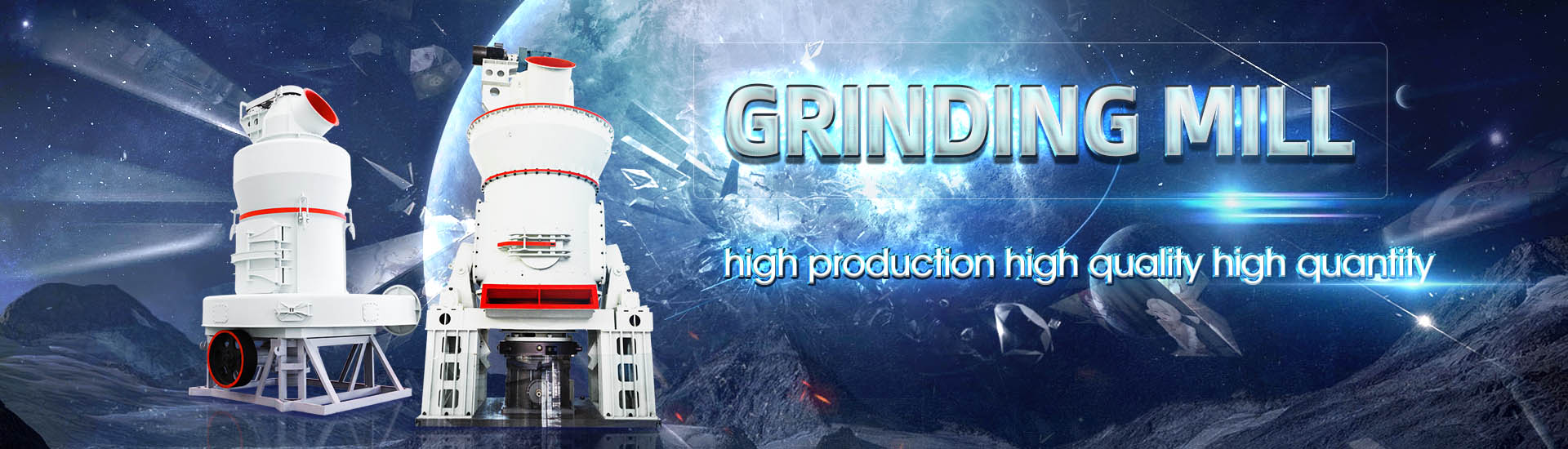
Ultrasonic ore mill for mining
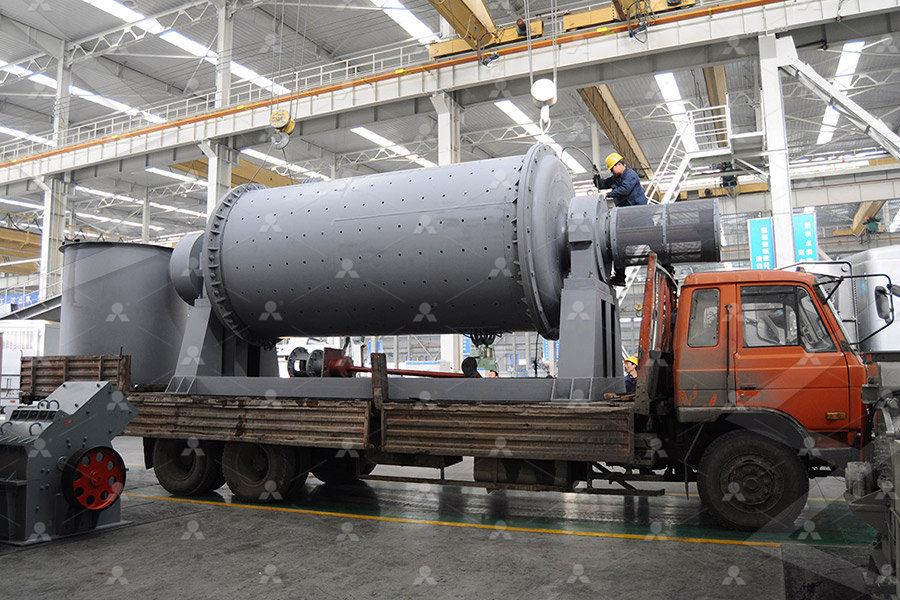
Ultrasonic Waves in Mining Application IntechOpen
ultrasonic pulses are high in homogenous rock masses with high mechanical properties (UCS, tensile strength, cohesion, internal friction angle), which can be used as identification method of the quality of any rock structure2023年1月1日 A solution could be the application of power ultrasound The new design addresses the milling problems by combining mechanical characteristics of a conventional Applications of power ultrasound in mining ScienceDirect2015年1月1日 This chapter deals with the application of power ultrasound in the mining industry The uses of power ultrasound are addressed in three aspects: (1) determination of the stress The use of power ultrasound in mining ScienceDirect2015年12月31日 The uses of power ultrasound are addressed in three aspects: (1) determination of the stress state of rock mass for safety reasons and to plan mining work; (2) The use of power ultrasound in mining Request PDF ResearchGate
.jpg)
Mining Mill Condition Monitoring Using Water Jet Ultrasonics
water jet ultrasound scanning system for condition monitoring of the shell of a rotating mining mill The practical requirements of such a system were first analyzed, which shows that it is 1993年6月1日 This paper presents grinding results obtained with a Chilean porphyry copper ore in the ultrasonic nip roll grinder of the US Comminution Center Comparison with ball milling is Exploring the ultrasonic comminution of copper oresThe OPUS ultrasonic extinction system from Sympatec monitors the particle size distribution as well as the solid concentration in opaque and highly concentrated ore and mineral slurries on Ultrasonic extinction for full concentration, real time particle size 2014年1月1日 The research aims to improve indicators of mined ore mass extraction when mining rich iron ores through studying and optimizing consumption of explosives, enhancing Ultrasonic facilities for the ground materials characteristics control
.jpg)
Study of the effect of ultrasonic treatment on mineral materials of
2016年5月1日 Ultrasonic treatment was concluded to be capable of assisting in the comminution of friable ores more prominently than the hard and porous materials Coal, iron and Coal, iron and manganese ore samples were exposed to different ultrasonic intensities of 250, 300 and 350 W/L for ¿ve minutes and to an ultrosonic intensity of 270 W/L for different time Study of the effect of ultrasonic treatment on mineral materials of 2017年2月24日 If you’d like to learn more about the application of ultrasonic testing at your mining operation or would information on any other nondestructive testing equipment, you should call the Ultrasonic testing – An essential NDT technique for the mining 1993年6月1日 This paper presents grinding results obtained with a Chilean porphyry copper ore in the ultrasonic nip roll grinder of the US Comminution Center Comparison with ball milling is performed by scalingdown industrial ball mill behavior to the ultrasonic grinding conditions International Journal of Mining Science and TechnologyExploring the ultrasonic comminution of copper ores
.jpg)
UNDErsTaNDINg MINE TO MILL 911 Metallurgist
Understanding Mine to Mill is presented in five parts Part A – Setting the Scene provides some definitions of Mine to Mill (M2M) and the historical background A chronology of Mine to Mill developments is followed by brief descriptions of the very wide range of Mine to Mill applications which have been implemented over the last 15 yearsAfter passing the measuring zone the ultrasonic waves are received by an ultrasonic detector and converted into an electrical signal The extinction of the ultrasonic waves is calculated from the ratio of the signal amplitudes on the generator and detector side, the frequency of the ultrasonic wave may be varied between 100 KHz and 200 MHzUltrasonic extinction for full concentration, real time particle size Water flow ultrasonics was used to measure discontinuities in mining mill shell by Stenström et al (2012, 2015); see Figure 11 This project extends the previous research on mill shells to the study of mill lining thickness Nondestructive testing (NDT) refers to noninvasive techniques used for characterisation and inspection of objectsUltrasonics for Monitoring of Mining Mill Linings DiVA2015年9月1日 A larger test setup is to be designed for measurement through steel Also, new projects have been initiated as a result, regarding periodic ultrasonic testing of bricks of pelletizing plant, of conveyor belts in mining and of ReRail for railways The pilot project is also interesting for lining in pipes and pipelinesMeasuring the thickness of mill lining with ultrasound during operation
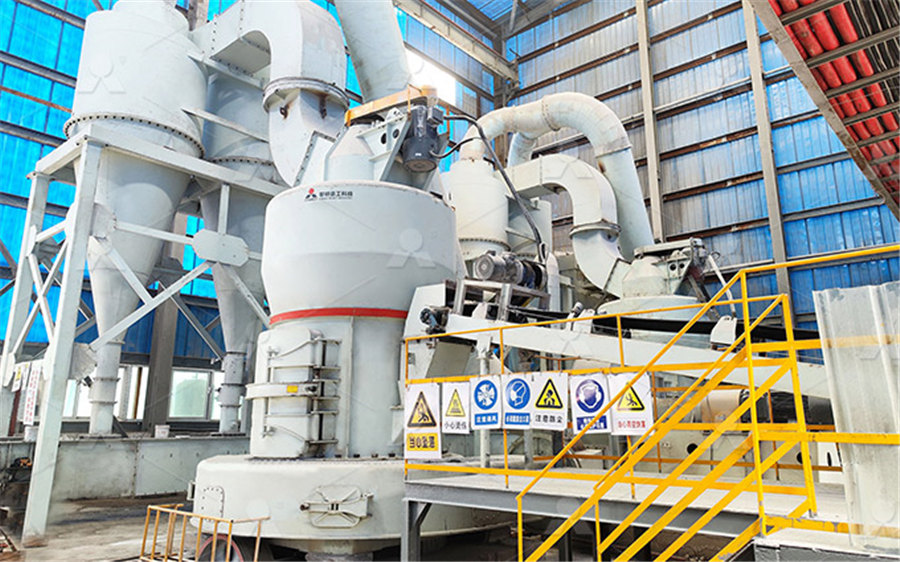
Conveyor Transfer Chute Level Monitoring Hawk Measurement
Blocked chute detection in a Mining process application is crucial to the operational performance of the site Hours lost to downtime caused by a blockage in a conveyor transfer chute can take hours to clear, which in dollar terms can mean thousands of dollars in lost production and a delay in production schedulesmill charge enables not only solving the problem of filtration aimed to obtain data on the object’s current state, but also predicting its state 1 Introduction Development of resourcesaving technologies and automated control means for ore mining and processing is required to assure competitive products of mining and concentrationAdaptive control of ore mill charge2023年7月22日 Ore fine crushing is a process of crushing ore blocks with a feeding particle size of 50–150 mm to 5–25 mm, and the maximum crushing ratio of fine crushing is about five The main equipment suitable for fine crushing operations includes a fine crushing jaw crusher, short head cone crusher, highpressure roller mill, etc Ore superfine crushingOre Crushing SpringerLink2023年6月17日 The aim of a mineral processing operation is to concentrate a raw ore for the subsequent mineral extraction stage Usually, the valuable minerals are first liberated from the ore matrix by comminution and size separation processes (crushing, grinding, and size classification) and then separated from the gangue using processes capable of selecting the particles Automation and Robotics in Mining and Mineral Processing
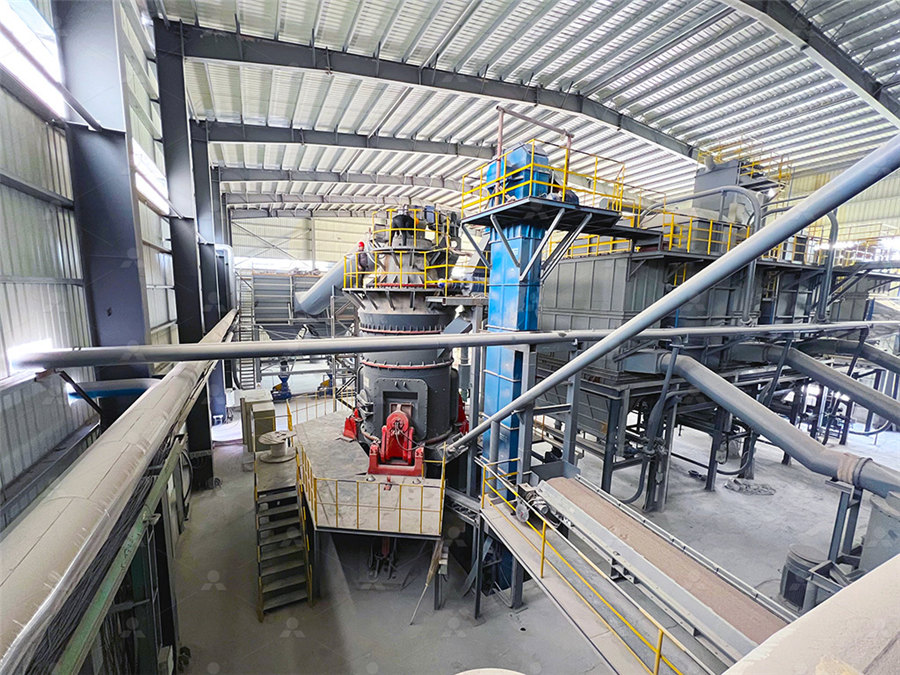
Effect of Combined Mechanical and Ultrasonic Milling on the Size
2019年7月16日 This study aims to investigate the effect of combined mechanical and ultrasonic milling on the size reduction of talc Firstly, the talc sample was wet ground in a stirred media mill for five different times (30, 60, 90, 120, and 150 min), and the optimum result was subsequently achieved with treatment by ultrasonication The effects of amplitude (20, 35, and 50 μm), solid 2018年2月1日 We have carried out Ultrasonic Pulse Velocity (UPV) measurements and Uniaxial Compressive Strength (UCS) tests on a large number of sandstone samples of coal mining industry in our laboratoryHighprecision Ultrasonic Flowmeter for Mining 2021年12月21日 A common asset maintenance problem across the mining and metals industry is the predictive maintenance of wear linersTraditionally, the erosion of wear liners could only be measured by ultrasonic thickness Wireless realtime liner wear monitoring improves volved in constructing an ultrasonic inspection system suitable for condition monitoring of a fullscale mining mill If amplitudes of reflected ultrasound waves are to be used to image the interior of the mill shell, the maximum achievable spatial resolution of this image (ie the C Mining Mill Condition Monitoring Using Water Jet Ultrasonics
.jpg)
Exploring the ultrasonic comminution of copper ores
1993年6月1日 Minerals Engineering, Vol 6, No 6, pp 607617, 1993 08926875/93 $600+000 Printed in Great Britain 1993 Pergamon Press Ltd EXPLORING THE ULTRASONIC COMMINUTION OF COPPER ORES C YERKOVICi, J MENACHOi and L GAETEt The Mining Metallurgical Research Center of Chile, CIMM, PO Box 170, Santiago 10, Chile t University The extravagance of the mill was detailed by Eliot Lord in his 1883 book Comstock Mining and Miners: “The extraordinary mill of the Gould Curry Company was, It is almost impossible to describe, let alone do justice to, the variety of processes that have been used to mill oreWinning the Metal: Ore Mills of the West Western Mining magnetic separator using ultrasonic methods, developing and substantiating methods to enhance efficiency of iron ore magnetic separation by applying ultrasonic technologies 1 Introduction Sustainable industrial development calls for solving the topical problem of reducing costs and energyintensity of iron ore mining and processing [15]Increasing efficiency of iron ore magnetic separation by using data of size degradation of one kilogram of sample weights in a ball mill Ultrasonic treatment of skarn scheelitesulphide ore was performed using UZDN2T content is decreasing in head ore For plant finishing field mining, the increase in feasibility of mining is connected with the stimulation of flotation processes by means of ore feed, Skarnscheelite ores beneficiation stimulation using ultrasonic
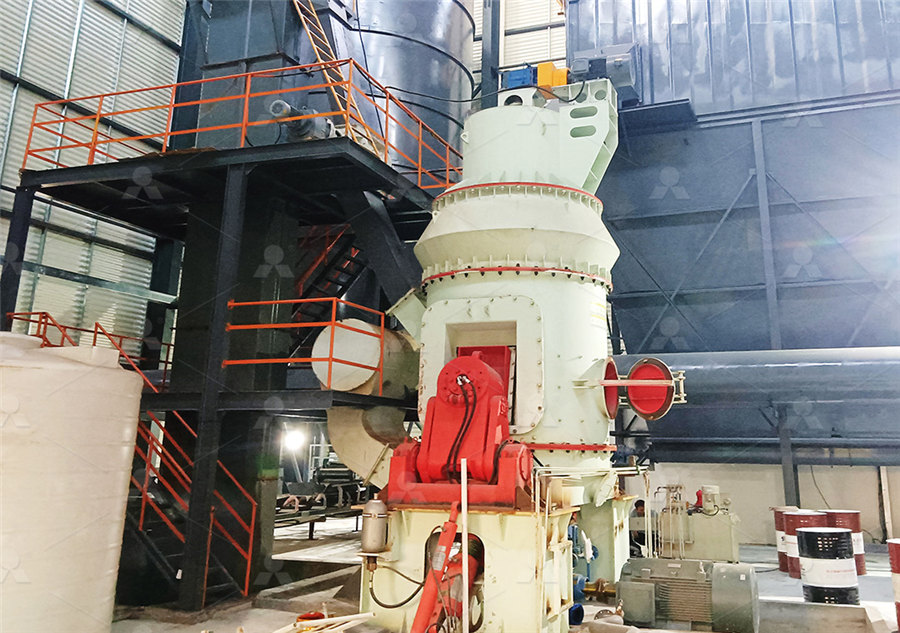
Stutenroth Impact Mill – GameChanging Gold Mining Machinery
Its ability to effectively crush and grind hard rocks, coupled with its adjustable settings and durable construction, make it a standout performer in the industry If you’re looking for a reliable and efficient gold ore mill that can handle the demands of hard rock mining, the Stutenroth Impact Mill should be at the top of your listWhen choosing your equipment we not only keep in mind mill performance, but also considering how your Premier™ or Select™ mill will optimize your minerals processing circuit Performance Metso Premier™ mills and Select™ mills are built with a robust design and components to eliminate unplanned downtime leading to high availability and reliabilityGrinding mills for mining and minerals processing Metso2021年4月19日 PDF Published in MATERIA 2021;23:6366 The idea of minetomill optimization has been tested in various mines in last decades, resulting in higher Find, read and cite all the research you (PDF) Feasibility and necessity of mine to mill 2018年2月15日 Ultrasonic vibration assisted grinding (UAG) is a nonconventional machining process which plays an important role in machining hard and brittle material with a success in terms of decreased cutting force, extended tool life and significant reduced cutting temperature [15], [16], [17]As an alternative to reactive ion etching and laser micromachining, UAG Ultrasonic vibration millgrinding of singlecrystal silicon carbide
.jpg)
Boltstress Mining Technology
Boltstress Ultrasonics has been providing bolting solutions for over 30 years to the mining, refining Since the mid 1990’s mill manufacturers have been using Ultrasonic Bolt Tension mills are a key piece of equipment widely used in 2016年2月1日 The purpose of this study is to understand how ore loss and dilution affect the mine call factor, with the aim of subsequently improving the quality of ore mined and fed to the millMonitoring ore loss and dilution for minetomill integration in The ball mill is the key equipment for crushing materials after they have been crushed It is suitable for grinding ores and other materials and is widely used in nonferrous metal mining, nonmetallic mining building materials, the chemical industry, electric power, coal, transportation, cement, silicate products, new building materials, refractory materials, and glass ceramics, etcAIMIX Ball Mill For Sale For Gold Mining ProcessingHGM ultrafine grinding mill can process nonmetallic ores with Mohs hardness less than 7 The equipment has stable operation, simple operation, long service life, low carbon and environmental protection There are 5 models of HGM ultrafine grinding mill, SBM Ore Ultrafine Grinding Mill
.jpg)
Common Basic Formulas for Mineral Processing Calculations
2016年3月21日 where R represents the ratio: % Pb in crude ore/% Cu in crude ore Formula (32) is very convenient for milling calculations on ores of this type Example: An ore contains 5% lead and 1% copper The ratio of perfect concentration for a concentrate of maximum grade and 100% recoveries of lead and copper would be:Ore seParatiOn PrOJect The concept behind the UG2 ore separation project was derived from the unique nature of UG2 mineralogy, namely: • Most PGM rich minerals in the runofmine ore are associated with the chromerich fraction in the ore (the UG2 reef itself) The friable nature of the ore and the intergranularPGM Ore Processing at Impala's UG2 Concentrator SGS2023年9月26日 Has anyone here have had experience grinding ore with an air mill? if so, any info on its use and operation would be very helpful thank you! Buck Forums New posts forums What's new New posts Latest activity It works by ultrasonic distortion of an air vortex with increasing collision rate https://flexicone Vortex Air Mill Ore Grinding Gold Refining Metal Extraction Variability in ore type and changes in liner materials can impact the wear rates experienced by the liners used to protect the inner walls of transfer and feed chutes This variability can lead to increased operational costs due to unplanned maintenance which may be required to replace highly worn linersReducing operating costs by monitoring chute liner wear in real
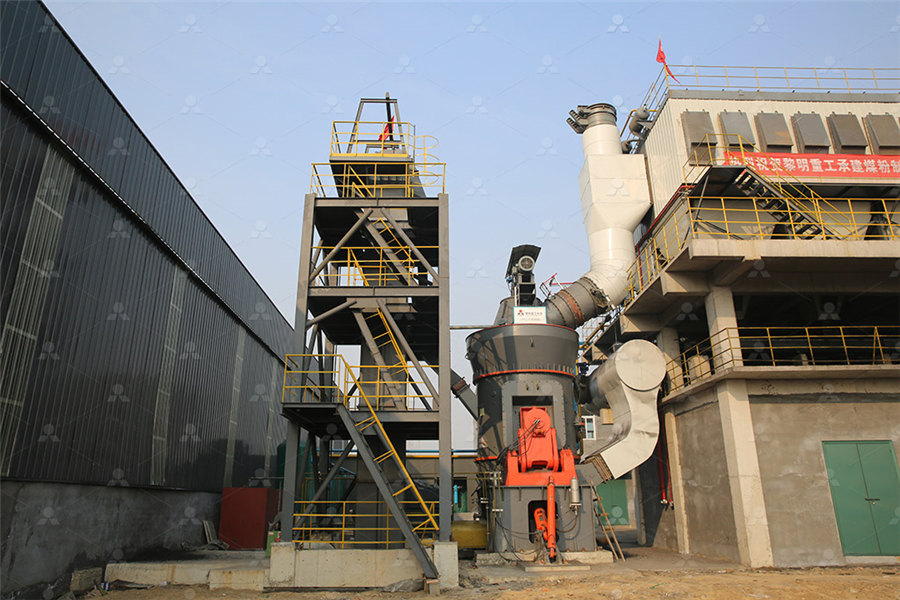
(PDF) Ore Sorting Automation for Copper Mining
PDF On Mar 25, 2021, Jukka Raatikainen and others published Ore Sorting Automation for Copper Mining with Advanced XRF Technology: From Theory to Case Study Find, read and cite all the Based on the model of mining and processing equipment, the design, putting into production, joint tests of lining with the customer are carried out Warranty is provided Generic Lining Products Overall wearresistant plates Used for Rubber Lining for Ore Grinding Mills and Mining and However, emphasis on generating more tonnage to the mill in mining operations has resulted in loss of focus in this area There is a need to close this gap The primary objective of this study was to understand how ore loss and dilution Monitoring ore loss and dilution for minetomill 2023年10月27日 The ball mill is a rotating cylindrical vessel with grinding media inside, which is responsible for breaking the ore particles Grinding media play an important role in the comminution of mineral ores in these mills This work reviews the application of balls in mineral processing as a function of the materials used to manufacture them and the mass loss, as A Review of the Grinding Media in Ball Mills for Mineral Processing
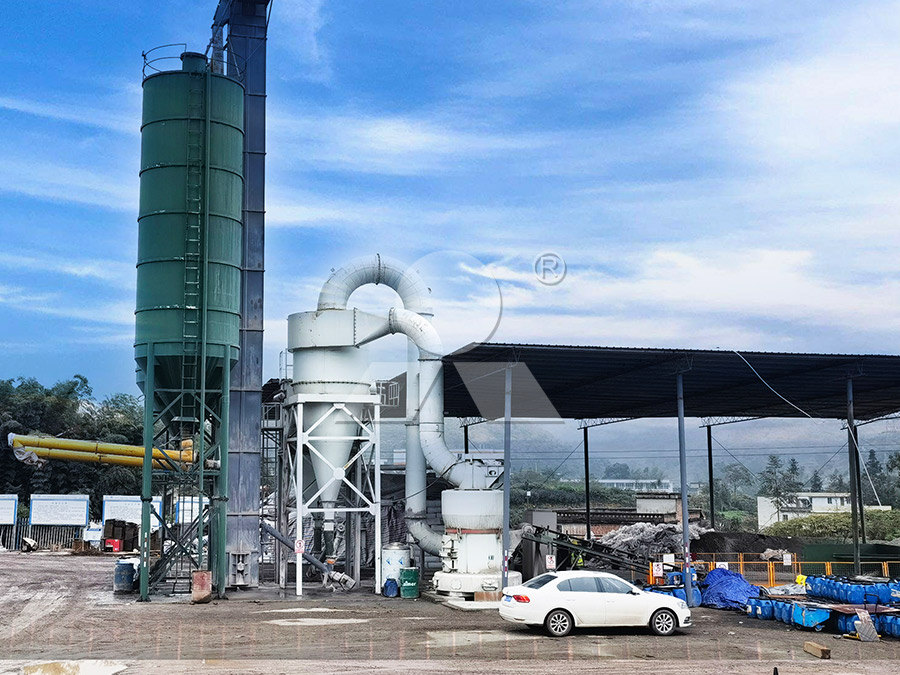
Improved flotation of arsenopyrite by ultrasonic pretreatment
Key words: Ultrasonic pretreatment, Flotation, Zetapotential, Arsenopyrite flotation, Gold recovery Introduction The continued and increased mining for gold has decreased the availability of freemilling ores, which can be treated easily by cyanidation In recent years, the mining of refractory ore deposits has increasedUltrasonic vibration lapping is a highly precise metalcutting manufacturing technique According to the DIN 8589 standard, ultrasonic vibration lapping is classified as lapping Unlike other lapping processes, it is only used for drilling and cutting The tool vibrates at ultrasonic frequency in the longitudinal directionULTRASONIC Machining Tools DMG MORI USAUltrasonic cleaning provides reliable, efficient and environmentally friendly cleaning solutions in mining facilities and industrial plants Systems can be used to clean parts and components in the field, in mines, in industrial plants and within manufacturing facilities reducing the amount of time that it takes to render components safe, clean and ready for useMining Benefits Sunflower UltrasonicDOI: 101016/JULTSONCH201904033 Corpus ID: ; Ultrasonicassisted flotation for enhancing the recovery of flaky graphite from lowgrade graphite ore @article{Barma2019UltrasonicassistedFF, title={Ultrasonicassisted flotation for enhancing the recovery of flaky graphite from lowgrade graphite ore}, author={Santosh Deb Barma and Ultrasonicassisted flotation for enhancing the recovery of flaky
.jpg)
MARC Technologies » ISO Tumbler / Tumble Mill for Iron Ore
ISO Tumbler / Tumble Mill for Iron Ore MARC designs and manufactures an ISO Tumble Mill for Iron Ore This product is available in two versions for two budget ranges: Basic and Advanced Our Basic version is shown below, however our Advanced product has many enhancements – c ontact us via our “Contact US” page to discuss your needs2019年2月27日 Ultrasonic Sensors in Mining Equipment In mining, mineral and metal processing technology is essential This technology separates the valuable minerals from waste which is usually done so using magnets Challenge: Monitor water level in the dirty tank In this mining application, ferrous minerals are being removed from a slurry via a magnetic How Ultrasonic Sensors Can Be Used in Mining Equipment