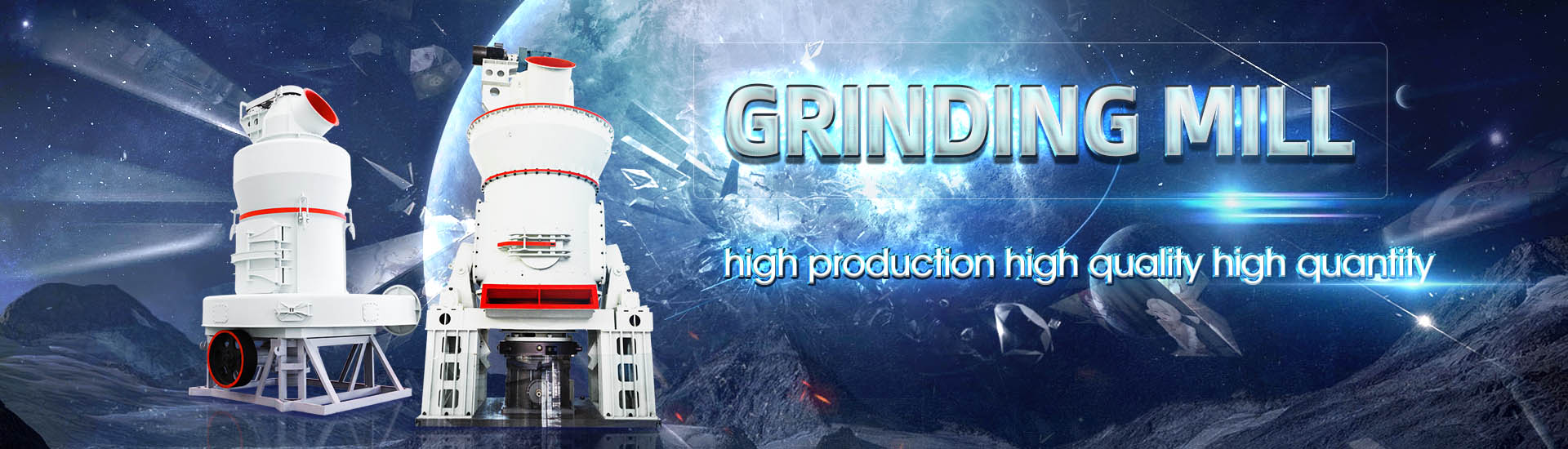
Coal mill output
.jpg)
Coal Mill an overview ScienceDirect Topics
Coal mills or pulverizers play a very essential part in the coalfired power production system Coal mills grind the coal into fine powder, and the primary air entering the mill dries and drives the coal into the power plant furnace for combustion Mills can be a bottleneck for the power generation Coal mill is an important component of the thermal power plant It is used to grind and dry the moisturized raw coal and transport the pulverized coal – air mixture to the boiler Poor dynamic Modeling and Control of Coal MillCoal mill is an important component of the thermal power plant It is used to grind and dry the moisturized raw coal and transport the pulverized coal – air mixture to the boiler Poor dynamic (PDF) Modeling and Control of Coal Mill Academia1997年8月1日 This paper describes the analysis results of the dynamic characteristics of coal grinding mills used in a large coalfired power generation unit The aim of the work is to Analysis of coal Mill Dynamic Characteristics Under Normal and
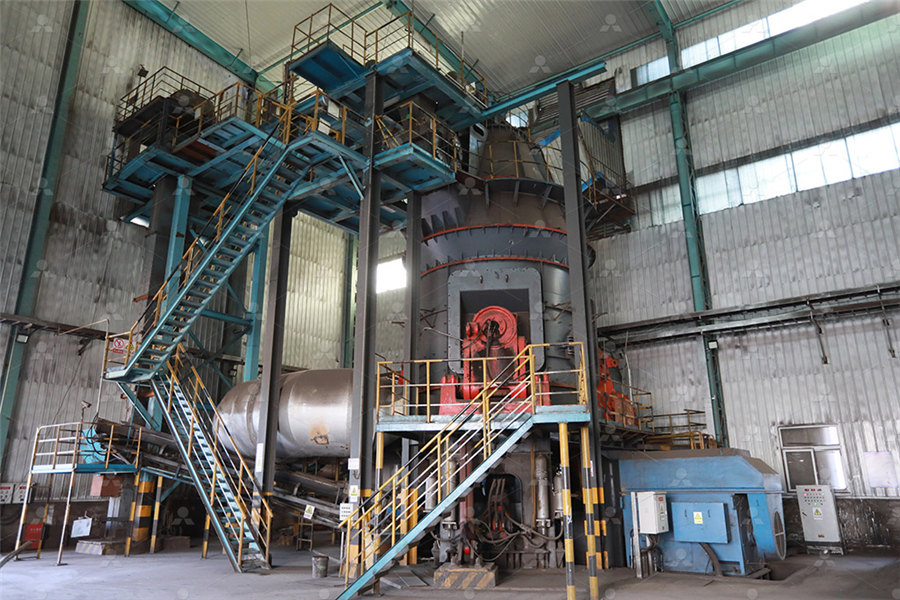
Derivation and validation of a coal mill model for control
2012年5月1日 The paper presents development and validation of a coal mill model to be used for improved mill control, which may lead to a better load following capability of power plants 2009年9月20日 This paper presents a novel coal mill modeling technique using genetic algorithms (GAs) based on routine operation data measured onsite at a National Power (NP) power station in the UKModeling and Parameter Identification of Coal Mill2020年8月12日 In a power plant, the coal mill is the critical equipment, whose effectiveness impacts the overall power plant efficiency Uniform coal feeding mass flow rate and required particle size andAn investigation of performance characteristics and 2020年8月12日 In a power plant, the coal mill is the critical equipment, whose effectiveness impacts the overall power plant efficiency Uniform coal feeding mass flow rate and required An investigation of performance characteristics and energetic
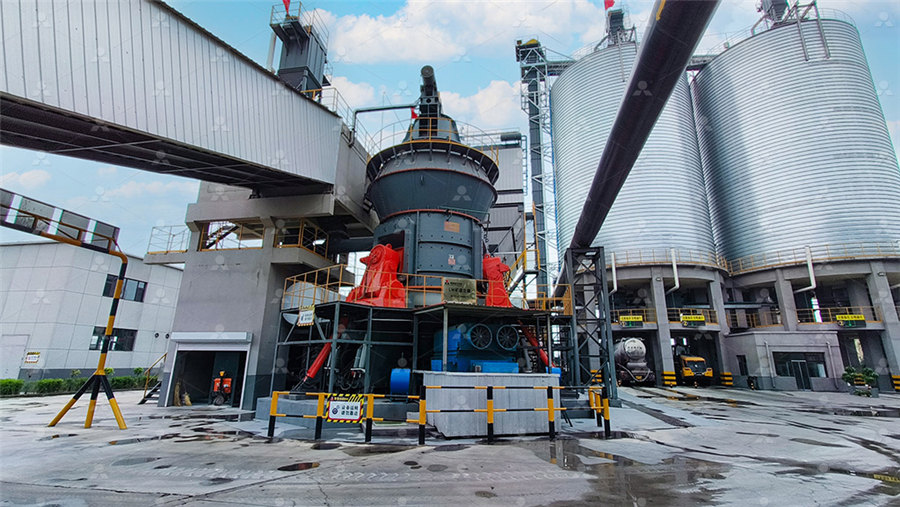
(PDF) Modeling and Control of Coal Mill Academia
Comparison of response of pulverized coal flow for a setpoint of 1 kg/sec in the presence of PID and MPC 40 C 100 C ACKNOWLEDGEMENT Output Outlet temperature We would like to thank the Control and Instrumentation department members of the North Chennai Thermal Power Plant for providing us the raw plant data which helped in modeling and 2021年2月15日 of double inlet and double outlet ball mill output system is established, and SPSS is used to fit the The coal mill model was developed and the unknown model coefficients were obtained System dynamics model of output of ball mill2012年5月1日 Sensors for coal flow measurement from the mill to the furnace have become available on the market (Blankinship, 2004, Department of Trade and Industry, 2001, Laux et al, 1999)Unfortunately the equipment tends to be expensive and requires frequent calibration; thus it cannot be used directly for control purposes at this time of writingDerivation and validation of a coal mill model for controlNote: 1 The basic output in the table refers to the grinding capacity of the coal mill under the working conditions of high volatile bituminous coal 8% and low volatile bituminous coal 12%, with the GHI of coal power of 55, coal fineness of 785% passing the 0075mm sieveHP Bowl type millspower plant equipment
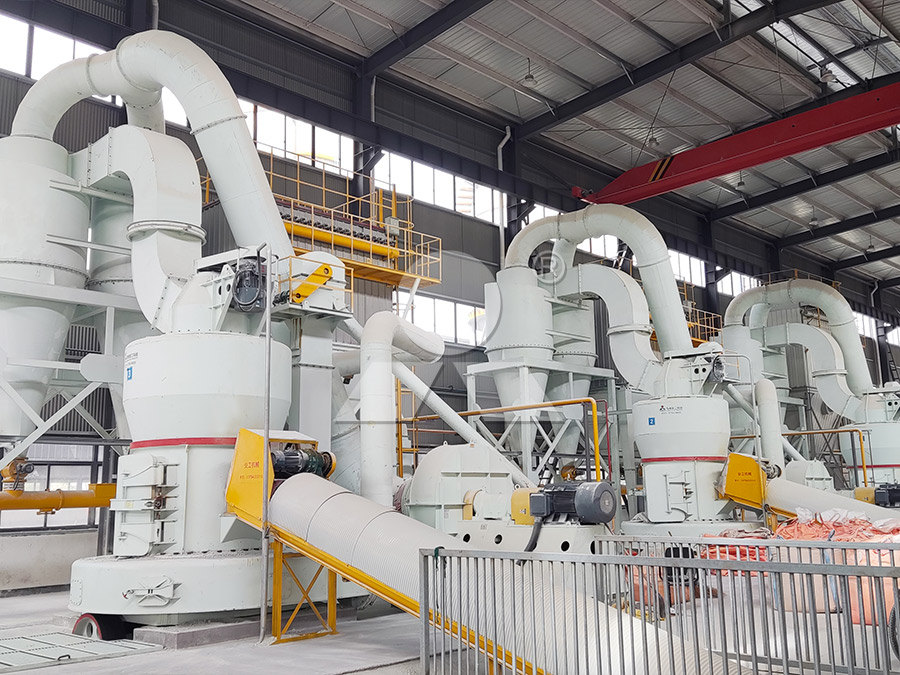
A unified thermomechanical model for coal mill operation
2015年11月1日 As presented by Andersen et al (2009) and Odgaard, Stoustrup, and Mataji (2007), coal moisture imposes limit on the maximum load at which a coal mill can be operated and the load gradient (how fast the mill may change its operating point), if it is desired that the pulverized coal entering the furnace has moisture content less than or equal to a certain value Ball mill coal pulverizing system is a multipleinput multipleoutput (MIMO) process characterized with strong couplings and nonlinearities Conventional control methods maybe work well initially, but will deviate from optimal work point for a period of time and even cease to be functionally effective A multilayer structure with direct control and optimization is presented for the control Coal Mill Control and Optimization Using a Multilayer StructureCoal grinding mills LOESCHE coal grinding mills are distinguished by characteristics that improve efficiency, safety and environmental protection, from the standard version to topoftherange installations Special versions are available with characteristics that meet special safety regulation or output control requirementsCoal Mills for Cement Plants LoescheIn this way a calibration curve is constructed which can eventually be used to forecast mill output with a new coal, from a measurement of the Index However, there are several defects of the test, two of which may be noted here as examples: Example 1 Batch versus continuous milling:COAL PREPARATION AND FIRING INFINITY FOR CEMENT EQUIPMENT
.jpg)
vertical roller mill, vertical coal mill, vertical slag mill, superfine
25TPH LM1700 Coal Grinding Mill Capacity: 2025T/H Output size: 200 mesh Calcium carbonate ultrafine vertical mill Capacity: 8T/H Output size: 3253000 mesh Get prices and discounts * * * * * * * * * Order Now 40 Yrs HistoryGrinding of coal, petcoke, clay, limestone, quicklime, gypsum, MPS 200 BK coal mill, Krimzement Bakhchisarayski, Ukraine MPS 3070 BK coal mill, Jaypee Cement Balaji, India MPS 180 GC vertical roller mill for the grinding, drying and calcining of gypsum, Knauf Knin, CroatiaCoal mill, gypsum mill, clay mill, etc Pfeiffer MPS mills2014年1月1日 Two mill systems are employed for most coal grinding applications in the cement industry These are, on the one hand, vertical roller mills (VRM) that have achieved a share of almost 90% and, on (PDF) MPS mills for coal grinding ResearchGate2022年7月26日 diagnosis of the major faults in the coal mill system [4] Fan et al, designed a knowledgebased finegrained coal mill operator support/control system for coal plants The system is composed of mathematical coal mill model and expert knowledge database and has the ability of parameter estimation, coal mill performance monitoring, fault diagnosisFault Diagnosis of Coal Mill Based on Kernel Extreme Learning
.jpg)
Pemanfaatan Gas Buang Rotary Kiln sebagai Gas Panas Coal Mill
The kiln can process 241 ton per hour of semidried lateritic ore with an average output of 3500 ton Energy recovery of 142 GJ/hour can be achieved and fuel cost saving for coal mill hot gas generation approximately USD 25 million annually with additional environmental benefit from 803% reduction of greenhouse gasses emission and 2024年5月1日 The coal mill operating status variables are measured by pressure sensors, RTD temperature sensors, and so on Then, the measurement data is transmitted to the DCS for storage Deflagration of coal mill mainly occurs in the Dual fault warning method for coal mill based on ScienceDirect2023年4月27日 At present, the economic benefits of double inlet and double outlet ball mills, which are commonly used in coalfired power plants, need to be improved Based on this, this paper explores the factors influencing the output of double inlet and double outlet ball mill by establishing the output system of double inlet and double outlet ball millSystem dynamics model of output of ball mill Sciendo2020年1月1日 The coal mill model was developed and the unknown model coefficients were The output variables of mill current and mill outlet temperature as obtained by GA were compared with onsite (PDF) Modelling and multiloop selective control of industrial coal
.jpg)
Modeling of Coal Mill System Used for Fault Simulation
2020年4月7日 is the total output energy of coal mill system (kJ), which mainl y includes the heat brought out by primary air, evaporated water, coal powder and heat loss, it can be expressed as: 22017年6月1日 The coal mill is assumed to be a lumped parameter object, and a calculation method based on the static heat balance of the coal mill calculates all heat input into or output from the coal mill quantitatively; however, a model of the coal mill has yet to be established on this basis (Feng et al, 1997, Ganapathy (2002), Magdalinović (1989))Optimization control of a pulverizing system on the basis of the 2019年11月7日 The speed of coal feeder is 320350 r/min, the output of coal mill is 5155 t/h, and the output of coal mill is increased by more than 30% on aver age 333Optimization and transformation of 300MV units steel ball coal mill 1927 First Loesche coal mill delivered for the Klingenberg power station in Berlin 1953 500th coal mill plant sold worldwide 1961 Introduction of hydraulic spring assembly system 1965 Construction of first pressure mill (LM 122 D) 1980 Delivery of first modular coal mill (LM 263 D) 1985 Delivery of first selfinerting coal grinding plant (LM 212 D) for the steel industry (PCI LOESCHEMILLS
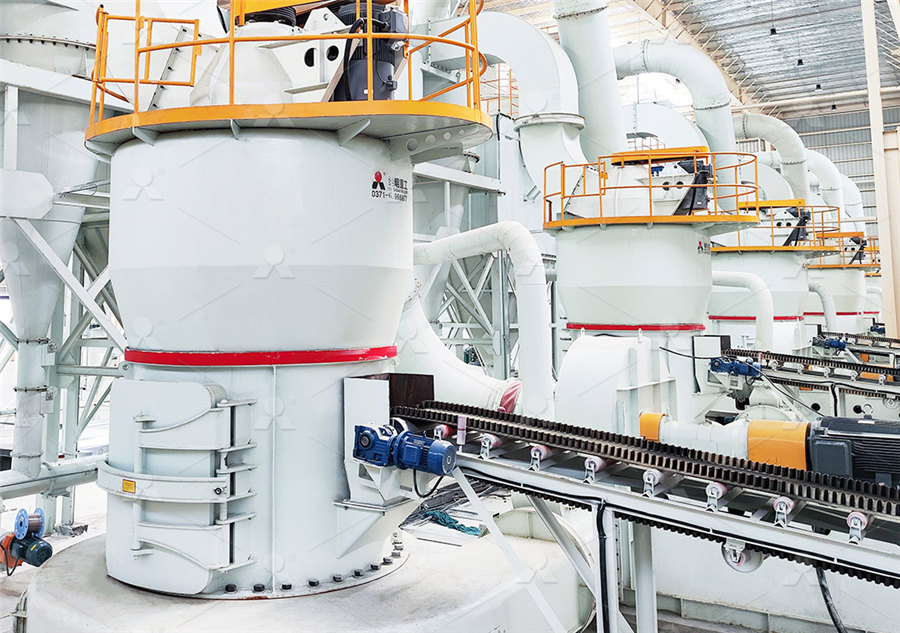
Double inlet outlet ball mill Geckointech
Coal mill could run a long time as long as boiler is not shut down Screw impeller and lining plate could be changed during boiler overhaul 2 Low air/coal ratio, stable output and particle size This coal mill structure results in a low air/coal 2022年5月31日 By reviewing the relevant literature, it is not difficult to find that the modeling approaches used to judge the current operating status of coal mills mainly contains mechanism modeling methods, signal analysis methods and artificial intelligence methods in past research [2]The purpose of mechanism modeling methods is to determine an accurate mathematical A brannew performance evaluation model of coal mill based on 2021年8月1日 Yukio et al [7] proposed a model consisting of blending, grinding and classifying processes for pulverizer control Agarawal et al [8] differentiated coal powder into ten size groups, divided the bowl mill into four zones, and developed a unified model Palizban et al [9] derived nonlinear differential mass equations of raw coal, recirculation coal and suspension coal in Coal mill model considering heat transfer effect on mass 2009年9月20日 A control oriented model was then developed by Fan (1994) and Fan and Rees (1994) In 2009, coal flow and outlet temperature of mill were modelled using mass and heat balance equations for startup Modeling and Parameter Identification of Coal Mill
.jpg)
Effect of Coal Quality and Performance of Coal pulverisers / Mills
2021年3月31日 3 COAL QUALITY –IMPACT COMPLEX • Pulverizer capacity, fineness wear • Slagging fouling in boiler • Corrosion erosion in boiler • Ash characteristics affect efficient collection in ESP • Affects furnace convective pass heat absorption boiler availability • Quantification of impact is complex 31Mar2021 total output power solutions 31997年8月1日 A series of similar tests were carried out on both C and D mill so that their dynamic performance can be compared The mill tests were carried out by regulating mill coal feeder speed and primary air flow The temperature of the mill input primary air flow varies with raw coal moisture and the mill output temperatureAnalysis of coal Mill Dynamic Characteristics Under Normal and 2020年4月7日 Monitoring and diagnosis of coal mill systems are critical to the security operation of power plants The traditional datadriven fault diagnosis methods often result in low fault recognition rate or even misjudgment due to the imbalance between fault data samples and normal data samples In order to obtain massive fault sample data effectively, based on the Modeling of Coal Mill System Used for Fault Simulation MDPIis assumed to have a constant value, while this parameter might vary in actual coal mill operations In the model, the effect of coal moisture on the energy balance of the coal mill is considered to increase the model's accuracy All heat input into or output from the coal mill is calculated quantitatively to reduce the number of unknownDecision Support System for Coal Mill Fault Diagnosis in Coal
.jpg)
Optimization control of a pulverizing system on the basis of the
2017年6月30日 Then, an estimated signal of the outlet coal powder flow of the coal mill was constructed as a new output control target of the pulverizing system Finally, Test results of coal feeder output Coal mill current (A) 365 43 494 576 712 835 905 ICAMMT 2019 IOP Conf Series: Materials Science and Engineering 631 (2019) Optimization and transformation of 300MV units steel ball coal mill Comparison of response of pulverized coal flow for a setpoint of 1 kg/sec in the presence of PID and MPC 40 C 100 C ACKNOWLEDGEMENT Output Outlet temperature We would like to thank the Control and Instrumentation department members of the North Chennai Thermal Power Plant for providing us the raw plant data which helped in modeling and (PDF) Modeling and Control of Coal Mill Academia2021年2月15日 of double inlet and double outlet ball mill output system is established, and SPSS is used to fit the The coal mill model was developed and the unknown model coefficients were obtained System dynamics model of output of ball mill
.jpg)
Derivation and validation of a coal mill model for control
2012年5月1日 Sensors for coal flow measurement from the mill to the furnace have become available on the market (Blankinship, 2004, Department of Trade and Industry, 2001, Laux et al, 1999)Unfortunately the equipment tends to be expensive and requires frequent calibration; thus it cannot be used directly for control purposes at this time of writingNote: 1 The basic output in the table refers to the grinding capacity of the coal mill under the working conditions of high volatile bituminous coal 8% and low volatile bituminous coal 12%, with the GHI of coal power of 55, coal fineness of 785% passing the 0075mm sieveHP Bowl type millspower plant equipment2015年11月1日 As presented by Andersen et al (2009) and Odgaard, Stoustrup, and Mataji (2007), coal moisture imposes limit on the maximum load at which a coal mill can be operated and the load gradient (how fast the mill may change its operating point), if it is desired that the pulverized coal entering the furnace has moisture content less than or equal to a certain value A unified thermomechanical model for coal mill operationBall mill coal pulverizing system is a multipleinput multipleoutput (MIMO) process characterized with strong couplings and nonlinearities Conventional control methods maybe work well initially, but will deviate from optimal work point for a period of time and even cease to be functionally effective A multilayer structure with direct control and optimization is presented for the control Coal Mill Control and Optimization Using a Multilayer Structure
.jpg)
Coal Mills for Cement Plants Loesche
Coal grinding mills LOESCHE coal grinding mills are distinguished by characteristics that improve efficiency, safety and environmental protection, from the standard version to topoftherange installations Special versions are available with characteristics that meet special safety regulation or output control requirementsIn this way a calibration curve is constructed which can eventually be used to forecast mill output with a new coal, from a measurement of the Index However, there are several defects of the test, two of which may be noted here as examples: Example 1 Batch versus continuous milling:COAL PREPARATION AND FIRING INFINITY FOR CEMENT EQUIPMENT25TPH LM1700 Coal Grinding Mill Capacity: 2025T/H Output size: 200 mesh Calcium carbonate ultrafine vertical mill Capacity: 8T/H Output size: 3253000 mesh Get prices and discounts * * * * * * * * * Order Now 40 Yrs Historyvertical roller mill, vertical coal mill, vertical slag mill, superfine Grinding of coal, petcoke, clay, limestone, quicklime, gypsum, MPS 200 BK coal mill, Krimzement Bakhchisarayski, Ukraine MPS 3070 BK coal mill, Jaypee Cement Balaji, India MPS 180 GC vertical roller mill for the grinding, drying and calcining of gypsum, Knauf Knin, CroatiaCoal mill, gypsum mill, clay mill, etc Pfeiffer MPS mills