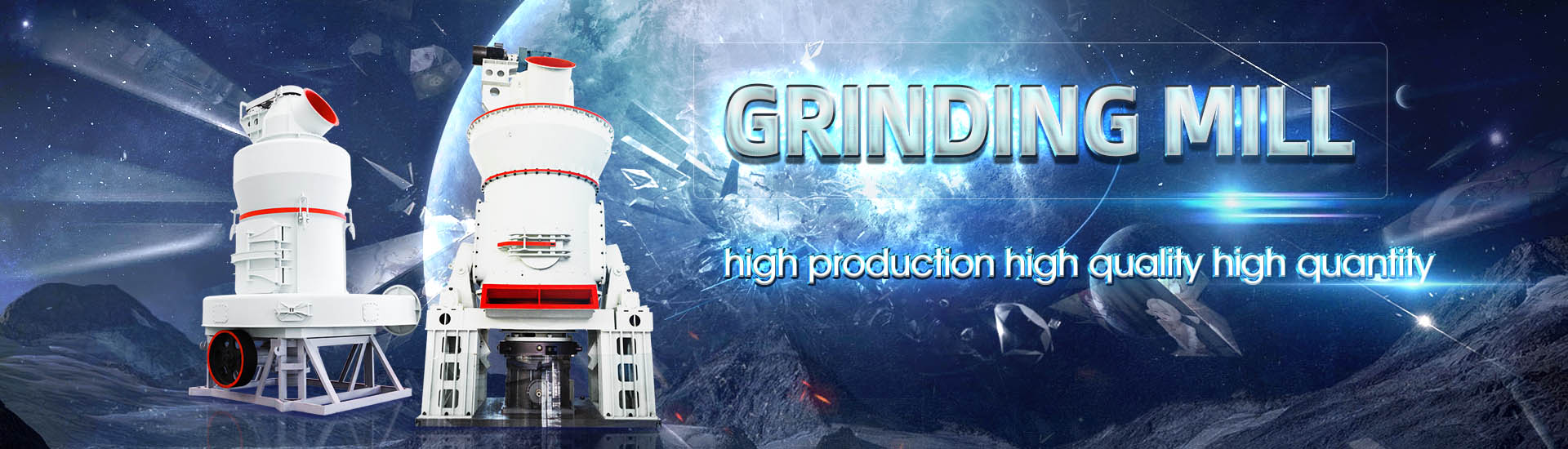
Production of energy consumption indicators of compound pendulum ore grinding mill
.jpg)
Predicting Grinding Mill Power Consumption in Mining: A
These methods offer valuable insights to improve the overall energy efficiency of grinding mills in mining In this article, a comparative study is conducted to investigate the use of machine 2022年6月25日 In this article, a literature review on the application of artificial intelligence models to predict the energy consumption of grinding mills has been conducted This research Predicting energy consumption of grinding mills in mining On the basis of experimental data, in terms of production and processing production show based on the power consumption of the mill motor when working on the ores of different composition Experimental studies of energy technology indicators during ore 2023年12月1日 In this study, we (i) provide the first bottomup assessment of the mining industry’s final energy consumption globally (1971–2015), (ii) use 15°C consistent socio Global energy consumption of the mineral mining industry:
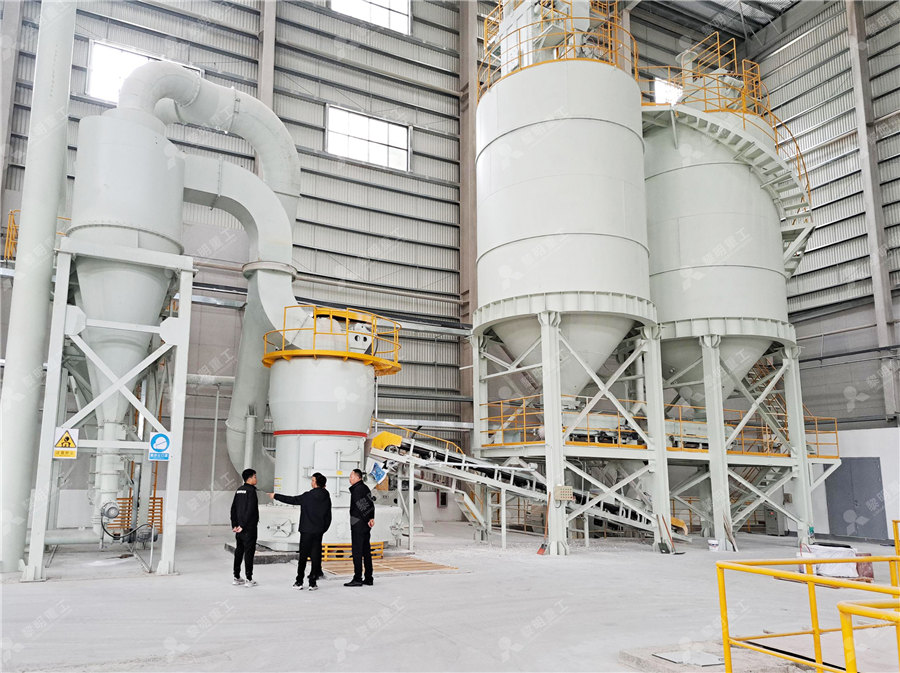
Predicting energy consumption of grinding mills in mining
2023年1月1日 The sensitivity analysis of the GANN model shows that the work index, inlet water to the SAG mill, mill load cell weight, SAG mill solid percentage, mass flowrate and feed 2013年12月18日 Fine grinding, to P80 sizes as low as 7 μ m, is becoming increasingly important as mines treat ores with smaller liberation sizes This grinding is typically done using stirred mills such as the Isamill or Stirred Energy Use of Fine Grinding in Mineral Processing2017年1月17日 This paper reports the results of an investigation targeting two objectives: (1) characterising energy outputs in industrial grinding mill circuits, and (2) identifying the potential forBreaking down energy consumption in industrial 5 天之前 This paper reports the results of an investigation targeting two objectives: (1) characterising energy outputs in industrial grinding mill circuits, and (2) identifying the potential Breaking Down Energy Consumption in Industry Grinding Mills
.jpg)
Energy efficiency of stateoftheart grinding processes
2018年1月1日 Specific energy consumption was determined as a function of material removal rate and compared to results of milling and turning processes The key influence factors on 2016年1月1日 The Ball Mill Abrasion (BMA) test was developed by the University of Queensland Materials Performance group to simulate the high stress abrasion conditions experienced in production ball mills(PDF) A comparison of wear rates of ball mill 2021年2月26日 Milling is among the most energyconsuming technological stages of copper ore processing It is performed in mills, which are machines of high rotational masses The start of a mill filled to capacity requires Energy Efficiency Analysis of Copper Ore Ball Mill 2022年3月15日 The grinding efficiency is a function of the quality of the final product, the energy (kWh), and the power (kW), which are used to determine the energy consumption of the mill [4] (PDF) Power consumption management and
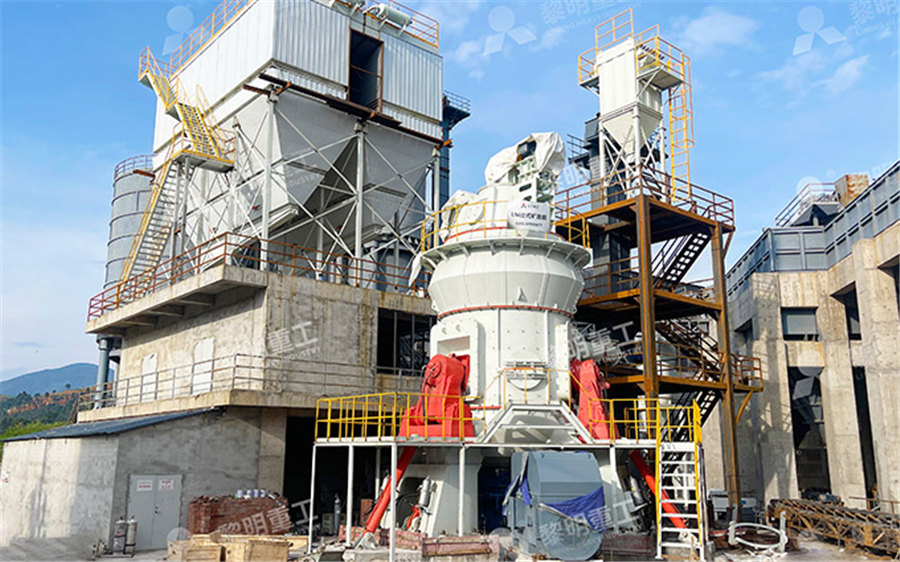
Research of iron ore grinding in a verticalrollermill
2015年3月15日 Coals used for power plants normally have different ash contents, and the breakage of coals by the ballandrace mill or roller mill is an energyintensive process Grinding phenomena in mill of 2013年12月18日 Fine grinding, to P80 sizes as low as 7 μm, is becoming increasingly important as mines treat ores with smaller liberation sizes This grinding is typically done using stirred mills such as the Isamill or Stirred Media Detritor While fine grinding consumes less energy than primary grinding, it can still account for a substantial part of a mill’s energy budget Overall Energy Use of Fine Grinding in Mineral Processing2022年5月9日 Cement production is one of the most energyintensive manufacturing industries, and the milling circuit of cement plants consumes around 4% of a year's global electrical energy production It is Modeling of energy consumption factors for an industrial 2021年3月23日 The energy performance analysis of the three solutions was based on the average energy consumption indicator per mass unit of the milled material and on the energy consumption per hourEnergy Efficiency Analysis of Copper Ore Ball Mill Drive
.jpg)
Energy consumption of twostage fine grinding of Douglas
2018年3月12日 The specific energy consumption increased with the decrease of median particle sizes, with a transition at around 100 µm after which the energy consumption increased exponentially This largescale grinding trial provides the reliable energy consumption data for design and process economic analysis of mechanical biomass preprocessing2018年3月29日 Comparison of dry and wet grinding process in an electromagnetic mill is presented in this paper The research was conducted in a batch copper ore grinding Batch mode allows for precise parametrization and constant repetitive conditions of the experiments The following key aspects were tested: processing time, feed size, size of the grinding media, Comparison of Wet and Dry Grinding in Electromagnetic Mill MDPI2012年6月1日 Cement production in the world is currently about 16 billion ton per year About 2% of the electricity produced in the whole world is used during the grinding process of raw materials [1]While total electrical energy consumption for cement production is about 100 kWh/ton of cement, roughly two thirds are used for particle size reduction [2] Reducing energy consumption of a raw mill in cement industry2016年1月1日 The proposed model for determining the power consumption of a ball mill allows an assessment of the efficiency of electric energy consumption and electric mills identify qualitative indicators of Modeling of power consumption of ball mill Request PDF
.jpg)
An investigation of performance characteristics
2020年8月12日 This study shows the performance of a currently running vertical roller coal mill (VRM) in an existing coalfired power plant In a power plant, the coal mill is the critical equipment, whose 2016年4月25日 Keeping the vibration values on the main driving motors less than 4 mm/s by periodical maintenance, the specific electrical energy consumption of the mill has reduced by 216% to 2497 kWh/ton Determination of correlation between specific The HC vertical pendulum mill is a technical update based on the Rtype mill The technical indicators of this product have been greatly improved compared with the Rtype mill It is a new type of highefficiency and energysaving mill The fineness of the finished product can be adjusted arbitrarily between 22180μm (80600 mesh)HC series pendulum mill HCM Grinding Mill2023年7月19日 Pendulum mill is a widely used grinding equipment in powder processing industry Less indepth studies have been carried out especially for grinding efficiency and wear so the choice of spindle speed should consider both grinding efficiency and energy consumption The spade degree determines the spade position, the closer the spade is to Research of grinding efficiency and main duct wear of pendulum mill
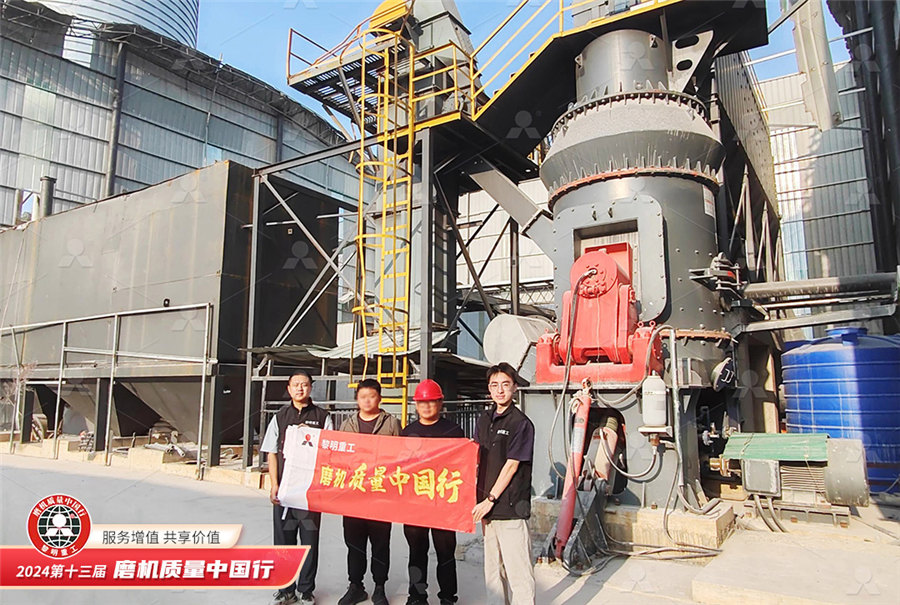
Research of grinding efficiency and main duct wear of pendulum mill
2023年7月19日 Pendulum mill is a widely used grinding equipment in powder processing industry Less indepth studies have been carried out especially for grinding efficiency and wear2021年9月5日 Size reduction is a necessary operation in mineral processing plants and provides the desired size for separation operations and the liberation of the valuable minerals present in ores Estimations on energy consumption indicate that milling consumes more than 50 % of the total energy used in mining operations Despite the fact that ball milling is an efficient Modeling of Bauxite Ore Wet Milling for the Improvement of 2003年1月1日 A correlation between required energy and fineness of grind in comminution is obtained by considering the process over the full range from primary crushing to the production of ultrafine The Effects of Blasting on Crushing and Grinding Efficiency and Energy 2012年12月1日 The inmill load volume and slurry solids concentration have significant influence on the ball mill product size and energy expenditure Hence, better energy efficiency and quality grind can only (PDF) Optimization of inmill ball loading and slurry solids
.jpg)
(PDF) Grinding of Australian and Brazilian Iron Ore Fines for
2024年2月26日 Furthermore, ore blending can reduce grinding energy consumption and improve settling and filtration rates, and the addition of finely ground Australian ores improves the balling performance of 2011年1月1日 In this paper a new digital energy meter is being evaluated as a means of measuring the energy required to grind ore in the Bond mill and to test if the results are consistent with Bond's original Measurement of electrical energy consumption Prediction and optimization of tower mill grinding power consumption based on GABP neural network Ziyang Wang 1, Ying Hou 1, Ahmed Sobhy 2,3 was used in a comminution circuit instead of the energyinefficient ball mill in the copperleadzinc ore processing plant after the primary jaw crusher, secondary cone crusher, and tertiary highpressurePrediction and optimization of tower mill grinding 2016年10月5日 In this chapter an introduction of widely applied energyefficient grinding technologies in cement grinding and description of the operating principles of the related equipments and comparisons over each other in EnergyEfficient Technologies in Cement
.jpg)
Hybrid nonlinear model predictive control of a runofmine ore
2018年7月1日 A hybrid nonlinear model predictive controller (HNMPC) is developed for a runofmine ore grinding mill circuit A continuoustime grinding mill circuit model is presented with a hydrocyclone 2023年7月31日 operation (1) Structure parameters of grinding mill, including its specifications, model, aspect ratio, ore discharging method, and liner form (2) Various working parameters of grinding mill, including fraction of critical speed for grinding mill, filling rate for grinding mill, grinding concentration,grindingcycleload,etc(3)AndgrindOre Grinding Methods and Process of Ore Grinding2014年3月1日 In [2, 36] it was experimentally shown that the lowest energy consumption of dry grinding of cement clinker, limestone, and quartz in a ball mill is achieved at ψ ω = 055 In work [36], the (PDF) Analysis of ball mill grinding operation using mill power 2020年12月21日 Tumbling mills have been widely implemented in many industrial sectors for the grinding of bulk materials They have been used for decades in the production of fines and in the final stages of ore Increasing Energy Efficiency and Productivity of the
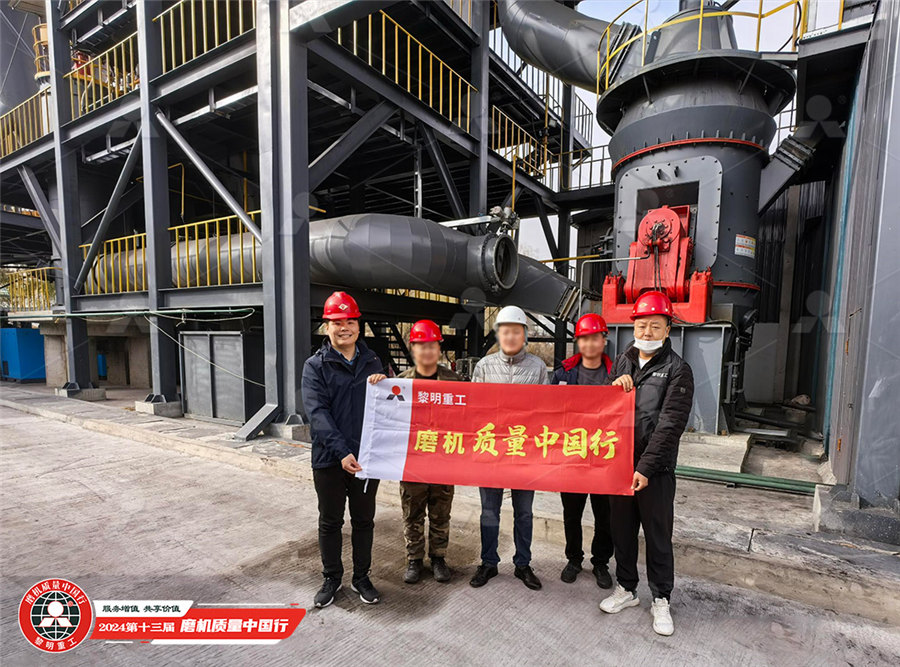
Analysis and Optimization of Grinding Performance of
2022年1月23日 This work concentrates on the energy consumption and grinding energy efficiency of a laboratory vertical roller mill (VRM) under various operating parameters2023年7月4日 The vertical roller mill has the advantages of low energy consumption, high output, easy maintenance, etc, and has been widely applied in cement, steel and power industry, the preparation of nonmetallic ore ultrafine powder, manganese ore fine grinding, and other fields Horizontal Cylinder Roller MillRoller Mill Springer2020年9月20日 The history of grinding aids in dry fine grinding processes starts in the late 1930s with the application of the first commercial grinding aids in the cement industry [1]Since that time, the importance of grinding aids in industrial dry fine grinding processes has strongly increased; so did the number of scientific papers dealing with this topicGrinding aids for dry fine grinding processes ScienceDirect2016年1月1日 The Ball Mill Abrasion (BMA) test was developed by the University of Queensland Materials Performance group to simulate the high stress abrasion conditions experienced in production ball mills(PDF) A comparison of wear rates of ball mill
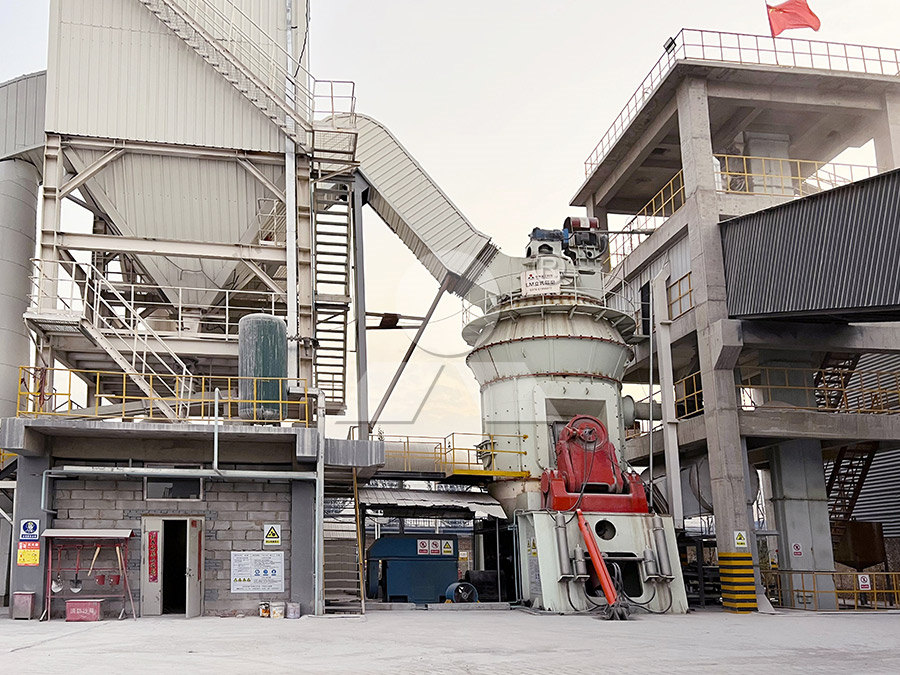
Energy Efficiency Analysis of Copper Ore Ball Mill
2021年2月26日 Milling is among the most energyconsuming technological stages of copper ore processing It is performed in mills, which are machines of high rotational masses The start of a mill filled to capacity requires 2022年3月15日 The grinding efficiency is a function of the quality of the final product, the energy (kWh), and the power (kW), which are used to determine the energy consumption of the mill [4] (PDF) Power consumption management and 2015年3月15日 Coals used for power plants normally have different ash contents, and the breakage of coals by the ballandrace mill or roller mill is an energyintensive process Grinding phenomena in mill of Research of iron ore grinding in a verticalrollermill2013年12月18日 Fine grinding, to P80 sizes as low as 7 μm, is becoming increasingly important as mines treat ores with smaller liberation sizes This grinding is typically done using stirred mills such as the Isamill or Stirred Media Detritor While fine grinding consumes less energy than primary grinding, it can still account for a substantial part of a mill’s energy budget Overall Energy Use of Fine Grinding in Mineral Processing
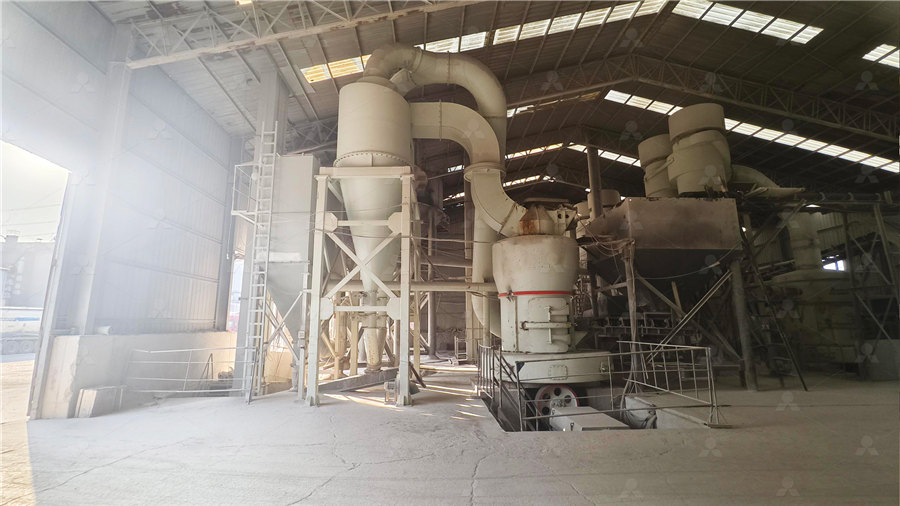
Modeling of energy consumption factors for an industrial
2022年5月9日 Cement production is one of the most energyintensive manufacturing industries, and the milling circuit of cement plants consumes around 4% of a year's global electrical energy production It is 2021年3月23日 The energy performance analysis of the three solutions was based on the average energy consumption indicator per mass unit of the milled material and on the energy consumption per hourEnergy Efficiency Analysis of Copper Ore Ball Mill Drive 2018年3月12日 The specific energy consumption increased with the decrease of median particle sizes, with a transition at around 100 µm after which the energy consumption increased exponentially This largescale grinding trial provides the reliable energy consumption data for design and process economic analysis of mechanical biomass preprocessingEnergy consumption of twostage fine grinding of Douglas 2018年3月29日 Comparison of dry and wet grinding process in an electromagnetic mill is presented in this paper The research was conducted in a batch copper ore grinding Batch mode allows for precise parametrization and constant repetitive conditions of the experiments The following key aspects were tested: processing time, feed size, size of the grinding media, Comparison of Wet and Dry Grinding in Electromagnetic Mill MDPI
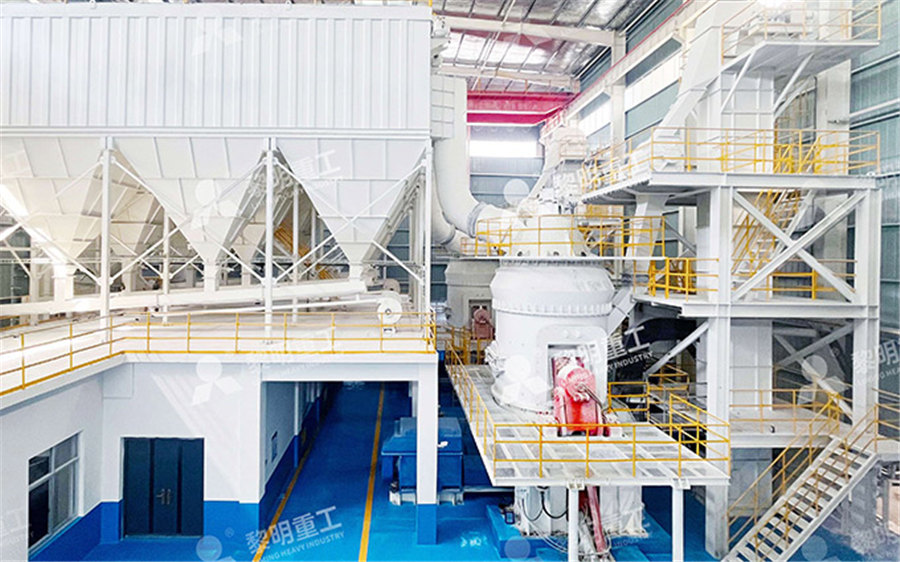
Reducing energy consumption of a raw mill in cement industry
2012年6月1日 Cement production in the world is currently about 16 billion ton per year About 2% of the electricity produced in the whole world is used during the grinding process of raw materials [1]While total electrical energy consumption for cement production is about 100 kWh/ton of cement, roughly two thirds are used for particle size reduction [2]