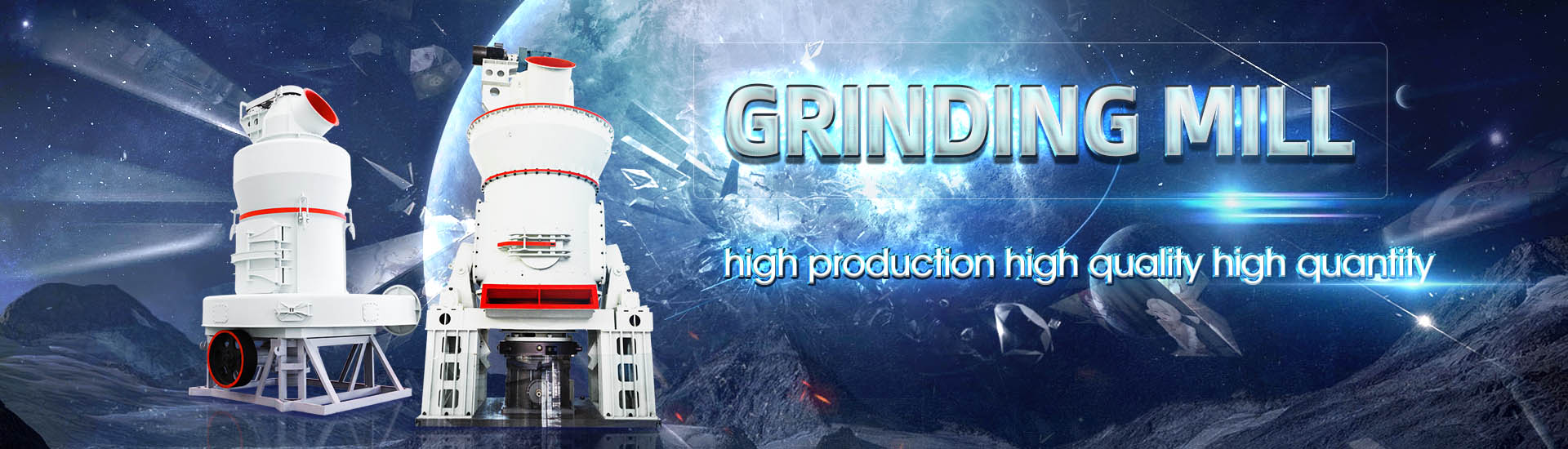
Pulverized coal injection tank Pulverized coal injection tank Pulverized coal injection tank
.jpg)
Pulverized Coal Injection Tank Pressure Control Using Fuzzy Based
Lyapunovbased model reference adaptive controller is implemented in a pulverized coal injection tank pressure control system at a PCI facility, which is critical for energy consumption in2022年5月1日 Pulverized coal injection (PCI) is generally used in modern blast furnace (BFs) ironmaking to reduce coke consumption by burning cheaper coal This paper presents a Optimization of pulverized coal injection (PCI) rate in an The pulverized coal injection technology is based on a combination of several unit operations Main unit operations include: Hot blast backpressure as well as pressure drops in pneumatic Pulverized Coal Injection Paul WurthAbstract This article describes new advanced nonlinear dynamic models for a pulverized coal injection (PCI) plant into blast furnaces A complete new approach for modelling is developed Advanced Dynamic Models for a Pulverized Coal Injection Plant
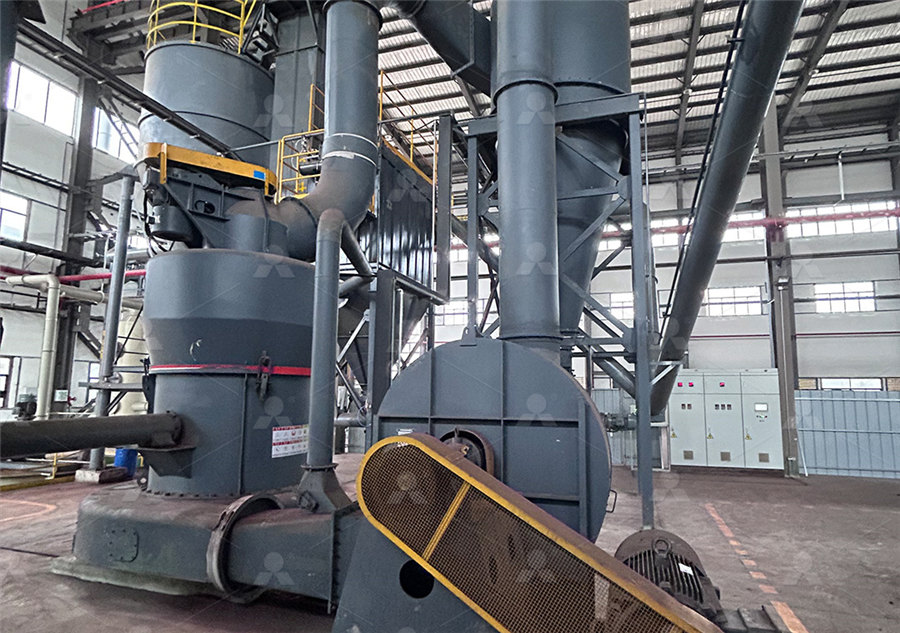
Technological advancements in evaluating the
2020年9月11日 The pulverized coal injection (PCI) is pursued to reduce the hot metal production cost by replacing the expensive metallurgical coke with the noncoking coal Increasing the PCI2024年1月15日 The application of hydrogenrich gas in the pulverized coal injection technology represents a precious solution to mitigate carbon emissions In this research, a three Numerical investigation of hydrogenrich gas and pulverized coal 2024年1月1日 Pulverized coal for blast furnace injection requires high combustibility, reducing the content of unburned pulverized coal in the furnace, improving the coal coke displacement Pulverized Coal Injection of Blast Furnace Ironmaking2024年6月3日 In this study, a discrete phase model is used to describe the complex flow and thermochemical behavior associated with the coinjection of hydrogen and pulverized coal in Numerical Simulation Study of Coinjection of Pulverized Coal and
.jpg)
Analysis of the combined injection of pulverized coal and charcoal
2013年10月1日 The simultaneous injection of pulverized coal and charcoal in the blast furnace has recently received remarkable attention due to its potential to decrease the coke 2011年3月17日 In order to understand the complicated phenomena of pulverized coal injection (PCI) process in blast furnace (BF), several mathematical models have been developed by the CFD Modelling and Analysis of Pulverized Coal Injection in Blast pulverized coal injection ft ft fc fy fc fy wt pc wt pc pc wt wt fs fc fs fy ft ft ft wt fc fy fc fy fc fc fc wt wt fc fy ft 6 unit operations of pulverized coal injection pressurizing gas vessel nitrogen global flow rate closed loop control conveying hoppers static distributor injection lines pulverized coal tuyeres conveying line closed loop Pulverized Coal Injection Paul Wurth1996年4月10日 New pulverized coalfired systems routinelyinstalled today generate power at net thermal cycle efficienciesranging from 34 to 37% (higher heating value) while removingup to 97% of the combined Developments in Pulverized CoalFired Boiler
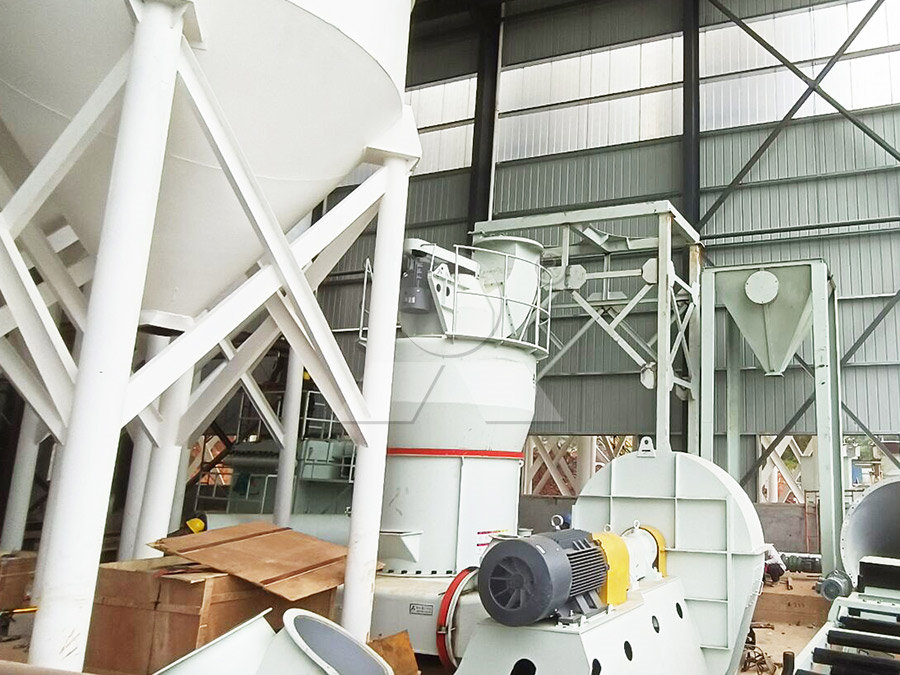
Numerical Simulation Study of Coinjection of Pulverized Coal
2024年6月3日 Hydrogen can replace partially pulverized coal in the blast furnace injection as the clean and highcalorific energy, which can reduce energy consumption and carbon emission in molten iron production In this study, a discrete phase model is used to describe the complex flow and thermochemical behavior associated with the coinjection of hydrogen and pulverized coal 161 Pulverized coal combustion In pulverized coal combustion (PCC), dust burners are used to feed coal into the combustion chamber, where flame core zones of the combustion chamber having a temperature range between 1450°C and 1600°C are present To attain the required efficiency, pulverized coal is given a swirling motion around the flame Pulverised Coal Combustion an overview ScienceDirect Topics2023年7月25日 Burnout rate is an important index to judge the combustion condition of pulverized coal in BF tuyere Investigating the effects of NG injection rate and different thermal compensation measures on PC burnout rate can intuitively compare the infurnace phenomenon of PCI and NG / coal coinjectionNumerical study of natural gas and pulverized coal coinjection 2023年1月13日 The pulverized coal combustion process in power boilers is still being improved by the preliminary cleaning of coal Distribution of velocities in the dust ductliquid injection for L1 (PDF) Pulverized CoalFired Boilers: Future Directions of Scientific
.jpg)
Combustion Characteristics of Coal for Pulverized Coal Injection
Various characterization methods are used to investigate the physical and chemical properties of steel plant flying dust and waste oil sludge, and the combustion characteristics of the mixtures with pulverized coal are studied via thermogravimetric analysis; the catalytic combustion mechanism is also explored The results show that two types of metallurgical byproducts with 2018年11月4日 The injection of the pulverized coal into the BF results into (i) increase in the productivity of the BF, ie the amount of hot metal (HM) produced per day by the BF, (ii) reduce the consumption of the more expensive coking coals by replacing coke with cheaper soft coking or thermal coals, (iii) assist in maintaining furnace stability, (iv) improve the consistency of the Understanding Blast Furnace Ironmaking with Pulverized Coal Injection 2018年2月21日 4 The pulverized coal is deposited in a single reservoir bin and stored under inert conditions 5 The flow rate of the pulverized coal is regulated by inert gas pressure as a function of feed tank weight change 6 The single stream of dense phase coal from a feed tank is combined with transport gas (nitrogen) at the mixing tee 7Pulverized coal injection PPT Free Download SlideShare2024年4月15日 Aslan Ö, Hacıoğlu R, Altan A Pulverized Coal Injection Tank Pressure Control Using Fuzzy Based Gain Regulation for Model Reference Adaptive Controller[J] Google Scholar [19] H Li, Q Chang, R Gao, et al Fractal characteristics and reactivity evolution of lignite during the upgrading process by supercritical CO2 extraction[J]Combustion behavior of coinjecting flux, pulverized coal, and

Technological advancements in evaluating the
2020年9月11日 The pulverized coal injection (PCI) is pursued to reduce the hot metal production cost by replacingthe expensive metallurgical coke with the noncoking coalPulverized Coal Injection (PCI) using the denseflow method The Küttner developed and perfected denseflow method offers several advantages over a lowerdensity system Higher injection rates are achieved with simultaneously lower coke rates, which can optimize the fuel costs of the blast furnacePulverized coal injection (PCI) Iron Steel Kuettner GroupIn the paper, Computational Fluid Dynamics (CFD) is applied to simulate the pulverized coal injection with natural gas (NG) coinjection inside the blow pipe and tuyere of a blast furnaceNumerical Simulation of the CoInjection of Natural Gas and Pulverized 2022年3月16日 The production process of direct reduced iron from titanomagnetite by coal reduction in air in rotary kiln is a key step in the extraction of titanium and iron This process is conducive to alleviating the stocking problem of a large amount of Tibearing blast furnace slag The relationships between particle movement and pulverized coal injection combustion in Particle motion simulation and pulverized coal injection
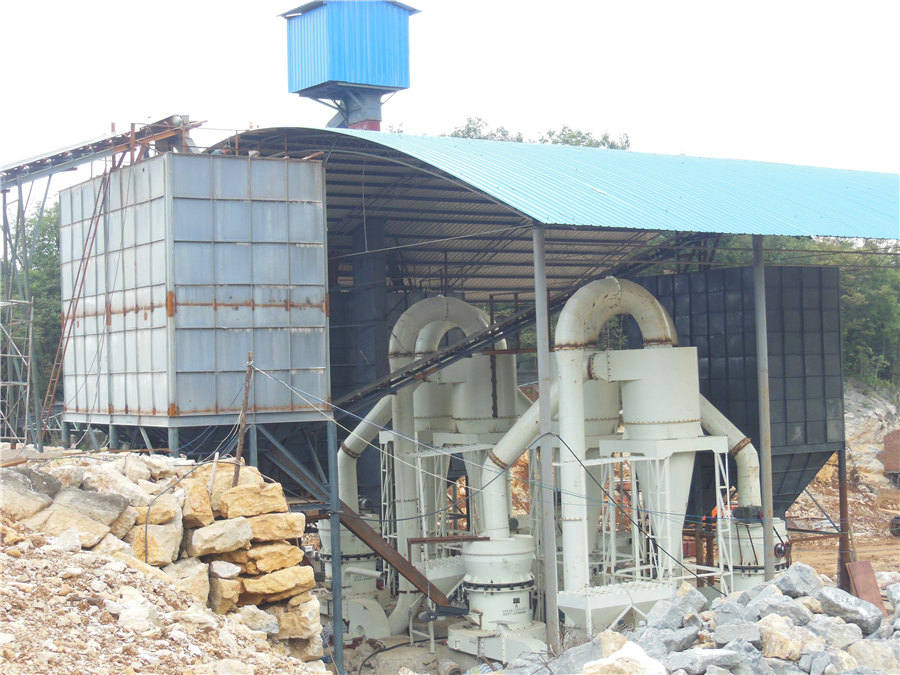
Pulverised Coal an overview ScienceDirect Topics
Because pulverized coal firing uses less excess air than stoker firing, and because the rate of coal combustion is governed by particle size, firing pulverized coal in boilers of this vintage elevated combustion temperatures and the process had a high propensity to form slag in Fig 1 Pulverized coal injection station III INITIAL CONSIDERATIONS P The pulverized coal injection vessel can be modelled as if it were a pressurised tank where the principles of mass conservation and ideal gas law can be used However, neither the vessel nor the four control valves have a linear behaviour easy to be modelledAdvanced Dynamic Models for a Pulverized Coal Injection Plant2022年1月11日 Substantial semicoke has been produced through the industrialized lowtemperature pyrolysis process, which has great potential as an alternative fuel for pulverized coal injection (PCI) and iron ore sintering Xray diffraction, Raman spectroscope, and thermal analysis were used to compare the carbon chemical structure and combustion reactivity of semicoke, Comparison of semicoke with traditional pulverized coal injection Control Blast Furnace Pulverized Coal Injection to Increase PCI Rates Roland Weiser, Ingo Braune, Peter Matthes AMEPA GmbH Jülicher Str 320 D52070 Aachen Germany Tel: +49241168040 Fax: +492411680444 Email: info@amepa Key words: Pulverized coal injection, Coal flow meter, Controlled injection, Equal distribution, Increase of PCIControl Blast Furnace Pulverized Coal Injection to Increase PCI
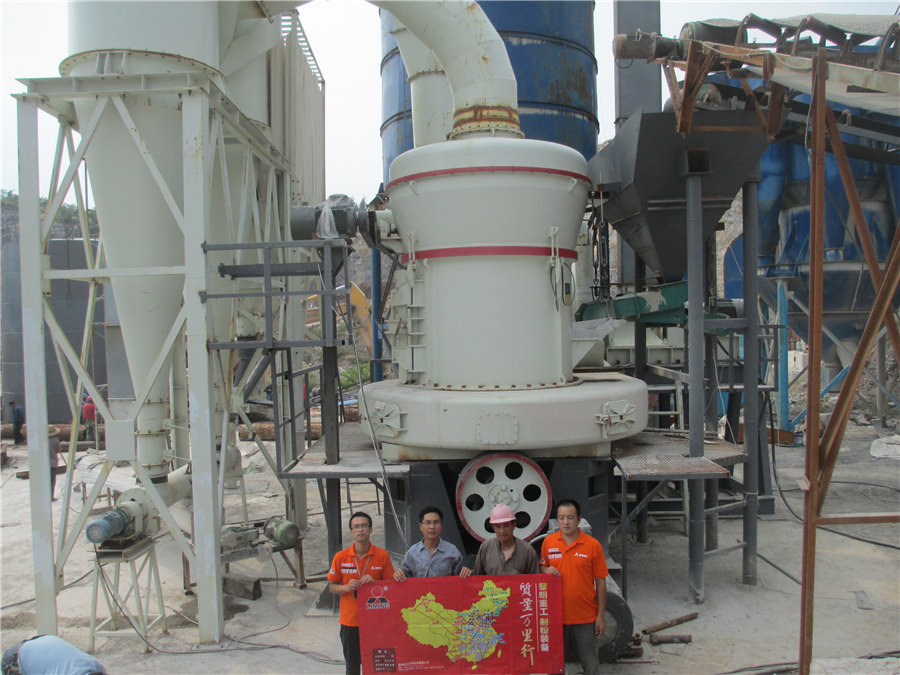
Pulverized coal injection method Wikipedia
Pulverized coal injection was developed in the 19th century, but was not implemented industrially until the 1970s Rises in the cost of coke due to increased global demand and thus more competition for the resource have made this method attractive to the ironproducing industries and increased its value The PCI method is based on the simple concept of primary air (termed Fuel preparation for a pc boiler occurs in a mill, where coal is typically reduced to 70% through a 200mesh (74μm) screen Figure 2 shows a particlesize distribution from a bowlmill grinder typically used in power plants A typical utility specification for particle size distribution of the coal is that 70% of the mass should pass through a 200mesh screen, which is equivalent to 70% Pulverized Coal Boiler an overview ScienceDirect Topics2022年3月1日 Blast furnace hydrogenrich metallurgyresearch on efficiency injection of natural gas and pulverized coal Author links open overlay panel Cuiliu Zhang a b, Listopadov Vladislav c, Runsheng Xu a b, Grachev Sergey c, Kexin Jiao a b, Jianliang Zhang a b, Tao Li a b, Ternovykh Aleksei c, Chuan Wang d e, Guangwei Wang a b Show moreBlast furnace hydrogenrich metallurgyresearch on efficiency injection 2011年3月17日 In order to understand the complicated phenomena of pulverized coal injection (PCI) process in blast furnace (BF), several mathematical models have been developed by the UNSW and BSR cooperation These models are featuring from coal combustion in a pilotscale test rig, to coal combustion in a real BF, and then to coal/coke combustion in a real BF, CFD Modelling and Analysis of Pulverized Coal Injection in
.jpg)
Combustion Characteristics of Coal for Pulverized Coal Injection
In the pulverized coal injection (PCI) process of a blast furnace (BF), intensifying the combustion of pulverized coal in the raceway and tuyere is the key to increasing the injection ratio3,4 In addition to widely used technologies that cooperate with PCI, such as oxygen enrichment and high temperature of2022年4月7日 To solve the energy crisis and slow down the greenhouse effect, it is urgent to find alternative energy sources for the iron and steel production process Hydrochar is an auxiliary fuel and the only renewable carbon source that could reduce the injection of bituminous coal into the blast furnace Numerical simulation is an effective method of understanding the Numerical Simulation Study on the Effects of CoInjection of Pulverized 2019年2月14日 The aim of present paper is to review various aspects of pulverized coal combustion such as oxyfuel combustion, cocombustion of coal and biomass, emissions from pulverized coal furnaces, ash formation and deposition, and carbon capture and sequestration (CCS) technologies to outline the progress made in these aspectsA complete review based on various aspects of pulverized coal 2020年10月1日 Coal is the most important primary energy source in China According to statistics, its energy reserves account for 9422% of China's primary energy reserves [1], and coal consumption accounted for 59% of total energy consumption in 2018 [2]At the same time, data analysis shows that China will continue to maintain this status for a long time [3]Coke generation and conversion behavior of pulverized coal combustion
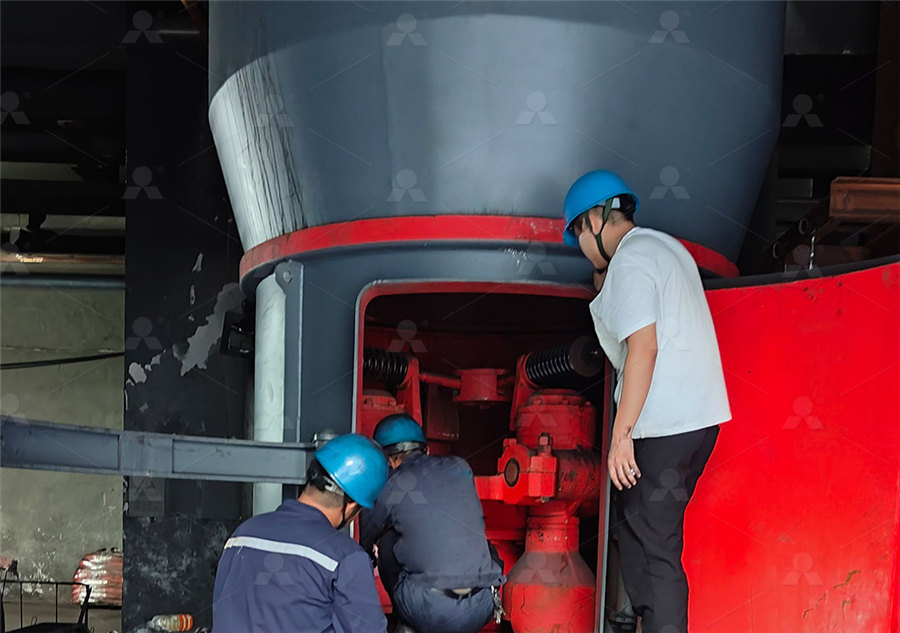
Combustion visualization analysis of alternative fuels in the
2024年9月15日 Currently, the steelmaking process uses a pulverized coal injection (PCI) system that serves as the heat source and reductant for ironmaking (blast furnace and FINEX) where system uses expensive highgrade coal and high operating costs Hydrogen steelmaking is currently being developed to achieve carbonfree operation To achieve a softlanding during Injecting pulverized coal and natural gas into blast furnaces for ironmaking decreases metallurgical coke requirements, providing a net decrease in the CO 2 emissions and in many cases, operating costs associated with iron production Ideally, the fuel would enter the raceway partially reacted and the injection would not have negative impacts on the equipment or processInjection of Pulverized Coal and Natural Gas into Blast Furnaces pulverized coal injection ft ft fc fy fc fy wt pc wt pc pc wt wt fs fc fs fy ft ft ft wt fc fy fc fy fc fc fc wt wt fc fy ft 6 unit operations of pulverized coal injection pressurizing gas vessel nitrogen global flow rate closed loop control conveying hoppers static distributor injection lines pulverized coal tuyeres conveying line closed loop Pulverized Coal Injection Paul Wurth1996年4月10日 New pulverized coalfired systems routinelyinstalled today generate power at net thermal cycle efficienciesranging from 34 to 37% (higher heating value) while removingup to 97% of the combined Developments in Pulverized CoalFired Boiler
.jpg)
Numerical Simulation Study of Coinjection of Pulverized Coal
2024年6月3日 Hydrogen can replace partially pulverized coal in the blast furnace injection as the clean and highcalorific energy, which can reduce energy consumption and carbon emission in molten iron production In this study, a discrete phase model is used to describe the complex flow and thermochemical behavior associated with the coinjection of hydrogen and pulverized coal 161 Pulverized coal combustion In pulverized coal combustion (PCC), dust burners are used to feed coal into the combustion chamber, where flame core zones of the combustion chamber having a temperature range between 1450°C and 1600°C are present To attain the required efficiency, pulverized coal is given a swirling motion around the flame Pulverised Coal Combustion an overview ScienceDirect Topics2023年7月25日 Burnout rate is an important index to judge the combustion condition of pulverized coal in BF tuyere Investigating the effects of NG injection rate and different thermal compensation measures on PC burnout rate can intuitively compare the infurnace phenomenon of PCI and NG / coal coinjectionNumerical study of natural gas and pulverized coal coinjection 2023年1月13日 The pulverized coal combustion process in power boilers is still being improved by the preliminary cleaning of coal Distribution of velocities in the dust ductliquid injection for L1 (PDF) Pulverized CoalFired Boilers: Future Directions of Scientific
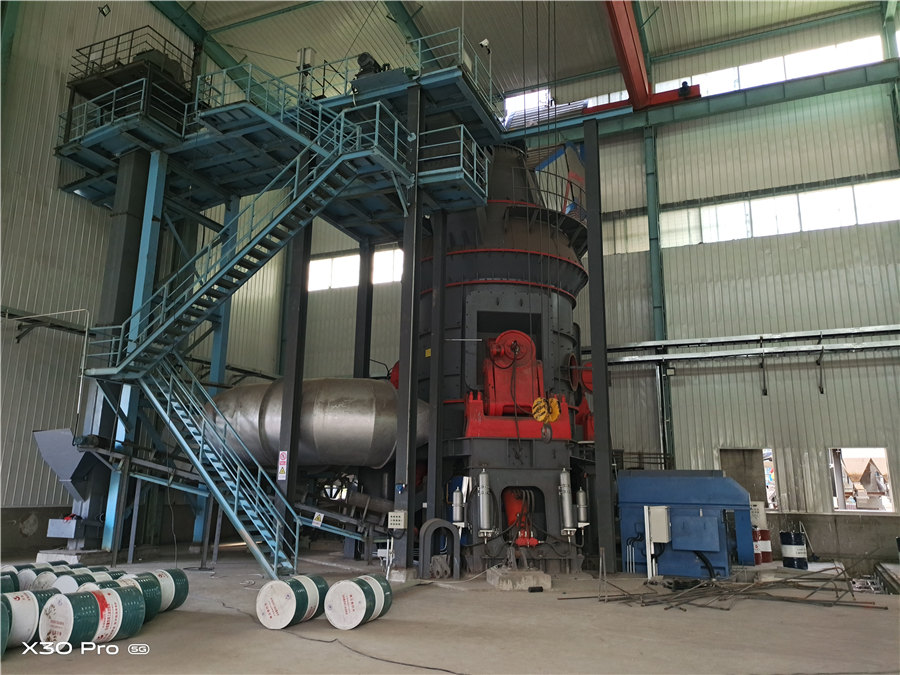
Combustion Characteristics of Coal for Pulverized Coal Injection
Various characterization methods are used to investigate the physical and chemical properties of steel plant flying dust and waste oil sludge, and the combustion characteristics of the mixtures with pulverized coal are studied via thermogravimetric analysis; the catalytic combustion mechanism is also explored The results show that two types of metallurgical byproducts with 2018年11月4日 The injection of the pulverized coal into the BF results into (i) increase in the productivity of the BF, ie the amount of hot metal (HM) produced per day by the BF, (ii) reduce the consumption of the more expensive coking coals by replacing coke with cheaper soft coking or thermal coals, (iii) assist in maintaining furnace stability, (iv) improve the consistency of the Understanding Blast Furnace Ironmaking with Pulverized Coal Injection 2018年2月21日 4 The pulverized coal is deposited in a single reservoir bin and stored under inert conditions 5 The flow rate of the pulverized coal is regulated by inert gas pressure as a function of feed tank weight change 6 The single stream of dense phase coal from a feed tank is combined with transport gas (nitrogen) at the mixing tee 7Pulverized coal injection PPT Free Download SlideShare2024年4月15日 Aslan Ö, Hacıoğlu R, Altan A Pulverized Coal Injection Tank Pressure Control Using Fuzzy Based Gain Regulation for Model Reference Adaptive Controller[J] Google Scholar [19] H Li, Q Chang, R Gao, et al Fractal characteristics and reactivity evolution of lignite during the upgrading process by supercritical CO2 extraction[J]Combustion behavior of coinjecting flux, pulverized coal, and