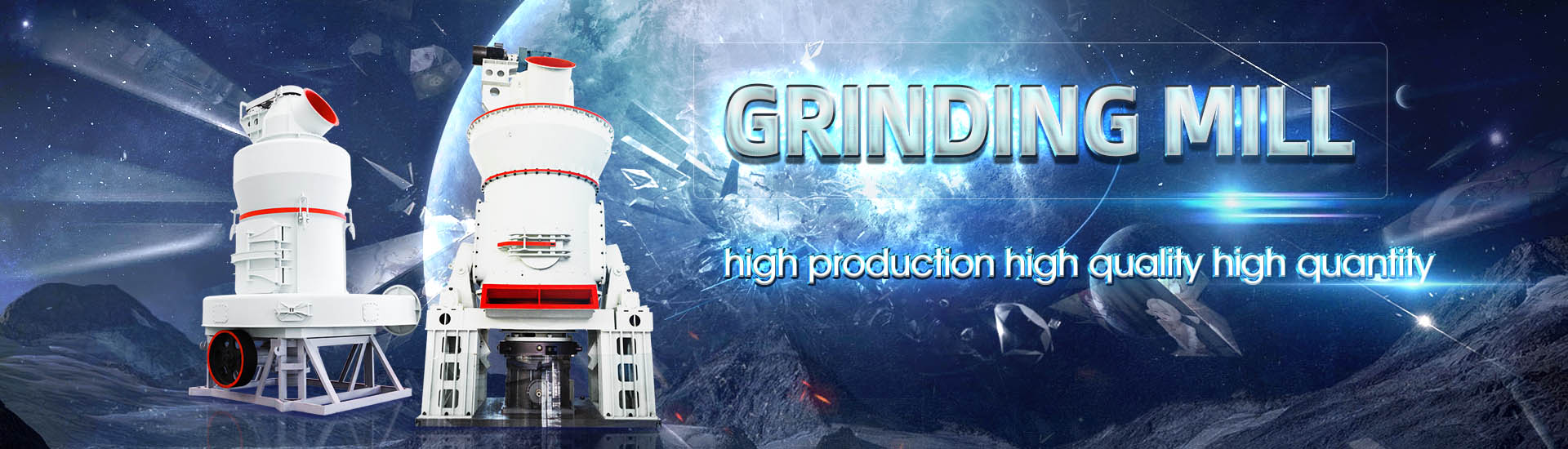
Method of grinding polymer materials into fine particles
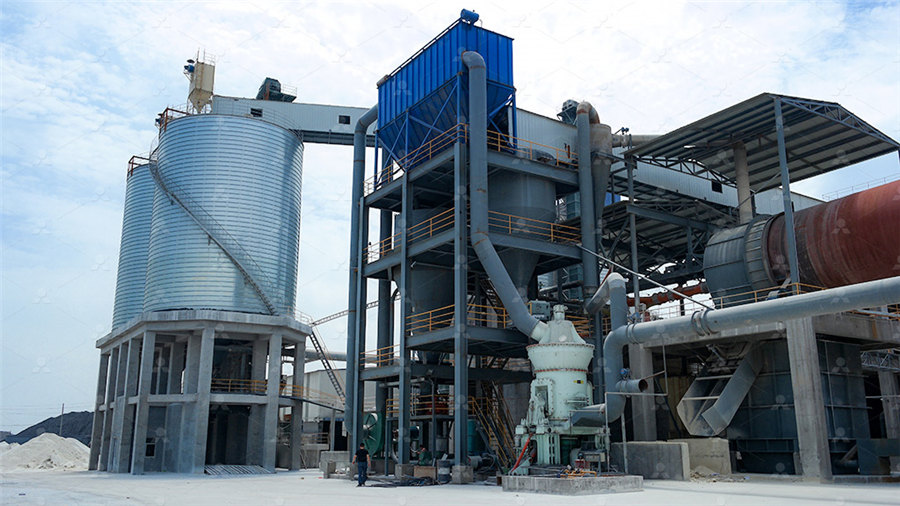
Producing Fine Particles for Multiple Applications AZoM
With the increase in demand for higher performance plastics, the industry has been searching for more efficient, hightech grinding solutions that can produce even finer polymer particles that are distributed more evenly All this needs to be achieved whilst also maximising throughputs For example, the food packaging 展开Ball milling is a mechanical technique widely used to grind powders into fine particles and blend materials18 Being an environmentallyfriendly, costeffective technique, it has found wide application in industry all over the worldBall milling: a green technology for the preparation and 2015年7月1日 Milling involves the application of mechanical energy to physically break down coarse particles to finer ones and is regarded as a “top–down” approach in the production of Overview of milling techniques for improving the solubility of 2012年9月1日 It is shown that wet grinding of polymers in a stirred media mill and organic solvents (ethanol, hexane) at reduced temperatures down to − 80 °C is a suitable method to Production of polymer particles below 5 μm by wet grinding
.jpg)
Effect of grinding aids and process parameters on dry fine
2021年7月1日 CO(NH 2) 2 was the optimal milling aid for the fine grinding of PTFE based on comprehensive consideration of the particle size of the prepared sample and safe production 2023年7月10日 The present literature review explores the energyefficient ultrafine grinding of particles using stirred mills The review provides an overview of the different techniques for size reduction and the impact of energy EnergyEfficient Advanced Ultrafine Grinding of 2024年4月3日 Deposition methods such as CVD and ALD all present highly efficient operations in fluidized beds for the fabrication of functional fine particle materials, specifically functional nanoparticles such as CNTsA review on applications of fine particles integrated Hosokawa’s attrition plates are uniquely engineered to finely grind heat sensitive materials, and in many cases, without cooling gas or liquid nitrogen The serrated teeth of the rotating and FINE GRINDING OF POLYMERIC HEAT SENSITIVE MATERIALS
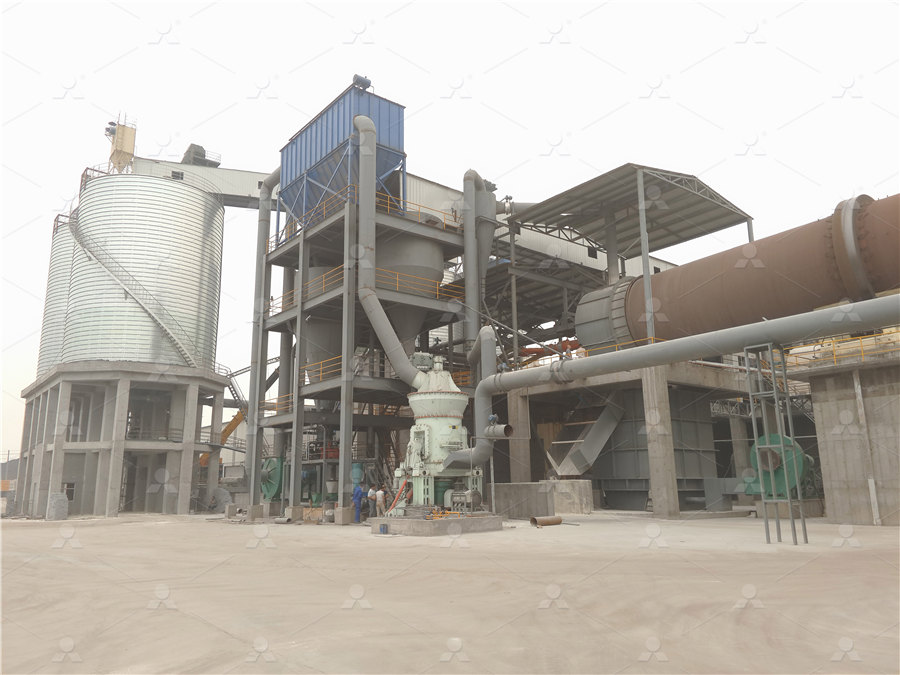
Production of Polymer Particles Below 5 μm by Wet Grinding
2012年5月7日 It is shown that wet grinding of polymers in a stirred media mill and organic solvents (ethanol, hexane) at reduced temperatures down to − 80 °C is a suitable method to 2023年6月29日 Shear force is in favor of exfoliating layered compounds, and impact force can efficiently grind the powders into fine particles As for highenergy ball milling, the heat generated by friction can be used to induce the Facile Ball Milling Preparation of FlameRetardant Production of polymer particles below 5μm by wet grinding × Close Log In Log in with Materials and methods 21 Materials Polystyrene (PS) (Carl Roth) of a particle size fraction of 250 07 mm, 125 mm and 20 mm, respectively, have been used Approximately 1500 g of grinding beads have been introduced into the grinding Production of polymer particles below 5μm by wet grinding2024年4月3日 As discussed, the awareness of grinding raw materials into fine particulates to achieve desired performance came remarkably early in human civilization, but the specific usage of particles within a comparably uniform A review on applications of fine particles integrated
.jpg)
Nanoparticle and Nanostructure Synthesis and
2022年9月16日 Nanomaterials are materials with one or more nanoscale dimensions (internal or external) (ie, 1 to 100 nm) The nanomaterial shape, size, porosity, surface chemistry, and composition are controlled at the It has been discovered that by using very fine particle size grinding media beads, in the range of 70125 microns, grinding materials into the nanometer range is economically feasible Or for dispersing nanometer sized particles using beads even as fine as 3050 microns shows a significant improvement in process efficiencyEffectively Grinding and Dispersing Nanoparticles Using a Fine 2023年7月10日 The present literature review explores the energyefficient ultrafine grinding of particles using stirred mills The review provides an overview of the different techniques for size reduction and the impact of energy requirements on the choice of stirred mills It also discusses the factors, including the design, operating parameters, and feed material properties, EnergyEfficient Advanced Ultrafine Grinding of Particles UsingWhen plane grinding, abrasive particles can become embedded in soft materials Continue with a somewhat finer grit surface (ie MD/DPPan with DiaPro Pan 15 um) as a second plane grinding step and MDLargo for fine grinding Embedded particles should Metallographic grinding and polishing insight Struers
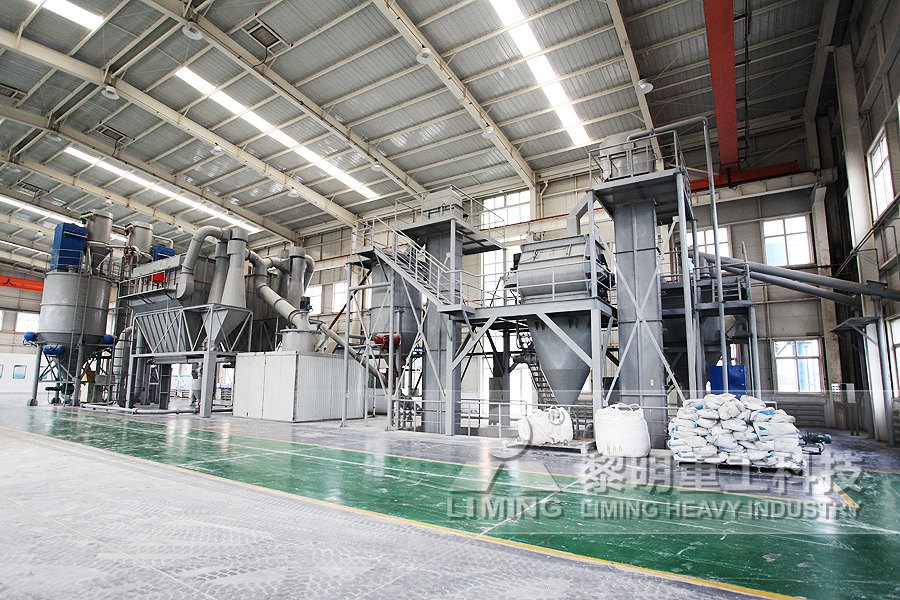
Nanomaterials: Synthesis and Applications in Theranostics
They are topdown and bottomup approaches In topdown approaches, the bulk materials are mechanically machined and converted into fine particles in nano dimensions In bottomup approaches, the fine particles are assembled to build the nanomaterials through selfassembly or coprecipitation methods 212012年9月1日 Polymeric microparticles that may be used in rapid prototyping processes typically are produced by either polymerization processes or cryogenic grinding in impact mills at liquid nitrogen temperature (− 196 °C) or by dry grinding at solid carbon dioxide temperature (− 78 °C) Within this account an alternative approach for the production of polymer particles is Production of polymer particles below 5 μm by wet grindingBall milling is a mechanical technique widely used to grind powders into fine particles and blend materials 18 Being an environmentally carefully monitored to avoid excessive grinding of the raw materials the Microstructure and Rheological Properties of Microcrystalline Cellulose as a Sustainable Polymer Additive, Materials, Ball milling: a green technology for the preparation and 2004年12月1日 7 For example, cryogenic (at 40 to 195 C) high energy grinding systems have been design that are capable of converting elastic materials like tire rubber and plastics into particles that pass Optimised technologies for cryogenic grinding Request PDF
.jpg)
Effectively Grinding And Dispersing Nanoparticles Using A Fine
economically grind materials into the nanometer range It has also been discovered that unique mill designs using ultra fine grinding beads 3050 m in size offer an effective solution for dispersing these particles with significantly improved process efficiency2022年5月20日 Particlesize reduction is a result of particle–particle and particle–wall collisions upon feeding of solids into the air stream (Fig 46) Normally, gas velocities are such that a sonic flow is achieved, and only particles that reach a predetermined particle size will be able to leave the vortex through the exitMechanical ParticleSize Reduction Techniques SpringerLinktwo particles Shear refers to cutting of particles resulting in fracture The particles are broken into fine particles by squeezing action in compression force type Main objective of milling: Particle size reduction (main purpose), Particle size growth, shape change, agglomeration (joining of particles together), solid state alloying,Powder metallurgy – basics applications IIT GuwahatiIntroduction to Supercritical Fluids Richard Smith, Cor Peters, in Supercritical Fluid Science and Technology, 2013 413 Particle Formation Fine particles are needed in many technological fields [PF1]In pharmaceutical fields, fine particles are used into tablets and capsules to provide reliable and stabilized drug delivery drug formulation processesFine Particle an overview ScienceDirect Topics
.jpg)
Nanomaterials: a review of synthesis methods, properties, recent
Hydrothermal and solvothermal methods are generally carried out in closed systems 66 The microwaveassisted hydrothermal method has recently received significant attention for engineering nanomaterials, combining the merits of both hydrothermal and microwave methods 67 Hydrothermal and solvothermal methods are exciting and useful methods for producing 2019年10月31日 The particle is broken up into several pieces, and this process continues until the particle gradually turns into fine particles Volume grinding is dominant in compression pulverization and impact pulverization(*3)(*4)。 Mechanism of pulverization The external force applied to particles can be roughly divided into four types, “compression Pulverization 1: Definition and purpose THINKY MIXER2017年3月4日 In materials processing, a grinder is a m achine for producing fine particle size reduction through attrition and compressive forces at the g rain size level In general, grinding processes requ ire aSIZE REDUCTION BY GRINDING METHODS ResearchGateof grinding polymer waste is several times higher than for most brittle mineral materials Cutting and impact equipment is often used to shred plastic waste To obtain micronsized polymer particles, the technologies of cryogenic grinding and wet grinding in solvents are used, which is followed by high operating costsShredding of polyethylene terephthalate waste e3s
.jpg)
Shredding of polyethylene terephthalate waste ResearchGate
2021年1月1日 [Show full abstract] demonstrate that wet grinding of polymers is a feasible approach for production of fine polymer particles that eg may be used as a starting material in a process chain for 2013年9月9日 Size reduction is a process of reducing large solid unit masses into small unit masses, coarse particles or fine particles Size reduction process is also termed as Comminution or Diminution or METHODS OF SIZE REDUCTION AND FACTORS AFFECTING SIZE 2002年4月1日 In order to produce fine polymer powders, a special and unconventional cryogenic grinding system was established using liquid nitrogen, where a jetvortex mill was used as the grinding millProduction of Fine Polymer Powder under Cryogenic Conditions Abstract Triboelectrostatic separation is a technology which allows the separation of polymer materials based on their surface charging characteristics As plastic waste is collected in various large sizes, it is necessary to control the particle size using crushing and shredding units to bring the particles into a proper size before theyInfluence of Particle Size after Grinding in Electrostatic IJEEES
.jpg)
Damaging effect of fine grinding treatment on the microstructure
In this study, the sprayinggrindingfine grinding method was used to prepare PUA materials into particles and powder materials of different sizes The particle size composition and characteristics of PUA materials after fine grinding were studied and analyzed2024年6月17日 The benefits of cryogenic size reduction are numerous: Prevents caking: Cryogenic feeds safeguard temperaturesensitive materials against thermal deteriorationThis process eliminates the risk of product caking in the mill Creates ultrafine particular grinding: Compared to traditional milling methods, cryomilling produces finer ground particlesBenefits of Cryogenic Grinding Pulva2023年1月27日 Recycling Today Magazine Hosokawa Micron Group “Ask the Experts” – Fine Grinding of Plastics July Issue focusing on Plastics Recycling Five questions and answers about fine grinding of plastics, totaling 400450 words What limitations does the plastic industry face when it comes to size reduction and fine grinding of polymers? The manufacture of polymer Ask the Expert: 5 Questions about Fine Grinding of Plastics2023年9月4日 Surface analysis FTIR Fouriertransform infrared (FTIR) spectroscopy was used to verify polymer chemistry before and after the cryomilling process using a Bruker VERTEX 70v FTIR Spectrometer with a platinum diamond attenuated total reflectance (ATR) crystal in the wavenumber range from 4000 cm −1 to 400 cm −1Data was collected at a spectral resolution An assessment of methods used for the generation and
.jpg)
Machine Learning in the Analysis of the Mechanical Shredding
2024年6月28日 Artificial intelligence methods and techniques creatively support the processes of developing and improving methods for selecting shredders for the processing of polymer materials This allows to optimize the fulfillment of selection criteria, which may include not only indicators related to shredding efficiency and recyclate quality but also energy consumption 2017年12月15日 Request PDF Production of PBT/PC particle systems by wet grinding Comminution of plastic or viscoelastic materials is known to be energyintensive and costly Typically impact mills, cutting Production of PBT/PC particle systems by wet grinding2018年6月1日 In this review, fine grinding is considered as the size reduction where the product mass median particle size is below 500 μm, which also means that virtually all particles are less than 1 mm 500 μm is a practical limit in dry grinding that is difficult or even impossible to achieve with moist wood because size reduction will be limited by the agglomeration of particles, Fine grinding of wood – Overview from wood breakage to 2021年7月1日 Highenergy ballmilling techniques, also called mechanochemical processes, have been widely used in nanomaterial synthesis, nanoparticle preparation, organic matter degradation, et cetera [[10], [11], [12]]Strong shear, friction, and extrusion forces act on the raw materials during the ballmilling process, thereby reducing the particle size and inducing Effect of grinding aids and process parameters on dry fine grinding
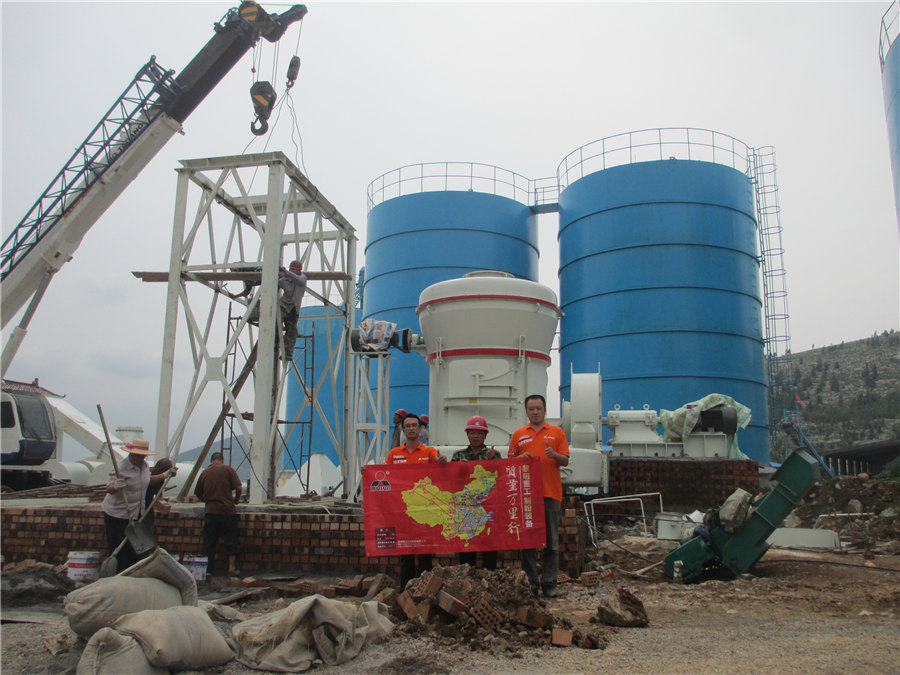
Production of polymer particles below 5μm by wet grinding
Production of polymer particles below 5μm by wet grinding × Close Log In Log in with Materials and methods 21 Materials Polystyrene (PS) (Carl Roth) of a particle size fraction of 250 07 mm, 125 mm and 20 mm, respectively, have been used Approximately 1500 g of grinding beads have been introduced into the grinding 2024年4月3日 As discussed, the awareness of grinding raw materials into fine particulates to achieve desired performance came remarkably early in human civilization, but the specific usage of particles within a comparably uniform A review on applications of fine particles integrated 2022年9月16日 Nanomaterials are materials with one or more nanoscale dimensions (internal or external) (ie, 1 to 100 nm) The nanomaterial shape, size, porosity, surface chemistry, and composition are controlled at the Nanoparticle and Nanostructure Synthesis and It has been discovered that by using very fine particle size grinding media beads, in the range of 70125 microns, grinding materials into the nanometer range is economically feasible Or for dispersing nanometer sized particles using beads even as fine as 3050 microns shows a significant improvement in process efficiencyEffectively Grinding and Dispersing Nanoparticles Using a Fine
.jpg)
EnergyEfficient Advanced Ultrafine Grinding of Particles Using
2023年7月10日 The present literature review explores the energyefficient ultrafine grinding of particles using stirred mills The review provides an overview of the different techniques for size reduction and the impact of energy requirements on the choice of stirred mills It also discusses the factors, including the design, operating parameters, and feed material properties, When plane grinding, abrasive particles can become embedded in soft materials Continue with a somewhat finer grit surface (ie MD/DPPan with DiaPro Pan 15 um) as a second plane grinding step and MDLargo for fine grinding Embedded particles should Metallographic grinding and polishing insight StruersThey are topdown and bottomup approaches In topdown approaches, the bulk materials are mechanically machined and converted into fine particles in nano dimensions In bottomup approaches, the fine particles are assembled to build the nanomaterials through selfassembly or coprecipitation methods 21Nanomaterials: Synthesis and Applications in Theranostics2012年9月1日 Polymeric microparticles that may be used in rapid prototyping processes typically are produced by either polymerization processes or cryogenic grinding in impact mills at liquid nitrogen temperature (− 196 °C) or by dry grinding at solid carbon dioxide temperature (− 78 °C) Within this account an alternative approach for the production of polymer particles is Production of polymer particles below 5 μm by wet grinding
.jpg)
Ball milling: a green technology for the preparation and
Ball milling is a mechanical technique widely used to grind powders into fine particles and blend materials 18 Being an environmentally carefully monitored to avoid excessive grinding of the raw materials the Microstructure and Rheological Properties of Microcrystalline Cellulose as a Sustainable Polymer Additive, Materials, 2004年12月1日 7 For example, cryogenic (at 40 to 195 C) high energy grinding systems have been design that are capable of converting elastic materials like tire rubber and plastics into particles that pass Optimised technologies for cryogenic grinding Request PDF