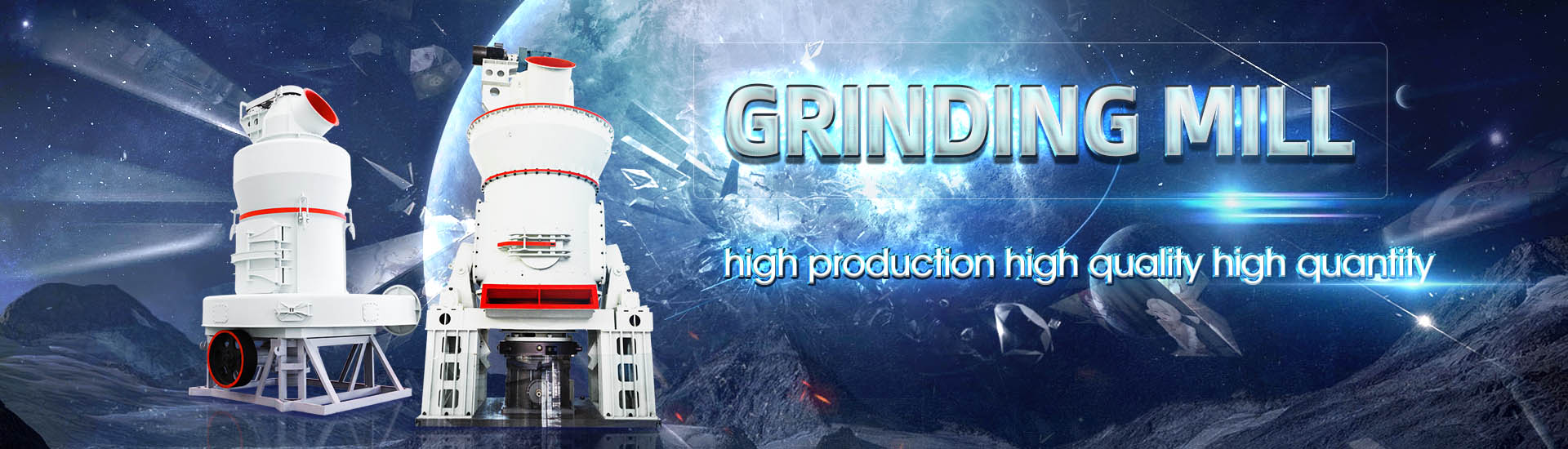
Ball mill lining improvement
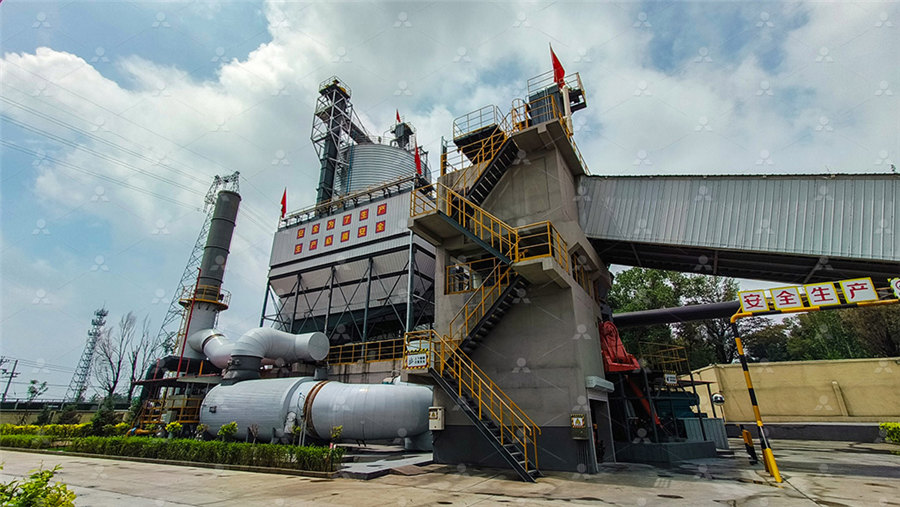
Improving the design of the lining of the ball mill used
Based on the study, an improved lining design was developed in order to reduce the impact load and increase the friction surface between the lining and the balls (Figure 2) As a result, the 2022年11月1日 Another obvious difference in design between the full and labscale ball mills is the lining plates, also known as liners The main role of liners is to protect the mill shell from Impact of ball size distribution, compartment configuration, 2007年10月19日 With the current improvement in computer power and speed, the DEM has emerged as a powerful tool for modelling mill load behaviour, hence may be useful in selection A new approach to optimising the life and performance of 2023年12月1日 One method of preventing ball mill failures and minimizing company losses on a large scale is to predict the life of ball mill liners or predictive maintenance Using a 3D laser Predictive maintenance on ball mill liner using 3D scanner
.jpg)
Friction and wear characteristics and simulation study of NM500 lining
2024年9月12日 Peng et al conducted experiments on Mn16 stainless steel lining samples using the ball indentation method under dry grinding and wet grinding conditions to simulate the This article discusses the traditional ball mill lining used and the improved ball mill lining Experimental data of the proposed and previous linings are presented The economic effect of [PDF] Improving the design of the lining of the ball mill used 2024年7月24日 Through a modification of the liner design, simulations demonstrated the potential benefit associated to reduction in ultraprojection and improvement in mill capacity Continuous improvement in SAG mill liner design using 2014年10月20日 Through a modification of the liner design, simulations demonstrated the potential benefit associated to reduction in ultraprojection and improvement in mill capacity Implementation of the new(PDF) Continuous improvement in SAG mill liner
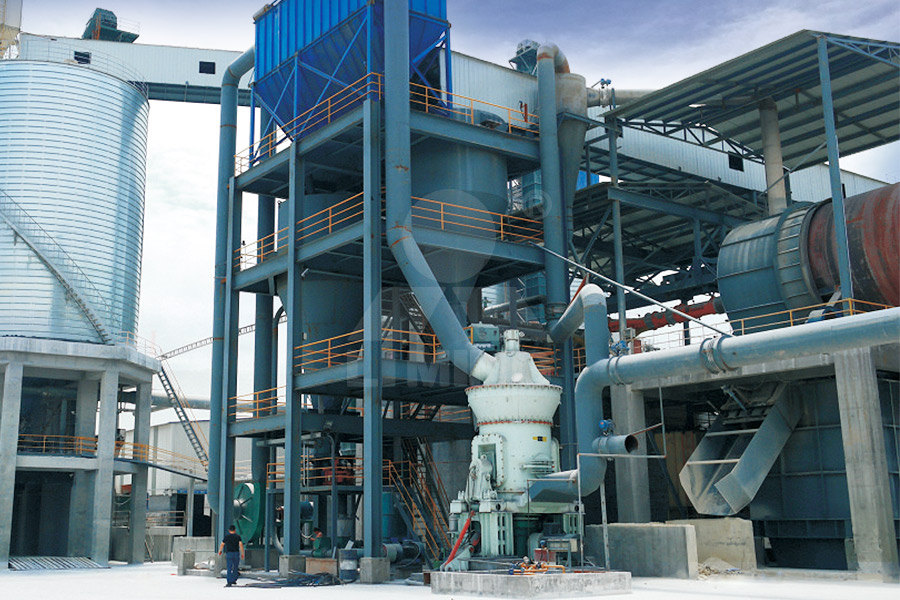
Mill lining solutions for horizontal Metso
2021年8月11日 Using each lining material where it performs the best makes it possible to achieve results, such as energy savings by reducing the mill’s overall weight, balanced wear conditions of shock – abrasive wear [6] The current structure of the lining in the mill works at high shock loads, and in addition, as a result of the impact of the balls on the surface of the lining under the action of a certain force, the balls are destroyed The lining experiences a high impact load, and the balls are chippedImproving the design of the lining of the ball mill used The Tega DynaWear® rubber lining system is the preferred lining system for secondary ball mills, regrind mills and scrubbers DynaWear® rubber mill linings are individually designed for your particular working conditions and goals, with Tega DynaWear Rubber Mill Liner Manufacturer 2016年1月5日 Mill HEAD LINERS Head liners are of the segmental type constructed of Manganese Steel, Chrome molybdenum, or NiHard and are designed to pass easily through the manhole opening or discharge opening in Ball Mill Liner Design 911Metallurgist
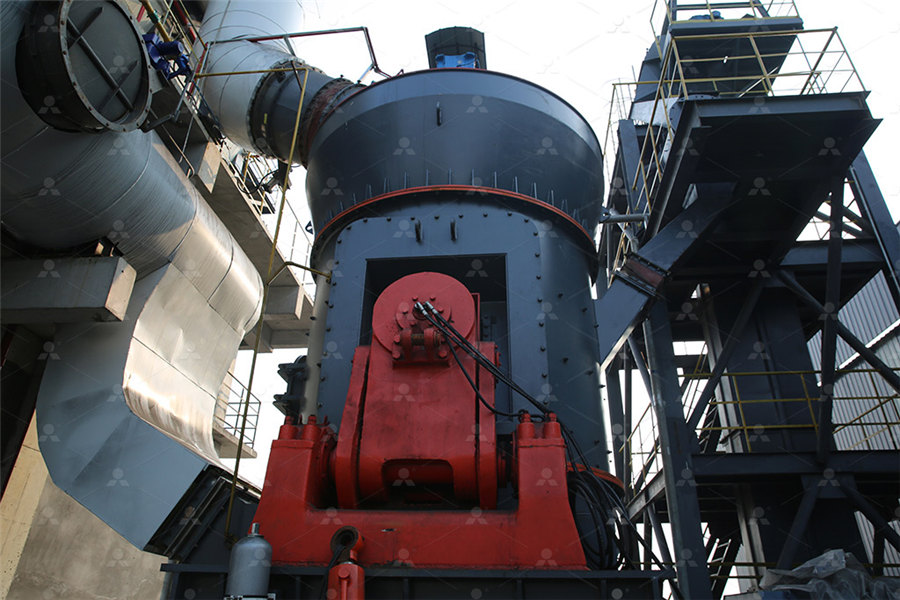
(PDF) Continuous improvement in SAG mill liner design
2014年10月20日 The smoothed particle hydrodynamic (SPH) method is used to model a ball charge and its interaction with the mill structure, while the flexible rubber lifter and the lining are modelled with the Optimal mill lining solution for your specific mill Promote safety, improve grinding efficiency, reduce downtime and enhance profitability Continuous improvement A mill lining is a customized wear part Identifying the appropriate type of lining and design is vital for optimizing mill throughput and total grinding costs, including costs Mill liners Metso2023年8月21日 In most cases, ball mills do not consider the wear of the mill lining, the filling of balls, the speed of rotation of the mill drum for the consumed electrical energy The main problemImprovement of methods to ensure energy efficiency of ball mills 2024年8月13日 MAGNETIC MILL LINERS: An Innovative Ball Mill Lining Technology Jaime Sepúlveda1*, Walter Gómez 2, Alejandro Rodríguez3 and José Marín4 1 Director Ejecutivo, JConsultores Ltda, Chile 2 Jefe de Molienda y Concentración Magnética, CMP Planta Pellets, Chile 3 Consultor de Procesos, Polimin SPA, ChileMAGNETIC MILL LINERS: An Innovative Ball Mill Lining

Mill lining solutions for horizontal Metso
2021年8月11日 With Metso Outotec mill lining solutions, we help you overcome these challenges We have years of experience Together towards continuous improvement 4 All types of mill linings No other mill lining supplier has as wide a and the discharge system The concept is best suited for large AG, SAG and ball mills with large trunnions and where 2024年7月24日 Steel balls with a diameter ranging between 1030 mm and a density of 7800 kg/m3 were used a b Figure 1 Mill experimental setups a) Pilot mill with rubber lining b) Lab mill for torque Continuous improvement in SAG mill liner design using Ball mills are used for the stage of grinding ore in mining operations with the alignment of grinding balls Controlling the operating conditions of ball mills is a key factor for optimal mill operation and high mill productivity The main factors affecting the efficiency of a ball mill are ball loading, drum rotation, lining wearImprovement of methods to ensure energy efficiency of Depending on your goals and application, we offer a range of premium composite and rubber mill lining solutions for rod, ball, AG and SAG mills Rubber mill lining is predominately used for smaller secondary and tertiary ball milling (regrind), whereas our composite mill liners (made from one or more materials) are used for heavyduty primary and secondary AG / SAG mill lining Customised Vulco® Mill Lining Systems Weir Weir Group
.jpg)
Impact of ball size distribution, compartment configuration,
2022年11月1日 Another obvious difference in design between the full and labscale ball mills is the lining plates, also known as liners Overall, compared to the spatially uniform distribution of the ball mixture, significant improvement was not observed when using a classifying liner in both threecompartment and twocompartment mills These results 1 Tashkent State Technical University, Tashkent, , Uzbekistan 2 Namangan EngineeringConstruction Institute, Namangan, , Uzbekistan 3 National University of Science and Technology “MISIS” in Almalyk, Uzbekistan * Corresponding author: anvarovichsarvar908@gmail Abstract This article discusses the traditional ball mill lining Improving the design of the lining of the ball mill used to 2022年6月30日 When grinding cement, ferrous and nonferrous metals is commonly used drum ball mills For example, the share of cement in grinding mill consumes more than 60% of the energy used to manufacture itImprovement of the structure of a ball mill with the purpose 2024年9月12日 The ball mill is one of the most commonly used equipment in industrial production, widely used in fields such as mining, building materials, and the chemical industry []As one of the critical components of the ball mill, the liner plate bears the impact and friction of the grinding ball []Therefore, improving the material of the liner plate is of great significance Friction and wear characteristics and simulation study of NM500 lining
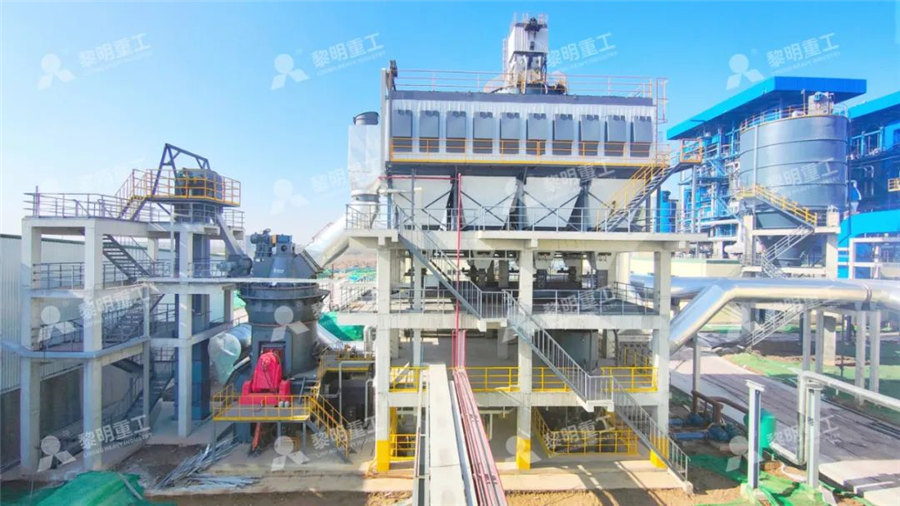
Ball Mills 911Metallurgist
2017年2月13日 Rubber lining, grate mill Ball Mill Charge volume The mill power is approximately directly proportional to the charge volume within the normal range When calculating a mill 40 % charge volume is generally used In pebble and ball mills quite often charge volumes close to 50 % are used In a pebble mill the pebble consumption ranges from The mill liner is installed inside the ball mill barrel to protect the inner wall of the barrel from the impact of materials and grinding media (steel balls, steel sylpebs, steel rods, etc) to avoid premature damage to the barrelAs an important part of the ball mill, the mill lining needs to be designed according to the materials to be processed and different grinding typesMill Linings for Sale, Types of Ball Mill Liners ball mills 2023年10月2日 design to maximize mill availability The shell lining has a major influence on grinding efficiency It transforms the mill rotation into charge motion, and both profile and spacing must be selected to suit each specific mill When designing a shell lining, the type of ore, mill size and speed, maintenance schedules, safety,Taking your grinding to the next level Mill lining 2018年3月1日 Download Citation Improvement of high manganese steel in ball mill lining The problem of easy cracking and deformation of high manganese steel wear liner was studied by analysis of composition Improvement of high manganese steel in ball mill lining
.jpg)
(PDF) Performance optimization of an industrial ball mill for
2017年1月1日 An increase of over 10% in mill throughput was achieved by removing the ball scats from a single stage SAG mill These scats are non spherical ball fragments resulting from uneven wear of balls 2020年11月22日 Wear Resistance Improvement for Grinding Balls of Horizontal Cement Mill in Cement Plant by NanoCoating Technique of Cement Clinker in the Ball Mill", IOP Conf, Series: Materials Science and Wear Resistance Improvement for Grinding Balls of The unique wearprogression model predicts the performance of the lining extremely accurately and can be calibrated using wearmonitoring data to further optimize the liner design It is the market’s most advanced software for Mill liner wear and performance monitoring2023年3月17日 factors in choosing the diameters of steel balls in order to reduce the maxi mum specific pressures (stresses) on the rubber lining of the mill Starting in 1965 to create a rubber lining design, the above arguments and the factor of impact energy transfer propagated in the lining array in the form ofPerspective of Use of Rubber Linings in Drum Ball Mills
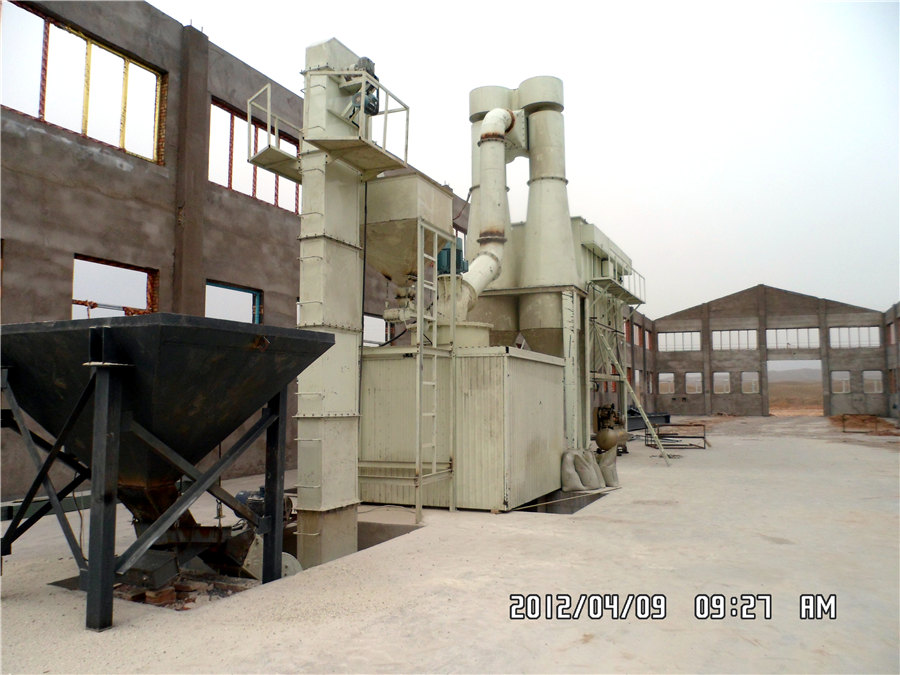
Products BA Mining Solutions Pte Ltd
Ball Mill Lining, Scrubber Lining, Batch Mill Lining, Rod Mill Lining, Mixing Drum Lining , Pebble Mill Lining, Sag Mill Lining, FGD Mill Lining, Regrind Mill Lining FEATURES BENEFITS; Longer Wear life BAM's ball mill rubber liners are pressure moulded to ensure highest density and engineered for maximum abrasion resistance Industry 2024年8月8日 A notable case involved a manufacturer facing contamination issues with steel balls, which affected the consistency and effectiveness of their medication By transitioning to zirconia balls, they observed a marked improvement in product purity, with no detectable contamination, leading to enhanced drug performance and patient safetyBall Mill Success: A StepbyStep Guide to Choosing the Ball Mill Liners We are regularly supplying rubber liners up to 26 ft diameter ball mills We design liners to optimize power for maximum throughput and increased liner life These liners are custom designed for your mills Mining; Ball Mill Liners; PolyStl™ LinersBall Mill Liners PolycorpVega offers optimized CrMo steel, martensitic steel and white iron (16 25% Cr) alloys for Ball Mill Lining System Benefits: Increased life; Optimal lifter profile from process and maintenance benefits; Improved ball trajectory with custom lifter design; Mill Throughput Improvement 5 20 % Mill Energy Reduction 25 40 % Mineral Mining Welcome to AIA Engineering/Vega Industries
.jpg)
Grinding Mill Liners 911Metallurgist
2015年8月6日 Ball mills working as the secondary portion of a grinding circuit will utilize the lower profile liners The reason is as lift decreases, friction increases Instead, three design concepts based on rubber as a lining material will be discussed These are combination liners, rubber grates and rubber covered pulp lifters2020年5月19日 The ball mill liner replacement should in time when the lining plate is excessively worn Therefore, the selection and design of mill liners have always been of great concern to users Function Design of Ball Mill Liners As one of the professional ball mill liners manufacturers, we summarize the main functions of the threepoint ball mill linersBall Mill Liners Selection and Design Ball Mill Rubber LinerMill Lining THOR – R mill liners are manufactured from specially formulated rubber compounds, which are blends of Natural and Synthetic rubbers The T800 rubber formulation series have proved its robustness over time, through installations across a wide range of Ball Mill Lining Thejo Australiaconditions of shock – abrasive wear [6] The current structure of the lining in the mill works at high shock loads, and in addition, as a result of the impact of the balls on the surface of the lining under the action of a certain force, the balls are destroyed The lining experiences a high impact load, and the balls are chippedImproving the design of the lining of the ball mill used
7TOCS.jpg)
Tega DynaWear Rubber Mill Liner Manufacturer
The Tega DynaWear® rubber lining system is the preferred lining system for secondary ball mills, regrind mills and scrubbers DynaWear® rubber mill linings are individually designed for your particular working conditions and goals, with 2016年1月5日 Mill HEAD LINERS Head liners are of the segmental type constructed of Manganese Steel, Chrome molybdenum, or NiHard and are designed to pass easily through the manhole opening or discharge opening in Ball Mill Liner Design 911Metallurgist2014年10月20日 The smoothed particle hydrodynamic (SPH) method is used to model a ball charge and its interaction with the mill structure, while the flexible rubber lifter and the lining are modelled with the (PDF) Continuous improvement in SAG mill liner design Optimal mill lining solution for your specific mill Promote safety, improve grinding efficiency, reduce downtime and enhance profitability Continuous improvement A mill lining is a customized wear part Identifying the appropriate type of lining and design is vital for optimizing mill throughput and total grinding costs, including costs Mill liners Metso
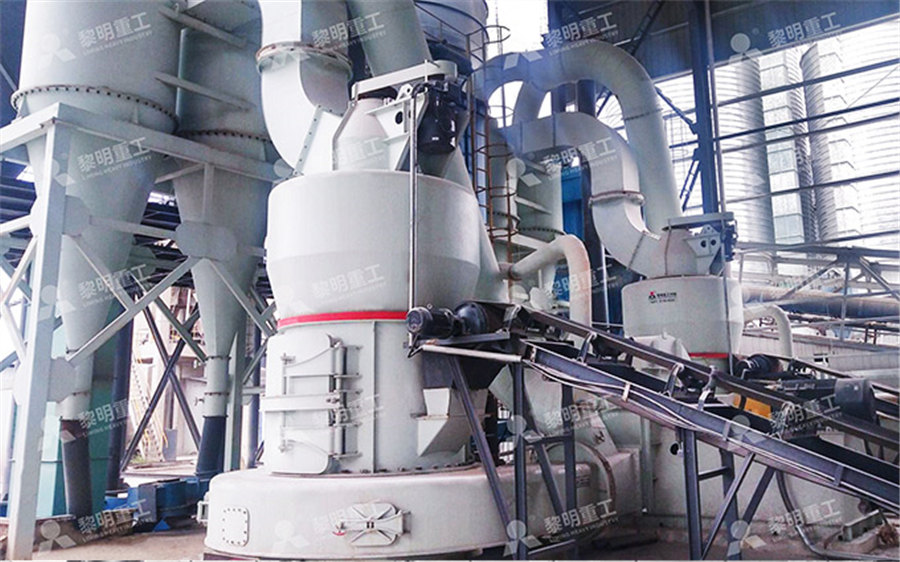
Improvement of methods to ensure energy efficiency of ball mills
2023年8月21日 In most cases, ball mills do not consider the wear of the mill lining, the filling of balls, the speed of rotation of the mill drum for the consumed electrical energy The main problem2024年8月13日 MAGNETIC MILL LINERS: An Innovative Ball Mill Lining Technology Jaime Sepúlveda1*, Walter Gómez 2, Alejandro Rodríguez3 and José Marín4 1 Director Ejecutivo, JConsultores Ltda, Chile 2 Jefe de Molienda y Concentración Magnética, CMP Planta Pellets, Chile 3 Consultor de Procesos, Polimin SPA, ChileMAGNETIC MILL LINERS: An Innovative Ball Mill Lining 2021年8月11日 With Metso Outotec mill lining solutions, we help you overcome these challenges We have years of experience Together towards continuous improvement 4 All types of mill linings No other mill lining supplier has as wide a and the discharge system The concept is best suited for large AG, SAG and ball mills with large trunnions and where Mill lining solutions for horizontal Metso2024年7月24日 Steel balls with a diameter ranging between 1030 mm and a density of 7800 kg/m3 were used a b Figure 1 Mill experimental setups a) Pilot mill with rubber lining b) Lab mill for torque Continuous improvement in SAG mill liner design using

Improvement of methods to ensure energy efficiency of
Ball mills are used for the stage of grinding ore in mining operations with the alignment of grinding balls Controlling the operating conditions of ball mills is a key factor for optimal mill operation and high mill productivity The main factors affecting the efficiency of a ball mill are ball loading, drum rotation, lining wear