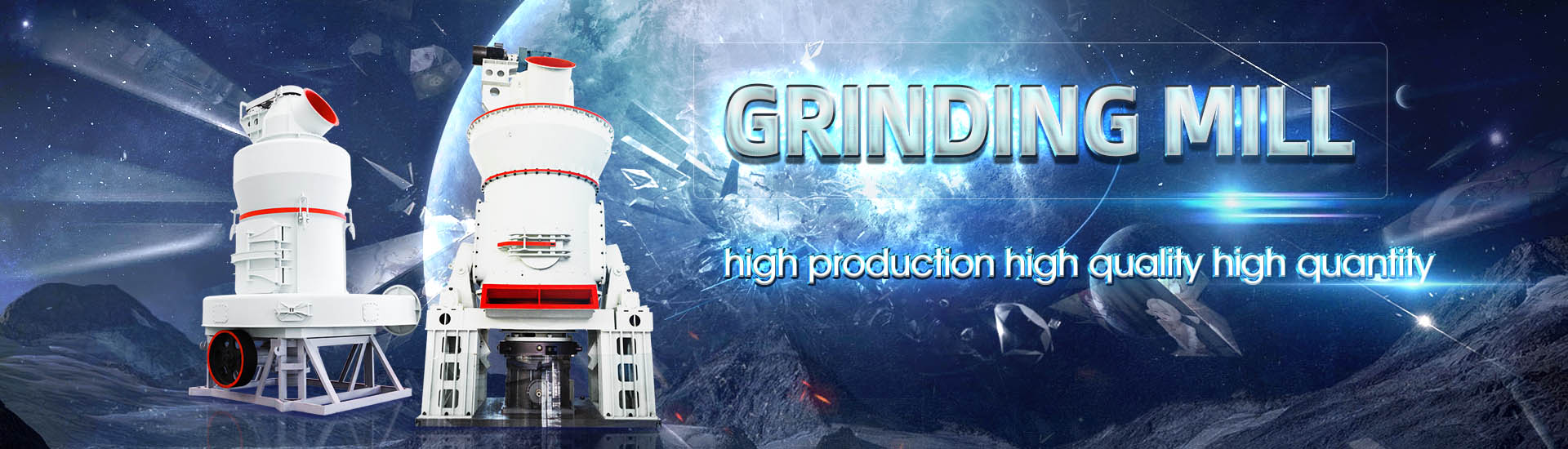
Iron Ore Crushing O limestone ration
.jpg)
Effect of Adding Limestone on the Metallurgical Properties of Iron
One of the most common fluxing materials for iron ore pellet production is limestone, which is mainly calcium oxide (CaO) In this study, the effect of adding limestone on the metallurgical 2014年10月31日 This study is concentrated on optimization of MgO (olivine) flux addition and basicity and finally used calcined lime in place of limestone in developing good quality iron ore pellets withDevelopment on Iron Ore Pelletization Using Calcined In this study, the effect of adding limestone on the metallurgical properties (reducibility, swelling, cracking, softening temperature, LowTemperature Disintegration, Cold Crushing Strength) of Effect of adding limestone on the metallurgical properties of iron This study is concentrated on optimization of MgO (olivine) flux addition and basicity and finally used calcined lime in place of limestone in developing good quality iron ore pellets with Development on Iron Ore Pelletization Using Calcined Lime and
.jpg)
Full article: Observation of the reactions between iron ore and
2021年7月16日 This work investigates the melting behaviour of iron ore with calciumbased fluxes, including lime, limestone and basic oxygen furnace (BOF) steelmaking slag With an 2023年12月1日 In this paper, the crushing process of spherical iron ore particles in a cone crusher has been numerically reproduced by DEM The effects of operation parameters Crushing characteristics and performance evaluation of iron ore in 2024年4月4日 In this study, the interaction between calcium carbonate and iron ore powder and the mineralization mechanism of fluxed iron ore pellet in the roasting process were Diffusion and reaction mechanism of limestone and quartz in 2017年3月4日 Crushing is the first step of mineral processing where the ore/rocks from the mine site is fed into the mechanical equipment in order to reduce the size of masses for subsequent usage by SIZE REDUCTION BY CRUSHING METHODS
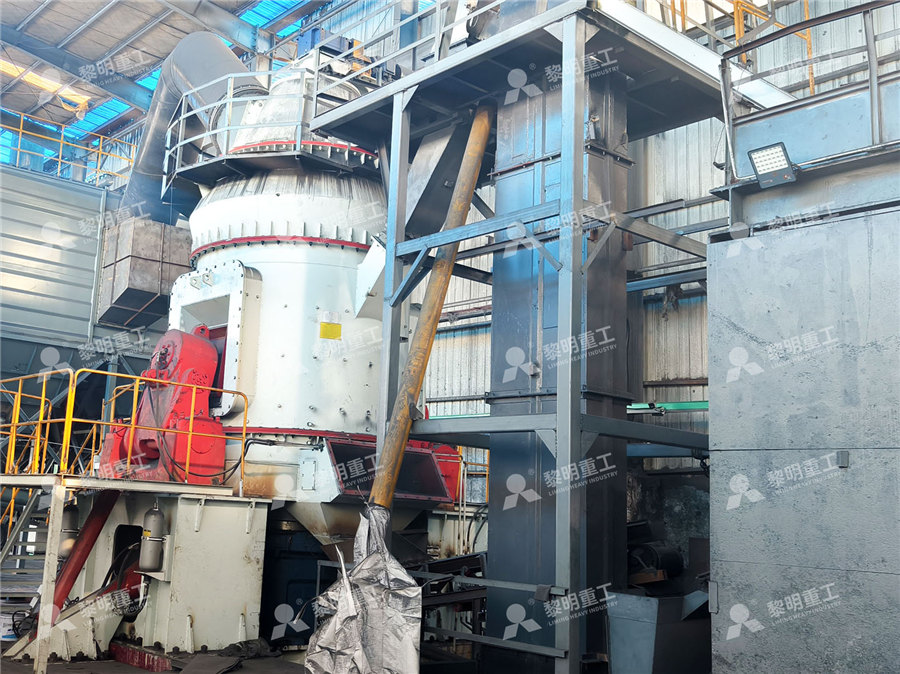
Effect of adding limestone on the metallurgical properties of iron
2015年8月10日 In this study, the effect of adding limestone on the metallurgical properties (reducibility, swelling, cracking, softening temperature, LowTemperature Disintegration, Cold 2024年4月26日 Learn about the key stages in iron ore processing, including crushing, screening, and beneficiation techniques for optimal resource utilization +86 ; xlyin@xinhaimining; Follow us; Home; In a blast Iron Ore Processing: From Extraction to Manufacturing2017年2月16日 PDF Sintering is a thermal agglomeration process that is applied to a mixture of iron ore fines, recycled ironmaking products, fluxes, slagforming Find, read and cite all the research you (PDF) Iron Ore Sintering: Process ResearchGate2015年4月3日 blasting, crushing, Hematite, Iron ore, magnetite, open pit mining, screening, underground mining, Understanding Iron Ores and Mining of Iron Ore Iron (Fe) is an abundant and a widely distributed element in the in the crust of Understanding Iron Ores and Mining of Iron Ore –
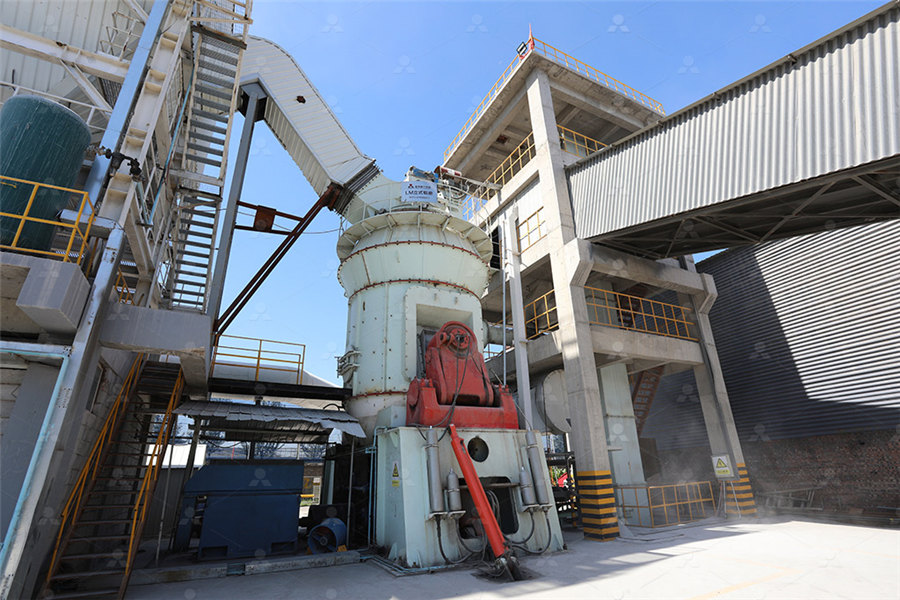
AMIT 135: Lesson 5 Crushing – Mining Mill Operator Training
Image of a “Classical” 3stage ore crushing prior to rod mill [image: (13551)] Diagram of Typical 12 stage ore crushing prior to AGSAG mill [image: (13552)] High reduction ration for amount of investment Impactor provides a high degree of fines (for ores) Can handle up to 2500 MTPH2015年8月10日 In this study, the effect of adding limestone on the metallurgical properties (reducibility, swelling, cracking, softening temperature, LowTemperature Disintegration, Cold Crushing Strength) of acid iron ore pellets was investigated using a comprehensive set of metallurgical laboratory testsEffect of adding limestone on the metallurgical properties of iron ore 2024年7月17日 Crushing is a multistage process that includes primary crushing, secondary crushing, and tertiary crushing Different types of crushing equipment are used at each stage to meet various crushing requirements Primary crushing breaks down large raw materials into mediumsized pieces for easier handling in subsequent processesTypes of Crushers: Choosing the Right One for Each Stage1 Firststage Crushing The Limestone raw material is transported to the jaw crusher by the vibrating feeder for coarse crushing 2 Secondstage Crushing Screening After coarse crushing, the Limestone enters the impact crusher for fine crushing and then uses a vibrating screen for screening operation, and the qualified materials flow into the next process, and the Limestone Aggregate Crushing JXSC Machine
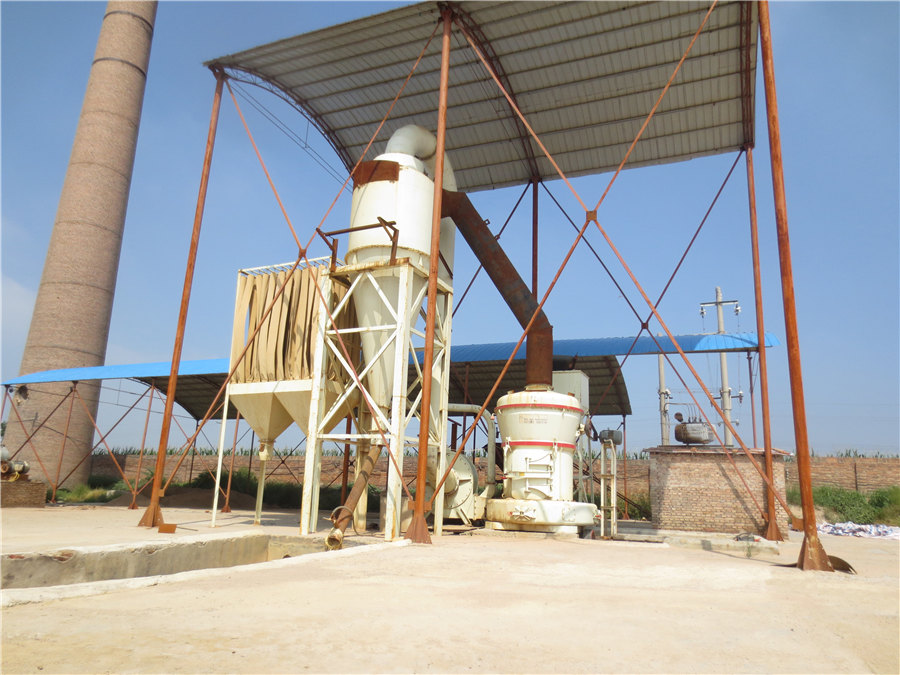
Effect of Adding Limestone on the Metallurgical Properties of Iron Ore
One of the most common fluxing materials for iron ore pellet production is limestone, which is mainly calcium oxide (CaO) In this study, the effect of adding limestone on the metallurgical properties (reducibility, swelling, cracking, softening temperature, LowTemperature Disintegration, Cold Crushing Strength) of acid iron ore pellets was2023年12月1日 Due to the decreasing reserves of highgrade iron ore and secondary resources used for steelmaking, it has become an important research and development area to improve the grade of iron ore through crushing (Gul et al, 2014)The quality of iron ore crushing directly affects the performance of pellets and sinter, so as to influence the quality and performance of Crushing characteristics and performance evaluation of iron ore 2016年3月30日 In book: Encyclopedia of Iron, Steel, and Their Alloys (pppp 10821108) Chapter: i) Direct Reduced Iron: Production; Publisher: CRC Press, Taylor and Francis Group, New York(PDF) i) Direct Reduced Iron: Production ResearchGate2013年8月1日 PDF Sintering is a process by which a mixture of iron ores, fl uxes and coke is agglomerated in a sinter plant to manufacture a sinter product of a Find, read and cite all the research you (PDF) Iron ore sintering Part 1 Theory and practice of
.jpg)
Phase and Microstructural Characterization of Iron
2016年6月20日 Phase and Microstructural Characterization of Iron Ore Pellet and Their Relation with Cold Crushing Strength TestOnce impurities are removed from the ore, the treated iron ore is mixed with limestone and coke in sintering beds These sintering beds are used to compact the iron ore, limestone, and coke materials into a solid mass Loose materials are usually compacted into a solid mass as they are heated with burnersLesson Explainer: Extracting Iron NagwaIron Ore decreased 3393 USD/MT or 2488% since the beginning of 2024, according to trading on a contract for difference (CFD) that tracks the benchmark market for this commodity Iron Ore values, historical data, forecasts and news updated on December of 2024Iron Ore Price Chart Historical Data News2024年11月4日 Carbon monoxide reduces the iron(III) oxide in the iron ore to form iron This will melt and collect at the bottom of the furnace, where it is tapped off iron(III) oxide + carbon monoxide → iron + carbon dioxide Limestone (calcium carbonate) is added to the furnace to remove impurities in the oreExtraction of iron IGCSE Chemistry Revision Notes Save My
.jpg)
SIZE REDUCTION BY CRUSHING METHODS By ResearchGate
3 Size reduction of ores is normally done in order to liberate the value minerals from the host rock This means that we must reach the liberation size, normally in the interval 100 – 10 micron 2019年11月30日 The iron ore mine also uses contractors for cleaning purposes The contractors use 40t payload Articulated Dump Trucks (ADT) 27 Quality/Grade Control At the iron ore mine, the Run of Mine (ROM) is taken through a grade control process to check if the ROM meets the product specifications in respect to the physical properties and gradeMine Planning and Optimisation Techniques Applied in an Iron Ore 2017年10月10日 Roasting or calcination of the ore oxidizes some of the sulfur, phosphorus and arsenic impurities Sulfur oxide is volatile and evaporates off or is washed out Iron is mainly extracted from hematite (Fe 2 O 3) and magnetite ores Natural or direct shipping iron ores contain between 5070% iron and can be fed directly into the blast furnace Fe Ironmaking 101 – From Ore to Iron with Blast Furnaces2022年1月1日 Hematite and magnetite, the two predominant iron ores, require different processing routes Highgrade hematite direct shipping ores generally only require crushing and screening to meet the size requirements of lump (typically between 6 and 30 mm) and fines (typically less than 6 mm) minution and classification technologies of iron ore
.jpg)
Crushing in Mineral Processing 911Metallurgist
2015年12月26日 In mineral processing or metallurgy, the first stage of comminution is crushing Depending of the type of rock (geometallurgy) to be crushed, there are 2 largely different techniques at your disposition for crushing rocks In principle, compression crushing is used on hard and abrasive rocks by placing them between a high wearresistant plate/surface2018年3月1日 The ratio for iron ore, coking coal and limestone required in the manufacture for steel is 4:2:1 Explanation: Steelmaking is an important metallurgical process; Steel is the basic requirement in the century; The ratio of iron ore is required as the basic material, 2 Part of coking coal is required for reducing the oxide layer present on the oreIn what ratio are iron ore, coking coal and limestone Brainly2023年12月19日 The principal iron ores contain hematite (Fe 2 O 3) and magnetite (Fe 3 O 4) Hematite is an iron oxide mineral It is nonmagnetic and has colour variations ranging from steel silver to reddish brown Pure hematite Iron Ore Geoscience AustraliaThe most important iron oreforming minerals are: • Magnetite Magnetite (Fe3O4) forms magnetic black iron ore There are large deposits of magnetite in Russia and Sweden • Hematite Hematite (Fe2O3) is a red iron ore Hematite occurs in almost all forms, from solid rock to loose earth It is the most plentiful iron ore and occurs in Energy and Environmental Profile of the US Mining Industry 4
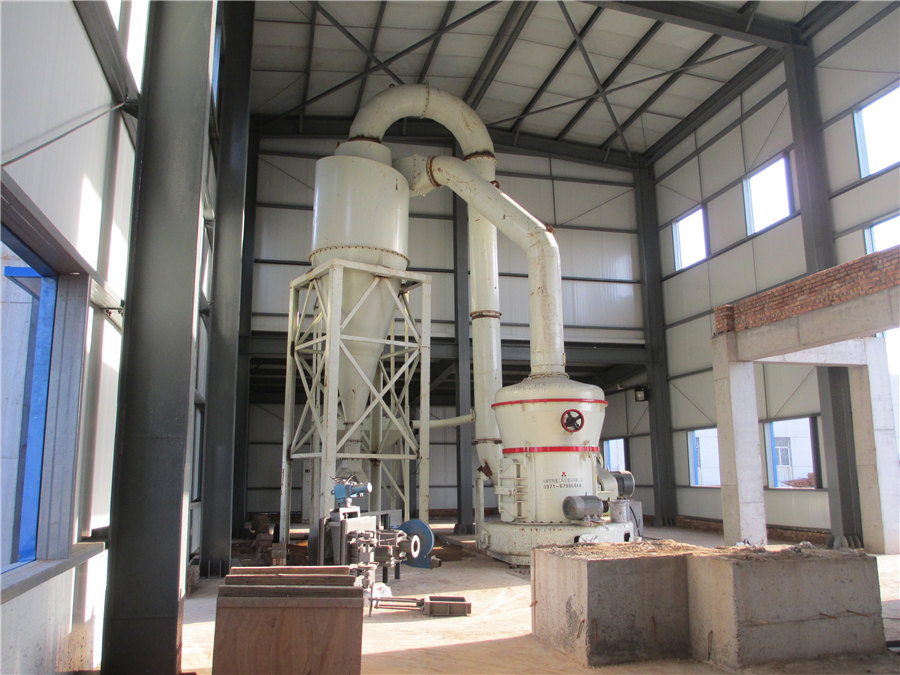
Jaw Crusher ScienceDirect
2016年1月1日 In some industries, for example, iron ore or coal, where a specific product size is for comparison and applies for the crushing conditions of uniform full capacity feeding of dry thick bedded mediumhard limestone where K = 1 prior to crushing The ore is to be broken down in a jaw crusher to pass through a 115 cm 2021年1月1日 Currently, approximately 14 billion tons per year of iron ore tailing wastes (IOT) are generated, mainly in Australia, Brazil, and China This work describes the characterization and application Iron Ore Tailings: Characterization and Applications2021年2月1日 Owing to the depletion of highgrade iron ore quality, many steel plants over the world are now using pellets after beneficiation of low grade ores as blast furnace feed For the effective utilization of lowgrade iron ore resources (59–62% Fe) with high loss of ignition (LOI), mineralogical characteristics play the vital role to improve the process efficiencyEffect of limestone and dolomite flux on the quality of pellets 2021年1月15日 In the sintering of iron ores, the partial substitution of anthracite for coke breeze has been considered to be an effective way of reducing pollutant emissions and production cost In this study Partial substitution of anthracite for coke breeze in iron ore
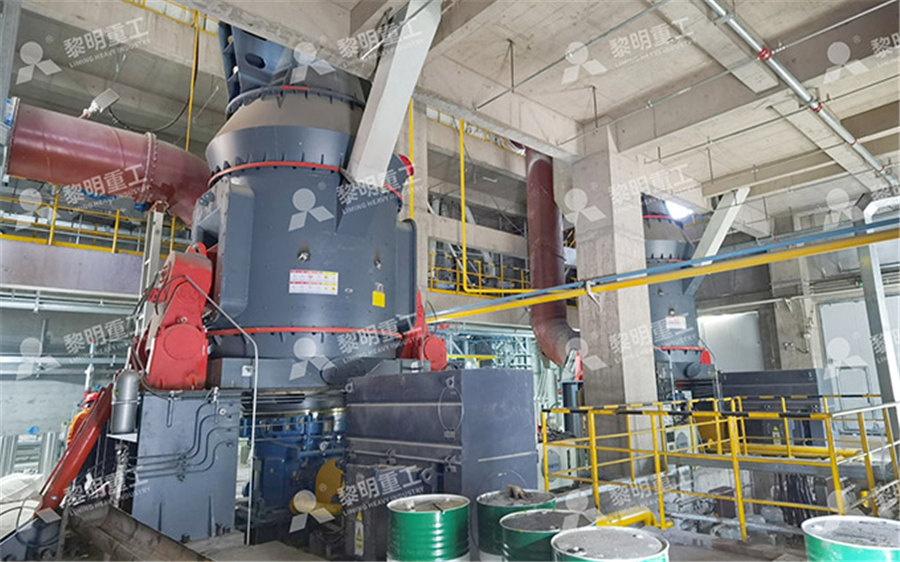
Iron Ore Pelletizing Process: An Overview ResearchGate
PDF On Jul 11, 2018, Sandra Lúcia de Moraes and others published Iron Ore Pelletizing Process: An Overview Find, read and cite all the research you need on ResearchGate2023年1月15日 Moreover, the conventional iron making unit, ie blast furnace requires the raw material in the form of iron oxide with a size range of 10–120 mm Sintering is the oldest agglomerate thermal process using iron ore mineral fines of 05–8 mm, along with the reductant, fluxes, and other byproducts of the iron and steel industry operated around a temperature of Reductants in iron ore sintering: A critical review ScienceDirectPDF On Oct 1, 2021, Chun Feng and others published Numerical Study on Crushing Law of Iron Ore under Different Impact Velocity Using CDEM Find, read and cite all the research you need on Numerical Study on Crushing Law of Iron Ore under Different 2024年4月26日 Learn about the key stages in iron ore processing, including crushing, screening, and beneficiation techniques for optimal resource utilization +86 ; xlyin@xinhaimining; Follow us; Home; In a blast Iron Ore Processing: From Extraction to Manufacturing
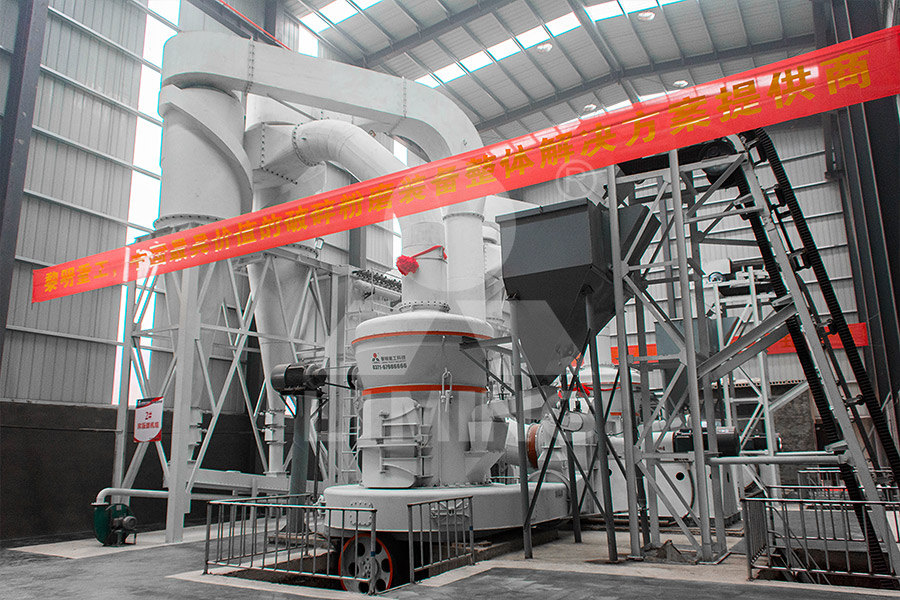
(PDF) Iron Ore Sintering: Process ResearchGate
2017年2月16日 PDF Sintering is a thermal agglomeration process that is applied to a mixture of iron ore fines, recycled ironmaking products, fluxes, slagforming Find, read and cite all the research you 2015年4月3日 blasting, crushing, Hematite, Iron ore, magnetite, open pit mining, screening, underground mining, Understanding Iron Ores and Mining of Iron Ore Iron (Fe) is an abundant and a widely distributed element in the in the crust of Understanding Iron Ores and Mining of Iron Ore – Image of a “Classical” 3stage ore crushing prior to rod mill [image: (13551)] Diagram of Typical 12 stage ore crushing prior to AGSAG mill [image: (13552)] High reduction ration for amount of investment Impactor provides a high degree of fines (for ores) Can handle up to 2500 MTPHAMIT 135: Lesson 5 Crushing – Mining Mill Operator Training2015年8月10日 In this study, the effect of adding limestone on the metallurgical properties (reducibility, swelling, cracking, softening temperature, LowTemperature Disintegration, Cold Crushing Strength) of acid iron ore pellets was investigated using a comprehensive set of metallurgical laboratory testsEffect of adding limestone on the metallurgical properties of iron ore
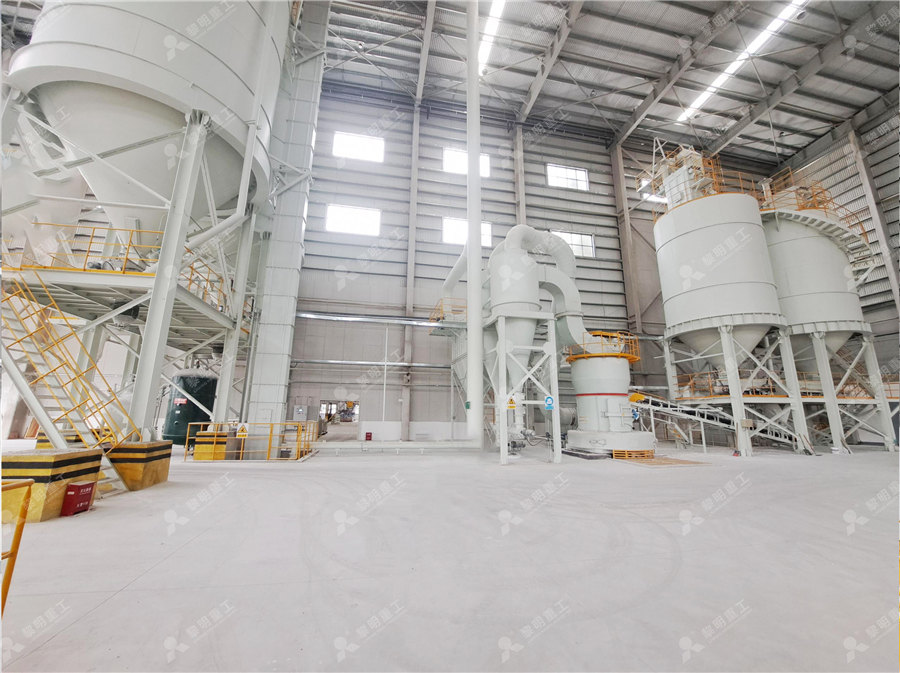
Types of Crushers: Choosing the Right One for Each Stage
2024年7月17日 Crushing is a multistage process that includes primary crushing, secondary crushing, and tertiary crushing Different types of crushing equipment are used at each stage to meet various crushing requirements Primary crushing breaks down large raw materials into mediumsized pieces for easier handling in subsequent processes1 Firststage Crushing The Limestone raw material is transported to the jaw crusher by the vibrating feeder for coarse crushing 2 Secondstage Crushing Screening After coarse crushing, the Limestone enters the impact crusher for fine crushing and then uses a vibrating screen for screening operation, and the qualified materials flow into the next process, and the Limestone Aggregate Crushing JXSC MachineOne of the most common fluxing materials for iron ore pellet production is limestone, which is mainly calcium oxide (CaO) In this study, the effect of adding limestone on the metallurgical properties (reducibility, swelling, cracking, softening temperature, LowTemperature Disintegration, Cold Crushing Strength) of acid iron ore pellets wasEffect of Adding Limestone on the Metallurgical Properties of Iron Ore 2023年12月1日 Due to the decreasing reserves of highgrade iron ore and secondary resources used for steelmaking, it has become an important research and development area to improve the grade of iron ore through crushing (Gul et al, 2014)The quality of iron ore crushing directly affects the performance of pellets and sinter, so as to influence the quality and performance of Crushing characteristics and performance evaluation of iron ore
制粉-10.25公众号.jpg)
(PDF) i) Direct Reduced Iron: Production ResearchGate
2016年3月30日 In book: Encyclopedia of Iron, Steel, and Their Alloys (pppp 10821108) Chapter: i) Direct Reduced Iron: Production; Publisher: CRC Press, Taylor and Francis Group, New York