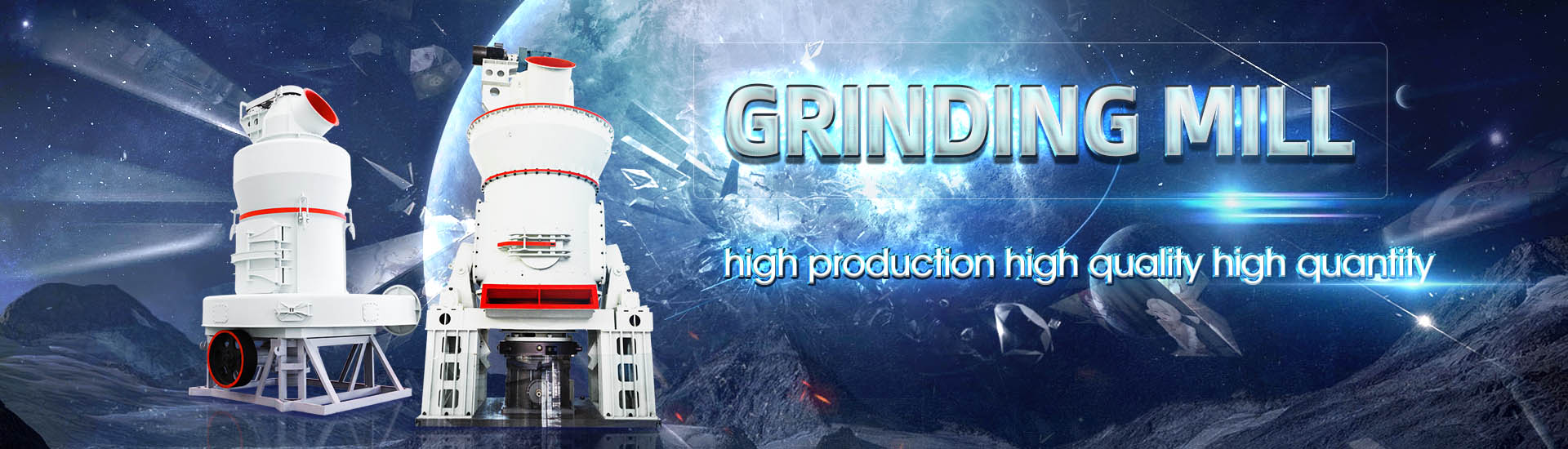
Ore grinding mill particle size factors
.jpg)
Fine grinding: How mill type affects particle shape characteristics
2017年9月1日 This study explored the influence of wet and dry grinding conditions on breakage rate, shape factor and surface roughness of ground particles, induction time (the threshold for 2018年6月1日 In this article the effect of grinding media size distribution and feed material particle size distribution (PSD) on the product fineness requirements were investigated A Effect of ball and feed particle size distribution on the milling 2023年7月20日 According to the particle sizes of grinding products, the grinding process is divided into coarse grinding, medium grinding, fine grinding, microfine grinding, and ultrafine Ore Grinding SpringerLink2017年9月1日 Traditionally, design and optimisation of comminution circuits was based on the production of a target particle size distribution at an optimised throughput with consideration of Fine grinding: How mill type affects particle shape characteristics
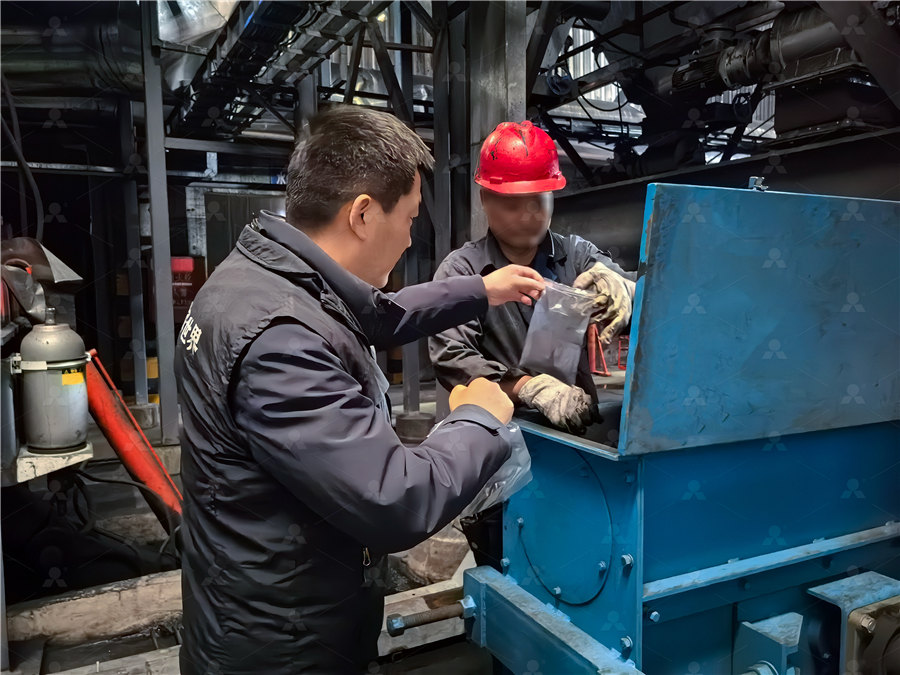
Research on Grinding Characteristics and Comparison
2022年10月26日 Through the JK dropweight test, the batch grinding test, and the populationbalance kinetic model of grinding with the Simulink platform, the grinding characteristics of the two types of ores and the particlesize 2017年9月1日 Particle size distribution (PSD) is a key factor in size reduction processes These processes are widely used worldwide and in the Colombian industry However, they represent [PDF] Fine grinding: How mill type affects particle shape 2022年10月13日 The results show that grinding time is a significant factor affecting the particle size composition The suitable grinding concentration of Tongkeng ore and Gaofeng ore is 70% and 75%, respectively The effect of Research on Grinding Law and Grinding Parameters 2020年1月3日 Based on the total retention time of each ore, the optimum grinding time for each ore was identified to obtain the desired P 80 passing particle size with acceptable hematite Estimation of Grinding Time for Desired Particle Size Distribution
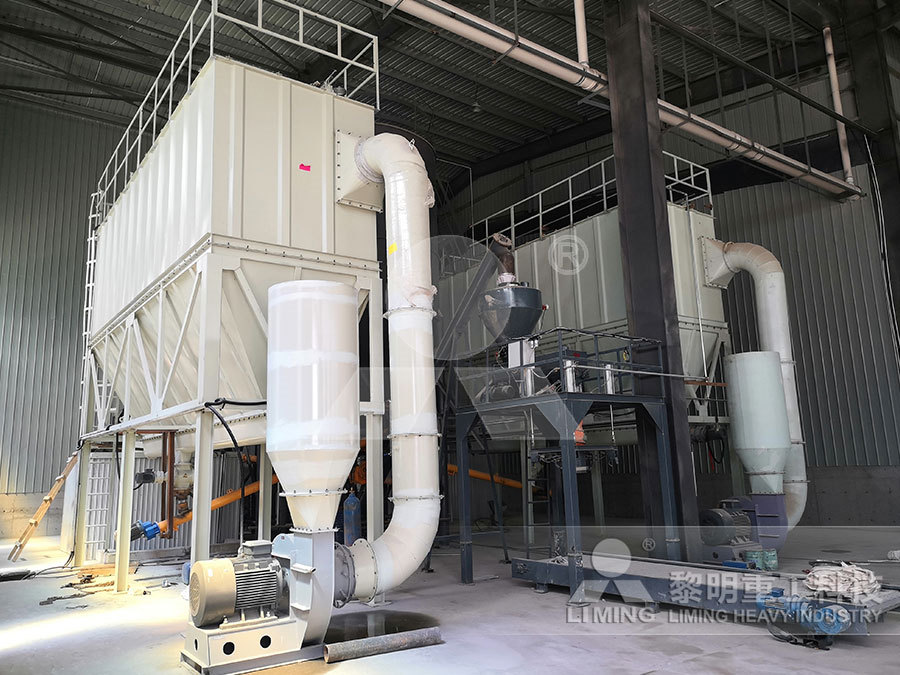
Estimating Ore Particle Size Distribution using a Deep
grinding mill performance Tessier et al (2007) also notes that feed size variations strongly affect mill performance, along with ore composition and grindability Particle size analysis is a crucial 2022年8月31日 The results show that grinding time is a significant factor affecting the particle size composition The suitable grinding concentration of Tongkeng ore and Gaofeng ore is 70% and 75%, respectively The effect of Grinding Modeling and Energy Efficiency in Ore/Raw 2019年3月28日 In the ball mill, the main grinding method was the impact of the steel ball medium with the finer ore particles, and the Ecs was high because the weight of the single steel ball was significantly Research on prediction model of ore grinding particle size distribution2022年10月26日 The particle size composition of grinding products will significantly affect the technical and economic indexes of subsequent separation operations The polymetallic complex ores from Tongkeng and Gaofeng are Research on Grinding Characteristics and Comparison

Physicochemical Problems of Mineral Processing Investigation
2017年3月20日 An effect of a grinding method, that is ball mill and high pressure grinding rolls (HPGR), on the particle size, specific surface area and particle shape of an iron ore concentrate was studied2024年1月1日 According to the different grinding medium, the grinding mill is divided into three types: (1) ball mill – it is used widely, and almost all materials can be triturated by ball mill; (2) rod mill – its efficiency is relatively high with the feeding particle size less than 30 mm and the product particle size around 3 mm, and the produced product particle size is uniform with less Ore Grinding SpringerLink2021年3月26日 Ball mill grinding efficiency is influenced by many factors: ore grindability, feed size, grinding product size, ball mill diameter and length, ball mill working speed, liner type, steel ball loading system, grinding concentration, return sand ratio in closedcircuit grinding and feed rate (Ball mill) To improve the ball mill grinding efficiency, you must first understand the What Factors Will Influence Ball Mill Grinding Efficiency?2020年1月1日 INTRODUCTION Silva and Casali (2015) argues that comminution (espe cially milling) is the most important minerals processing operation, partly because of its effect on the downstream processes, and further that the feed size distribution is one of the most important factors affecting semiautogenous grinding mill performanceEstimating Ore Particle Size Distribution using a Deep Convolutional

Research on Grinding Law and Grinding Parameters Optimization
2022年10月13日 Therefore, in order to facilitate the research, the particle size of −015 + 0038 mm in the grinding products of polymetallic complex ores is regarded as qualified particle size, the particle size of +015 mm is regarded as undergrinding particle size, and the particle size of −0038 mm is regarded as overgrinding particle size [29,30,31]2015年6月19日 Likewise, a similar confusion surrounds the length of a mill Therefore, when comparing the size of a mill between competitive manufacturers, one should be aware that mill manufacturers do not observe a size convention Ball Mill Power/Design Calculation Example #2 In Example No1 it was determined that a 1400 HP wet grinding ball mill was Ball Mill Design/Power Calculation 911MetallurgistThe shape of crushed ore affects the product particle size in a ball mill grinding circuit It has also been proposed that green pellet quality is directly related to the amount of fine particles in a pelletizing plant (Dwarapudi et al, 2008; Umadevi et al, 2008; Gul et al, 2014; Van der Meer, 2015) Particle size distributionInvestigation on the particle size and shape of iron ore pellet feed 2016年7月7日 The recovery of gold by ore leaching is influenced by the size of the particles and the chemical environment The effect of particle size on the dissolution of gold is usually studied using mono Effect of Particle Size and Grinding Time on Gold

Iron Ore Processing: From Extraction to Manufacturing
2024年4月26日 The choice of grinding mill depends on factors such as the desired product size, capacity requirements, and energy consumption b Autogenous and SemiAutogenous Mills: In some cases, autogenous (AG) 2017年7月3日 Closedcircuit grinding was employed to study the different ball loads Effect of Particle Size and Mill Power The influence that particle size may have on power is illustrated in table 5 There the variation in comminution was moderate but the power varied almost 10 percentVariables Affecting Grinding Mill Power 911Metallurgistthe particle and the weaker the ore breakage properties A sharp particle size distribution in the product of a unit will occur when the production of ultrafi nes during grinding is minimised This occurs when the probability of breakage of the coarser particles is much higher than the fi Particle Size Distribution Effects that Should be Considered when Fine grinding: How mill type affects particle shape characteristics and minution circuits was based on the production of a target particle size distribution at an optimised throughput which involved batch grinding of UG2 ore in a ball mill and in a stirred mill These experiments were effectively conducted in parallel, Fine grinding: How mill type affects particle shape characteristics
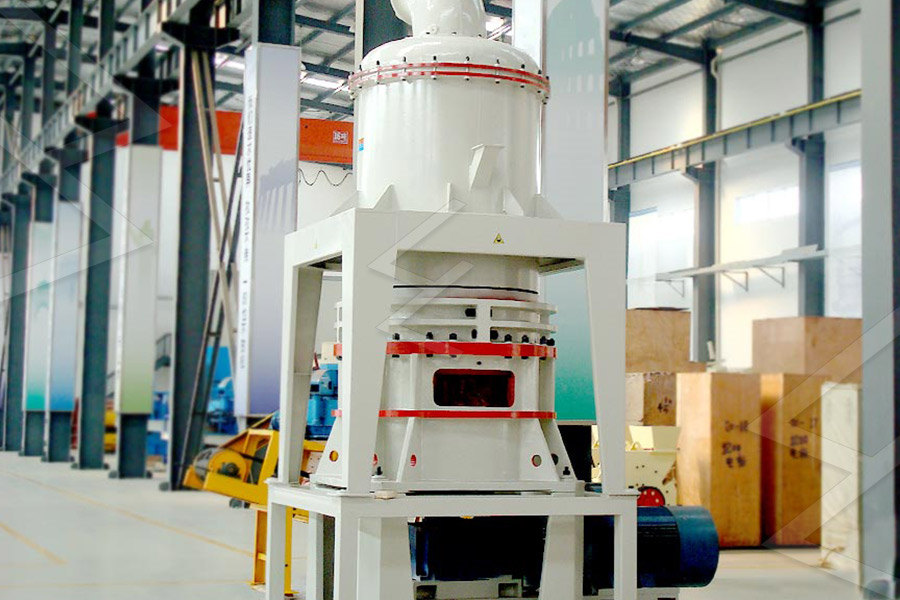
Investigating of the effect of ore work index and particle size on
2016年4月1日 These experiments were conducted for the same 3 sample with providing d80 of 1000 μm to show the effect of increasing feed size on the modeling processThe 1000 μm feed size of same copper samples were obtained by grinding ores in laboratory jaw and roll crusher until the d80 of product reached 1000 μmTherefore, six ore samples were treated for grinding 2017年9月1日 This situation makes it necessary to examine parameters such as the type of grinding material (coal/ore), grinding type/medium, grinding technique, particle size, shape, size distribution Fine grinding: How mill type affects particle shape characteristics 2024年5月20日 The ball mill lifts the grinding media by rotation of its horizontal cylindrical part which then falls back impacting the ore particles The grinding action is then achieved by attrition, abrasion, and impact between the ore and the grinding media 3 Spherical media has been commonly used in ball mills; however, different shapes of grinding media have different Effect of grinding media shape on the particle size distribution of affecting the particle size composition The suitable grinding concentration of Tongkeng ore and Gaofeng ore is 70% and 75%, respectively The effect of mill filling ratio on Gaofeng ore is not Optimization of Polymetallic Complex Ores ResearchGate
.jpg)
Understanding the operation of grinding mills in the mining and
Factors Affecting Grinding Mill Performance: 1 Grindability: The grindability of the ore affects the efficiency of the grinding mill Harder ores require more energy and longer grinding times, The particle size distribution of the mill's output directly impacts the efficiency of the flotation processB21 Rationale For Developing Generalized Particle Size Distributions B26 EMISSION FACTORS (Reformatted 1/95) 9/90 Table B21 PARTICLE SIZE CATEGORY BY AP42 SECTION Anode baking furnace 9 1218 Leadbearing ore crushing and grinding 4 Prebake cell a Miscellaneous sourcesAP42, Appendix B2 Generalized Particle Size Distributions2019年5月10日 Factors Influence Ore Grinding Mill Efficiency Abstract 1 Ore particle size In the most grinding process of the concentrator, the construction investment and production and operation cost of grinding operation is much Factors Influence Ore Grinding Mill Efficiency JXSC 11 Grinding media size specification A number of researchers (Deniz, 2012; Bwalya et al, 2014; Petrakis et al, 2016) carried out studies about the effect of feed particle size and grinding media size on the grinding kinetics of different ores Khumalo et Effect of ball and feed particle size distribution on the milling
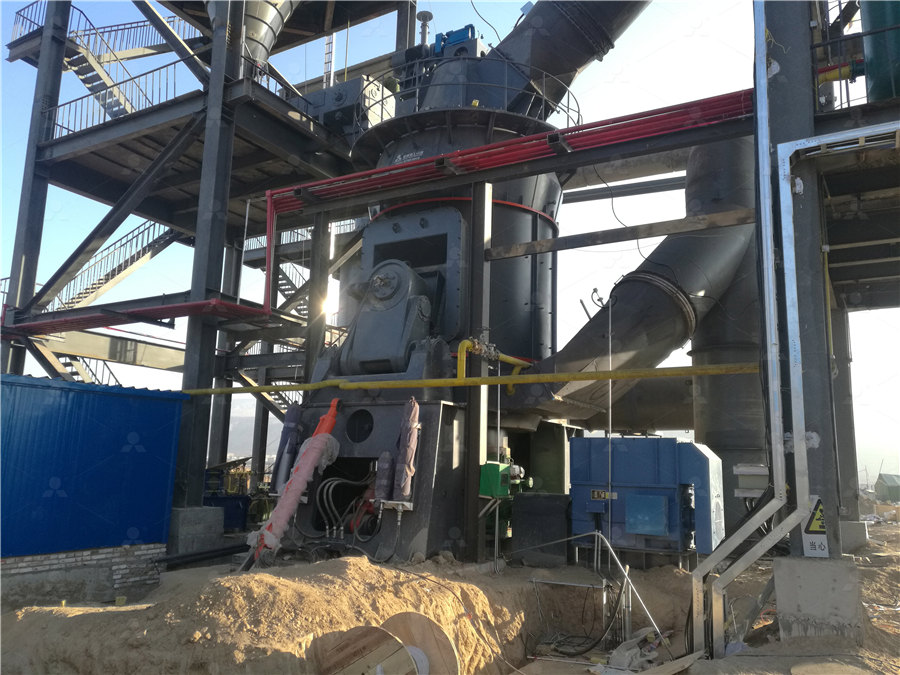
Grinding Media in Ball MillsA Review ResearchGate
Grinding is the final stage of comminution, which reduces particle size to micron size level The size reduction is achieved by attrition, abrasion, and impact between the ore itself and between Estimating Ore Particle Size Distribution grinding mill performance Tessier et al (2007) of the most important factors affecting semiautogenous grinding mill performance Tessier et al (2007) also notes that feed size variations strongly affect mill performance,Estimating Ore Particle Size Distribution using a Deep Download scientific diagram Iron ore particle size distribution from publication: Impact Load Behavior between Different Charge and Lifter in a LaboratoryScale Mill The impact behavior Iron ore particle size distribution Download Scientific DiagramThere are several impact factors of the grinding operation (1) Structure parameters of grinding mill, including its specifications, model, aspect ratio, ore discharging method, and liner form (2) Various working parameters of grinding mill, including fraction of critical speed for grinding mill, filling rate for grinding mill, grinding conOre Grinding Methods and Process of Ore Grinding
.jpg)
Estimation of Grinding Time for Desired Particle Size Distribution
Ball mills are progressively used to grind the ores for particle size reduction and to liberate valuable minerals from the ores The grinding of ore is a highly energyintensive process [1–4] In this process, the size of the particle obtained depends on the energy consumption of the ball mill The major challenge encountered in thetheir bond strength Ore size reduction is the result of the following three main fragmentation mechanisms 1 Abrasion 2 Cleavage 3 Fracture Figure 1 Grinding of ores inside a ball mill In practice, the three mechanisms never operate separately, and in the process of particle size reduction, they all work with possible advantage depending Control of ball mill operation depending on ball load and ore Unlike other grinding mills, the VSI Mill offers more control over particle size distribution It can produce both coarse and fine particles through an adjustable rotor speed feature Additionally, it has low operating costs due to its simple structure and requires minimal maintenanceUnderstanding the SAG Mill in Copper Ore Mining Process2022年8月31日 The results show that grinding time is a significant factor affecting the particle size composition The suitable grinding concentration of Tongkeng ore and Gaofeng ore is 70% and 75%, respectively The effect of Grinding Modeling and Energy Efficiency in Ore/Raw
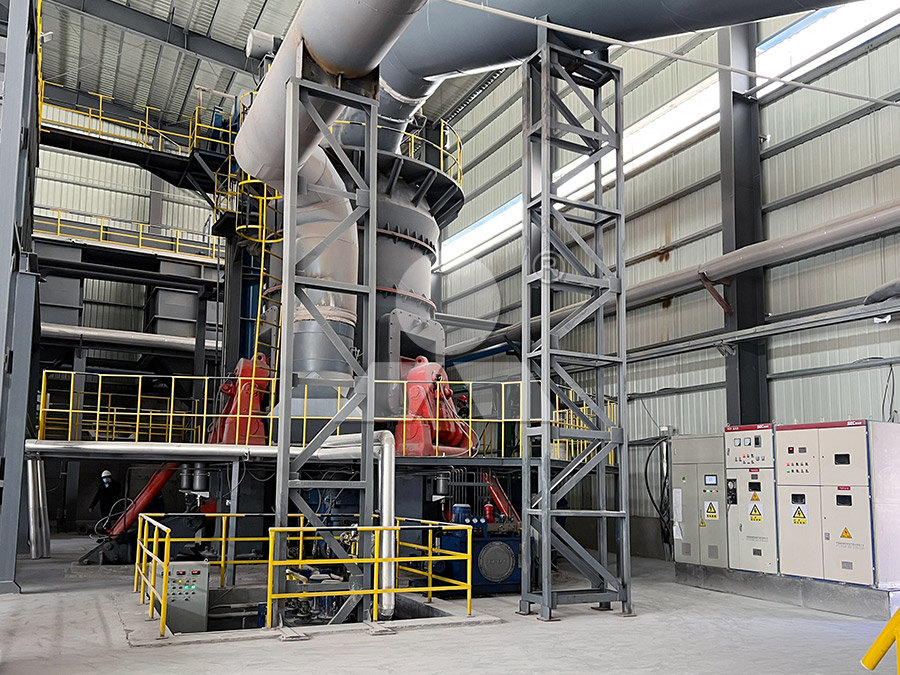
Research on prediction model of ore grinding particle size distribution
2019年3月28日 In the ball mill, the main grinding method was the impact of the steel ball medium with the finer ore particles, and the Ecs was high because the weight of the single steel ball was significantly 2022年10月26日 The particle size composition of grinding products will significantly affect the technical and economic indexes of subsequent separation operations The polymetallic complex ores from Tongkeng and Gaofeng are Research on Grinding Characteristics and Comparison 2017年3月20日 An effect of a grinding method, that is ball mill and high pressure grinding rolls (HPGR), on the particle size, specific surface area and particle shape of an iron ore concentrate was studiedPhysicochemical Problems of Mineral Processing Investigation 2024年1月1日 According to the different grinding medium, the grinding mill is divided into three types: (1) ball mill – it is used widely, and almost all materials can be triturated by ball mill; (2) rod mill – its efficiency is relatively high with the feeding particle size less than 30 mm and the product particle size around 3 mm, and the produced product particle size is uniform with less Ore Grinding SpringerLink
.jpg)
What Factors Will Influence Ball Mill Grinding Efficiency?
2021年3月26日 Ball mill grinding efficiency is influenced by many factors: ore grindability, feed size, grinding product size, ball mill diameter and length, ball mill working speed, liner type, steel ball loading system, grinding concentration, return sand ratio in closedcircuit grinding and feed rate (Ball mill) To improve the ball mill grinding efficiency, you must first understand the 2020年1月1日 INTRODUCTION Silva and Casali (2015) argues that comminution (espe cially milling) is the most important minerals processing operation, partly because of its effect on the downstream processes, and further that the feed size distribution is one of the most important factors affecting semiautogenous grinding mill performanceEstimating Ore Particle Size Distribution using a Deep Convolutional 2022年10月13日 Therefore, in order to facilitate the research, the particle size of −015 + 0038 mm in the grinding products of polymetallic complex ores is regarded as qualified particle size, the particle size of +015 mm is regarded as undergrinding particle size, and the particle size of −0038 mm is regarded as overgrinding particle size [29,30,31]Research on Grinding Law and Grinding Parameters Optimization 2015年6月19日 Likewise, a similar confusion surrounds the length of a mill Therefore, when comparing the size of a mill between competitive manufacturers, one should be aware that mill manufacturers do not observe a size convention Ball Mill Power/Design Calculation Example #2 In Example No1 it was determined that a 1400 HP wet grinding ball mill was Ball Mill Design/Power Calculation 911Metallurgist
.jpg)
Investigation on the particle size and shape of iron ore pellet feed
The shape of crushed ore affects the product particle size in a ball mill grinding circuit It has also been proposed that green pellet quality is directly related to the amount of fine particles in a pelletizing plant (Dwarapudi et al, 2008; Umadevi et al, 2008; Gul et al, 2014; Van der Meer, 2015) Particle size distribution