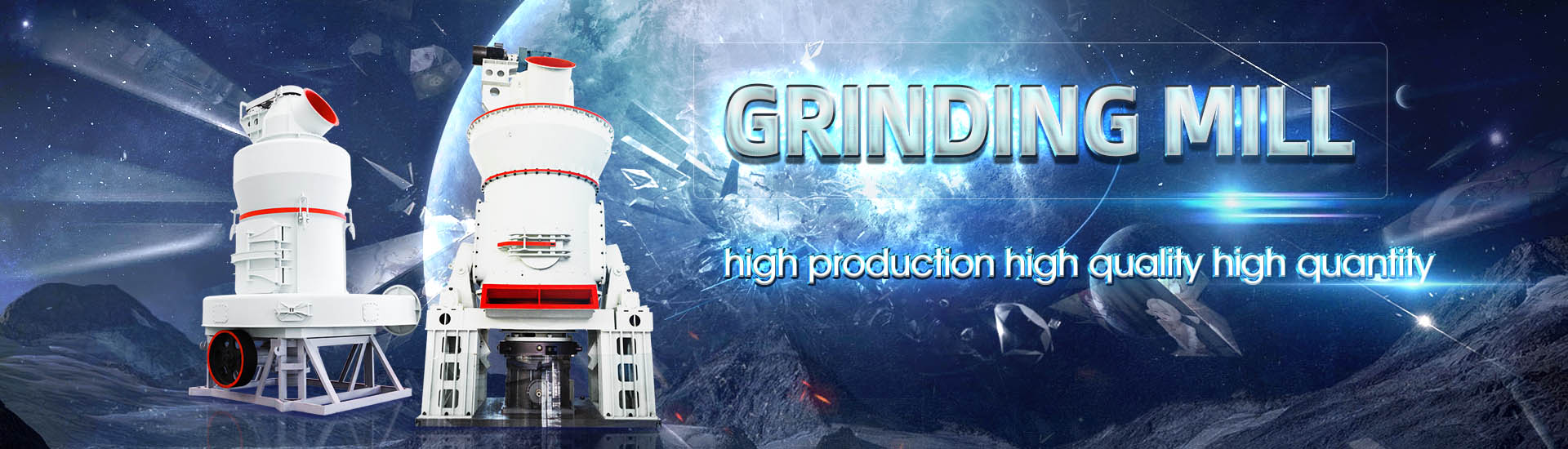
Nickel iron rotary kiln
.jpg)
What Is Rotary KilnElectric Furnace Process?
What Is Rotary KilnElectric Furnace Process? The production of ferronickel by the rotary kilnelectric furnace (RKEF) process is a rapidly developing nickel laterite ore treatment process2016年10月25日 Among these methods, the rotary kilnelectric furnace (RKEF) process has the advantages of yielding high nickel/iron grade from crude ferronickel products, less harmful Material and energy flows in rotary kilnelectric furnace smelting 2021年9月16日 The primary pyrometallurgical route to produce ferronickel from laterite nickel ores is the Rotary KilnElectric Furnace (RKEF) process In the RKEF process, minerals undergo calcination and(PDF) Improving the rotary kilnelectric furnace Rotary kilnelectric furnace (RKEF) smelting is currently the worldwide mainstreaming process for ferronickel production from nickeliferous laterite ore, in spite of the high power consumptionFerronickel Preparation from Nickeliferous Laterite by Rotary Kiln
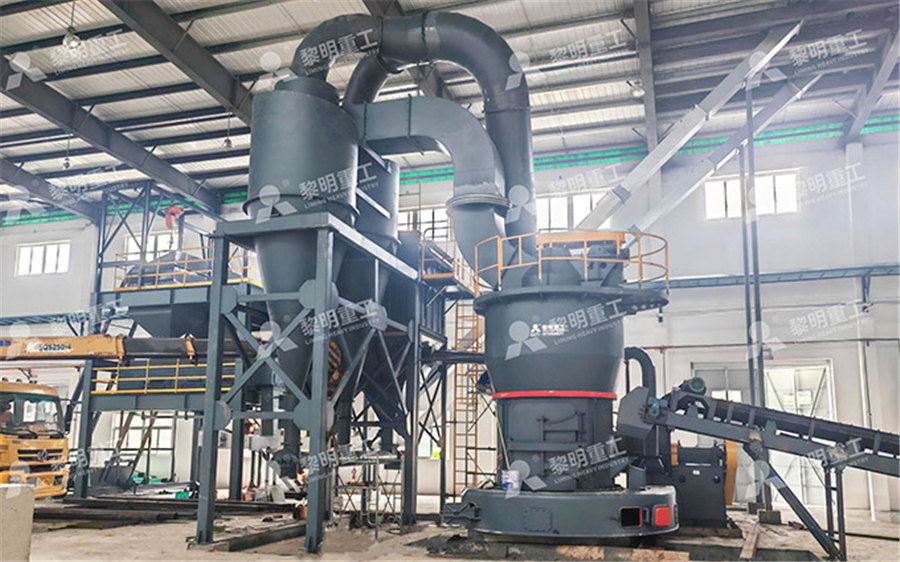
Design of process control system of rotary klin process for nickel iron
Due to the large delay, strong nonlinearity and coupling among variables of the rotary kiln production process, we select the roasting material temperature, oxygen content and kiln tail In order to overcome the control difficulties of Nickeliron rotary kiln, such as nonlinear, timevarying, strong coupling and large time delay, we design an intelligent control system, which Research on the intelligent control system of Nickeliron rotary kiln 2018年10月1日 In this paper, by collaborating with an enterprise, its aim is to validate and promote a practical and efficient pretreatment technology to upgrading of lowgrade nickel Separation and Recovery of Iron and Nickel from LowGrade 2018年8月19日 Therefore, a novel process is proposed to directly produce ferronickel from nickel laterite ore by semimolten reduction , which is expected to be realized in a rotary hearth Preparation of Ferronickel from Nickel Laterite Ore via Semi
.jpg)
(PDF) Nickel Laterite Smelting Processes and Some
2019年9月3日 Industrially, the pyrometallurgical treatment of laterites is mostly accomplished with a wellestablished method, namely, the rotary kiln–electric arc furnace (RKEF) process, Primary world nickel production in 2020 was 24307 kt Ni; 69% (16777 kt) of them came from oxidized nickel ores (laterites) and 31% from sulfides Productionwise, 877% of the 16777 kt came from pyrometallurgical and The Nickel Production Methods from Laterites Due to the large delay, strong nonlinearity and coupling among variables of the rotary kiln production process, we select the roasting material temperature, oxygen content and kiln tail temperature as control objectives of a nickeliron rotary kiln, then the intelligent sampling and PID control system based on operating conditions identification is designed At the same time, a Design of process control system of rotary klin process for nickel iron 2016年10月25日 Meanwhile, quicklime can permute the nickel/iron oxide from mineral which enhances the activity of metallic oxide [18], For improving the resource utilization, the slag is reutilized as construction material and the nickel is recycled from dust into rotary kiln Moreover, the flue gas and furnace gas are recycled as energy supply to Material and energy flows in rotary kilnelectric furnace smelting
.jpg)
Nickel industry Part 2 Processing nickel laterites and
2024年8月7日 Smelting is used primarily on saprolite ores to obtain an ironnickel alloy (ferronickel – FeNi, Nickel Pig Iron – NPI) while HPAL is used primarily to process limonite or for higherpurity end products In the rotary kiln, more heat is added through combustion of fossil fuels to raise the temperature to around 900 °C A highcarbon 2015年7月3日 of iron ore reduction in a generic rotary kiln Rotary kiln model Kiln modelling consists of two steps Firstly, an Excel®based calculation is used to determine the kiln bed profile and residence time based on specific operating conditions and the kiln configuration This is followed by a calculation of the kiln operating characterModelling and optimization of a rotary kiln direct 3 High production quality: nickel iron produced by laterite nickel ore Rotary kiln is of high quality, containing about 20% Ni, and can be directly used as raw material for stainless steel production 4 Diversified uses: The nickel products produced have a wider range of uses and can also be used as a coolant for molten steel meltingLaterite Nickel Ore Rotary KilnAGICO CEMENT is devoted to being the No1 rotary kiln manufacturer and professional enterprise of import and export trade Our main business is rotary kiln equipment such as cement kiln, lime rotary kiln, and shaft kiln Direct Line: +86 : info@rotarykilnfactoryRotary Kiln for Liion Battery Material Preparation
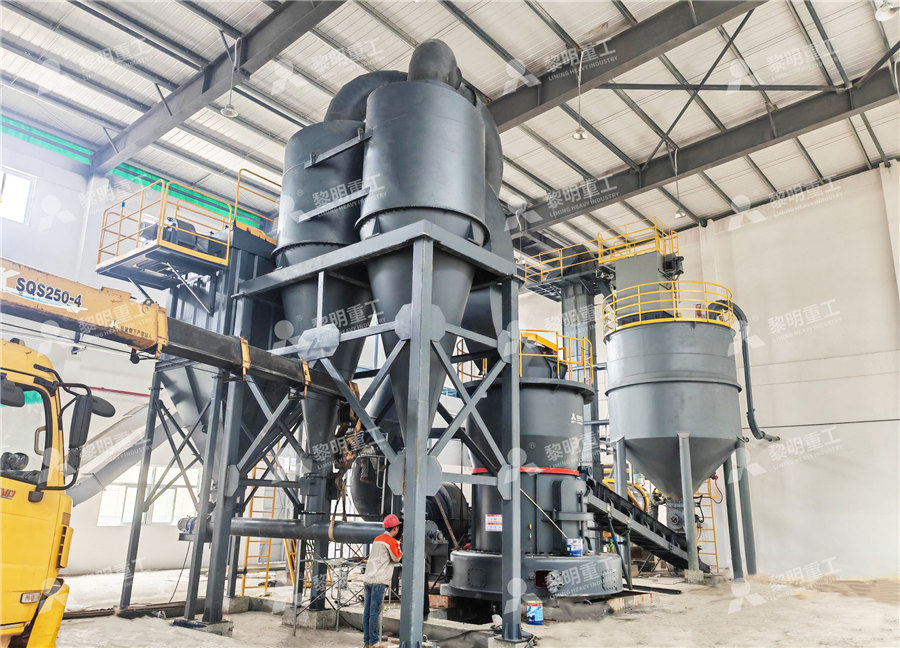
The effect of sulfur in rotary kiln fuels on nickel laterite
2020年10月1日 The rotary kilnelectric furnace (RKEF) process is the primary method for extracting nickel from saprolite ores In this technique, the ore is first calcined and prereduced at 850–1000 °C in a rotary kiln followed by smelting in an electric furnace at 1500–1600 °C (Eliott, 2015, Warner et al, 2006)2020年11月1日 In addition, the effect of the magnetic intensity on the separation indexes of nickel and iron were investigated, as shown in Fig 4 (e) and (f) The recovery ratios of nickel and iron continuously increased from 8253% to 9244% and from 8583% to 9117%, respectively, as the magnetic intensity increased from 50 to 100 mT As the magnetic Separation and recovery of iron and nickel from lowgrade 2021年9月16日 The primary pyrometallurgical route to produce ferronickel from laterite nickel ores is the Rotary KilnElectric Furnace (RKEF) process In the RKEF process, minerals undergo calcination and (PDF) Improving the rotary kilnelectric furnace process for China is smelt to produce ferronickel (comprising nickelcontained pig iron) the first big country with lateritetype nickel ore in the world, and big or small hundreds of smeltery is arrangedWherein, smelting process used has respectively blast furnace process, local method sinteringelectric furnace reduction smelting, sintering machine sinteringelectric furnace Rotary kiln for producing ferronickel from Indonesia Sulawesi nickel
.jpg)
Rotary Kiln Tanabe Co, Ltd 株式会社タナベ
A rotary kiln is a heating furnace that rotates a cylinder (retort), supplies raw materials into the furnace (inside the retort) using a feeding device (screw feeder, etc), and uniformly heattreats the raw materials while stirring it is possible to customize the processing object contact part with a special alloy such as nickel It is a The invention relates to a method for preparing nickel iron by using a rotary kiln for directly reducing nickel silicate ores The method comprises the steps of breaking the raw ores, placing in a drying kiln for drying, grinding into powder, adding 15% of fluoride, 520% of calcium oxide or 1030% of limestone, 01%05% of copper chloride, 1025% of iron oxide and 520% of coke Method for preparing nickel iron by using rotary kiln for In order to overcome the control difficulties of Nickeliron rotary kiln, such as nonlinear, timevarying, strong coupling and large time delay, we design an intelligent control system, which includes rotary kiln conditions recognition module, composite controllers, ratio module and operating conditions compensation module The mathematical model of kiln tail temperature, Research on the intelligent control system of Nickeliron rotary kiln 2016年10月25日 Among these methods, the rotary kilnelectric furnace (RKEF) process has the advantages of yielding high nickel/iron grade from crude ferronickel products, less harmful elements, raw materials with strong adaptability, high production efficiency and mature processMaterial and energy flows in rotary kilnelectric furnace smelting
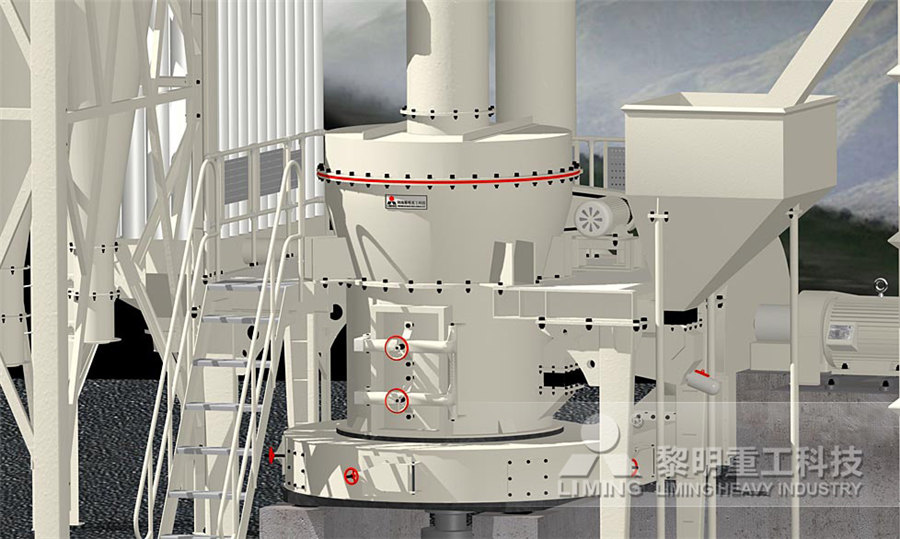
Enhancing Rotary KilnElectric Furnace Process of Saprolitic
2023年11月27日 How to reduce the energy consumption of the rotary kilnelectric furnace (RKEF) process has become an important issue for the stainless steel industry The aim of this study is to reduce the energy consumption of ferronickel production from saprolite nickel laterite in the RKEF process The effects of the slag binary basicity, FeO content, and Cr2O3 content on Electromagnetic heated rotary kiln for sale Compared to traditional rotary kilns, it has higher thermal efficiency, more uniform heat distribution, and longer service life Ore, slag, coal, lowgrade iron ore, roasted iron ore, nickeliron ore, highalumina bauxite, magnesite, nickel ore, chrome ore, etc Metallurgical IndustryElectromagnetic Heated Rotary Kiln2021年8月23日 At present, rotary kilnelectric furnace (RKEF) The lownickel ironbased alloy concentrates contain metals content of 7243 wt% with Ni grade of 465% and Fe/Ni of 1458 Furthermore, the harmful elements involving S and P are very low Hence, the used lownickel concentrates can meet the requirement of nucleating agent Upgrade of nickel and iron from lowgrade nickel laterite by 2024年1月1日 Nickel oxide ore gets its name for it is a kind of laterite ore with high iron content Nickel laterite, as the main landbased nickel resource, has total resource of 126 billion tons with an average nickel content of 128%, accounting for 72% of the total nickel resources The factory has five rotary kiln production lines with an annual Nickel Laterite Metallurgy SpringerLink
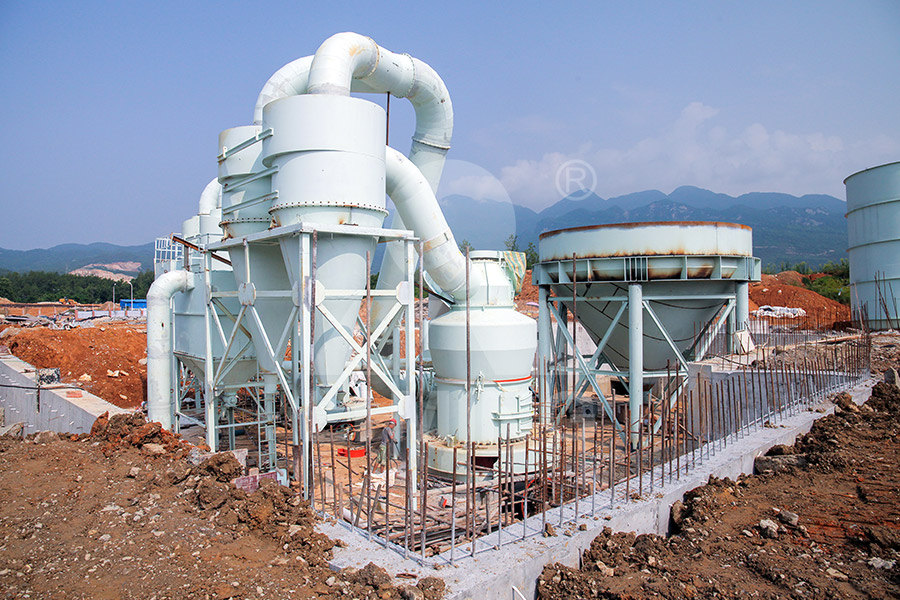
Improving the rotary kilnelectric furnace process for
2023年10月8日 ronickel from laterite nickel ores is the Rotary KilnElectric Furnace (RKEF) process In the oxygen is (partially) removed from nickel and iron oxides by CO from coal gasification [1,4] The 2022年5月5日 This paper summarizes more than a decade of systematic studies of the flow field in an iron ore pelletizing rotary kiln using computational fluid dynamics (CFD) on simplified models of a real kiln Physical, laserbased The Aerodynamics of an Iron Ore Pelletizing 2013年9月26日 Both the consumption and production of crude stainless steel in China rank first in the world In 2011, the nickel production in China amounted to 446 kilotons, with the proportion of electrolytic nickel and nickel pig iron (NPI) registering 415% and 565%, respectively NPI is a lowcost feedstock for stainless steel production when used as a substitute for electrolytic Carbothermic Reduction of Nickeliferous Laterite Ores for Nickel 2020年1月14日 The Effect of Sulfur in Rotary Kiln Fuels on Nickel Laterite Calcination by Muhammad Haziq Uddin BASc, The University of British Columbia, 2017 Lastly, the sum of the metallized and sulfurized iron/nickel was found to increase with an increase in P SO2 iv Lay Summary Rotary Kiln Electric Furnace (RKEF) process is a pyrometallurgical The Effect of Sulfur in Rotary Kiln Fuels on Nickel Laterite
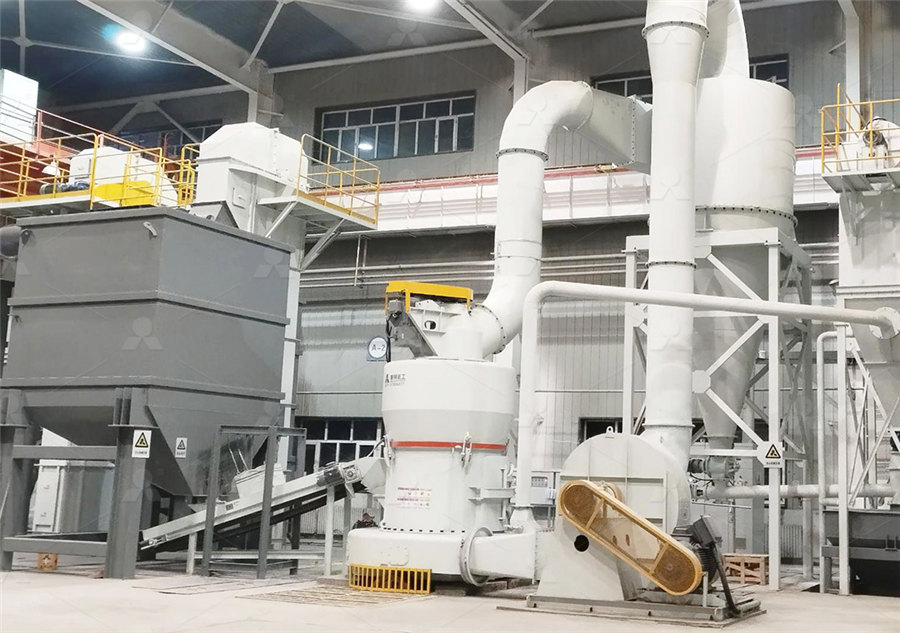
Temperature curve and reduction situation inside the rotary kiln
In 2011, the nickel production in China amounted to 446 kilotons, with the proportion of electrolytic nickel and nickel pig iron (NPI) registering 415% and 565%, respectively2020年10月1日 The rotary kilnelectric furnace (RKEF) process is the primary method for extracting nickel from saprolite ores In this technique, the ore is first calcined and prereduced at 850–1000 °C in a rotary kiln followed by smelting in an electric furnace at 1500–1600 °C (Eliott, 2015, Warner et al, 2006)The effect of sulfur in rotary kiln fuels on nickel laterite The invention provides a method for producing ferronickel by adopting a rotary kiln direct reductionRKEF (Rotary KilnElectric Furnace) combination method The method comprises the following steps: drying a laterite nickel ore for later use; crushing and screening an appropriate amount of the dried laterite nickel ore, and then mixing the screened laterite nickel ore with a Method for producing ferronickel by adopting rotary kiln 2024年9月13日 The global smelting business of nickel using rotary kilns and electric furnaces is expanding due to the growth of the secondary battery market Efficient operation of electric furnaces requires consistent calcine temperature in rotary kilns Direct measurement of calcine temperature in rotary kilns presents challenges due to inaccuracies and operational limitations, Operating Key Factor Analysis of a Rotary Kiln Using a
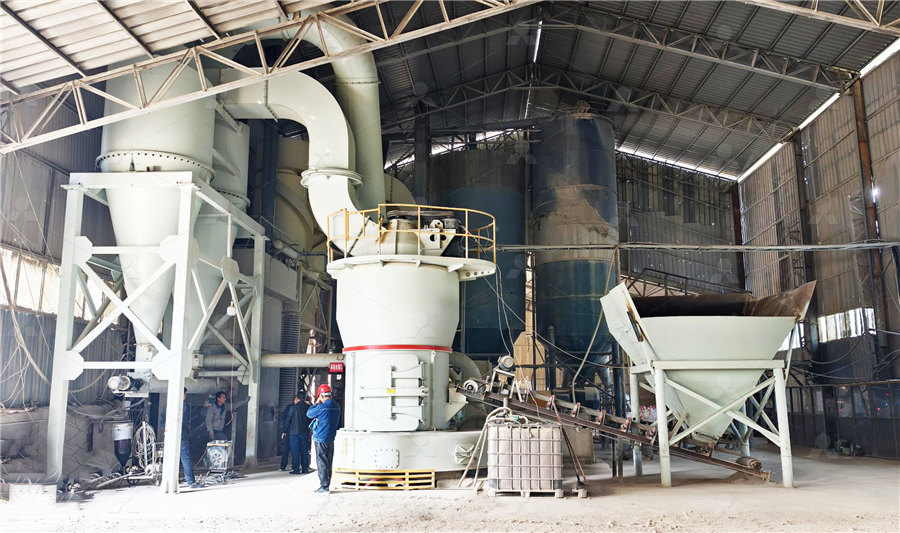
Nickel Mines increases interest in nickel pig iron Rotary Kiln
2020年5月17日 An Australian nickel producer has increased its stake in an Indonesian nickel iron plant Nickel Mines announced in a statement this week that it has increased its interest in the underconstruction Rotary Kiln Electric Furnace (RKEF) plant by 35% in a deal worth $70 million The company’s interest in the project now stands at 60%2018年8月19日 The rotary kilnelectric furnaceElectric furnace (RKEF) process is the main method for producing ferronickelFerronickel from nickel lateriteNickel laterite oreOre It is seen that the grade of the nickel and iron growing obviously with the increase of basicity When the basicity was 060, the nickel grade reached 1263% and the recovery Preparation of Ferronickel from Nickel Laterite Ore via Semi 1 Sponge iron rotary kiln 2 Central burner system 3 Cooling rotary kiln 4 Crushing magnetic separation system 5 Warehouse 6 Metering pneumatic conveying device 7 Mingled storehouse 8 Air supply equipment 9 Air nozzle 10 Coarse coal pipe 11 Fine coal pipe 12 Dust settling chamber 13 Scraper machine 14 Waste heat boiler 15 Turbine New Sponge Iron Rotary Kiln Design In Sponge Iron Primary world nickel production in 2020 was 24307 kt Ni; 69% (16777 kt) of them came from oxidized nickel ores (laterites) and 31% from sulfides Productionwise, 877% of the 16777 kt came from pyrometallurgical and The Nickel Production Methods from Laterites
.jpg)
Design of process control system of rotary klin process for nickel iron
Due to the large delay, strong nonlinearity and coupling among variables of the rotary kiln production process, we select the roasting material temperature, oxygen content and kiln tail temperature as control objectives of a nickeliron rotary kiln, then the intelligent sampling and PID control system based on operating conditions identification is designed At the same time, a 2016年10月25日 Meanwhile, quicklime can permute the nickel/iron oxide from mineral which enhances the activity of metallic oxide [18], For improving the resource utilization, the slag is reutilized as construction material and the nickel is recycled from dust into rotary kiln Moreover, the flue gas and furnace gas are recycled as energy supply to Material and energy flows in rotary kilnelectric furnace smelting 2024年8月7日 Smelting is used primarily on saprolite ores to obtain an ironnickel alloy (ferronickel – FeNi, Nickel Pig Iron – NPI) while HPAL is used primarily to process limonite or for higherpurity end products In the rotary kiln, more heat is added through combustion of fossil fuels to raise the temperature to around 900 °C A highcarbon Nickel industry Part 2 Processing nickel laterites and 2015年7月3日 of iron ore reduction in a generic rotary kiln Rotary kiln model Kiln modelling consists of two steps Firstly, an Excel®based calculation is used to determine the kiln bed profile and residence time based on specific operating conditions and the kiln configuration This is followed by a calculation of the kiln operating characterModelling and optimization of a rotary kiln direct
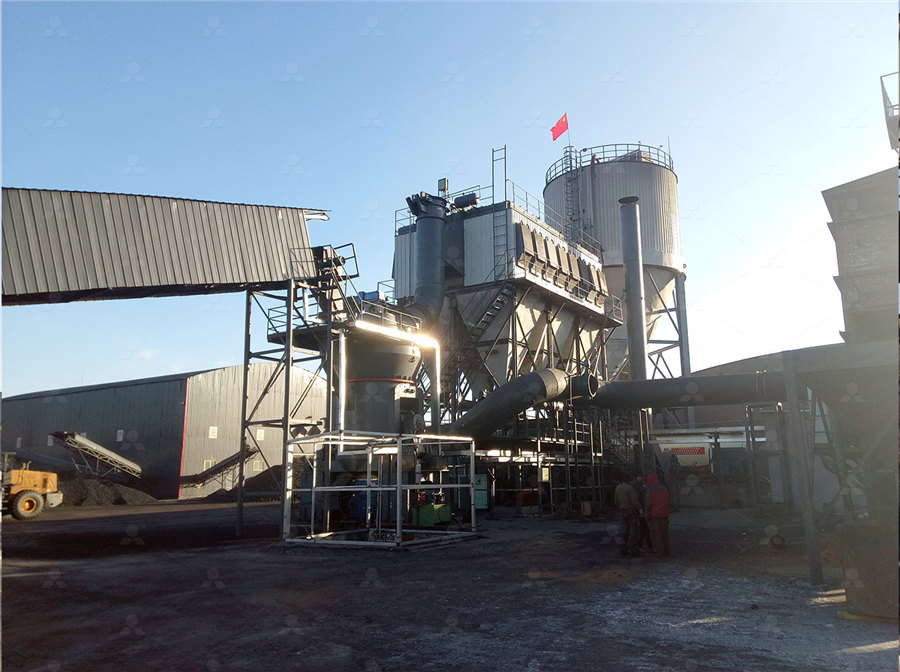
Laterite Nickel Ore Rotary Kiln
3 High production quality: nickel iron produced by laterite nickel ore Rotary kiln is of high quality, containing about 20% Ni, and can be directly used as raw material for stainless steel production 4 Diversified uses: The nickel products produced have a wider range of uses and can also be used as a coolant for molten steel meltingAGICO CEMENT is devoted to being the No1 rotary kiln manufacturer and professional enterprise of import and export trade Our main business is rotary kiln equipment such as cement kiln, lime rotary kiln, and shaft kiln Direct Line: +86 : info@rotarykilnfactoryRotary Kiln for Liion Battery Material Preparation2020年10月1日 The rotary kilnelectric furnace (RKEF) process is the primary method for extracting nickel from saprolite ores In this technique, the ore is first calcined and prereduced at 850–1000 °C in a rotary kiln followed by smelting in an electric furnace at 1500–1600 °C (Eliott, 2015, Warner et al, 2006)The effect of sulfur in rotary kiln fuels on nickel laterite 2020年11月1日 In addition, the effect of the magnetic intensity on the separation indexes of nickel and iron were investigated, as shown in Fig 4 (e) and (f) The recovery ratios of nickel and iron continuously increased from 8253% to 9244% and from 8583% to 9117%, respectively, as the magnetic intensity increased from 50 to 100 mT As the magnetic Separation and recovery of iron and nickel from lowgrade
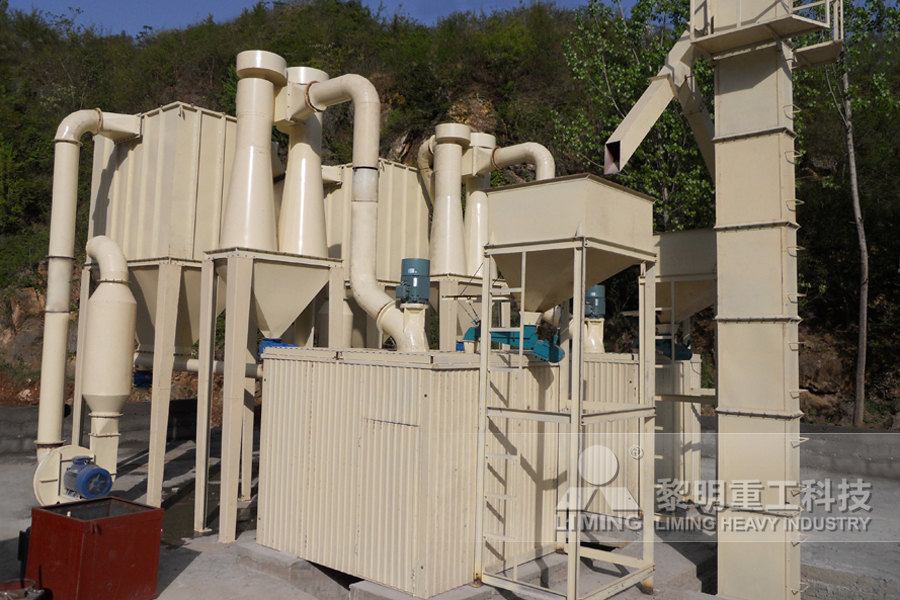
(PDF) Improving the rotary kilnelectric furnace process for
2021年9月16日 The primary pyrometallurgical route to produce ferronickel from laterite nickel ores is the Rotary KilnElectric Furnace (RKEF) process In the RKEF process, minerals undergo calcination and