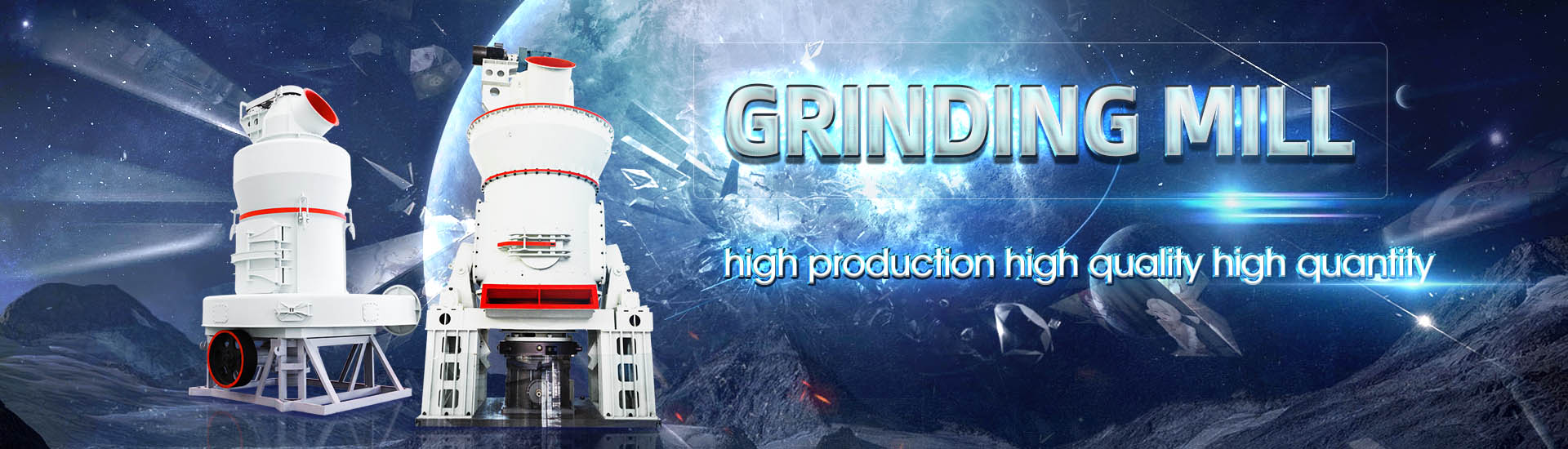
Working principle of raw material mill
.jpg)
Rawmill Wikipedia
A raw mill is the equipment used to grind raw materials into "rawmix" during the manufacture of cement Rawmix is then fed to a cement kiln, which transforms it into clinker, which is then ground to make cement in the cement mill The raw milling stage of the process effectively defines the chemistry (and therefore 展开The tube mill comminutes raw materials by impact and friction between grinding balls, which hit raw materials as well as between grinding ball and mill lining Many of this type mills have two Vertical roller mill for raw Application p rocess materialsIn the cement manufacturing process, raw mill in cement plant grind cement raw materials into the raw mix, and the raw mix is sent to the cement kiln to make cement clinker, next, clinker and other admixtures will be ground into finished Raw mill Cement PlantProviding a comprehensive guide to the entire cement production process from raw material extraction to the finished product, the industry’s favourite technical reference book is now fully The Cement Plant Operations Handbook International Cement
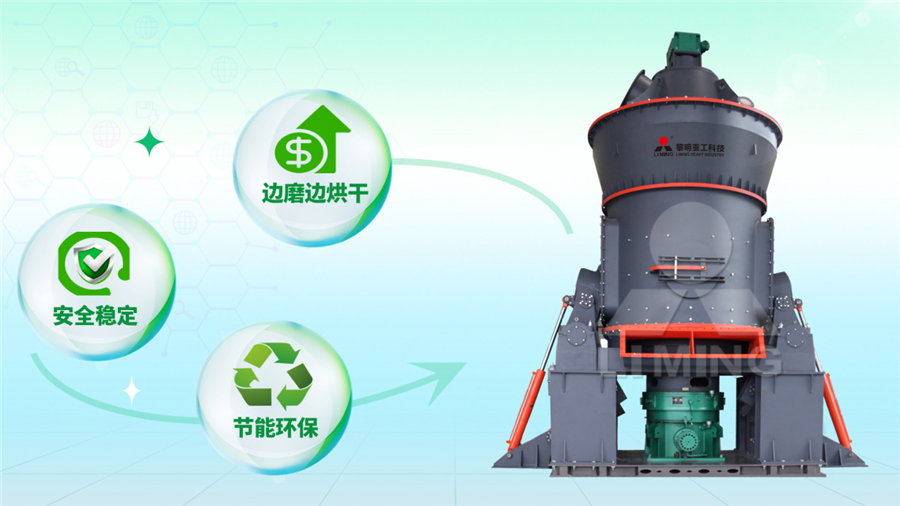
Working principle and characteristics of vertical mill
The working principle of a vertical mill involves the rotation of a grinding table with rollers attached to it Raw materials are fed into the table and ground between the rollers and table The 2023年7月4日 Working principle: the motor drives the grinding table to rotate through the reducer, the material falls into the center of the grinding table from the feed inlet through the Roller Mill SpringerLinkCement is typically made from limestone and clay or shale These raw materials are extracted from the quarry crushed to a very fine powder and then blended in the correct proportions This blended raw material is called the 'raw feed' or Cement manufacturing: components of a cement plant The mill will not run at this time The feed group is stopped when there is sufficient material in the mill The material is then distributed in the mill manually with a shovel When the mill is too full the mill main drive can be overloaded PROCESS TRAINING for operators of Vertical RAW Mills
.jpg)
All about Tube Mill Machine: Components, Working Principle
SS304 Heat Exchanger Industrial Tube Mill Working Principle of Tube Mill Machines: The working principle of an industrial pipe mill involves several stages: 1 Material Feeding: The raw material, usually in the form of a steel coil, is fed into the uncoiler, where it is unwound and continuously fed into the forming section of the machine 2 Principles of Hot Rolling The Art Science Making, Shaping and Treating of Steel: 101 Comparison of Hot Rolling Processes 1 2 11/2/2020 2 Making, Shaping and Treating of Steel: 101 Where does a Hot Strip Mill fit in the flatroll production process? Making, Shaping and Treating of Steel: 101 3 4 11/2/2020 3 HSM Raw Material Steel Slabs Principles of Hot Rolling AISTRaw mill is generally called cement raw mill, raw mill in cement plant, it refers to a common type of cement equipment in the cement plantIn the cement manufacturing process, raw mill in cement plant grind cement raw materials into the raw mix, and the raw mix is sent to the cement kiln to make cement clinker, next, clinker and other admixtures will be ground into finished cement by Raw mill Cement PlantThe vertical works according to the principle of layer material to powder Low energy, the powder consumption of vertical mill is 20%30% less than that of ball mill With the incensement of moisture of the raw material, the powder consumption will decrease obviously The vertical mill saves 30%40% of energy consumption compared to the ball millVertical Cement Mill

(PDF) Design of Threechamber Ball Mill ResearchGate
2021年1月1日 Ball mill is a kind of raw material processing machinery which plays the role of grinding Its working principle is that the movement and force are transmitted to the barrel of ball mill through Application of Vertical Roller Mill in Cement Industry Vertical roller mill (VRM) technology has become an integral part of the cement industry, offering several advantages over traditional grinding mills Today, this type of grinding machine is becoming more and more popular in both the raw material grinding process and the cement grinding Application of Vertical Roller Mill in Cement ProductionWorking Principle of Pin Mill Pin mills or centrifugal impact mills (CIM) function on the principle of impact and are used for of particles They work without the use of external knives, hammers, screens or rolls Construction Working of Pin Mill Weighed quantity of raw material to be milled is fed into the machine through the feeding What is Pin Mill? Working Principle, Construction, Diagram, Vertical raw mill is one kind of raw mill, generally used to grind bulk, granular, and powder raw materials into required cement raw meal in the cement manufacturing plantVertical raw mill is an ideal grinding mill that crushing, drying, grinding, grading transfer set in one It can be widely used in cement, electric power, metallurgy, chemical industry, nonmetallic ore, and other industriesVertical raw mill Cement Plant
.jpg)
Working Principle Of Wood Pellet Mill
2024年7月18日 Working Principle Of Wood Pellet Mill By Published On: July 18, 2024 Categories: Articles 735 words Views: 55 If the wood waste raw material is wet (more than 15%), it needs to be dried After shaping and drying (if necessary), 2024年3月13日 The working principle of the roller mill is mainly divided into two steps: 1 The material first enters the center of the grinding wheel through the feeding hopper, and is then ground into fine powder by the grinding wheel"Working principle and application of roller mill"2024年4月17日 The product to be shared is passed through the inlet which is on top of the mill known as a hopper It is then passed through to the narrow gap between the rotor and stator The rugged edges shear the material into the tiniest particles depending on the rotation speed This mill uses a hydraulic system to shear the material into the final productWorking and Principle of Colloidal Mill PharmaguidelineBrief Introduction The raw material mill is the key equipment for the material to be crushed again after being crushed by the crusher After longterm exploration and summarization in the design and production process, our company has Raw Material MillFote Machinery
.jpg)
What is The Working Principle of Attritor Mill? ball mills supplier
Pharmaceuticals: The attritor mill is used for grinding and dispersing pharmaceutical powders and suspensions, producing fine particles with a narrow size distribution The attritor mill has revolutionized the world of grinding with its unique working principle and many advantages over traditional grinding mills2023年4月29日 The grinding steel ball production line is a process that involves several stages from raw material preparation to finished product packing The working principle of the grinding steel ball production line involves the following steps: Raw material preparation: The raw materials used in the production of grinding steel balls includeThe Working principle of grinding steel ball production lineThe material formed in the kiln is described as 'clinker' and is typically composed of rounded nodules between 1mm and 25mm across After cooling, the clinker may be stored temporarily in a clinker store, or it may pass directly to the cement mill The cement mill Cement manufacturing components of a cement plantA section cutthrough of ball mills A ball mill is a type of grinder filled with grinding balls, used to grind or blend materials for use in mineral dressing processes, paints, pyrotechnics, ceramics, and selective laser sinteringIt works on the principle of impact and attrition: size reduction is done by impact as the balls drop from near the top of the shellBall mill Wikipedia
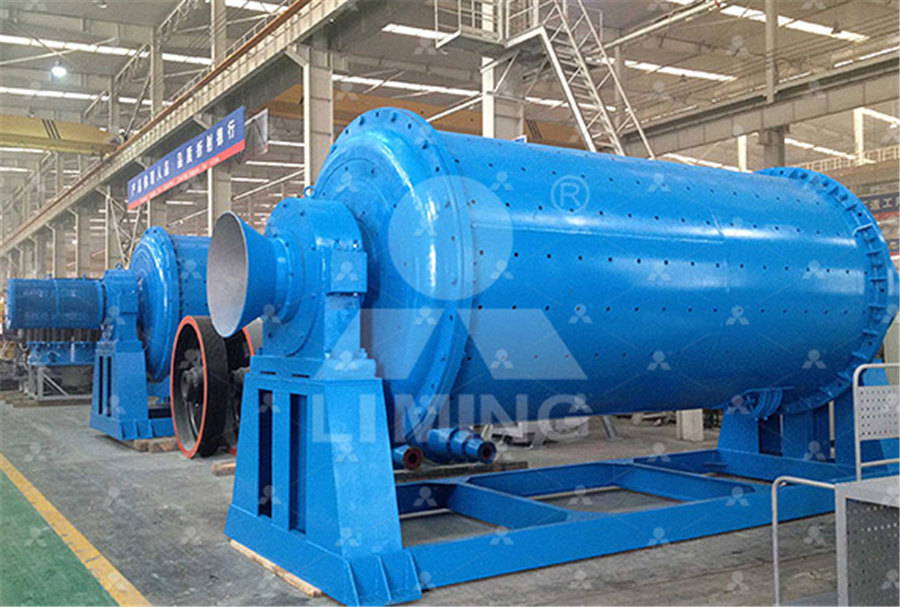
Flat Die Pellet Mill Design Strategies Key to Successful Production
The working principle of flat die pellet mill is very easy to understand, which is to use rolling pressure and friction between the rollers to make the raw materials form a continuous compression, cutting and molding process between the Providing a comprehensive guide to the entire cement production process from raw material extraction to the finished product, – 4 Ball mill circuit control – 5 Cement storage – 6 Cement dispatch – 7 Distribution – 8 Quality assurance and customer service 7 Quality control 134 1 Sampling – 2 Chemical analysis – 3The Cement Plant Operations Handbook International Cement 2024年1月28日 2 Liners: An abrasionresistant material such as manganese steel or rubber typically lines the inner surface of the cylindrical shell to protect it from wear due to the grinding action 3 Balls: They place steel or ceramic balls, typically used as grinding media in a ball mill, inside the shell and rotate them with it 4 Feed and Discharge: Entering the hollow shell at the Ball mill: Principles, construction, working, uses, merits, and finer, depending on the material An air classifier mill applies impact grinding and air classification in one step The mill uses airflow to convey feed material to the mill’s grinding chamber, classifies the material into fine and coarse fractions, recirculates the coarse fraction for further grinding, and conveys fine particles outHow to operate an air classifier mill to meet your fine grinding goals
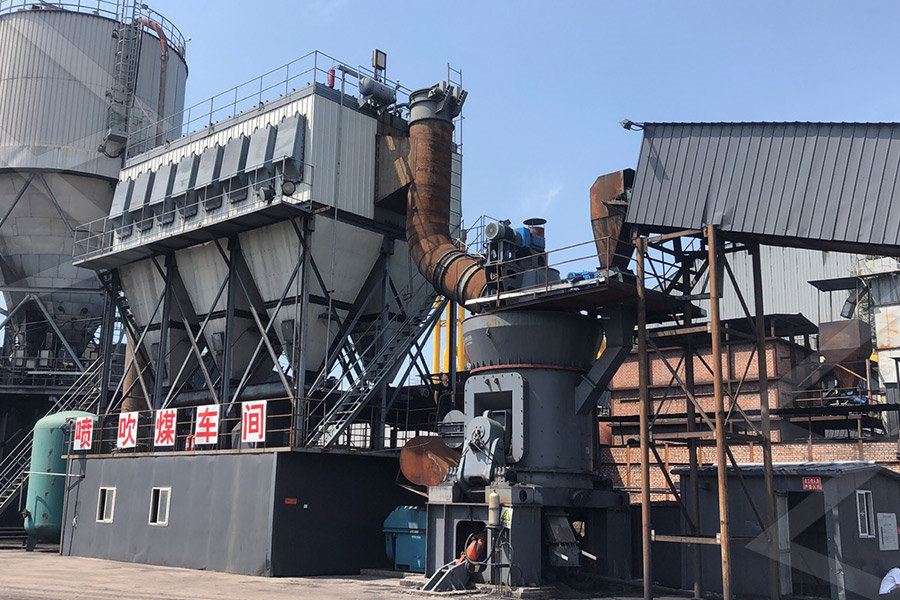
What is the working principle of tube mill? Cncmachiningworks
2023年11月30日 The working principle of a tube mill involves the rotation of a cylinder, often cylindrical steel tubes or shells, containing grinding media, such as balls or rods The material to be ground is loaded into the mill, and as the cylinder rotates, the grinding media collide with the material, resulting in size reduction and mixing2023年7月4日 The Raymond grinding mill, Raymond mill for short, is a roller mill in which the central spindle drives the multiple grinding rollers installed on the plumblossom rack to swing outwardly under the action of centrifugal force and press the grinding ring on the inner wall of the casing to grind the material The Raymond mill is mainly composed Roller Mill SpringerLinkWorking principle of vertical raw mill When the vertical raw material mill in the cement plant starts to run, the material enters the mill through the feed port on the upper side of the mill, and then falls in the center of the millstone The transmission drives the millstone to rotate, Vertical Raw Mill ball mills supplierMultimill working principle By subjecting the raw material to intense mechanical forces, the Multimill effectively reduces particle size, thus facilitating downstream processes and enhancing product uniformity Cone Mill Multimill; Operates on the principle of Multimill In Pharma 2023 » Flair Pharma The Knowledge Kit
.jpg)
Ball Mill Grinding Machines: Working Principle, Types, Parts
Ball Mill, Working Principle, Types, Parts, Applications and Advantages Ball Mill Grinding Machines: Exploring the Working Principle, Types, Parts, Applications, Ball mills are extensively used in the ceramic industry for grinding and blending ceramic powders, glazes, and raw materials to achieve the desired consistency and propertiesWorking Principle of Fluid Energy Mill Fluid energy mill is also known as jet mill It works on the principle of impact and interparticle attrition to achieve the desired particle size Construction of Fluid Energy Mill It consists of a grinding chamber which is an oval loop of pipe It has a diameter of about 25200 m and its height is 122 What is Fluid Energy Mill? Working Principle, Construction, 2024年2月5日 By knowing the working principle of hammer mills and various aspects that determine production, your equipment will definitely operate optimally Conclusion Clearly, the working principle of hammer mill is simple to understand It only requires choosing an appropriate motor, crushing hammers/knives and material you intend to crushThe Working Principle of Hammer Mills (Stepbystep Guide)This article aims to describe the working principle of a jet mill A jet mill, also called fluid energy mill, is used for solid material micronization Micronization is a term used to describe size reduction where the resulting particlesize distribution is less than 10 micronsJet mill working principle
2FD{P}PC]854]XQ.jpg)
Ball Mill Principle, Construction, Working, and More Soln
The residence time of the material in the mill chamber The size, density, and the number of the balls The nature (hardness) of the balls and material to be grinded Feed rate and feed level in the vessel Rotation speed of the cylinder Working of Ball Mill: Several types of ball mills exist They differ to an extent in their operating principle2 Working Principle of Vertical Grinding Mill The Vertical Grinding Mill working principle is simple and begins with the jaw crusher crushing the raw material to the required size The crushed material is then added to the hopper (situated Vertical Grinding Mill: How it Works, Application And In a modern works, the blended raw material enters the kiln via the preheater tower Here, hot gases from the kiln, and probably the cooled clinker at the far end of the kiln, are used to heat the raw meal As a result, the raw meal is Manufacturing the cement kiln Understanding 2015年7月22日 Material input into the pelleting chamber Regulated material input into the pellet mill is important for maintaining consistent pellet quality During the pellet production process moisture is released as steam If the rate Working Principles of pellet mill
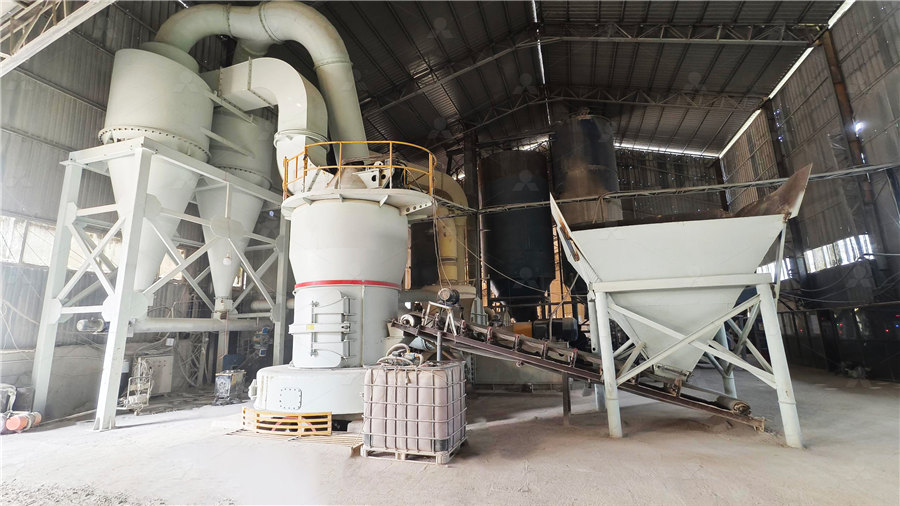
Raw Material Ball Mill
Ball Mill Working Principle; Specifications; Application: Cement Plant, Thermal Power Plant, Steel Mill, Mining: Capacity: 21210 t/h: Motor Power: 4753550 kW: Fineness: 3300~3800 cm²/g: Strong adaptability to raw material 2 Continuous production 3 Large crushing ratio 4 Easy to adjust the size of the products 5Material is held in the grinding chamber until it is reduced to the size of the openings in the screen The number of hammers on a rotating shaft, Fig 1 Hammer Mill 22 Attrition Mills Attrition mills use the hammermill principle to a certain extent; ie, shattering by/impactChapter 18 Feed Milling Processes Food and Agriculture 2012年6月1日 The feed material is typically composed of the BFRs and the catalyst, both in powder form As the cylinder starts to rotate, the grinding balls inside the cylinder crush and grind the feed Grinding in Ball Mills: Modeling and Process Control2023年10月30日 The working principle of jet milling is based on the physical properties of highspeed jet fluid Usually, the jet fluid is composed of highpressure gas or liquid, which is sprayed onto the surface of the material at a very high speed through a nozzle, generating cutting force or impact force to achieve cutting, grinding and polishing of the How Jet Milling Works: A Detailed Analysis of the Process Jet Mill
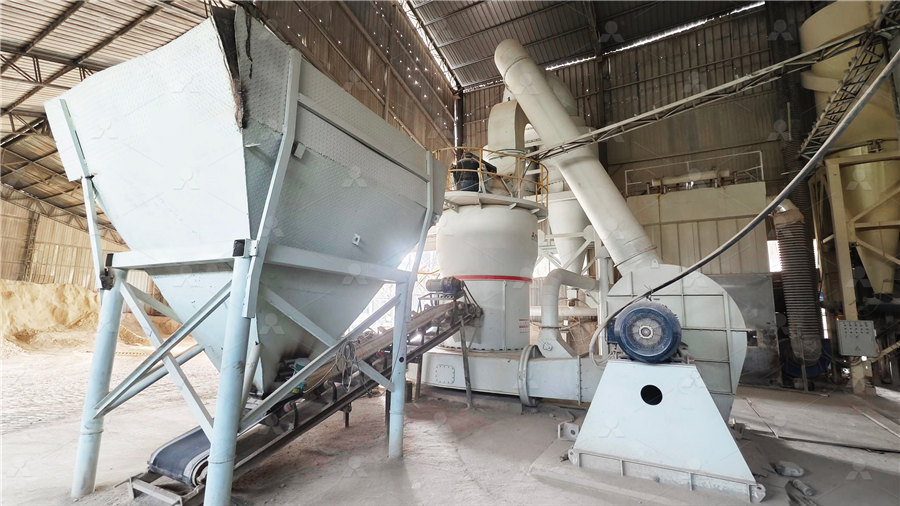
The working principle and scope of use of rod and pin type bead mill
2024年8月15日 Its unique working principle and wide application range make it an indispensable processing tool in many fields such as pigments, coatings, cosmetics, food and fine chemicals This article will explore the working principle of pintype bead mill and its diverse application scenarios ### Working principle of pintype bead mill