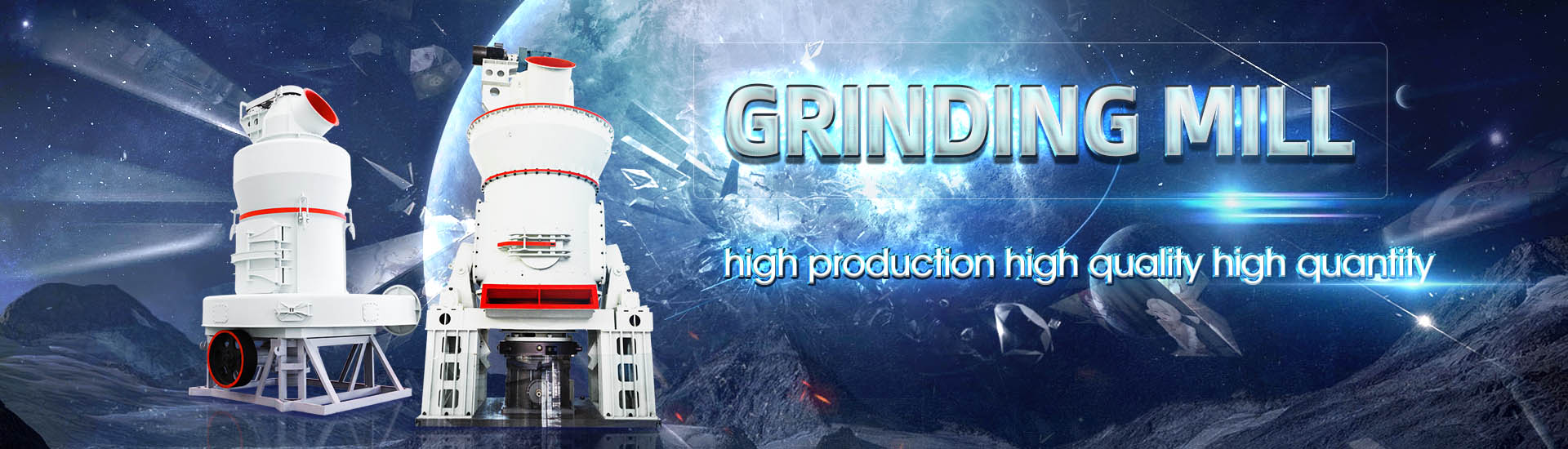
Is the specification of vertical mill based on the diameter of the grinding disc
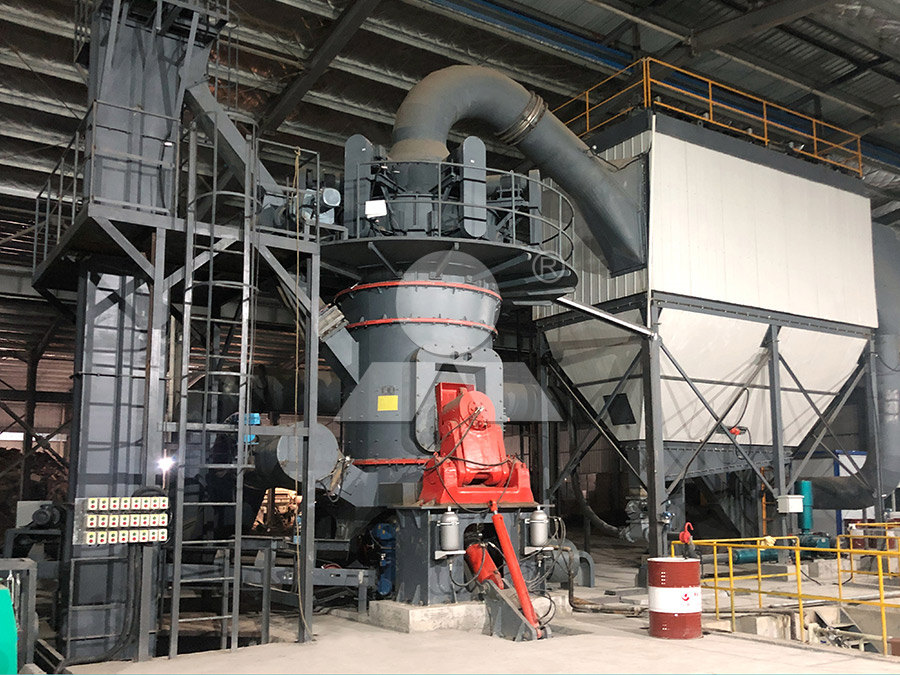
Vertical roller mill for raw Application p rocess materials
Vertical roller mills are adopted in 20 cement plants (44 mills) in Japan In the vertical roller mill which is widely used in the raw material grinding process, raw materials input grinding table are crushed and pulverized on it and transported to separator by kiln exit gas introduced into the Vertical Coal Mill (VCM) is equipment for grinding and pulverizing coal into micron size Rotary kilns then use the powders as fuel burners The VCM has a housing section equipped with aTechnical specifications of vertical roller coal mill2021年1月1日 Big feed size The vertical roller mill can grind the material of particle size of 5% of the grinding roller diameter The feed size is generally 40 to 100 mm and can reach 120 mm Review on vertical roller mill in cement industry its performance 2017年9月11日 In this study, an extensive sampling study was carried out at vertical roller mill of ESCH Cement Plant in Luxemburg Samples were collected from mill inside and around the circuit toPerformance Evaluation of Vertical Roller Mill in
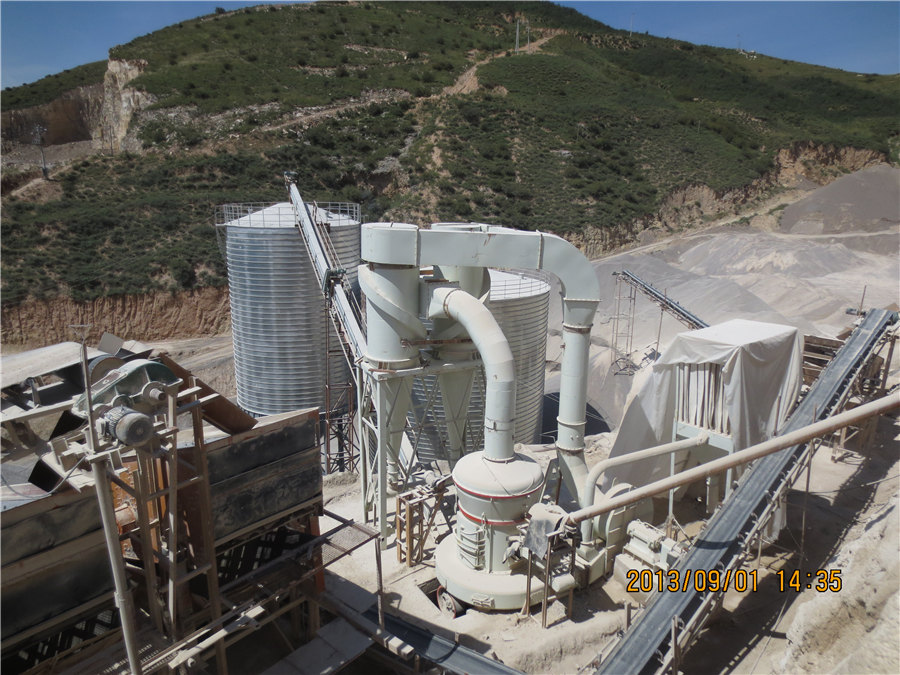
Operational parameters affecting the vertical roller mill
2017年4月1日 Vertical roller mills (VRM) have found applications mostly in cement grinding operations where they were used in raw meal and finish grinding stages and in power plants 2021年9月1日 An energysize reduction equation was derived to estimate the specific grinding energy of the vertical roller mill based on a laboratory characterization test The model was Predicting the grinding energy of vrm depending on material 2019年1月17日 The vertical grinding disc diameter of this design exceeds five meters and is a largescale equipment in the industry In order to shorten the product development cycle as Solid Edge’s Application in Vertical Mill Design2022年1月23日 This work concentrates on the energy consumption and grinding energy efficiency of a laboratory vertical roller mill (VRM) under various operating parameters For design of experiments (DOE), the response surface method Analysis and Optimization of Grinding Performance of
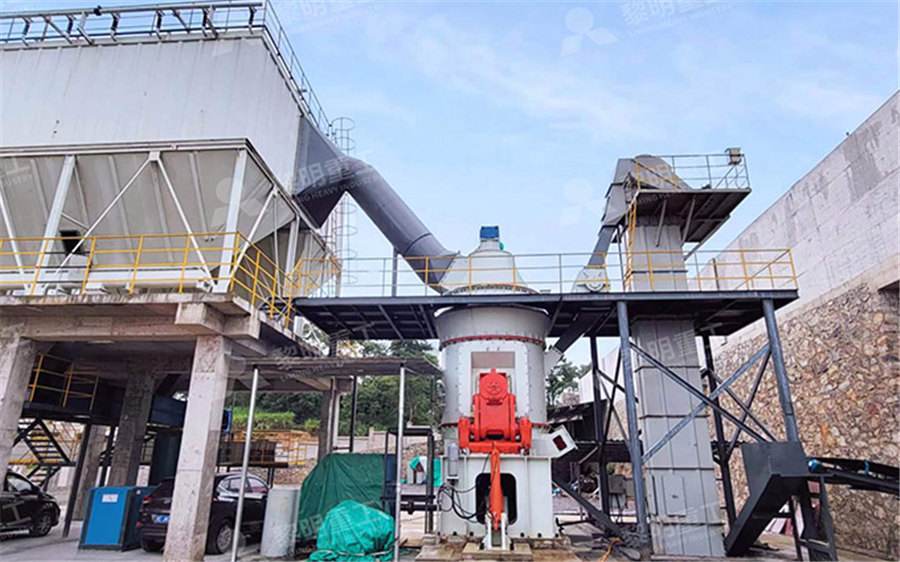
Solid Edge’s Application in Vertical Mill Design Springer
Vertical grinding is an indispensable key equipment for cement industry grinding system, the performance of the vertical mill depends on the design of its internal structural parameters, The VRM is a type of grinding mill integrated with multi functions such as grinding, drying and separation, used for grinding of coal, petroleum coke and minerals Most recently this PROCESS CONTROL FOR CEMENT GRINDING IN VERTICAL link of the main components of vertical mill, carried out the antijamming analysis, and solved the problems in the assembly, overall design of vertical mill was completed well and achieved the expect of design Fig 6 Vertical roll grinding explosion Fig 7 Vertical grinding structure Solid Edge’s Application in Vertical Mill Design 1101Solid Edge’s Application in Vertical Mill Design Springer2023年12月1日 The vibration of the rolling mill has been a persistent issue affecting its safe and stable operation To address the vibration problem in the F2 stand of a continuous rolling mill, this paper establishes a digital twin model of the rolling mill Based on the digital twin model, a rolling mill virtual commissioning framework has been proposed to enhance the accuracy of realtime Virtual commissioning and process parameter optimization of
.jpg)
Surface Grinder Types of Grinders How They Work
2021年1月16日 Your Single Disc Surface Grinding Machine will look like a horizontal spindle surface grinding machine albeit smaller in size since it does not need a reciprocating or circular table The grinding action in your machine 2024年6月14日 The grinding process plays a crucial role in industry, allowing for the reduction of particle sizes of raw materials and substances to the required fineness—either as a finished product or for further technological processes The high demand for micro and nanopowders or suspensions is associated with the high energy consumption of the milling process Therefore, The Influence of the Grinding Media Diameter on Grinding 2020年8月12日 Vertical Coal Mill (VCM) is equipment for grinding and pulverizing coal into micron size Rotary kilns then use the powders as fuel burners The VCM has a housing section equipped with a lining An investigation of performance characteristics and energetic 2021年5月5日 The grinding wheel reciprocate called a roll grinder cylindrical grinders are identified by the maximum diameter and length of the workpiece that can be ground similar to engine lathes In universal grinders, both the workpiece and the wheel axes can be moved and swiveled around a horizontal plane permitting the grinding of tapers and other shapesGrinding Machine: Definition, Parts, Working Principle, Operation
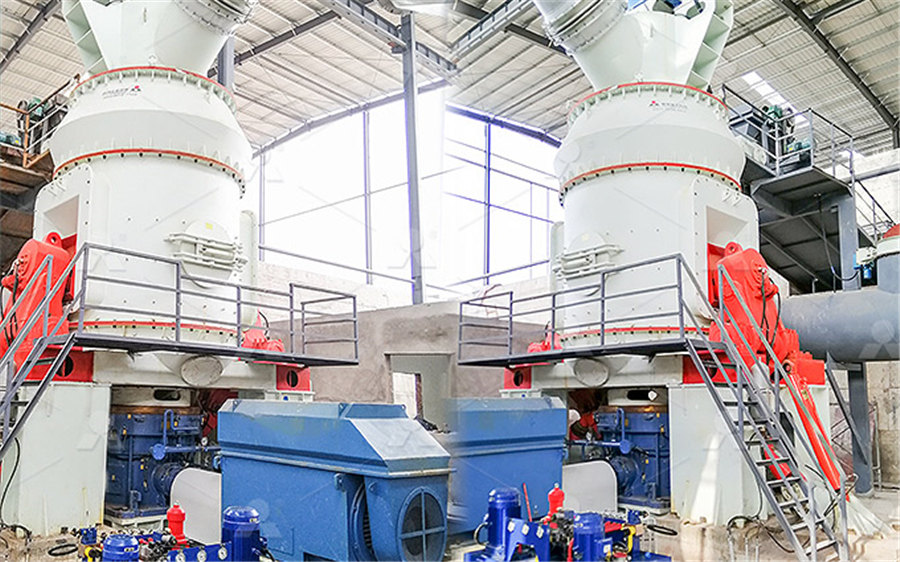
Grinding in Ball Mills: Modeling and Process Control
2012年6月1日 sizes of the balls ranging from 10 to 150 mm in diameter Mathematical models based on energybalance equations are also used approach is most frequently used in ball mill grinding circuits2021年4月24日 Based on the motion of the grinding media in stirred media mills with disc stirrer different grinding mechanisms are possible: product particles can be stressed by grinding media which are Predicting the effect of operating and design variables in grinding 2020年3月15日 In this work the grinding media motion inside a vertical stirred mill was investigated using the Discrete Element Method (DEM) and the results were qualitatively compared against similar conditions from published literatureInvestigating grinding media dynamics inside a vertical stirred mill 2023年10月27日 The ball mill is a rotating cylindrical vessel with grinding media inside, which is responsible for breaking the ore particles Grinding media play an important role in the comminution of mineral ores in these mills This work reviews the application of balls in mineral processing as a function of the materials used to manufacture them and the mass loss, as A Review of the Grinding Media in Ball Mills for Mineral
.jpg)
The impact of different stirrer designs and mill orientations on the
2024年4月1日 The current chapter presents the performances of the grinding of four varied stirrer types with identical diameters based on the outcomes obtained from the vertical orientation of the mill Fig 8 depicts the variation in the d 50 values with respect to SI GM , namely varied stirrer velocities and media sizes while maintaining a 750 kJ/kg constant E i Grinding and separation efficiency of vertical roller mill were evaluated In addition to these, performance figures of vertical roller mill and conventional closed ball mill circuit were comparedPerformance Evaluation of Vertical Roller Mill in Cement Grinding2013年1月1日 Principles of Modern Grinding Technology explains the principles that led to rapid improvements in modern grinding technology over recent decadesPrinciples of Modern Grinding Technology2022年6月24日 Ni J, Yang Y, Wu C Assessment of waterbased fluids with additives in grinding disc cutting process J Clean Prod 2019; 212: 593–601 Crossref Google Scholar 149 Singh H, Sharma VS, Singh S, et al Nanofluids assisted environmental friendly lubricating strategies for the surface grinding of titanium alloy: Ti6Al4VELIA comprehensive review on the grinding process: Advancements
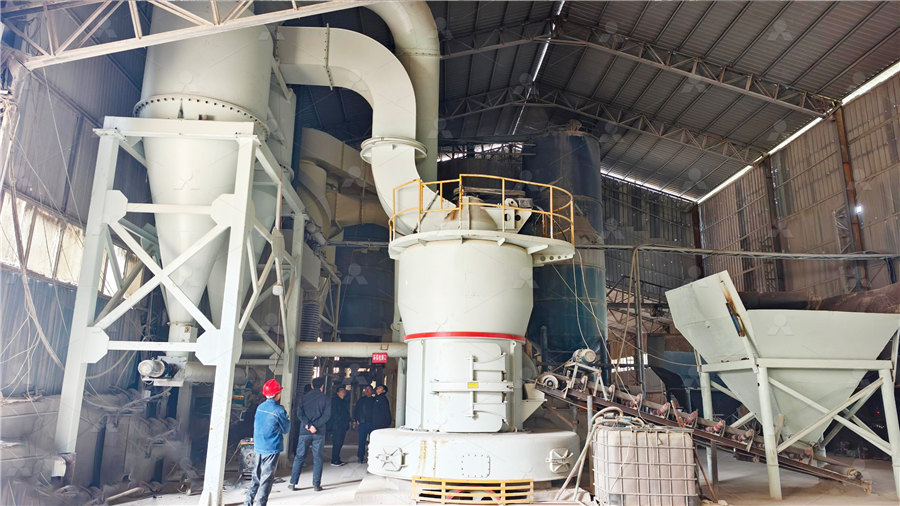
Optimisation of the performance of a new vertical roller mill by
2024年1月15日 An industrialscale vertical roller mill (M600) was analysed for air flow in this study This led to proposed modifications, which were implemented in a new mill design (M350) The M600 mill can operate under continuous mode and is used for fine grinding of materials The design of this mill is depicted in Fig 12021年6月17日 Due to its strong lifting capacity and excellent grinding performance, the trapezoidal liner is widely used in the SAG mill The structure of the trapezoidal liner is shown in Fig 1, the main dimensions are: dip angle \(\tau\), length of the top edge \(L\) and height \(h\)Dip angle \(\tau\) determines the trajectory of the mediums in the SAG mill, which directly affects PARAMETER OPTIMIZATION OF LARGE SAG MILL LINER BASED 2019年9月6日 The grain geometrical features of grinding wheels are critically important to evaluate their quality and grinding performance Therefore, grain geometrical features should be comprehensively and systematically characterized Such characterization parameters were defined from the geometric features of individual grains (for each grain) to the distribution Characterization of grain geometrical features for monolayer 2023年12月21日 where C is the density of the grinding grain and r is the widthtothickness ratio of the chip In Malkin’s model, the maximum UCT was based on the uniform location distribution and grain size Under these assumptions, the calculated UCT was estimated to be 02~1 μm [], 06 μm [] or 03~098 μm [], and less than the critical depth of plowingcutting transition (1~2 A multiscale model revealed in the grinding process and its
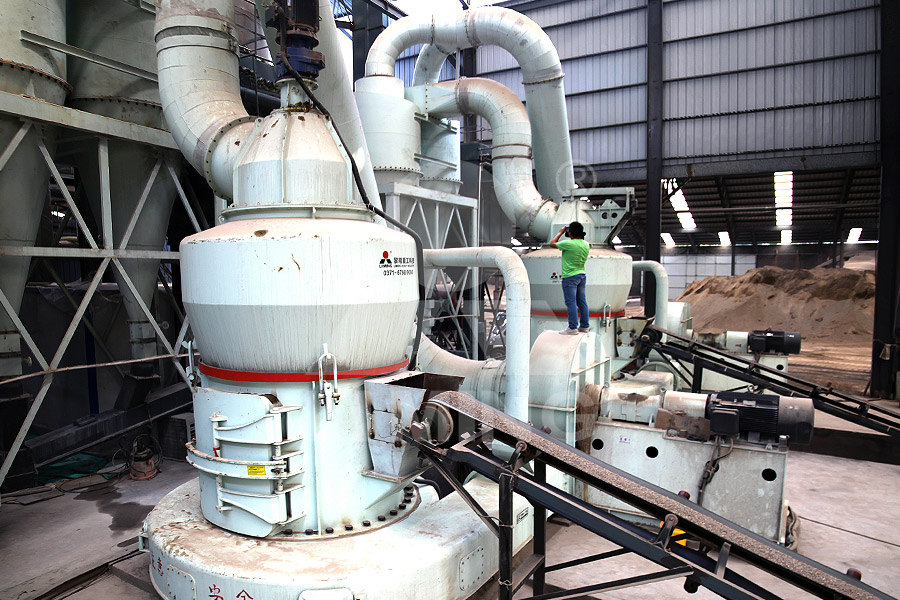
Vertical roller mill for raw Application p rocess materials
Recently, the vertical roller mill having great grinding performance is widely applied to the raw material grinding process However, tube mill, which has about 30% poor grinding performance as power consumption, has been still used many existing cement plant The improvement of this tube mill grinding system is highly expected DescriptionsFig 1 Flowsheet of modular vertical roller mill 5000 R4 The required throughput rates were achieved in short time All fineness figures met the target values as well without anyGrinding Process Optimization Featuring Case Studies and 2021年1月1日 Grinding Mill Vertical Roller Mill or Ball Mill: The reclaimed raw mix fed to Raw Mills, for drying and fine grinding of Raw meal for kiln feed: 4: Coal Grinding: Grinding Mill Vertical Roller Mill or Ball Mill: Coal is ground in Coal mill, which is a fuel for use in Kiln firing: 5: Pyro Section, Clikerization: In line calciner six stage Review on vertical roller mill in cement industry its It is known that the variable is strong coupling, nonlinear, multivariable and large timedelay dynamic characteristics in the raw cement vertical mill grinding process Against the problem which is difficult to establish accurate mathematical model, this paper establishes a production index prediction model of vertical mill raw meal grinding process by using echo state network Modelling of the vertical raw cement mill grinding process based
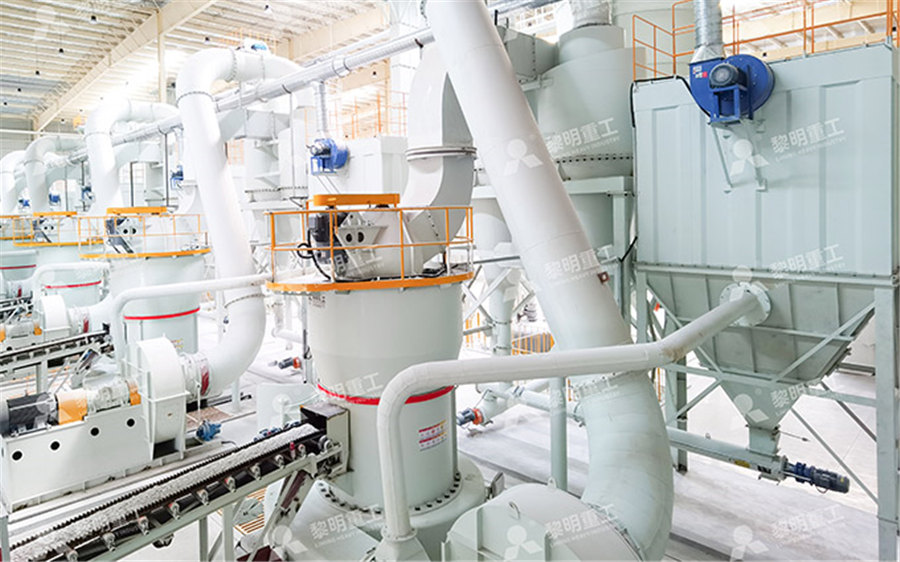
Predicting the grinding energy of vrm depending on material
2021年9月1日 Another study will address the feed size effect extensively As a consequence of this study, an energysize reduction equation was derived for the pilotscale vertical roller mill and this study has shown that it is possible to estimate the specific grinding energy of the vertical roller mill based on a laboratory characterization test2020年11月4日 Based on the DPM (Discrete Phase Model) and continuous phase coupling model, the flow field characteristics in the vertical roller mill including the velocity and pressure fields and the discrete Effects of Blade Parameters on the Flow Field and Classification 2023年7月19日 Schematic diagram of the main machine of pendulum mill 1 – Shall; 2 – Particles inlet; 3 – Returnair duct; 4 – Air inlet; 5 – Base; 6 – Support frame; 7 – Rollers; 8 – Grinding Research of grinding efficiency and main duct wear of pendulum mill 2023年4月23日 pending on the process parameters which are fill rate, mill spe ed, ball diameter, ball shape and grinding time [41] In the ball mill, friction is formed due to the difference between surfa ces (PDF) Grinding Media in Ball MillsA Review ResearchGate
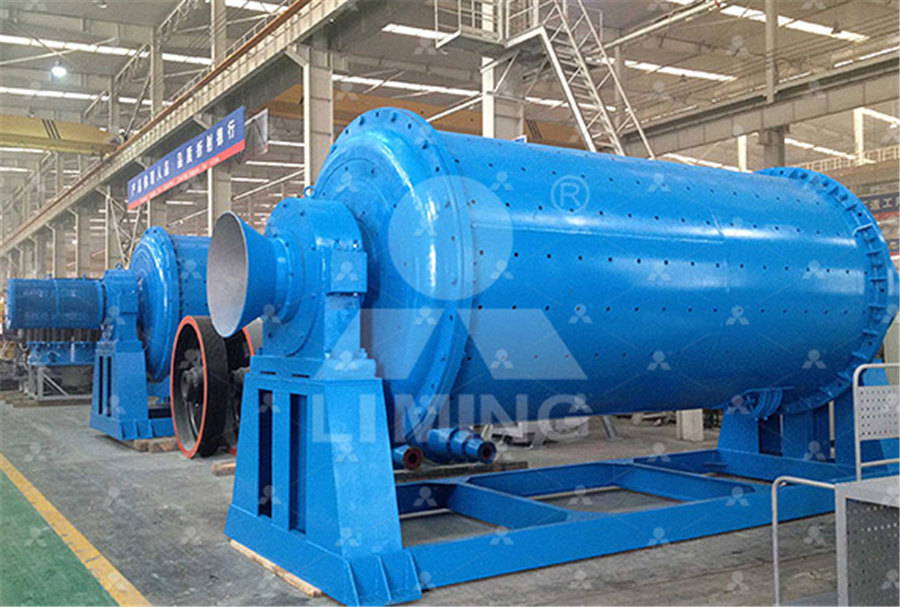
Guide about Grinding Wheels Types, Material Specifications
2021年4月7日 Selection of grinding wheels is challenging task for every manufacturer That is why our abrasive experts summarized this this process in simple words to help you into making informed decision while selecting different types of grinding wheel based on material, specifications The various choices for the following include:2024年9月1日 The vertical stirred mill, as key grinding equipment, is widely used for the fine and ultrafine grinding of minerals, ceramic materials, chemical products, and others [1]The main structure of the vertical stirred mill includes a frame, a driving device, a cylinder, and a helical agitator, which drives the slurry and grinding media inside the vertical stirred mill to grind Performance analysis of vertical stirred mill based on multi June 2022; ARCHIVE Proceedings of the Institution of Mechanical Engineers Part C Journal of Mechanical Engineering Science 19891996 (vols 203210) 236(2):1107(PDF) A comprehensive review on the grinding process: 2021年4月21日 The purpose of this study was to investigate the dry grindability of calcite powders in a vertically and horizontally orientable laboratory batch type stirred mill The experimental results were evaluated using stress intensity analysis The performance was also compared in terms of mill orientation The results showed that the d50 values decreased with The Influence of Stirred Mill Orientation on Calcite Grinding
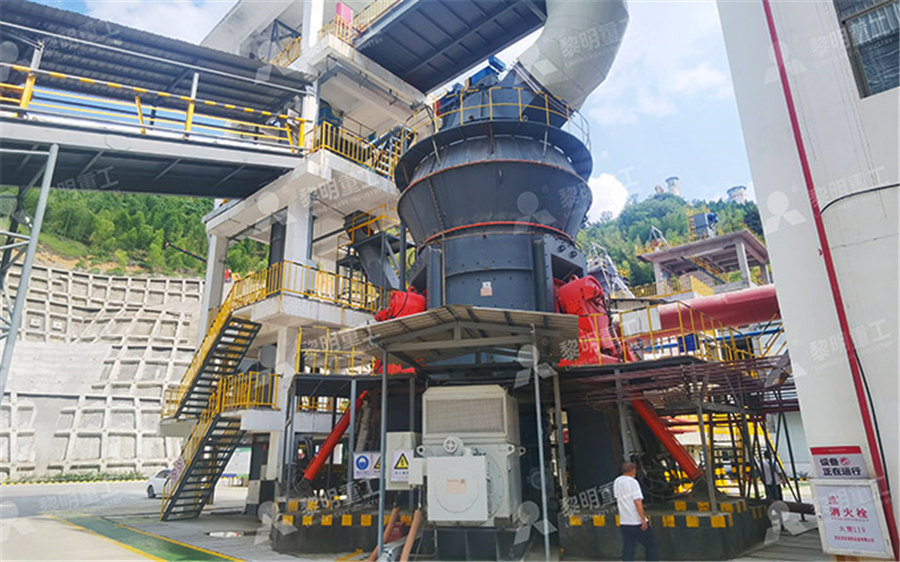
Electromechanical coupling characteristics analysis of vertical
2024年1月15日 DEM [[28], [29], [30]], as a specialized approach for studying particle dynamics, has been widely employed by researchers to simulate the operational processes of stirred mills and the dynamic behaviour of grinding media inside the millSinnott et al [31] conducted a study on tower mills and pin mills, utilizing threedimensional DEM simulations to analyse the flow 2023年12月4日 A vertical roller mill (VRM) is a grinding equipment used for the size reduction of minerals, cement, and ceramics The capacity of the VRM depends not only on the grinding material properties but also on the operational parameters of the VRM This study investigatedNumerical Investigation of Vertical Roller Mill Operation Using The performance of a ball mill is highly dependent on its specifications, which determine the grinding efficiency and quality of the final product 1 Mill Diameter and Length: The diameter and length of the ball mill are the primary dimensions that define its capacity and performanceUnderstanding ball mill specifications for optimal performance2022年5月31日 Mineral crushing is the main source of energy consumption in mineral processing According to statistics, this consumption accounts for about 35–50% of the total cost of the mine (Curry et al, 2014), or even higherIt may also account for 18% of the global electrical energy consumption (NapierMunn, 2015)More efficient crushing equipment needs to be Analysis of vertical roller mill performance with changes in
.jpg)
Basic specifications of the rolling mill Download Table
The following calibration scheme for rolling round steel is used for producing thermally hardened grinding balls with a diameter of 40 mm at JSC SSGPO for 320 variety rolling mill: a round billet 2024年1月27日 This involves selecting the right grinding wheel based on the material of the workpiece Factors like wheel diameter, abrasive material, and grit size are critical considerations Securing the Workpiece: The workpiece is then securely mounted on the machineWhat is a Grinding Machine: Definition, Types, Components2021年7月12日 The plots in Fig 2 are in good agreement with Kadivar et al [] and Sadeghi et al [] outputsFigure 2 suggests that the depth of cut (a e) is the most influential parameter on the normal grinding force in the chosen rangeOther input parameters such as cutting speed and feed speed are in the next orders As depicted in Fig 2, the highest grinding wheel speed (35 m/s) Development of an expert system for optimal design of the grinding The mill itself consists of a rotating disk with 4 grinding pins at its periphery and an impeller wheel classifier integrated into the top section of the mill chamber The diameter of the grinding disk is 200 mm and the one of the classifier is 100 mm Both parts rotate with a (PDF) Grinding in an air classifier mill Academia
.jpg)
14 Types of Grinding Machines [Working, Diagram PDF] The
2021年11月23日 These grinders are used for grinding round and hollow jobs whether the internal surface of this job is completely round, ditched round, or is in taper Small grinding wheels of 3 cm to 5 cm, are used in such grinders Sometimes grinding wheels of special shape 02 cm to 03 cm These grinders can be divided into two parts a Chucking Grinder2022年5月28日 Internal Grinding Internal grinding or inner diameter (ID) grinding is used to grind the inner diameter of holes in parts It uses a tiny highspeed grinding wheel to work on tubular or cannular parts The high speed applied helps to keep up the proper surface speed A chuck or collet holds the workpieces in position during the operationPrecision Grinding: Understanding the Principle, Types, and