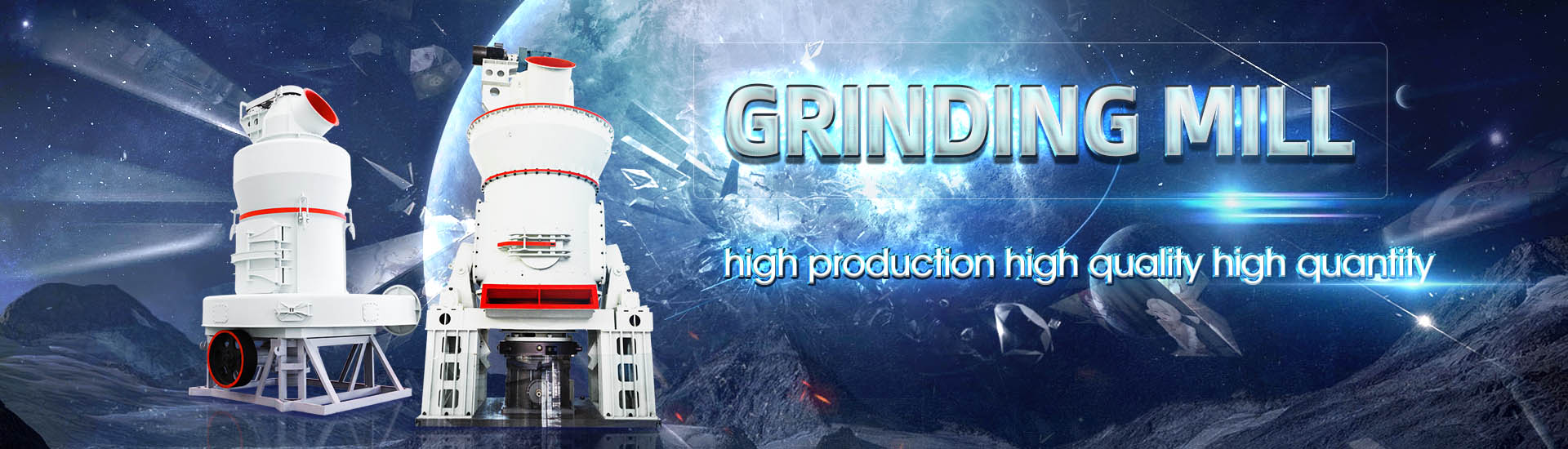
Parameters of talc 4roller anthracite lignite mill
.jpg)
Impact of Operating Parameters on the Breakage Process of Talc
The grinding capacity of mills was determined based on operational conditions and the grinding mechanism One of the most important operating parameters is the 展开2023年9月9日 Within the scope of this study, the changes in the “U” parameter (the ratio of the amount of ground material to the grinding media) in the grinding experiments performed with a laboratoryscale ball mill were investigated for The Effects of BallMill Grinding Parameters on Lignite 2013年1月1日 Following technological parameters of the mechanical activation were monitored: time of mechanical activation, circumferential rotor speed, capacity of ultracentrifugal mill, and specificComparative Analysis of Process Parameters of Talc 2014年1月6日 Ultra fine grinding of talc in attrition mill (attritor) was carried out in various time intervals from 5 to 15 min The following technological parameters of the mechanical COMPARATIVE ANALYSIS OF PROCESS PARAMETERS OF TALC
FYEFEPS2HDZ49G5Z0[B.jpg)
Comparative Analysis of Process Parameters of Talc Mechanical
Ultra fine grinding of talc in attrition mill (attritor) was carried out in various time intervals from 5 to 15 min The following technological parameters of the mechanical activation were 2023年10月18日 Firstly, the conventional ball mill parameters such as mill speed (% of critical speed), material filling ratio (Jb), ball filling ratio (fc), ball size distribution (10203040 mm, Combination of Conventional Ball Mill and Stirred Mill to Obtain Within the scope of the research, the effects of operating parameters including media filling ratio, solid mass fraction, grinding media size, and grinding time were studied The findings were Impact of Operating Parameters on the Breakage Process of Talc2019年10月31日 In this study, we investigate the effect of the ball size in a highenergy ball mill on the comminution rate and particle size reduction Highenergy ball milling at 2000 rpm produces ultrafine talc particles with a surface area of Effects of Ball Size on the Grinding Behavior of Talc
.jpg)
Effect of Hydrophobicity on Talc Grinding in Attritor Mill
2024年3月10日 In this paper, the effect of talc hydrophobicity and grinding conditions in terms of grinding balls size, mill filling, grinding time, stirrer speed, and solids% on producing –45 2009年7月1日 Talc exhibited degree of crystallinity from 276% to 853% even at a high feed rate level due to its softness and selective plane rupture preferential Talc ground at 4 kg/h, Mechanochemical effects on talc during fine grinding process in a 2022年1月23日 This work concentrates on the energy consumption and grinding energy efficiency of a laboratory vertical roller mill (VRM) under various operating parametersAnalysis and Optimization of Grinding Performance of 2012年12月31日 This phenomenon reveals that during combustion the emission of fine PM, especially the PM 25 , is greatly affected by coal fineness, which is consistent with the work by Ninomiya et al (2004)The Research on Design Parameters of Fan Mill Direct Pulverizing
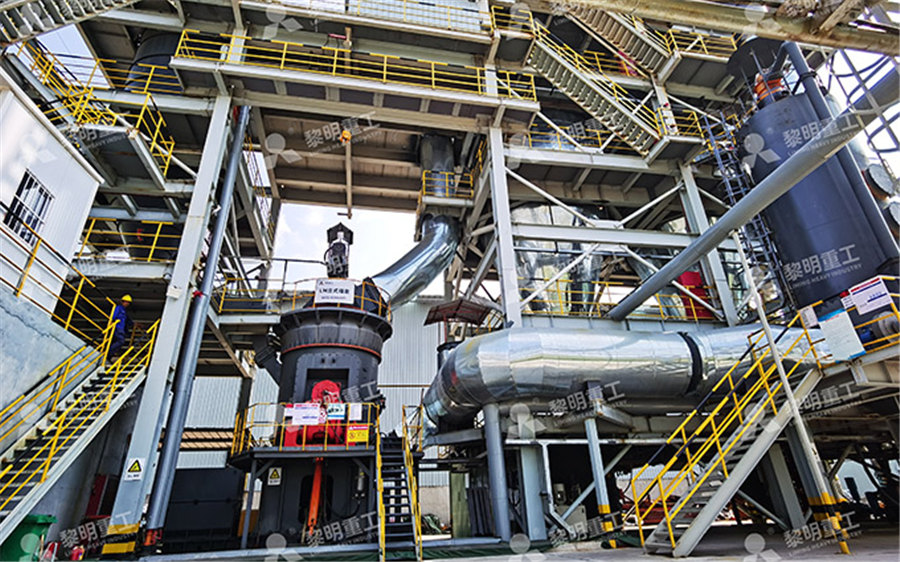
RAYMOND® ROLLER MILLS Thomasnet
Major factors affecting the capacity of a roller mill include desired fineness, grindability and initial moisture Talc 80 325 17 60 75 10 16 25 38 87 Mill Size Nominal Airflow Fan Power Mill Powermax Turbine Power Water Evaporation in mm acfm m3/hr hp kW hp kW hp kW 1000 lb/hr2021年1月1日 Grinding Mill Vertical Roller Mill or Ball Mill: The reclaimed raw mix fed to Raw Mills, for drying and fine grinding of Raw meal for kiln feed: 4: Coal Grinding: Grinding Mill Vertical Roller Mill or Ball Mill: Coal is ground in Coal mill, which is a fuel for use in Kiln firing: 5: Pyro Section, Clikerization: In line calciner six stage Review on vertical roller mill in cement industry its 2023年12月4日 A vertical roller mill (VRM) is a grinding equipment used for the size reduction of minerals, The roller and the table gap does not affect the speed of the roller when other parameters are kept constant Fig 7 Effect of the gap between the roller and table on (a) Vertical force; (b) Roller speedNumerical Investigation of Vertical Roller Mill Operation Using The limestone powder ultrafine vertical roller mill is mainly used in the production of 3 Product parameter of limestone powder grinding mill; 4 Advantages and disadvantages of limestone powder ultrafine 45t/h Max Feeding Size: 10 mm M 1 Set Price: $ Range Of Application: Limestone, Calcium Carbonate, Talc Limestone Powder Ultrafine Vertical Roller Mill

The Effects of BallMill Grinding Parameters on Lignite Morphology
2023年9月9日 In recent years, because of the decreasing liberation sizes of the minerals, processes such as grinding need to be evaluated in more detail As is well known, size reduction processes are very important both in mineral processing and in many industrial applications However, to increase the efficiency of the processes after size reduction, variations in particle 2023年12月1日 The vibration of the rolling mill has been a persistent issue affecting its safe and stable operation To address the vibration problem in the F2 stand of a continuous rolling mill, this paper establishes a digital twin model of the rolling mill Based on the digital twin model, a rolling mill virtual commissioning framework has been proposed to enhance the accuracy of realtime Virtual commissioning and process parameter optimization of This document discusses beater wheel mills used in lignitefired boilers It includes: 1 An overview of beater wheel mills, including their components, typical sizes and capacities, and the comminution process within the mill 2 Diagrams of beater wheel mills with different configurations, such as with or without a separating classifier or with a precrusher 3 Photos of Beater Wheel Mill PDF Lignite Mill (Grinding)2020年3月1日 In this study, the influence of grinding parameters of talc sample in the conventional ball mill on waterbased paint properties was investigated, and the results obtained from the experiments The Influence of Grinding Parameters of Talc on WaterBased
.jpg)
PELLET MILLS
Roller speed m /s 05 to 08 Drive motor kW Drive motor kW/ min1 3 2100 860 1125 855 Type 25 – 500 Die diameter mm 500 Roller diameter / width mm 230 / up to 75 Number of rollers 4 Roller speed m / s 17 Drive motor kW / min1 36 / 1500 Type 33 – 390 Die diameter mm 390 Roller diameter / width mm 230 / up to 75 Number of rollers 2 Roller PDF On Jan 1, 2023, Mohsen Mhadhbi published Effect of Milling Parameters on DEM Modeling of a Planetary Ball Mill Find, read and cite all the research you need on ResearchGateEffect of Milling Parameters on DEM Modeling of a 2018年6月8日 Properties of coal surface and pore structure are important aspects to be investigated in coal preparation and utilization In order to investigate the limits of different probe methods, a Surface Properties and Pore Structure of Anthracite, 2024年11月15日 Figure 4 shows a schematic diagram of the force on the pressure rollers of a highpressure roller mill, The shaded area is the influence area of the working pressure, in the region of the pressure Optimization of working parameters of highpressure roller mill
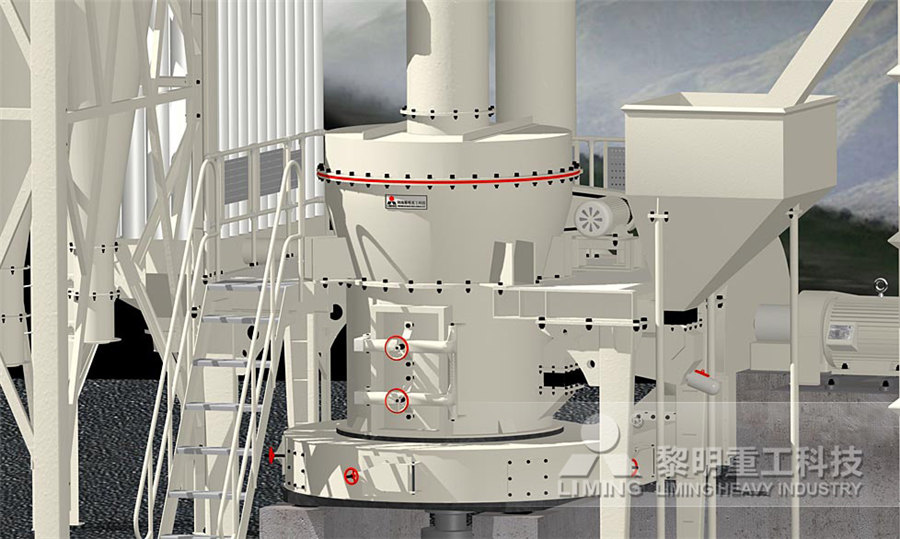
VRM In Cement Plant Maximize Energy Saving CNBMSINOMA
The 4roller mill can run with 2 rollers, and the operation rate is high Technical Parameter Type Dia of table (mm) Installation of power (KW) Capacity (t/h) Annual capacity; TRMS56: 5600: 5600: Wide range of applications, bituminous coal, anthracite, lignite, petroleum coke, and so on Free Inquiry Technical Parameter Type2014年1月1日 Two mill systems are employed for most coal grinding applications in the cement industry These are, on the one hand, vertical roller mills (VRM) that have achieved a share of almost 90% and, on (PDF) MPS mills for coal grinding ResearchGate2021年6月29日 This article deals with the preparation and laboratory milling of βdicalcium silicate Dicalcium silicate is the second most important calcium silicate of Portland clinker βC 2 S is usually Effects of Mill Speed and Air Classifier Speed on Performance of 2016年1月1日 The aim of this work was to investigate micro fine size dry grindability of talc in a stirred ball mill The effects of various parameters such as grinding time, stirrer speed, powder filling Dry grinding of talc in a stirred ball mill ResearchGate
.jpg)
Operational parameters affecting the vertical roller mill
Request PDF On Sep 1, 2016, Deniz Altun and others published Operational parameters affecting the vertical roller mill performance Find, read and cite all the research you need on ResearchGate2014年1月1日 The efficiency of talc mechanical activation by means of two different mechanoactivators centrifugal and attrition mill is investigated in this study and the comparative analysis of the Comparative analysis of process parameters of talc mechanical kaolin, talc, pozzolana and many more: Information on preparation of other materials References MPS 180 GC vertical roller mill for the grinding, drying and calcining of gypsum, Knauf Knin, Croatia MPS 100 GC vertical roller mill Coal mill, gypsum mill, clay mill, etc Pfeiffer MPS mills2009年9月20日 A control oriented model was then developed by Fan (1994) and Fan and Rees (1994) In 2009, coal flow and outlet temperature of mill were modelled using mass and heat balance equations for startup Modeling and Parameter Identification of Coal Mill
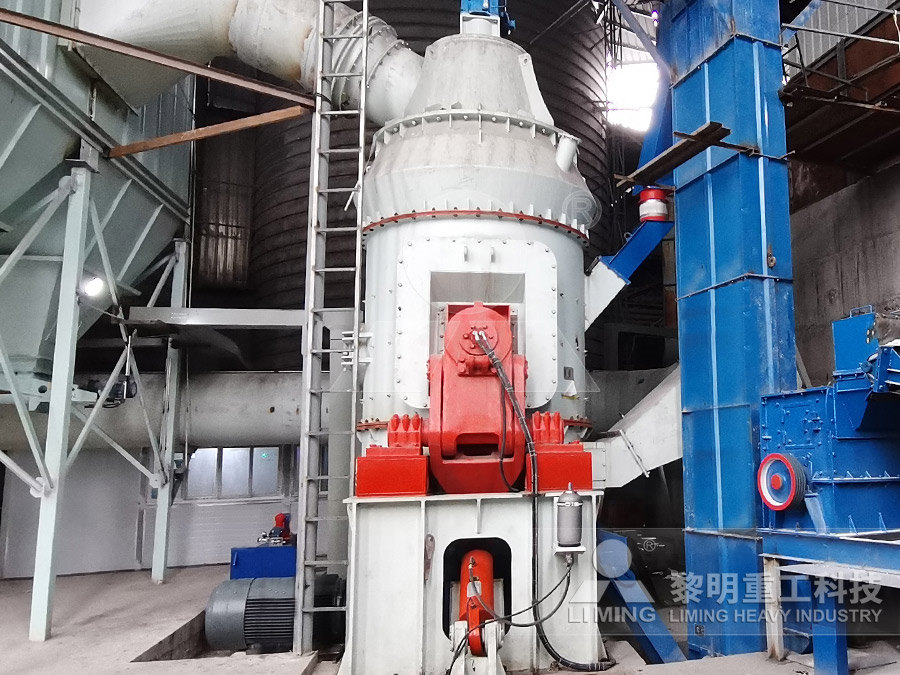
Optimizing Dry Ultrafine Grinding of Talc in Attritor Mill
Different mill fillings (25%, 30%, and 35% by volume) at 270 rpm, and ball sizes (70% of 10 mm balls with 30% of 4 mm balls) at 30 min grinding time were testedAverage grain size d' of mechanically activated talc vs circumferential rotor speed v of ultracentrifugal mill for sieve mesh size 500 m Achieved results of mechanical activation of talc by means of attrition mill Fine and ultra fine milling of talc in attrition mill (attritor) were carried out at various time periods from 5 to 15 parative Analysis of Process Parameters of Talc Mechanical 2015年2月20日 The principal types of coal, in order of metamorphic development, are lignite, subbituminous, bituminous, and anthracite While not generally considered a coal, peat is the first development stage in the “coalification” process, in which there is a gradual increase in the carbon content of the fossil organic material and concomitant reduction in oxygenCoals, Lignite, and Peat Keppeler Wiley Online LibraryRaymond Mill Working Principle In the Raymond mill, a Raymond mill spring with a pressure of 10001500 kg is fastened to the grinding roll hanger After starting work, the grinding roller rotates around the main shaft and rolls close to the grinding ring under the action of the Raymond mill spring and centrifugal forceRaymond Roller Grinding Mill
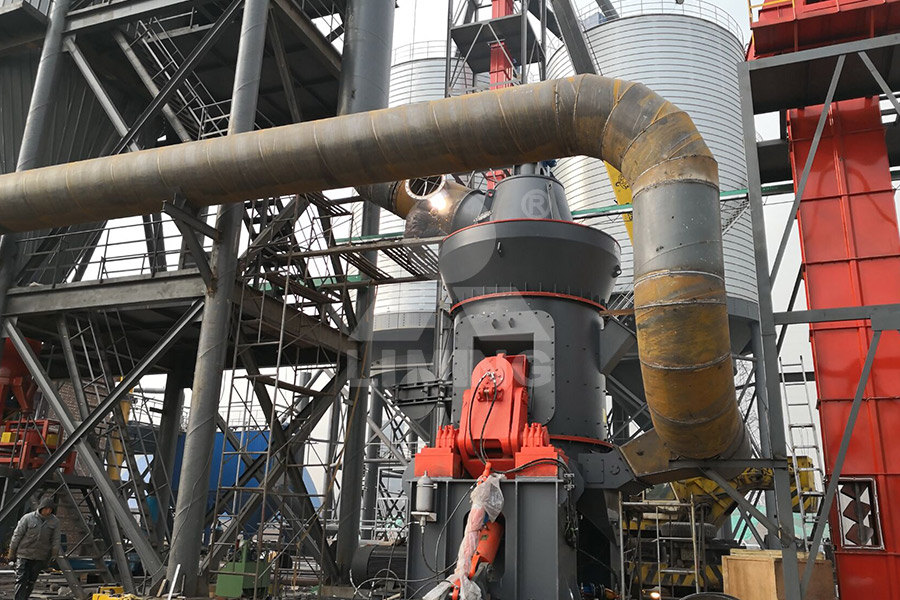
(PDF) Performance Evaluation of Vertical Roller Mill in
2017年9月11日 PDF In this study, an extensive sampling study was carried out at vertical roller mill of ESCH Cement Plant in Luxemburg Design parameters of vertical roller mill Table diameter (m) 46 2022年1月1日 Calcite, in other words, calcium carbonate (CaCO 3), is a glassy shimmer, transparent, easily breakable, large crystal marble mineralIts Mohs hardness is 3 and specific gravity is in the range of 26–28 It is micronized by grinding then classification processes are applied, and offered to the user as natural ground or ground and coated calcite according to The effects on the grinding parameters of chemical, Dry grinding of talc in a stirred ball mill Serkan Cayirli1,a 1Nigde University, Department of Mining Engineering, 51240 Central Campus, Turkey Abstract The aim of this work was to investigate micro fine size dry grindability of talc in a stirred ball mill The effects of various parameters such as grinding time, stirrer speed,Dry grinding of talc in a stirred ball mill e3sconferences2019年2月21日 The new design of roller mill assembly consists of two rotating rollers with outer rings, between which a grinding plate is fixed permanently and the rollers are connected to drive shafts The mill is equipped with a hopper and a grinding product basketA study of operating parameters of a roller mill with a new design
.jpg)
Analysis and Optimization of Grinding Performance of
2022年1月23日 This work concentrates on the energy consumption and grinding energy efficiency of a laboratory vertical roller mill (VRM) under various operating parameters2012年12月31日 This phenomenon reveals that during combustion the emission of fine PM, especially the PM 25 , is greatly affected by coal fineness, which is consistent with the work by Ninomiya et al (2004)The Research on Design Parameters of Fan Mill Direct Pulverizing Major factors affecting the capacity of a roller mill include desired fineness, grindability and initial moisture Talc 80 325 17 60 75 10 16 25 38 87 Mill Size Nominal Airflow Fan Power Mill Powermax Turbine Power Water Evaporation in mm acfm m3/hr hp kW hp kW hp kW 1000 lb/hrRAYMOND® ROLLER MILLS Thomasnet2021年1月1日 Grinding Mill Vertical Roller Mill or Ball Mill: The reclaimed raw mix fed to Raw Mills, for drying and fine grinding of Raw meal for kiln feed: 4: Coal Grinding: Grinding Mill Vertical Roller Mill or Ball Mill: Coal is ground in Coal mill, which is a fuel for use in Kiln firing: 5: Pyro Section, Clikerization: In line calciner six stage Review on vertical roller mill in cement industry its
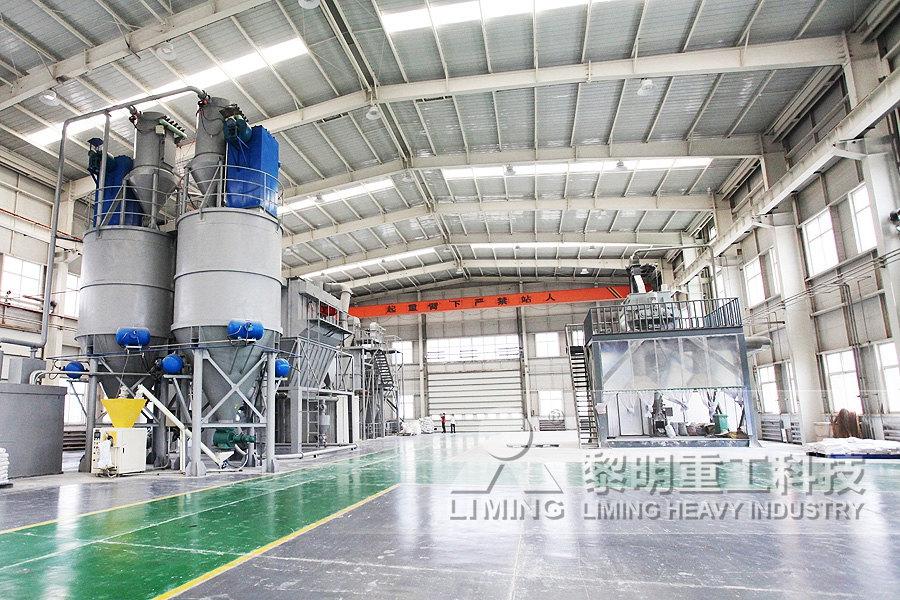
Numerical Investigation of Vertical Roller Mill Operation Using
2023年12月4日 A vertical roller mill (VRM) is a grinding equipment used for the size reduction of minerals, The roller and the table gap does not affect the speed of the roller when other parameters are kept constant Fig 7 Effect of the gap between the roller and table on (a) Vertical force; (b) Roller speedThe limestone powder ultrafine vertical roller mill is mainly used in the production of 3 Product parameter of limestone powder grinding mill; 4 Advantages and disadvantages of limestone powder ultrafine 45t/h Max Feeding Size: 10 mm M 1 Set Price: $ Range Of Application: Limestone, Calcium Carbonate, Talc Limestone Powder Ultrafine Vertical Roller Mill2023年9月9日 In recent years, because of the decreasing liberation sizes of the minerals, processes such as grinding need to be evaluated in more detail As is well known, size reduction processes are very important both in mineral processing and in many industrial applications However, to increase the efficiency of the processes after size reduction, variations in particle The Effects of BallMill Grinding Parameters on Lignite Morphology2023年12月1日 The vibration of the rolling mill has been a persistent issue affecting its safe and stable operation To address the vibration problem in the F2 stand of a continuous rolling mill, this paper establishes a digital twin model of the rolling mill Based on the digital twin model, a rolling mill virtual commissioning framework has been proposed to enhance the accuracy of realtime Virtual commissioning and process parameter optimization of
.jpg)
Beater Wheel Mill PDF Lignite Mill (Grinding)
This document discusses beater wheel mills used in lignitefired boilers It includes: 1 An overview of beater wheel mills, including their components, typical sizes and capacities, and the comminution process within the mill 2 Diagrams of beater wheel mills with different configurations, such as with or without a separating classifier or with a precrusher 3 Photos of 2020年3月1日 In this study, the influence of grinding parameters of talc sample in the conventional ball mill on waterbased paint properties was investigated, and the results obtained from the experiments The Influence of Grinding Parameters of Talc on WaterBased