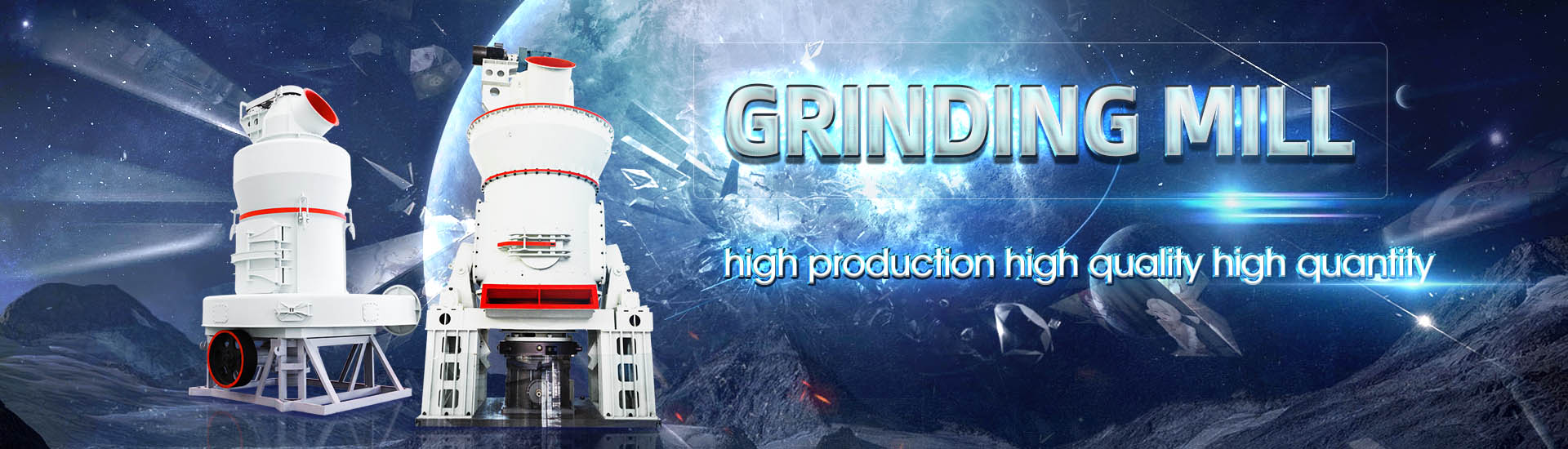
HOME→Flue gas desulfurization equipment procurement Flue gas desulfurization equipment procurement Flue gas desulfurization equipment procurement
Flue gas desulfurization equipment procurement Flue gas desulfurization equipment procurement Flue gas desulfurization equipment procurement
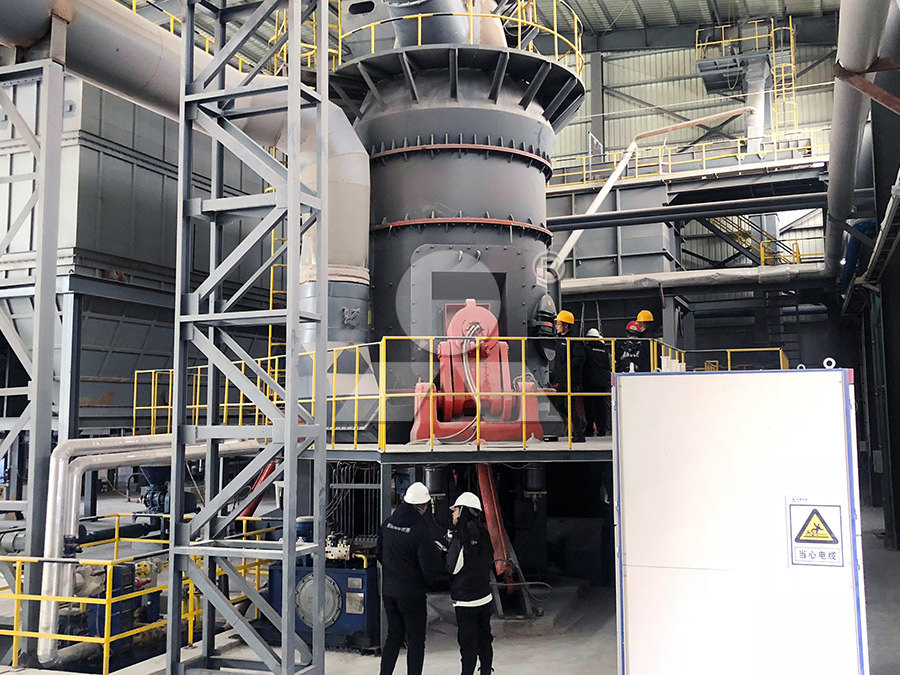
Summary of research progress on industrial flue gas
2022年1月15日 Through the purification technology of flue gas desulfurization, ultralow emissions of SO 2 flue gas in industrial flue gas can be achieved This article involves dry 2022年12月1日 This research offers a new fluegas integrated desulfurization and denitrification technology The mass transfer area of the gasliquid phase is increased by the coupling effect Simultaneous desulfurization and denitrification of flue gas 2015年7月27日 The various flue gas desulfurization (FGD) technologies available in the market, for the reduction of sulfur dioxide emissions, are presented The process descriptions are Review of Design, Operating, and Financial Considerations in Flue Gas Sodiumbased dry desulfurization technology is widely used in the flue gas desulfurization processes of blast furnace hot stoves, heating furnaces, coke ovens, and gas boilers due to its Recent advances in process and materials for dry desulfurization
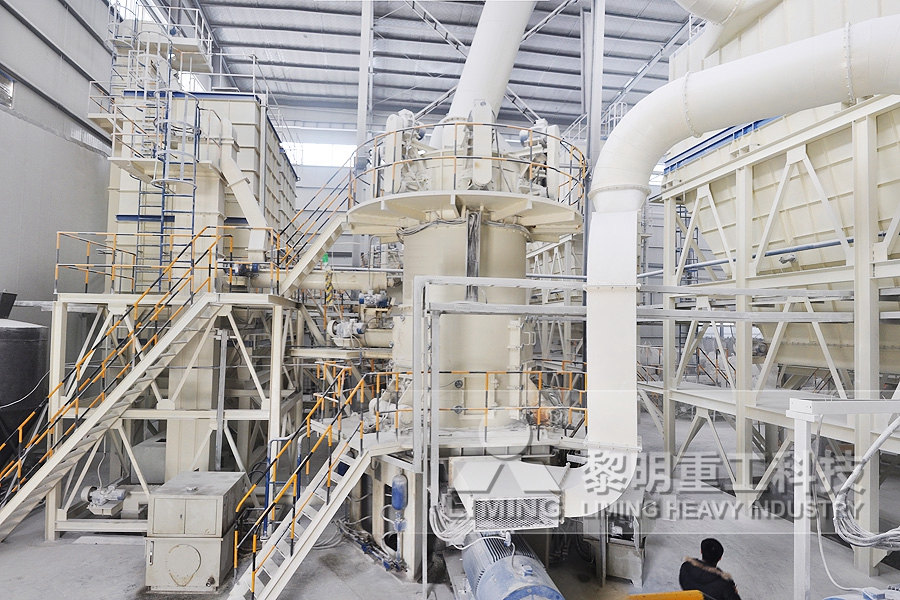
Sulfur dioxide removal: An overview of regenerative flue gas
2020年5月16日 In this paper, various processes of existing and emerging reversible SO 2 emission control focusing on flue gas desulfurization will be studied The details of each 2020年8月15日 Postcombustion flue gas desulfurization and denitrification technologies are essential in achieving the full compliance of fine particulate matter (PM 25, aerodynamic Comprehensive evaluation of flue gas desulfurization and 2020年8月27日 Addressing climate change may require rapid global diffusion of Carbon Capture and Storage (CCS) To understand its potential diffusion, we analysed a historical analogy: Diffusion of flue gas desulfurization reveals barriers and 2024年2月12日 The flue gas analysis system is employed to measure the composition and concentration of pollutants in the postpurification flue gas Ultimately, the purified flue gas is Experimental study on integrated desulfurization and
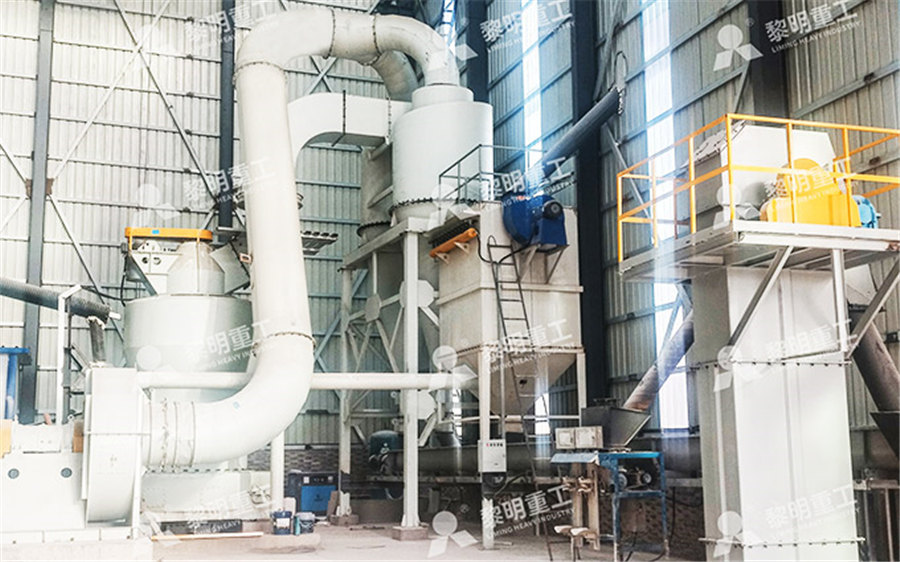
(PDF) Flue Gas Desulfurization: The State of the
2002年1月1日 This paper presents a comprehensive review of the state of the art in flue gas desulfurization (FGD) technologies for coalfired boilers Data on worldwide FGD applications reveal that wet1 天前 Flue gas desulfurization (FGD) technologies play a critical role in the reduction of oxides of sulfur (SO x) emissions from coalfired power plants, a significant source of air pollution and Performance Evaluation of SemiDry Flue Gas Desulfurization Currently, desulfurization technologies can be categorized into three main types: wet flue gas desulfurization (FGD) [11], [12], [13], semidry desulfurization [14] and dry desulfurization [15]Wet flue gas desulfurization is widely employed in largescale desulfurization processes due to its high efficiency and low energy consumption [16]However, it poses a significant environmental Recent advances in process and materials for dry desulfurization 2024年2月12日 Experiment system As depicted in Fig 1, the simulated flue gas experimental system is primarily designed for catalyst screening under laboratory conditionsThis experimental setup comprises a Experimental study on integrated desulfurization and
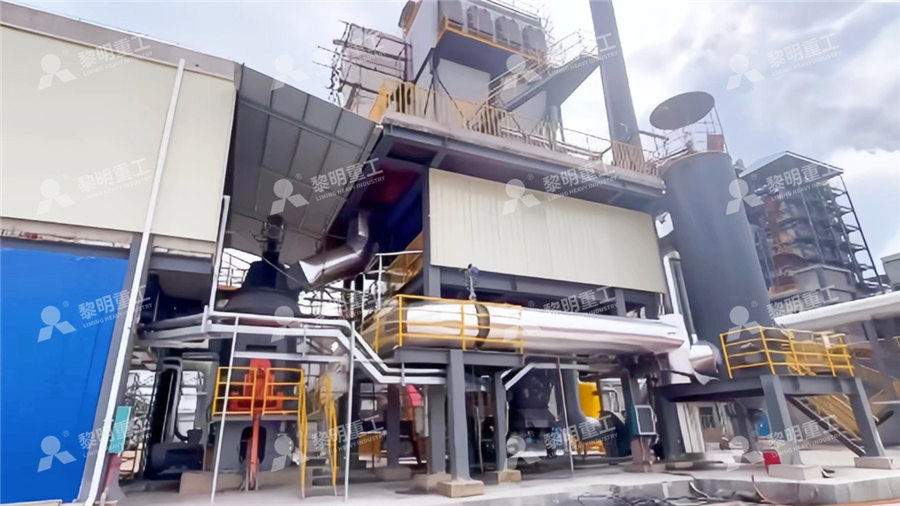
Flue Gas Desulfurization (FGD) Scrubber Systems
5 天之前 A flue gas desulfurization scrubber is a system designed to remove sulfur compounds from the airflow produced by industrial plants and power stations The method works through a chemical reaction between sulfur dioxide (SO₂) and an absorbent solution, usually lime or magnesiumbased, which results in the formation of neutral compounds such as 2020年2月7日 Wet flue gas desulfurization is widely used in power plants because of its high desulfurization efficiency The reason why it is difficult to predict sulfur dioxide removal efficiency in flue gas is that it is related to many factors In this paper, the SO2 was removed by absorbing with ammonia solution in a packed tower Experimental studies have shown that the operating Prediction of SO2 removal efficiency for ammoniabased wet flue gas 2002年1月1日 This paper presents a comprehensive review of the state of the art in flue gas desulfurization (FGD) technologies for coalfired boilers handling equipment, the concentrated waste is sent for (PDF) Flue Gas Desulfurization: The State of the Art [J]2018年12月1日 The design parameters of this wet FGD unit are listed in Table 1, and the simplified process flow chart of its five systems is shown in Fig 1As for the detailed process flow chart of the unit, it can be referred to the literature [31]Field investigation was performed in the sequence from the limestone preparation system and the boiler air and gas system in the Corrosion evaluation of one wet desulfurization equipment – Flue gas
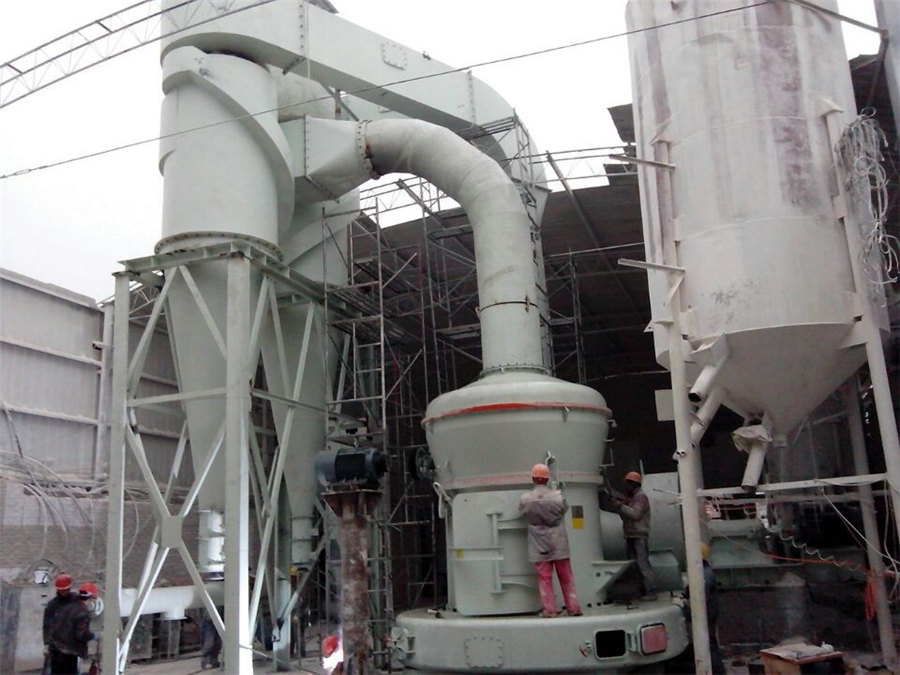
Best Flue Gas de Sulphurization System Solution Enquire
Your trusted partner in advanced Flue Gas Desulfurization (FGD) solutions At RIECO, we harness the power of innovation, engineering excellence, and rigorous research to deliver worldclass Flue Gas Desulfurization (FGD) systems With nearly half a century's experience in the air pollution control equipment and systems business, we have a Control and Treatment of Air Emissions Shahryar Jafarinejad, in Petroleum Waste Treatment and Pollution Control, 2017 515 FlueGas Desulfurization Fluegas desulfurization (FGD) is a scrubbing technique that uses an alkaline reagent (typically a sodium or calciumbased alkaline regent) to remove SO 2 from flue gas (TriState Synfuels Company, 1982; Tilly, 1983; FlueGas Desulphurization an overview ScienceDirect Topics2022年1月15日 In the industrial production of China, the processing of phosphate rock, volcanic eruptions, kerosene combustion and aluminum smelting will lead to flue gas emissions containing a large amount of SO 2SO 2 is a highly irritating gas Because SO 2 is freely soluble in water and enters the respiratory tract, it can generate corrosive sulfurous acid, sulfuric acid, and sulfate Summary of research progress on industrial flue gas desulfurization 2021年11月1日 Flue gas desulfurized gypsum mainly comes from thermal power plants, smelters, and largeenterprise boilers, and contains industrial byproducts produced through a wet desulfurization combustion process, where SO 2 gas and lime slurry react under strong oxidation conditions The main component of this gypsum is calcium sulfate dihydrate, which also Production and resource utilization of flue gas desulfurized
.jpg)
Advanced and Intensified Seawater Flue Gas
2020年11月13日 Seawater flue gas desulfurization (SWFGD) is considered to be a viable solution for coastal and naval applications; however, this process has several drawbacks, including its corrosive absorbent; low vapor loading Electrooxidation flue gas desulfurization is a gas–liquid reaction, but the solubility of SO 2 in aqueous solution is very low with the solubility of only 94 g/100 mL at 25 °C Thus it is necessary to strengthen the contact between SO 2 and ROSs to achieve successful flue gas desulfurization Namely, the mass transfer of flue gas in electrolyte should be strengthened [314,315]Flue Gas Desulfurisation an overview ScienceDirect Topics2024年8月13日 This blog post is the third in a threepart series that discusses flue gas desulfurization (FGD) The first post provides overviews of sulfur dioxide (SO 2) and emissions regulations, the FGD industry, and global FGD market trendsThe second post provides highlevel overviews of wet, semidry, and dry FGD technologies with respect to SO 2 capture Flue Gas Desulfurization: Detailed Process Overview2020年5月25日 industrialization level of lowconcentration flue gas desulfurization is relatively low The technologies that have been applied are mainly flue gas desulfurization equipment imported from abroad in the 1970s and simple dust removal and desulfurization equipment for small and medium boilersResearch on Petroleum Flue Gas Desulfurization System
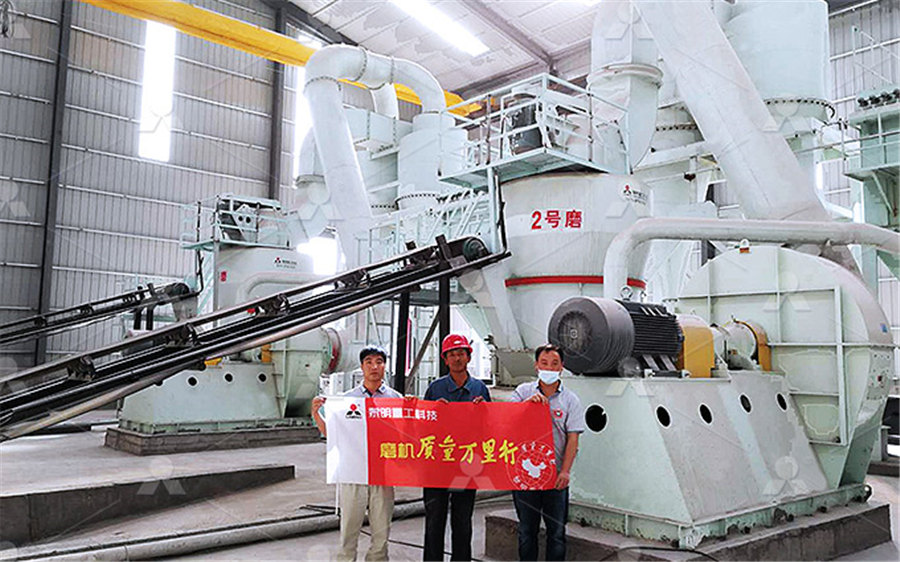
Progress of Desulfurization and Denitration Technology of Flue Gas
2019年3月30日 Gas–solid twophase flow and water vaporization processes tend to have a significant impact on the efficiency of flue gas desulfurization with a powderparticle spouted bed2000年7月31日 Dry Flue Gas Desulfurization Technology Dry FGD technology includes lime or limestone spray drying; dry sorbent injection, including furnace, economizer, duct, and hybrid methods; and circulating fluidizedbed scrubbers Table 63 shows the mercury forms in coalfired flue gas before and after the flue gas desulfurization equipment of five Dry Flue Gas Desulfurisation Technology ScienceDirect2023年2月11日 Calciumbased desulfurization ash (CDA) is mainly produced in dry and semidry flue gas desulfurization processes The property of CDA is extremely unstable because its main component, calcium sulfite, makes it difficult to be directly applied to the field of building materials The modification of desulfurization ash can be realized by hightemperature Resource utilization of flue gas calciumbased desulfurization 2018年10月15日 Research Cottrell has demonstrated the commercial availability of limestone flue gas desulfurization on a 115 MW installation Certain chemistry and process considerations were taken into account (PDF) Comparison of flue Gas Desulfurization Technologies
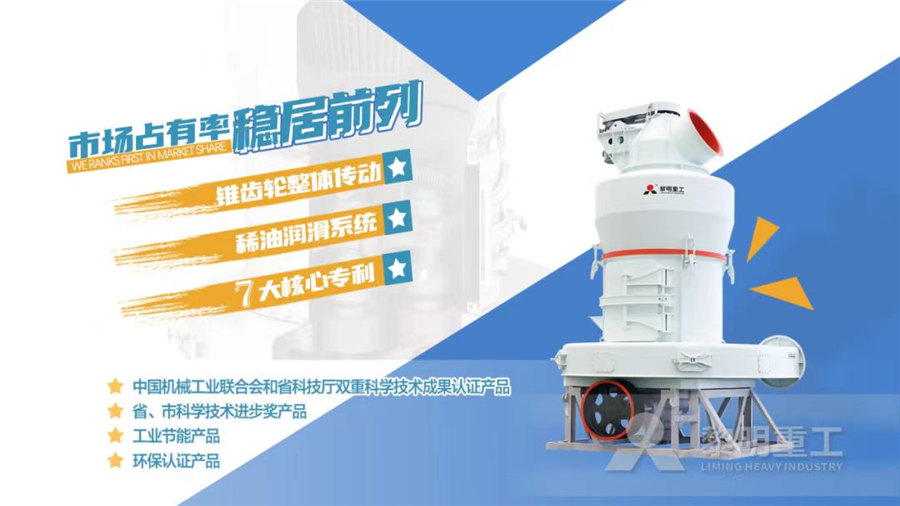
Corrosion evaluation of one wet desulfurization equipment – Flue gas
2018年12月1日 Flue gas desulfurization (FGD) technology is now basically compulsory in the fossil power industry under the pressing environmental challenges globally, and the wet type of it particularly prevails thanks to the higher desulfurization efficiency than the dry type However, the service conditions of wet FGD units are usually so harsh due to corrosivity and erosivity of the 2017年5月16日 Flue gas flow rate (max) 3310 m /hr Flue Gas Temperature 280 C Patricia Córdoba presented a general review of the Flue Gas Desulphurization (FGD) technologies used to abate sulphur emissions from coalfired power plants, and exposes the major physicchemical processes occurring during wet limestone FGD( Patricia Córdoba, 2014)Analytical Investigation and Design of Flue Gas FGD Systems: Transforming Flue Gas Desulfurization Enviropol's Flue Gas Desulfurization (FGD) systems significantly reduce sulfur emissions from industrial flue gasses These devices are intended to guarantee that stringent Flue Gas Desulfurization Equipment/System 2023年4月20日 emissions into the atmosphere, industrial flue gas desulfurization technology has been developed rapidly, and a large number of industrial flue gas desulfurization equipment has been constructed Industrial flue gas desulfurization equipment in China will reach 109,200 sets in 2025 [7, 8] The desulfurization methods include the calciumResource utilization of flue gas calciumbased
.jpg)
Flue Gas Desulfurization: Industry and Market Overview
2024年7月29日 This blog post is the first in a threepart series that discusses flue gas desulfurization (FGD) This post provides overviews of sulfur dioxide pollution (SO 2) and emissions regulations, the FGD industry, and global FGD market trendsThe second post provides highlevel overviews of wet, semidry, and dry FGD technologies with respect to SO 2 capture 2016年9月3日 At present, the main sintering flue gas desulfurization technologies used in European and North American are (1) spray dryer absorption (SDA) semidry desulfurization, as used in the Duisburg Iron and Steel plant sintering machine in Germany; (2) novel integrated desulfurization (NID) dry desulfurization, as used by Alstom in France; (3) MEROS Pollutants Emission and Control for Sintering Flue GasThe biggest market for Flue Gas Desulfurization equipment is coalfired power plants As of 2016, the International Energy Agency reports that there are approximately 62,000 thermal power plants in 115 countries, producing 80% of the global kilowatt capacityFlue Gas Desulfurization EKT Interactive2024年1月11日 semidry flue gas desulfurization technology, it is outcome of joint efforts made by the American JOY and Denmark NIRO [2],[5] Since the 1st industrial unit adopting such process was built in the Application and Development Trend of Flue Gas
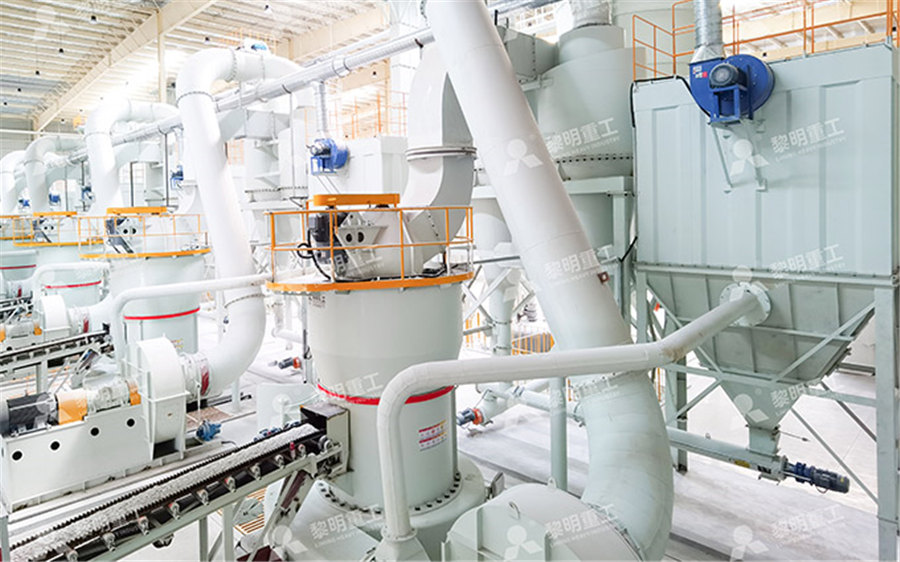
Resource utilization of semidry flue gas desulfurization ash
2024年4月1日 Semidry desulfurization technology has gained prominence in sintering flue gas desulfurization due to its notable advantages such as minimal equipment corrosion, dry waste products, low water consumption, straightforward processing, and low capital investment, which effectively integrates the drawbacks of wet and dry desulfurization methods2024年4月19日 Limestone gypsum wet flue gas desulfurization process 2 Magnesium oxide desulfurization process The basic principle of magnesium oxide desulfurization is similar to that of limestone (lime) method, that is, the SO2 in the flue gas is absorbed by magnesium oxide slurry, which mainly generates trihydrate and polyhydrate magnesium sulfite, and then generates 4 Flue Gas Desulfurization Process You Should Never Miss2024年9月25日 Enhancement of selenium removal in coalfired flue gas across wet flue gas desulfurization spray tower by internal componentspart 1: Demister and wall ring Author links open overlay panel Renjie Zou a, Zehua Li b, (WFGD) device is a key piece of equipment used to control selenium, but its removal efficiency is highly variable (13%–95% Enhancement of selenium removal in coalfired flue gas across wet flue Currently, desulfurization technologies can be categorized into three main types: wet flue gas desulfurization (FGD) [11], [12], [13], semidry desulfurization [14] and dry desulfurization [15]Wet flue gas desulfurization is widely employed in largescale desulfurization processes due to its high efficiency and low energy consumption [16]However, it poses a significant environmental Recent advances in process and materials for dry desulfurization
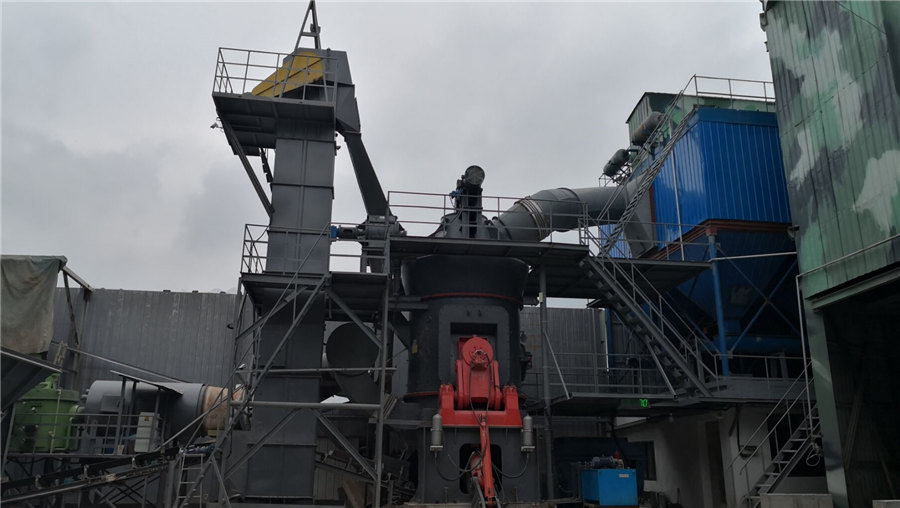
Experimental study on integrated desulfurization and
2024年2月12日 Experiment system As depicted in Fig 1, the simulated flue gas experimental system is primarily designed for catalyst screening under laboratory conditionsThis experimental setup comprises a 5 天之前 A flue gas desulfurization scrubber is a system designed to remove sulfur compounds from the airflow produced by industrial plants and power stations The method works through a chemical reaction between sulfur dioxide (SO₂) and an absorbent solution, usually lime or magnesiumbased, which results in the formation of neutral compounds such as Flue Gas Desulfurization (FGD) Scrubber Systems2020年2月7日 Wet flue gas desulfurization is widely used in power plants because of its high desulfurization efficiency The reason why it is difficult to predict sulfur dioxide removal efficiency in flue gas is that it is related to many factors In this paper, the SO2 was removed by absorbing with ammonia solution in a packed tower Experimental studies have shown that the operating Prediction of SO2 removal efficiency for ammoniabased wet flue gas 2002年1月1日 This paper presents a comprehensive review of the state of the art in flue gas desulfurization (FGD) technologies for coalfired boilers handling equipment, the concentrated waste is sent for (PDF) Flue Gas Desulfurization: The State of the Art [J]
.jpg)
Corrosion evaluation of one wet desulfurization equipment – Flue gas
2018年12月1日 The design parameters of this wet FGD unit are listed in Table 1, and the simplified process flow chart of its five systems is shown in Fig 1As for the detailed process flow chart of the unit, it can be referred to the literature [31]Field investigation was performed in the sequence from the limestone preparation system and the boiler air and gas system in the Your trusted partner in advanced Flue Gas Desulfurization (FGD) solutions At RIECO, we harness the power of innovation, engineering excellence, and rigorous research to deliver worldclass Flue Gas Desulfurization (FGD) systems With nearly half a century's experience in the air pollution control equipment and systems business, we have a Best Flue Gas de Sulphurization System Solution Enquire Control and Treatment of Air Emissions Shahryar Jafarinejad, in Petroleum Waste Treatment and Pollution Control, 2017 515 FlueGas Desulfurization Fluegas desulfurization (FGD) is a scrubbing technique that uses an alkaline reagent (typically a sodium or calciumbased alkaline regent) to remove SO 2 from flue gas (TriState Synfuels Company, 1982; Tilly, 1983; FlueGas Desulphurization an overview ScienceDirect Topics2022年1月15日 In the industrial production of China, the processing of phosphate rock, volcanic eruptions, kerosene combustion and aluminum smelting will lead to flue gas emissions containing a large amount of SO 2SO 2 is a highly irritating gas Because SO 2 is freely soluble in water and enters the respiratory tract, it can generate corrosive sulfurous acid, sulfuric acid, and sulfate Summary of research progress on industrial flue gas desulfurization

Production and resource utilization of flue gas desulfurized
2021年11月1日 Flue gas desulfurized gypsum mainly comes from thermal power plants, smelters, and largeenterprise boilers, and contains industrial byproducts produced through a wet desulfurization combustion process, where SO 2 gas and lime slurry react under strong oxidation conditions The main component of this gypsum is calcium sulfate dihydrate, which also