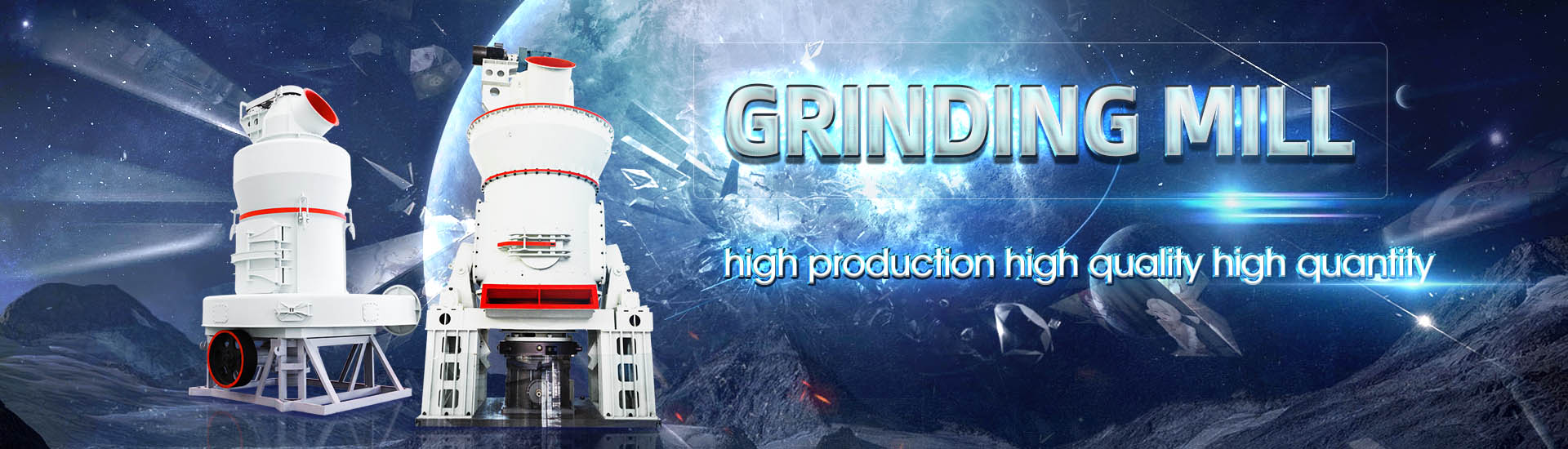
Simulation of mechanical loads for barite grinding
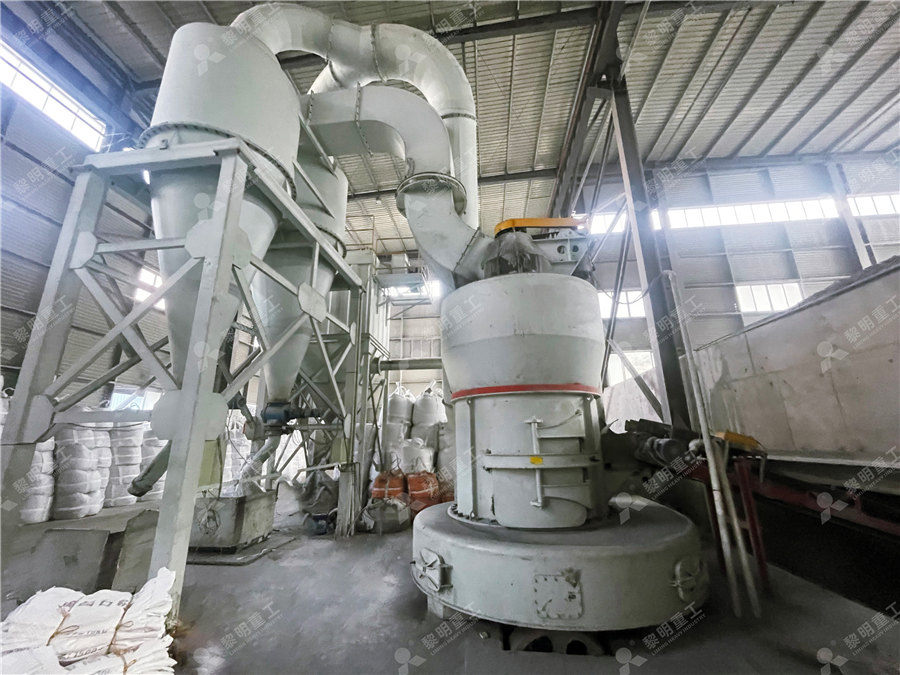
Advances in Modeling and Simulation of Grinding Processes
2006年1月1日 This keynote paper results from a collaborative work within the STC G and gives an overview of the current state of the art in modeling and simulation of grinding processes: 1992年1月1日 Makin uses his grinding energy model to simulate a peripheral plunge grinding process Due to mechanical, geomemc and thermal aspects, as well as due to the wear of the Modelling and Simulation of Grinding Processes ScienceDirect2023年1月22日 4 Analysis of thermomechanical loads In grinding, the heat developed during the machining process is a major challenge due to the small chip space, a large number of Potentials of grinding process simulations for the analysis of 2014年7月20日 We present recent developments in modelling and simulation of internal traverse grinding, a high speed machining process which enables both a large material removal rate (PDF) A Hybrid Approach to the Modelling and Simulation of
.jpg)
Mechanical behavior and modeling of grinding force: A
2023年9月29日 The force model, which plays a significant role for the application of grinding in various fields, is the most straight forward and comprehensive mathematical expression to 2022年1月13日 In this research, a comprehensive model was used to analyze and predict the grinding forces both under dry conditions and in the presence of grinding fluid In this research, Analytical simulation of grinding forces based on the micro We present recent advances in the modelling and simulation of Internal Traverse Grinding, a high performance grinding process incorporating a high rate of material removal combined with a A HYBRID APPROACH TO THE MODELLING AND SIMULATION OF 2014年1月22日 The grinding process can be optimized by means of a simulative prediction of the occurring forces In this paper, a geometrickinematic simulation coupled with a finite Simulation of grinding processes using finite element analysis and
.jpg)
Potentials of grinding process simulations for the analysis of
macroscopic model approaches can be used to estimate the thermomechanical loads occurring in the contact zone, explicit modeling of the individual abrasive grains is required to2008年11月15日 This article presents an overview of current simulation methods describing the interaction of grinding process and grinding machine structure, eg, vibrations, deflections, or Modelling and simulation of process: machine interaction in grindingFor the third component of the simulation framework, namely a finite element model on the macroscale, the load compound from the preceding steps is applied as boundary condition in terms of a moving heat source in combination with a distributed mechanical surface load Apart from this thermomechanical load compound, the exact tool and theModelling and simulation of Internal Traverse Grinding: bridging 2022年10月1日 Grinding is one of the most widely used material removal methods at the end of many process chains Grinding force is related to almost all grinding parameters, which has a great influence on (PDF) Modelling of grinding mechanics: A review
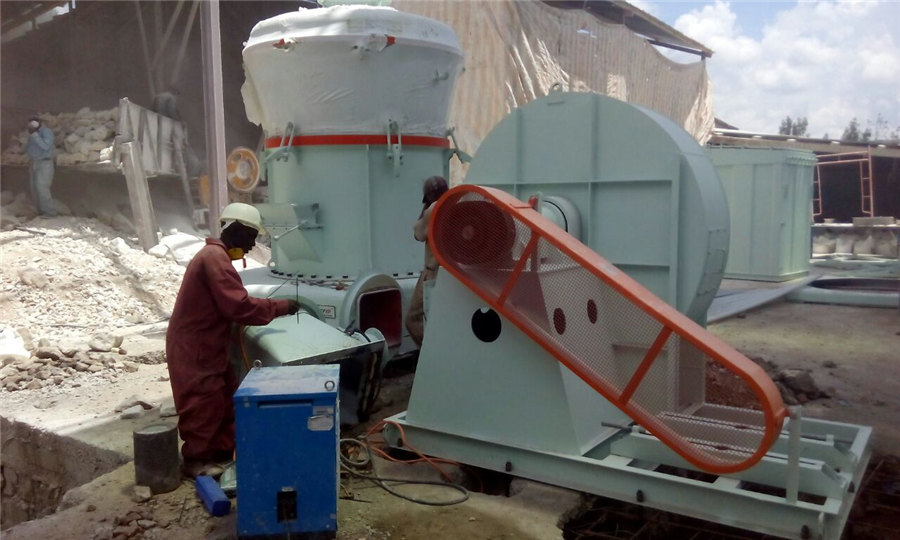
Investigation of Mechanical Loads Distribution for the
In grinding, interaction between the workpiece material and rotating abrasive tool generates high thermomechanical loads in the contact zone If these loads reach critically high values, workpiece material properties deteriorate To prevent the Numerical Simulation of Force Distributions in the Grinding Contact Zone M Srinivasaraghavan1, Z Shi2, H Attia1, 2,* and V Thomson1 1McGill University, Department of Mechanical Engineering 2 Numerical Simulation of Force Distributions in the Grinding A model for numerical simulation of grinding is presented taking into account both thermal, mechanical and metallurgical aspects ABSTRACT: Key words: Grinding, residual stresses, finite element analysis 1 INTRODUCTION 2 GRINDING MODELING The grinding process consists of an abrasive contact between a moving workpiece and a wheel in rotation [1]Residual Stresses prediction with a new Thermo Mechanical simulation of 2021年2月6日 The micro singlelip deep hole drilling process is subjected to many difficulties Especially the machining of difficulttocut materials like the nickelbased alloy Inconel 718 results in high thermal and mechanical loads Irregularities in the drilling process, which lead to early tool failures must be avoided A major challenge for micro singlelip deep hole drilling is to generate Chip formation simulation and analysis of the mechanical loads

Modelling and simulation of the grinding process ResearchGate
PDF On Nov 1, 2008, Alexandre Brosse and others published Modelling and simulation of the grinding process Find, read and cite all the research you need on ResearchGate2006年1月1日 In the last decade the relevance of modeling and simulation of grinding processes has significantly risen which is caused by industrial needs and is indicated by the number of publications and Proceeding of the Institution of Mechanical Engineers/B, Journal of Engineering Manufacture, 218 (10) (2004), pp 13391356 View in Advances in Modeling and Simulation of Grinding Processes1992年1月1日 Aeynore raper Modelling and Simulation of Grinding Processes H K Tonshoff (l), J Peters (1) I lnasaki (l), T Paul Abstract This paper describes the stateoftheart in the modelling and simulation of grinding processes The kinematics of the grinding process are characterised by a series of statistically irregular and separate engagementsModelling and Simulation of Grinding Processes ScienceDirect2014年7月20日 During grinding processes, numerous grains interact with the workpiece material producing mechanical and thermal loads on the surface In the field of thermal simulation of grinding processes, a (PDF) A Hybrid Approach to the Modelling and Simulation of Grinding
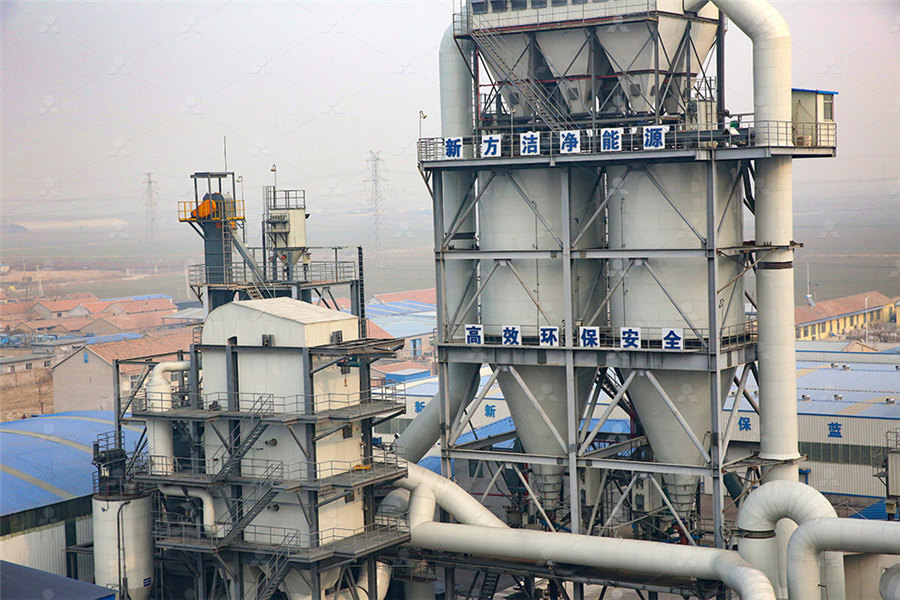
Residual stresses in gear form grinding by considering carburizing
2024年2月29日 The residual stresses of the grinding surface exert a significant effect on the strength, fatigue life and corrosion resistance of gears To investigate the variations and distributions of grindinginduced residual stresses, a novel multiphysics coupling numerical simulation model in gear form grinding was developed Compared with traditional calculation 2021年10月2日 The present study is directed to the temperature and residual stress fields in the hardfacing remanufacturing for a largescale grinding roller with damage For this purpose, a numerical procedure for the hardfacing process based on the thermal cycle curve method was established, and the effectiveness of the proposed procedure was verified by the Numerical simulation of hardfacing remanufacturing for large 2024年9月12日 Friction and wear test equipment, scanning electron microscope, abrasion balls made of CGr15 high carbon chromium bearing steel, and liners made of NM500 steel were used for wear simulation and friction–wear experiments The variation trends of friction coefficient, wear amount, and subsurface characteristics under dry friction and slurry conditions were studied Friction and wear characteristics and simulation study of NM500 June 2022; ARCHIVE Proceedings of the Institution of Mechanical Engineers Part C Journal of Mechanical Engineering Science 19891996 (vols 203210) 236(2):1107(PDF) A comprehensive review on the grinding process:
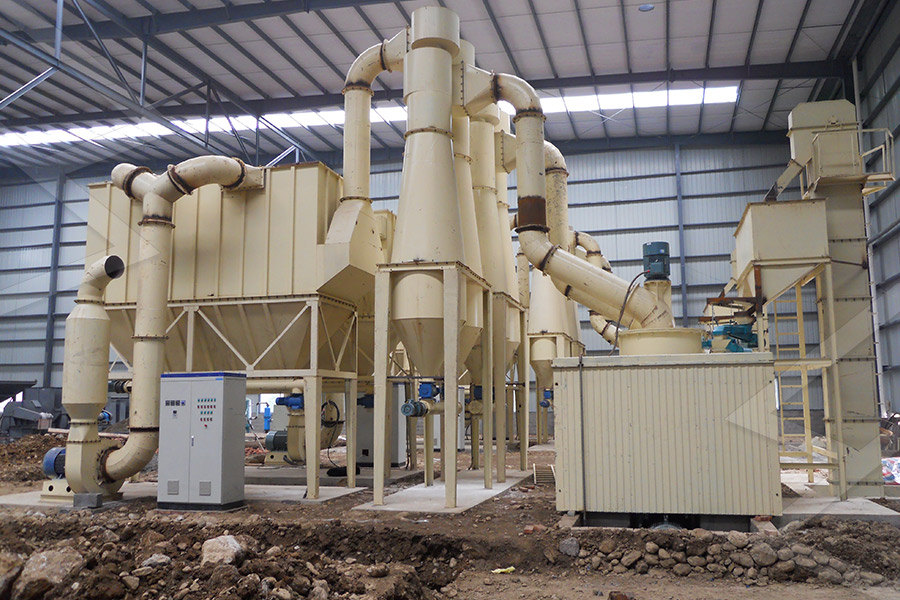
Analysis of loads on grinding wheel binder in grinding process
2015年1月21日 The load on grinding wheel (GW) binder in grinding process is an important issue in grinding studies It affects binder behaviors, wheelworkpiece interaction, grinding force, heat and energy, machined surface quality, GW life, etc However, few studies have systematically studied this topic and the conclusions proposed so far have been established and * = +, *; roughness = 、 = ' ' ′ ( ) ( ),, = = = = = Forming mechanisms based simulation and prediction of grinding 2021年2月6日 Chip formation simulation and analysis of the mechanical loads during micro singlelip deep hole drilling of Inconel 718 with varying cooling lubricant pressure February 2021 Production (PDF) Chip formation simulation and analysis of the mechanical loads 2001年12月1日 The mechanicalplastic deformation effect and the thermalplastic deformation effect could take place simultaneously during grinding metallic materials (ie, steels, titanium alloys, and nickel Simulation of thermal stresses due to grinding Request PDF
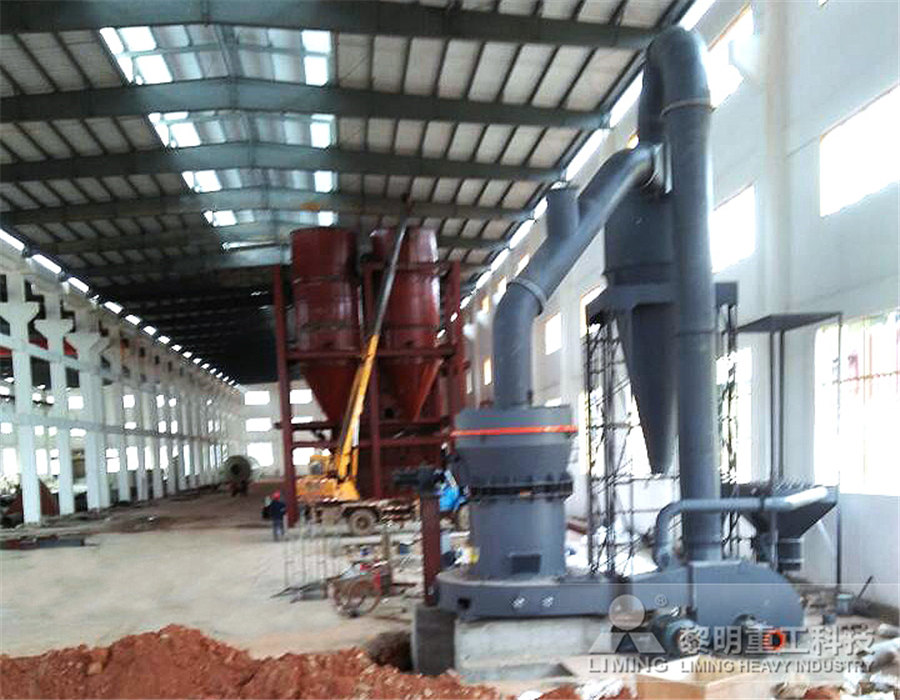
Modelling and simulation of Internal Traverse Grinding: bridging
2015年4月29日 In this work, we focus on the computational bridging between the meso and macroscale in the context of the hybrid modelling of Internal Traverse Grinding with electroplated cBN wheels This grinding process satisfies the manufacturing industry demands for a high rate of material removal along with a high surface quality while minimising the number of 2002年11月1日 shows the initial grinding results of calcite mineral plotted in firstorder form for varying feed size fractions of À 850 + 600, À 600 + 425, À 425 + 300, À 300 + 212 AmKinetics of dry grinding of industrial minerals: Calcite and barite2024年5月4日 Walking is one of the main activities of daily life and gait analysis can provide crucial data for the computation of biomechanics in many fields In multiple applications, having reference data that include a variety of gait Biomechanical Analysis of Human Gait When Changing 2020年9月15日 A new heat transfer model for profile grinding was developed to analyze distortions caused by residual tensile stresses in linear guide rails The simulative analysis of the thermal effects caused by a nonuniform heat 3D modeling and simulation of thermal effects during
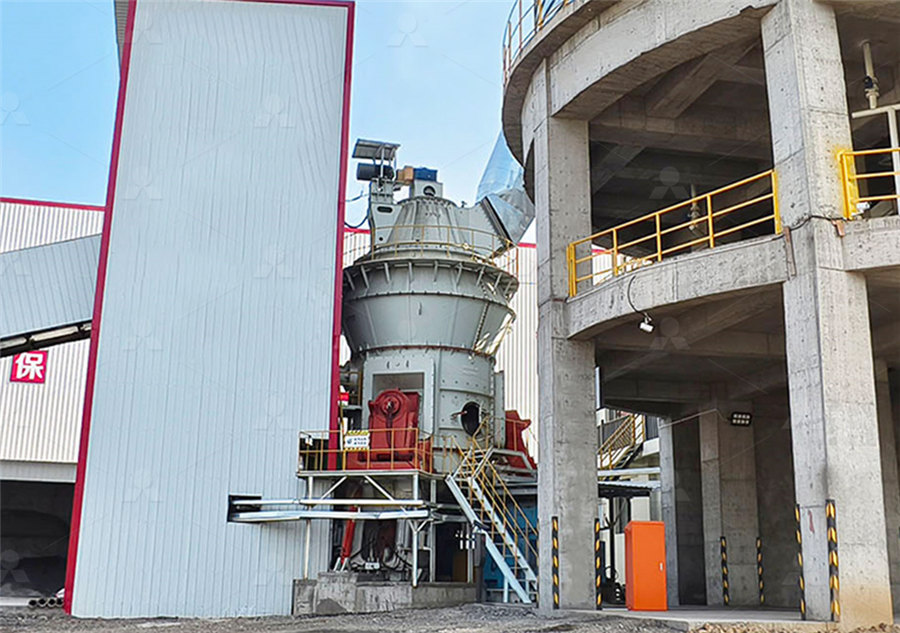
Peridynamic simulation of the mechanical responses and
2022年1月13日 Note that \(\mathrm{\Delta x}\) is the material point spacing The influences of different microelastic moduli on the macroscopic mechanical responses, peak strength and fracturing behaviors of rock samples obtained by the proposed method will be discussed in Sect 5 23 Failure criteria The previous work [] discussed the composite failure criterion based on 2016年6月29日 Nowadays, the modeling and simulation of grinding have become powerful tools in predicting the process performance and work results However, common simulations focus on material removal process of abrasive grains and neglect deformations of machine structure The grinding quality can be influenced by various factors, of which the processmachine interaction Simulation of grinding process for cemented carbide based on 2024年5月31日 Ultrasonic vibrationassisted grinding (UVAG) enhances surface integrity in machined parts, especially in achieving greater compressive residual stress Typically, the calculation of residual stresses in UVAG relies on generic finite element software that is not optimized for this purpose, suffering from cumbersome modeling and inefficient calculations Calculation of residual stress in ultrasonic vibration assisted 2016年6月1日 All the 66 mechanical cells were replaced by 6 flotation columns (30 m × 45 m × 145m), resulting in improved selectivity and recovery and significant reductions in the consumption of the Flotation and Grinding for Beneficiation of Barite ore from China
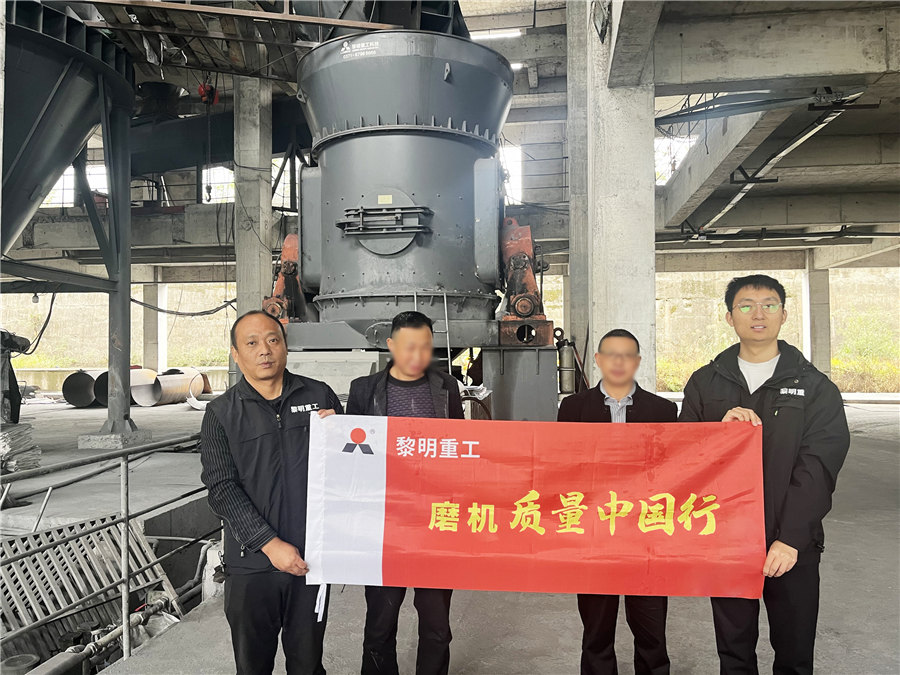
Dynamic Emulation of Mechanical Loads ResearchGate
Dynamic emulation of mechanical loads presents a modern and interesting approach for testing and validating performance of electrical drives without a real mechanical load included in the test rig2022年1月13日 The grinding process is one of the most important and widely used machining processes to achieve the desired surface quality and dimensional accuracy Due to the stochastic nature of the grinding process and process conditions, the instantaneous micromechanisms between each grain and the workpiece are momentarily changing and are different from the Analytical simulation of grinding forces based on the micro 2021年6月21日 Based on threedimensional simulation software DEFORM3D, the simulation model of high speed cylindrical grinding with single grit was established, and the relevant experiment of 3D simulation for Real single grain grinding FEM simulation for case2020年1月1日 Initially carried out experimental research on the surface roughness of rail belt 5th CIRP CSI 2020 Forming mechanisms based simulation and prediction of grinding surface roughness for abrasive belt rail grinding Chaoyue ZHAOa, Jianyong LIa,c, Wenxi WANGa,b* a School of Mechanical, Electronic and Control Engineering, Beijing Jiaotong University, Beijing Forming mechanisms based simulation and prediction of grinding
.jpg)
Modelling and simulation of Internal Traverse Grinding: bridging
For the third component of the simulation framework, namely a finite element model on the macroscale, the load compound from the preceding steps is applied as boundary condition in terms of a moving heat source in combination with a distributed mechanical surface load Apart from this thermomechanical load compound, the exact tool and the2022年10月1日 Grinding is one of the most widely used material removal methods at the end of many process chains Grinding force is related to almost all grinding parameters, which has a great influence on (PDF) Modelling of grinding mechanics: A reviewIn grinding, interaction between the workpiece material and rotating abrasive tool generates high thermomechanical loads in the contact zone If these loads reach critically high values, workpiece material properties deteriorate To prevent the Investigation of Mechanical Loads Distribution for the Numerical Simulation of Force Distributions in the Grinding Contact Zone M Srinivasaraghavan1, Z Shi2, H Attia1, 2,* and V Thomson1 1McGill University, Department of Mechanical Engineering 2 Numerical Simulation of Force Distributions in the Grinding
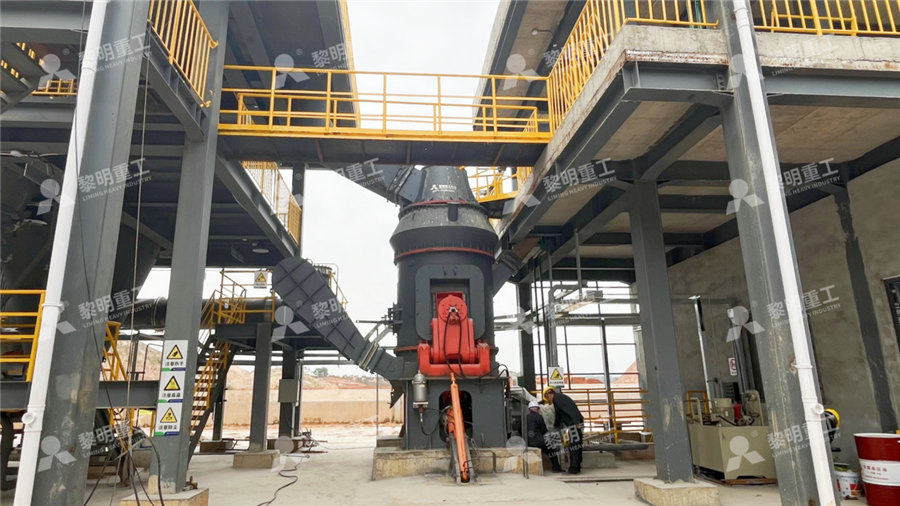
Residual Stresses prediction with a new Thermo Mechanical simulation of
A model for numerical simulation of grinding is presented taking into account both thermal, mechanical and metallurgical aspects ABSTRACT: Key words: Grinding, residual stresses, finite element analysis 1 INTRODUCTION 2 GRINDING MODELING The grinding process consists of an abrasive contact between a moving workpiece and a wheel in rotation [1]2021年2月6日 The micro singlelip deep hole drilling process is subjected to many difficulties Especially the machining of difficulttocut materials like the nickelbased alloy Inconel 718 results in high thermal and mechanical loads Irregularities in the drilling process, which lead to early tool failures must be avoided A major challenge for micro singlelip deep hole drilling is to generate Chip formation simulation and analysis of the mechanical loads PDF On Nov 1, 2008, Alexandre Brosse and others published Modelling and simulation of the grinding process Find, read and cite all the research you need on ResearchGateModelling and simulation of the grinding process ResearchGate2006年1月1日 In the last decade the relevance of modeling and simulation of grinding processes has significantly risen which is caused by industrial needs and is indicated by the number of publications and Proceeding of the Institution of Mechanical Engineers/B, Journal of Engineering Manufacture, 218 (10) (2004), pp 13391356 View in Advances in Modeling and Simulation of Grinding Processes
.jpg)
Modelling and Simulation of Grinding Processes ScienceDirect
1992年1月1日 Aeynore raper Modelling and Simulation of Grinding Processes H K Tonshoff (l), J Peters (1) I lnasaki (l), T Paul Abstract This paper describes the stateoftheart in the modelling and simulation of grinding processes The kinematics of the grinding process are characterised by a series of statistically irregular and separate engagements2014年7月20日 During grinding processes, numerous grains interact with the workpiece material producing mechanical and thermal loads on the surface In the field of thermal simulation of grinding processes, a (PDF) A Hybrid Approach to the Modelling and Simulation of Grinding