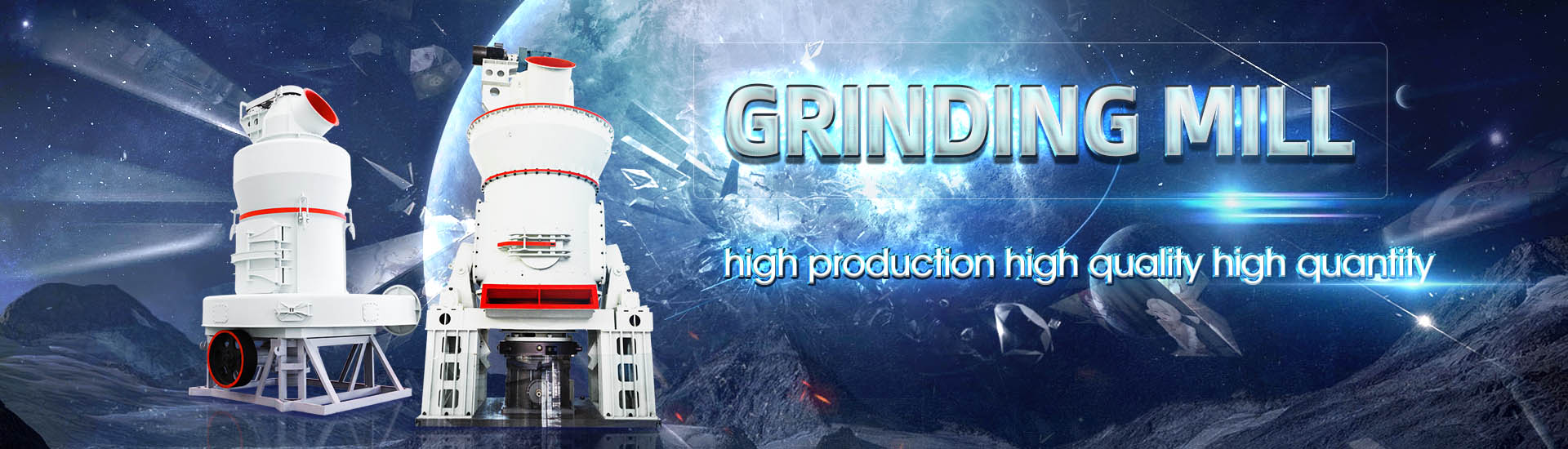
Coal mill related knowledge
43.jpg)
Coal Mill an overview ScienceDirect Topics
Mills are mechanical devices used to break different types of solid materials in small pieces by grinding, crushing or cutting In pulverised coalfired power plants, a pulveriser coal mill grinds the raw coal into a combustible dustThe first is that the CO 2 concentration in the flue gas is noticeably higher in a Cement Plant2015年8月1日 In this paper, a review of researches done on the mill control and methods employed for fault diagnosis of coal mills is provided, with the aim of improving performance Review of control and fault diagnosis methods applied to coal Coal mill is an important component of the thermal power plant It is used to grind and dry the moisturized raw coal and transport the pulverized coal – air mixture to the boiler Poor dynamic (PDF) Modeling and Control of Coal Mill Academia
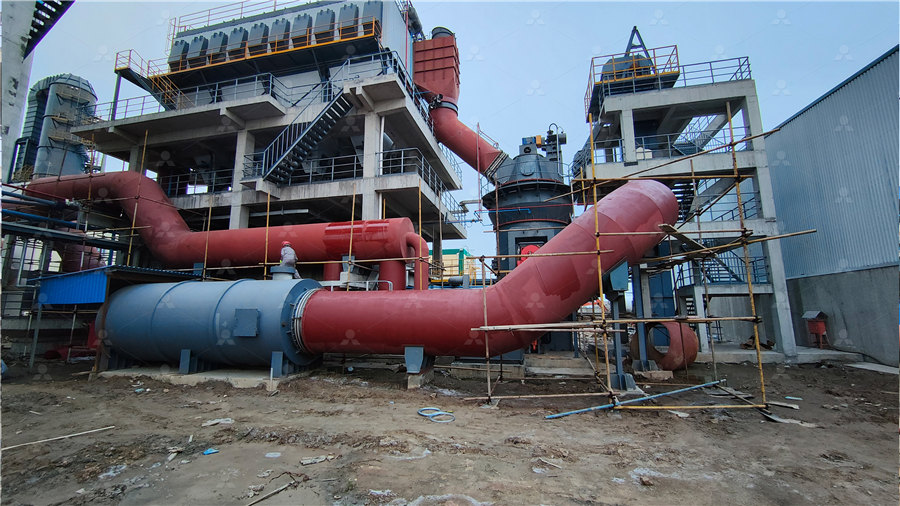
A unified thermomechanical model for coal mill operation
2015年11月1日 Coal mills are bottleneck in coal–fired power generation process due to difficulty in developing efficient controls and faults occurring inside the mills In this paper, a dynamic Coal quality, that is the properties of coal, has an impact on many parts of a power plant including the coal handling facilities, pulverising mills, boiler, air heater, ESP, ash disposal as well as Expert systems and coal quality in power generation USEA2020年4月7日 The main task of a coal mill system is to provide qualified fuel for the pulverized coal boiler In the coal mill system, raw coal is firstly grinded into fine powder, and then dried and transmitted into the boiler by the primary airModeling of Coal Mill System Used for Fault Simulation 2020年8月12日 This study shows the performance of a currently running vertical roller coal mill (VRM) in an existing coalfired power plant In a power plant, the coal mill is the critical An investigation of performance characteristics and energetic
.jpg)
Classification performance of model coal mill classifiers with cip
Abstract: The classification performance of model coal mill classifiers with different bottom incoming flow inlets was experimentally and numerically studied The flow field adjacent to two 2019年1月1日 Abnormal condition monitoring is an essential part in ensuring the reliability and safety and guaranteeing the efficiency for industrial processes This paper proposes a Abnormal Condition Monitoring and Diagnosis for Coal Mills 2022年10月4日 The reliability of a coal mill's operation is strongly connected with optimizing the combustion process Monitoring the temperature of a dust–air mixture significantly increases The Disturbance Detection in the Outlet Temperature of a Coal 2020年8月12日 Ultimately, the energetic efficiency of coal mill has been investigated and performance value has been found to be a maximum value of 962% KEYWORDS: Vertical roller coal mill; energetic performance; coalfired power plant; Related Research People also read lists articles that other readers of this article have readAn investigation of performance characteristics and energetic
.jpg)
An investigation of performance characteristics and
2020年8月12日 This study shows the performance of a currently running vertical roller coal mill (VRM) in an existing coalfired power plant In a power plant, the coal mill is the critical equipment, whose 2014年1月1日 Two mill systems are employed for most coal grinding applications in the cement industry These are, on the one hand, vertical roller mills (VRM) that have achieved a share of almost 90% and, on (PDF) MPS mills for coal grinding ResearchGateLike for cement, coal mills can be vertical (roller) or horizontal (ball) and the circuit are similar, depending on the type of mill, vertical or horizontal ball mill From bag filter point of view, consideration are the same for raw and cement mills: Horizontal mill= low dust load (eg 200 g/Nm3) and low operating negative pressure (10 mbar) Discovering cement: coal mill CTP2019年1月1日 The work in this part is based on a ZGM113N medium speed coal mill equipped in a subcritical 600MW unit Combined with existing research [1, 53] and relevant theoretical knowledge [54], 15 Abnormal Condition Monitoring and Diagnosis for Coal Mills
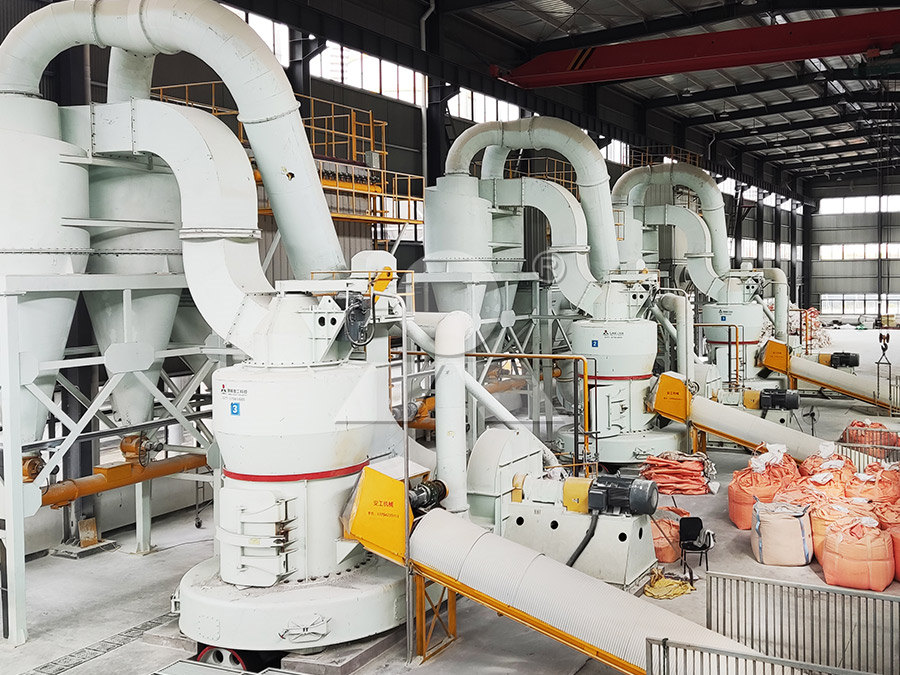
Dual fault warning method for coal mill based on ScienceDirect
2024年5月1日 Knowledge, information and data are being integrated into predictive methods for condition assessment and predictive maintenance becoming mainstream [9] The distributed control system (DCS) of the power plant records variables related to many aspects of coal mill2009年9月1日 The coal mill used in the coalfired power plants is modeled in view of the controller design rather than the educational simulator The coal mass flow and the outlet temperature are modeled by reinvestigating the mass balance and heat balance models physically The archived data from a plant database are utilized to identify the model Modeling and Parameter Identification of Coal MillStrength is very much less in tension, a typical value being around 15 N/mmz for a hard coal Mill wear rate is also related to compressive strength, as will be demonstrated later Other mechanical and physical properti~ that may be expected to affect the performance of a mill with a specific coal are less easy to findCOAL PREPARATION AND FIRING INFINITY FOR CEMENT EQUIPMENTCan GE service my boiler mills? YES Our boiler mills and coal pulverizers span the globe and are built in a variety of sizes and capacitiesWe provide customized maintenance solutions, and offer a full spectrum of highquality solutions for each—in addition to our thousands of standard boiler mill parts and boiler service solutionsThis is the Power of YesBoiler Mill and Coal Pulverizer Performance GE Steam Power
.jpg)
PowerGen 2008, Orlando, USA Online measurement of coal fineness
Knowledge of the coal particle size distribution, coal mass flow and the air/fuel ratio inside Next to the apparent mill related issues, the coal particle size spectrum and also very important the airfuel ratio (AFR) have a significant impact on the combustion process inside 1997年8月1日 DOI: 101016/S14746670(17)464470 Corpus ID: ; Analysis of coal Mill Dynamic Characteristics Under Normal and Abnormal Operating Conditions @article{Fan1997AnalysisOC, title={Analysis of coal Mill Dynamic Characteristics Under Normal and Abnormal Operating Conditions}, author={G Q Fan and N W Rees and David Parker}, Analysis of coal Mill Dynamic Characteristics Under Normal and Key words: Coal mill classifier, Cut size, Nonswirling inlet, Particle image velocimetry, Impeller rotational speed 摘要: The classification performance of model coal mill classifiers with different bottom incoming flow inlets was experimentally and numerically studiedThe flow field adjacent to two neighboring impeller blades was measured using the particle image velocimetry techniqueClassification performance of model coal mill classifiers with cip2020年8月14日 The coal mill is one of the important auxiliary engines in the coalfired power station Its operation status is directly related to the safe and steady operation of the units(PDF) Application of ModelBased Deep Learning Algorithm in Fault
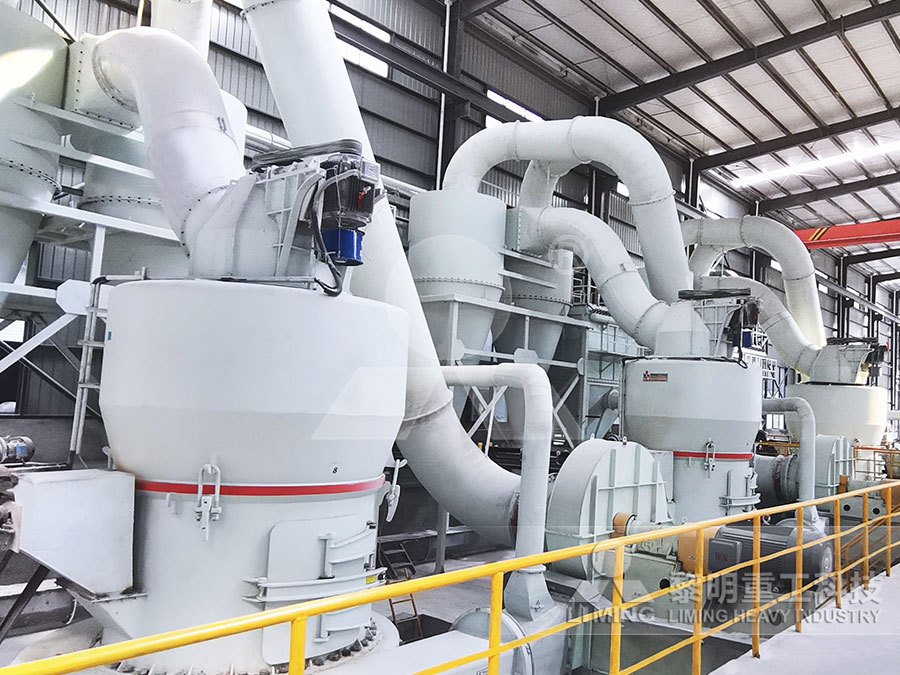
A unified thermomechanical model for coal mill operation
2015年11月1日 Further, the performance and availability of the plant is influenced by several faults occurring in the milling system and various mill related factors such as incorrect fineness, improper air/fuel ratios, coal hang up at the mill inlet, overloading, fire /explosion, and wear of milling components (Maloney, Benson, Tous (1981), Sathyanathan (2010), Fan, Rees, Coal Mills are used to pulverize and dry to coal before it is blown into the power plant furnace Operation The coal is feed into the coal mill through a central inlet pipe where gravity is used to lead the coal to the bottom of the mill, where the grinding table and some heavy rollers pulverizes the coal to particlesCoal Mills SolidsWikiDirect firing coal mill plant is what is installed in most power generation facilities The coal mill is operated as an airswept mill and “blows” directly into the combustion zone of the steam boiler, via a pipeline connection In case of an explosion, normally as consequence of ignition within the mill chamber, there will beExplosion protection for coal grinding plants What should2022年4月13日 The shaft oil seals supplied by XI’AN XINBEILANG IMPEXP CO,LTD for BPEG coal mills can guarantee good performance in coal mill pulverizers for thermal power plants The material used for making the oil seal for coal mills is FKM (fluororubber), which is a very good material with features of heat resistance, antioxidation resistance, oil resistance, corrosion What is the oil seal for BPEG coal mill pulverizers ? Knowledge
.jpg)
(PDF) Modeling and Control of Coal Mill Academia
Related papers Derivation and validation of a coal mill model for control T Pedersen, Palle Andersen Control 2013 Mumbai, India Modeling and Control of Coal Mill P Pradeebha, N Pappa, D Vasanthi Department of Instrumentation Engineering, Madras Institute of Technology, Anna University, India : pradeebhamit@gmail 2016年3月1日 Similarly, in October 2014, Misr Beni Suef Cement announced plans to build a US$279m coal mill by the end of 2015 Next, in November 2014, Titan Cement ordered a Gebr Pfeiffer SE type MPS 2800 BK vertical roller mill for coal Coal for cement: Present and future trends520 P Niemczyk et al / Control Engineering Practice 20 (2012) 519–530 Nomenclature Dpmill mc mpc mcair mass of unground coal on the table (kg) mass of pulverized coal on the table (kg) mass of pulverized coal carried by Derivation and validation of a coal mill model for The coal mill is a key ancillary to any pulverized fuel boiler It grinds the coal to a fine powder so that it can be burned with maximum efficiency Biomass also moves through hammer mills, dryers and pulverizers during the production process Avoiding mill explosions is essential for personnel safety and asset protectionMilling Biomass / Coal AMETEK Land
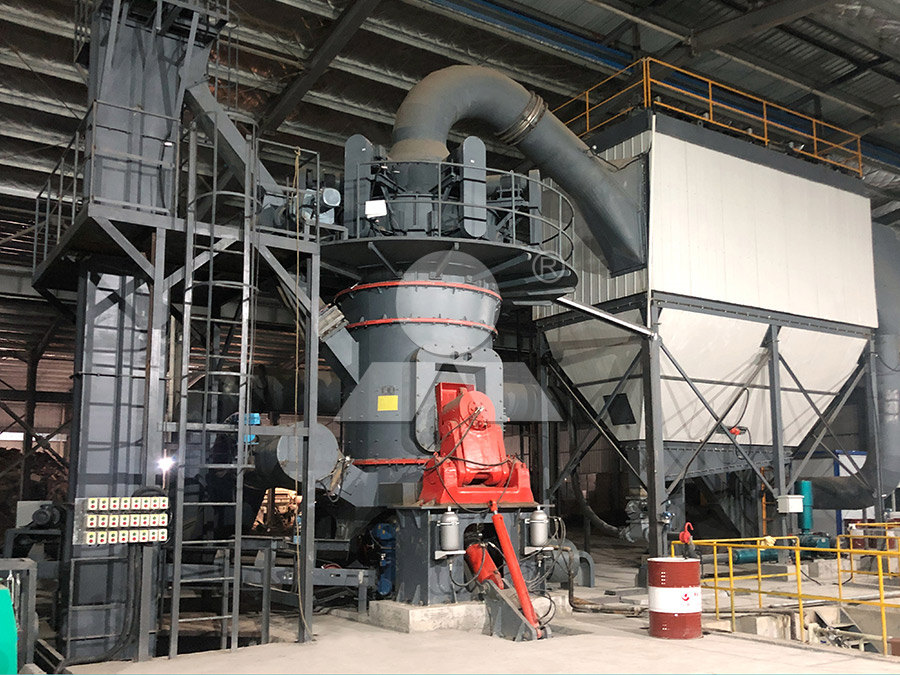
Coal Mills SolidsWiki
Coal Mills are used to pulverize and dry to coal before it is blown into the power plant furnace Operation The coal is feed into the coal mill through a central inlet pipe where gravity is used to lead the coal to the bottom of the mill, where the grinding table and some heavy rollers pulverizes the coal to particlesModernisation of the coal mill in terms of explosion safety was necessitated the hazards posed by the coal dust/air mixture at the time of contact with eg hot surface, mechanical and electrostatic sparks, open fire source as a source of ignition The risk was related as well as delivered and assembled explosionproof systems Knowledge Comprehensive explosion protection of technological equipment in a coal 2020年1月1日 Coal mills have a significant influence on the reliability, efficiency, and safe operation of a coalfired power plant Coal blockage is one of the main reasons for coal mill malfunctionEarly Warning of Critical Blockage in Coal Mills Based on 2020年4月2日 co related to the boiler combustion capacity Coal mill motor power (kW) 0 4171 4548 4390 4586 More important contributions can be achieved by knowledge based Analysis of the Coal Milling Operations to the Boiler Parameters
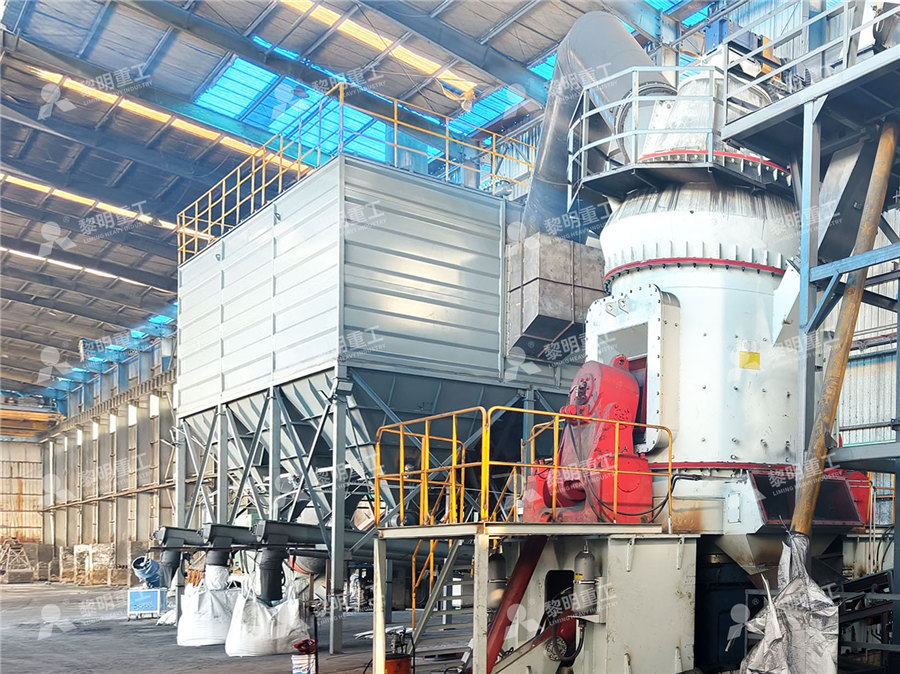
Measurement and Control of Coal Pipe Temperature of Coal Mills
and analysis of coal mill related problems REFERENCES [1] Damian Flynn, “Thermal Power Plant Simulation and control”, The Institution of Electrical Engineers, 2003 [2] K E Bollinger and H R Snowden, “The Experimental Determination of Coal Mill Models”, IEEE Transactions on Power ApparatusDOI: 101016/S09670661(96)002134 Corpus ID: ; An intelligent expert system (KBOSS) for power plant coal mill supervision and control @article{Fan1997AnIE, title={An intelligent expert system (KBOSS) for power plant coal mill supervision and control}, author={G Q Fan and N W Rees}, journal={Control Engineering Practice}, year={1997}, volume={5}, An intelligent expert system (KBOSS) for power plant coal mill 2020年8月12日 Ultimately, the energetic efficiency of coal mill has been investigated and performance value has been found to be a maximum value of 962% KEYWORDS: Vertical roller coal mill; energetic performance; coalfired power plant; Related Research People also read lists articles that other readers of this article have readAn investigation of performance characteristics and energetic 2020年8月12日 This study shows the performance of a currently running vertical roller coal mill (VRM) in an existing coalfired power plant In a power plant, the coal mill is the critical equipment, whose An investigation of performance characteristics and

(PDF) MPS mills for coal grinding ResearchGate
2014年1月1日 Two mill systems are employed for most coal grinding applications in the cement industry These are, on the one hand, vertical roller mills (VRM) that have achieved a share of almost 90% and, on Like for cement, coal mills can be vertical (roller) or horizontal (ball) and the circuit are similar, depending on the type of mill, vertical or horizontal ball mill From bag filter point of view, consideration are the same for raw and cement mills: Horizontal mill= low dust load (eg 200 g/Nm3) and low operating negative pressure (10 mbar) Discovering cement: coal mill CTP2019年1月1日 The work in this part is based on a ZGM113N medium speed coal mill equipped in a subcritical 600MW unit Combined with existing research [1, 53] and relevant theoretical knowledge [54], 15 Abnormal Condition Monitoring and Diagnosis for Coal Mills 2024年5月1日 Knowledge, information and data are being integrated into predictive methods for condition assessment and predictive maintenance becoming mainstream [9] The distributed control system (DCS) of the power plant records variables related to many aspects of coal millDual fault warning method for coal mill based on ScienceDirect
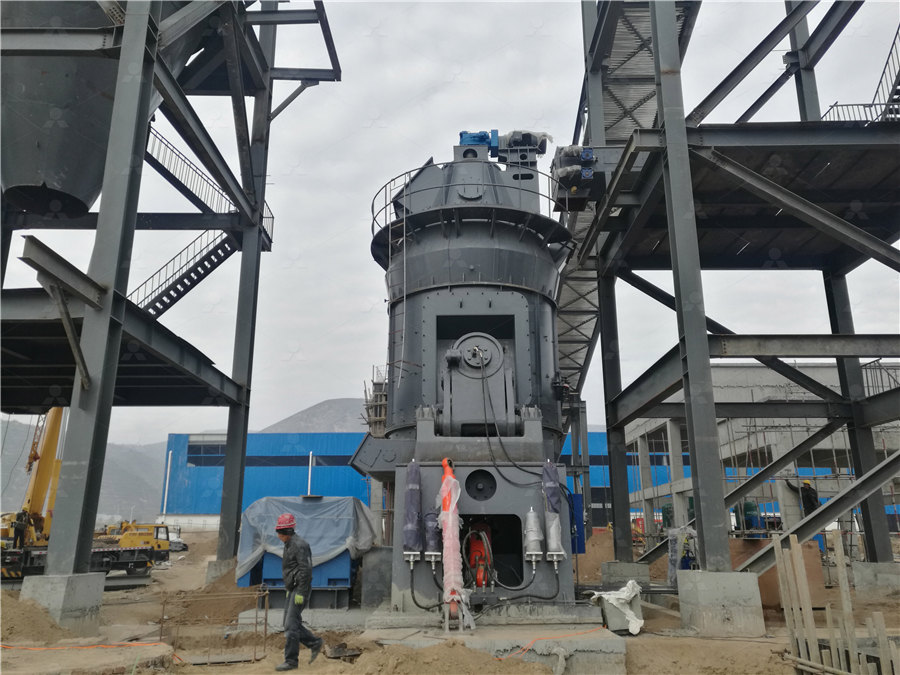
Modeling and Parameter Identification of Coal Mill
2009年9月1日 The coal mill used in the coalfired power plants is modeled in view of the controller design rather than the educational simulator The coal mass flow and the outlet temperature are modeled by reinvestigating the mass balance and heat balance models physically The archived data from a plant database are utilized to identify the model Strength is very much less in tension, a typical value being around 15 N/mmz for a hard coal Mill wear rate is also related to compressive strength, as will be demonstrated later Other mechanical and physical properti~ that may be expected to affect the performance of a mill with a specific coal are less easy to findCOAL PREPARATION AND FIRING INFINITY FOR CEMENT EQUIPMENTCan GE service my boiler mills? YES Our boiler mills and coal pulverizers span the globe and are built in a variety of sizes and capacitiesWe provide customized maintenance solutions, and offer a full spectrum of highquality solutions for each—in addition to our thousands of standard boiler mill parts and boiler service solutionsThis is the Power of YesBoiler Mill and Coal Pulverizer Performance GE Steam Power