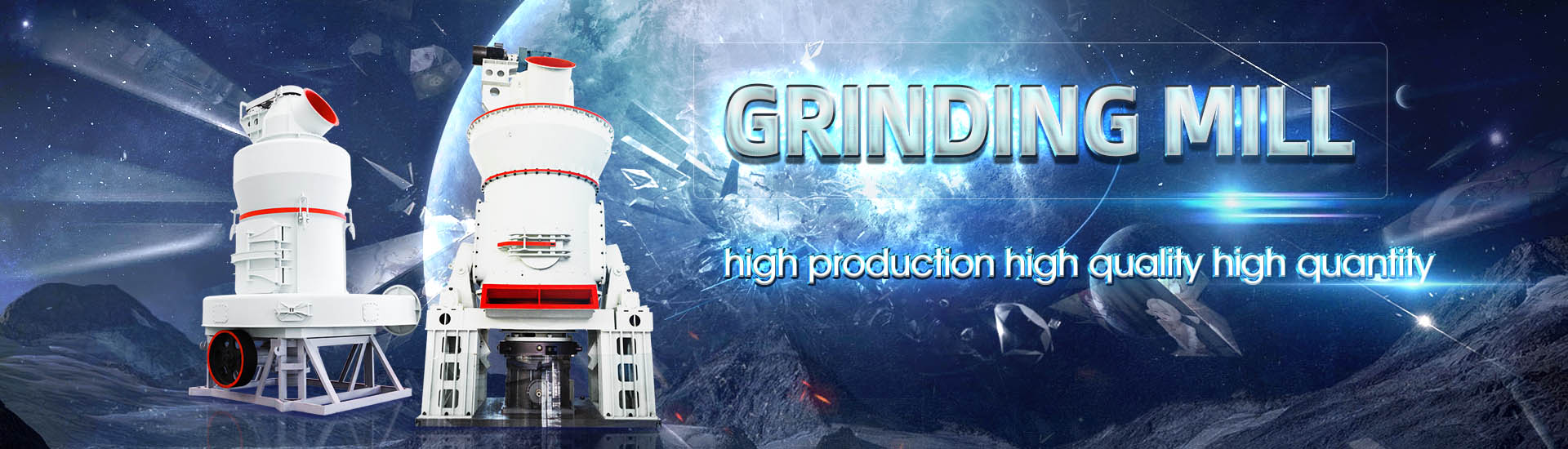
Large alkaline furnace lining material powder making process equipment
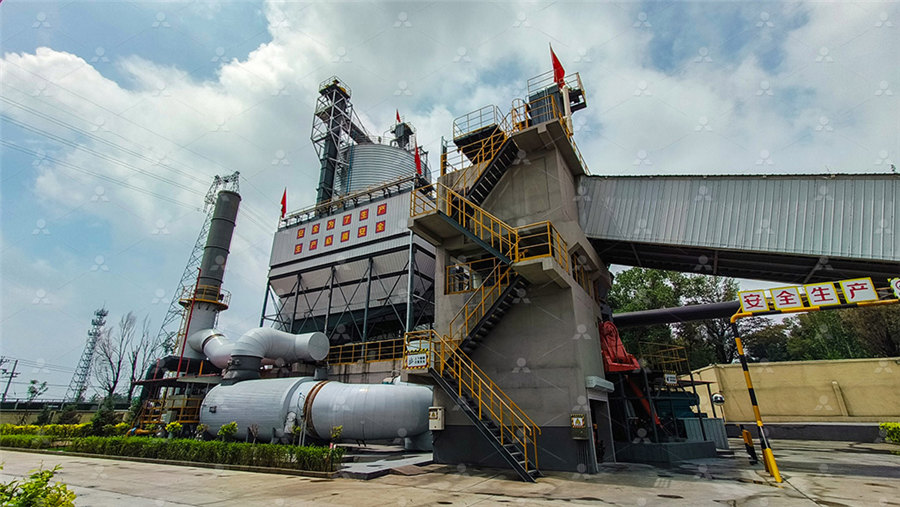
Powder Processing Furnaces Thermal Systems From 500 to
Harper is trusted worldwide for high temperature powder processing furnaces for powders and granular materials, including inorganic chemicals, catalysts, phosphors and powdered metalsCapital Refractories offer a full range of coreless induction furnace linings, topping and patching products for a wide range of steels and high temperature alloys A range of air setting, chemically bonded high strength materials and dry Coreless Induction Furnace Linings Capital 2024年11月24日 Our rotary drum furnace is the perfect choice for all processes with high heat up gradients and high throughput ONEJOON's patented sealing system stands for the best atmosphere purity and control The tube furnace is Heat treatment of powder ONEJOON Kilns2017年6月3日 Hightemperature metallic materials or alloys used in process heating equipment (furnaces, heaters, ovens, kilns, etc) have significant effect on thermal efficiency, productivity Materials Selection Considerations for Thermal Process
.jpg)
Design, fabrication and properties of lightweight wear lining
2022年3月1日 The design of lightweight wear linings is crucial in terms of the energy and resource efficiency of industrial furnaces and quality of final products This review aims to Versatile Material Processing: Rotary furnaces can handle a wide range of materials, including battery scraps, blast furnace waste, lead ores, lead dross, and baghouse powder Higher Lead Recovery: Compared to blast or fixed Rotary Furnaces: Advanced Materials Processing 2017年3月14日 However, identifying the need for new furnace lining and installing the right material is not easy To do it right, here are five primary tips for maximum furnace lining efficiency: 1Ensuring Furnace Lining Efficiency Foundry 2020年2月15日 Lining iron and steel furnaces is critical to extend the life of the furnaces and to protect the purity of the metals being heat treated Therefore, choosing the best material to meet these needs is criticalThe Future of Kiln Lining Thermal Processing
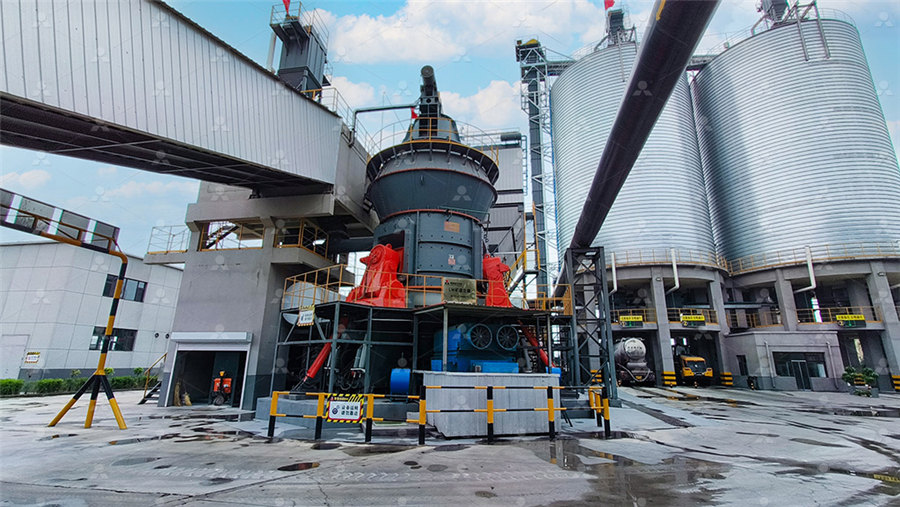
Five Tips for Achieving Furnace Lining Efficiency
2023年12月4日 Five Tips for Achieving Furnace Lining Efficiency By Steve Chernack, Morgan Advanced Materials An efficient furnace lining is key to reducing overall maintenance costs 2024年6月22日 Lightweight aggregates are the key materials to produce lightweight refractories for the working lining of hightemperature furnaces, which play an important role in the State of the art of lightweight aggregates used in lightweight 2017年5月30日 If you install a brick lining without adequate expansion joints, the brick can grow so large that it pushes up the entire lining off the furnace wall This will lead to further inefficiency, requiring the entire process to be repeated 4 Ensuring Effective Furnace Lining Efficiency2022年11月29日 5 New process and new materials of furnace lining materials ① In the traditional lining materials, ultrafine powder (mostly in a few microns) can improve the corrosion resistance and thermal shock stability of lining What are the types of lining materials for
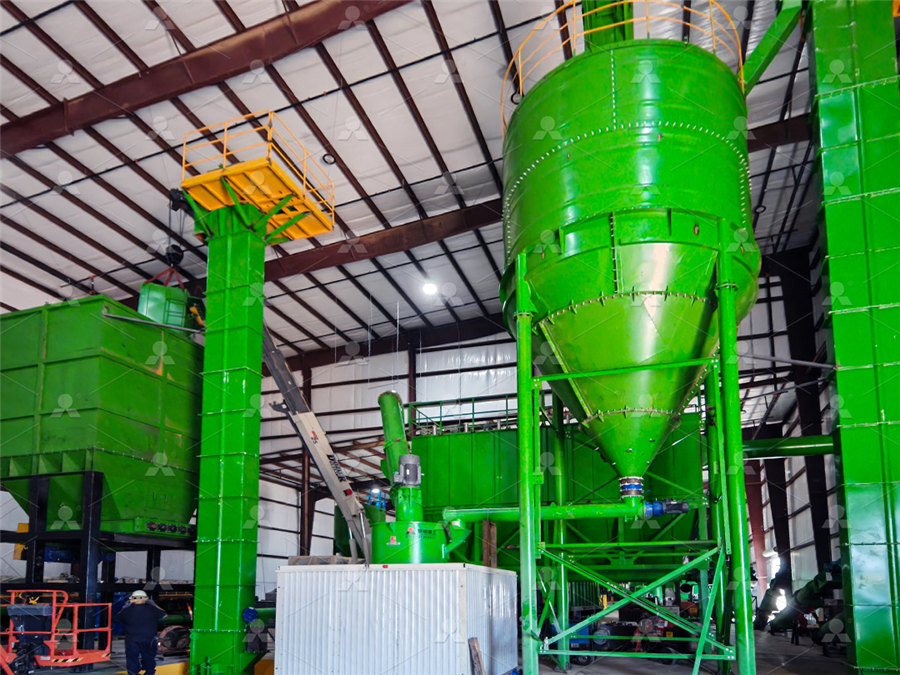
Refractory Materials for 30 tons Copper Melting Furnace — Lining
2024年8月19日 Medium frequency centerless induction copper melting furnace — 30 tons copper melting furnace Due to the substantial increase in the size of the furnace, new requirements have been put forward The most commonly used lining material for induction furnace is acidic lining It normally consists of high purity silica ramming mass that the rise of the temperature of 100 deg C/hour is achieved for furnaces up to 6 tons capacity and 50 deg C/hour for big furnaces with thick lining This rise in temperature is monitored up to about 800 Induction Furnace Refractory Lining with Silica Ramming Mass2010年5月1日 A furnace is one of the most important pieces of equipment in a process plant Furnace firing provides a large part of the heat for the process The heat for the process comes from the combustion FURNACE SELECTION, SIZING AND TROUBLESHOOTING, Kolmetz Handbook 2024年1月1日 Induction furnace melting is a process of melting metal by using electromagnetic induction to produce eddy current heating in metal materials in induction furnace, also called induction melting It has low melting point and poor stability, usually in melting and holding of nonferrous metals and cast iron Alkaline furnace lining is made of Induction Furnace Melting SpringerLink
.jpg)
Design, fabrication and properties of lightweight wear lining
2022年3月1日 The design of lightweight wear linings is crucial in terms of the energy and resource efficiency of industrial furnaces and quality of final products This review aims to present a systematic overview of the design, fabrication, properties, and application of lightweight wear lining refractories2020年10月19日 According to the raw materials and smelting furnace need different acid and alkaline divided into lining, our factory is using acidic lining Play lining, is to use the material such as quartz sand, the furnace wall do a layer isolation smelting furnace materials and within the induction coils, protect the induction coilsHow to improve the induction furnace lining lifeGeneral purpose lining with a wide melting temperature range Ceramic: 1700* 1730† Coral HB: Tough general purpose lining Ceramic: 1680* 1720† Coral SMC: Incorporates complex chromes for improved slag resistance Ceramic: 1700* 1750† Coral 85: High performance lining designed for large furnaces operating at high temperatures Ceramic Coreless Induction Furnace Linings Capital Refractories2014年10月1日 Alkalis (K and Na compounds, Kobayashi et al, 1979) enter in the blast furnace with the charge materials (should be limited to 2530 kg alkalis/ton pig iron, Kurunov et al, 2009 or 2585 kg (PDF) Alkaline carbonates in blast furnace process
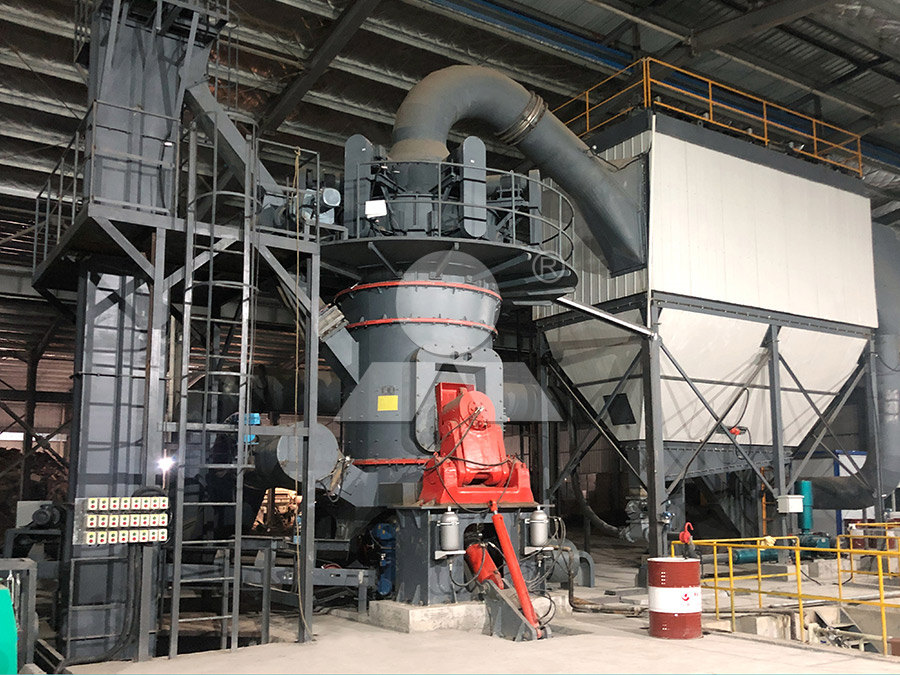
Induction Furnace Lining Systems Foundry
2019年8月16日 Gradmatic Equipment Inc is a world leader in providing a complete induction melting furnace lining solution when using dry vibratable refractory Gradmatic Equipment’s Refractory Installation and Vibration Induction furnace melting is a process of melting metal by using electromagnetic induction to produce eddy current heating in metal materials in induction furnace, also called induction melting It has low melting point and poor stability, usually in melting and holding of nonferrous metals and cast iron Alkaline furnace lining is made of Induction Furnace Melting SpringerLink2017年6月3日 Process Equipment Introduction Hightemperature metallic materials or alloys used in process heating equipment (furnaces, heaters, ovens, kilns, etc) have significant effect on thermal efficiency, productivity and operating cost of the equipment These materials are used inMaterials Selection Considerations for Thermal Process 2024年1月26日 in induction furnace lining that are monolithic This dry powder must be compacted with homogenous density Because lining material’s lifetime, depends on this fact Refractory ramming process has been done by pneumatic vibrators operated manually so far Doing this process by hand cannot guarantee homogenous ramming which willInduction Furnace Lining and Industrial Vibrator Design
.jpg)
Powder Metallurgy: A Comprehensive Guide for Beginners
2023年9月5日 The production of highperformance materials such as rare earth permanent magnets, rare earth hydrogen storage materials, rare earth luminescent materials, rare earth catalysts, hightemperature superconductors, and new metal materials like AlLi alloy, heatresistant Al alloy, superalloy, powder corrosionresistant stainless steel, powder high Powder processing technology conditions these primary materials to create a vast range of products, from chemicals and foods to pharmaceuticals and ceramics Which powder technology do you need? Select your production processPowder Manufacturing Equipment Making2020年2月15日 Lining iron and steel furnaces is critical to extend the life of the furnaces and to protect the purity of the metals being heat treated because RCF has strong characteristics that make it ideal for use in chemical processing, iron and steel processing, and ceramics factories Superwool® XTRA showed 50 percent less shrinkage compared The Future of Kiln Lining Thermal Processing MagazineA refractory lining is a safety protective layer in industrial furnaces, pipes, or equipment that provides hightemperature resistance and protects the structure from thermal shock, wear and erosion The refractory lining protects the pipe or equipment material from direct exposure to heat from fire or fluidsWhat is a Refractory Lining? Materials, Selection, and Types
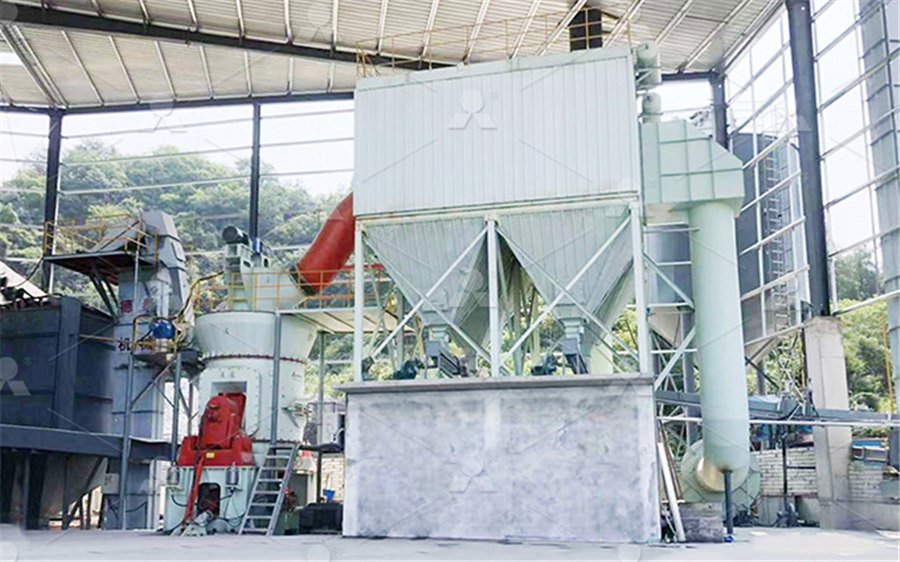
Metal powder manufacturing equipment Making
Complete metal powder manufacturing with sintering Metal powder blends are delivered for fabrication in the form of briquettes Blend the alloys and materials in a mixer to ensure a uniform particle distribution Then compact the mixture at a temperature lower than the melting point of the metals A widespread technique is sintering2021年7月9日 Talc is finally applied in powder form, therefore, fine grinding and ultrafine grinding are one of the necessary processing techniques for talc Talc has a Mohs hardness of 1, which is naturally crushable and has good grindability At present, the processing of ultrafine talc powder mainly adopts a dry processThe processing and application of talc ALPA Powder EquipmentVersatile Material Processing: Rotary furnaces can handle a wide range of materials, including battery scraps, blast furnace waste, lead ores, lead dross, and baghouse powder Higher Lead Recovery: Compared to blast or fixed Rotary Furnaces: Advanced Materials Processing 2023年2月15日 PE jaw crusher is an ideal primary crushing equipment, which can reduce the various rocks into the desired size Heavyduty hammer crusher: With high productivity and a large crushing ratio (usually 1025, sometimes Lime Production Process and Required
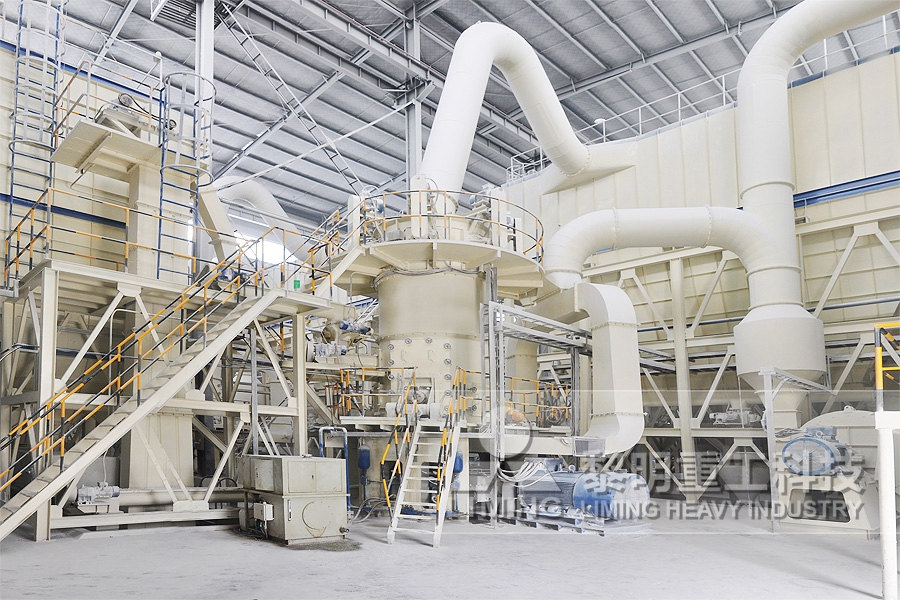
Face powder making equipment Making
Queen Elizabeth I knows this well Just think she used so many cosmetics and makeup containing toxic materials, especially leadbased face powder, that she even died from them Today fortunately, you no longer need lead to make face 2023年7月5日 Coreless induction furnace is one of the most widely used equipment in the steelmaking sector, while the lining refractory are the key factors in determining the lifetime of the induction furnace The multiphysics field dominates the operating conditions of the lining refractory which can be wellstudied using numerical simulation techniques Based on the Effects of induction furnace conditions on lining refractory 2013年12月1日 For the production of suitable sized feed materials (40+15mm) for Blast Furnace, during comminution process (crushing, grinding and screening) of the Run of Mines (ROM) generates a lot of fines Technological Changes in Blast Furnace Iron Making in India Alkaline Lining Materials includes mainly metallurgical magnesia with more than 92% magnesium oxide and fused magnesia,suitable for melting low silicon alloy steel and alkaline steel。 The intermediate frequency furnace magnesium material has the advantages of high refractoriness, good resistance to alkaline slag and stability against physical and chemical effects, but its Lining Material (Refractories Material) Huaxin Electric
.jpg)
Understanding Steel Making Operations in Basic Oxygen Furnace
2015年3月2日 The term ‘basic’ refers to the refractory linings of the furnace which are made of alkaline materials (dolomite and magnesite) Refractory linings must have specific properties to withstand high temperatures, the corrosive action of the highly oxidized and basic slags, and abrasion during charging and blowingpact and alkali content in a selected blast furnace ALKALINE CARBONATES IN THE BLAST FURNACE PROCESS Alkalis enter blast furnaces in all parts of the blast furnace charge, but mainly in manganese ore and in metallurgical waste materials A large part of alkalis is brought by coke In operating conditions, the amountALKALINE CARBONATES IN BLAST FURNACE PROCESS2023年1月6日 Where T n is the thickness of the nth layer, V p is the Pwave speed, α is the thermal correction factor, β is the shape correction factor, and f is the frequency of the reflection Up until recently, this is the extent to which AUE signals were collected are processed However, recent advancements in data collection, data processing, and information visualization have Imaging the Remaining Refractory Lining in Operating FurnacesReturn Conveyor System and Automation The calcination process of Cathode Active Material (CAM) is carried out in powdery form The material mixture of NCM or NCA precurser and lithium powder source (hydroxide or carbonate) will be normally filled into a prismatic ceramic saggar which finally is the transportation vehicle of the powder through the kilnFurnaces and process equipment for Cathode Active Material ONEJOON
.jpg)
Ensuring Effective Furnace Lining Efficiency
2017年5月30日 If you install a brick lining without adequate expansion joints, the brick can grow so large that it pushes up the entire lining off the furnace wall This will lead to further inefficiency, requiring the entire process to be repeated 4 2022年11月29日 5 New process and new materials of furnace lining materials ① In the traditional lining materials, ultrafine powder (mostly in a few microns) can improve the corrosion resistance and thermal shock stability of lining What are the types of lining materials for 2024年8月19日 Medium frequency centerless induction copper melting furnace — 30 tons copper melting furnace Due to the substantial increase in the size of the furnace, new requirements have been put forward Refractory Materials for 30 tons Copper Melting Furnace — Lining The most commonly used lining material for induction furnace is acidic lining It normally consists of high purity silica ramming mass that the rise of the temperature of 100 deg C/hour is achieved for furnaces up to 6 tons capacity and 50 deg C/hour for big furnaces with thick lining This rise in temperature is monitored up to about 800 Induction Furnace Refractory Lining with Silica Ramming Mass
.jpg)
FURNACE SELECTION, SIZING AND TROUBLESHOOTING, Kolmetz Handbook
2010年5月1日 A furnace is one of the most important pieces of equipment in a process plant Furnace firing provides a large part of the heat for the process The heat for the process comes from the combustion 2024年1月1日 Induction furnace melting is a process of melting metal by using electromagnetic induction to produce eddy current heating in metal materials in induction furnace, also called induction melting It has low melting point and poor stability, usually in melting and holding of nonferrous metals and cast iron Alkaline furnace lining is made of Induction Furnace Melting SpringerLink2022年3月1日 The design of lightweight wear linings is crucial in terms of the energy and resource efficiency of industrial furnaces and quality of final products This review aims to present a systematic overview of the design, fabrication, properties, and application of lightweight wear lining refractoriesDesign, fabrication and properties of lightweight wear lining 2020年10月19日 According to the raw materials and smelting furnace need different acid and alkaline divided into lining, our factory is using acidic lining Play lining, is to use the material such as quartz sand, the furnace wall do a layer isolation smelting furnace materials and within the induction coils, protect the induction coilsHow to improve the induction furnace lining life
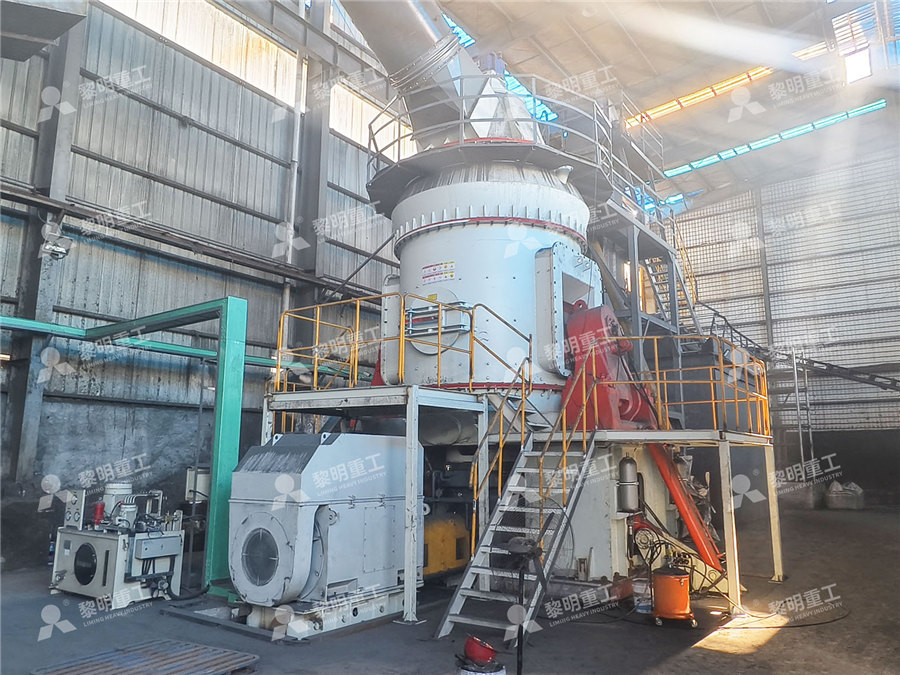
Coreless Induction Furnace Linings Capital Refractories
General purpose lining with a wide melting temperature range Ceramic: 1700* 1730† Coral HB: Tough general purpose lining Ceramic: 1680* 1720† Coral SMC: Incorporates complex chromes for improved slag resistance Ceramic: 1700* 1750† Coral 85: High performance lining designed for large furnaces operating at high temperatures Ceramic 2014年10月1日 Alkalis (K and Na compounds, Kobayashi et al, 1979) enter in the blast furnace with the charge materials (should be limited to 2530 kg alkalis/ton pig iron, Kurunov et al, 2009 or 2585 kg (PDF) Alkaline carbonates in blast furnace process