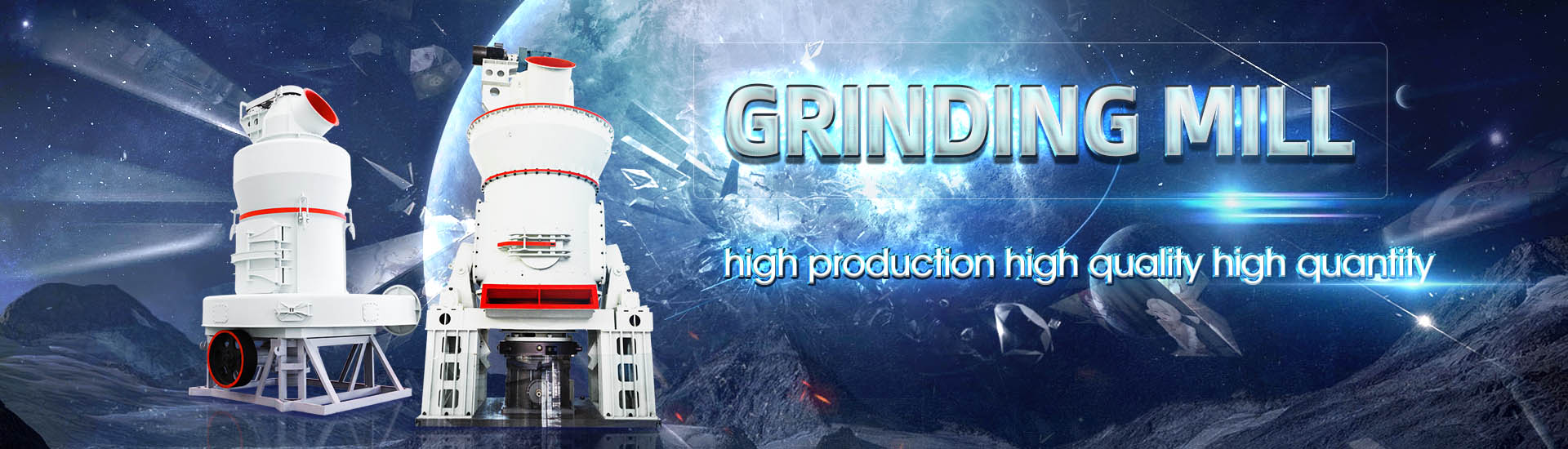
Less clinker cement grinding technology
.jpg)
Alternative Clinker Technologies for Reducing Carbon Emissions in
Cement with high ye’elimite contents (>50% wt) can be used in combination with OPC to produce a fastsetting, rapid hardening cement CSACs cements with less ye’elimite (25–50% wt) 2021年12月28日 The current paper presents a critical review of the existent alternative clinker technologies (ACTs) that are under an investigation trial phase or under restricted use for niche applicationsAlternative Clinker Technologies for Reducing Carbon 2016年1月1日 Amongst these, one of the most popular and effective methods has been to reduce the clinker factor, that is, replace cement clinker with supplementary cementitious Low clinker cement as a sustainable construction material2015年12月1日 A lower clinkertocementratio also results in less energy demand per unit of cement because the energy and CO 2 emissions from the decarbonation of the limestone are Process technology for efficient and sustainable cement production
.jpg)
(PDF) A study of different grinding aids for lowenergy
2023年10月23日 Grinding aids can improve production and fineness and decrease energy consumption by reducing the agglomeration of particles and protecting the balls and liners in the mill In this studyThe polysius ® booster mill is an additional stage grinding solution, particularly efficient for finer grinding Therefore, it enables customer to produce ultrahigh performance cements or sustainable cements with a lower clinker factor polysius® booster mill thyssenkrupp Polysius2019年1月21日 The grinding of clinker combined with around 5% of gypsum (calcium sulphate) forms Portland cement Approximately 50% emissions of CO 2 are directly emitted from the calcination process (decarbonation of limestone), Recent Progress in Green Cement Technology Utilizing 2023年1月7日 Practical and feasible methods were applied to reduce nitrogen oxides, carbon dioxide and particulate matter emissions during the clinker manufacturing process This study Emission reduction through process integration and exploration of

Cement and Concrete Composites ScienceDirect
2024年3月1日 Additionally, the optimization of cement clinker composition is a crucial step toward reducing the environmental impact Cement plants have used new grinding equipment, We also show that nearly all of the highest cement producing nations can locally generate and use secondary CMs to substitute up to 50% domestic Portland cement clinker, with many Cement substitution with secondary materials can reduce annual It is not uncommon to produce the cement in an open circuit Advances in cement grinding technology is slow and these advances are limited to more developed countries Approximately 95% of the feed to the cement grinding circuit are clinker and the rest of the feed are “additives” which includes grinding aids(PDF) Cement grinding optimisation Alex Jankovic2021年12月28日 Currently, the production of one ton of ordinary Portland cement (OPC) releases considerable amounts of CO2 into the atmosphere As the need and demand for this material grows exponentially, it Alternative Clinker Technologies for Reducing
.jpg)
EnergyEfficient Technologies in Cement Grinding
2016年10月5日 In this chapter an introduction of widely applied energyefficient grinding technologies in cement grinding and description of the operating principles of the related equip‐ ments and comparisons over each other in 2024年8月23日 ICR explores the details of the grinding process, which is a critical stage in cement manufacturing, which significantly impacts the final product’s quality and characteristics By finely grinding raw materials into clinker and mixing them with gypsum, cement manufacturers ensure the fineness and uniformity essential for strong and durable cement The grinding From Clinker to Cement Indian Cement Review2024年3月15日 Proper clinker storage is also important to ensure consistent quality for final cement grinding reducing the risk of clinker degradation and ensuring product quality Conventional models may have less effective sealing, clinker silo technology will continue advancing to support the lowcarbon transition of the industrySustainable Cement Storage: The Impact of Clinker Silo Technology2023年8月21日 ICR looks at the inner workings of grinding mills in the cement industry to understand the technological advancements that are reshaping the landscape against the foreground of sustainability Innovations to enhance the grinding processes are aimed at minimising their environmental footprint while increasing efficiency and performance In CuttingEdge Grinding Solutions Indian Cement Review
.jpg)
Cement Technology
When a 5 000 t/d cement clinker production line adopts dry desulfurization technology, there are problems such as the desulfurization effect being greatly affected by kiln operating conditions, the thermal stability of the kiln system being affec ted by water desulfurizers, and the possibility of "sticking bags" in bag dust collectors at the preheaterThe main grinding equipment cement mills grind the clinker to finished cement powders Material – batching – Cement Mill – cement packing – bulk loading In the process, the clinker, gypsum, and additives are ground into particles with a certain fineness that forms a Cement Grinding Units Cement Plant Equipment CNBMSINOMAIt is not uncommon to produce the cement in an open circuit Advances in cement grinding technology is slow and these advances are limited to more developed countries Approximately 95% of the feed to the cement grinding circuit are clinker and the rest of the feed are “additives” which includes grinding aidsCement grinding optimisation Academia2022年11月17日 China has witnessed a construction boom and thus an enormous amount of cement use in the past decades At the same time, cement manufacturing technology has been upgraded rapidly Here, based on Modernizing cement manufacturing in China leads to substantial

Recent Progress in Green Cement Technology
2019年1月21日 Table 3 shows specific thermal consumption in cement clinker process, which is linked to the technology used Using suitable kiln type can reduce energy consumption to less than 29 GJ/ton clinker, while a typical settings and grinding aids In cement technology, fineness, clinker content and strength are in close connection Exact relations can be determined for different local conditions As a first approximation, increasing specific surface according to Blaine by additional 100cm²/g leads to enhanced strength development in the scale ofConcepts for 'Green' cement SikaCondition in one of the grinding chambers of the mill Results of Optimization The graphical analysis presented in Figure 2 represents progress of grinding along the length of the mill after optimizing the grinding process rogress of grinding is clearly visible in Desired p the graphs Figure 2: Analysis of longitudinal samplesOPTIMIZATION OF CEMENT GRINDING OPERATION IN BALL MILLSOnce clinker is produced, it is mixed with gypsum and clinker substitutes which are then ground to the correct fineness to create cement Importantly, there are no further CO 2 emissions at this stage – however, electricity is used for grinding and mixing, and incoming materials as well as final cement products are transported The opportunities in cement manufacturing are Our 2050 Roadmap The 5C Approach: Cement Cembureau
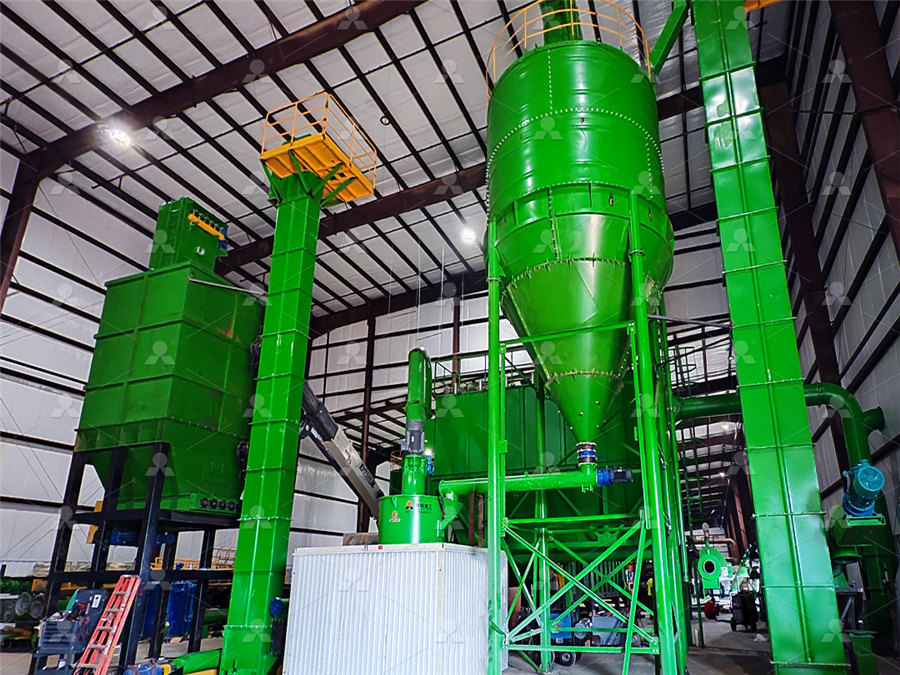
(PDF) A study of different grinding aids for lowenergy cement clinker
2023年10月23日 A feed particle size less than 335 mm was required for the particles of ground cement clinker without grinding aids for the European Cement and Concrete I ndustry Technology assessment Advances in Cement Research, 2009, 21, No 1, Month, 1–8 doi: 101680/adcr20082111 J J Assaad*, S E Asseily* and J Harb FS Use of cement grinding aids to optimise clinker factor Holderchem Building Chemicals SAL, Lebanon; Notre Dame University, Lebanon Introduction OO A comprehensive research project was undertaken to evaluate the effect of grinding aids Use of cement grinding aids to optimise clinker factorThe cement clinker grinding circuit reduces the feed from 80% passing size between 12 and 20 mm to 100% passing 90 microns The conventional size reduction takes place in aCONVENTIONAL CLINKER GRINDING A NEW APPROACH TO 2006年11月1日 Cement production is an energy intensive process Grinding is a highcost operation consuming approximately 60% of the total electrical energy expenditure in a typical cement plant(PDF) Pregrinding technology ResearchGate
.jpg)
Breakthrough in Clinker Grinding Massachusetts Institute of Technology
2012年11月8日 grinding seeks to reduce materials from roughly one meter cubes of blasted stone to a size where at least 80 percent of the raw material is less than 75 microns Finish grinding of clinker and other cement ingredients reduces 25 mm clinker balls to particle sizes optimally ranging from 3 to 30 microns Themore strengths with less clinker CHRYSO offers a full range of Activators, designed to improve cement strengthsThey aim at either increasing strengths at equal cement composition and same cement fineness, or reducing clinker/cement ratio Moreover, CHRYSO® Activators also deliver grinding properties which canAdditives for cement Chryso Group2021年12月28日 Currently, the production of one ton of ordinary Portland cement (OPC) releases considerable amounts of CO2 into the atmosphere As the need and demand for this material grows exponentially, it has become a Alternative Clinker Technologies for Reducing Download Citation On Jan 1, 2023, Vipin Kant Singh published Overview of cement clinker grinding Find, read and cite all the research you need on ResearchGateOverview of cement clinker grinding ResearchGate

Grinding Solutions Indian Cement Review
2015年1月31日 From hubandspoke model to split grinding; from singlegrinding solution to a combination of system solutions; and from energyintensive traditional ball mill to upgraded versions and use of pregrinders, the cement The cement industry is also exploring the potential for development of low CO 2 binders Projects such as Solidia cement, EcoBinder, Celitement, explore the technologies leading to around 30% lower CO 2 emissions in clinker production by using less limestone, a lower clinker burning temperature, and lower grinding energy requirementsCement Cembureau2022年8月10日 Cement grinding station can greatly digest the slag, fly ash, slag, coal gangue and other industrial waste residues near the city, is a green industry Evolution of cement grinding technology A cement mill is the equipment used to grind the hard, nodular clinker from the cement kiln into the fine grey powder that is cementGrinding: Smarter Solutions Indian Cement Review2004年11月1日 The current world consumption of cement is about 15 billion tonnes per annum and it is increasing at about 1% per annum The electrical energy consumed in cement production is approximately 110 kWh/tonne, and around 40% of this energy is consumed for clinker grindingThere is potential to optimise conventional cement clinker grinding circuits and in the Cement grinding optimisation ScienceDirect
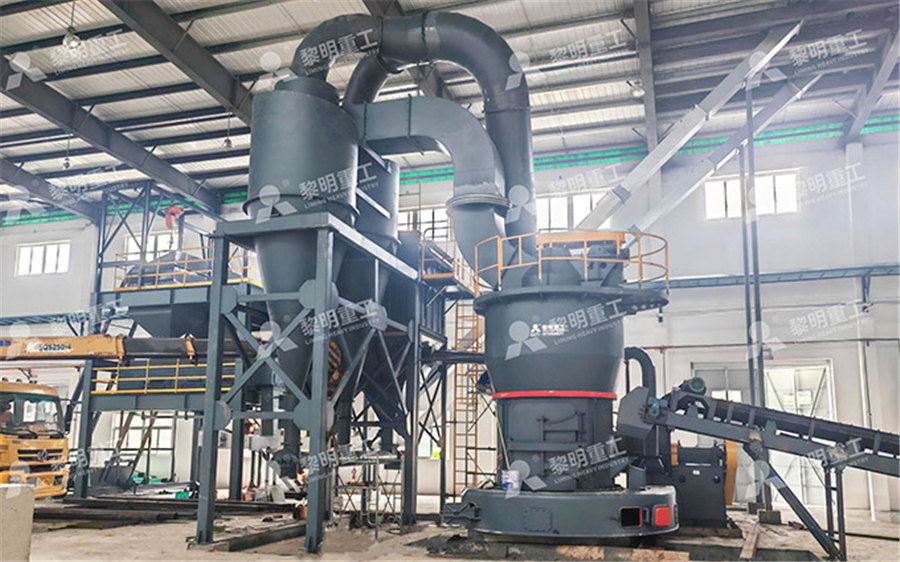
Cement Extraction, Processing, Manufacturing Britannica
2024年11月23日 There are four stages in the manufacture of portland cement: (1) crushing and grinding the raw materials, (2) blending the materials in the correct proportions, (3) burning the prepared mix in a kiln, and (4) grinding the burned product, known as “ clinker,” together with some 5 percent of gypsum (to control the time of set of the cement)2020年7月31日 Grinding processes in cement production technology are quite energyintensive The mechanism of action of surfactants on the course of the clinker grinding process has not been fully studied According to the theory of PA Rebinder, surfactants change the mechanicalInfluence of Clinker Microstructure on Grinding Efficiency in The cement industry processes requiring fine grinding are rawmix preparation, fuel preparation and grinding of clinker to make cement All three may require a preliminary crushing stage In the case of raw materials, attempts have always been made to minimise the amount of crushing needed by extracting the rock in the finest possible stateCement Kilns: Size Reduction and GrindingTable (2) Using less clinker Grinding Aids (GA) with Clinker Producing a composite cement from clinker and pozzolan with added grinding aid can lead to 158 % and 105 % clinker reductions with energy savings of 45 % and 23 %, respectively and without any effects in compressive strength when adding appropriate quantity from grinding Aids [11]`Grinding Aid Effectiveness in Cement Ball Mill Academia
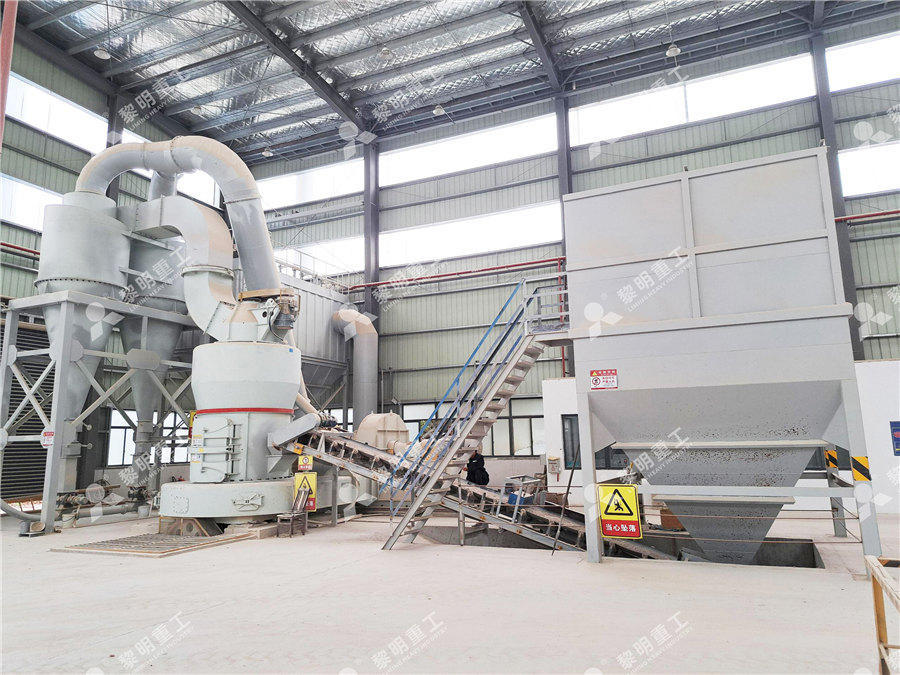
(PDF) Cement grinding optimisation Alex Jankovic
It is not uncommon to produce the cement in an open circuit Advances in cement grinding technology is slow and these advances are limited to more developed countries Approximately 95% of the feed to the cement grinding circuit are clinker and the rest of the feed are “additives” which includes grinding aids2021年12月28日 Currently, the production of one ton of ordinary Portland cement (OPC) releases considerable amounts of CO2 into the atmosphere As the need and demand for this material grows exponentially, it Alternative Clinker Technologies for Reducing 2016年10月5日 In this chapter an introduction of widely applied energyefficient grinding technologies in cement grinding and description of the operating principles of the related equip‐ ments and comparisons over each other in EnergyEfficient Technologies in Cement Grinding2024年8月23日 ICR explores the details of the grinding process, which is a critical stage in cement manufacturing, which significantly impacts the final product’s quality and characteristics By finely grinding raw materials into clinker and mixing them with gypsum, cement manufacturers ensure the fineness and uniformity essential for strong and durable cement The grinding From Clinker to Cement Indian Cement Review
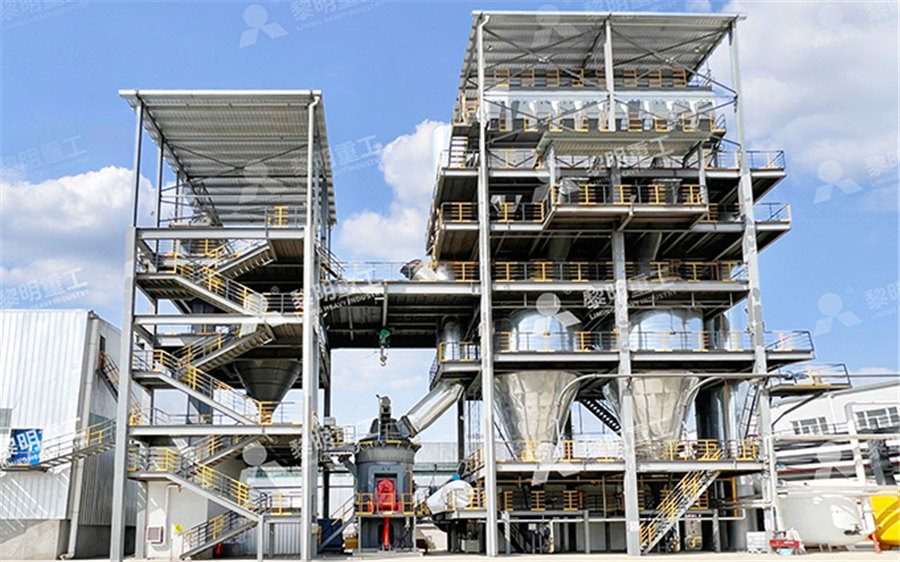
Sustainable Cement Storage: The Impact of Clinker Silo Technology
2024年3月15日 Proper clinker storage is also important to ensure consistent quality for final cement grinding reducing the risk of clinker degradation and ensuring product quality Conventional models may have less effective sealing, clinker silo technology will continue advancing to support the lowcarbon transition of the industry2023年8月21日 ICR looks at the inner workings of grinding mills in the cement industry to understand the technological advancements that are reshaping the landscape against the foreground of sustainability Innovations to enhance the grinding processes are aimed at minimising their environmental footprint while increasing efficiency and performance In CuttingEdge Grinding Solutions Indian Cement ReviewWhen a 5 000 t/d cement clinker production line adopts dry desulfurization technology, there are problems such as the desulfurization effect being greatly affected by kiln operating conditions, the thermal stability of the kiln system being affec ted by water desulfurizers, and the possibility of "sticking bags" in bag dust collectors at the preheaterCement TechnologyThe main grinding equipment cement mills grind the clinker to finished cement powders Material – batching – Cement Mill – cement packing – bulk loading In the process, the clinker, gypsum, and additives are ground into particles with a certain fineness that forms a Cement Grinding Units Cement Plant Equipment CNBMSINOMA
.jpg)
Cement grinding optimisation Academia
It is not uncommon to produce the cement in an open circuit Advances in cement grinding technology is slow and these advances are limited to more developed countries Approximately 95% of the feed to the cement grinding circuit are clinker and the rest of the feed are “additives” which includes grinding aids2022年11月17日 China has witnessed a construction boom and thus an enormous amount of cement use in the past decades At the same time, cement manufacturing technology has been upgraded rapidly Here, based on Modernizing cement manufacturing in China leads to substantial