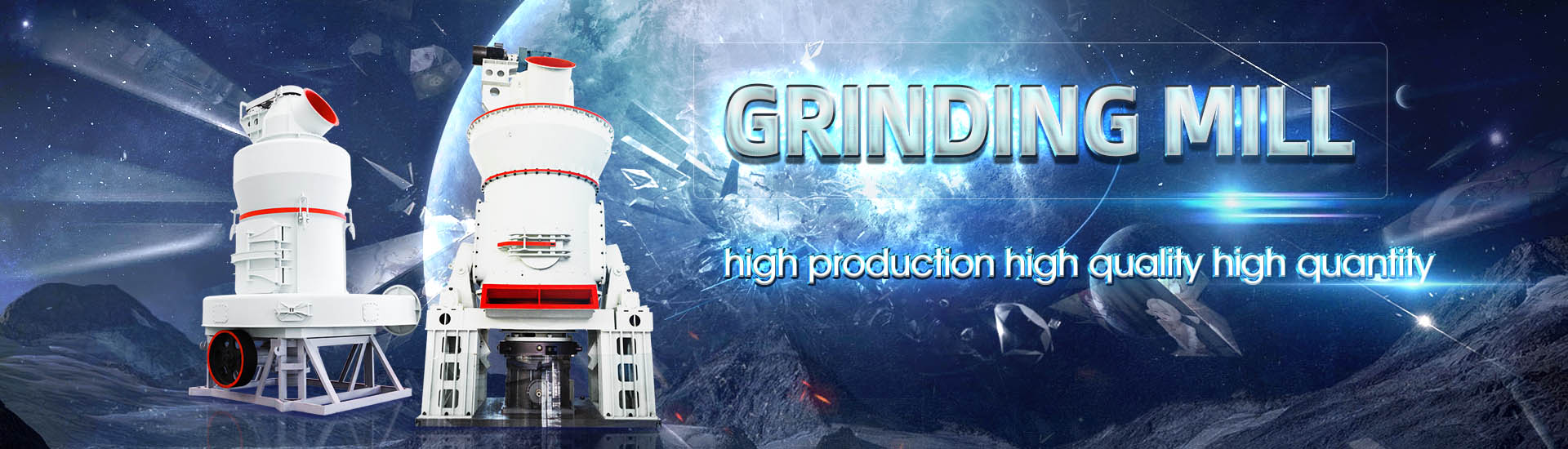
Ultrafine grinding cement plant process flow

What is a ultrafine slag grinding plant? ultrafine slag
2023年10月19日 Simplified process flow It facilitates the implementation of a negative pressure operation system, resulting in dust emissions (under standard conditions) of less than 10 mg/m3, ensuring clean2015年7月21日 This article discusses the range of application of ultrafine grinding for processing mineral raw materials and presents examples of the successful use of this technology in the Ultrafine Grinding in Contemporary Flow Diagrams for Mineral The basic idea of a multistage grinding plant involves a centralisation of all grinding tasks (raw material and cement) in one grinding facility with at least three grinding stages (GS) which provide equipment for coarse/pregrinding (GS1), Study on the production of cements using a multi 2023年7月20日 Ultrafine grinding process is to produce ultrafine ore particles There is no unified standard for the size of ultrafine particles, but it is generally believed that the ultrafine Ultrafine Grinding Process SpringerLink
.jpg)
Typical cement manufacturing process flow diagram
The purpose of this study is to examine the production process, its economic support, raw material availability, demand, process modification, optimization steps to implement the production 2021年3月9日 In this study the process flow diagram for the cement production was simulated using Aspen HYSYS 88 software to achieve high energy optimization and optimum cement flow rate by varying the flow rate of calcium Simulation and Optimization of an Integrated Process Explore Amrit Cement's stateoftheart cement grinding unit Learn about our cement grinding process and plant stages for high quality cementCement Grinding Unit Process High Quality Cement ange of different systems in raw material, coal, and cement grinding While new plants mainly focus on highly energy‐eficient systems, using roller comminution systems like vertical roller Thomas Holzinger, Holzinger Consulting, grinding system
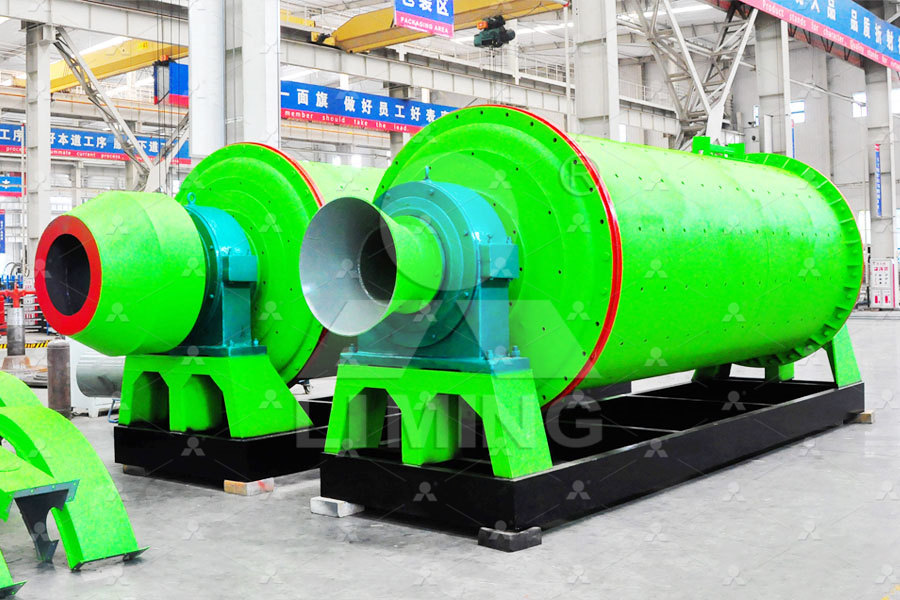
Optimisation of clinkerefficient cements by means of multimodal
2015年1月10日 Separate ultrafine grinding of cement Energyefficient grinding meets optimised cement and concrete properties Today, futureoriented cements can already be Stage 2: Grinding, Proportioning, and Blending The crushed raw ingredients are made ready for the cementmaking process in the kiln by combining them with additives and grinding them to ensure a fine homogenous mixture The composition of cement is proportioned here depending on the desired properties of the cement Generally, limestone is 80%, and the remaining 20% How Cement is Made Cement Manufacturing ProcessWhite Cement Plant The production process of white Portland cement is quite different from ordinary Portland cement It is unique in both process flow and cement equipment selection In white cement plants, the main manufacturing White Cement Manufacturing – White Cement PlantAGICO offers cement production line, stone crushing plant, cement grinding unit, and fly ash processing plant We customize the cement EPC projects for customers according to their requirements Skip to content Blog It acts as CEMENT MANUFACTURING PLANT
.jpg)
Cement Grinding Unit Cement Grinding Plant Cement Grinding
Equipment in cement grinding plant The cement grinding machine includes cement vertical mill, cement ball mill, cement roller press, cement seperator, conveyor and other cement equipmentWe can provide scheme design for free according to the requirements of users, and offer appropriate equipment to ensure smooth production with less investment and high profitThe final manufacturing stage at a cement plant is the grinding of cement clinker from the kiln, mixed with 45% gypsum and possible additives, into the final product, cement In a modern cement plant the total consumption of electrical energy is about 100 kWh/t The cement grinding process accounts for approx 40% if this energy consumptionCEMENT GRINDING SYSTEMS INFINITY FOR CEMENT EQUIPMENTWhat Is Ultra Fine Grinding Mill The ultrafine powder grinding system is a new product independently developed by our company, mainly used to grind and classify various nonmetallic ores in cement plants, such as the grinding of limestone powder, deep processing of pulverized coal, etcThis system is composed of an elevator, airlock device, superfine vertical mill (ultra Ultra Fine Grinding Mill Ultra Fine Powder Grinder AGICOConcrete Cement After grinding, the fly ash can be used as a partial substitute for concrete raw materials Different incorporation of fly ash will affect the hardening level, strength, dry shrinkage and other characteristics of concrete, with an ideal content of 40%Fly Ash Processing Plant Cement Equipment Manufacturing
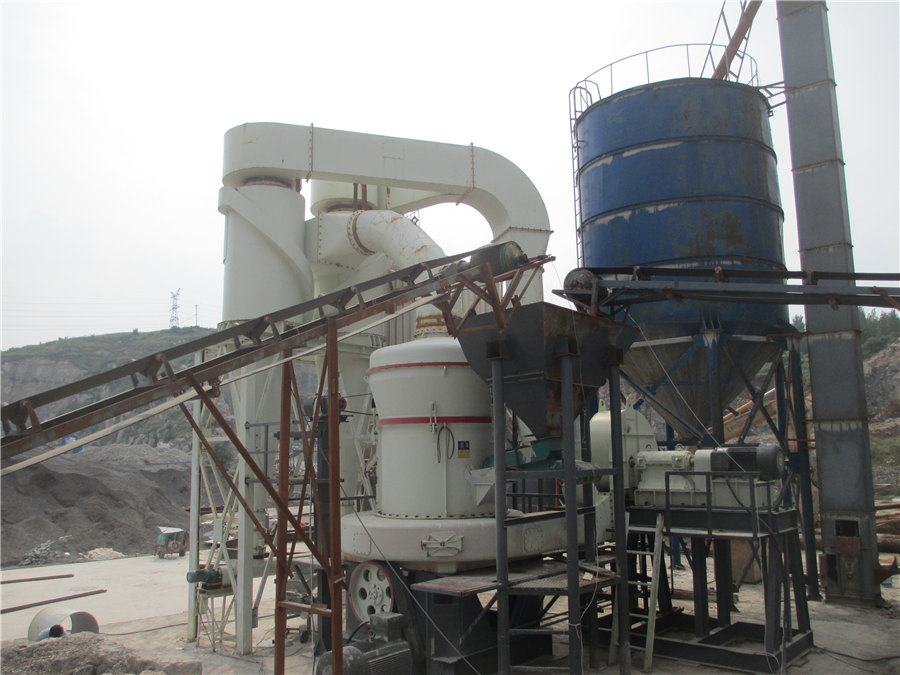
Grinding SpringerLink
2022年2月28日 It is reported that grinding aids improve the grinding process by altering the adhesive forces, the state of fine particle dispersion, and powder flow characteristics Additionally, some research has proven that adding grinding aids can decrease fine particles’ tendency to become agglomerated [ 97 ]2014年6月10日 Evolution of the cement Process • Wet process easiest to control chemistry better for moist raw materials • Wet process high fuel requirements fuel needed to evaporate 30+% slurry water • Dry process kilns less fuel requirements • Preheater/Precalciner further enhance fuel efficiency allow for high production ratesCement manufacturing process PPT Free Download SlideShareIn this universal grinding unit, raw grinding is to be realised by the crusher as well as the conventional grinding unit, and cement grinding by the conventional as well as the ultrafine grinding unit In this study, mass flows as well as heat balances will be considered under various scenarios involving different raw materials and end productsFuture Grinding Technologies Kickstarter Q3i Typo3 11 HeadlessPrecalciner is also called cement calciner Calciner in cement plant is mainly used for the predecomposition of cement clinker and forms the clinker calcining system in the new dry process cement plant together with preheater, cement Precalciner – Calciner In Cement Plant, Cement
.jpg)
Thomas Holzinger, Holzinger Consulting, grinding system
Thomas Holzinger, Holzinger Consulting, discusses cement grinding system optimisation Introduction The cement industry uses a wide range of different systems in raw material, coal, and cement grinding While new plants mainly focus on highly energy‑efficient systems, using roller comminution systems like vertical roller mills (VRMs) and high2020年8月25日 Cement grinding: The clinker is taken from the clinker silo and sent to the feed bin where it is mixed with gypsum and additives before entering the cement grinding plant In the cement grinding process, the clinker is Cement Production Process Cement Manufacturing AGICO Cement is a cement grinding plant manufacturer, we'd like to helps you learn more about cement grinding plant and cement grinding machines Skip to content +86 Cement Grinding Plant Overview Cement Grinding Unit AGICO CementFinally, during the cement grinding and distribution process, firstly the cooled clinker is ground with around 5% of gypsum and other 17 JRTE2020 cementitious materials to form the final cement Typical cement manufacturing process flow diagram [4]
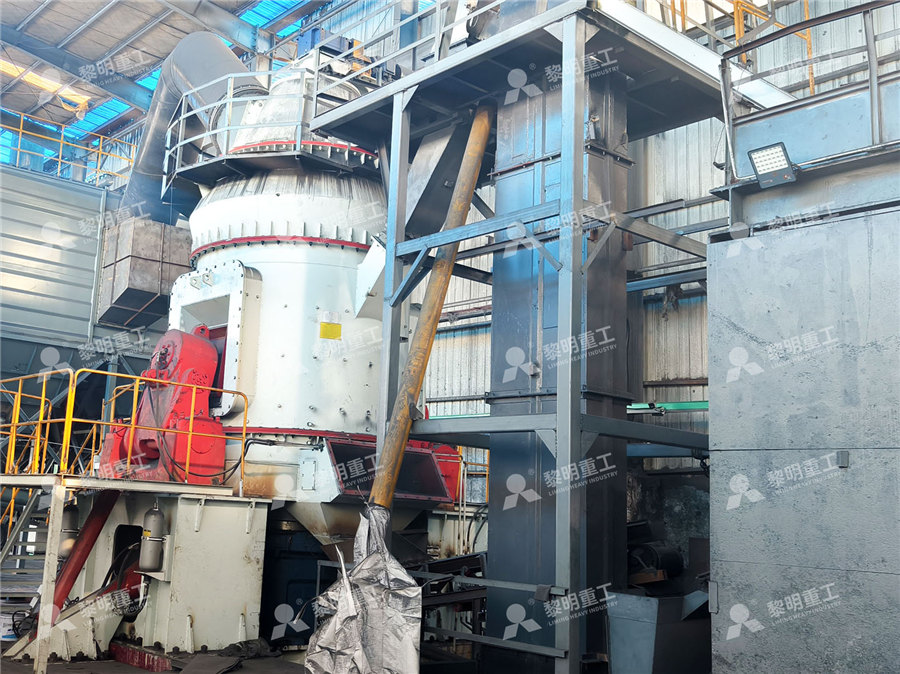
Cement Manufacturing Process INFINITY FOR CEMENT EQUIPMENT
Cement Manufacturing Process by TIZITA MOGES , SELAMU ABULE DEREJE ENDALAMAW IF YOU NEED THIS GUIDE AND ALL OTHER USEFUL EXCEL SHEETS WHICH WILL MAKE YOU MASTER THE PRODUCTION , PROCESS , MAINTENANCE ACTIVITY IN YOUR CEMENT PLANT KINDLY CLICK HERE Raw Material Preparation and 2015年7月21日 This article discusses the range of application of ultrafine grinding for processing mineral raw materials and presents examples of the successful use of this technology in the concentration of polymetallic ores and the hydrometallurgy of gold A description is given of the principle of operation of bead mills and their main technological parameters (the size of the Ultrafine Grinding in Contemporary Flow Diagrams for Mineral PENGFEI dry process cement plant avails of MLS3626 vertical grinding mill, designed to produce 2500 tons of cement clinker everyday Its φ4×60m rotary kiln combines preheating and decomposing system and fivestage cyclone preheater2500 Ton Dry Process Cement Plant PENGFEI Groupkiln feed preparation, pyroprocessing, and finished cement grinding Each of these process components is described briefly below The primary focus of this discussion is on pyroprocessing operations, which constitute the core of a portland cement plant The initial production step in portland cement manufacturing is raw materials acquisition116 Portland Cement Manufacturing US Environmental
.jpg)
Study on the production of cements using a multistage grinding
2 Schematic flow sheet of a multistage grinding plant for the production of Portlandcements including three different Cement grinding – as also shown in Prof DrIng Philipp M Fleiger 2, Faculty of Mechanical and Process Engineering, DrIng Stefan Seemann 1, Head of Mechanical Process Department 1 VDZ Technology gGmbH EVERYTHING YOU NEED TO KNOW ABOUT ESTABLISHING CEMENT GRINDING PLANT 1MTY the plant layout and flow process Plant Capacity The plant will have a capacity to produce 10 million tonnes of cement per EVERYTHING YOU NEED TO KNOW ABOUT Process Flowsheet Selection D Lunt, T Weeks, in Gold Ore Processing (Second Edition), 2016 92 Ultrafine Grinding Ultrafine grinding (UFG) has continued to evolve in terms of equipment development A number of specialist machines are commercially available including Xstrata's IsaMill ®, Metso's Vertimill ®, Outotec's High Intensity Grinding (HIG) ® mill, and the Ultrafine Grinding an overview ScienceDirect TopicsAGICO CEMENT helps you turn waste into worth with a slag grinding plant easily Capacity: 20170tph, FREE to contact! Skip to content +86 s about blog contact EN ES Menu Menu Home; Slag Grinding Plant GGBS Plant Slag Mill, Slag
.jpg)
Coal Grinding Cement Plant Optimization
Most commonly used mills for coal grinding in cement plants are closed circuit air swept (Single chamber) ball mills and vertical mills Ball Mill: Single chamber ball mills (with classifying liners and dam ring) with drying chamber and static or dynamic separator are commonly existing for coal grinding in cement plant for one or more kilns as per capacityCement Grinding: cement grinding is the final stage in Portland cement manufacturing In this step, clinker will be ground in grinding mill to reach the qualified fineness of cement product During the grinding, we usually add gypsum, fly ash and other raw materials into the cement to realize the different usage of cementPortland Cement Manufacturing Process In Cement Plant AGICOThe mill came into use in the 1890s, initially for regrinding rejects, both in dry rawmix and cement grinding Later, they came to be used for the entire grinding process Martin Earles first installed them for autonomous cement grinding in 1899, and in 1904, they were used exclusively at Norman for rawmillingCement Kilns: Size Reduction and Grinding2024年7月15日 With our ultrafine production technology we are proud to play our part in decarbonation to reduce carbon footprint of cement This is the first ultrafine grinding plant based on booster mill technology to be sold worldwide We look forward, together with the Eqiom/CRH team, to a successful projectEqiom Lumbres Cement Plant, a CRH Company thyssenkrupp
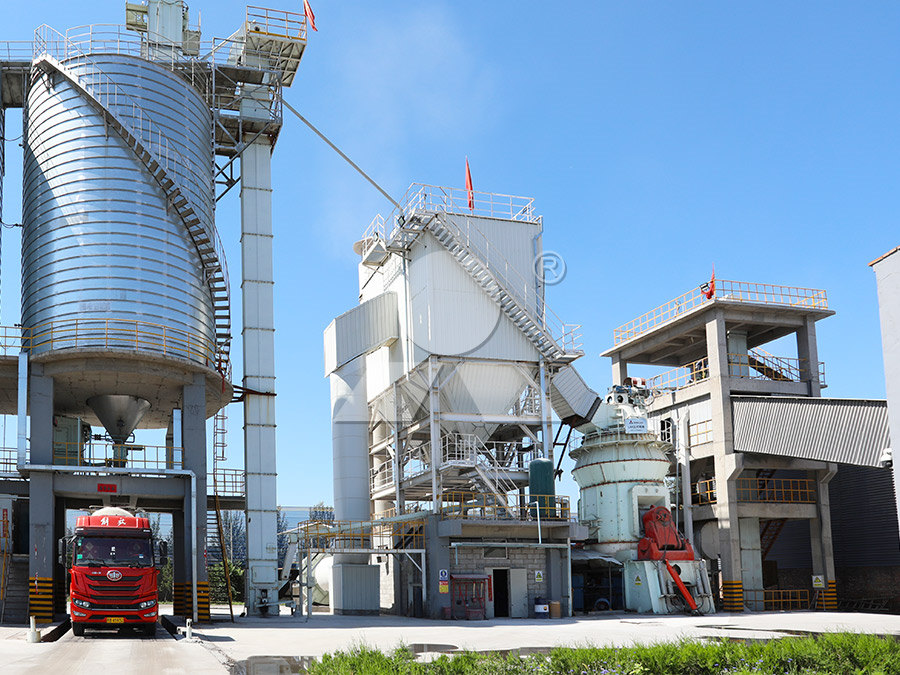
EnergyEfficient Technologies in Cement Grinding IntechOpen
2015年10月23日 In this chapter an introduction of widely applied energyefficient grinding technologies in cement grinding and description of the operating principles of the related equipments and comparisons over each other in terms of grinding efficiency, specific energy consumption, production capacity and cement quality are given A case study performed on a 2017年8月15日 To produce powdered cement, the nodules of clinker are ground to the consistency of powder Grinding of clinker, together with additions of approximately 5 percent gypsum to control the setting properties of the cement can be done in ball mills, ball mills in combination with roller presses, roller mills, or roller pressesThe Cement Manufacturing Process2021年3月9日 In this study the process flow diagram for the cement production was simulated using Aspen HYSYS 88 software to achieve high energy optimization and optimum cement flow rate by varying the flow rate of calcium oxide and silica in the clinker feed Central composite Design (CCD) of Response Surface Methodology was used to design the ten experiments for Simulation and Optimization of an Integrated Process Flow Sheet Years of cement production practice shows that cement particle gradation should be distributed continuously within a certain size range Generally speaking, the cement particles smaller than 32 μm are beneficial to reduce bleeding and Ball Mill In Cement Plant Cement Ball Mill AGICO
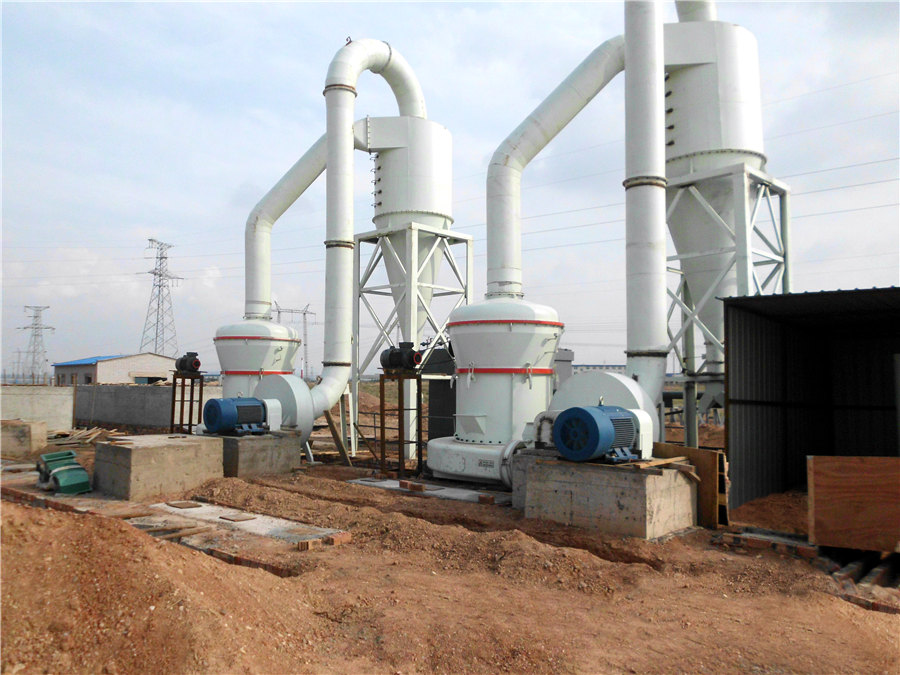
World Cement Grinding Milling QA
2022年2月18日 As well the consideration of production costs and carbon footprints, one key issue is energy consumption For reference, the grinding process represents a significant part of a cement plant’s electrical demand, in IsaMills have similar ultrafine grinding efficiencies to SMDs given in efficiently milling cement clinker, particularly for specialised fine cements [29, 35], but this must be a dry process to prevent premature cement hydration [36 pumping due to improved flow properties [24,25] Grinding, which is central in mineral processing to Ultrafine Grinding an overview ScienceDirect Topics2024年11月23日 Cement Extraction, Processing, Manufacturing: Raw materials employed in the manufacture of cement are extracted by quarrying in the case of hard rocks such as limestones, slates, and some shales, with the aid of blasting when necessary Some deposits are mined by underground methods Softer rocks such as chalk and clay can be dug directly by Cement Extraction, Processing, Manufacturing BritannicaIf you want to upgrade your current cement grinding plant to achieve the purpose of energysaving and profit increase, the most direct way is to carry out a technical transformation on traditional cement mills or replace a batch of new energysaving grinding equipment, such as the cement vertical mill grinding system, new type cement ball mill grinding system, cement roller press, Making Your Cement Grinding Plant Energy Saving Cement Grinding
.jpg)
The Cement Plant Operations Handbook International Cement
15 Cement plant construction and valuation 244 1 New plant construction – 2 Project management – 3 Cement plant investment costs – 4 Project phases – 5 Plant valuation Section B – Process calculations and miscellaneous data B1 Power 262 1 Specific power consumption 2 Power conservation – 3 Threephase power – 4Everything you need to know about clinker/cement Grinding if You read and understand this article , you will be ready to be a cement grinding area manager FEED AND FEED SYSTEM Feed Temperature Plants with satellite coolers have high clinker temperatures: eg Cumarebo, Oujda Exit satellite cooler 200250°C Exit grate cooler 100150°CEverything you need to know about clinker/cement Grinding2023年8月21日 ICR looks at the inner workings of grinding mills in the cement industry to understand the technological advancements that are reshaping the landscape against the foreground of sustainability Innovations to enhance the grinding processes are aimed at minimising their environmental footprint while increasing efficiency and performance In CuttingEdge Grinding Solutions Indian Cement ReviewProcess measured value Disturbance variable Setpoint value 4 – Continuous and Dynamic Process Optimisation • is an online application for closedloop control of a grinding plant This involves integrated process optimisation which is based on a dynamic process model This process model provides continuous realtime optimisation of the plantPROCESS OPTIMISATION FOR LOESCHE GRINDING PLANTS
.jpg)
Fine grinding: How mill type affects particle shape characteristics
2017年9月1日 With the continual depletion of high grade simple ore bodies, more complex, finely disseminated ore bodies are being processed, which has led to an increase in the prevalence of fine grinding (Sinnott et al, 2006)This has been evident in the platinum group element (PGE) industry in South Africa, where the Bushveld Complex hosts 70% of global