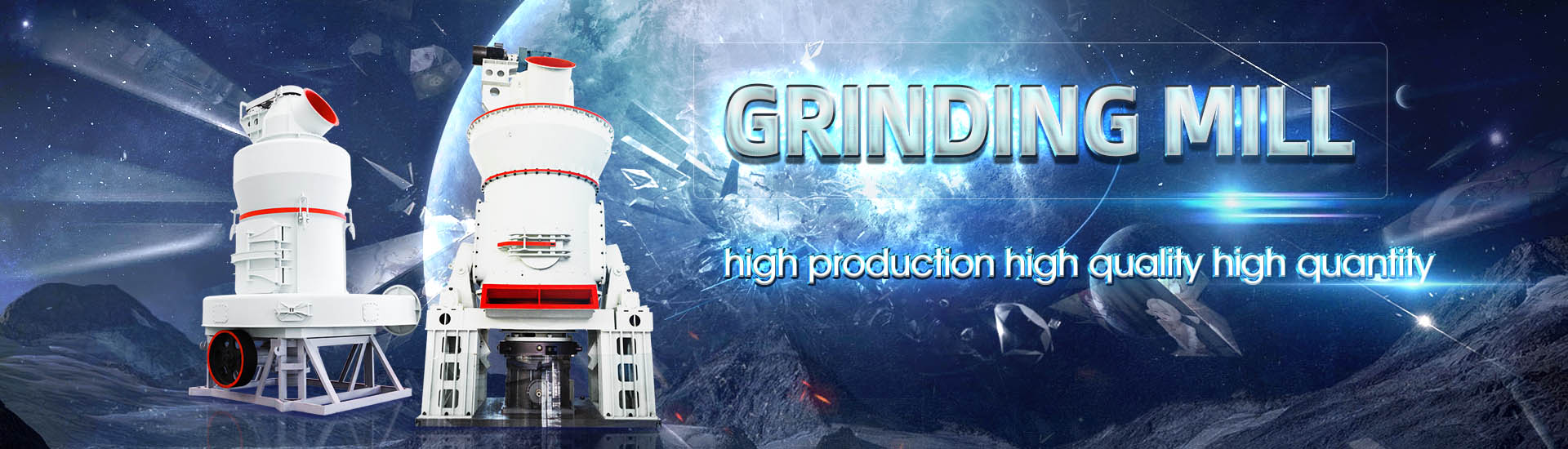
Some common processes in cement production
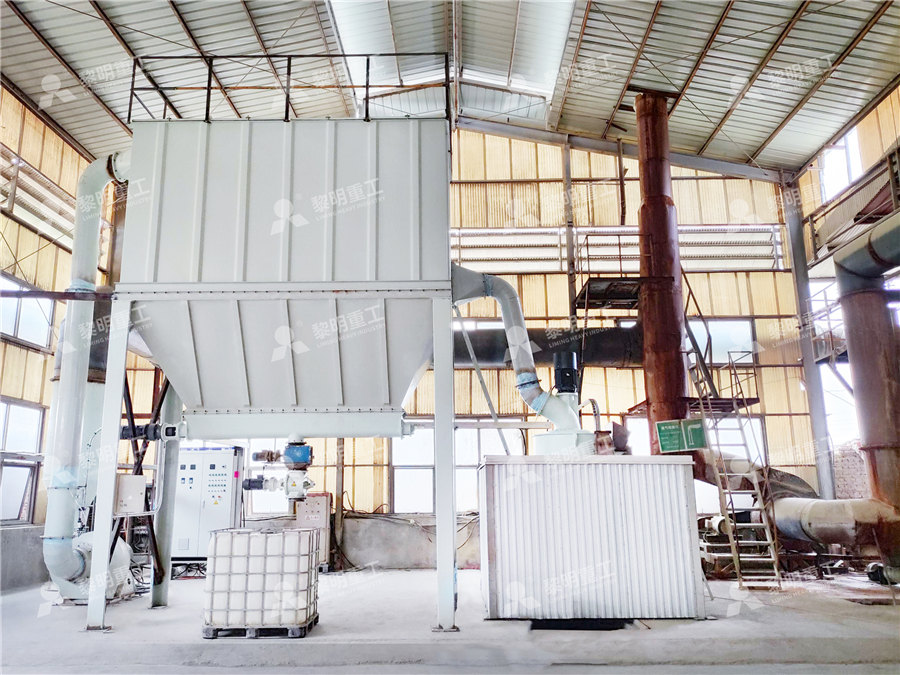
StepbyStep Guide to the Manufacturing of
This article will guide readers through each step in the manufacturing of cement, detailing critical processes such as blending, hydration, and the role of calcium carbonate, silica, alumina, and iron oxide in cement production2024年11月16日 There are six main stages of the cement manufacturing process The raw cement ingredients needed for cement production are limestone (calcium), sand and clay How Cement is Made Cement Manufacturing ProcessConcrete is formed when portland cement creates a paste with water that binds with sand and rock to harden Concrete is the most widely used resource in the world after water Cement is manufactured from materials heated together at How Cement is Made Portland Cement 2 天之前 The Cement Plant Operations Handbook is a concise, practical guide to cement manufacturing and is the standard reference used by plant operations personnel worldwide The Cement Plant Operations Handbook International
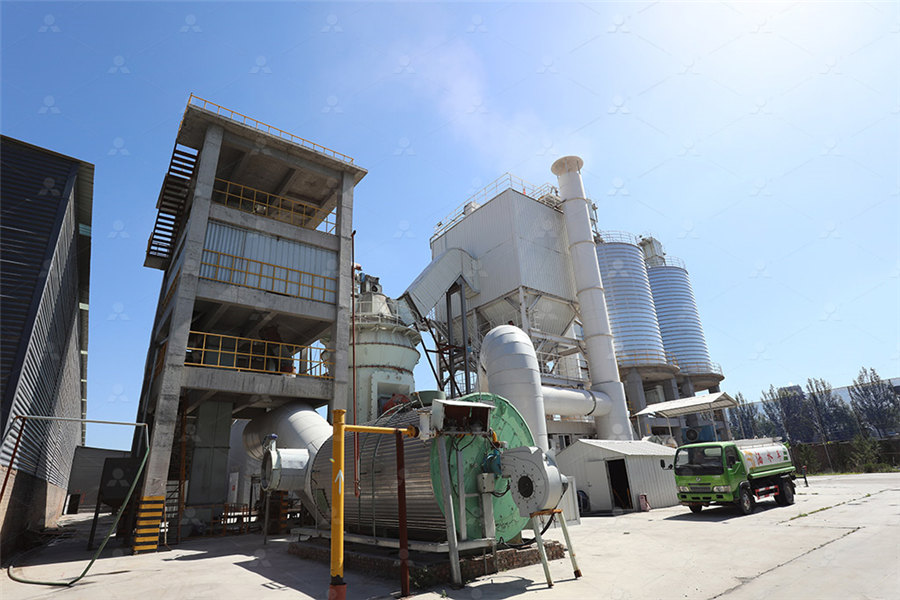
The Cement Production Process mcilvainecompany
2010年3月27日 The three broad processes of cement manufacturing are: Raw milling — the preparation of the kiln feed Calcining and burning or clinkering — the conversion process that 2024年5月22日 There are 4 stages of cement production that help maintain consistent raw material quality with minimal chemistry deviation, from quarry to silo to customer The Quarry: A practical guide to improving cement manufacturing 2024年1月18日 Innovative production processes: There are several innovative production processes that are being developed to make cement production more efficient and Cement Production Demystified: StepbyStep Process and 5 天之前 The manufacture of Portland cement is a complex process and done in the following steps: grinding the raw materials, mixing them in certain proportions depending upon their purity and composition, and burning them to sintering in Manufacturing of Portland Cement – Process

Cement manufacturing components of a
This page and the linked pages below summarize the cement manufacturing process from the perspective of the individual components of a cement plant the kiln, the cement mill etc For information on materials, including reactions in 2024年4月24日 weighting 50 kg each Most cement is used in concrete as an essential material in the construction industry [38, 40] There are two types of processes used in cement production: the dry process and the wet process [38] • Dry process: In this process, the raw materials are dried using different types of dryers or air separators,Impacts of Cement Production on the Environment with 2020年8月25日 A full cement production process includes the cement crushing process, raw mill process, clinker process, and cement grinding process, cement packing process, and related process the clinker, and some mixed Cement Production Process Cement 2021年3月3日 Cement is produced by a hightemperature (about 1500 °C) reaction in a rotary kiln of carefully proportioned and blended ratios of lime (CaO), silica (SiO 2), alumina (Al 2 O 3), and iron oxide (Fe 2 O 3)The production of cement is a chemical process requiring an accurate blend of the previously cited four key organic oxides and the limitation of several undesirable Cement SpringerLink
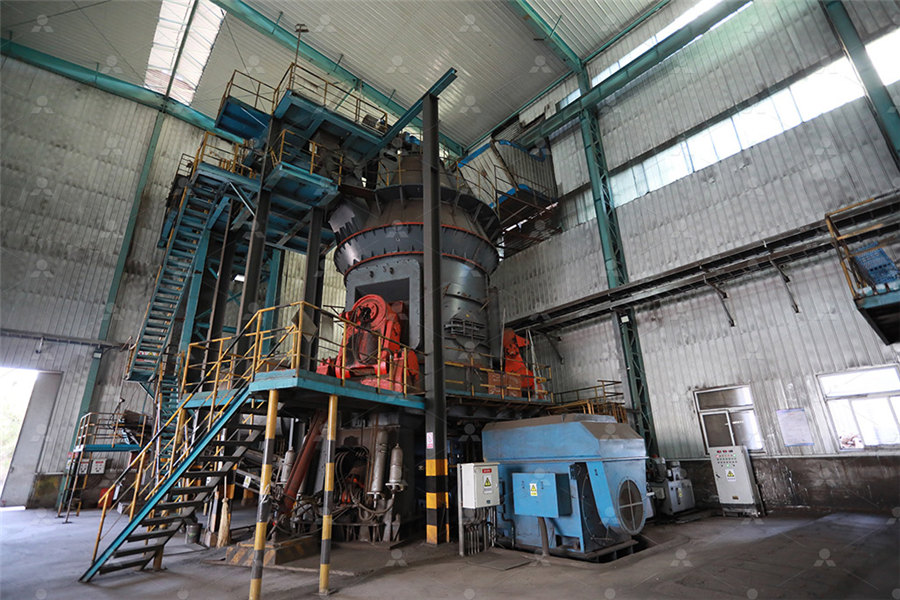
How Cement is Made Cement Manufacturing Process
2024年11月16日 Stage of Cement Manufacture There are six main stages of the cement manufacturing process Stage 1: Raw Material Extraction/Quarry The raw cement ingredients needed for cement production are limestone (calcium), sand and clay (silicon, aluminum, iron), shale, fly ash, mill scale, and bauxite The ore rocks are quarried and crushed into smaller In this process, the hydrated cement reacts with CO 2 in the air, slowly reversing some of the processes that took place in the kiln when the cement was made (this is the carbonation process; it also causes reinforcement corrosion, see Section 2532) It is estimated that this may reduce the carbon footprint of the cement industry by 3–5%Cement Production an overview ScienceDirect TopicsSome manufacturers grind the raw materials dry, while others use a wetgrinding process involving water Quarrying Cement manufacturers quarry raw materials including limestone, clay, and sand They use fewer resources and contribute to a circular economy by adding raw substances called alternative raw materials, including fly ash, blast How Cement is Made Portland Cement Association2012年8月4日 required for the production of cement from aro und 5 700kJ/kg in the old wet processes to 3 100 kJ/kg3 600 kJ/kg in modern plants [Zur Strassen, 1957; Johansen Kouznetsova, 1992; Popescu et al (PDF) An Overview of Cement production: How “green
.jpg)
Energy and Economic Comparison of Different Fuels in
2021年5月26日 production cost in Nigeria depending on the production process and type of cement environmental pollution, storage, and cost are some of the factors that determine the selection of fuel [5] In cement production, the energy use is distributed as 927% for pyroprocessing, The calorific value of common fuels used in cement production is Comprehensive Guide to Cement Kilns: Processes, Types, Efficiency, and Innovations The dry process kiln is the most common type used in modern cement production It is more energyefficient and environmentally friendly than the wet process kiln A precalciner is an additional combustion chamber used in some cement kilns to further Comprehensive Guide to Cement Kilns: Processes, Types, 2021年11月1日 The benefits of using blast furnace slag are that it can improve the workability of concrete, obtain higher longterm compressive and flexural strengths, reduce permeability, and improve An Overview of EcoFriendly Alternatives as the Replacement of Cement 2021年8月30日 The cement manufacturing industry has played a fundamental role in global economic development, but its production is a major facilitator to anthropogenic CO2 release and solid waste generationHealth Risk and Environmental Assessment of
.jpg)
Projecting future carbon emissions from cement production
2023年12月11日 CO 2 emissions in the cement industry occur primarily in the production process of clinker – an intermediate product for cement 5,6 – where CO 2 is released through both the combustion of 2024年10月3日 Types of Cement Manufacturing Processes Cement manufacturing involves various processes tailored to different cement types Manufacturers primarily categorize the methods as follows: 1 Dry Process The dry process currently stands as the most prevalent method in cement production due to its efficiency and environmental benefitsManufacturing of Cement Key Steps and Processes2 天之前 Providing a comprehensive guide to the entire cement production process from raw material extraction to the finished product, the industry’s favourite technical reference book is now fully Finish milling is the grinding together of clinker with some 35 per cent gypsum, natural or synthetic, for set control, and quite often other components:The Cement Plant Operations Handbook International 2021年8月30日 The cement manufacturing industry has played a fundamental role in global economic development, but its production is a major facilitator to anthropogenic CO2 release and solid waste generation Nigeria has the largest cement industry in West Africa, with an aggregate capacity of 589 million metric tonnes (MMT) per year The Ministry for Mines and Steel Health Risk and Environmental Assessment of Cement Production
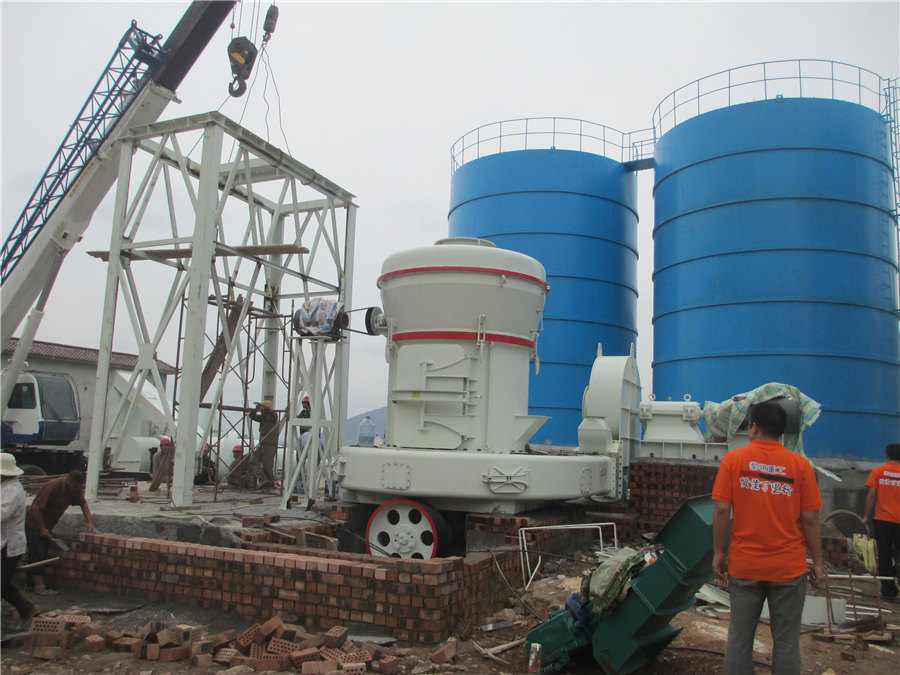
Manufacturing of Portland Cement – Process and Materials
5 天之前 The Fig1 show the flow diagram of the dry process of the manufacture of cement 1 Dry Process In the dry and semidry process the raw materials are crushed in a dry state Then, they are processed in grinding mill, dried and reduced to very fine powderlike That dry power is further blended, corrected for the right composition and mixed 2024年3月1日 The concrete is the final product used in buildings, roads, infrastructure, etc You can think of cement as the “glue” that holds the sand and gravel and rebar (reinforcement bar) together to make concrete PGNAA Improves Process and Quality Control in Cement Production Traditional cement plants conduct material analysis by taking samples Everything about Cement Production Thermo Fisher Scientific2011年8月9日 Cement production is an energyintensive process consuming thermal energy of the order of 33 GJ/tonne of clinker produced, which accounts for 30 – 40 percent of production costs (Giddings et al, 2000; EC, 2001) Worldwide, coal is Alternative Fuels in Cement Manufacturing IntechOpen2020年2月15日 Cement production processes involve complex chemical and physical reactions during the conversion of raw materials to the final product Moreover, the clinker burning process, which has a decisive (PDF) Parametric Studies of Cement Production Processes
.jpg)
The LCA of portland cement production in China
2014年9月23日 In 2008, the global cement production stood at 28 billion tons, up to 34 % from the previous year according to World Bank After 4 years, China witnessed its cement production up to 218 billion tons accounting for more than 60 % of global production according to China Cement Association (CCA 2013)The Chinese cement demand is anticipated to double at least 2023年10月13日 The production process of cement releases large amounts of CO2, mainly due to the hightemperature firing of raw materials, such as limestone and clay, but also due to energy and resource Global database of cement production assets and upstream 2015年4月14日 The diagrams illustrate the phases and apparatus to make cement and how cement is utilised in the production of concrete for construction The production of cement involves a 5 stage, linear process that begins with IELTS Task 1 Process Cement and Concrete 2021年10月22日 While critical to many aspects of the built environment, the high levels of demand for cement currently results in more than 7% of anthropogenic greenhouse gas (GHG) emissions 8 The majority of the CO 2 emissions from cement production are from fossil resources (ie, mineral or energy resources that are not renewable on a short time horizon), Achieving net zero greenhouse gas emissions in the cement
.jpg)
(PDF) Environmental Pollution by Cement Industry
2019年7月31日 In cement production, the rotary cement kiln is one of the main components that play a significant role in producing environmental pollutants such as NOX, VOC, CO, and CO22024年10月1日 The demand for cement has significantly increased, growing by 8% in the year 2022 and by a further 12% in 2023 It is highly anticipated that this trend will continue, and it will result in significant growth by 2030 However, cement production is highly energyintensive, with 70 to 80% of the total energy consumed during the clinker formation, which is the main cement Integrating Process ReEngineering Models in Cement Production 2021年5月3日 In the paper, the energy potential of different fossil fuels is analyzed and the environmental aspect from pairing fossil fuels with refusederived fuel (RDF) in the cement production processEnergy and Economic Comparison of Different Fuels in Cement Production2021年10月14日 Some SCMs such as fly ash and slag are byproducts of other industrial processes, meaning that their use in cement production reduces waste and enhances resource efficiency Moreover, the use of SCMs can enhance the properties of concrete, thereby increasing its durability and service life which helps to further reduce the overall embodied The prospects and challenges of the Indian cement industry
.jpg)
Energy and Economic Comparison of Different Fuels in Cement Production
2020年11月6日 Cement clinkerisation is the major energyconsuming process in cement manufacturing due to the hightemperature requirement In this paper, energy data including specific energy consumption, forms, and types of energy used at different units of cement manufacturing processes were analyzed and compared for effectiveness, availability, cost, Growing awareness of the importance of mitigating climate change is driving research efforts toward developing economically viable technologies for reducing greenhouse gas emissions The high energy consumption and carbonintensive nature of cement manufacturing make it worthwhile to examine the environmental and economic characteristics of process Continuous Assessment of the Environmental Impact and 2024年1月3日 This is a common problem across heavy industry: fossil fuels have become ingrained in production processes because of their low cost, says Rebecca Dell, head of the industry group at the nonprofit Cracking the problem of cement, one of climate’s hardest 2024年4月24日 weighting 50 kg each Most cement is used in concrete as an essential material in the construction industry [38, 40] There are two types of processes used in cement production: the dry process and the wet process [38] • Dry process: In this process, the raw materials are dried using different types of dryers or air separators,Impacts of Cement Production on the Environment with
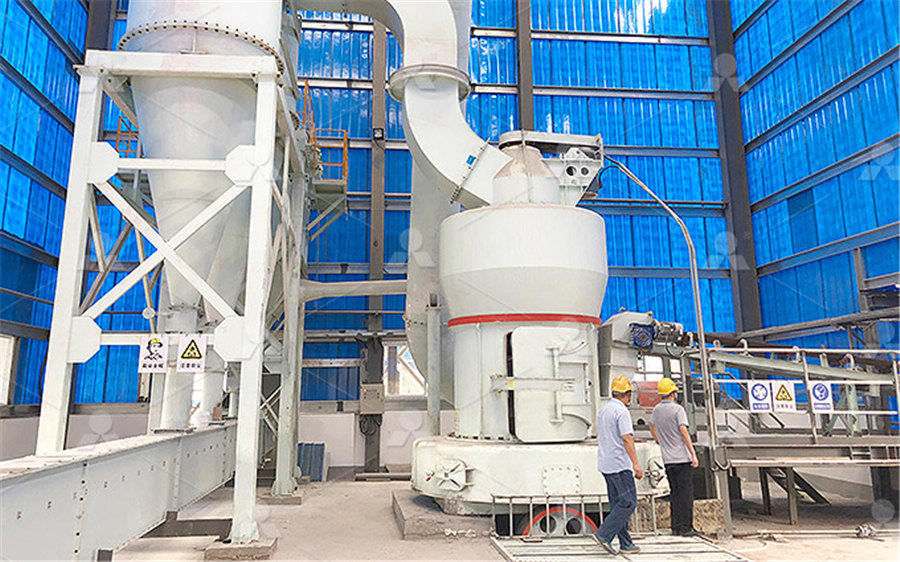
Cement Production Process Cement
2020年8月25日 A full cement production process includes the cement crushing process, raw mill process, clinker process, and cement grinding process, cement packing process, and related process the clinker, and some mixed 2021年3月3日 Cement is produced by a hightemperature (about 1500 °C) reaction in a rotary kiln of carefully proportioned and blended ratios of lime (CaO), silica (SiO 2), alumina (Al 2 O 3), and iron oxide (Fe 2 O 3)The production of cement is a chemical process requiring an accurate blend of the previously cited four key organic oxides and the limitation of several undesirable Cement SpringerLink2024年11月16日 Stage of Cement Manufacture There are six main stages of the cement manufacturing process Stage 1: Raw Material Extraction/Quarry The raw cement ingredients needed for cement production are limestone (calcium), sand and clay (silicon, aluminum, iron), shale, fly ash, mill scale, and bauxite The ore rocks are quarried and crushed into smaller How Cement is Made Cement Manufacturing ProcessIn this process, the hydrated cement reacts with CO 2 in the air, slowly reversing some of the processes that took place in the kiln when the cement was made (this is the carbonation process; it also causes reinforcement corrosion, see Section 2532) It is estimated that this may reduce the carbon footprint of the cement industry by 3–5%Cement Production an overview ScienceDirect Topics
.jpg)
How Cement is Made Portland Cement Association
Some manufacturers grind the raw materials dry, while others use a wetgrinding process involving water Quarrying Cement manufacturers quarry raw materials including limestone, clay, and sand They use fewer resources and contribute to a circular economy by adding raw substances called alternative raw materials, including fly ash, blast 2012年8月4日 required for the production of cement from aro und 5 700kJ/kg in the old wet processes to 3 100 kJ/kg3 600 kJ/kg in modern plants [Zur Strassen, 1957; Johansen Kouznetsova, 1992; Popescu et al (PDF) An Overview of Cement production: How “green2021年5月26日 production cost in Nigeria depending on the production process and type of cement environmental pollution, storage, and cost are some of the factors that determine the selection of fuel [5] In cement production, the energy use is distributed as 927% for pyroprocessing, The calorific value of common fuels used in cement production is Energy and Economic Comparison of Different Fuels in Comprehensive Guide to Cement Kilns: Processes, Types, Efficiency, and Innovations The dry process kiln is the most common type used in modern cement production It is more energyefficient and environmentally friendly than the wet process kiln A precalciner is an additional combustion chamber used in some cement kilns to further Comprehensive Guide to Cement Kilns: Processes, Types,
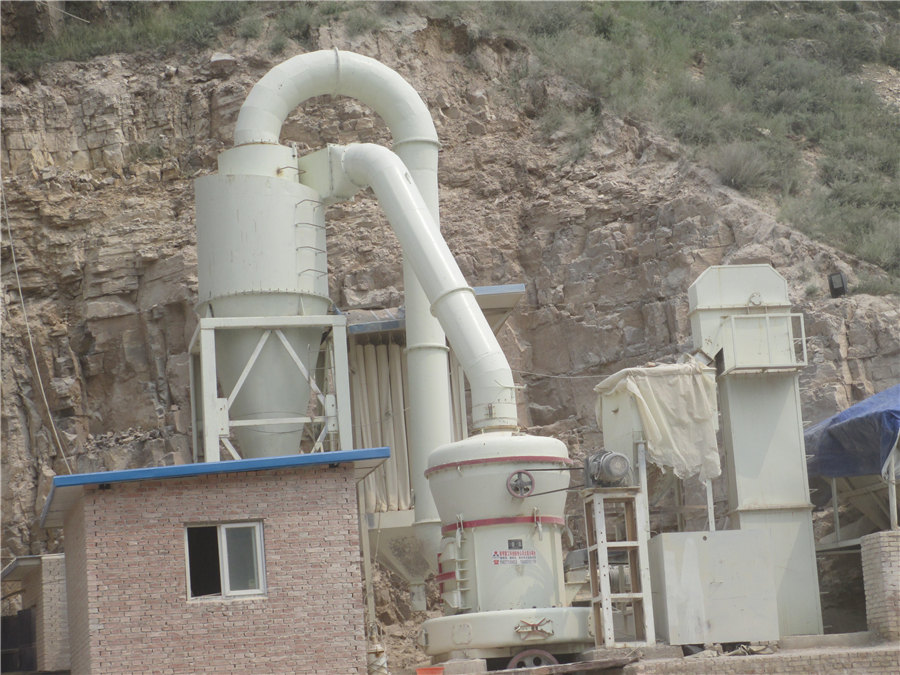
An Overview of EcoFriendly Alternatives as the Replacement of Cement
2021年11月1日 The benefits of using blast furnace slag are that it can improve the workability of concrete, obtain higher longterm compressive and flexural strengths, reduce permeability, and improve