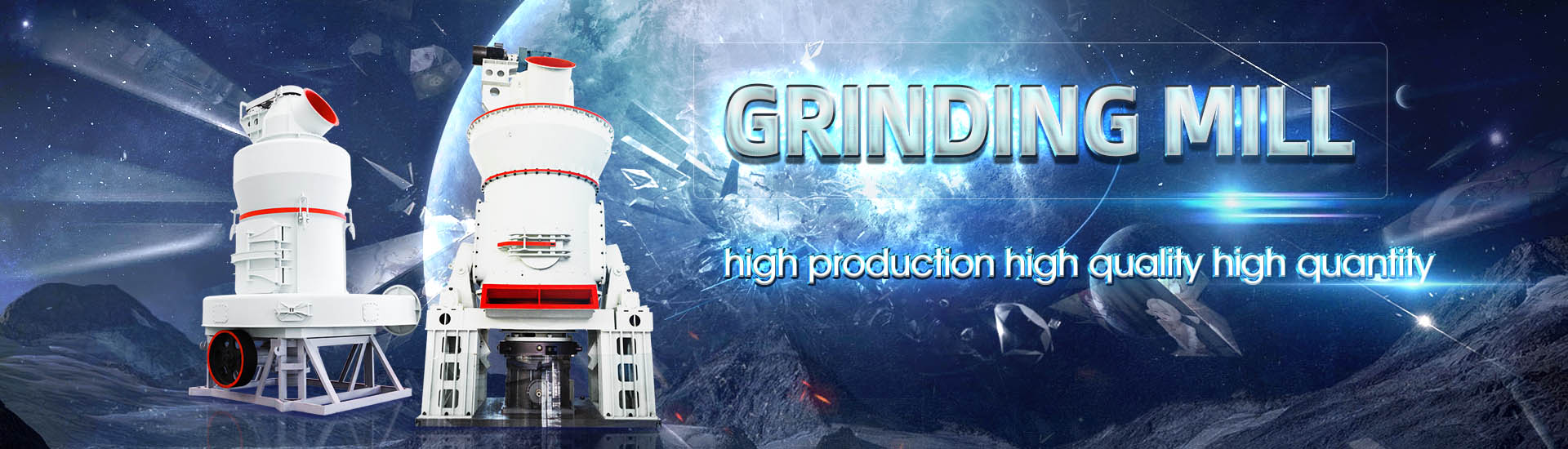
Cement pregrinding flow chart

Process flow diagram for the cement manufacturing
According to [39], Figure 4 provides a process flow diagram of the general cement production process and the associated inputs, during various steps of the production process consumption ofFig Flow chart of roller mill adopting the external circulating system It depends on scale of facilities For example, about 820,000 US$ per unit At the beginning stage when vertical roller Vertical roller mill for raw Application p rocess materialsThe flow diagram of a typical cement manufacturing process is shown in Fig 1 [3] Finally produced cement is transported in bags (packages) or as a bulk powder Cement manufacturing processTypical cement manufacturing process flow diagram This study provides an overview of the incumbent methodology for cement production as well as specific pathways towards decarbonization that are emerging for the cement industryStages in cement production flow chart [43] ResearchGate
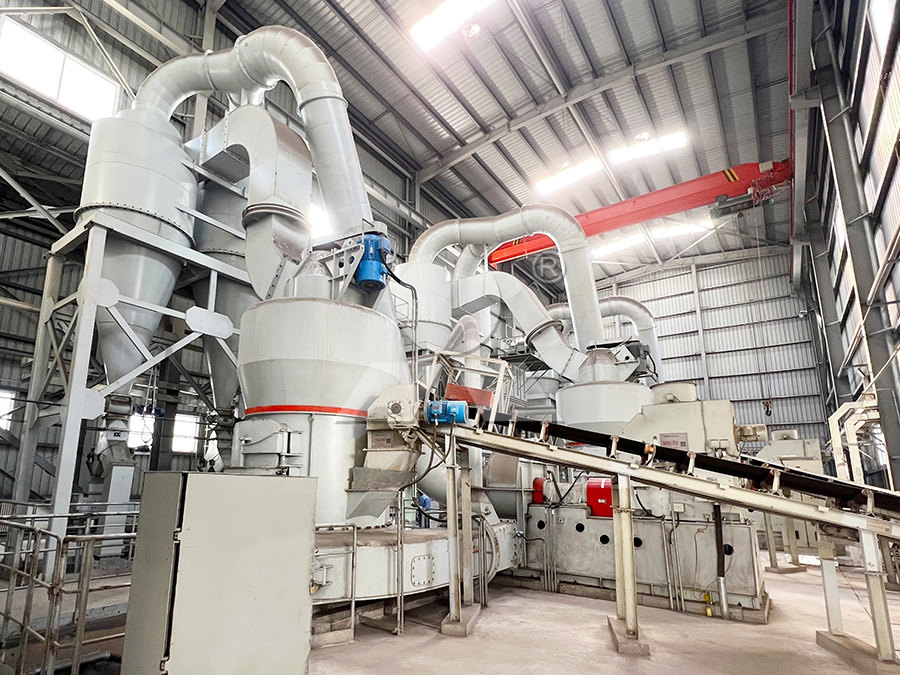
116 Portland Cement Manufacturing US Environmental
kiln feed preparation, pyroprocessing, and finished cement grinding Each of these process components is described briefly below The primary focus of this discussion is on In the cement plant, the preheater system functions as heat exchanger The hot gas generated in the kiln to burn the clinker leaves the kiln and moves up the preheater to heat up the raw meal Chapter 4 Cement Manufacturing and Process ControlThe Cement Plant Operations Handbook is a concise, practical guide to cement manufacturing and is the standard reference used by plant operations personnel worldwide Providing a The Cement Plant Operations Handbook International Cement Our ProTIR system will provide accurate temperature monitoring at the burning zone to driving off unwanted elements as gases and creating clinker of the required composition Continuous CEMENT MANUFACTURING PROCESS VisionTIR
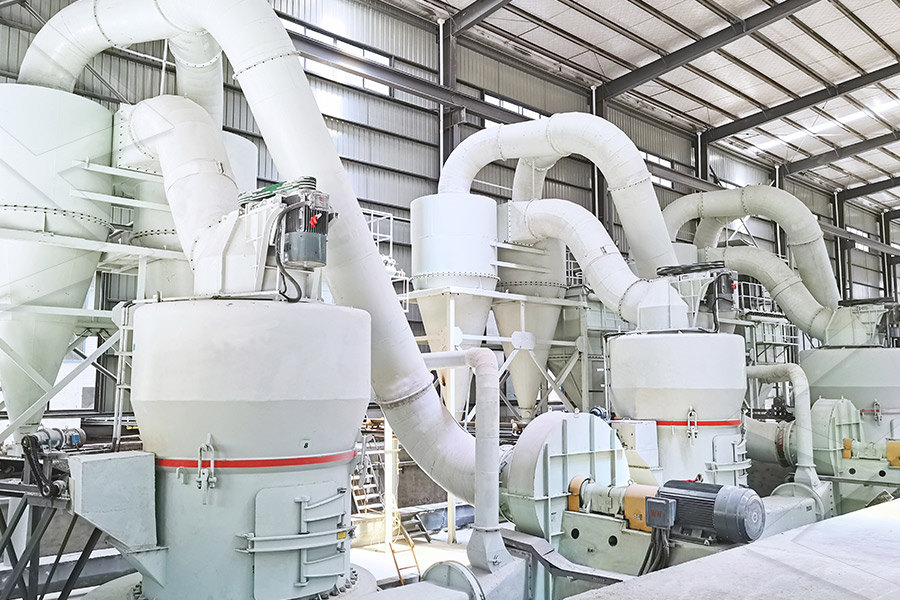
Wet Process Of Cement Manufacturing With Flow
Wet Process Of Cement Manufacturing With Flow Chart The raw materials are calcareous materials, like limestone or chalk, and argillaceous material such as shale or clay Skip to content Grinding of Raw Materials: The crushed Download scientific diagram Process flow diagram for the cement manufacturing process, showing electricity and heat consumption or inputs [39] from publication: Energy Savings Associated with Process flow diagram for the cement manufacturing 2014年6月10日 This document discusses Portland cement and the cement manufacturing process It begins with an overview of what cement is and how it is used to make concrete It then describes the industrial process for Cement manufacturing process PPT Free Download6 Cement Production Technology –Cement Grinding –Mechanical Design and Function of Separator Separators –General Classification of Separating Principles •according to flow direction relative to particle track •according to kind of separating field separation by gravitational force separation by centrifugal forceCement Grinding myPolysiusService
.jpg)
The flowchart of cement grinding, A, Bsampling points
Download scientific diagram The flowchart of cement grinding, A, Bsampling points (evacuation stacks) [37] from publication: Dust Emission Monitoring in Cement Plant Mills: A Case Study in 2016年10月5日 In this chapter an introduction of widely applied energyefficient grinding technologies in cement grinding and description of the operating principles of the related equipments and comparisons over each other in terms of grinding efficiency, specific energy consumption, production capacity and cement quality are given A case study performed on a EnergyEfficient Technologies in Cement Grinding IntechOpenIn the wet process, which involves grinding raw materials into a slurry and then feeding them into a rotary kiln for drying and calcination Total Time: 3 minutes Raw Material Preparation The raw materials such as limestone, clay, Flowchart of cement manufacturing Wet Process Source Building materials by SKDuggal Dry process Source 2 Types of Manufacturing of Cement Wet and Dry ProcessDownload scientific diagram Flow chart of the grinding and blending process from publication: Effective Optimization of the Control System for the Cement Raw Meal Mixing Process: I PID Tuning Flow chart of the grinding and blending process
.jpg)
The Cement Plant Operations Handbook International Cement
1 The basics of cement manufacture – 2 History of cement manufacture – 3 Portland cement in today’s world 2 Raw materials management system – 22 Concrete problems 16 1 Raw materials – 2 Raw mix – 3 Reserves – 4 Crushing – 5 Drying – 6 Preblending – 7 Storage and handling 3 Raw milling and blending 32020年10月5日 12 Working In case of continuously operated ball mill, the material to be ground is fed from the left through a 60° cone and the product is discharged through a 30° cone to the right As the shell rotates, the balls are lifted up on the rising side of the shell and then they cascade down (or drop down on to the feed), from near the top of the shellCement industry : grinding process of ball mill PPT SlideShare2021年3月9日 In this study the process flow diagram for the cement production was simulated using Aspen HYSYS 88 software to achieve high energy optimization and optimum cement flow rate by varying the flow rate of calcium Simulation and Optimization of an Integrated Process The cyclone preheating system Phase IV: Calcination The calcination is the core phase of the cement making dry process The calcination of the preheated raw meal takes place in the rotary kiln of the cement plant The rotary kiln is a How Is Cement Produced in Cement Plants Cement
.jpg)
Finish grinding INFINITY FOR CEMENT EQUIPMENT
Presumably this film tends to pre thermodynamic conditions and the amount of cooling air must be deter mined by a separate heat balance for each grinding mill Fig 1019 shows a flow chart of a The calculation illus trates the degree of Explore Amrit Cement's stateoftheart cement grinding unit Learn about our cement grinding process and plant stages for high quality cement Amrit Support About Amrit Support; Services; Activities; Corporate Annual Return FY 202021; FY 202122; FY 202223; Nomination and Remuneration Policy;Cement Grinding Unit Process High Quality Cement Grinding 1971年8月17日 116 Portland Cement Manufacturing 1161 Process Description17 Portland cement is a fine powder, gray or white in color, that consists of a mixture of hydraulic cement materials comprising primarily calcium silicates, aluminates and aluminoferrites More than 30 raw materials are known to be used in the manufacture of portland cement, and these116 Portland Cement Manufacturing US EPACEMENT GRINDING UNIT[CODE NO4173] Cement is a material that binds together solid bodies (aggregate) by hardening from a plastic state Many materials act as adhesives or cement according to this definition The cement referred to above, which is used for civil engineering and the constructionDetailed Project Report on cement grinding unit
.jpg)
How Cement is Made Cement Manufacturing Process
Stage 2: Grinding, Proportioning, and Blending The crushed raw ingredients are made ready for the cementmaking process in the kiln by combining them with additives and grinding them to ensure a fine homogenous mixture The composition of cement is proportioned here depending on the desired properties of the cement Generally, limestone is 80%, and the remaining 20% AGICO Cement is a cement equipment manufacturer supplies EPC projects for cement grinding station with a simple process, easy operation, low investment Get a FREE quote now! Skip to content +86 s about The newtype cement grinding units adopt pregrinding technologycement grinding Unit2021年3月9日 In this study the process flow diagram for the cement production was simulated using Aspen HYSYS 88 software to achieve high energy optimization and optimum cement flow rate by varying the flow Simulation and Optimization of an Integrated Process Flow Sheet Quality Control: Postgrinding, the cement undergoes screening to ensure it meets the specified quality standards Any cement that does not meet the specifications is sent back for further processing Storage Preventing Moisture Contact: Cement is hygroscopic and absorbs moisture, which can compromise its qualityStepbyStep Guide to the Manufacturing of Cement PRACTICAL
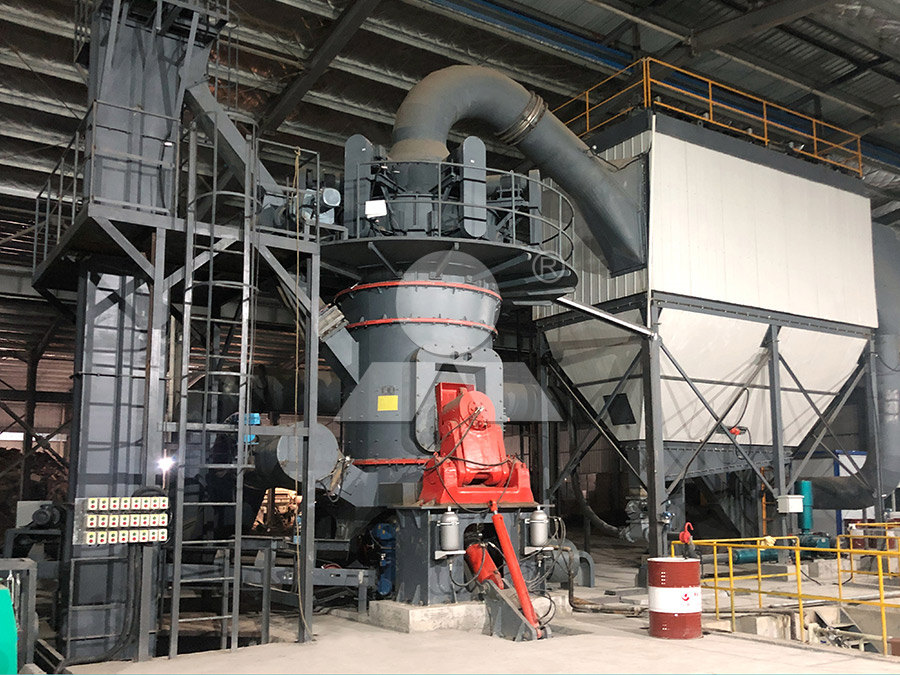
(PDF) Analysis of material flow and consumption in
2015年8月1日 The results show that approximately 248t, 469t, and 341t of materials are required to produce a ton of the product in raw material preparation, clinker production, and cement grinding stages 4 raw meal grinding process Cement grinding mill and cement mill including raw materials , equipment commonly used in ball mill, vertical mill , roller press and so on Dry grinding generally use closed operating system Normally open wet Flow Chart Of Cement Industry { Dry Process } BloggerThe mill came into use in the 1890s, initially for regrinding rejects, both in dry rawmix and cement grinding Later, they came to be used for the entire grinding process Martin Earles first installed them for autonomous cement grinding in Cement Kilns: Size Reduction and GrindingThe flow chart below shows the process of cement manufacturing Figure 1: Process Flow Chart Proposed Integrated Cement Project (Clinker: 35 MTPA; Cement: ♦ Clinkerisation of the raw meal in a rotary kiln with multistage preheater and precalcinator ♦ Grinding, storage and packing ♦ Final dispatch 22 Captive Power Plant M/s Ultratech Cement Limited (UTCL) 11 DETAILS OF THE PROJECT
.jpg)
OPTIMIZATION OF CEMENT GRINDING OPERATION IN BALL MILLS
Condition in one of the grinding chambers of the mill Results of Optimization The graphical analysis presented in Figure 2 represents progress of grinding along the length of the mill after optimizing the grinding process rogress of grinding is clearly visible in Desired p the graphs Figure 2: Analysis of longitudinal samplesHero to Net Zero Cement Production Using Chart's Cryogenic Carbon Capture™ (CCC) to capture some of the 35 billion tonnes of carbon dioxide emissions from the world's cement factories Download Holcim Cement Main Filter Fan Energy savings and increased capacity for Holcim plant Download Lafarge Cement Kiln ID fans in EgyptCement Manufacture Chart IndustriesCement manufacturing is the source of 5% of global CO 2 emissions 60% of emissions are due to the transformation of raw materials at high temperatures and 40% results from the combustion required to heat the cement kilns 1400°C to1500°C Therefore emissions monitoring is extremely critical for cement plants to meet regulatory requirementsA practical guide to improving cement manufacturing processes 2015年1月31日 From hubandspoke model to split grinding; from singlegrinding solution to a combination of system solutions; and from energyintensive traditional ball mill to upgraded versions and use of pregrinders, the cement industry is shifting towards more energyefficient grinding solutions ICR trains its spotlight on the current technology trends The cement Grinding Solutions Indian Cement Review
.jpg)
Cement Manufacturing Process INFINITY FOR CEMENT EQUIPMENT
The commnation method belongs to the most efficient grinding processes applied in the cement manufacturing Separation: the ground and dried material is lifted up Precast, prefired shapes made with lowcement castables usually last from 3 to 10 years without maintenance in cooler walls The back wall and the hood ceiling can be 5 天之前 The manufacture of Portland cement is a complex process and done in the following steps: grinding the raw materials, mixing them in certain proportions depending upon their purity and composition, and burning them to sintering in a kiln at a temperature of about 1350 to 1500 ⁰C During this process, these materials partially fuse to form nodular shaped clinker by Manufacturing of Portland Cement – Process and MaterialsWet Process Of Cement Manufacturing With Flow Chart The raw materials are calcareous materials, like limestone or chalk, and argillaceous material such as shale or clay Skip to content Grinding of Raw Materials: The crushed Wet Process Of Cement Manufacturing With Flow Download scientific diagram Process flow diagram for the cement manufacturing process, showing electricity and heat consumption or inputs [39] from publication: Energy Savings Associated with Process flow diagram for the cement manufacturing
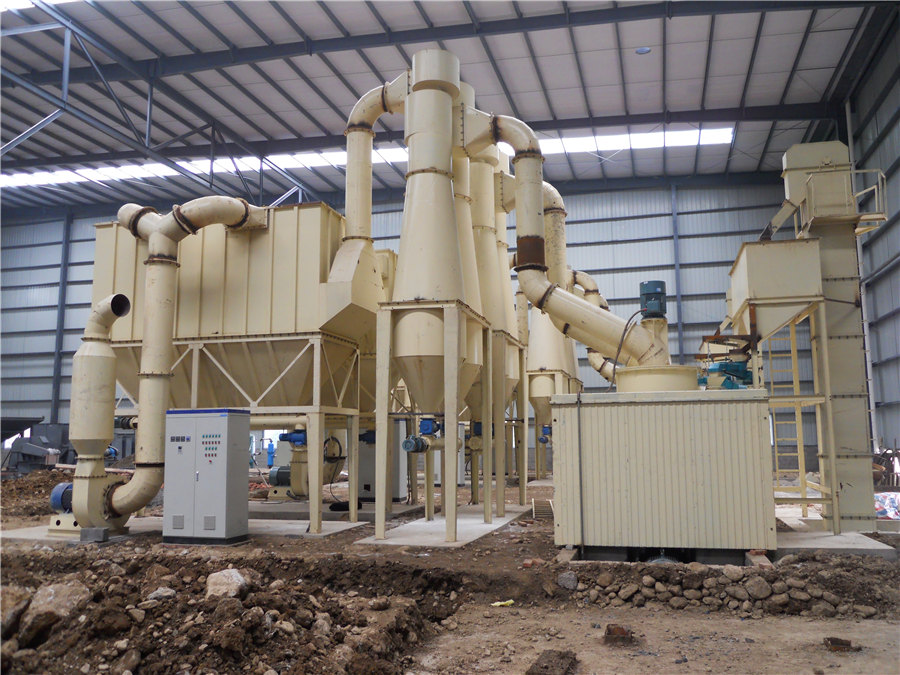
Cement manufacturing process PPT Free Download
2014年6月10日 This document discusses Portland cement and the cement manufacturing process It begins with an overview of what cement is and how it is used to make concrete It then describes the industrial process for 6 Cement Production Technology –Cement Grinding –Mechanical Design and Function of Separator Separators –General Classification of Separating Principles •according to flow direction relative to particle track •according to kind of separating field separation by gravitational force separation by centrifugal forceCement Grinding myPolysiusServiceDownload scientific diagram The flowchart of cement grinding, A, Bsampling points (evacuation stacks) [37] from publication: Dust Emission Monitoring in Cement Plant Mills: A Case Study in The flowchart of cement grinding, A, Bsampling points 2016年10月5日 In this chapter an introduction of widely applied energyefficient grinding technologies in cement grinding and description of the operating principles of the related equipments and comparisons over each other in terms of grinding efficiency, specific energy consumption, production capacity and cement quality are given A case study performed on a EnergyEfficient Technologies in Cement Grinding IntechOpen
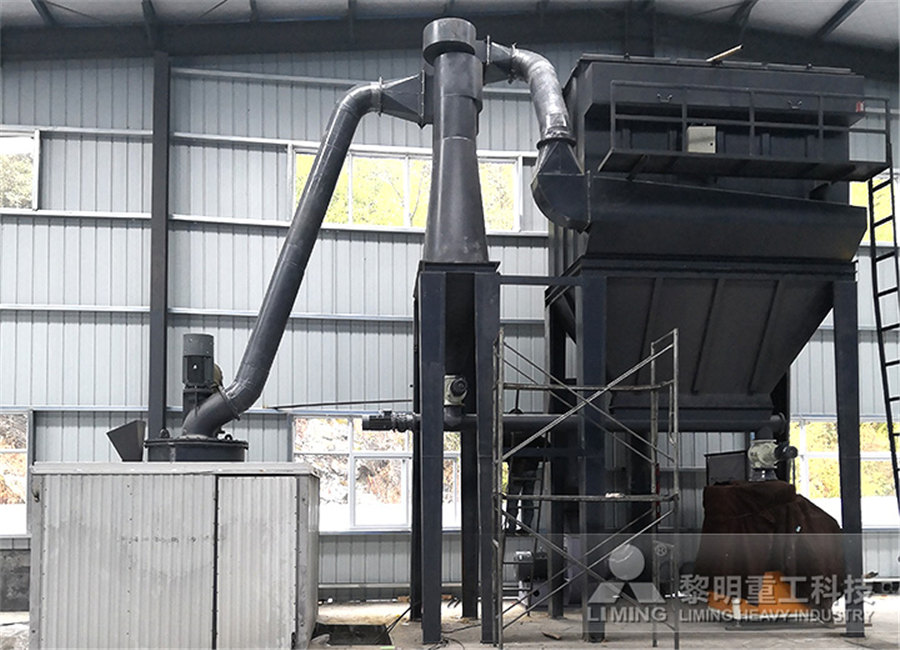
2 Types of Manufacturing of Cement Wet and Dry Process
In the wet process, which involves grinding raw materials into a slurry and then feeding them into a rotary kiln for drying and calcination Total Time: 3 minutes Raw Material Preparation The raw materials such as limestone, clay, Flowchart of cement manufacturing Wet Process Source Building materials by SKDuggal Dry process Source Download scientific diagram Flow chart of the grinding and blending process from publication: Effective Optimization of the Control System for the Cement Raw Meal Mixing Process: I PID Tuning Flow chart of the grinding and blending process1 The basics of cement manufacture – 2 History of cement manufacture – 3 Portland cement in today’s world 2 Raw materials management system – 22 Concrete problems 16 1 Raw materials – 2 Raw mix – 3 Reserves – 4 Crushing – 5 Drying – 6 Preblending – 7 Storage and handling 3 Raw milling and blending 3The Cement Plant Operations Handbook International Cement 2020年10月5日 12 Working In case of continuously operated ball mill, the material to be ground is fed from the left through a 60° cone and the product is discharged through a 30° cone to the right As the shell rotates, the balls are lifted up on the rising side of the shell and then they cascade down (or drop down on to the feed), from near the top of the shellCement industry : grinding process of ball mill PPT SlideShare