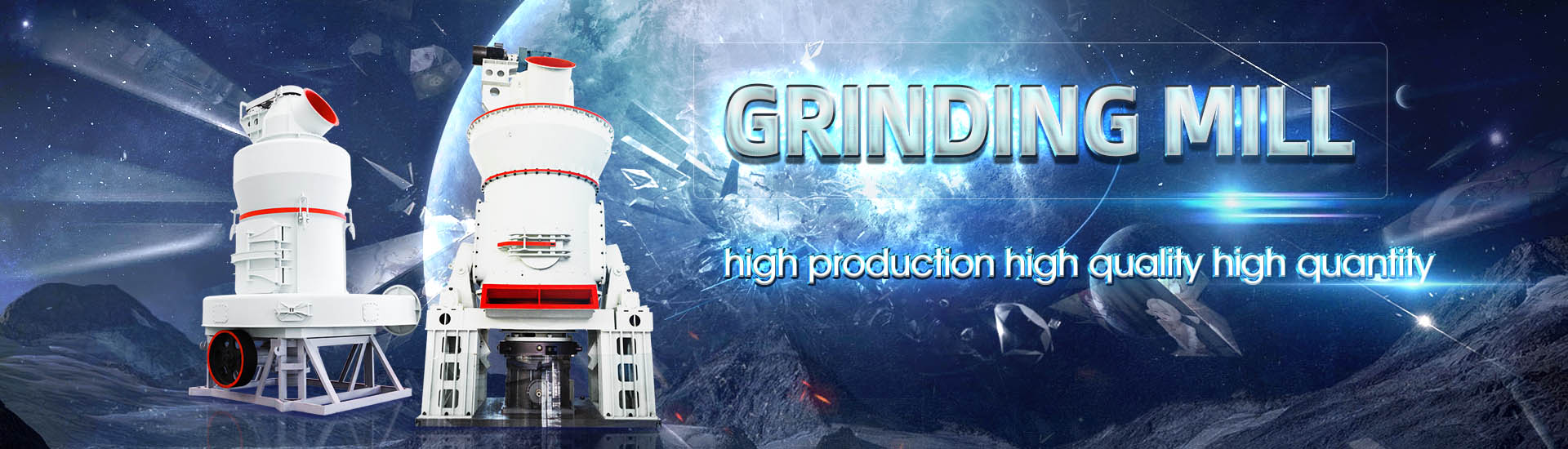
3. What is the production capacity of highfine cement mill
.jpg)
Global cement industry statistics facts Statista
2024年5月22日 Cement production capacity ranking worldwide by leading country 2022 Production capacity of cement worldwide in 2022, by leading country (in million metric tons per 2024年1月3日 China's cement production capacity in 2022 included an estimated 151 billion metric tons from its integrated cement plants, and a further estimated 1245 million metric tons per year fromChina: cement production capacity 2022 StatistaIn 2022, China had the highest cement production capacity in the world by far, at an estimated 164 billion metric tons per year (or more) China's cement production capacity includedCement capacity: global ranking by country 2022 2023年10月13日 The production process of cement releases large amounts of CO2, mainly due to the hightemperature firing of raw materials, such as limestone and clay, but also due to Global database of cement production assets and upstream
.jpg)
The Cement Plant Operations Handbook International
2 天之前 The Cement Plant Operations Handbook is a concise, practical guide to cement manufacturing and is the standard reference used by plant operations personnel worldwide 2021年12月21日 Almost 409Mt/yr of new cement capacity and 270Mt/yr of new clinker capacity is provided by these projects 272% of the new cement capacity comes from new separate Global Projects: Cement capacity expansion to 2025 Global Cement2020年12月15日 Recent decades have proven the great effectiveness of a vertical roller mill for grinding raw materials Its effectiveness, combined with the implementation of drying, grinding (PDF) Capacity of roller mill for cement grinding2023年1月1日 It is estimated that global cement production reached 41 gigatons in 2019, with China producing the large share Because of the importance of cement as a construction Production of cement and its environmental impact
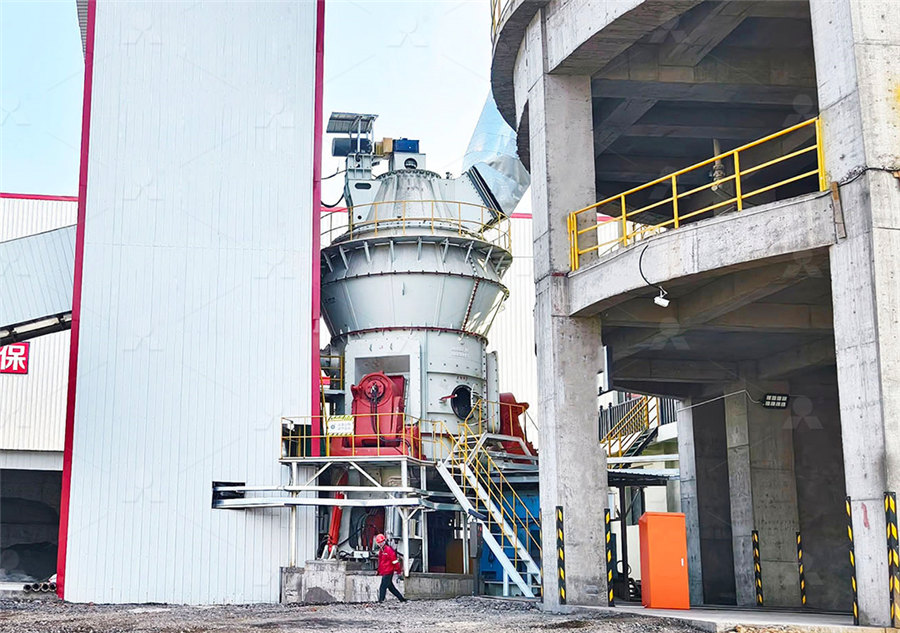
(PDF) Performance Evaluation of Vertical Roller
2017年9月11日 In this study, an extensive sampling study was carried out at vertical roller mill of ESCH Cement Plant in Luxemburg Samples were collected from mill inside and around the circuit toThe ball mill price is affected by the following factors, you can choose a suitable cement ball mill according to these factors Cost of production: materials cost, human cost, electricity power cost, etc; Technical costs: technology import, Cement Ball Mill Ball Mill For Sale Cement Mill 2021年3月30日 Global cement production is regionally concentrated Top five countries account for nearly three quarters of the world’s cement production which hovers around ~43 bln tons and around ~45% of the global capacity is occupied by the top 10 players China leads with a ~57% share, followed by India (~8%), Vietnam, USA and IndonesiaCement PACRA2 天之前 justification – 3 Capacity increase by process change – 4 Project cost estimation – 5 Financial statements 13 Technical and process audits 224 1 Historical performance – 2 Kiln specific fuel consumption – 3 Cement mill specific power consumption – 4 Other systems – 5 Debottlenecking – 6 Project audit – 7 Risk The Cement Plant Operations Handbook International
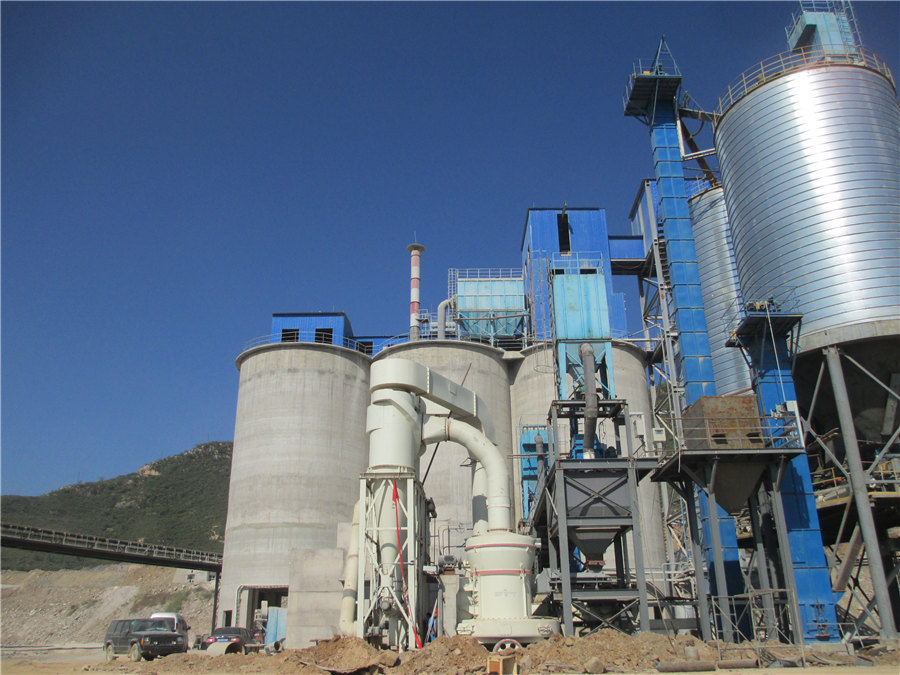
Understanding the Difference Between Raw Mill and Cement Mill
In the raw mill, vertical roller mills are used to grind the raw materials into fine particles On the other hand, in the cement mill, ball mills are used to grind the clinker into a powder Production Capacity The production capacity of a raw mill is generally lower than that of a cement millCement mills are the milling machines used in cement plants to grind hard clinker into fine cement powders Cement ball mill and vertical roller mill are two most widely used cement mills in today’s cement grinding plants and are also the main types of cement mill we produce As a professional cement equipment manufacturer, AGICO has rich experience in the designing and Cement Mill for Sale Buy Cement Ball Mill AGICO Cement 2021年1月1日 India is the world's second largest producer of cement and produces more than 8 per cent of global capacity Due to the rapidly growing demand in various sectors such as defense, housing, commercial and industrial construction, government initiative such as smart cities PMAY, cement production in India is expected to touch 550–600 million tones per Review on vertical roller mill in cement industry its Adjusting mill parameters: Finetuning mill parameters such as mill speed, ball charge, filling ratio, and grinding media size can have a substantial impact on the grinding efficiency of the mill For example, a 10% increase in mill speed can result in up to 10% higher production rate, while optimizing the ball charge can lead to a 510% Cement Mill Optimization: Practical Strategies for Enhanced
.jpg)
EnergyEfficient Technologies in Cement Grinding
2016年10月5日 In this chapter an introduction of widely applied energyefficient grinding technologies in cement grinding and description of the operating principles of the related equipments and comparisons over each other in terms of grinding efficiency, specific energy consumption, production capacity and cement quality are given A case study performed on a 2015年10月15日 A) Total Apparent Volumetric Charge Filling – including balls and excess slurry on top of the ball charge, plus the interstitial voids in between the balls – expressed as a percentage of the net internal mill volume (inside liners) B) Overflow Discharge Mills operating at low ball fillings – slurry may accumulate on top of the ball charge; causing, the Total Charge Calculate Ball Mill Grinding Capacity 911Metallurgist2020年12月9日 HIGH STRENGTH MICRO/NANO FINE CEMENT A GarcíaLuna (1), H Minard(1) for the commercial production of high strength micro/nanofine cement As a consequence, then in the longterm range, this technique should also be applied for (Capacity Force max= 1300 kN, by Controls) after 1, 3, 7 and 28 days of curing HIGH STRENGTH MICRO/NANO FINE CEMENT iccc 2020年1月6日 Figure 3 shows that, should all of the planned capacity additions be realised, the next two years to the end of 2021 could see the addition of a further 77Mt/yr of cement production capacity to 435Mt/yr This is around 21% more than 358Mt/yr at present‘Build, Build, Build’ing in the Philippines Global Cement
.jpg)
Coal utilization in the cement and concrete industries
2023年1月1日 The utilization of coal in the cement and concrete industries takes three basic forms: (1) as a fuel in the production of cement clinker; (2) ash produced by burning coal in power stations is used as a component in cement rotary kiln feeds; (3) ash produced by burning coal in power stations is used as a mineral additive in concrete mixes2020年11月5日 As you all know, the process of a cement manufacturing plant can be divided into several steps, including crushing, raw milling, clinker calcining, cement milling (or cement grinding), packing and etc In the complete cement 3 Necessary Cement Milling Comparison Ball 2023年8月23日 A cement mill is a fundamental component of the cement manufacturing process, playing a vital role in breaking down and grinding cement clinker into fine powder This finely ground powder, when mixed with other materials, produces the building material we commonly know as cement To achieve this crucial transformation, a cement mill comprises What Are the Parts of a Cement Mills? Cement Ball Mill Production 2008年8月1日 Ultra high strength steel rebars have recently been developed for super highrise reinforced concrete construction buildings The rebars have mechanical properties exceeding those conventionally High production capacity steel bar mill of high strength steel
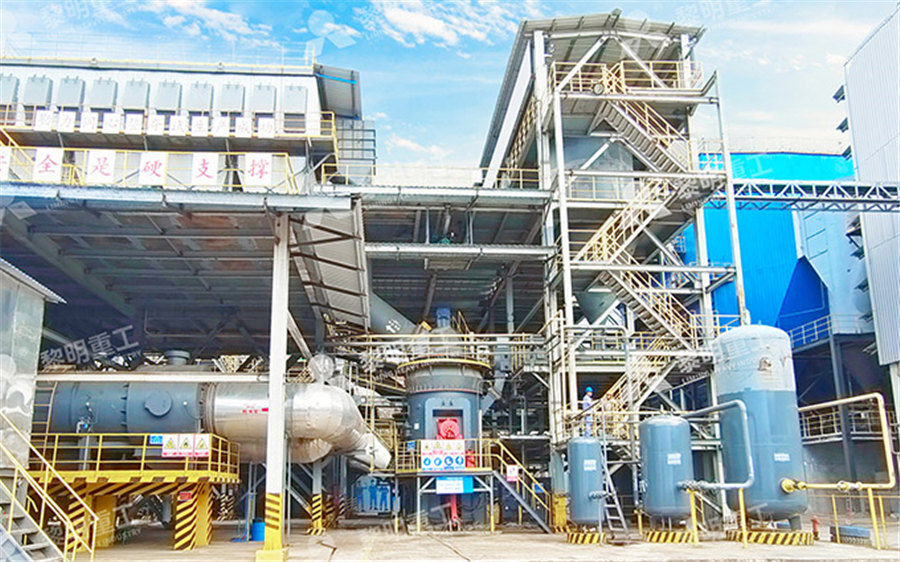
Raw Mill, Cement Raw Mill, Raw Mill In Cement Plant Cement
Raw mill is generally called cement raw mill, raw mill in cement plant, it refers to a common type of cement equipment in the cement plantIn the cement manufacturing process, raw mill in cement plant grind cement raw materials into the raw mix, and the raw mix is sent to the cement kiln to make cement clinker, next, clinker and other admixtures will be ground into finished cement by 2024年10月12日 Why install Roller Press in Cement Manufacturing Plant The overall trend is to increase the capacity of pregrinding bed, and transfer 60% to 70% of of the ball mill functions section to it and high fine airflow classification equipment to complete the system, with a large range of increased production and power saving capacityRoller Press Install For PreGrinding Before Cement Ball Mill2022年5月23日 The company's total cement capacity is now 2930 million tonnes 5: Dalmia Bharat Ltd Is ranked fifth among some of the top ten cement companies in total revenue The company operates a cement production factory with a capacity of 9 million tonnes per year in the southern regions of Tamil Nadu (Dalmiapuram Ariyalur) and Andhra (Kadapa)List of Top Largest Cement Manufacturing Companies in 2021年4月27日 The consumption of energy by the cement grinding operation amounts to one third of the total electrical energy used for the production of cement The optimization of this process would yield substantial benefits in terms of energy savings and capacity increase Optimization of the Cement Ball Mill OperationOPTIMIZATION OF CEMENT GRINDING OPERATION IN
.jpg)
Assessment on Cement Production Practice and Potential Cement
2020年1月1日 The combination effect of supplementary cementitious materials in the production of highstrength concrete production is an effective way to reduce the amount of cement required while contributing 2017年9月11日 A conventional cement grinding circuit is composed of a two compartment tube mill, a mill filter which collects the fine material inside the mill and a dynamic air separator where final product (PDF) Performance Evaluation of Vertical Roller 2023年7月10日 The cement manufacturing process involves the extraction and processing of raw materials, such as limestone, clay, and shale, which are then heated in a kiln at high temperatures to form clinkerCement Manufacturing Process and Its 2020年8月25日 A full cement production process includes the cement crushing process, raw mill process, clinker process, and cement grinding process, cement packing process, and related process the raw materials are processed by Cement Production Process Cement
.jpg)
Global database of cement production assets and upstream
2023年10月13日 Literature sources 2,3,5,6,10,13,21,26 identify several reasons for discrepancies between global cement production capacity and actual production Sentinel2 has a high revisit rate (3–5 days 2010年3月27日 The Cement Production Process as a result, the rotary kiln capacity is increased by a factor of more than 25 The efficiency of ball mills can be improved by modernising the internal components of the mill and fine tuning such things as The Cement Production Process mcilvainecompanyCement production capacity of selected top companies 年12月28日 1 The technical content of the ball mill must be high The technological content of a ball mill not only affects its price but also affects its production capacity Ball mills are updated relatively quickly, and only with high technical content can they achieve better production and increase production capacity 2Factors Affect The Output and Quality of Ball Mills And How
.jpg)
BALL MILLS Ball mill optimisation Holzinger Consulting
2021年3月12日 in combination with a ball mill for cement grinding applications and as finished product grinding units, as well as raw ingredient grinding equipment in mineral applications This paper will focus on the ball mill grinding process, its tools and optimisation possibilities (see Figure 1) The ball mill comminution process has a high electrical2021年1月29日 VRM Production Rate and Specific Power It can be clearly seen in Figure 3 that last 6 months average breakdown frequency Rate was 6016 tripping per month means per day more than 2 trippingIncrease productivity of vertical roller mill using seven QC tools2012年6月1日 An important characteristic of an indus trial ball mill is its production capacity which is measured in tons of producti on per hour The production capacity depends(PDF) Grinding in Ball Mills: Modeling and Process ControlThe ball mill price is affected by the following factors, you can choose a suitable cement ball mill according to these factors Cost of production: materials cost, human cost, electricity power cost, etc; Technical costs: technology import, Cement Ball Mill Ball Mill For Sale Cement Mill
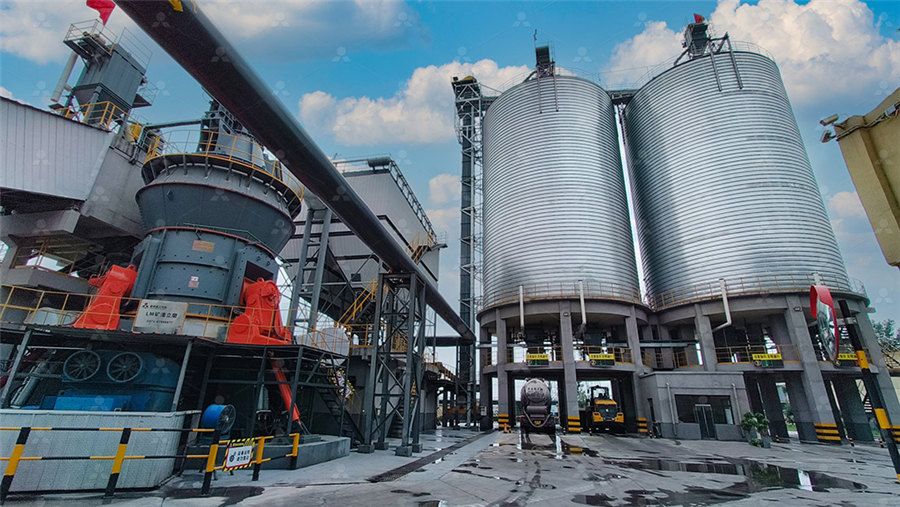
Cement PACRA
2021年3月30日 Global cement production is regionally concentrated Top five countries account for nearly three quarters of the world’s cement production which hovers around ~43 bln tons and around ~45% of the global capacity is occupied by the top 10 players China leads with a ~57% share, followed by India (~8%), Vietnam, USA and Indonesia2 天之前 justification – 3 Capacity increase by process change – 4 Project cost estimation – 5 Financial statements 13 Technical and process audits 224 1 Historical performance – 2 Kiln specific fuel consumption – 3 Cement mill specific power consumption – 4 Other systems – 5 Debottlenecking – 6 Project audit – 7 Risk The Cement Plant Operations Handbook International In the raw mill, vertical roller mills are used to grind the raw materials into fine particles On the other hand, in the cement mill, ball mills are used to grind the clinker into a powder Production Capacity The production capacity of a raw mill is generally lower than that of a cement millUnderstanding the Difference Between Raw Mill and Cement MillCement mills are the milling machines used in cement plants to grind hard clinker into fine cement powders Cement ball mill and vertical roller mill are two most widely used cement mills in today’s cement grinding plants and are also the main types of cement mill we produce As a professional cement equipment manufacturer, AGICO has rich experience in the designing and Cement Mill for Sale Buy Cement Ball Mill AGICO Cement
.jpg)
Review on vertical roller mill in cement industry its
2021年1月1日 India is the world's second largest producer of cement and produces more than 8 per cent of global capacity Due to the rapidly growing demand in various sectors such as defense, housing, commercial and industrial construction, government initiative such as smart cities PMAY, cement production in India is expected to touch 550–600 million tones per Adjusting mill parameters: Finetuning mill parameters such as mill speed, ball charge, filling ratio, and grinding media size can have a substantial impact on the grinding efficiency of the mill For example, a 10% increase in mill speed can result in up to 10% higher production rate, while optimizing the ball charge can lead to a 510% Cement Mill Optimization: Practical Strategies for Enhanced 2016年10月5日 In this chapter an introduction of widely applied energyefficient grinding technologies in cement grinding and description of the operating principles of the related equipments and comparisons over each other in terms of grinding efficiency, specific energy consumption, production capacity and cement quality are given A case study performed on a EnergyEfficient Technologies in Cement Grinding2015年10月15日 A) Total Apparent Volumetric Charge Filling – including balls and excess slurry on top of the ball charge, plus the interstitial voids in between the balls – expressed as a percentage of the net internal mill volume (inside liners) B) Overflow Discharge Mills operating at low ball fillings – slurry may accumulate on top of the ball charge; causing, the Total Charge Calculate Ball Mill Grinding Capacity 911Metallurgist
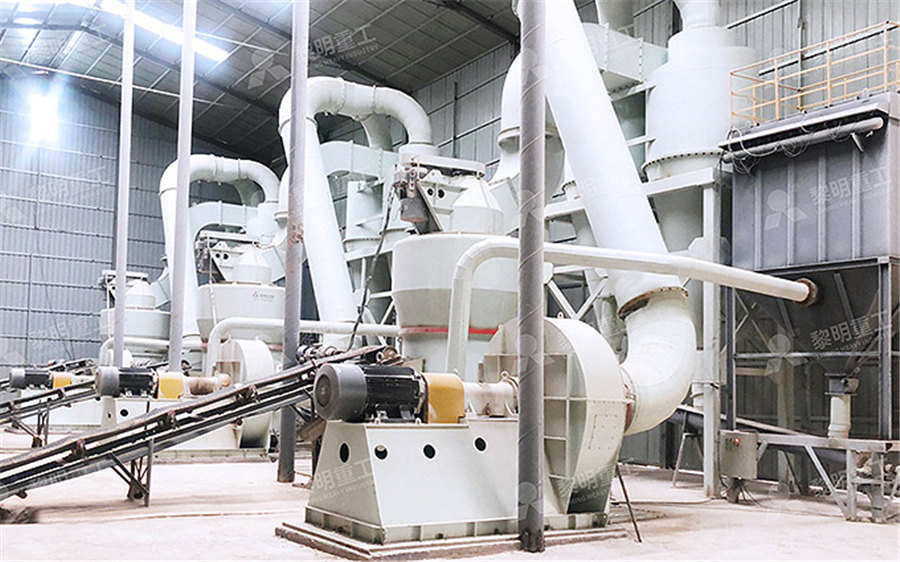
HIGH STRENGTH MICRO/NANO FINE CEMENT iccc
2020年12月9日 HIGH STRENGTH MICRO/NANO FINE CEMENT A GarcíaLuna (1), H Minard(1) for the commercial production of high strength micro/nanofine cement As a consequence, then in the longterm range, this technique should also be applied for (Capacity Force max= 1300 kN, by Controls) after 1, 3, 7 and 28 days of curing