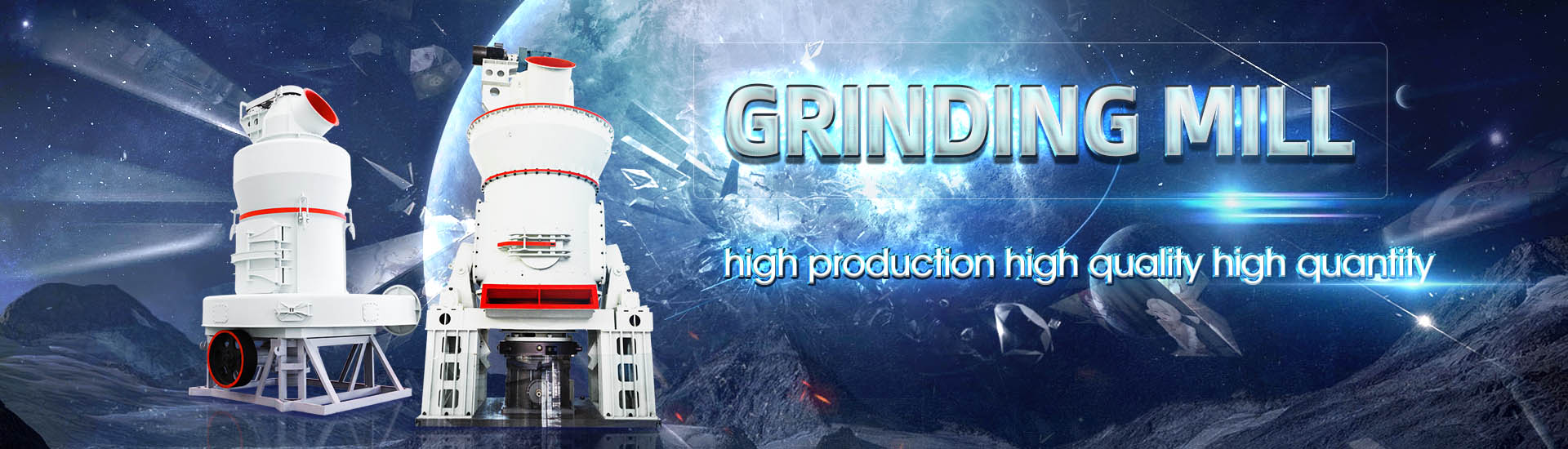
Process flow of laterite nickel crushing machinery
.jpg)
Preconcentration strategies in the processing of nickel laterite ores
2015年8月1日 By far the most common preconcentration process used ahead of commercial hydrometallurgical processing of Ni laterites is the removal of a coarse fraction from the feed Nickel laterites are currently processed with the exception of the hybrid Caron process by either a Pyrometallurgical route or a Hydrometallurgical route Most pyrometallurgical routes HydroPyro Integration in the processing of Nickel Laterites2024年11月1日 The oxygenrich sideblow sulfide smelting nickel matte technology of nickel laterite ore has advantages such as low investment, low energy consumption, short process Review on comprehensive utilization of nickel laterite ore2024年8月7日 The two main processing methods for laterite ores are smelting and HighPressure Acid Leaching (HPAL) Smelting is used primarily on saprolite ores to obtain an iron Nickel industry Part 2 Processing nickel laterites and smelting
.jpg)
Nickel laterite processing and electrowinning practice
2002年8月1日 Laterites are the main source of feedstock for production of ferronickel as described herein The paper includes information regarding nickelbearing deep sea nodules The established LCA models of three nickel laterite processing technologies are shown as Fig1, which demonstrates the process of electric furnace smelting reduction process, blast furnace LCA EVALUATION FOR DIFFERENT TREATMENT PROCESSES OF 2019年9月3日 The typical nickel grades and recoveries for the RKEF process, the lowgrade ferronickel production process, the ESS process, the Vaniukov process, and the reduction roasting–magnetic separation process are Nickel Laterite Smelting Processes and Some Examples In this article, we mainly introduces the smelting methods and technologies of different laterite nickel ore from different ore layers, summarizes the laterite nickel ore of different ore layers Research Status of Laterite Nickel Ore Processing Technology
.jpg)
Recent Progress in Hydrometallurgical Processing of Nickel
Laterite ore contributes to about 70% of the world’s landbased nickel resources Hydrometallurgical techniques such as heap leaching (HL), atmospheric leaching (AL), high 2024年1月1日 The nickel laterite in upper layer of the ore deposit, with higher content of iron (Fe) and lower content of silica (SiO 2) and magnesium (Mg) in general, belongs to the limonite type, and usually contains lower nickel of about 1%, but a certain amount of cobalt (Co), while the nickel laterite in lower layer of the ore deposit, with higher content of silica (SiO 2) and Nickel Laterite Metallurgy SpringerLink2023年2月15日 The crushing process is necessary because when raw laterite nickel ore is excavated, it is often accompanied by columnar rocks with incomplete weathering and with large size After crushing, the huge block of The Best Mining Equipment for Philippines Nickel Download scientific diagram Highpressure acid leaching (HPAL) process flowsheet operating at Moa Bay (Adapted from Monhemius 1987) from publication: Advanced Review on Extraction of Nickel Highpressure acid leaching (HPAL) process
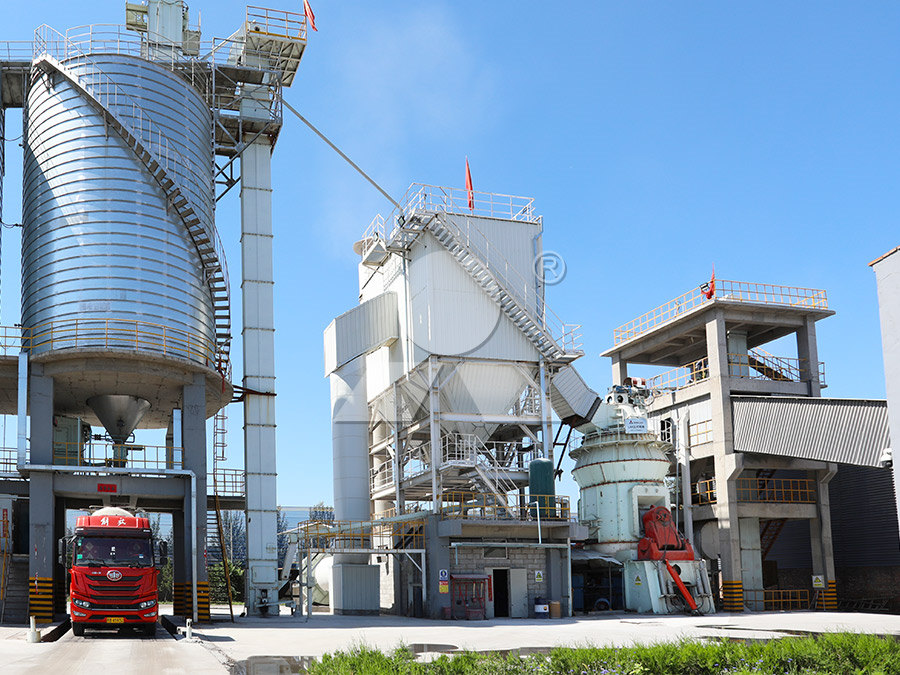
Alkaline Hydrothermal Treatment and Leaching Kinetics of Silicon
2021年12月2日 A new process of extracting silica from laterite nickel ore by hydrothermal treatment with sodium hydroxide as reaction auxiliary agent was proposed The mineralogical transformation and silicon extraction kinetics of laterite nickel ore in alkaline hydrothermal treatment were studied The effects of reaction temperature (175 ~ 250℃), molar ratios of OF NICKEL LATERITE ORE Shuai Wang1,2, Hongxu Li*1,2, Chao Li1,2, Xiangxin Hao1,2, Qinghua Bao , Lifeng Nickeliron production electric furnace process flow is shown in Fig1 [5] First of all, crushing the ore to 50~150mm, send the ore to drying kiln for drying, making the oreLCA EVALUATION FOR DIFFERENT TREATMENT PROCESSES OF NICKEL LATERITE 2023年5月28日 The nickel laterite in upper layer of the ore deposit, with higher content of iron (Fe) and lower content of silica (SiO 2) and magnesium (Mg) in general, belongs to the limonite type, and usually contains lower nickel of about 1%, but a certain amount of cobalt (Co), while the nickel laterite in lower layer of the ore deposit, with higher content of silica (SiO 2) and Nickel Laterite Metallurgy SpringerLinkThe present invention embodies a process for extraction of nickel, cobalt, and other metals from laterite ores by heap leaching, and of the product obtained as well, characterized by the fact that it is comprised of crushing (I), agglomeration (II), stacking (III), and heap leaching (IV) stages, with this last stage being a continuous, countercurrent, heap leaching system with two or more Process for extraction of nickel, cobalt, and other base metals
.jpg)
Improving Sinter Consolidation Characteristics of Nickel Laterite
2024年5月20日 The size distributions of raw materials in the conventional sintering process are shown in Table 2After simple roll crushing by means of an independently designed roll crusher with the capacity of 15 kg, the contents of − 1 mm fractions of nickel laterite, flux I, and burnt lime all exceed 85%, which are suitable for the hybrid sintering process (Table 3)either from a direct precipitation process (containing approx 36% Ni) or via Ion Exchange (>50% Ni) There are many existing pyrometallurgic al facilities which could easily be adapted to take this nickel intermediate giving them significant potential benefits especially as nickel laterite ore grades diminish The nickel productionHydroPyro Integration in the processing of Nickel LateritesIt is an essential raw material in military manufacturing, machinery manufacturing, atomic energy, ultrasonic, and communication Nickel Ore Type At present, there are more than 50 kinds of nickelcontaining minerals known However, it is mainly divided into nickel sulfide ore and nickel oxide ore (laterite nickel ore) Nickel sulfide oresNickel Ore Processing Plant JXSC Mineral2019年3月20日 Extraction of Nickel This paper introduces the extraction of nickel process and characteristics of laterite nickel ore dressing, highlights the nickel ore crushing, washing in the nickel production process design 1 Extraction of Nickel Nickel Ore Mining Mining
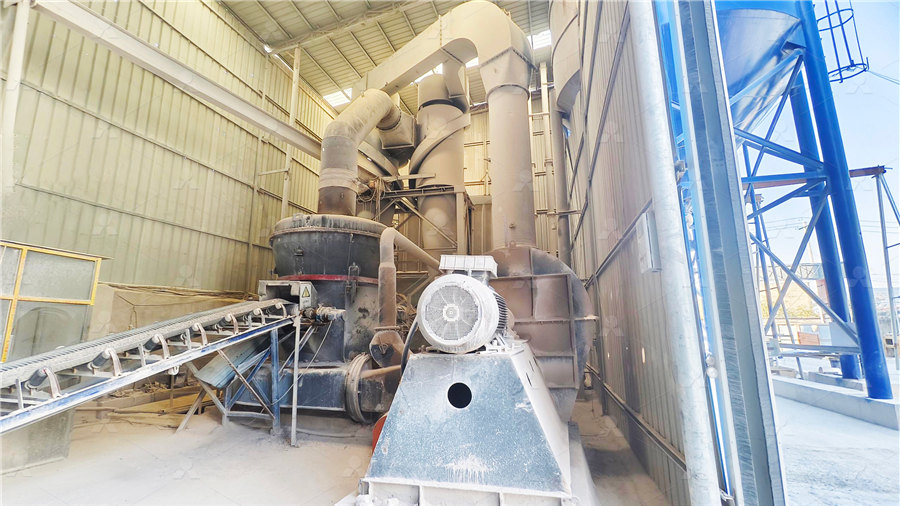
Process Flow Diagram of nickellaterite ore
Download scientific diagram Process Flow Diagram of nickellaterite ore from publication: Experimental Study on Utilization of LowGrade Complex Ore through Direct ReductionMelting and 2018年9月6日 Therefore, a novel process was proposed to directly produce ferronickel alloy nugget at a related low temperature from nickel laterite by the semimolten reduction in the reactor like the rotary Reduction process of lowgrade nickel laterite 2024年1月19日 1) HighPressure Acid Leaching (HPAL): HPAL is a widely used method for extracting nickel from laterite ores, which are lowgrade and high in impurities The process involves the leaching of nickel and other metals from the ore using sulfuric acid at high temperatures and pressuresThe Comprehensive Guide to Nickel Processing Miningpedia2013年5月16日 Use of CementSand Admixture in Laterite Brick Production for Low Cost Housing process flow chart in australian nickel laterite ore processing plant manufacturer Nickel laterite ore processing plant, nickel manufacturing laterite processing for cement Mining Quarry Plant
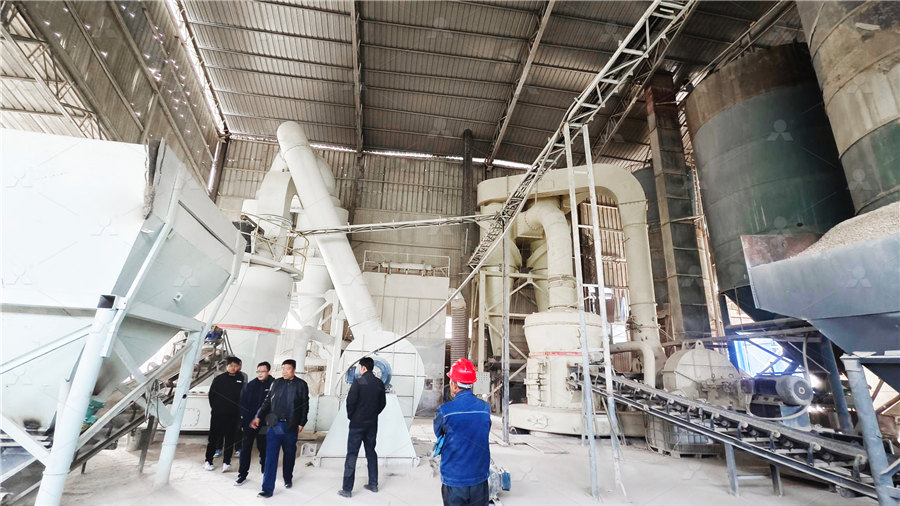
Optimization of The Electro Metal Electrowinning Process for Nickel
2020年1月1日 Slag from the manufacturing of nickel pig iron (NPI) from laterite soil was still containing 82370 ppm of cobalt In this research, the separation process was carried out from slag NPI by using 2015年4月2日 Despite the growth in nickel laterite processing, upgrading these ores remains a challenge This is mainly because of their complex and variable mineralogy and the lack of definite nickelbearing Preconcentration strategies in the processing of nickel laterite 2023年1月19日 Dong J, Wei Y, Zhou S et al (2018) The effect of additives on extraction of Ni, Fe and Co from nickel laterite ores JOM 70:2365–2377 Article Google Scholar Guo X, Li D, Park KH et al (2009) Leaching behavior of metals from a limonitic nickel laterite using a sulfation–roasting–leaching processAn Overview of Nickel Utilization from Laterite OreNickel and Cobalt Production Michael S Moats, William G Davenport, in Treatise on Process Metallurgy: Industrial Processes, 2014 2231 Laterite Ore Upgrading Laterite ores are upgraded before smelting or leaching The upgrading entails gently crushing and/or grinding the ore and then separating the resulting small, soft, lowdensity Nirich laterized mineral particles from Laterite Ore an overview ScienceDirect Topics
.jpg)
Characterization and Beneficiation of Fanibi Laterite for Nickel
2024年6月5日 This study investigates the characterization of Fanibi Laterite and the efficiency of froth flotation to beneficiate nickel from its host rock sourced in Akure, Ondo State, NigeriaExplore the economic recovery of nickel from laterite ores using highpressure acid leaching (HPAL) Understand the process, from crushing and screening to autoclave leaching, and the advantages of the HPAL processthe hpal process Total Materia2021年8月23日 Lowgrade saprolite nickel laterite, characterized by complicated minerals composition and finegrained and complex dissemination, was commonly treated with a low recovery efficiency of Ni and Fe by conventional methods Hence, an improved direct reduction and magnetic separation process was proposed Meanwhile, the mechanisms on the Upgrade of nickel and iron from lowgrade nickel laterite by Explore the extraction processes of nickel from laterite ore, including acid leaching, smelting, and the Caron process Discover the Direct Nickel Process DNi, an atmospheric hydrometallurgical processing route that uses nitric acid The Direct Nickel Process Total Materia
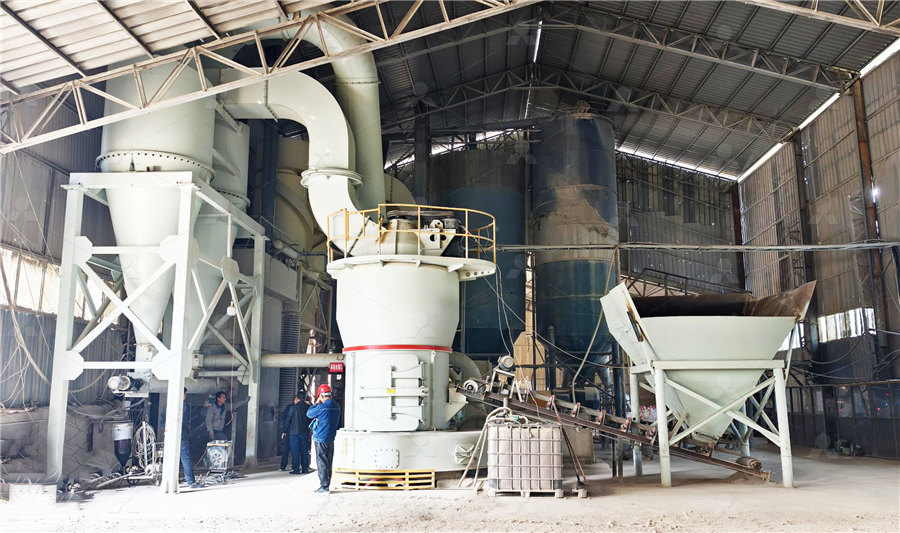
Recent Developments in the Chloride Processing of Nickel Laterites
2011年5月1日 Therefore, research in hydrometallurgical processing of laterite nickel ores has been vibrant, at least in the last three decades, resulting in many new technological development such as nickel and cobalt from lowgrade nickel laterite is hydroelectrometallurgy In the previous research phase of solvent extraction, Versatic Acid 10 was chosen as an extractant to separate calcium andOptimization of The Electro Metal Electrowinning Process for Nickel 2015年7月27日 4 j ENVIRONMENTAL PROCESSING DESIGN VERIFICATION PRODUCT INNOVATION PROJECT MANAGEMENT OPERATIONS TRAINING SKILLSHIRE Outline • Introduction to nickel – sources and uses • Look at the market and some interesting production statistics • Today’s nickel processing status − Brief overview of hydrometallurgical and Nickel Processing and The Rise of Laterites SlideShare2019年3月11日 Ravensthorpe Nickel /Cobalt Project proposed flow sheet CONCLUSIONS The solvent extraction of nickel and cobalt from laterite leach solutions and recent development of hydrometallurgical nickel (PDF) Hydrometallurgical Processing of Nickel Laterites—A
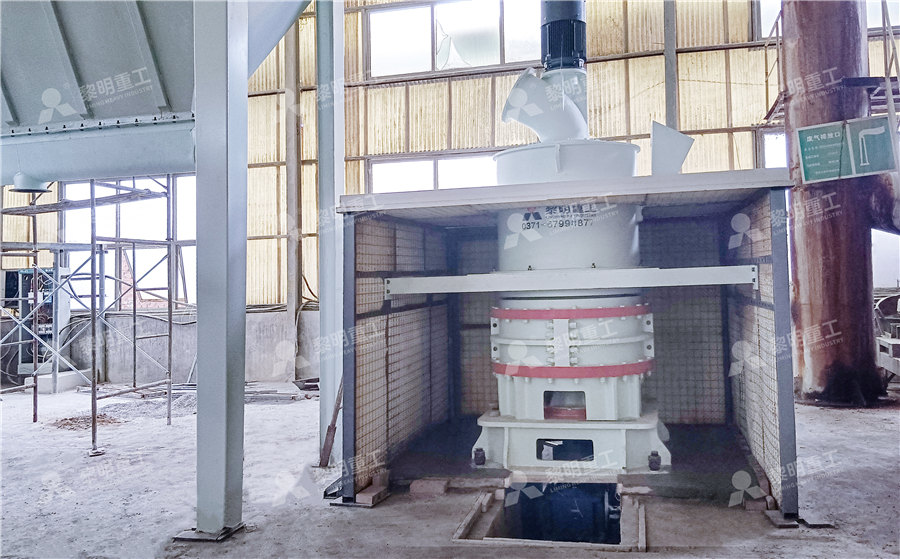
Preparation of Ferronickel from Nickel Laterite Ore via Semi
2018年8月19日 Nickel plays an important role in modern manufacturing []It is the essential element for stainless steel production, which accounts for 65% of nickel consumption []In recent years, the global annual demand for nickel has increased tremendously due to soaring stainless steel production, particually in China [3,4,5]Nickel sulfide and laterite ores are the two main 2023年2月2日 Home » Solutions » Nickel Ore Beneficiation Process Contact Now +86 Nickel Ore machinery manufacturing, atomic energy, ultrasonic, and communication The main minerals of nickel If you need a coppernickel ore solution, please click here to ask for the flow design Related Product Flotation Machine Rotary Nickel Ore Beneficiation Process JXSC MachineThe invention provides a method for treating lateritenickel ore by a combination of a pyrogenic process and a wet process, which comprises the following steps: (1) pretreating the lateritenickel ore, including crushing, screening, forming and drying; (2) processing the lateritenickel ore green pellets by adopting a rotary hearth furnace direct reduction process to obtain metallized pellets Method for treating lateritenickel ore by combination of 2008年1月1日 Australia has large reserves of limonite and claybased laterites that are currently underutilized This review summarizes the latest nickel laterite upgrading studies reported in the literature Process flowsheet development for beneficiation of
.jpg)
Preconcentration strategies in the processing of nickel laterite
Preconcentration strategies in the processing of nickel laterite ores Part 1: Literature review Keith Quasta,⇑, Jason N Connora,b, William Skinnera, David J Robinsonc, Jonas AddaiMensaha a Nickel Processesppt Free download as Powerpoint Presentation (ppt), PDF File (pdf), Text File (txt) or view presentation slides online The document provides information on nickel/cobalt laterite processes, including: 1) It Nickel Processes PDF Nickel Smelting2021年10月24日 Nickel laterite ore is used to produce nickel metal, predominantly to manufacture stainless steel as well as nickel sulfate, a key ingredient in the batteries that drive electric vehicles Nickel laterite production is on the rise and surpassing conventional sulfide deposits The efficiency of mining and processing nickel laterites is defined by their Nickel Laterites—Mineralogical Monitoring for Grade Definition 31 MATERIALS RESEARCH COMMUNICATIONS 1(1) (2020) 2633 Fakhreza et al Based on the peak contained in the XRD results in Fig 6, the sintered results of sintering of laterite nickel ore with air air flow rate of 545 m3/min revealed the major phase of sintered namely Pyroxene (CaFeSi2O4) and Olivine ((Fe,Mg)2SiO4) and several phases minor from sintered are Nickel The Effect of Air Flow Rate on Sinter Yield, Sinter Strength and Ni
.jpg)
(PDF) New Method of Laterite Ore Processing: Smelting in Two
The process flowsheet is as follows: Ore crushing and dryingBriquettingRoasting of briquettes in Tubular Rotary kilnSmelting of hot briquettes in Twozone Vaniukov Furnace to Ferronickel and dump The addition of 10% sodium sulfate additives by weight in the reduction process of laterite nickel ore produced higher concentrations of 2018年9月21日 Production of nickel from laterite ores has occurred for over 100 years beginning with processing of garnieritic ores from New Caledonia However, until now the world nickel supply has been (PDF) INVESTIGATION OF PROCESSING OF PYROMETALLURGICALLY PRETREATED 2008年8月13日 The Ravensthorpe Nickel Operation (Australia) was sold by BHP Billiton to First Quantum Minerals Australia on 9 December 2009 Due to reduced profitability prospects, decreasing scope of the nickel market, and a gap between projected capital expenditure and production volumes, BHP Billiton decided to sell the operation for $340mBHP Ravensthorpe Nickel Operation, Australia Mining 2015年9月1日 Numerous studies have demonstrated that Na2SO4 can significantly inhibit the reduction of iron oxide in the selective reduction process of laterite nickel oreGeneration process of FeS and its inhibition mechanism on iron
.jpg)
Literature Review: Comparison of Caron Process and RKEF On The
Hydrometallurgical of Nikel Laterite: Caron Process Figure 4 Caron Process Flowchart In the process of processing nickel laterite with limonite type, using the process flow provided in Figure 4 above ISSN 25497197 (cetak), ISSN 2549564X (online) JMEL, Volume 6 Nomor 2, 2022 1