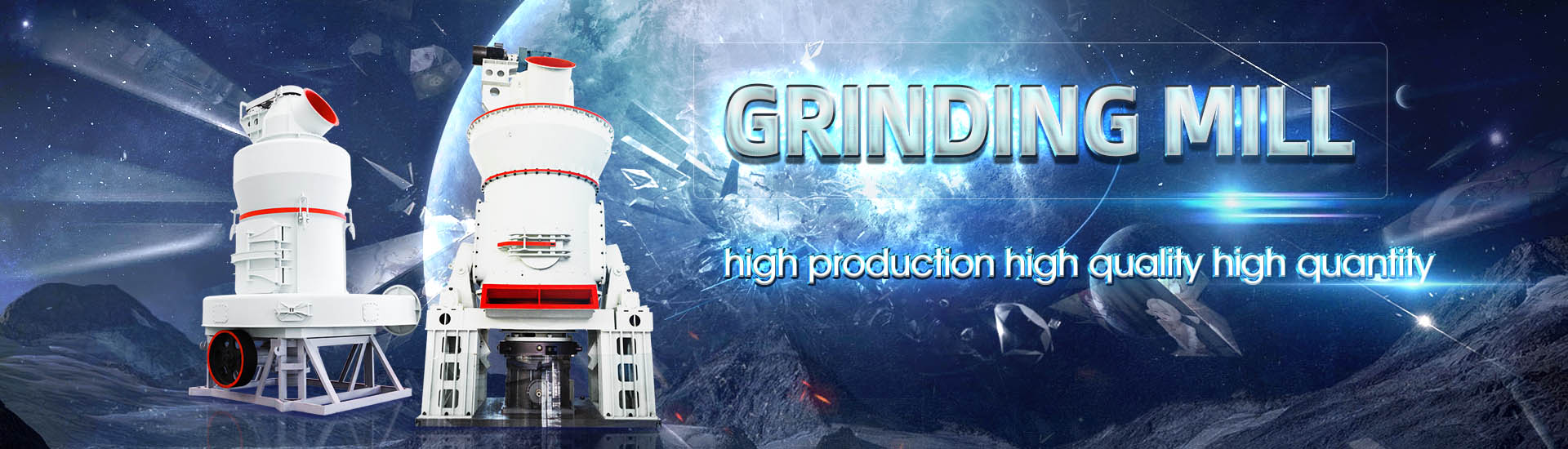
Washboard coal raw coal mill
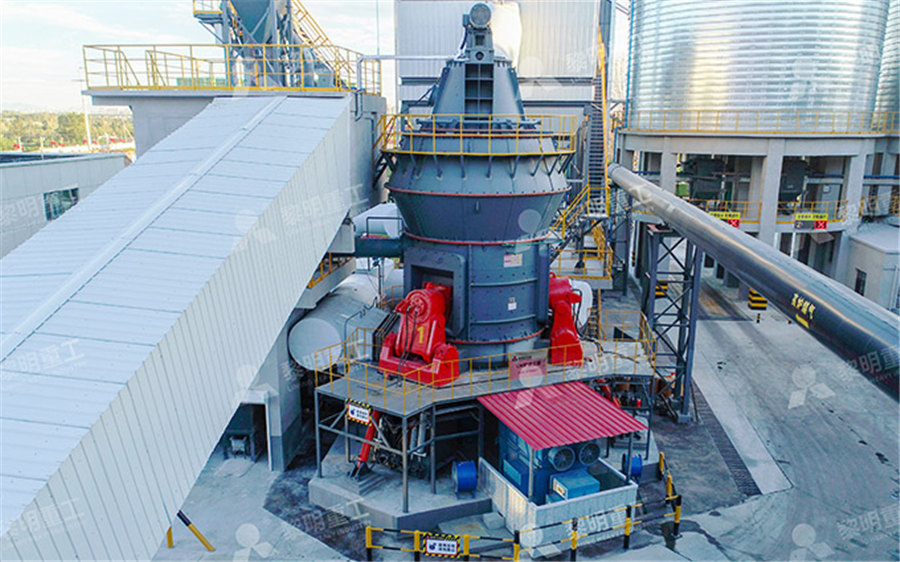
Modeling and Control of Coal Mill
Coal mill is an important component of the thermal power plant It is used to grind and dry the moisturized raw coal and transport the pulverized coal – air mixture to the boiler Poor dynamic Mills are mechanical devices used to break different types of solid materials in small pieces by grinding, crushing or cutting In pulverised coalfired power plants, a pulveriser coal mill grinds Coal Mill an overview ScienceDirect Topics2012年5月1日 The paper presents development and validation of a coal mill model to be used for improved mill control, which may lead to a better load following capability of power plants Derivation and validation of a coal mill model for controlCoal mill is an important component of the thermal power plant It is used to grind and dry the moisturized raw coal and transport the pulverized coal – air mixture to the boiler Poor dynamic (PDF) Modeling and Control of Coal Mill Academia
.jpg)
ATOX COAL MILL
The ATOX mill will grind and dry coal containing more than 20% moisture in one operation The possibility of customersupplied parts, along with the low civil costs that accompany compact mill installation, add to the excellent economy of the ATOX coal mill Working principles The raw coal enters the mill via a rotary sluice and feed chuteCoal mill is an important component of the thermal power plant It is used to grind and dry the moisturized raw coal and transport the pulverized coal – air mixture to the boiler Poor dynamic performance of coal mill will lead to decrease in the overall efficiency of the power plant, slow load take up rate and frequent shut down(PDF) Modeling and Control of Coal Mill Academia2012年5月1日 A simplified design schematic of a socalled roll mill is presented in Fig 2 Raw coal is transported on a conveyor belt and dropped into the mill, where it falls onto a grinding table and is crushed by rollers Primary air, blown from the bottom of the mill, picks up fine coal particles and transports them into the classifier sectionDerivation and validation of a coal mill model for controlTo convert raw coal into fine coal powder, coal grinding mills are essential Coal grinding mills are specialized equipment designed to break down coal into fine particles suitable for combustion The coal grinding process involves crushing and grinding coal into small particles, which are then heated to high temperatures in a furnace, producing steam that drives a turbine to generate What is a Coal Grinding Mill
CFB石灰石脱硫剂制备——磨机公众号12.8 推送案例(8)53.jpg)
Modeling and Control of Coal Mill
Coal mill is an important component of the thermal power pla nt It is used to grind and dry the moisturized raw coal and transport the pulverized coal ± air mixture to the boiler Poor dynamic performance of coal mill will lead to decrease in the overall efficiency of the power plant, slow load take up rate and fr equent shut down2009年9月20日 A control oriented model was then developed by Fan (1994) and Fan and Rees (1994) In 2009, coal flow and outlet temperature of mill were modelled using mass and heat balance equations for startup Modeling and Parameter Identification of Coal MillA coal mill is also called a coal pulverizer or coal grinder It is a mechanical device used to grind raw coal into pulverized coal powders The most used coal mills in cement plants are airswept ball mills and vertical roller mills At present, most cement plants use coal as the main fuel in the clinker production processCoal Mill in Cement PlantRaw coal enters the coal ball mill through the feeding device At this time, hot air with a temperature up to 300℃ enters the coal mill barrel from the intake pipe The raw coal falls on the lifting plate of the drying chamber and is continuously raised In the process of heat exchange between raw coal and hot air, water is continuously Coal Ball Mill Grinding for Different Kinds of Pulverized Coal
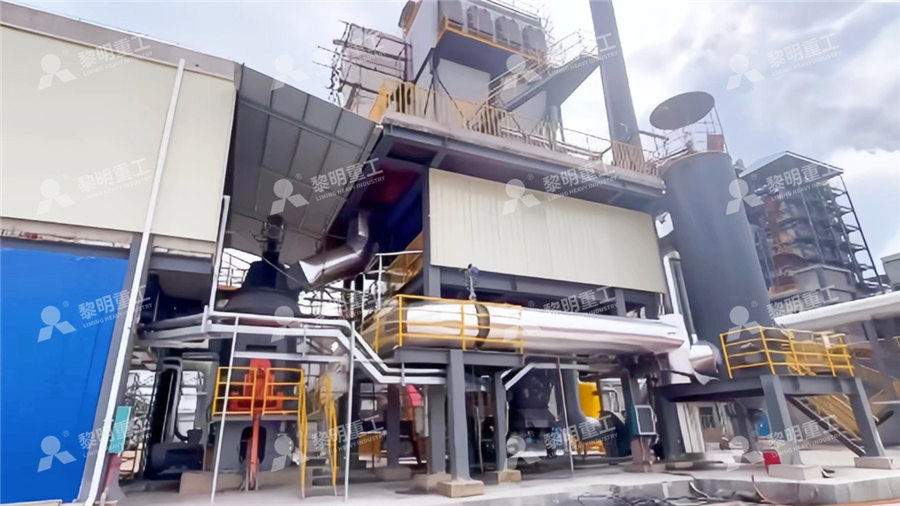
(PDF) MPS mills for coal grinding ResearchGate
2014年1月1日 The emission factors of kiln end, kiln head, coal mill, crushing and cement mill was 0156 clinker g/t, 3914 clinker g/t, 1538 coal g/t, 0016 stone g/t and 0056 cement g/t respectively, the 2024年5月1日 The applicable coal types are bituminous coal, partly poor coal and partly lignite For normal operation of coal mill, the hardgrove grind ability index is between 40 and 80; the particle size of raw coal is smaller than 40 mm Additional specific technical data for the coal mills are listed in Table 1Dual fault warning method for coal mill based on ScienceDirectSafe operation of coal grinding systems: Raw coal silo protection against fire and explosions Safe operation of coal grinding systems: Raw coal yard management The purchasing process for coal grinding systems needs changes Talk at a virtual seminar, November 2023 Accept the probability that the fire and explosion safety of your coal grinding Best Practices and Precautions Coal Mill Safety, Explosion and This flow sheet and sampling map shows the process flow for a cement plant Key components include: 1) Raw materials like iron sand, silica sand, limestone, clay and gypsum being fed into crushers and mills 2) Processed materials Flow Sheet Kiln, Raw Mill N Coal Mill PDF Cement
.jpg)
Analysis of the Coal Milling Operations to the Boiler
2020年4月2日 Milling system in coal power plant purposely to process the raw coal to become as pulverise fuel before enter to the Coal mill motor power (kW) 0 4171 4548 4390 4586 4562 Feeding device sends raw coals into drying oven; drying oven is equipped with special lifting plate to scatter coal and make coal get strong heat exchange so that raw coal is dried; dry raw coal is sent into grinding storehouse via doublecompartment plate is equipped with grinding balls so that raw coal can be crushed and ground into coal powder in this compartment, while, a Air Swept Coal Mill Cement Plant Machinery– Interruptions in raw coal feed – Lower feeder speeds – This occurs because a minimum airflow through the coal mill must be maintained to insure that burner line velocities are not too low to allow settling of coal in the fuel lines or burner components – Not uncommon to achieve air to fuel ratios of 3 to 5 pounds of air per pound Mill Inerting and Pulverizer/Mill Explosion Mitigation15 Mill Wear and Ash Content in Raw Coal The coal is abrasive in nature due to the presence of hard materials like pyrites, α quartz etc, Due to the grinding nature and abrasiveness of coal, the mill parts tend to wear depending on the hours of service and A Study on 500 MW Coal Fired Boiler Unit’s Bowl Mill
.jpg)
Sectional view of MBF coal mill Download Scientific Diagram
Di dalam coal mill, raw coal masuk di antara griding table dan roller untuk digiling Hasil dari penggilingan raw coal, kemudian batubara akan menuju dust collector yang berfungsi untuk menyaring Safe operation of coal grinding systems: Raw coal silo protection against fire and explosions Safe operation of coal grinding systems: Raw coal yard management The purchasing process for coal grinding systems needs changes Talk at a virtual seminar, November 2023 Accept the probability that the fire and explosion safety of your coal grinding Coal Mill Safety: A Critical Aspect of Power Plant Operations Coal Safe operation of coal grinding systems: Raw coal silo protection against fire and explosions Safe operation of coal grinding systems: Raw coal yard management The purchasing process for coal grinding systems needs changes Talk at a virtual seminar, November 2023 Accept the probability that the fire and explosion safety of your coal grinding system is nothing more than a mirageCoal Mill Safety In Cement Production Industries2024年10月15日 Pulverized coal drying: Raw coal is grinded in the vertical coal mill and dried by hot air (usually below 300°) into the vertical roller coal mill, which meets the drying standard of finished pulverized coal For the safety operation of the following parameter are controlled to avoid the explosion of the coal mill bag filterCashew Nutshell and Raw Coal Cogrinding for Sustainability

coal grinding machine CHAENG
Vertical Coal Mill is specially used for ultrafine grinding of raw coal and bituminous coal materials in cement, power plants, iron and steel plants and other fields The GRMC coal vertical mill produced by CHAENG adopts special structural design and production process, which is energysaving and environmentally friendly2015年11月1日 The coal mill grinds the raw coal into fine powder and hot air entering the mill dries and carries the pulverized coal to the burners of the furnace Maffezzoni (1986) emphasized that coal mills are the primary cause of slow load following capability and regular plant shutdownsA unified thermomechanical model for coal mill operation2020年8月12日 This study shows the performance of a currently running vertical roller coal mill (VRM) in an existing coalfired power plant In a power plant, the coal mill is the critical equipment, whose An investigation of performance characteristics and 2021年8月1日 Yukio et al [7] proposed a model consisting of blending, grinding and classifying processes for pulverizer control Agarawal et al [8] differentiated coal powder into ten size groups, divided the bowl mill into four zones, and developed a unified model Palizban et al [9] derived nonlinear differential mass equations of raw coal, recirculation coal and suspension coal in Coal mill model considering heat transfer effect on mass
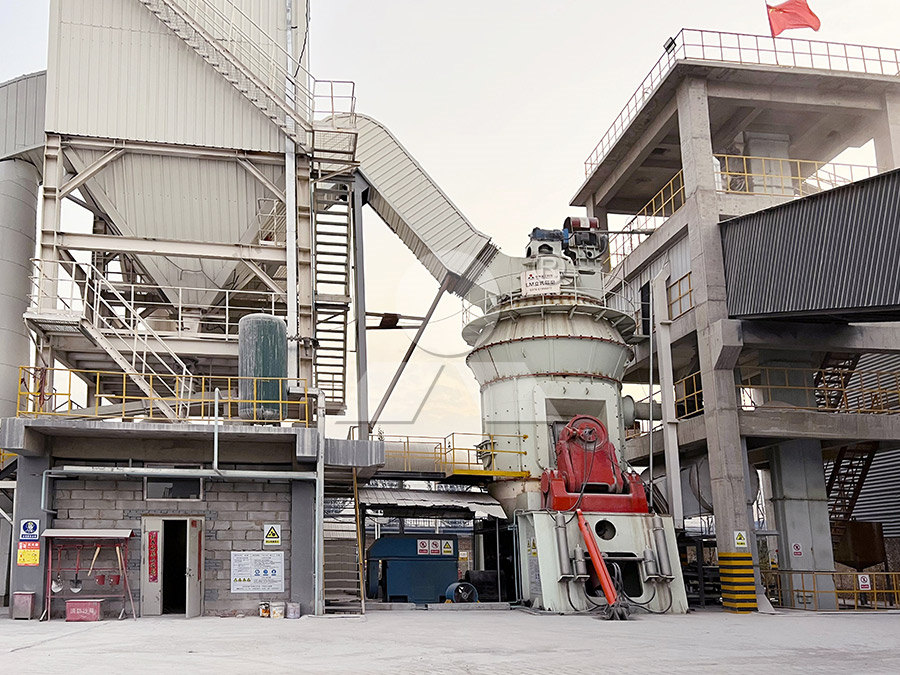
COAL GRINDING SYSTEMS SAFETY CONSIDERATIONS PEC
If the flow of raw coal to the coal mill is interrupted for any reason (for example: plugging, failure of the coal feeder, etc), the outlet temperature of the coal mill can climb to dangerous levels The quickly risk of explosions or fires can be extreme when the coal mill inlet temperature increases toYou will be surprised about what has gone wrong with fire and explosion protection of your system(s) Be sure about that! Evaluation of a coal grinding system’s fire and explosion protection, including the raw coal storage and the fine coal silo storage normally can be done in one day, mostly without having to stop coal grindingFire and explosion protection of coal grinding systems Where are functions to grind the raw coal to become pulverised fuel Besides that, mill system to ensure the continuously supply pulverised coal to the firing system of the boiler Each milling circuit is independent and includes: 1 Single bunker of raw coal storage with maximum 608 tonne capacity 2 Single raw coal feeders at maximum flow rate 70 t/hAnalysis of the Coal Milling Operations to the Boiler ParametersFurther pulverization of coal is achieved as the smaller coal particles are ground through attrition against each other and the grinding face Vertical Roller Mills This mill uses hydraulically loaded vertical rollers resembling large tires to pulverize raw coal fed down onto a rotating tableCoal Pulverizer – Power Plant Pall Corporation
.jpg)
Washed Coal from a Utilization Perspective Coal Combustion
washed coal has less ash and more moisture than the raw coal product This paper will use the following characteristics to compare washed coal to a raw product of the seam: Washed Coal Characteristics Less Ash Higher Moisture Smaller Sizing More Consistent Less Abrasive Lower Slagging Potential More Expensive in Cost per Calorific ValueCoal mill is an important component of the thermal power pla nt It is used to grind and dry the moisturized raw coal and transport the pulverized coal ± air mixture to the boiler Poor dynamic performance of coal mill will lead to decrease in the overall efficiency of the power plant, slow load take up rate and fr equent shut downModeling and Control of Coal MillThe ATOX mill will grind and dry coal containing more than 20% moisture in one operation The possibility of customersupplied parts, along with the low civil costs that accompany compact mill installation, add to the excellent economy of the ATOX coal mill Working principles The raw coal enters the mill via a rotary sluice and feed chuteATOX COAL MILLCoal mill is an important component of the thermal power plant It is used to grind and dry the moisturized raw coal and transport the pulverized coal – air mixture to the boiler Poor dynamic performance of coal mill will lead to decrease in the overall efficiency of the power plant, slow load take up rate and frequent shut down(PDF) Modeling and Control of Coal Mill Academia
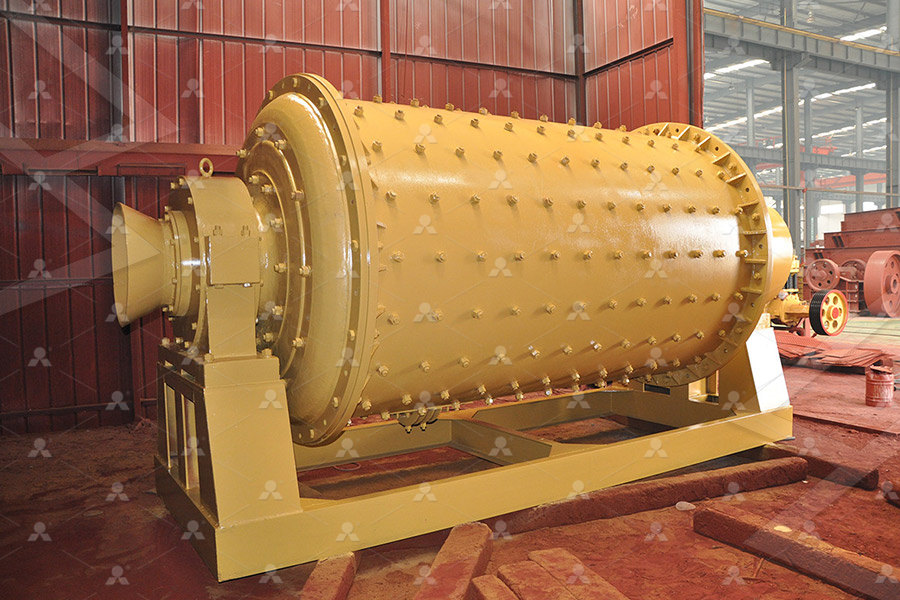
Derivation and validation of a coal mill model for control
2012年5月1日 A simplified design schematic of a socalled roll mill is presented in Fig 2 Raw coal is transported on a conveyor belt and dropped into the mill, where it falls onto a grinding table and is crushed by rollers Primary air, blown from the bottom of the mill, picks up fine coal particles and transports them into the classifier sectionTo convert raw coal into fine coal powder, coal grinding mills are essential Coal grinding mills are specialized equipment designed to break down coal into fine particles suitable for combustion The coal grinding process involves crushing and grinding coal into small particles, which are then heated to high temperatures in a furnace, producing steam that drives a turbine to generate What is a Coal Grinding MillCoal mill is an important component of the thermal power pla nt It is used to grind and dry the moisturized raw coal and transport the pulverized coal ± air mixture to the boiler Poor dynamic performance of coal mill will lead to decrease in the overall efficiency of the power plant, slow load take up rate and fr equent shut downModeling and Control of Coal Mill2009年9月20日 A control oriented model was then developed by Fan (1994) and Fan and Rees (1994) In 2009, coal flow and outlet temperature of mill were modelled using mass and heat balance equations for startup Modeling and Parameter Identification of Coal Mill
.jpg)
Coal Mill in Cement Plant
A coal mill is also called a coal pulverizer or coal grinder It is a mechanical device used to grind raw coal into pulverized coal powders The most used coal mills in cement plants are airswept ball mills and vertical roller mills At present, most cement plants use coal as the main fuel in the clinker production processRaw coal enters the coal ball mill through the feeding device At this time, hot air with a temperature up to 300℃ enters the coal mill barrel from the intake pipe The raw coal falls on the lifting plate of the drying chamber and is continuously raised In the process of heat exchange between raw coal and hot air, water is continuously Coal Ball Mill Grinding for Different Kinds of Pulverized Coal2014年1月1日 The emission factors of kiln end, kiln head, coal mill, crushing and cement mill was 0156 clinker g/t, 3914 clinker g/t, 1538 coal g/t, 0016 stone g/t and 0056 cement g/t respectively, the (PDF) MPS mills for coal grinding ResearchGate2024年5月1日 The applicable coal types are bituminous coal, partly poor coal and partly lignite For normal operation of coal mill, the hardgrove grind ability index is between 40 and 80; the particle size of raw coal is smaller than 40 mm Additional specific technical data for the coal mills are listed in Table 1Dual fault warning method for coal mill based on ScienceDirect