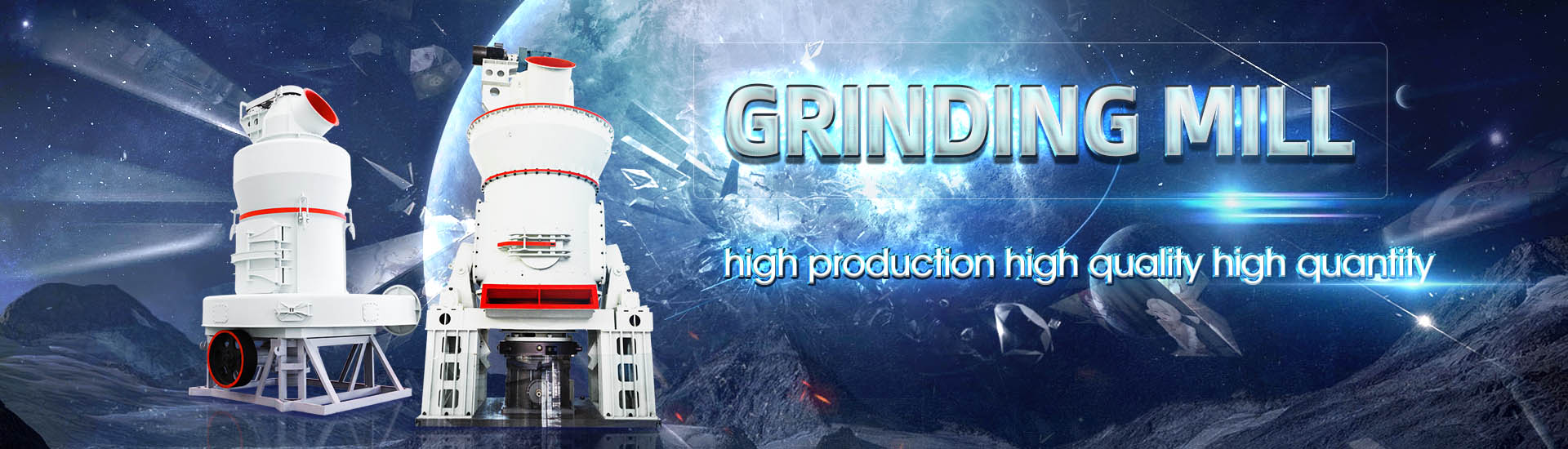
Sintering ore processing equipment working principle
.jpg)
(PDF) Iron Ore Sintering: Process ResearchGate
2017年2月16日 Sintering is a thermal agglomeration process that is applied to a mixture of iron ore fines, recycled ironmaking products, fluxes, slagforming The sintering process begins with the preparation of a sinter mixture consisting of iron ore fines, fluxes, solid fuel (called bonding agents in Japan) such as coke breeze, and return fines from Sintering Process an overview ScienceDirect Topics2022年1月1日 Sintering is the most economic and widely used agglomeration process to prepare iron ore fines for blast furnace use In this chapter, the sintering process is first Iron ore sintering ScienceDirectIn this chapter, a methodology for simulating the sintering process of iron ore is presented In order to study the process parameters and inner phenomena, a mathematical model based on Modeling Sintering Process of Iron Ore
.jpg)
Iron ore sintering ScienceDirect
2015年1月1日 Sintering is the most economic and widely used agglomeration process to prepare iron ore fines for blast furnace use In this chapter, the sintering process is first The iron ore sintering process prepares fine iron the ores for the blast furnace process Sinter plants agglomerate iron ore fines with other fine materials at high temperature in a mix bed Iron Ore Sinter Process (book)2020年8月19日 The sintering process can be defined as a thermal agglomeration process that is applied to a mixture of iron ore fines, recycled ironmaking products, fluxes, slagforming Sintering SpringerLink2017年3月24日 Sintering is a thermal agglomeration process that is applied to a mixture of iron ore fines, recycled ironmaking products, fluxes, slagforming agents, and solid fuel (coke) The Iron Ore Sintering: Process Taylor Francis Online
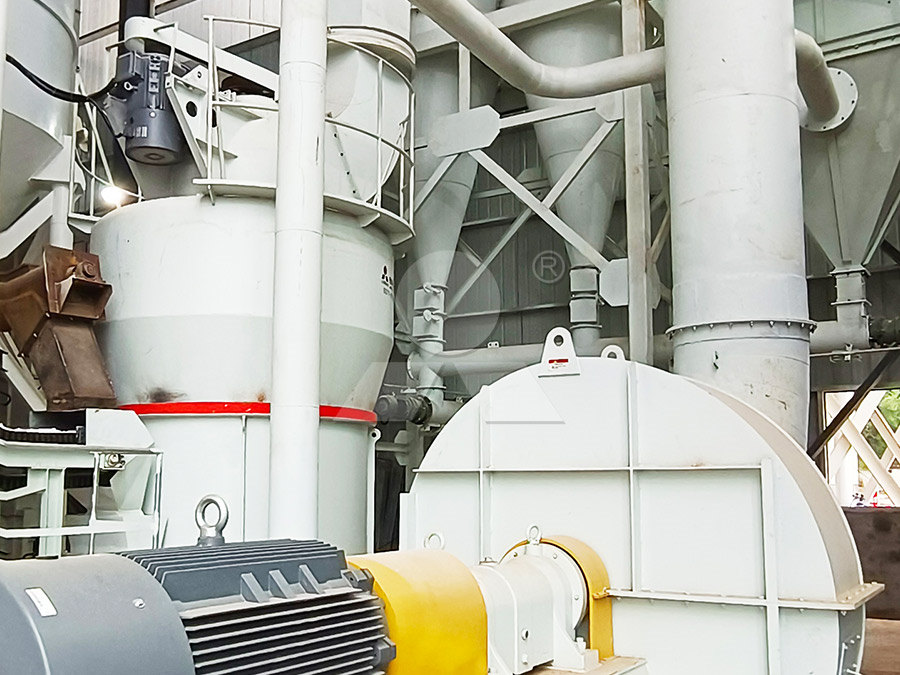
Iron Ore Sintering: Process ResearchGate
Sintering is a thermal agglomeration process that is applied to a mixture of iron ore fines, recycled ironmaking products, fluxes, slagforming agents, and solid fuel (coke) The purpose of2015年3月15日 Understanding Sinter and Sinter Plant Operations satyendra; March 15, 2015; 8 Comments ; fluxes, Iron ore fines, SCFA, sinter, sinter plant basic sinter, sintering machine,; Understanding Sinter and Sinter Plant Understanding Sinter and Sinter Plant OperationsSintering furnaces are widely available for a broad range of processing and manufacturing applications in which a material must be carefully densified through sustained stages of heating Mineralogical deposits are commonly formed Sintering Furnaces for Powder Metallurgy Thermcraft2023年11月15日 Iron Ore, Iron Ore Pellets, Direct Reduced Iron )DRI( Pellets, Iron Ore Pellets Market, Pelletizing Process, Sintering, Binder, Induration Technology, Straight Grate, GrateRotary kiln The iron (PDF) IRON ORE PELLETIZING PROCESS ResearchGate
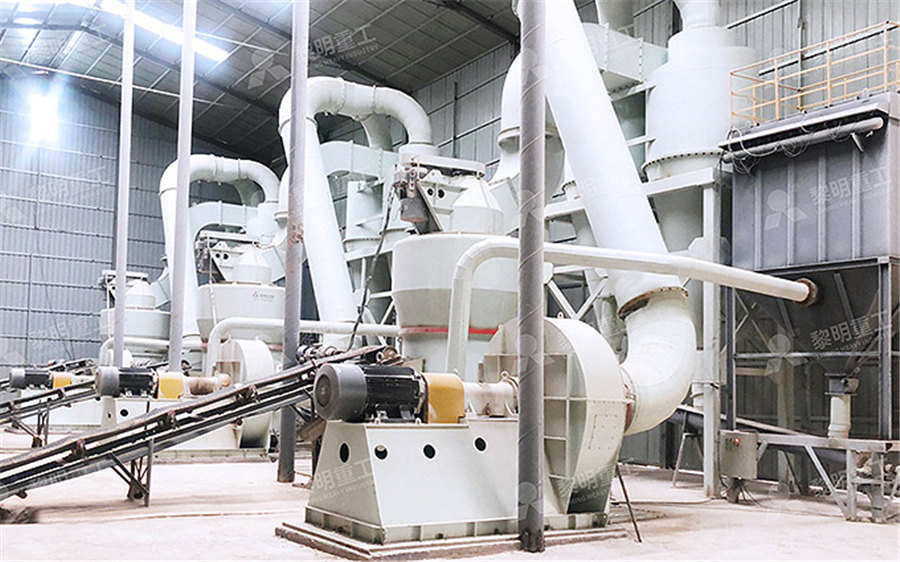
Selective Laser Sintering: Principle, Application, Disadvantages
2024年5月22日 Characteristics of Selective Laser Sintering Among the most effective types of 3D printing now in use is Selective laser sintering It is intended for use in industry and by professionals To cover the full workflow, postprocessing equipment including powder sieves and depowdering stations is requiredPROCESS BRIEF Sintering process is developed mainly to utilize under size of lump ore called iron ore fines; which otherwise, could not be charged directly in blast furnace In order to conserve these, otherwise waste material, they are compacted together and made into lumps by a process known as sinteringSintering is defined as thePROCESS BRIEF Ministry of Steel2017年3月24日 Sintering is a thermal agglomeration process that is applied to a mixture of iron ore fines, recycled ironmaking products, fluxes, slagforming agents, and solid fuel (coke) The purpose of the sintering process is manufacturing a product with the suitable characteristics (thermal, mechanical, physical and chemical) to be fed to the blast furnaceIron Ore Sintering: Process Taylor Francis Online2016年10月28日 Sintering is an agglomeration process that fuses iron ore fines, fluxes, recycled products, slagforming elements and coke The purpose of sintering is to obtain a product with suitable Iron Ore Sintering: Raw Materials and Granulation ResearchGate
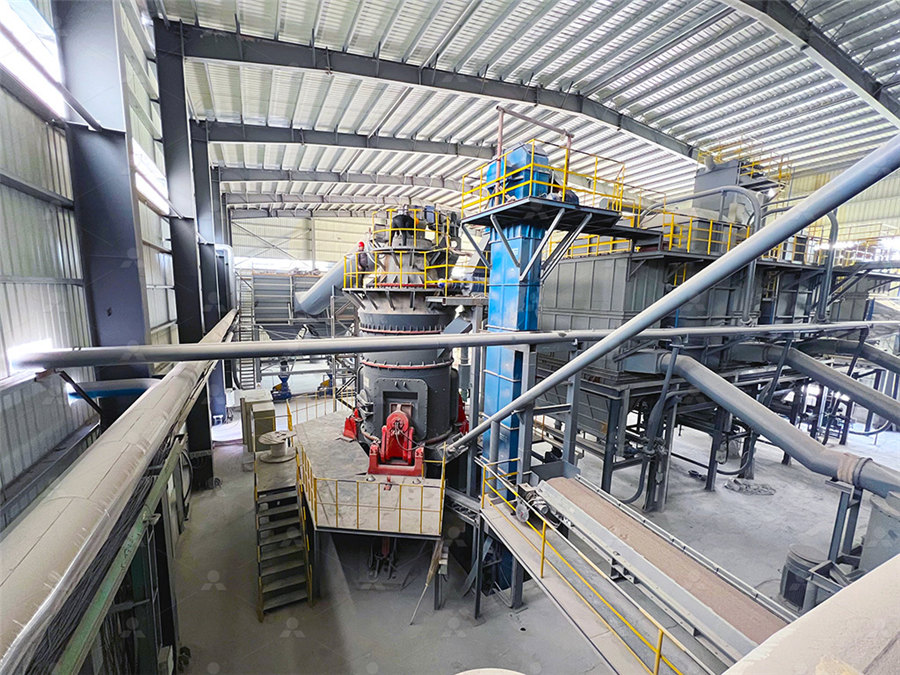
Sintering plant at a glance PPT SlideShare
2014年10月27日 25 PRINCIPLE OF THE SINTER MAKING PROCESS • Iron one sintering is carried out by putting GREEN MIX after Mixing and Nodulizing drum (a mixture of Base mode with iron ore fines, mixed with flux, coke breeze as a solid fuel, other additions, sinter return fines, lime, moisture) over a traveling gate in form of permeable bed and permeable bedSintering is a manufacturing process used for making various parts from metal or ceramic powder mixtures Sintering can be defined as the thermal transformation of bulk materials into compact solids at temperatures below their melting point [1–4]The main phenomenon is solid state diffusion, which occurs along the different interfaces of the crystals and through any vacanciesSintering an overview ScienceDirect Topics2022年1月1日 SO X removal is achieved via installation of sintering flue gas desulfurization equipment In addition to the (mosaic embedding iron ore sintering) process was therefore proposed as part of an Iron and Yazawa International Symposium: Metallurgical and Materials Processing: Principles and Techologies, Volume 1 Iron ore sintering ScienceDirectIn roasting, the ore is heated in a regular supply of air in a furnace at a temperature below the melting point of the metal Roasting is a metallurgical process involving gas–solid reactions at elevated temperatures with the goal of purifying the metal component(s) Often before roasting, the ore has already been partiallyPRINCIPLES OF ROASTING WITH ITS TYPES University of

Spark Plasma Sintering: Process Fundamentals: Advances in Processing
2019年1月1日 Spark plasma sintering (SPS) is a rapid technique Its processing parameters are usually lowvoltage and lowpressure acting, using a uniaxial force and pulsed direct current (DC) to carry out 2019年2月19日 Generally, sintering can be done using various methods such as conventional sintering, microwave sintering, hot press (HP), hot isostatic press (HIP) and sparkplasma sintering (SPS) SPS is an emerging powder Spark Plasma Sintering: Process FundamentalsEquipment Size: Φ16*20, Φ19/16*36, Φ28/25*55, Φ30*48 Zinc Oxide Kiln, etc The cement rotary kiln is mainly used for calcining cement clinker, dry process to produce cement kiln and the wet The operators of limestone slaking equipment are required to understand the working principle as well as the chemical process Cement Rotary Kiln for Dry Process Cement Plant2015年6月24日 13 CHAPTER: 3 LITERATURE SURVEY 31 Principle Of Sintering Process In iron – ore sintering, essence is carried out by putting mixture of iron bearing fines mixed with solid fuel on a permable grate Since coke breeze is available as a otherwise wasted product in an intergrated iron and steel plant Its universally incorporated as a solid fuel Design And Fabrication Of Iron Ore Sintering Machine
.jpg)
Identification of working conditions and prediction of FeO
2024年6月4日 The iron oxide (FeO) content had a significant impact on both the metallurgical properties of sintered ores and the economic indicators of the sintering process Precisely predicting FeO content possessed substantial potential for enhancing the quality of sintered ore and optimizing the sintering process A multimodel integrated prediction framework for FeO 2015年3月21日 The process of enriching taconite ore involved grinding the ore to remove gangues and upgrading the iron ore (ie, an ore beneficiation process) The resultant high grade ore is in the form of fine particles, as small as 01 mm or less, which are not suitable for sintering This issue led to the development of the pelletizing processUnderstanding Pellets and Pellet Plant Operations IspatGuru2023年6月8日 To intensify sintering, improve sinter quality, and conserve energy, certain technologies have been developed, such as hot air sintering, doublelayer sintering, oxygenrich sintering, lowtemperature sintering, minipellet sintering, flue gas circulation sintering, optimized ore proportioning, flux structure optimization, sintering expert system, and sintering flue gas Iron Ore Sintering SpringerLink2015年8月7日 The centrifugal force (the central Hydrocyclone Working Principle) that is generated by this spin, forces the “bigger particles outwards towards the wall of the cyclone If you were able to do a cross section of a cyclone while it is operating, you could see that the ground rock will become finer the closer that you get to the centre of the cycloneHydrocyclone Working Principle 911Metallurgist
.jpg)
How Does Selective Laser Sintering (SLS) Work?
2020年11月25日 The SLS process principle In the SLS process, a thin layer of powder is applied on the build platform and heated to just below the Melting Temperatures and Enthalpies The enthalpy of fusion of a substance, also known as latent heat, is a measure of the energy input, typically heat, which is necessary to convert a substance from solid to liquid state14th International Symposium on Process Systems Engineering Haoran Li, Tong Qiu, in Computer Aided Chemical Engineering, 2022 21 Process description The sintering process is an important thermochemical process in the blast furnace ironmaking system It involves the heating of fine iron ore with flux and coke fines or coal to produce a semimolten mass that Sintering Process an overview ScienceDirect Topics2017年2月16日 Sintering is a process of agglomeration of iron ore fines, fluxes, recycled products, slagforming elements and coke with the purpose of achieving an agglomerated product with the suitable Iron Ore Sintering: Environment Automatic and 2018年11月25日 Theory and Practice of Sintering of Iron ore satyendra; November 25, 2018; 0 Comments ; C2F, CF, CF2, Combustion zone, FF, melting, RDI, RI, SFCA, SI, sinter, Sinter mix, Softening, TI,; Theory and Practice of Theory and Practice of Sintering of Iron ore –
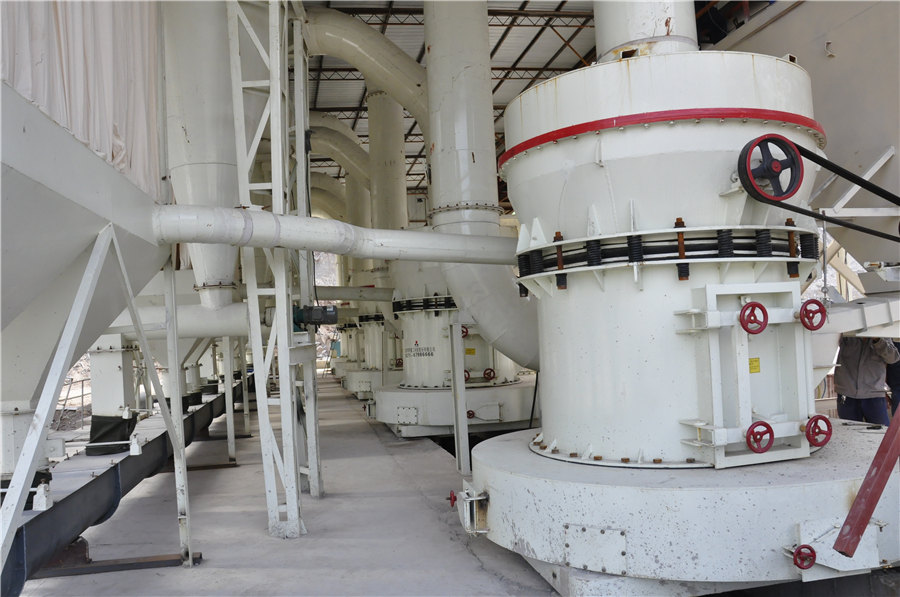
Sintering process using a DwightLloyd machine
Wu et al proposed a sintering area prediction method using RGB grayscale division of the sintering machine tail image [7] Chen et al used dark channel image processing to obtain sinter ore 2012年3月1日 An oreblending optimization model for the sintering process is an intelligent system that includes iron ore characteristics, expert knowledge and material balanceOreblending optimization model for sintering process based on 2023年10月9日 Fluidized bed technology has become a crucial method used to process iron ore powder in nonblast furnace ironmaking, such as smelting reduction and direct reduction This paper introduces the working principle and several typical working states of fluidized bed (FB) technology to clarify the key to fluidized bed process operationDevelopment and Problems of Fluidized Bed Ironmaking Process: 2022年12月29日 The roles of iron ore, fuel, fluxes, and moisture in sintering granulation are also analyzed, and finally advanced granulation equipment and processes for industrial production, as well as their (PDF) Iron Ore Granulation for Sinter Production: Developments
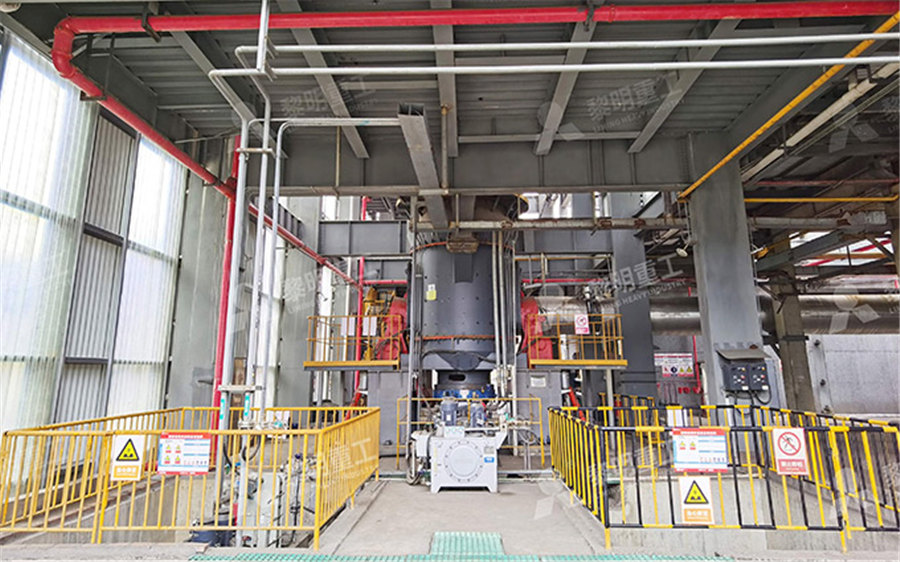
Iron ore sintering ScienceDirect
2015年1月1日 Like other sintering processes, iron ore sintering converts iron ore fines of often − 8 mm sizing into larger agglomerates, namely, sinter, between 5 and 50 mm particle size, which possess the physical and metallurgical characteristics and gas permeability required for efficient blast furnace operationAs shown in Figure 141, iron ore sintering is carried out in three 2024年3月20日 Sinter machine capacity depends on the quality of the sintering components and local process conditions The sintering area determines it, making it 1315 t/ m 2 h Technologies for Reducing Sintering Emissions Reduction of fuel consumption for the sintering process in ironmaking decreases emissions of harmful gaseous substances into the Iron Ore Sintering Process: Transforming Raw Ore into High dedication to pelletizing and sintering as they are the most used worldwide 21 Briquetting Briquetting is the simplest agglomeration process Fine grained iron ore is pressed into two pockets with the addition ofwater orsome other binder agent Iron Ore Agglomeration Technologies2015年3月15日 Understanding Sinter and Sinter Plant Operations satyendra; March 15, 2015; 8 Comments ; fluxes, Iron ore fines, SCFA, sinter, sinter plant basic sinter, sintering machine,; Understanding Sinter and Sinter Plant Understanding Sinter and Sinter Plant Operations
.jpg)
Sintering Furnaces for Powder Metallurgy Thermcraft
Sintering furnaces are widely available for a broad range of processing and manufacturing applications in which a material must be carefully densified through sustained stages of heating Mineralogical deposits are commonly formed 2023年11月15日 Iron Ore, Iron Ore Pellets, Direct Reduced Iron )DRI( Pellets, Iron Ore Pellets Market, Pelletizing Process, Sintering, Binder, Induration Technology, Straight Grate, GrateRotary kiln The iron (PDF) IRON ORE PELLETIZING PROCESS ResearchGate2024年5月22日 Characteristics of Selective Laser Sintering Among the most effective types of 3D printing now in use is Selective laser sintering It is intended for use in industry and by professionals To cover the full workflow, postprocessing equipment including powder sieves and depowdering stations is requiredSelective Laser Sintering: Principle, Application, DisadvantagesPROCESS BRIEF Sintering process is developed mainly to utilize under size of lump ore called iron ore fines; which otherwise, could not be charged directly in blast furnace In order to conserve these, otherwise waste material, they are compacted together and made into lumps by a process known as sinteringSintering is defined as thePROCESS BRIEF Ministry of Steel
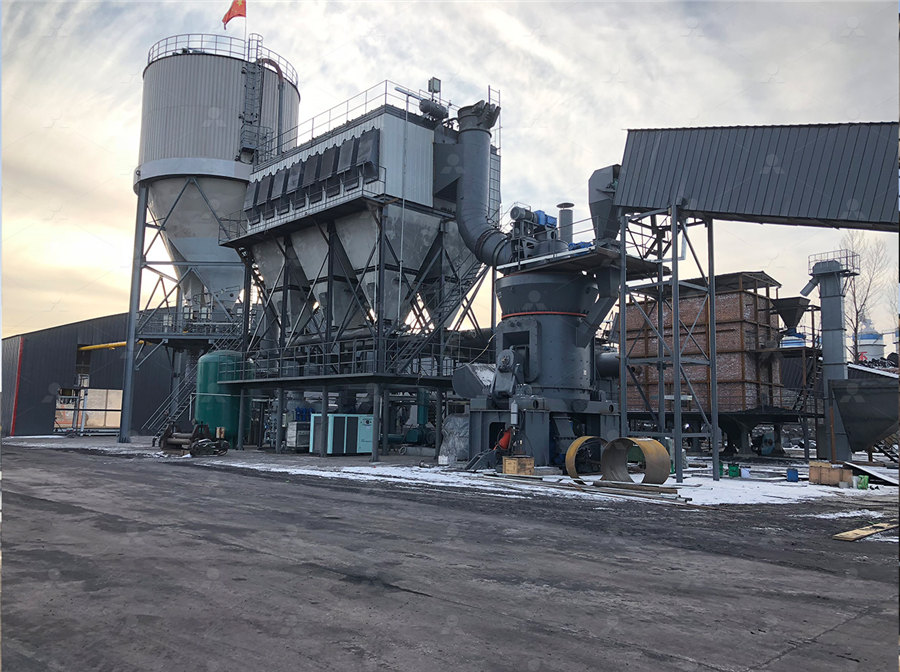
Iron Ore Sintering: Process Taylor Francis Online
2017年3月24日 Sintering is a thermal agglomeration process that is applied to a mixture of iron ore fines, recycled ironmaking products, fluxes, slagforming agents, and solid fuel (coke) The purpose of the sintering process is manufacturing a product with the suitable characteristics (thermal, mechanical, physical and chemical) to be fed to the blast furnace2016年10月28日 Sintering is an agglomeration process that fuses iron ore fines, fluxes, recycled products, slagforming elements and coke The purpose of sintering is to obtain a product with suitable Iron Ore Sintering: Raw Materials and Granulation ResearchGate2014年10月27日 25 PRINCIPLE OF THE SINTER MAKING PROCESS • Iron one sintering is carried out by putting GREEN MIX after Mixing and Nodulizing drum (a mixture of Base mode with iron ore fines, mixed with flux, coke breeze as a solid fuel, other additions, sinter return fines, lime, moisture) over a traveling gate in form of permeable bed and permeable bedSintering plant at a glance PPT SlideShareSintering is a manufacturing process used for making various parts from metal or ceramic powder mixtures Sintering can be defined as the thermal transformation of bulk materials into compact solids at temperatures below their melting point [1–4]The main phenomenon is solid state diffusion, which occurs along the different interfaces of the crystals and through any vacanciesSintering an overview ScienceDirect Topics

Iron ore sintering ScienceDirect
2022年1月1日 SO X removal is achieved via installation of sintering flue gas desulfurization equipment In addition to the (mosaic embedding iron ore sintering) process was therefore proposed as part of an Iron and Yazawa International Symposium: Metallurgical and Materials Processing: Principles and Techologies, Volume 1