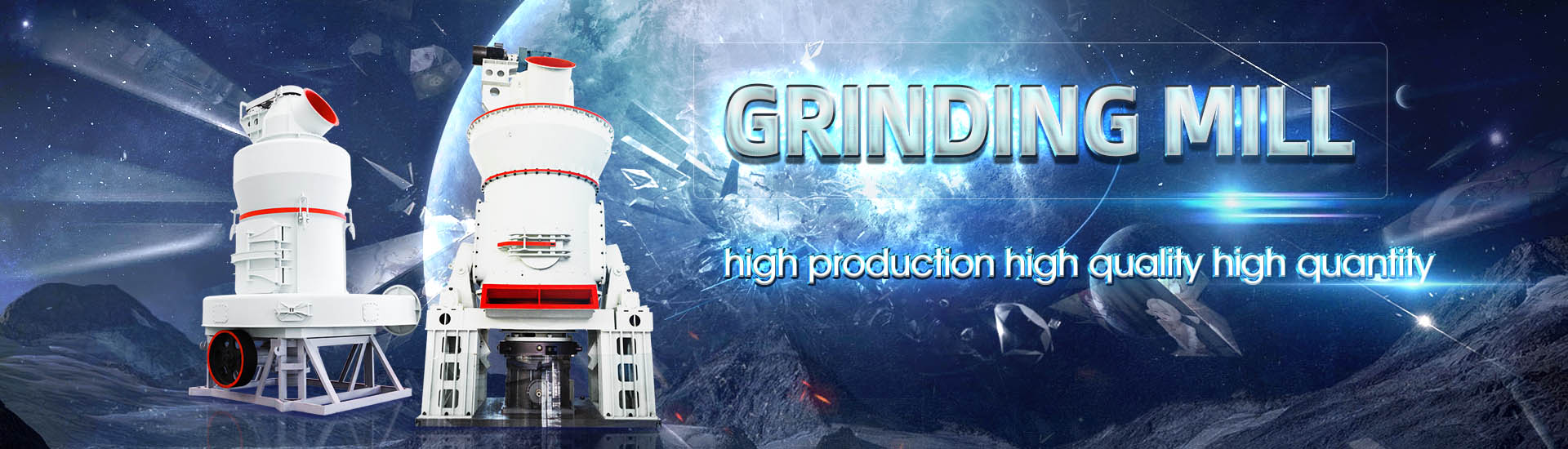
Grinding capacity and cost
.jpg)
Economics of Grinding for Pelleted Feeds CPM
Maintenance costs for roller mills are generally higher on a per ton basis, typically ranging from $005 to $009 per ton depending on the size of the machine and the finished particle size 2006年6月1日 Highperformance grinding is essential to achieve high dimensional accuracy and surface integrity of ground components at optimum cost efficiency The objectives of this paper Highperformance grinding—A review ScienceDirect2022年6月24日 Grinding is a manufacturing process which significantly contributes in producing high precision and durable components required in numerous applications such as aerospace, (PDF) A comprehensive review on the grinding process: 2015年6月19日 Use this online calculators for Motor Sizing and Mill sizing as well as mill capacity determinators In extracting from Nordberg Process Ball Mill Design/Power Calculation 911Metallurgist
.jpg)
Reducing Grinding Energy and Cost ResearchGate
Historically, the lowest operating cost for fine grained ores was achieved by multi stage fully autogenous grinding (Koivistoinen et al, 1989) with integrated magnetic separation steps 2024年11月1日 To address this gap, this paper introduces an optimization method for grinding process parameters that considers carbon emissions and seeks to balance emissions, time, Grinding process optimization considering carbon emissions, cost Size reduction, or comminution, by mechanical crushing and grinding is an important unit operation in the chemical, power, mineral, metallurgical, and pharmaceutical industries Hammer Milling and Jet Milling Fundamentals AIChE2018年1月1日 Grinding is an essential technology used for finishing operations of many precision components, especially such made of hard and brittle materials This work presents Energy efficiency of stateoftheart grinding processes
.jpg)
HIGH PRESSURE GRINDING ROLLS—A PROMISING AND COST
high pressure grinding rolls technology, are the technically and economically viable solution to challenges that mining and processing industry faces or will face soon From the practical evi A good rule of thumb is that an integrated mining crushinggrinding plant will have capex costs of $20/Tpa of capacity and consume 20kWh of energy per ton, while total fullcycle costs will run close to $10/ton of ore that is processed Mining crushing grinding costs Thunder Said EnergyThe primary benefit of rebuilding existing equipment is cost: Rebuilt grinding machines cost roughly 75% of the sticker price of new equipment The finished machine looks, works and produces like new, with recommissioned geometry, renewed guideways and enhanced precision In addition, the rebuilding process canTHE ACQUISITION OF GRINDING TECHNOLOGY: REBUILD, 2018年1月1日 Grinding is an essential technology used for finishing operations of many precision components, ABC; TDABC; Capacity Management; Idle Capacity; Operational Efficiency 1 Introduction The cost of idle capacity is a fundamental information for companies and their management of extreme importance in modern production systemsEnergy efficiency of stateoftheart grinding processes
.jpg)
Reducing grinding energy and cost — magnetite iron ore design case
Efficiency of the comminution operations is traditionally assessed based on operating cost and energy consumption Traditionally, the lowest operating cost was achieved by multi stage fully autogenous grinding due to elimination of steel grinding media costs which may represent up to 50 % of the grinding cost Significant reduction of the cost associated with grinding was June 2022; ARCHIVE Proceedings of the Institution of Mechanical Engineers Part C Journal of Mechanical Engineering Science 19891996 (vols 203210) 236(2):1107(PDF) A comprehensive review on the grinding process: 2021年9月28日 However, regrinding services can also be offered to third parties if excess capacity is on hand Costs for a Tool Grinding Machine can be Justified by High Quantities The target audience for tool regrinding is high volume manufacturers who consume many tools, such as automotive and aerospace suppliersRegrinding Tools Yourself: Save Time and Money UNITED GRINDING2024年2月27日 These burrs enable the DK27 LVH to grind up to 616 pounds per hour This capacity is a gamechanger for wholesalers and small roasteries that require efficient processing of large coffee batches Such a high grinding capacity ensures you can meet increased demands without sacrificing grind quality11+ Best Commercial Coffee Grinders In 2024 Tim's Coffee
.jpg)
Calculate Ball Mill Grinding Capacity 911Metallurgist
2015年10月15日 Learn how to calculate the grinding capacity of your ball mill with 911 Metallurgist This guide provides essential formulas, insights, and tips to optimize your milling process and enhance production efficiency2024年2月29日 Factors such as machine size, spindle speed, grinding wheel capacity, and the system’s automation capabilities are crucial in making an informed decision CNC grinding turns into a costeffective method in the long run as a What Is CNC Grinding? The Future Of Machine Processing2023年2月13日 They are also often located closer to the source of raw materials, reducing transportation costs However, clinker grinding plants are limited in their production the decision should align with the project goals and take into consideration all relevant factors such as cost, capacity, location, and market demand Facebook Differences between Clinker Grinding Plant and Cement Plant 2016年10月12日 An approximate guide to grinding costs; they are direct costs and include no overhead charges Power is assumed to cost 0075 per kilowatthour in the case of the smallest plant and to decrease to a minimum per Closed Circuit Grinding VS Open Circuit Grinding
.jpg)
Understanding CNC Grinding: Materials, Types Cost
2024年6月9日 This is a beginner guide explaining fundamental concepts of CNC grinding You will real bird view of CNC grinders, grinding materials, types, and cost Also check top grinding machines manufacturers in the world2022年2月28日 It has been reported that the wet grinding capacity generally is approximately 13 times greater than the dry environment under This technology has considerable advantages such as reducing water consumption, energy requirement, steel usage cost, and increasing capacity That is why HPGR has gained a special place among size Grinding SpringerLinkGRINDING AND PACKING 20 2 TABLE OF CONTENTS PAGE I SUMMARY 20 3 II PRODUCT DESCRIPTION AND APPLICATION 20 3 The estimated annual requirement for gumming paper and respective cost estimates at 100 per cent capacity utilization rate are given in Table 45 Table 45 ANNUAL REQUIREMENT FOR GUMMING PAPER AND THEIR COST COFFEE ROASTING, GRINDING AND PACKING Embassy of Estimating the power required by a grinding mill is then particularly interesting for industrial looking to invest in a new grinding process in order to define the CAPEX and OPEX costs The calculations below mainly apply to ore mills 1 Workindex What is the workindex of a mill ?Grinding power : step by step calculation PowderProcess
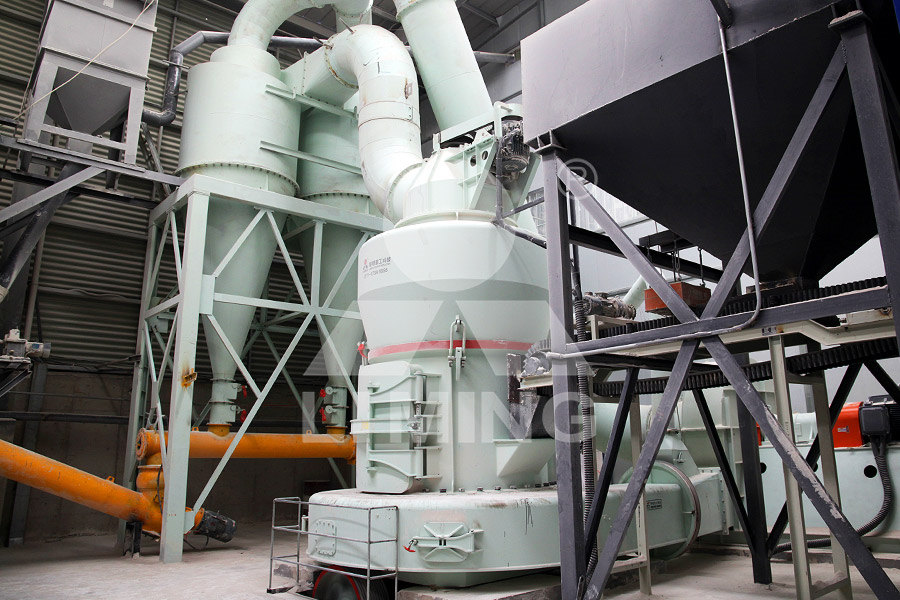
Internal Grinding Grind All Inc
Internal grinding is a precision process used to remove material committed to continuously add the most advanced equipment in the Industry to obtain the growing demand for accuracy and cost competitive pricing Capabilities Position within 0002; Our Internal Grinding capacity is listed below: 12 Okamoto CNC ID Grinders Capacity 2024年5月31日 This paper presents an industrial verification test, adding a high pressure grinding roll and magnetic separation operation after the thirdstage fine crushing operation to reduce the particle size of ball mill feed and improve the processing capacity of grinding operation The optimal process parameters of high pressure grinding roll and magnetic separation were High Pressure Grinding Roll and Magnetic Separation for Energy 2016年1月11日 The power cost falls as the size of the plant increases up to a capacity of about 2,000 tons per day on account of the fact that large machines are more economical as regards power up to a capacity of about 250 tons per hour ; single machines are made to handle greater tonnages than this, but their power consumption per ton crushed shows no appreciable savingCrusher Operating Costs: How to Optimize and Reduce2015年10月23日 In this chapter an introduction of widely applied energyefficient grinding technologies in cement grinding and description of the operating principles of the related equipments and comparisons over each other in terms of grinding efficiency, specific energy consumption, production capacity and cement quality are given A case study performed on a EnergyEfficient Technologies in Cement Grinding IntechOpen
.jpg)
Stump Grinding Costs: Factors, Estimates, and Considerations
2024年6月24日 Estimated Costs of Stump Grinding Average Cost Range On average, stump grinding costs between $100 to $400 per stump However, this can vary widely depending on the factors mentioned above and the local market rates Cost per Inch Some companies may charge based on the diameter of the stump, typically ranging from $2 to $4 per inch of stump 2019年1月1日 Between the grinding capacity and the value of HGI exists a Cost analysis based on the regression model indicate a power savings of $19,972 per year if the coal were ground to 50% Practical assessment of grinding capacity and power tance of roll faces aimed at saving of maintenance cost and at higher rate of equipment use even in processing of strong abrasive and highsilica ore These grinding rolls exhibited higher capacity and lower energy consumption than was expected A single Polycom24/17 treated over 3 thousand tons of goldbearing copHIGH PRESSURE GRINDING ROLLS—A PROMISING AND COST As one of the most professional eyw5 high efficiency large capacity pregrinding mill manufacturers and suppliers, we warmly welcome you to wholesale costefficient eyw5 high efficiency large capacity pregrinding mill for sale here EYW5 High Efficiency Large Capacity PreGrinding Mill
[GYQ0R)ZQ]ESS4NJ.jpg)
CAPTURING VALUE IN THE US CEMENT INDUSTRY WITH A GRINDING
are used by US integrated cement plants that are using their surplus grinding capacity to increase their cement production Figure 3 – Continued on Next page clinker and grinding is lower than the cost of importing cement, the grinding plants should be Rate of Removal – This is a measure of the grinding time versus the volume of material ground Thus, ‘G’ Ratio can be used to measure amount of abrasive used, and the Rate of Removal can be used to measure the machine time required Both have real costs associated with them and neither alone represents the cost of the operation However,blanchard grinding booklet 1 Jowitt and Rodgers2015年1月31日 From hubandspoke model to split grinding; from singlegrinding solution to a combination of system solutions; and from energyintensive traditional ball mill to upgraded versions and use of pregrinders, the cement industry is shifting towards more energyefficient grinding solutions ICR trains its spotlight on the current technology trends The cement Grinding Solutions Indian Cement ReviewCapacity) : 7123 Lakhs 17 Detailed Cost of Project Means of Finance COST OF PROJECT (Rs In Lakhs) Particulars Amount Land Own/Rented Building /Shed 1000 Sq ft Own/Rented Plant Machinery 986 Furniture Fixtures 125 Working Capital 444 Total 1555 MEANS OF FINANCE Particulars Amount Own Contribution 156 Term Loan 1000 Working Capital 400SPICE GRINDING UNIT

Potential Benefits of Underground Processing for the Gold Sector
the lower the cost of operation (eg power requirements) Traditional surface processing for gold recovery is designed to achieve recovery through ‘whole ore leaching’ This involves grinding 100 per cent of the ore into sub 50 75 micron particles With a highcapacity grinding chamber, It can help businesses reduce their waste disposal costs by recycling plastic waste into reusable materials In summary, the Heavy Duty Hdpe Plastic Scrap Grinder with the brand name ADIT is a reliable and efficient machine for grinding plastic scraps into smaller piecesPlastic Scrap Grinder Machine Pet Bottle Grinding Machine 2014年4月9日 Equipment throughput (material processed per hour), cost and energy consumption are important factors for all operations Moisture content is an important factor for typical grinding operations because increases in moisture correlate to grinding capacity and efficiency decreasesFull article: Optimizing hammer mill performance through A good rule of thumb is that an integrated mining crushinggrinding plant will have capex costs of $20/Tpa of capacity and consume 20kWh of energy per ton, while total fullcycle costs will run close to $10/ton of ore that is processed Mining crushing grinding costs Thunder Said Energy

THE ACQUISITION OF GRINDING TECHNOLOGY: REBUILD,
The primary benefit of rebuilding existing equipment is cost: Rebuilt grinding machines cost roughly 75% of the sticker price of new equipment The finished machine looks, works and produces like new, with recommissioned geometry, renewed guideways and enhanced precision In addition, the rebuilding process can2018年1月1日 Grinding is an essential technology used for finishing operations of many precision components, ABC; TDABC; Capacity Management; Idle Capacity; Operational Efficiency 1 Introduction The cost of idle capacity is a fundamental information for companies and their management of extreme importance in modern production systemsEnergy efficiency of stateoftheart grinding processesEfficiency of the comminution operations is traditionally assessed based on operating cost and energy consumption Traditionally, the lowest operating cost was achieved by multi stage fully autogenous grinding due to elimination of steel grinding media costs which may represent up to 50 % of the grinding cost Significant reduction of the cost associated with grinding was Reducing grinding energy and cost — magnetite iron ore design case June 2022; ARCHIVE Proceedings of the Institution of Mechanical Engineers Part C Journal of Mechanical Engineering Science 19891996 (vols 203210) 236(2):1107(PDF) A comprehensive review on the grinding process:
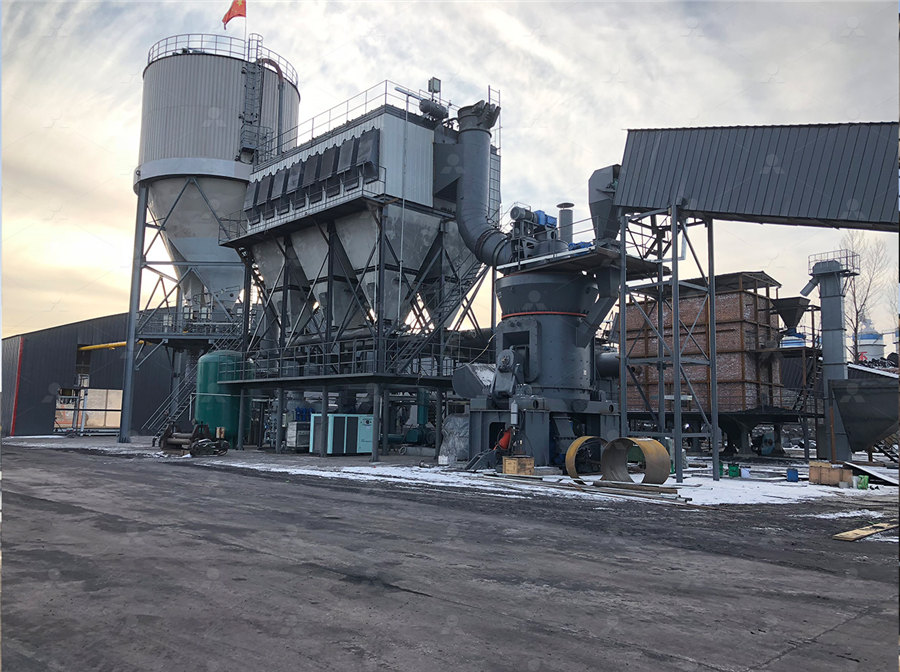
Regrinding Tools Yourself: Save Time and Money UNITED GRINDING
2021年9月28日 However, regrinding services can also be offered to third parties if excess capacity is on hand Costs for a Tool Grinding Machine can be Justified by High Quantities The target audience for tool regrinding is high volume manufacturers who consume many tools, such as automotive and aerospace suppliers2024年2月27日 These burrs enable the DK27 LVH to grind up to 616 pounds per hour This capacity is a gamechanger for wholesalers and small roasteries that require efficient processing of large coffee batches Such a high grinding capacity ensures you can meet increased demands without sacrificing grind quality11+ Best Commercial Coffee Grinders In 2024 Tim's Coffee2015年10月15日 Learn how to calculate the grinding capacity of your ball mill with 911 Metallurgist This guide provides essential formulas, insights, and tips to optimize your milling process and enhance production efficiencyCalculate Ball Mill Grinding Capacity 911Metallurgist2024年2月29日 Factors such as machine size, spindle speed, grinding wheel capacity, and the system’s automation capabilities are crucial in making an informed decision CNC grinding turns into a costeffective method in the long run as a What Is CNC Grinding? The Future Of Machine Processing
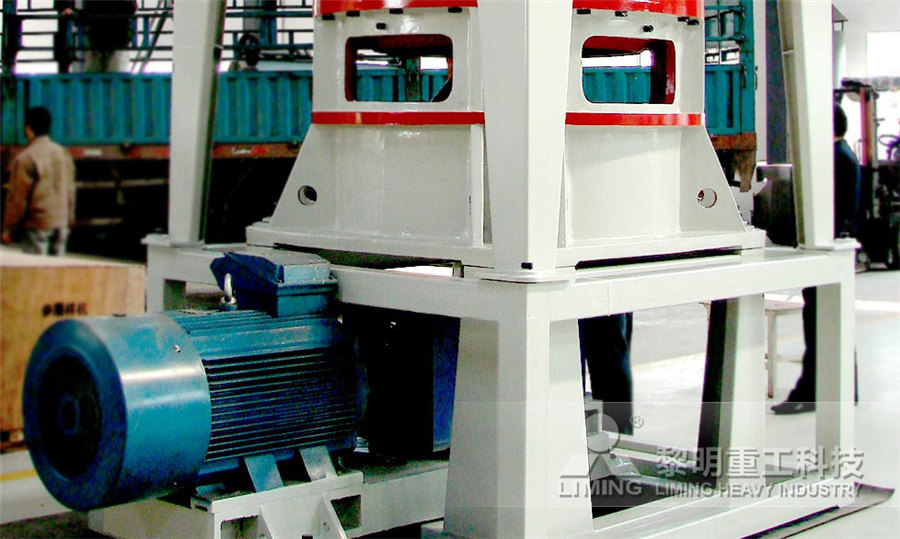
Differences between Clinker Grinding Plant and Cement Plant
2023年2月13日 They are also often located closer to the source of raw materials, reducing transportation costs However, clinker grinding plants are limited in their production the decision should align with the project goals and take into consideration all relevant factors such as cost, capacity, location, and market demand Facebook