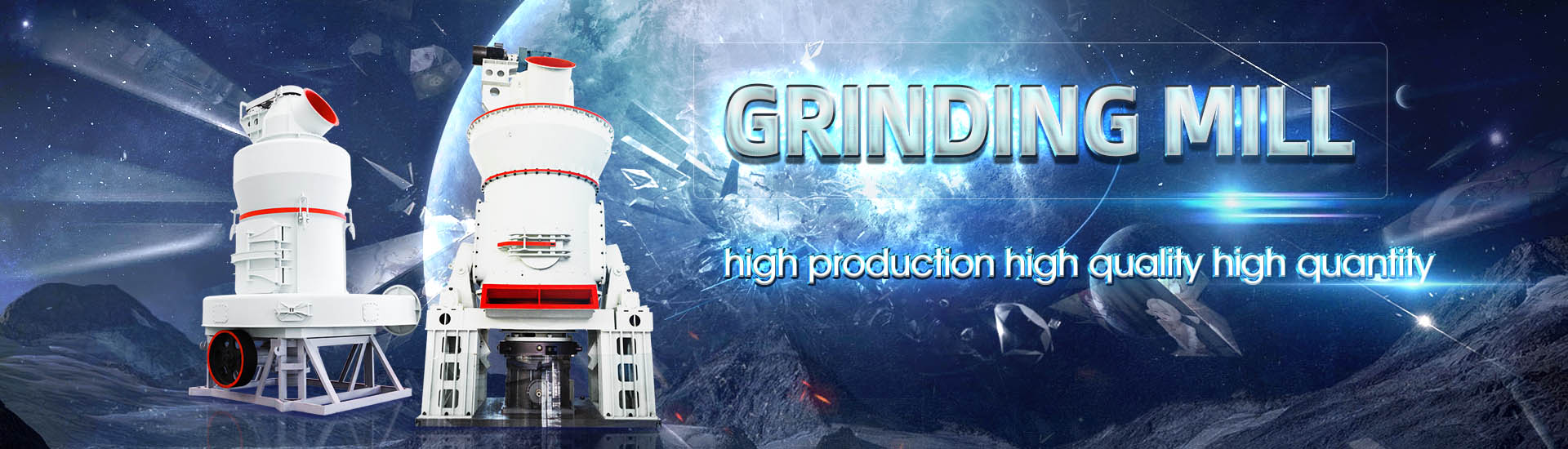
Steel slag treatment magnetic separation
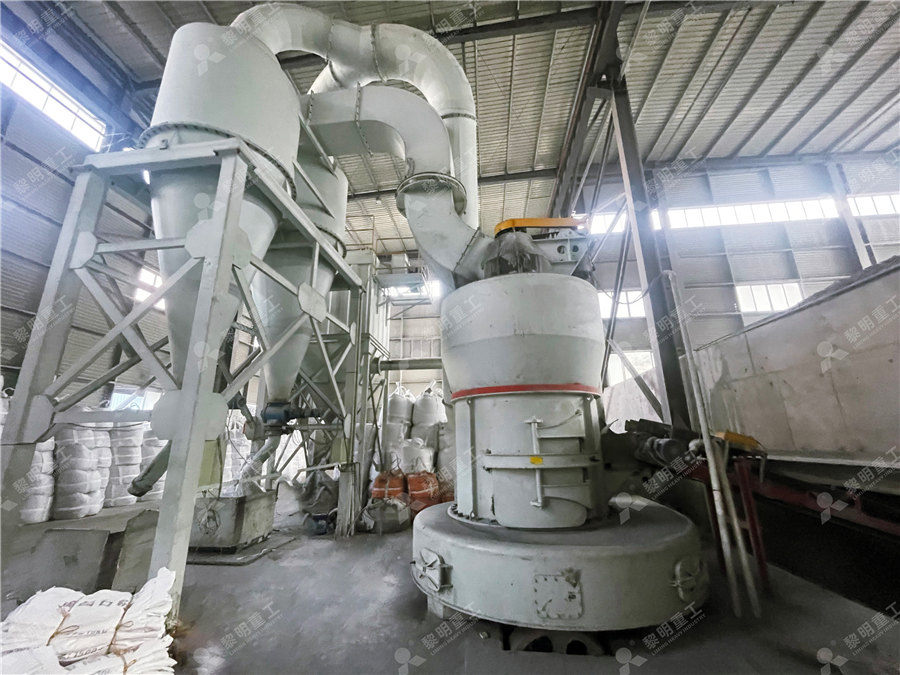
Steel slag in China: Treatment, recycling, and management
2018年8月1日 In China, after steelmaking, the steel slag is poured from the converter, transported to the slag stacking place, and treated by aging Then the steel slag is 2006年1月1日 The magnetic separation method is used for separating metallic iron and iron minerals from steel slag Commonly used magnetic machines are the crossbelt magnetic Application of magnetic separation to steelmaking slags for 2024年3月1日 In order to address the issue of magnetic agglomeration leading to poor magnetic separation efficiency and low activity enhancement, resulting in limited utilization of steel slag fine powder material, this study proposes a An airfluidized magnetic separator and its separation 2024年7月29日 Steel slag can separate inert minerals by the mineral separation method and prevent the hydration of active minerals caused by wet magnetic separationMagnetic separation characteristics of steel slag powder in a
.jpg)
(PDF) An airfluidized magnetic separator and its separation
2024年3月1日 In order to address the issue of magnetic agglomeration leading to poor magnetic separation efficiency and low activity enhancement, resulting in limited utilization of steel slag T he ways for magnetic separation of slag usually va ry with cooling methods of liquid steel slag and its chemical/mineralogical composition Mostly , steel slag magnetic separation process Optimization of magnetic separation process for iron Springer2023年2月1日 How to separate the elemental phosphorus has become a key issue In order to solve the problem of solid waste pollution of basic oxygen furnace (BOF) slag in the Efficient separation of iron elements from steel slag based on Since the calcium iron iron aluminum is magnetized to become a magnetic material, it can be separated and recovered from the steelmaking slag by magnetic separation Ironbased Magnetic separation method of steelmaking slag, and magnetic
.jpg)
Superconducting magnetic separation of ground steel slag
he steel slag contains valuable resources such as iron, copper, manganese, and magnesium Superconducting magnetic separation has been applied on recovery of the valuable resource 2024年7月29日 The mineral dry separation method is a technique for the comprehensive utilization of steel slag In this process, two products, ie, steel slag powder with high activity (reaches 75% of the cementitious activity of pure cement) and inert mineral material, are obtained by crushing and separating steel slag 12,13 If wet magnetic separation is adopted, the active Magnetic separation characteristics of steel slag powder in a DOI: 101016/jjmrt202301186 Corpus ID: ; Efficient separation of iron elements from steel slag based on magnetic separation process @article{Liu2023EfficientSO, title={Efficient separation of iron elements from steel slag based on magnetic separation process}, author={Xin Liu and Dazhi Wang and Zhiwei Li and Wei Ouyang and Yanping Bao and Chao Gu}, Efficient separation of iron elements from steel slag based on magnetic 2008年3月21日 Present study indicates that steel slag may be an effective adsorbent for phosphate removal from secondary effluents as well as solution after magnetic separation The steel slag showed good performance for phosphorus removal The maximum adsorption capacity of steel slag was 53 mg P/gPhosphate removal from solution using steel slag through magnetic
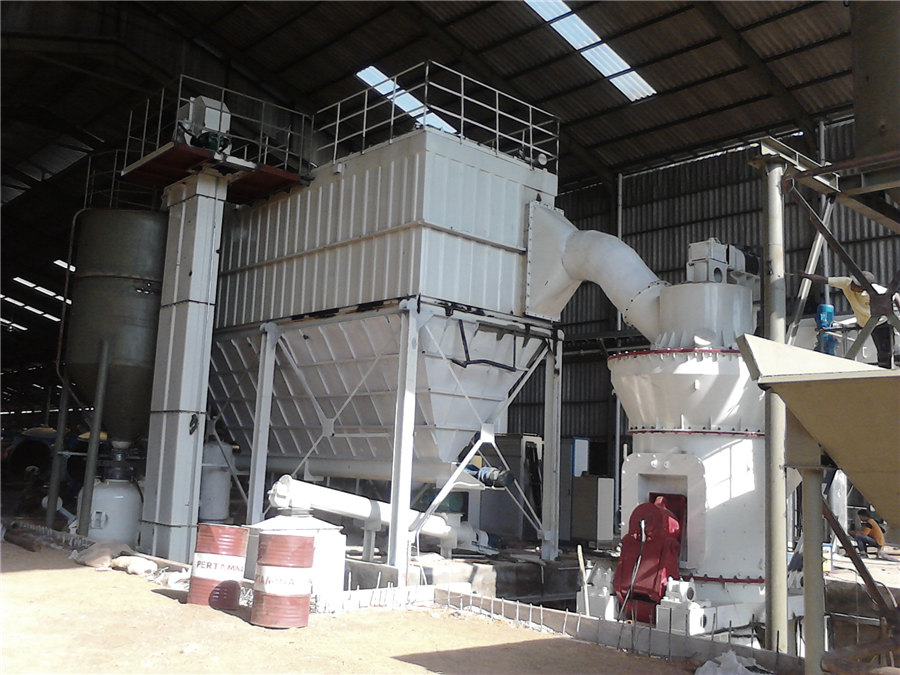
Processing and Reusing Technologies for Steelmaking Slag
The iron/steel slag processing flow is schematically shown in Fig 2 Steelmaking slag is subjected to the following four processes: ① solidify and cooling of the hot molten slag, ② crushing and magnetic separation treatment of the slag to recover the metal iron, ③ crushing and classification of the slag for grain size adjustment2022年4月11日 In order to solve the problem of solid waste pollution of basic oxygen furnace (BOF) slag in the metallurgical process, this paper took BOF slag as the research object, and carried out oxidation reconstruction of BOF slag and alcohol wet magnetic separation recovery of iron phase, so as to efficiently recover and utilize BOF slag In the early stages, the research Optimization of Iron Recovery from BOF Slag by Oxidation and Magnetic 2023年8月22日 It is found that the removal rate of hardtogrind minerals in steel slag is the highest when steel slag enters magnetic separation particle size of 1 mm and magnetic field strength of 1400 Gs Compared with untreated steel slag, the grinding efficiency of treated steel slag can be increased by 22%, and the hydration activity is not affectedThe Effect of Removing HardtoGrind Minerals from Steel Slag Steel slag is a byproduct generated during the steelmaking process As the largest steel producer in the world, China produces over 100 million tons of steel slag annually, accounting for approximately 15–20% of crude steel production (Rui et al 2022, Shi et al 2022)After steelmaking, the slag is placed in a slag heap and subjected to magnetic separation to recover Activation technology of steel slag for concrete exposed to

Recent research progress on recycling metallurgical waste slag
2024年11月1日 Magnetic separation method: By using steel slag’s varying magnetic characteristics to effectively separate the phosphorusrich phase: About 67 % of phosphorus is removed, and the operation is relatively simple: The phosphorus recovery rate is low and the volatilization rate is high [73], [74], [75] Wet acid leaching methodAvailable online at sciencedirect Journal of Hazardous Materials 152 (2008) 211–215 Phosphate removal from solution using steel slag through magnetic separation Jibing Xiong a , Zhenli He a,b , Qaisar Mahmood a , Dan Liu c , Xiaoe Yang a,∗ , Ejazul Islam a a MOE Key Laboratory of Environmental Remediation and Ecological Health, College of Natural Phosphate removal from solution using steel slag through magnetic PreReduction and Melting/Magnetic Separation Treatment Shaoyan Hu 1, Deyong Wang 1, especially for stainless steel Chromium slag is the waste re sidue generated by the indust rial process of Enrichment Characteristics of Cr in Chromium Slag after Pre 2017年2月1日 To improve the efficiency of iron recovery from steel slag and reduce the wearandtear on facilities, a new method was proposed by adding a secondary screen sizer to the magnetic separation process according to grain size distribution of Optimization of magnetic separation process for iron recovery
.jpg)
Steel slag in China: Treatment, recycling, and management
2018年8月1日 In this paper, we reviewed steel slag treatment, recycling, To improve the reactivity of BOF slag, the steel slag is ground to an ultrafine powder after the magnetic separation process2021年12月29日 Characterization of a ChromiumBearing Carbon Steel Electric Arc Furnace Slag after Magnetic Separation to Determine the The thermal treatment of steel slag up to 900 °C indicated that this Characterization of a ChromiumBearing Carbon Steel 2024年3月1日 Primary magnetic separation tests on a steel slag fine powder material demonstrate that the air fluidized dry magnetic separator effectively separates inert minerals from active minerals in the (PDF) An airfluidized magnetic separator and its separation Available online at sciencedirect Journal of Hazardous Materials 152 (2008) 211–215 Phosphate removal from solution using steel slag through magnetic separation Jibing Xiong a , Zhenli He a,b , Qaisar Mahmood a , Dan Liu c , Xiaoe Yang a,∗ , Ejazul Islam a a MOE Key Laboratory of Environmental Remediation and Ecological Health Phosphate removal from solution using steel slag through magnetic
.jpg)
BOF Steel Slag: Critical Assessment and Integrated Approach for
2021年9月24日 During steel production, the impurities in the hot metal react with the fluxes forming the steel slag Chemical constituents of this steel slag (SS) are relevant to iron/steelmaking or blended cement manufacture Harmful impurities present in it, however, limit its recycling to these applications Japan, Europe, and the US consume a significant amount of 2023年5月15日 Steel slag treatment process and comprehensive utilization analysis Energy Metallurg Indus (2020) P Kumar et al Pilotscale steam aging of steel slags 2023) Currently, there are several recycling methods for steel slag: magnetic separation, cement production, road engineering and railway track applications, and soil Comprehensive utilization of steel slag: A review ScienceDirect2023年11月7日 Magnetic separation has wideranging applications in both mineral processing and recycling industries Nevertheless, its conventional utilization often overlooks the interplay between mineral and particle characteristics and their impact on operational conditions, ultimately influencing the efficacy of the separation process This work describes a methodology able to Characterization of Magnetic and Mineralogical Properties of Slag Current study showed that an appropriate grinding of slag and magnetic separation lead to the recovery of metal resources from steel slag waste rather than dumping all of the volume Keywords: Highgradient magnetic separation, recovery, steel slag, environmental application, superconducting magnet * Corresponding author: erconducting magnetic separation of ground steel slag
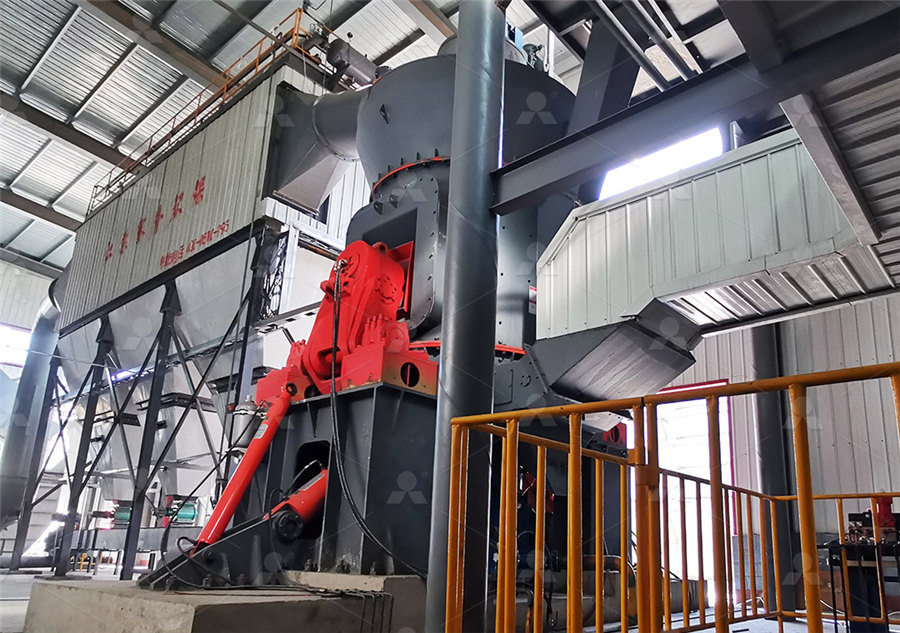
Separation and extraction of iron resources from hazardous
2024年10月1日 Magnetic separation is the main way of steel slag treatment at present The various mineral phases of steel slag exhibit different morphologies in terms of greyness and morphology, and their magnetic magnitude varies considerably (Zhao et al, 2017)2008年4月1日 Steel slag with magnetic separation was used to remove phosphate from aqueous solutions The influence of adsorbent dose, pH, and temperature on phosphate removal was investigated in a series of Phosphate Removal from Solution Using Steel Slag through Magnetic 2024年11月12日 The effectiveness of thermal treatment and magnetic separation as an upgrading Larger metallic particles promote liberation of ferronickel from slag during Huang XZ (2022) Upgrade of nickel and iron from lowgrade nickel laterite by improving direct reductionmagnetic separation process J Iron Steel Res Int 29: A Review of Direct Reduction–Magnetic Separation Process for 2021年12月29日 This study investigates the potential to recover iron and chromium from a chromiumbearing carbon steel Electric Arc Furnace (EAF) slag This slag contains indeed about 30 wt% Fe and 25 wt% Cr However, the Characterization of a ChromiumBearing Carbon
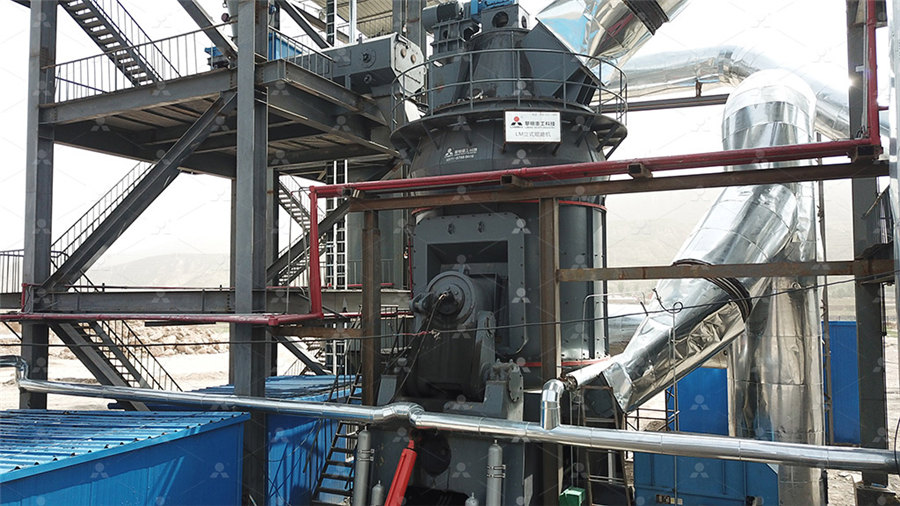
Recovery of high grade iron compounds from LD slag by enhanced magnetic
2014年1月10日 High gradient magnetic separation was used to separate the Pbearing dicalcium silicate from the iron and manganesebearing minerals Wang et al (2012) have reported that, the cooling manner is important for slag treatment According to them, the higher recovery yield of the iron from steel slag is obtained on the slag slowly cooledDOI: 101016/S1006706X(17)300237 Corpus ID: ; Optimization of magnetic separation process for iron recovery from steel slag @article{Lan2017OptimizationOM, title={Optimization of magnetic separation process for iron recovery from steel slag}, author={Yuanpei Lan and Qingcai Liu and Fei Meng and Deliang Niu and Heng Zhao}, Optimization of magnetic separation process for iron recovery processing characteristic Steel slag, selected from a factory, was crushed, ground sieved and into different particle size ranges for the singlefactor magnetic separation experiments It was determined that the optimum value ranges for the particle size, magnetic separation distance and rotating frequency were 015 mm03 mm, 10 mmDRY MAGNETIC SEPARATION TECHNOLOGY FOR THE 2012年1月1日 Benxi Iron and Steel Company produces 78,000 tons of slag steel and 89,000 tons of iron concentrate with the advanced slag hot disintegrating treatment technique and crusingscreeingbar mill purificationmagnetic separation combined process [10]An Overview of Utilization of Steel Slag ScienceDirect
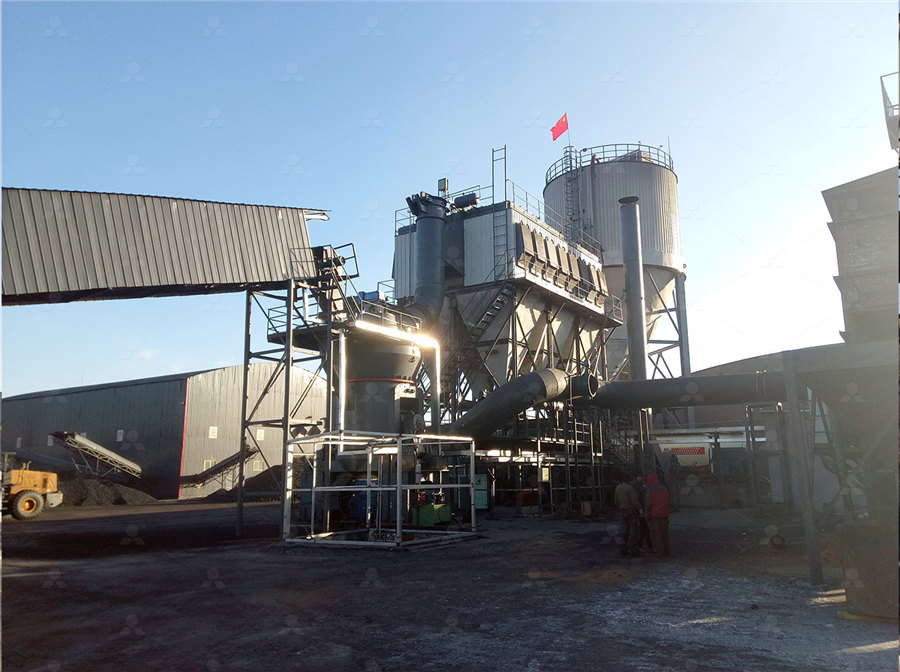
UpConcentration of Chromium in Stainless Steel Slag and
After gravity separation of the HC FeCr slag, a fraction with a Cr content close to high grade Cr ores ( 50% Cr2O3) can be obtained This fraction represents 12 wt% of the HC FeCr slag, and can probably be used directly in traditional smelting processes Keywords: stainless steel slag; ferrochromium slag; magnetic separation; gravity separation 12019年11月1日 Request PDF Characterization of the products obtained by pyrolysis of oil sludge with steel slag in a continuous pyrolysismagnetic separation reactor In this study, a strategy of combining Characterization of the products obtained by pyrolysis of oil 2021年8月30日 Characterization of Sustainable Asphalt Mixtures Containing High Reclaimed Asphalt and Steel Slag Previous Article in Journal Assessment of Microstructure and Release of Fluoride Ions from "Enrichment Characteristics of Cr in Chromium Slag after PreReduction and Melting/Magnetic Separation Treatment" Materials 14, no 17: 4937 Enrichment Characteristics of Cr in Chromium Slag after PreSeparation and extraction of iron resources from hazardous electric arc furnace (EAF) steel slag: Aggregation of Ferich layers, magnetic separation, powder characterization Process Safety and Environmental Protection ( IF 69) Pub Date : , DOI: 101016/jpsep202408064Separation and extraction of iron resources from hazardous
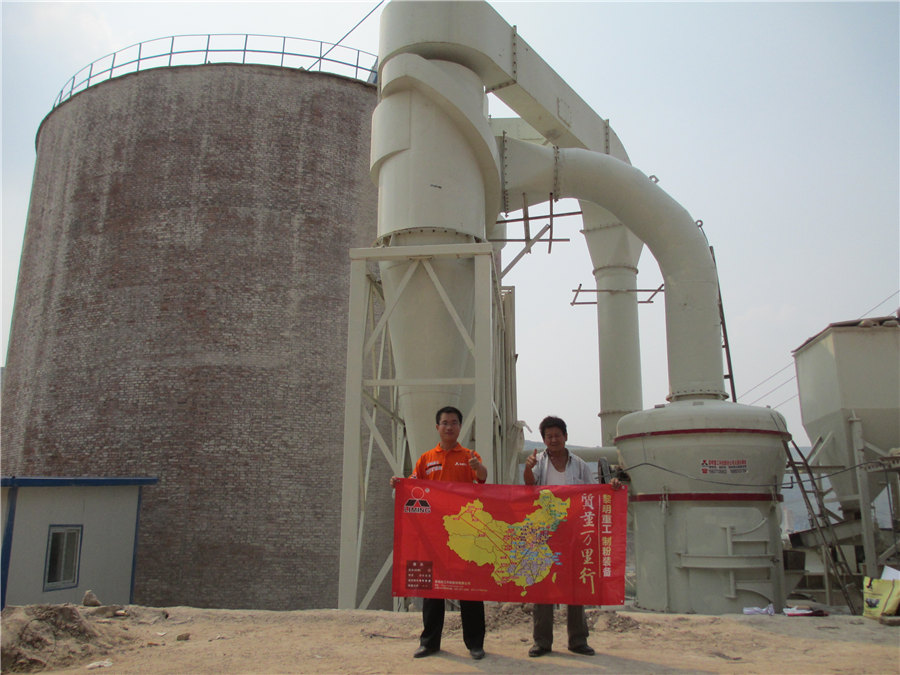
Application of magnetic separation to steelmaking slags for
2006年1月1日 The magnetic separation method is used for separating metallic iron and iron minerals from steel slag Commonly used magnetic machines are the crossbelt magnetic separator, Use of steel converter slag as nickel adsorber to wastewater treatment Waste Management, 21 (2000), pp 631635 Google ScholarIn the magnetic separation process, the fineness and processing of the slag significantly affect separation efficiency (He et al 2022, Zhang et al 2019a)XRD patterns of LD slag treated by magnetic separationTo provide a magnetic separation method of steelmaking slag capable of heightening Fe concentration in recovery, in a magnetic separation method for recovering a ferrous compound and metallic iron by magnetic separation from slurry steelmaking slagSOLUTION: A magnetic separation method of steelmaking slag includes steps of: bringing slurry containing crushed or Magnetic separation method of steelmaking slag, and magnetic 2020年10月12日 Slags coming from stainless steel (SS) and ferrochromium (FeCr) production generally contain between 1 and 10% Cr, mostly present in entrapped metallic particles (Fe–Cr alloys) and in spinel structures To recover Cr from these slags, magnetic and gravity separation techniques were tested for upconcentrating Cr in a fraction for further processing In case of UpConcentration of Chromium in Stainless Steel Slag and MDPI
.jpg)
Sustainable Utilization of Steel Slag from Traditional Industry and
2020年9月24日 Steel slag separated by magnetic separation contained a large amount of iron and magnetic iron Magnetic steel slag particles were used as particle electrodes to promote the degradation of organic Wang, M Steel slag in China: Treatment, recycling, and management Waste Manag 2018, 78, 318–330 [Google Scholar] 2020年10月12日 After gravity separation of the HC FeCr slag, a fraction with a Cr content close to high grade Cr ores ( 50% Cr2O3) can be obtained This fraction represents 12 wt% of the HC FeCr slag, and can probably be used directly in traditional smelting processes Keywords: stainless steel slag; ferrochromium slag; magnetic separation; gravity separation 1UpConcentration of Chromium in Stainless Steel Slag and magnetic separation It can be seen in Table 2 that the finegrained steel slag has higher iron content and the ignificance of recovery is obviouss The composition of the steel slag in terms of the ain m iron minerals’ and its theoretical grade were determined using the X DRY MAGNETIC SEPARATION TECHNOLOGY FOR THE 2020年1月27日 The modular structural design allows finegrained minerals with different magnetic susceptibility to be separated in one pass, according to their different processing characteristic Steel slag, selected from a factory, was crushed, ground and sieved into different particle size ranges for the singlefactor magnetic separation experimentsDry magnetic separation technology for the recovery of iron
.jpg)
Application of Magnetic Separation to Steelmaking Slags for
In 2006, 1015 million metric tons of steel slag were generated in the US Out of the total steel slag produced in the US every year, about 5070% is used as aggregate for road and pavement