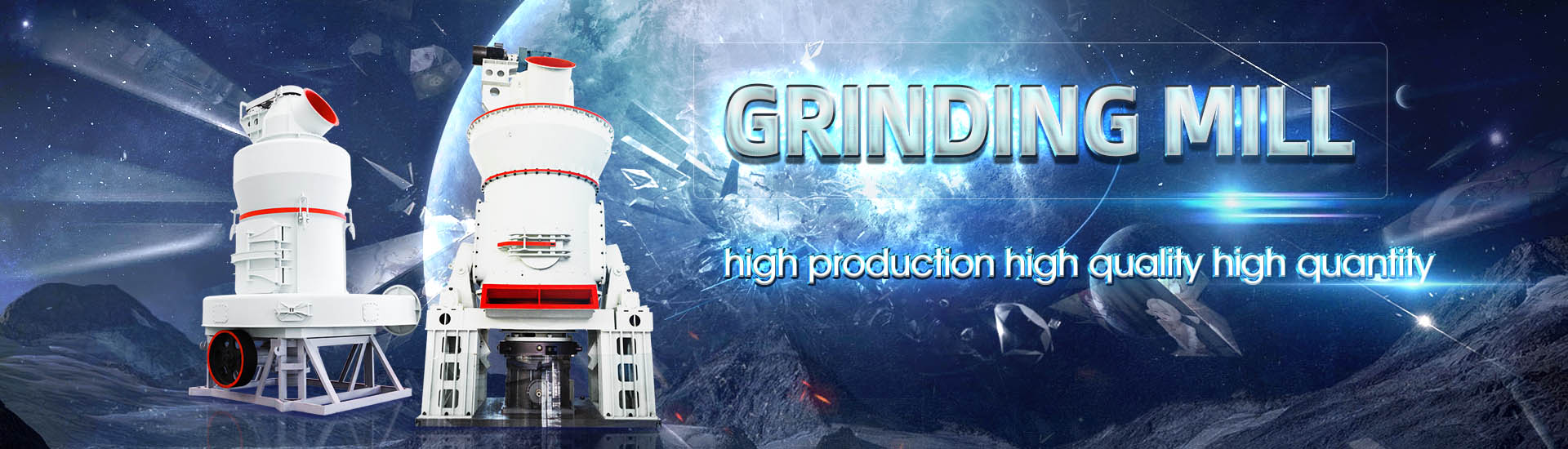
Process flow of cement production with vertical mill
.jpg)
Vertical roller mill for raw Application p rocess materials
The conventional process gas flow of the mill grinding system generally consists of vertical roller mill with separator, cyclone, mill circulation fan, and electrostatic precipitator (EP) and EP fan The vertical roller mill (VRM) is a type of grinding machine for raw material processing and cement grinding in the cement manufacturing process In recent years, the VRM cement mill has been equipped in more and more cement Vertical Roller Mill Operation in Cement Plant2017年9月11日 In this study, an extensive sampling study was carried out at vertical roller mill of ESCH Cement Plant in Luxemburg Samples were collected from mill inside and around the circuit to(PDF) Performance Evaluation of Vertical Roller Mill in The core elements of these plants are the Loesche vertical mills for drygrinding the abovementioned grinding stock Loesche has developed and built the largest and most efficient PROCESS OPTIMISATION FOR LOESCHE GRINDING PLANTS
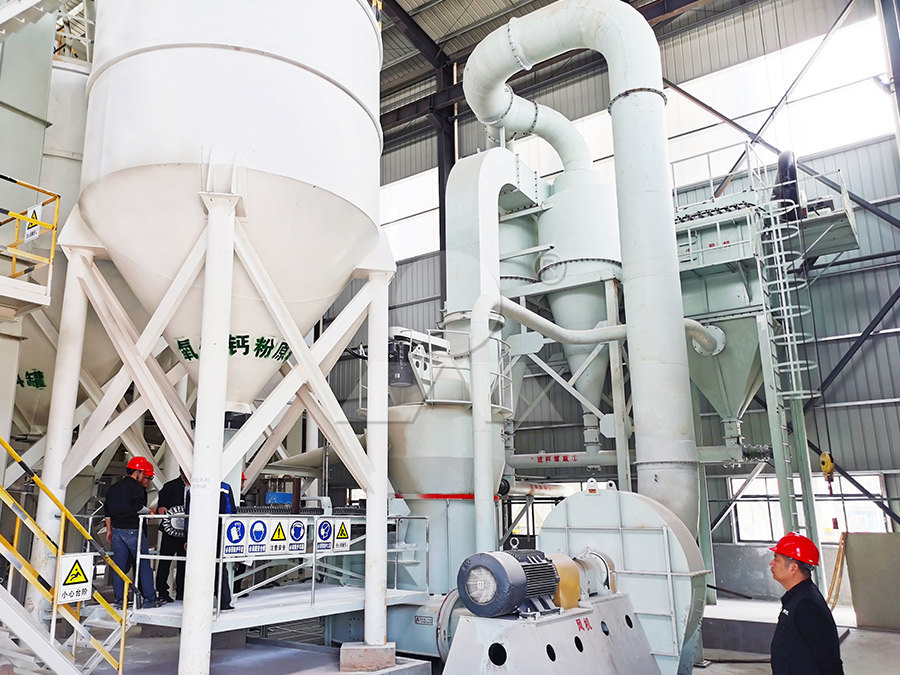
PROCESS CONTROL FOR CEMENT GRINDING IN VERTICAL
The Vertical Roller Mill (VRM) reduces the power consumption for cement grinding approximately 3040% associated with other grinding mills The process variables in cement grinding process The cement production process 1 The Quarry: The cement production process begins with the extraction of limestone and clay from the quarry 2 Crusher and PreBlending: The material is A practical guide to improving cement manufacturing processes Providing a comprehensive guide to the entire cement production process from raw material extraction to the finished product, the industry’s favourite technical reference book is now fully The Cement Plant Operations Handbook International Cement 2017年6月19日 The modular vertical roller mill for grinding cement raw material, cement clinker, and additives with an installed power of up to 12,000 kW was specifically designed to meet the Grinding process optimization — Featuring case studies and
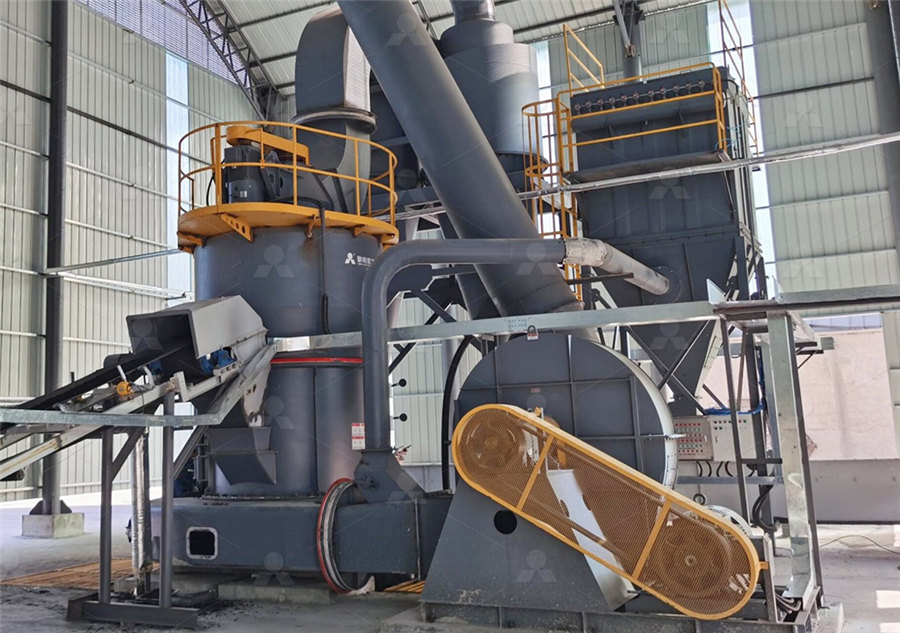
Operational parameters affecting the vertical roller mill
2017年4月1日 Vertical roller mills (VRM) have found applications mostly in cement grinding operations where they were used in raw meal and finish grinding stages and in power plants AGICO Cement provides vertical cement mill, vertical roller mill used for cement manufacturing, powerful grinding and homogenization, customdesign cement mill, onschedule delivery Skip to content +86 Vertical Cement Mill, Vertical Roller Mill Buy Mixing and Blending for the manufacturing of cement Dry Process In the dry process of cement manufacturing, workers first mine and crush raw materials such as limestone, clay, and sand, then transport them to a grinding mill StepbyStep Guide to the Manufacturing of CementCEMENT PRODUCTION AND QUALITY CONTROL A Cement manufacturing Process Source:civilengineeringforumme The whole process of cement manufacturing in Messebo Cement plant which consists of two separate Cement Production lines can be summarized into the following processes ;as can be seen in the process and Quality flow diagram below; 1CEMENT PRODUCTION AND QUALITY CONTROL
.jpg)
Vertical Cement Mill Magotteaux
Providing Consistent Results With Advanced Vertical Cement Mill Technology Magotteaux’s advanced vertical cement mill technology ensures consistent results by providing precise control over the grinding process, enabling the production of highquality cement with minimal variations in finenessMoreover, our use of advanced materials and innovative designs ensures that our The vertical roller mill fulfills four main functions in one compact piece of equipment: Grinding; increasing finish mill power consumption or reducing mill production as well as reduce cement strength (greater amounts of exhaust gases must be Cement Manufacturing Process INFINITY FOR CEMENT EQUIPMENTThe use of fossil fuels such as coal, natural gas, and oil is common in cement production, both as a fuel for the kiln and as a source of heat for other parts of the process which leads to CO2 emitted by combustionHowever chemical reactions happening in the kiln (calcination) are also responsible for up to 60% of the total of emissions of the cement production process [PCA]Cement Production Demystified: StepbyStep Process and A 10 MW cement mill, output 270 tonnes per hour A cement mill (or finish mill in North American usage [1]) is the equipment used to grind the hard, nodular clinker from the cement kiln into the fine grey powder that is cementMost cement is currently ground in ball mills and also vertical roller mills which are more effective than ball millsCement mill Wikipedia
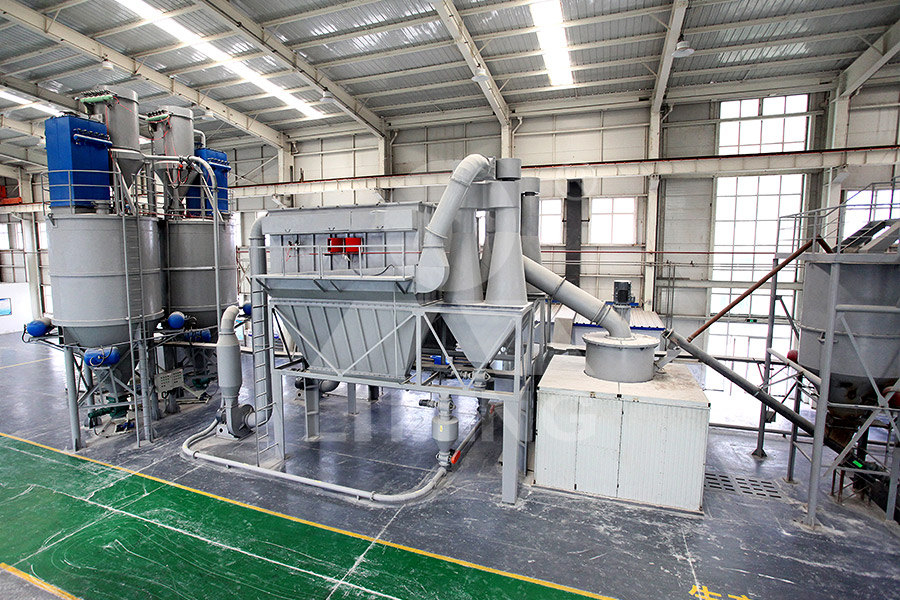
The Cement Production Process
The process of improving the energy efficiency of cement production is not complete What might be described as spectacular improvements are probably at an end as the limits of thermal efficiency are approached There is no longer any scope for further specialisation of the functions of the kiln and associated equipment2020年8月25日 A full cement production process includes the cement crushing process, raw mill process, clinker process, and cement grinding process, cement ball mill and cement vertical mill are generally used in the raw meal process; the finished raw meal are finally sent to the stacker and reclaimer for storage and further mixingCement Production Process Cement Manufacturing Process AGICO CEMENTProviding a comprehensive guide to the entire cement production process from raw material Finish mill – 12 Cement – 13 Quality control – 14 Packing and distribution – 15 Emission abatement (dust, NO x, SO 2, etc) – 16 mentioned in Chapter 3 for dry raw milling – ball mills, vertical roller mills, roll presses, Horomill The Cement Plant Operations Handbook International Cement The cement production process 1 The Quarry: The cement production process begins with the extraction of limestone and clay from the quarry 2 Crusher and PreBlending: The material is then crushed to reduce particle sizes and blended to reduce variability in composition 3 Raw Mill and Kiln: Raw materials and additives areA practical guide to improving cement manufacturing processes
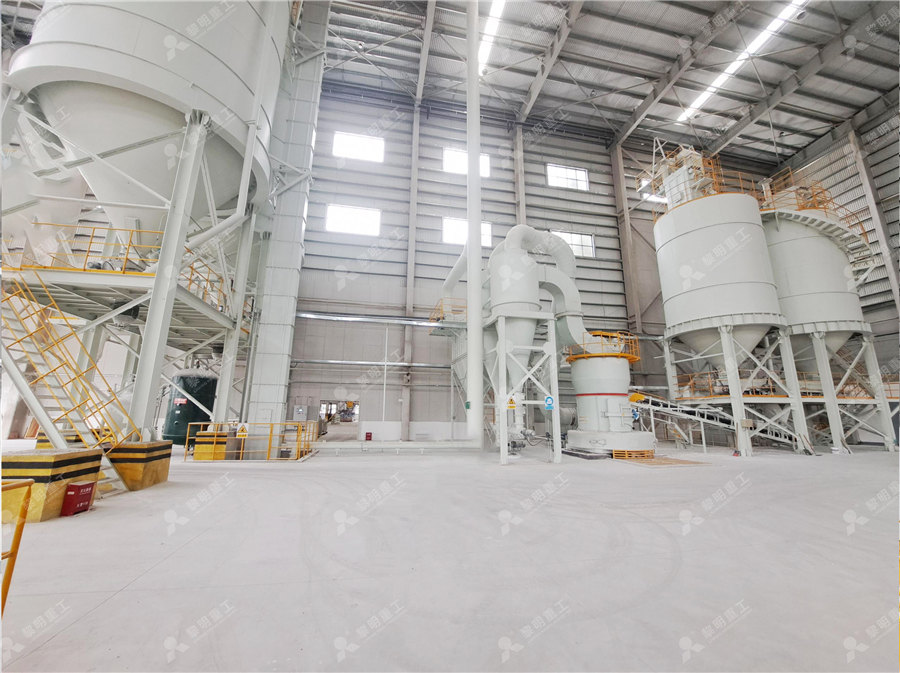
Heat Integration in a Cement Production IntechOpen
2017年10月20日 1 Introduction Nowadays, cement manufacturing is an energyintensive industry The energy costs of cement industry are about 40% of the product cost that indicates that this sector is one of the biggest CO 2 2018年8月28日 CEMENT MANUFACTURING PROCESS PHASES Production of cement completes after passing of raw materials from the following Rotating ball mill CEMENT MANUFACTURING PROCESS PHASE VI: PACKING AND Cement Manufacturing Process The Engineering Vertical roller mills and ball mills represent two clearly distinct technologies However, with proper adjustments to the operational parameters of the vertical roller mill almost identical cement properties can be achieved by the two mills that satisfy the cement user’s demandsNevertheless, the two types of mills have their distinctive meritsCement grinding Vertical roller mills VS ball millsApplication of Vertical Roller Mill in Cement Industry Vertical roller mill (VRM) technology has become an integral part of the cement industry, offering several advantages over traditional grinding mills Today, this type of grinding machine is becoming more and more popular in both the raw material grinding process and the cement grinding Application of Vertical Roller Mill in Cement Production
.jpg)
3 Necessary Cement Milling Comparison Ball Mill, Vertical Roller Mill
2020年11月5日 As you all know, the process of a cement manufacturing plant can be divided into several steps, including crushing, raw milling, clinker calcining, cement milling (or cement grinding), packing and etc In the complete cement production line, the cement mill process plays a very important role The design of cement milling and cement mill process will produce a 5 天之前 Dry process, wet process, how ,cement production, cement plant Skip to content November 28, 2024 The Fig1 show the flow diagram of the dry process of the manufacture of sixstage preheater, and vertical roller mill The latest Technology with a modern control system includes stacker and Manufacturing of Portland Cement – Process and Materialsconsumption and low production The consumption of energy by the cement grinding operation amounts to one third of the total electrical energy used for the production of cement The optimization of this process would yield substantial benefits in terms of energy savings and capacity increase Optimization of the Cement Ball Mill OperationOPTIMIZATION OF CEMENT GRINDING OPERATION IN BALL MILLSRaw mill is generally called cement raw mill, raw mill in cement plant, it refers to a common type of cement equipment in the cement plantIn the cement manufacturing process, raw mill in cement plant grind cement raw materials into the raw mix, and the raw mix is sent to the cement kiln to make cement clinker, next, clinker and other admixtures will be ground into finished cement by Raw mill Cement Plant

PROCESS TRAINING for operators of Vertical RAW Mills
PROCESS TRAINING for operators of Vertical RAW Mills feed rate to the mill, production rate (t/h]differential pressure of mill [mbar]air flow through mill [m3/h]vibration veloci ty at gearbox [mm/sec] The air flow throu gh mill is necessary for several reasons2017年8月15日 The materials reach temperatures of 2500°F to well above 3000°F in the kiln Rotary kilns are divided into two groups, dryprocess and wetprocess, depending on how the raw materials are prepared In wetprocess kilns, raw materials are fed into the kiln as a slurry with a moisture content of 30 to 40 percentThe Cement Manufacturing Process2020年9月26日 Cement Manufacturing Process: Both the materials are then channeled to mill equipment where they are intimately mixed in desired proportions to form a paste Coriolis Flow Transmitter Working November Cement Manufacturing Process Chemical The cyclone preheating system Phase IV: Calcination The calcination is the core phase of the cement making dry process The calcination of the preheated raw meal takes place in the rotary kiln of the cement plant The rotary kiln is a How Is Cement Produced in Cement Plants Cement
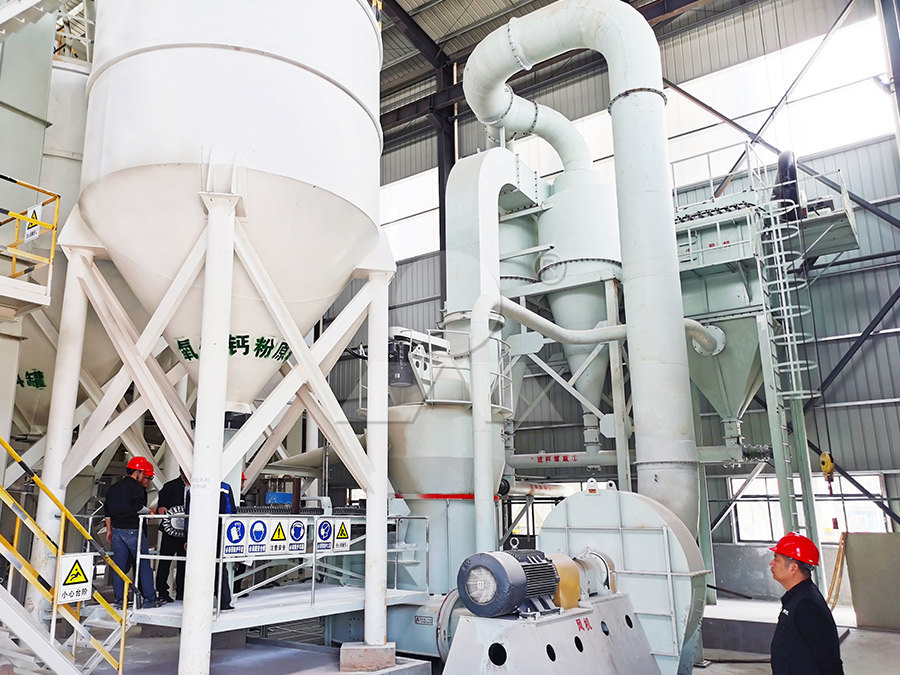
Modeling and simulation of vertical roller mill using population
Keywords: vertical roller mill, modeling, simulation, cement grinding, residence time distribution 1 Introduction Grinding operation is one of the important parts of the cement production processes Almost producing one ton of cement requires 15 tons of raw materials The electrical energy consumed in theVertical raw mill is one kind of raw mill, generally used to grind bulk, granular, and powder raw materials into required cement raw meal in the cement manufacturing plantVertical raw mill is an ideal grinding mill that crushing, drying, grinding, grading transfer set in one It can be widely used in cement, electric power, metallurgy, chemical industry, nonmetallic ore, and other industriesVertical raw mill Cement Plant2024年11月23日 Cement Extraction, Processing, Manufacturing: Raw materials employed in the manufacture of cement are extracted by quarrying in the case of hard rocks such as limestones, slates, and some shales, with the aid of blasting when necessary Some deposits are mined by underground methods Softer rocks such as chalk and clay can be dug directly by Cement Extraction, Processing, Manufacturing BritannicaA cement vertical raw mill process was studied in a cement plant, south west, Nigeria, and both input and output variables were collected Data was collected for about a month from the distributed control system database every minute The operational parameters of the cement plant for the year 2021 were analyzed and obtained from its recordsAssessment of the thermodynamics efficiency of a cement vertical
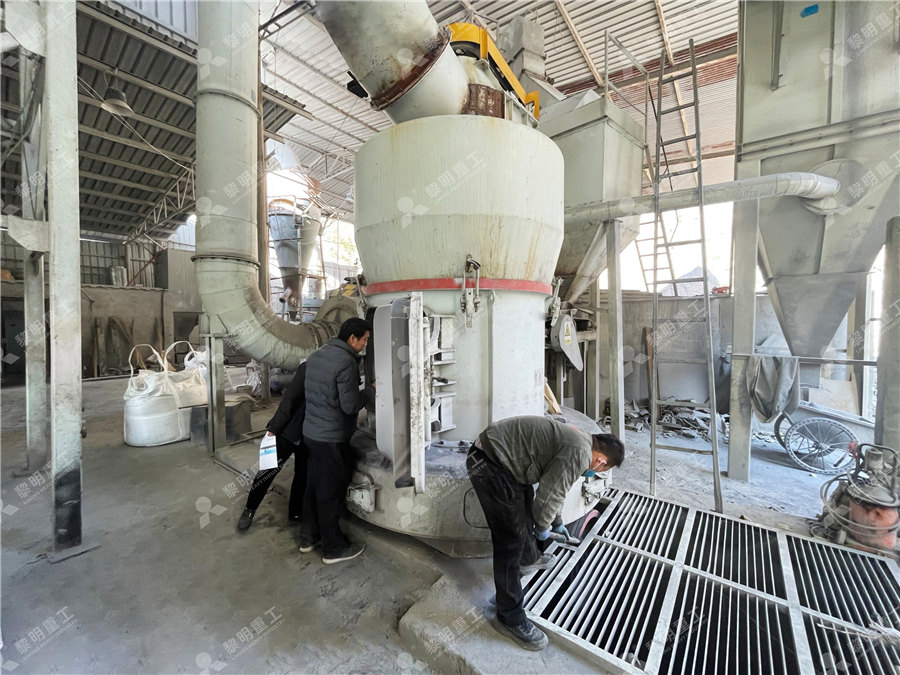
Cement Grinding Station Solution Ball Mill and Vertical Mill
cement product has excellent performance, cement particle shape is equivalent to ball mill, cement strength (3d, 7d, 28d strength) is equivalent to ball mill or even slightly higher, water requirement can be controlled at 2628%, the cement particle matching is convenient to adjust1 Jaw crusher hammer mill 2 Storage silo for raw material 3 Ball mill for raw mixer 4 Storage for raw mixer 5 Vertical Shaft Kiln 6 Storage silo for clinker 7 Ball mill for cement grinding 8 Storage silo for cement Figure 1 Process Flow sheet of Cement Manufacturing situated on the top of the kiln Kiln OperationCleaner production assessment in cement plant using vertical Process flow CKP type Vertical roller grinding mill is mainly composed of motor, reducer, grinding disc, grinding roller, hydraulic device, lubrication which has higher grinding effect than the existing roller press It can increase the production capacity of CKP vertical pregrinding millAGICO Cement provides vertical cement mill, vertical roller mill used for cement manufacturing, powerful grinding and homogenization, customdesign cement mill, onschedule delivery Skip to content +86 Vertical Cement Mill, Vertical Roller Mill Buy
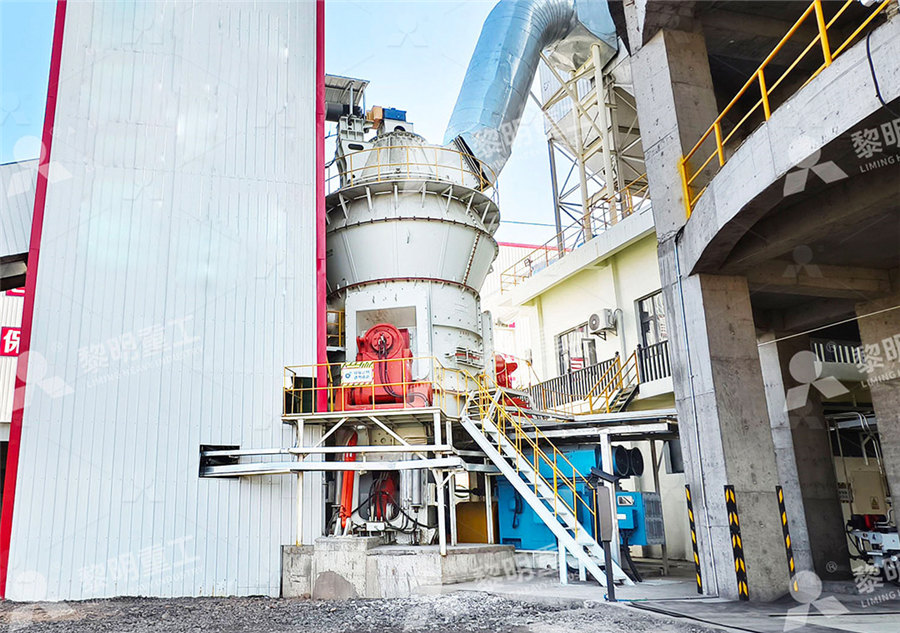
StepbyStep Guide to the Manufacturing of Cement
Mixing and Blending for the manufacturing of cement Dry Process In the dry process of cement manufacturing, workers first mine and crush raw materials such as limestone, clay, and sand, then transport them to a grinding mill CEMENT PRODUCTION AND QUALITY CONTROL A Cement manufacturing Process Source:civilengineeringforumme The whole process of cement manufacturing in Messebo Cement plant which consists of two separate Cement Production lines can be summarized into the following processes ;as can be seen in the process and Quality flow diagram below; 1CEMENT PRODUCTION AND QUALITY CONTROLProviding Consistent Results With Advanced Vertical Cement Mill Technology Magotteaux’s advanced vertical cement mill technology ensures consistent results by providing precise control over the grinding process, enabling the production of highquality cement with minimal variations in finenessMoreover, our use of advanced materials and innovative designs ensures that our Vertical Cement Mill MagotteauxThe vertical roller mill fulfills four main functions in one compact piece of equipment: Grinding; increasing finish mill power consumption or reducing mill production as well as reduce cement strength (greater amounts of exhaust gases must be Cement Manufacturing Process INFINITY FOR CEMENT EQUIPMENT
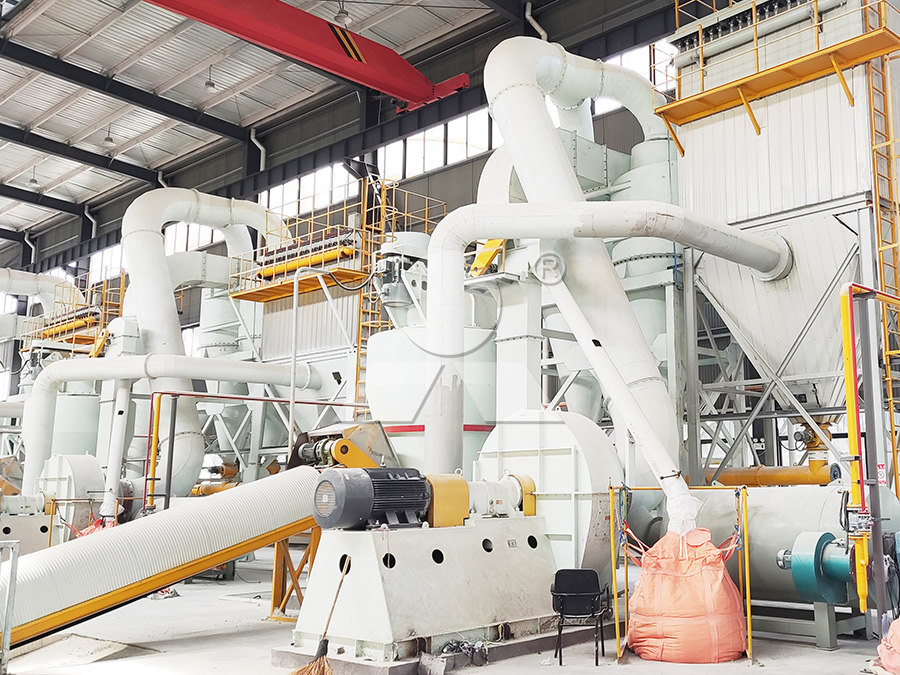
Cement Production Demystified: StepbyStep Process and
The use of fossil fuels such as coal, natural gas, and oil is common in cement production, both as a fuel for the kiln and as a source of heat for other parts of the process which leads to CO2 emitted by combustionHowever chemical reactions happening in the kiln (calcination) are also responsible for up to 60% of the total of emissions of the cement production process [PCA]A 10 MW cement mill, output 270 tonnes per hour A cement mill (or finish mill in North American usage [1]) is the equipment used to grind the hard, nodular clinker from the cement kiln into the fine grey powder that is cementMost cement is currently ground in ball mills and also vertical roller mills which are more effective than ball millsCement mill WikipediaThe process of improving the energy efficiency of cement production is not complete What might be described as spectacular improvements are probably at an end as the limits of thermal efficiency are approached There is no longer any scope for further specialisation of the functions of the kiln and associated equipmentThe Cement Production Process2020年8月25日 A full cement production process includes the cement crushing process, raw mill process, clinker process, and cement grinding process, cement ball mill and cement vertical mill are generally used in the raw meal process; the finished raw meal are finally sent to the stacker and reclaimer for storage and further mixingCement Production Process Cement Manufacturing Process AGICO CEMENT
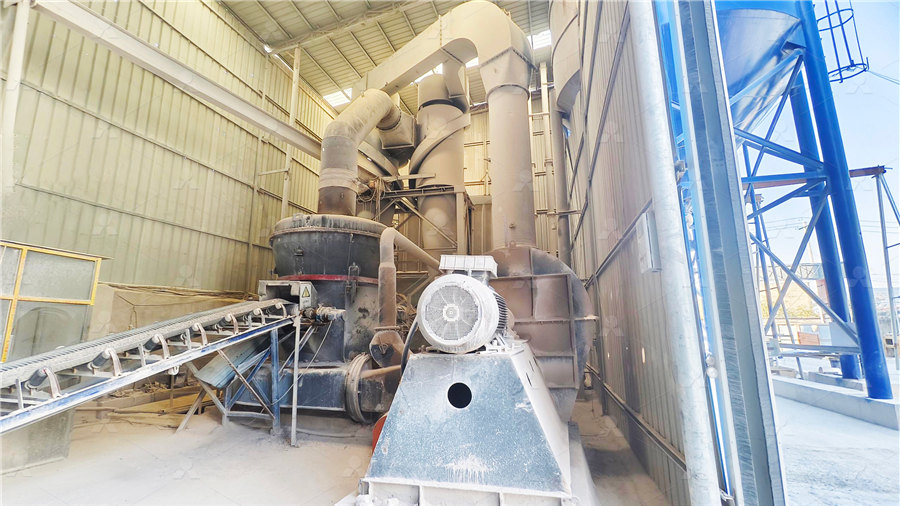
The Cement Plant Operations Handbook International Cement
Providing a comprehensive guide to the entire cement production process from raw material Finish mill – 12 Cement – 13 Quality control – 14 Packing and distribution – 15 Emission abatement (dust, NO x, SO 2, etc) – 16 mentioned in Chapter 3 for dry raw milling – ball mills, vertical roller mills, roll presses, Horomill