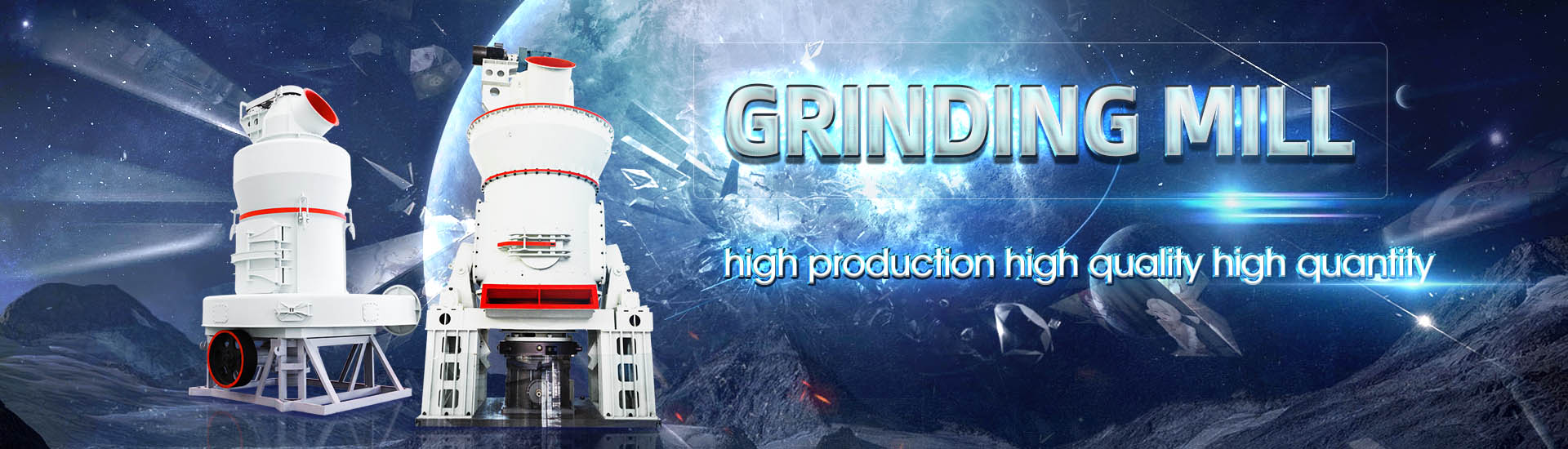
Processing process of refined iron oxide
.jpg)
Iron Ore Processing: From Extraction to Manufacturing
2024年4月26日 Iron ore, a naturally occurring mineral composed primarily of iron oxides, is mined and processed to extract iron for various industrial applications This article provides a comprehensive overview of the iron ore The primary objective of iron making is to release iron from chemical combination with oxygen, and, since the blast furnace is much the most efficient process, it receives the most attention here Alternative methods known as direct Iron processing Smelting, Refining, Alloying Britannica2019年3月15日 In the paper are shown the history, processing and applications of hematite Hematite is an oxide of iron having the composition Fe2O3 Pure hematite, also called “red ore” contains 70% Fe(PDF) Hematite Processing and Applications2024年1月1日 Ironmaking is the process of refining iron oxides in iron ores into metallic iron The earth’s crust is rich in iron, accounting for 42% of the total elements, ranking fourth With no Ironmaking SpringerLink
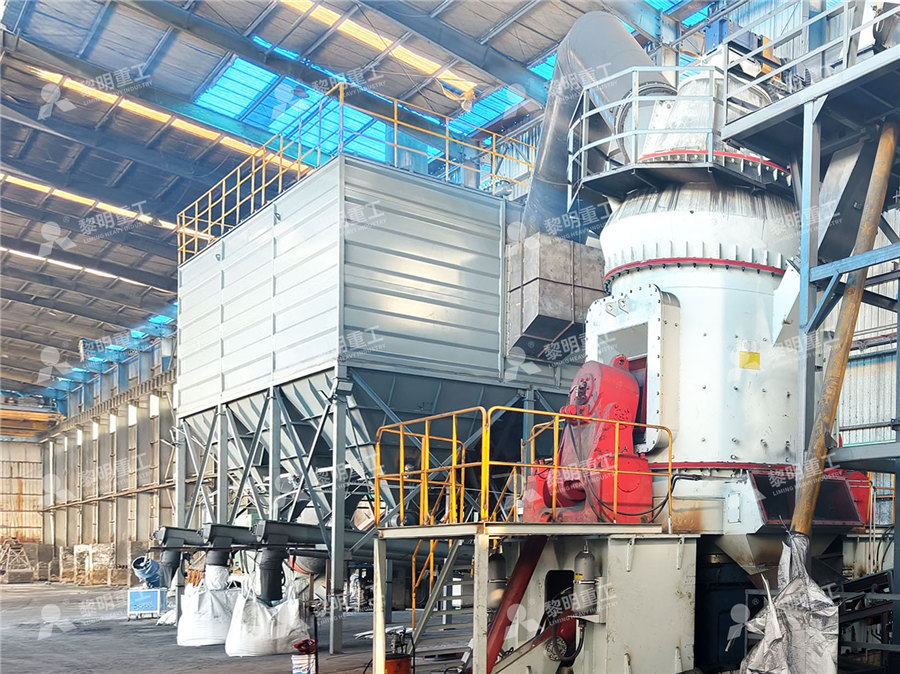
Iron processing Ores, Smelting, Refining Britannica
Iron processing Ores, Smelting, Refining: Iron ores occur in igneous, metamorphic (transformed), or sedimentary rocks in a variety of geologic environments Most are sedimentary, but many have been changed by 2022年8月23日 This study gave an overview of the reductionsmelting process as a third generational alternative for the modernday iron and steelmaking process whose hallmark is to mitigate the(PDF) An Overview of the ReductionSmelting Process In the following a new method for producing fine iron powders from iron oxide as byproduct of refined pickling slurries from steel makers as well as the relationship between the modification New Processing Route for Production of Fine Spherical Iron PowderThe four horizontal rotary kilns are the heart of the reduction process The residual char (carbon) remaining after the coal was heated is used to achieve the chemical reduction of iron oxide to iron A number of chemical reactions occur The Ironmaking Process New Zealand Steel
.jpg)
From Ore to Iron with Smelting and Direct Iron
2017年10月17日 The Hismelt process employs a single smelt reduction vessel (SRV) where iron oxide fines are injected deep into hot metal melt, which instantly reduces the ore to produce iron and carbon monoxide Flux and coal are also num oxide (Al 2 O 3) called alumina In the Western World, the Bayer 1 process, invented in the 19th century, is by far the most important process used in the production of aluminum oxide from bauxite The process has been refined and improved since its inception Fig 22 shows that the production of alumina is a complex chemical process The Chapter 2 Production and Processing of Aluminum The Iron processing Ores, Smelting, Refining: Iron ores occur in igneous, metamorphic (transformed), or sedimentary rocks in a variety of geologic environments Most are sedimentary, but many have been changed by Iron processing Ores, Smelting, Refining BritannicaCobalt processing, preparation of the metal for use in various products Magnetic alloys form the most important use of cobalt The second most important cobalt outlet is in the making of hightemperature alloys, in which it improves the hightemperature strength and corrosion resistanceCobalt processing Uses, Supply, Facts Britannica
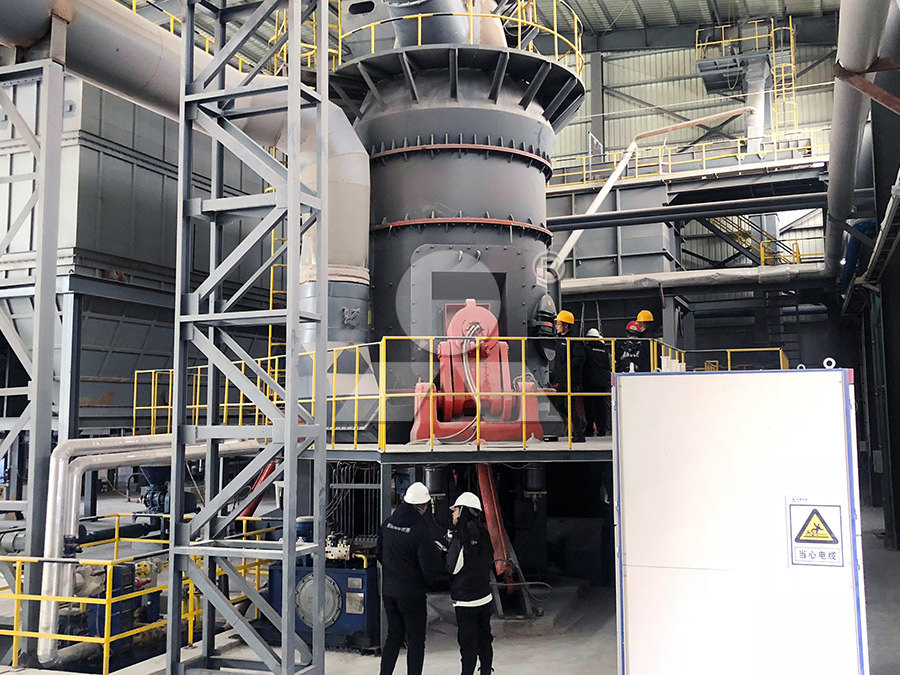
(PDF) i) Direct Reduced Iron: Production ResearchGate
2016年3月30日 In book: Encyclopedia of Iron, Steel, and Their Alloys (pppp 10821108) Chapter: i) Direct Reduced Iron: Production; Publisher: CRC Press, Taylor and Francis Group, New York2024年4月26日 During the extraction process, it is common to encounter a combination of iron oxides, impurities, and gangue minerals The extracted ore undergoes further processing to separate the valuable ironbearing minerals from the impurities and gangue minerals, as described in the subsequent stages of iron ore processingIron Ore Processing: From Extraction to Manufacturing2022年3月21日 Significant academic research and moderate commercial process innovation on rareearth element (REE) processing have been underway for decades The last several years have seen exponential growth in research due to growth in demand of REE that is threatened by supply risks and environmental obstacles The REE industry appears to be at the intersection Processing the ores of rareearth elements MRS Bulletin2024年11月14日 gold processing, preparation of the ore for use in various products For thousands of years the word gold has connoted something of beauty or value These images are derived from two properties of gold, its colour and its chemical stabilityThe colour of gold is due to the electronic structure of the gold atom, which absorbs electromagnetic radiation with Gold processing Refining, Smelting Purifying Britannica
.jpg)
Aluminum processing Ores, Refining, Alloying Britannica
Aluminum processing Ores, Refining, Alloying: Aluminum is the third most abundant element on Earth’s surface Only oxygen and silicon are more common Earth’s crust to a depth of 16 km (10 miles) contains 8 percent aluminum Aluminum has a strong tendency to combine with other common elements and so rarely occurs in nature in the metallic formChromium processing, preparation of the ore for use in various products Chromium (Cr) is a brilliant, hard, refractory metal that melts at 1,857 °C (3,375 °F) and boils at 2,672 °C (4,842 °F) In the pure state it is resistant to ordinary corrosion, resulting in its application as an electroplatedChromium processing Extraction, Uses Applications Britannica2018年12月11日 31 Characterization of Sample Received from Ilmenite Processing The composition of waste iron oxide powder obtained from ilmenite processing was chemically analyzed It contained 63% of iron (constitute ~ 90% Fe 2 O 3) along with some impurities such as Mn (08%), Mg (14%), Al (08%) and traces of Si, Ti, etcThe sample was also characterized Carbothermic Reduction of Iron Oxide Waste Generated During The aluminothermic process can also be carried out in a refractorylined steel pot or watercooled copper crucible A charge of V 2 O 5, iron oxide, and aluminum is ignited with a bariumperoxide fuse or a magnesium ribbon Vanadium metal In the production of pure metal, V 2 O 5 is reduced metallothermically by calcium or aluminumVanadium processing Extraction, Uses Applications Britannica
.jpg)
Titanium processing Technology, Methods, Facts
titanium processing, the extraction of titanium from its ores and the preparation of titanium alloys or compounds for use in various products Titanium (Ti) is a soft, ductile, silvery gray metal with a melting point of 1,675 °C (3,047 °F) Owing to In the following a new method for producing fine iron powders from iron oxide as byproduct of refined pickling slurries from steel makers as well as the relationship between the modification of powder morphology by powder processing and sintering properties will be will introduced 2 Experimental procedure 21 Innovative hydrogen reduction processNew Processing Route for Production of Fine Spherical Iron Powder2016年2月29日 In general, slag from smelting process arises from extraneous materials such as rust and oxides; oxidation of elements in the charge (eg iron, copper, zinc); residues from fuels; fluxes employed in the process (silica, borax, sodium nitrate, sodium carbonate, fluorspar); crucible erosionGold Smelting Refining Process 911Metallurgist2021年3月20日 This work introduces an innovative, sustainable, and scalable synthesis of iron oxides nanoparticles (NPs) in aqueous suspension The method, based on ion exchange process, consists of a onestep procedure, time and energy saving, operating in water and at room temperature, by cheap and renewable reagents The influence of both oxidation state of the New Sustainable, Scalable and OneStep Synthesis of Iron Oxide
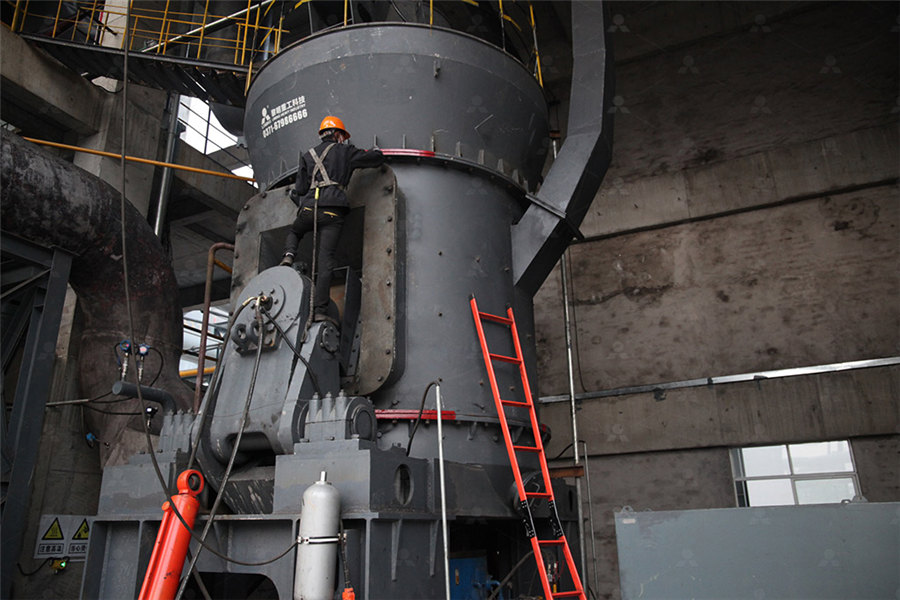
232: Principles of Extractive Metallurgy Chemistry LibreTexts
The separation of the minerals makes processing complex (that is, mixed) ores economically feasible and still the most common smelting process for oxide ores involves heating them in the presence of carbon Originally, What are the applications of pig iron and how might it be refined to make pure iron2020年6月10日 224 Direct Reduction of Iron Oxide by Solid Carbon The direct reduction process of iron oxide by solid carbon is highly endothermic in nature and occurs when the molten slag flows over incandescent coke in the bosh region at a temperature above 1000 °C Therefore, the corresponding reaction can be written as follows:Iron and SteelMaking Process SpringerLink2020年2月1日 Optimization studies were carried out in the production of γFe2O3 nanoparticles by using coprecipitation method Iron (II) chloride and iron (III) chloride were used as precursors which are dissolved in distilled water followed by centrifugation, drying and grinding process in order to obtain dried dark brown precipitated γFe2O3 powderProduction of Iron Oxide Nanoparticles by CoPrecipitation Following the leaching of oxide ores, copper and cobalt are separated using solvent extraction, and a number of impurities, such as iron, zinc, manganese, etc, are removed prior to cobalt Overview of the main processing routes for cobalt extraction as
.jpg)
Magnesium processing Techniques Methods Britannica
magnesium processing, preparation of magnesium ore for use in various products Magnesium (Mg) is a silvery white metal that is similar in appearance to aluminum but weighs onethird less With a density of only 1738 grams per cubic centimetre, it is the lightest structural metal known It has a hexagonal closepacked (hcp) crystalline structure, so that, like most metals of this 2019年8月1日 Life cycle assessment is a valuable tool that is used to conduct the environmental impact assessment of different metal extraction processes Life cycle assessment assesses impacts on the environment, human health, land, water, and soil during mining and other similar processes, as visible in some previous studies (Mahmud, Huda, Farjana, Lang, 2018a, 2018b)Life cycle assessment of cobalt extraction process2021年12月1日 Vanadium products include three grades, vanadium slag and other vanadium extraction raw materials are primary vanadium products, vanadium oxides such as V 2 O 3, V 2 O 5 are secondary vanadium products, and alloys such as Fe V, Al V and metallic vanadium are tertiary vanadium products [20]At present, there have been many research and review papers A critical review on extraction and refining of vanadium metalzinc processing, the extraction of zinc from its ores and the preparation of zinc metal or chemical compounds for use in various products Zinc (Zn) is a metallic element of hexagonal closepacked (hcp) crystal structure and a density of Zinc processing Extraction, Refining Uses Britannica
.jpg)
Processing of iron oxide nanoparticles by supercritical fluids
2008年1月1日 Finally, potential applications of supercritical fluid technology for the processing of iron oxide nanoparticles are presented workers and is known as RTDS 38,39,42,43 In this process, an ironBetween 30 and 40% of technical Mo oxide production is further processed into ferromolybdenum (FeMo) The oxide is mixed with iron oxide and reduced by aluminum in a thermite reaction, producing a ferromolybdenum ingot weighing several hundred kilograms The product contains between 60 and 75% molybdenum, and the balance is essentially ironMolybdenum Processing2024年8月7日 The two main processing methods for laterite ores are smelting and HighPressure Acid Leaching (HPAL) Smelting is used primarily on saprolite ores to obtain an ironnickel alloy (ferronickel – FeNi, Nickel Pig Iron – NPI) while HPAL is used primarily to process limonite or for higherpurity end productsNickel industry Part 2 Processing nickel laterites and smeltingaluminum processing, preparation of the ore for use in various products Aluminum, or aluminium (Al), is a silvery white metal with a melting point of 660 °C (1,220 °F) and a density of 27 grams per cubic cm The most abundant metallic element, it constitutes 81 percent of Earth’s crust In nature it occurs chemically combined with oxygen and other elementsAluminum processing History, Mining, Refining, Facts
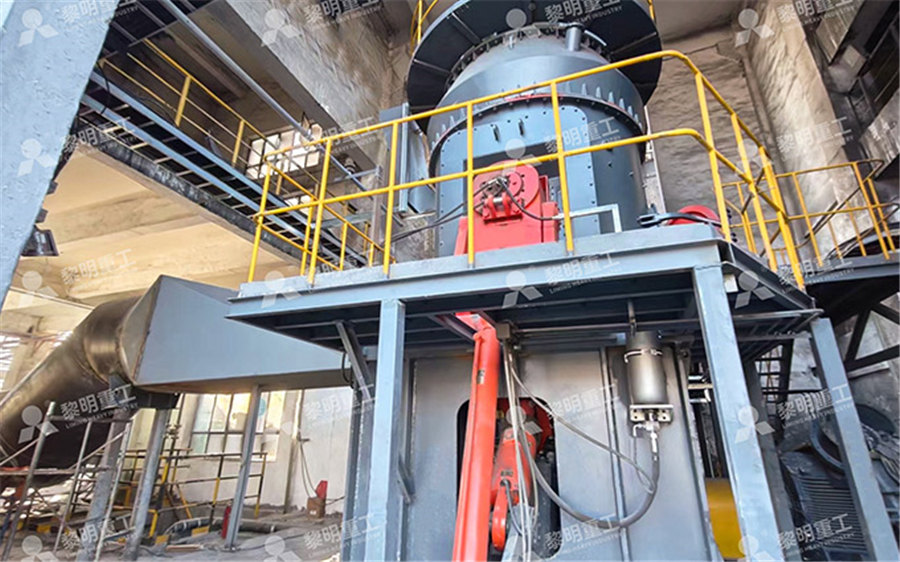
The Ironmaking Process New Zealand Steel
The four horizontal rotary kilns are the heart of the reduction process The residual char (carbon) remaining after the coal was heated is used to achieve the chemical reduction of iron oxide to iron A number of chemical reactions occur in the kilns because coal and ironsand are not pure substances like laboratory chemicalsResource Recovery and Recycling from Metallurgical Wastes S Ramachandra Rao, in Waste Management Series, 2006 98 Production of Ceramic Tiles from Iron Ore Tailings Current practice of washing iron ore before it is processed for extractive metallurgical operation results in three products, coarse ore lumps with sizes in the range 1080 mm, which are directly charged Iron Ore Processing an overview ScienceDirect Topics2023年4月5日 Among the reduction methods of iron oxides in ironmaking processes are direct reduction, blast furnace/blast oxygen furnace, and smeltingreduction process Reduction of iron oxide involves the upgrade of iron ore in pellets, lumps, or sintered form under a highly thermalcharged atmosphere in the presence of carbonaceous materials [18, 19 Recent Trends in the Technologies of the Direct Reduction and num oxide (Al 2 O 3) called alumina In the Western World, the Bayer 1 process, invented in the 19th century, is by far the most important process used in the production of aluminum oxide from bauxite The process has been refined and improved since its inception Fig 22 shows that the production of alumina is a complex chemical process The Chapter 2 Production and Processing of Aluminum The
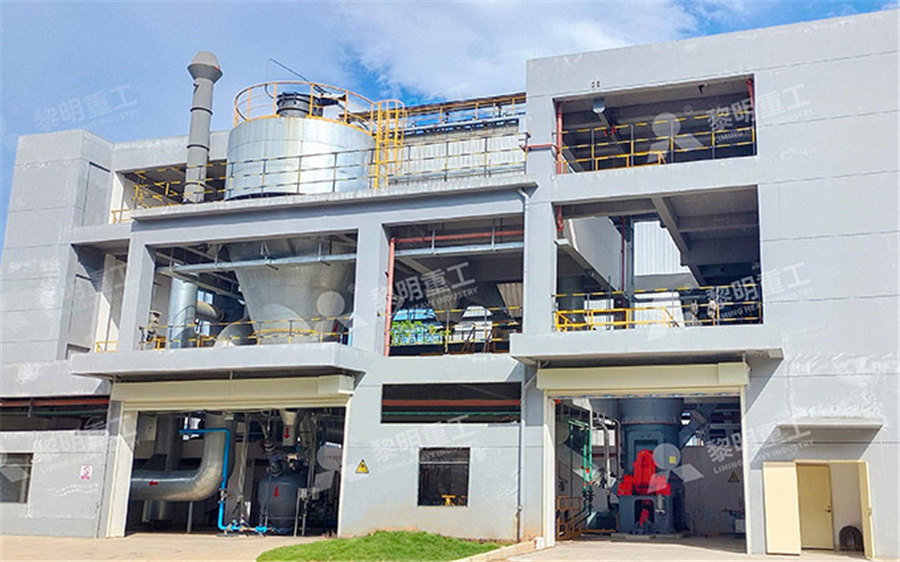
Iron processing Ores, Smelting, Refining Britannica
Iron processing Ores, Smelting, Refining: Iron ores occur in igneous, metamorphic (transformed), or sedimentary rocks in a variety of geologic environments Most are sedimentary, but many have been changed by Cobalt processing, preparation of the metal for use in various products Magnetic alloys form the most important use of cobalt The second most important cobalt outlet is in the making of hightemperature alloys, in which it improves the hightemperature strength and corrosion resistanceCobalt processing Uses, Supply, Facts Britannica2016年3月30日 In book: Encyclopedia of Iron, Steel, and Their Alloys (pppp 10821108) Chapter: i) Direct Reduced Iron: Production; Publisher: CRC Press, Taylor and Francis Group, New York(PDF) i) Direct Reduced Iron: Production ResearchGate2024年4月26日 During the extraction process, it is common to encounter a combination of iron oxides, impurities, and gangue minerals The extracted ore undergoes further processing to separate the valuable ironbearing minerals from the impurities and gangue minerals, as described in the subsequent stages of iron ore processingIron Ore Processing: From Extraction to Manufacturing
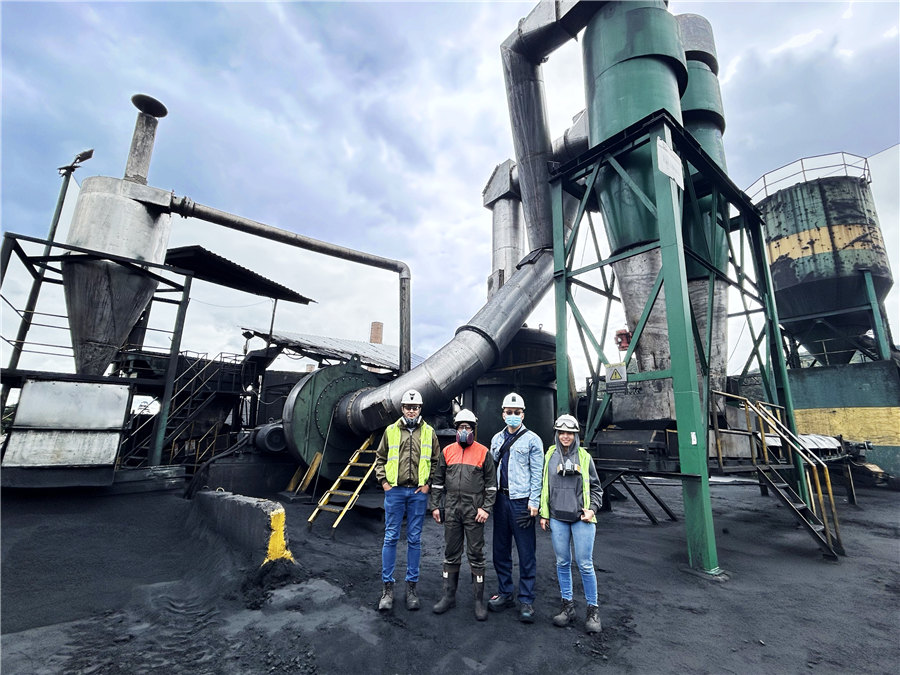
Processing the ores of rareearth elements MRS Bulletin
2022年3月21日 Significant academic research and moderate commercial process innovation on rareearth element (REE) processing have been underway for decades The last several years have seen exponential growth in research due to growth in demand of REE that is threatened by supply risks and environmental obstacles The REE industry appears to be at the intersection 2024年11月14日 gold processing, preparation of the ore for use in various products For thousands of years the word gold has connoted something of beauty or value These images are derived from two properties of gold, its colour and its chemical stabilityThe colour of gold is due to the electronic structure of the gold atom, which absorbs electromagnetic radiation with Gold processing Refining, Smelting Purifying BritannicaAluminum processing Ores, Refining, Alloying: Aluminum is the third most abundant element on Earth’s surface Only oxygen and silicon are more common Earth’s crust to a depth of 16 km (10 miles) contains 8 percent aluminum Aluminum has a strong tendency to combine with other common elements and so rarely occurs in nature in the metallic formAluminum processing Ores, Refining, Alloying BritannicaChromium processing, preparation of the ore for use in various products Chromium (Cr) is a brilliant, hard, refractory metal that melts at 1,857 °C (3,375 °F) and boils at 2,672 °C (4,842 °F) In the pure state it is resistant to ordinary corrosion, resulting in its application as an electroplatedChromium processing Extraction, Uses Applications Britannica
.jpg)
Carbothermic Reduction of Iron Oxide Waste Generated During
2018年12月11日 31 Characterization of Sample Received from Ilmenite Processing The composition of waste iron oxide powder obtained from ilmenite processing was chemically analyzed It contained 63% of iron (constitute ~ 90% Fe 2 O 3) along with some impurities such as Mn (08%), Mg (14%), Al (08%) and traces of Si, Ti, etcThe sample was also characterized