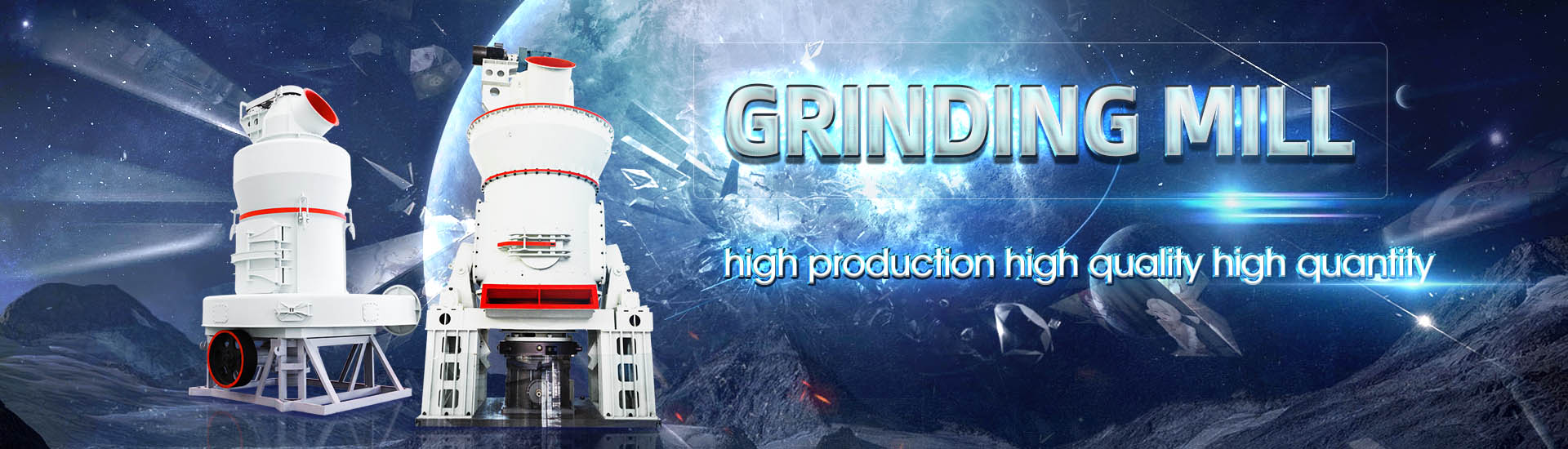
What is the role of cement grinding cooler
)D`ERF`389RMI4.jpg)
Clinkerization Cement Plant Optimization
Clinker cooler serves two main objective of cooling clinker from temperature of about 1350 0C to the temperature (65150 0C) where it can be handled by 2015年11月16日 The cooler is essential for recuperating heat from the clinker and cooling it sufficiently for the cement milling operation However, the primary objective of the cooler is to transport hot clinker from the kilnThe modern cooler International Cement ReviewAs the supporting equipment of a cement rotary kiln, a clinker cooler (also called cement cooler) is a kind of heat exchange device that transfers heat from hightemperature clinker to lowtemperature gas It plays an important role in the Clinker Cooler Cement Cooler AGICO Cooler In 2021年3月24日 Cement manufacturing requires cooling down of hot clinker at temperature of about 1350o C to temperature lower than 100 o C in a cooling system known as clinker cooler Many plants are unableModelling of clinker cooler and evaluation of its
.jpg)
Cement Cooler Clinker Cooler Types Of Clinker
Cement cooler is the important cement equipment in the cement production process Rotary cooler and grate cooler are two types of hotsale clinker coolers on the market AGICO offers highquality clinker coolers2023年3月3日 The cement industry includes energyintensive processes, eg, clinker rotary kilns and clinker grate coolers Clinker is obtained through chemical and physical reactions in a rotary kiln from raw meal; these reactions also Advanced Process Control for Clinker Rotary Kiln and 2018年7月31日 In cement plants clinker outlet temperature is directly evaluated by clinker cooler process efficiency Cooling processes may be evaluated as one of the energy input Development of Cooling Performance of Clinker Cooler Process 2023年10月19日 Explore the significance of clinker grinding in cement manufacturing, from particle size reduction to improved reactivity and quality control Learn how this integral process transforms clinker into the final Understanding the Role of Clinker Grinding in Cement
.jpg)
What is Cement Clinker? Composition, Types Uses
Clinker is a nodular material produced in the kilning stage during the production of cement and is used as the binder in many cement products The lumps or nodules of clinker are usually of diameter 325 mm and dark grey in color It is produced by heating limestone and clay to the point of liquefaction at about 1400°C1500°C in the rotary kiln The final manufacturing stage at a cement plant is the grinding of cement clinker from the kiln, mixed with 45% gypsum and possible additives, into the final product, cement In a modern cement plant the total consumption of electrical energy is about 100 kWh/t The cement grinding process accounts for approx 40% if this energy consumptionCEMENT GRINDING SYSTEMS INFINITY FOR CEMENT EQUIPMENTEverything you need to know about clinker/cement Grinding if You read and understand this article , you will be ready to be a cement grinding area manager FEED AND FEED SYSTEM Feed Temperature Plants with satellite coolers Everything you need to know about clinker/cement 2019年10月11日 AGICO Cement is a cement grinding plant manufacturer, we'd like to helps you learn more about cement grinding plant and cement grinding machines Skip to content +86 s about blog cement ball mill, cement vertical mill, cement roller press, cement kiln, dryer, clinker cooler, and related cement Cement Grinding Plant Overview Cement Grinding Unit AGICO Cement

Cement Cooler Clinker Cooler Types Of Clinker Cooler AGICO
Thermal Efficiency Formulas Q RI: The total heat recovered from the hightemperature clinker and then be transferred to the cement clinker calcination system Q o: Physical heat of hightemperature clinker (kJ/kg) Q loss s: Total heat loss of a cooler (kJ/kg) Q air: Heat is taken away by exhaust gas (kJ/kg) Q m: Heat is taken away by discharged clinker (kJ/kg)2015年11月16日 The clinker cooler is an essential element in the production of cement The cooler, as the name implies, cools the clinker to manageable levels while transporting it away from the kiln It also recovers heat from the clinker for use in the kiln, precalciner and other areas In addition, the cooler sizes the clinker, breaking up large piecesThe modern cooler International Cement Review2023年1月16日 Dr SB Hegde, Professor, Jain University, Bangalore, talks about pyroprocessing and the role of preheater, rotary kiln and clinker cooler in the cement manufacturing process In the concluding part of the twopart series, we will learn more about the various factors aiding pyroprocessing False Air in Pyro ProcessingIndia is the second largest cement producer in []Pyroprocessing and Kiln Operation Indian Cement ReviewWhether it is construction of homes, offices, bridges or pavements, cement plays a key role While cement can be any binding substance that hardens when it’s set, the term is mostly synonymous with construction of buildings In this article, we learn about what cement is, how it’s made, its types, benefits and more Cement – DefinitionCement: What is cement, Types Properties of Cement JK Cement
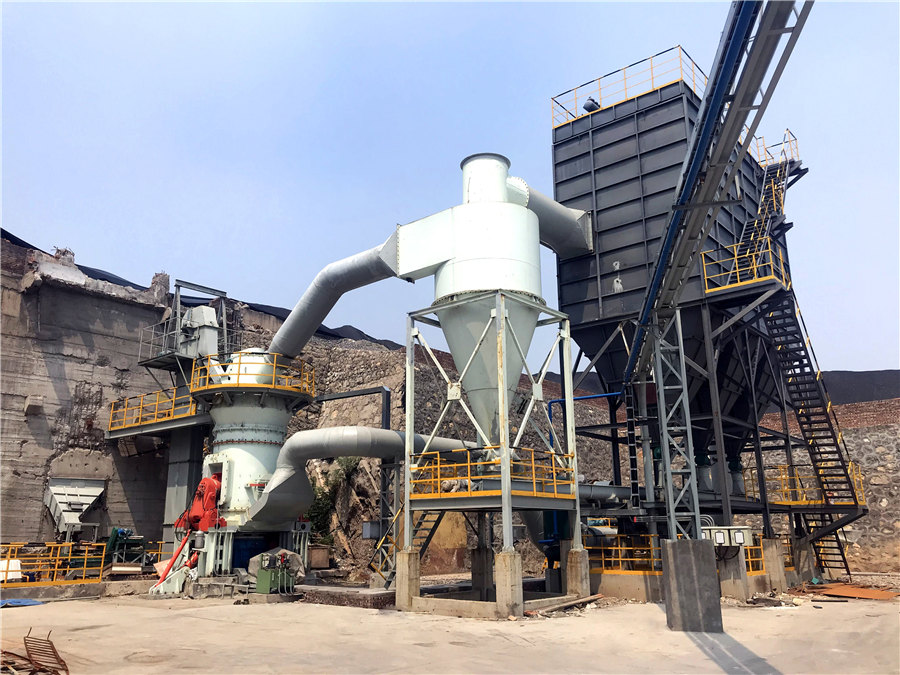
The Role of Cement in Modern Construction
In conclusion, cement’s role in modern construction is irreplaceable From its ancient origins to its evolution into a sustainable building material, cement has stood the test of time Its structural integrity, versatility, costeffectiveness, and commitment to sustainability make it an essential component of the construction industrySince the sample is usually taken from the outlet of the cooler, the results tell what was done 152 h before which, To control setting time, gypsum has to be added to the clinker during the finishgrinding process Typical portland cement contains approximately 5% of gypsum At this stage, the production of cement, EVERYTHING YOU NEED TO KNOW ABOUT THE CHEMISTRY OF Role in cement production Efficiency benefits Word count: 1000; Cooler Types (grate cooler, planetary cooler, etc) Impact on clinker quality and energy efficiency Word count: 1000; Section 4: Kiln Operation and Optimization Kiln Comprehensive Guide to Cement Kilns: Processes, 2022年12月23日 The physical/structural role of water in influencing the porosities in cements has been analyzed, raw material preparation and ca 40% for the grinding step The resulting cement is pneu(PDF) An Insight into the Chemistry of Cement—A

Development of Cooling Performance of Clinker Cooler Process
2018年7月31日 Cement manufacturing process comprises the main stages as mining and quarrying of raw materials, preparation of raw materials which includes raw material homogenizing and grinding, clinkering or burning of raw material to form clinker, and finally grinding of clinker and mixing with additives • Proportioning the clinker with gypsum and grinding it to the desired fineness in the finish mill systems to produce a high quality, uniform cement A cement plant will continue to operate successfully only if it can produce quality product with economic and material efficiency, and meet or exceed the required product performanceEverything you need to know about Kiln System Operations in Cement 2013年1月1日 This study assesses the use of hightemperature Xray diffraction (HTXRD) to study the mass transfer of raw meal constituents towards forming clinker phases and the occurrence of free CaO, also Modelling the cement process and cement clinker quality1 The basics of cement manufacture – 2 History of cement manufacture – 3 Portland cement in today’s world 2 Raw materials management system – 22 Concrete problems 16 1 Raw materials – 2 Raw mix – 3 Reserves – 4 Crushing – 5 Drying – 6 Preblending – 7 Storage and handling 3 Raw milling and blending 3The Cement Plant Operations Handbook International Cement
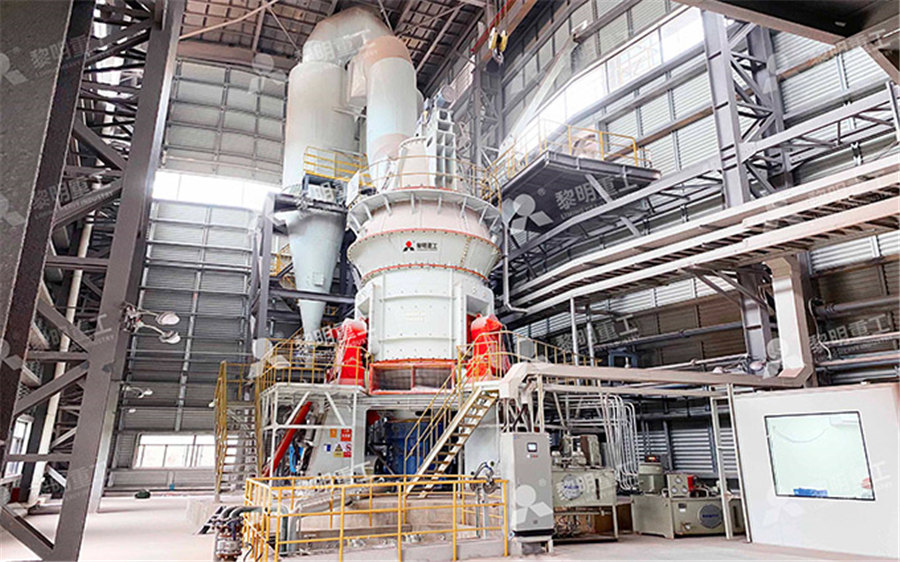
Cement SpringerLink
2021年3月3日 Cement is produced by a hightemperature (about 1500 °C) reaction in a rotary kiln of carefully proportioned and blended ratios of lime (CaO), silica (SiO 2), alumina (Al 2 O 3), and iron oxide (Fe 2 O 3)The production of cement is a chemical process requiring an accurate blend of the previously cited four key organic oxides and the limitation of several undesirable 2018年12月31日 Energy recovery and exergy recovery in a clinker cooler was a major factor in optimizing clinker production and cement grinding process, the running clinker cooler has an energy recovery was 4831 Energy and Exergy Analysis of Clinker Cooler in the Cement 2023年12月23日 Cooler Exhaust Fan: Cooling fans and clinker cooler exhaust fans are used to circulate fresh air to the clinker to cool down the material The cooler exhaust fans move 18 tons of exhaust air per 1 ton of clinker production This process is a part of the air blown into the cooler by cooling fans that is not useful for fuel combustionCentrifugal Fans in Cement Industry: Crucial Roles TechflowA review of the effectiveness of Life Cycle Assessment for gauging environmental impacts from cement production Oluwafemi E Ige, Collins Obiora, in Journal of Cleaner Production, 2021 223 Production of clinker The clinker production stage is where the raw material (the raw meal) converts into clinker The raw meal is fed into a rotary kiln through a preheater at about 1450 Clinker Production an overview ScienceDirect Topics
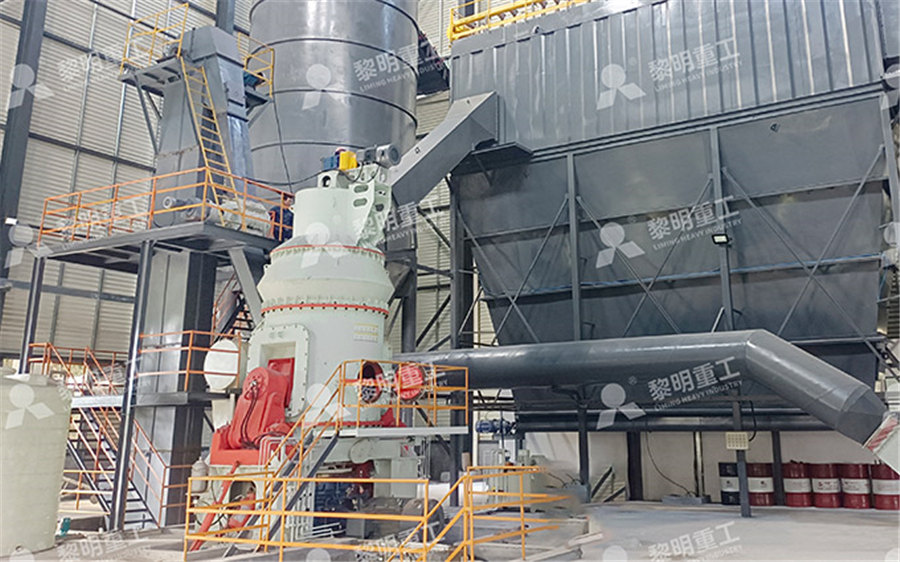
The Role of Dust Collectors in Cement Production SLY, LLC
2016年7月20日 The production of Portland cement makes up approximately 90% of the total cement produced in the US The main raw materials categories used to make Portland cement are lime, silica, alumina, and iron, but the process also consists of byproducts from other industries such as power plant fly ash, steel mill scale, and metal smelting slagAGICO Grate Clinker Cooler The grate cooler is a type of clinker cooler, it plays an important role in the clinker manufacturing process The grate cooler in a cement plant cools and transports the cement clinker from the rotary kiln, and Grate Cooler in Cement Plant Cement Clinker 2024年9月5日 Tricalcium silicate (C₃S): this compound gives strength to the cement and hardening properties Dicalcium silicate (C₂S): Strengthens cement hardening over time (C₃A) Tricalcium aluminate: regulates cement setting A Comprehensive Guide to the Cement Manufacturing The clinker cooler, also known as grate cooler or cement cooler, it is a necessary equipment of cement clinker productionThe clinker cooler is mainly used to cool and transport the cement clinker At the same time, cement cooler also provide hotair for rotary kiln and calciner, it is the main equipment of heat recovery for burning system The cooler will make a sufficient heat Clinker Cooler Cement Plant
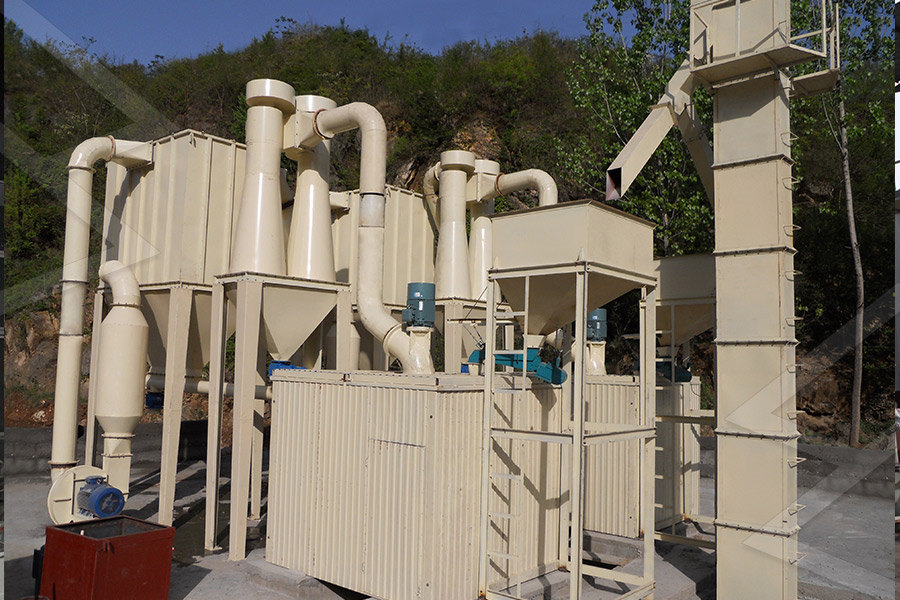
Solex Cement production and cooling
2023年3月22日 During the cement production process, these minerals are fused together by heating them to just under their melting point, forming a cement clinker between 3 to 20 mm in diameter Pure cement is formed when the cement clinker is ground into a fine powder To regulate how cement mortar or concrete will set, gypsum is added to this powderGrinding aids also serve to reduce coating problems in cement storage and enhances cement strengths GRINDING MILLS Mills will be selected according to type most suitable for required capacity and duty and for overall power consumption Cement grinding operation may be performed in one of the following mill setups Ball and tube millsCement Grinding Cement Plant Optimization2023年11月6日 Grinding aids (GAs) are polar chemicals introduced in cement mills in either liquid or powder form to improve on mill grindability efficiency(PDF) Review of the Effect of Grinding Aids and Admixtures on the Cement milling plays a crucial role in enhancing the quality of cement production By reducing the particle size of the clinker, cement manufacturers can produce a consistent quality product that offers better performance, energy efficiency, and cost savingsWhat is the Importance of Cement Milling ball mills supplier
.jpg)
Cement Extraction, Processing, Manufacturing Britannica
2024年11月23日 Cement Extraction, Processing, Manufacturing: Raw materials employed in the manufacture of cement are extracted by quarrying in the case of hard rocks such as limestones, slates, and some shales, with the aid of blasting when necessary Some deposits are mined by underground methods Softer rocks such as chalk and clay can be dug directly by Use white cement in projects that demand lighter shades of concrete Portlandlimestone cement tends to be slightly lightercolored than portland cement made from the same clinker, but factors other than the shade of cement also play a role in the color of concrete, including aggregate color and water contentApplications of Cement Portland Cement AssociationClinker is a nodular material produced in the kilning stage during the production of cement and is used as the binder in many cement products The lumps or nodules of clinker are usually of diameter 325 mm and dark grey in color It is produced by heating limestone and clay to the point of liquefaction at about 1400°C1500°C in the rotary kiln What is Cement Clinker? Composition, Types UsesThe final manufacturing stage at a cement plant is the grinding of cement clinker from the kiln, mixed with 45% gypsum and possible additives, into the final product, cement In a modern cement plant the total consumption of electrical energy is about 100 kWh/t The cement grinding process accounts for approx 40% if this energy consumptionCEMENT GRINDING SYSTEMS INFINITY FOR CEMENT EQUIPMENT
.jpg)
Everything you need to know about clinker/cement
Everything you need to know about clinker/cement Grinding if You read and understand this article , you will be ready to be a cement grinding area manager FEED AND FEED SYSTEM Feed Temperature Plants with satellite coolers 2019年10月11日 AGICO Cement is a cement grinding plant manufacturer, we'd like to helps you learn more about cement grinding plant and cement grinding machines Skip to content +86 s about blog cement ball mill, cement vertical mill, cement roller press, cement kiln, dryer, clinker cooler, and related cement Cement Grinding Plant Overview Cement Grinding Unit AGICO CementThermal Efficiency Formulas Q RI: The total heat recovered from the hightemperature clinker and then be transferred to the cement clinker calcination system Q o: Physical heat of hightemperature clinker (kJ/kg) Q loss s: Total heat loss of a cooler (kJ/kg) Q air: Heat is taken away by exhaust gas (kJ/kg) Q m: Heat is taken away by discharged clinker (kJ/kg)Cement Cooler Clinker Cooler Types Of Clinker Cooler AGICO2015年11月16日 The clinker cooler is an essential element in the production of cement The cooler, as the name implies, cools the clinker to manageable levels while transporting it away from the kiln It also recovers heat from the clinker for use in the kiln, precalciner and other areas In addition, the cooler sizes the clinker, breaking up large piecesThe modern cooler International Cement Review
.jpg)
Pyroprocessing and Kiln Operation Indian Cement Review
2023年1月16日 Dr SB Hegde, Professor, Jain University, Bangalore, talks about pyroprocessing and the role of preheater, rotary kiln and clinker cooler in the cement manufacturing process In the concluding part of the twopart series, we will learn more about the various factors aiding pyroprocessing False Air in Pyro ProcessingIndia is the second largest cement producer in []Whether it is construction of homes, offices, bridges or pavements, cement plays a key role While cement can be any binding substance that hardens when it’s set, the term is mostly synonymous with construction of buildings In this article, we learn about what cement is, how it’s made, its types, benefits and more Cement – DefinitionCement: What is cement, Types Properties of Cement JK CementIn conclusion, cement’s role in modern construction is irreplaceable From its ancient origins to its evolution into a sustainable building material, cement has stood the test of time Its structural integrity, versatility, costeffectiveness, and commitment to sustainability make it an essential component of the construction industryThe Role of Cement in Modern ConstructionSince the sample is usually taken from the outlet of the cooler, the results tell what was done 152 h before which, To control setting time, gypsum has to be added to the clinker during the finishgrinding process Typical portland cement contains approximately 5% of gypsum At this stage, the production of cement, EVERYTHING YOU NEED TO KNOW ABOUT THE CHEMISTRY OF