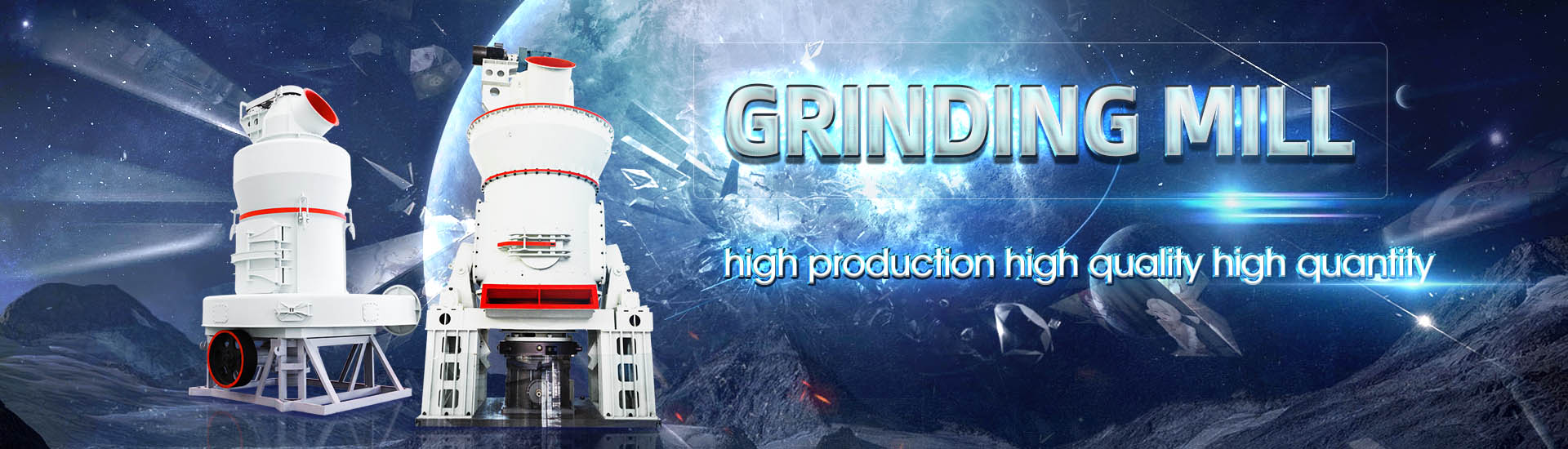
Manganese ore pretreatment

PROPERTIES OF MANGANESE ORES AND THEIR
2010年11月12日 Formation of a liquid slag in ores at equilibrium was predicted for Wessels, Groote Eylandt and Gabonese ores at 1200°C in air and 10001200°C in a reducing atmosphere No liquid slag was predicted for equilibrium phases in CVRD ore Industrial manganese ores 2024年9月15日 The reduction behaviour of South African Nchwaning manganese (Mn) ore using gaseous CO/CO 2, H 2 /H 2 O, and H 2 atmospheres was investigated experimentally in the Prereduction of Nchwaning manganese ore in CO/CO2, 2019年2月28日 With this as an opportunity, the Tokushima plant has constructed a new manganese ore pretreatment process by utilizing an idle rotary kiln, which can carry out not Manganese ore prereduction using a rotary kiln to Pilotscale experiments have been conducted at SINTEF/NTNU in a 440 kVA AC electric furnace utilizing different feed mixtures of untreated manganese ore, manganese ore preheated in air, Utilization of Pretreated MnOre in a PilotScale
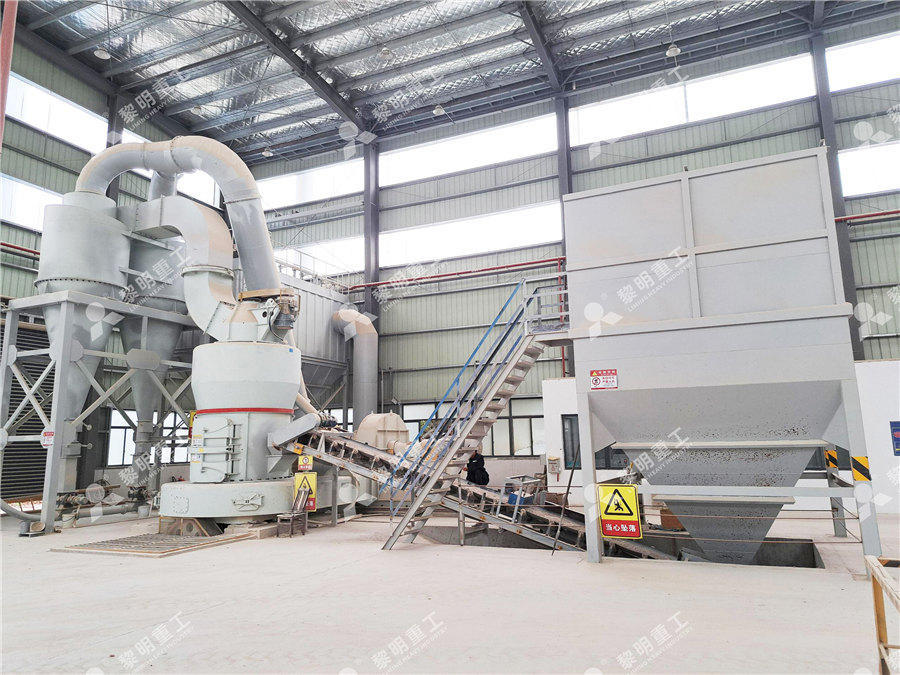
Prereduction Behaviour of Manganese Ores in
Manganese bearing minerals containing higher manganese oxides, namely MnO 2, Mn 2 O 3 and Mn 3 O 4 are found in the prereduction zone and are reduced to MnO in solid state in the 2021年4月29日 A reaction rate analysis of thermogravimetric data obtained for the reduction of Comilog and Nchwaning manganese ores in COCO2 atmosphere was performed Experimental variables were CO partial pressure, Reaction Rate Analysis of Manganese Ore 2021年9月12日 Preheating of feed for smelting in submerged arc furnace (SAF), has shown to have numerous advantages in the ferroalloy industry In ferrochrome smelting industry for Pretreatment of Manganese Ore for Improved Energy 2020年7月1日 In the present work, the thermal decomposition mechanism and phase structures of manganese ore were systematically investigated, calcined through microwave calcination Efficient improvement for dissociation behavior and thermal
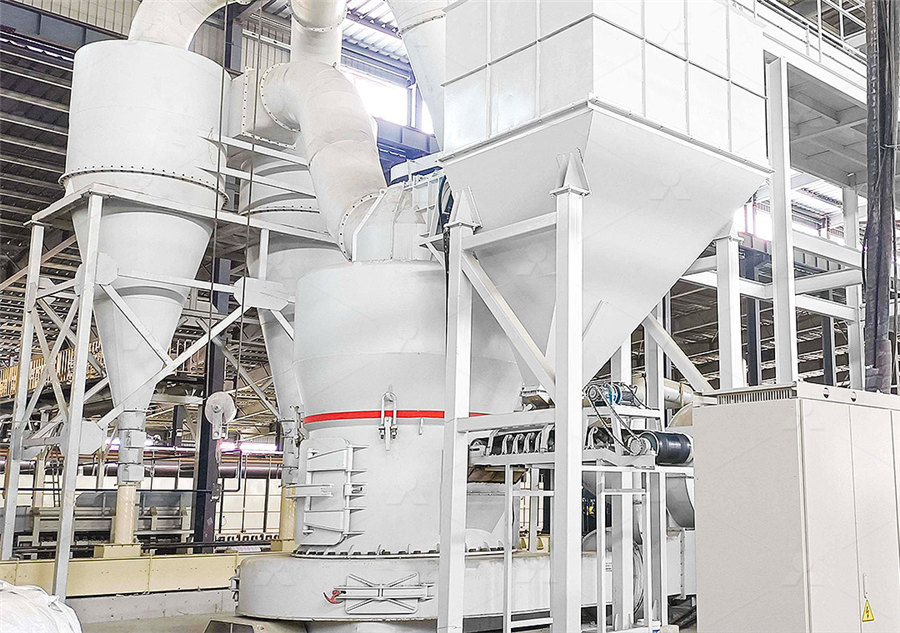
A Process for Extraction of Manganese from Manganese
2023年5月30日 The results indicated that manganese oxide ore can be reduced by alkali lignin by microwave roasting at a weight ratio of alkali lignin to ore 50% and a roasting temperature 150°C for 5 min, and under these roasting conditions, a leaching ratio of manganese of 9743% was obtained from manganese oxide ore with Mn content of 2778% using a 2024年6月20日 Methods PilotScale Sinter Pot Tests The pelletsintering process for manganese ore fines includes additional steps of raw material pretreatment and pelletizing, and it employs the technique of fuel fractionation as shown in Fig 1b First, the manganese ore fines are finely ground to − 0074mm accounted for 60% by the roll crusher (Φ200 × 125, 12 kW/h) and Study on Sintering Technology of Manganese Ore FinesThe production of highcarbon ferromanganese (HCFeMn) alloys is an energyintensive process where manganese ores are smelted in a submerged arc furnace (SAF) using carbon reductants thereby generating CO 2 emissions In the prereduction zone of the SAF, higher manganese oxides in the ore are reduced to MnO through solid–gas exothermic reactions and at a Utilization of Pretreated MnOre in a PilotScale 2021年9月12日 For the investigation of the pretreatment of manganese ores, an iterative procedure of experiments and process simulations has been applied The experiments have been conducted to extract necessary data for a more detailed simulation Static process simulations have been run using Metso Outotec’s HSC SIM toolProcess Design for the PreTreatment of Manganese Ores
.jpg)
Optimization of the synergy between reduction leaching of manganese
2019年12月6日 A new process for extracting gold from refractory gold ore and manganese from manganese anode slime was developed by combining the oxidative pretreatment of refractory gold ore and reductive leaching of manganese anode slime The response surface methodology was used to optimize the effects of time, temperature, and sulfuric acid concentration on the 2022年5月27日 Manganese is one of the most strategic metals The metal and its compounds are used extensively in metallurgy, chemistry, batteries, fertilizers, feed additives, particularly in the ferroalloy industry, for 90 percent of consumption (Mohanty et al 2018a; An et al 2021)The production of manganese ore in 2020 was 588 million tons due to higher steel production Manganese bioleaching: an emerging approach for manganese 2021年9月15日 Electrolytic manganese residue (EMR) has become a barrier to the sustainable development of the electrolytic metallic manganese (EMM) industry EMR has a great potential to harm local ecosystems and human health, due to it contains high concentrations of soluble pollutant, especially NH 4 + and Mn 2+, and also the possible dam break risk because of its A critical review on approaches for electrolytic manganese 2021年4月29日 Variations in energy efficiency and climate gas emissions in production of manganese ferroalloys are largely related to the solidstate reduction of the manganese ores used as raw material in the production The gassolid reduction is known to be dependent on the ore characteristics, making information on the factors governing the kinetics crucial A reaction Reaction Rate Analysis of Manganese Ore Prereduction in
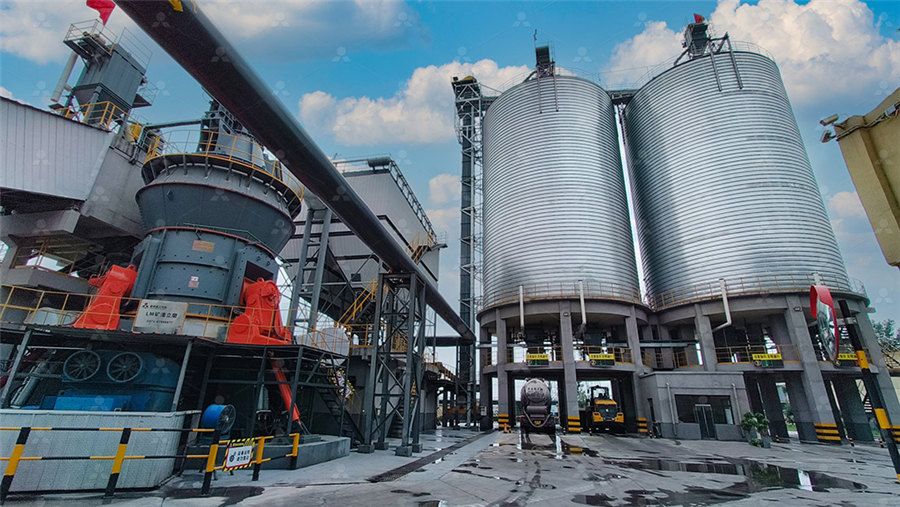
Ore Pretreatment Methods for Grinding: Journey and Prospects
2018年6月18日 ABSTRACT Pretreatment of ores to improve energy efficacy of grinding has been explored for decades However, many of these techniques are still at developmental stages and a review has been presented in this paper to discuss the research journey and problems associated with commercialization of these techniques2010年11月12日 grade manganese ore followed by magnetic separation, 60 % of phosphorus can also be removed After these tests Outotec has also continued studies into the pretreatment of different manganese ores Based on these studies, a process flowsheet for the industrialscale production of upgraded manganese ore has been developedUPGRADING OF Mn / Fe RATIO OF LOWGRADE DOI: 102139/ssrn Corpus ID: ; Pretreatment of Manganese Ore for Improved Energy Efficiency and Smelting Furnace Stability @article{Hamuyuni2021PretreatmentOM, title={Pretreatment of Manganese Ore for Improved Energy Efficiency and Smelting Furnace Stability}, author={Joseph Hamuyuni and Jarmo Saarenmaa and Pasi M{\"a}kel{\"a} and Olli Pretreatment of Manganese Ore for Improved Energy 2021年2月1日 Preheating of manganese ore alone in air Decomposition of Mn oxides in air in the range 700800°C Comparison of Mn ores behavior to preheating Prereduction campaign Prereduction of manganese ore in presence of reductant to generate CO Obtain calcined ore temperature similar to the first campaign: 700800°CPreheating manganese ore in a pilotscale rotary kiln
.jpg)
From Ore Body to High Temperature Processing of
2020年10月1日 ore layer has resulted in variable alteration to the ore, caused by meteoric fluids16,17 Ores The principal types of ores that occur in the main KMF deposit are the lowgrade, Mamatwantype ore, and the highgrade, Wesselstype ore18 Smaller concentrations of a supergene ore type occur in the southern margins of the KMD The Mamatwantype2018年7月17日 Characterization and calcination behavior of a lowgrade manganese ore, as a part of Mn ferroalloys production, was studied by XRF, exsitu XRD, insitu XRD, and SEMEDS techniquesManganese Ore Thermal Treatment Prior to SmeltingThe proposed article addresses the application of the different technologies to different ore types (oxide ore, carbonate ore and pyrolusite ore), technical advantages of each manganese ore pretreatment technology and the impact of each technology on operating and capital costManganese Ore Thermal Treatment Prior to Smelting Neliti2017年8月26日 Through acid pretreatment for cornstalk, the manganese dissolution ratio was improved from 5014% to 8346% The pre The lowgrade manganese ore used in this study was from Chaoyang, Liaoning Province, China In the ore used in the experiments, particles with a size smaller than 0074Reductive leaching of lowgrade manganese ore with
.jpg)
Energy efficient, primary production of manganese
Pretreatment of manganese ore for improved energy efficiency and smelting furnace stability by Joseph Hamuyunia, Jarmo Saarenmaaa, Pasi Mäkeläa, Olli Pekkalab, Mari Lindgrena 14 Process design for the pretreatment of manganese ores by Timur Kazdal, Richard HaasWittmuess, Sebastian Richter, Sebastian Lang, Christian Binder Markus Reuter2018年6月18日 Ore pretreatment methods for grinding: journey and prospects, Mineral Processing and Extractive Metallurgy Review, DOI: 101080/2018Ore Pretreatment Methods for Grinding: Journey and Prospects2015年2月27日 Following the concept of cement clinkering, fine manganese ore is reacted in a refractory lined countercurrent :flow horizontal rotary kiln to produce nodules in which most of the manganese is in the divalent oxidation state The process was first used in the USA and Norway for the treatment of manganese oxide ore fines and since 1968 by Partial metallisation of manganese before smelting is 2019年6月15日 Semantic Scholar extracted view of "The role of manganese ore reduction morphology development in setting reduction mechanisms" by T Coetsee Skip to search form Skip to main ore was investigated by isothermal reduction between 600 and 800 °C to optimize the conditions for industrial pretreatment of manganese ores Experiments were The role of manganese ore reduction morphology
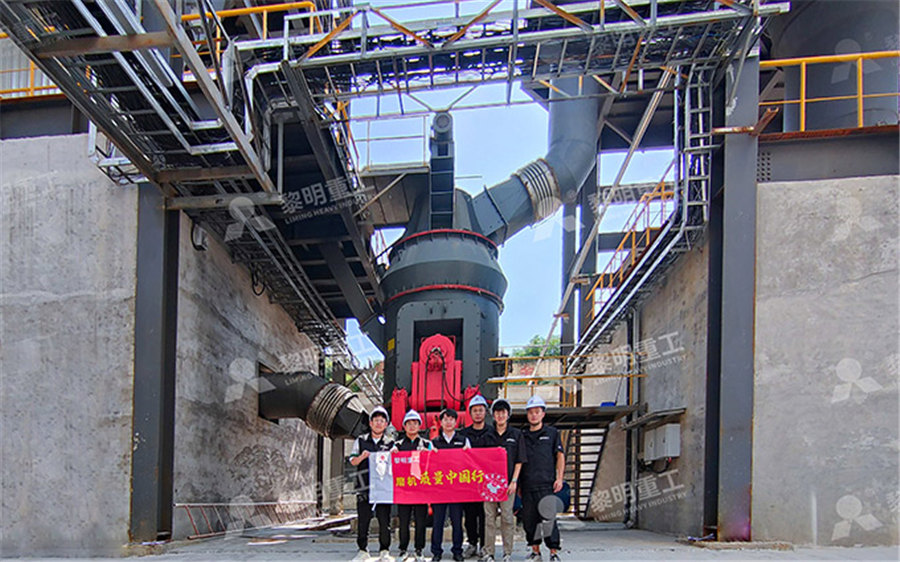
PROPERTIES OF MANGANESE ORES AND THEIR
2010年11月12日 Ferromanganese – Pretreatment For smelting The focus of this paper is on the phase composition of the ore in the temperature range 8001200°C Samples of manganese ore at UNSW were subjected to XRD, optical and electron microscope analyses XRD analysis was done using a Siemens D5000 XRay diffractometer The XRD patterns2010年11月12日 The Azul manganese mine is the largest producer of manganese ore (oxide) in Latin America, with an annual production of 25 Mt The ore produced is directed mainly to the production of ferroalloys and, Pretreatment For smelting The Twelfth International Ferroalloys Congress Sustainable Future June 6 – 9, 2010 Helsinki, Finland 451 Lump DECREPITATION OF BRAZILIAN MANGANESE LUMP ORES2019年7月29日 Manganese ore global production has consistently increased with a rapid growth rate of 1157% from 2000 to 2018 , and the annual production of manganese ore production reaches approximately 16 Mt A Review of Low Grade Manganese Ore Upgradation Processes2021年1月1日 Comilog is a high oxygen ore, where the majority of the ore is constituted by various tetravalent manganese minerals When heated in reducing atmosphere, MnO 2 oxides were reduced to MnO in a (PDF) Isothermal Reduction of Nchwaning Manganese Ore in
.jpg)
Prereduction of Nchwaning Ore in CO/CO2/H2 Gas
2021年10月28日 improving the reduction kinetics [15], it is an excellent candidate for pretreatment In this work, the reduction behavior of Nchwaning manganese ore was investigated in CO/CO2 atmospheres with and without H2, aiming to determine the optimal conditions for pretreatment While most of the previous work has been done using nonisothermal2019年9月13日 The optimum technological conditions were determined Under the condition of 85 °C, 20 min, sulfuric acid concentration of 1 mol l −1 and the ratio of two ores (Fe: Mn) of 05, the leaching rate of manganese is 8524% Gold ore is leached by noncyanide leaching after oxidation pretreatment of manganese anode slimeSynergistic effect of reduction leaching of manganese anode slime 2024年9月15日 The production of FeMn occurs in two distinct types of furnaces, categorised by the manganesetoiron mass ratio (Mn/Fe) Blast furnaces (BFs) are typically used when the ore has a Mn/Fe of 62 (Eissa et al, 2012)In 2014, global BFbased Mn ferroalloy production was a mere 05 Prereduction of Nchwaning manganese ore in CO/CO2, 2023年8月24日 to the processing and utilization of manganese oxide ores due to the large consumption of manganese carbonate ores5–7 Since MnO 2 is stable under direct acidic and alkaline conditions, the key to manganese oxide ore processing technology is to convert insoluble Mn(IV) to soluble Mn(II) in manganese oxide ore under the action of reducing agents,A Process for Extraction of Manganese from Manganese
.jpg)
MICROWAVE CALCINATION AND SINTERING OF MANGANESE CARBONATE ORE
2013年7月18日 Manganese carbonate ores are becoming an increasingly important source of manganese Usually these ores undergo thermal pretreatment which involves calcination and agglomeration using fossil fuels as the major energy source In this study, the application of microwave energy for the pretreatment step was investigated2020年11月20日 The reduction of higher manganese oxides to MnO in the prereduction zone of a ferromanganese furnace is largely decisive for the overall energy efficiency and climate gas emissions for the overall production process Kinetics of the gassolid reaction between the ore and CO(g) in the ascending furnace gas is dependent on the ore characteristics The aim of Reduction of Manganese Ores in COCO2 Atmospheres2023年5月30日 The results indicated that manganese oxide ore can be reduced by alkali lignin by microwave roasting at a weight ratio of alkali lignin to ore 50% and a roasting temperature 150°C for 5 min, and under these roasting conditions, a leaching ratio of manganese of 9743% was obtained from manganese oxide ore with Mn content of 2778% using a A Process for Extraction of Manganese from Manganese 2024年6月20日 Methods PilotScale Sinter Pot Tests The pelletsintering process for manganese ore fines includes additional steps of raw material pretreatment and pelletizing, and it employs the technique of fuel fractionation as shown in Fig 1b First, the manganese ore fines are finely ground to − 0074mm accounted for 60% by the roll crusher (Φ200 × 125, 12 kW/h) and Study on Sintering Technology of Manganese Ore Fines
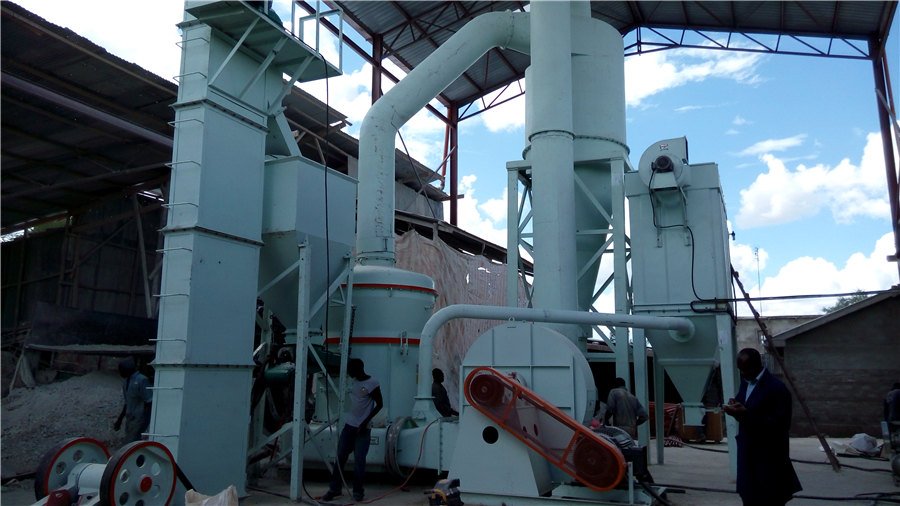
Utilization of Pretreated MnOre in a PilotScale
The production of highcarbon ferromanganese (HCFeMn) alloys is an energyintensive process where manganese ores are smelted in a submerged arc furnace (SAF) using carbon reductants thereby generating CO 2 emissions In the prereduction zone of the SAF, higher manganese oxides in the ore are reduced to MnO through solid–gas exothermic reactions and at a 2021年9月12日 For the investigation of the pretreatment of manganese ores, an iterative procedure of experiments and process simulations has been applied The experiments have been conducted to extract necessary data for a more detailed simulation Static process simulations have been run using Metso Outotec’s HSC SIM toolProcess Design for the PreTreatment of Manganese Ores2019年12月6日 A new process for extracting gold from refractory gold ore and manganese from manganese anode slime was developed by combining the oxidative pretreatment of refractory gold ore and reductive leaching of manganese anode slime The response surface methodology was used to optimize the effects of time, temperature, and sulfuric acid concentration on the Optimization of the synergy between reduction leaching of manganese 2022年5月27日 Manganese is one of the most strategic metals The metal and its compounds are used extensively in metallurgy, chemistry, batteries, fertilizers, feed additives, particularly in the ferroalloy industry, for 90 percent of consumption (Mohanty et al 2018a; An et al 2021)The production of manganese ore in 2020 was 588 million tons due to higher steel production Manganese bioleaching: an emerging approach for manganese
.jpg)
A critical review on approaches for electrolytic manganese
2021年9月15日 Electrolytic manganese residue (EMR) has become a barrier to the sustainable development of the electrolytic metallic manganese (EMM) industry EMR has a great potential to harm local ecosystems and human health, due to it contains high concentrations of soluble pollutant, especially NH 4 + and Mn 2+, and also the possible dam break risk because of its 2021年4月29日 Variations in energy efficiency and climate gas emissions in production of manganese ferroalloys are largely related to the solidstate reduction of the manganese ores used as raw material in the production The gassolid reduction is known to be dependent on the ore characteristics, making information on the factors governing the kinetics crucial A reaction Reaction Rate Analysis of Manganese Ore Prereduction in 2018年6月18日 ABSTRACT Pretreatment of ores to improve energy efficacy of grinding has been explored for decades However, many of these techniques are still at developmental stages and a review has been presented in this paper to discuss the research journey and problems associated with commercialization of these techniquesOre Pretreatment Methods for Grinding: Journey and Prospects2010年11月12日 grade manganese ore followed by magnetic separation, 60 % of phosphorus can also be removed After these tests Outotec has also continued studies into the pretreatment of different manganese ores Based on these studies, a process flowsheet for the industrialscale production of upgraded manganese ore has been developedUPGRADING OF Mn / Fe RATIO OF LOWGRADE