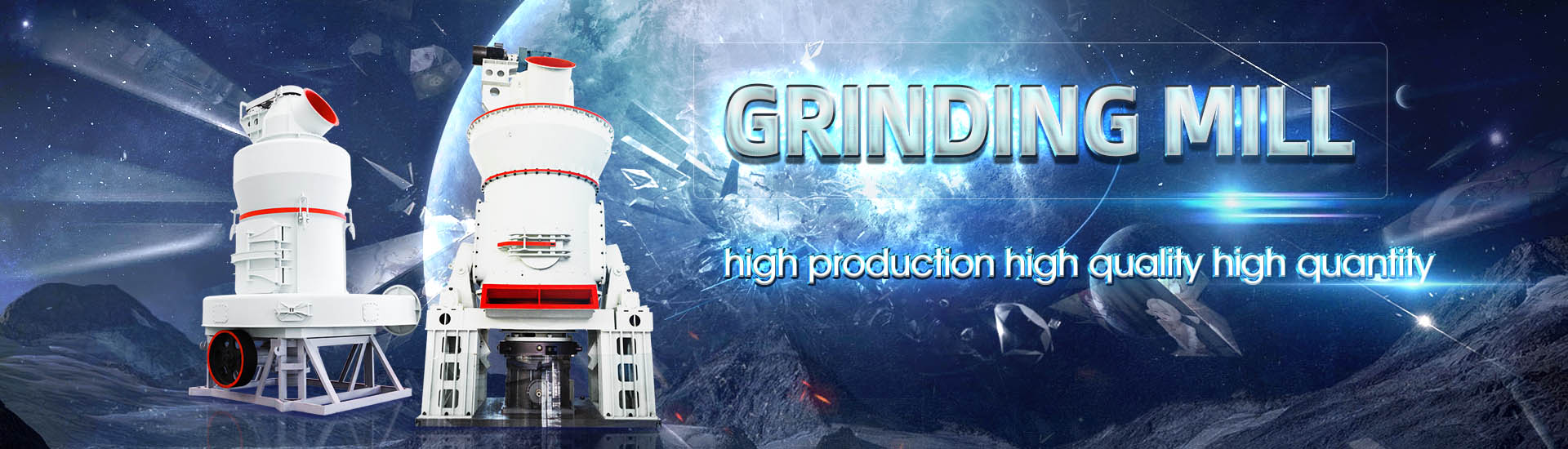
Mineral grinding mill 12 meters
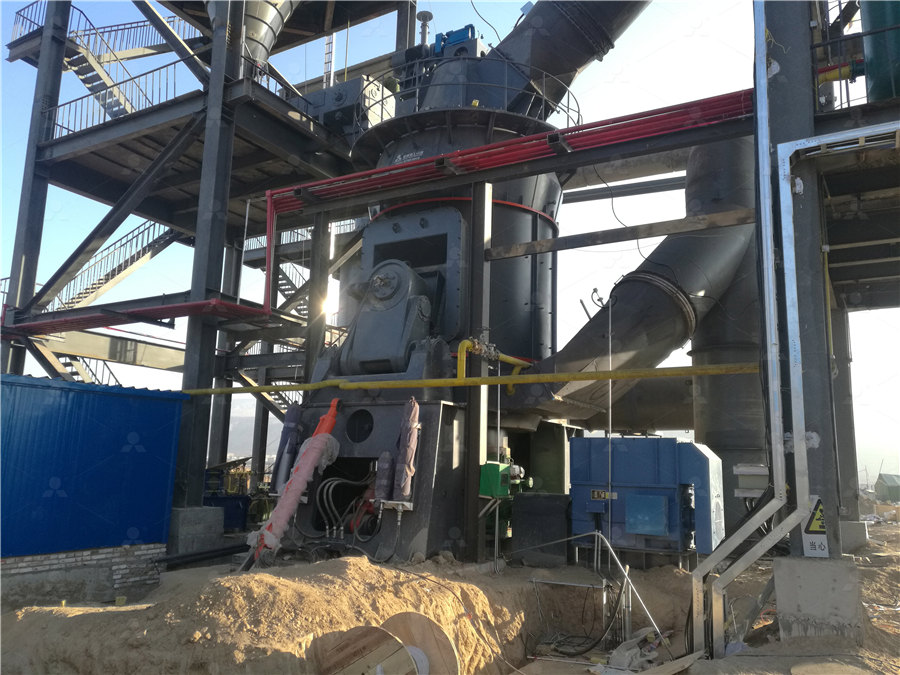
Grinding mills for mining and minerals processing
Browse Metso's wide offering of reliable grinding mills: AG mills, SAG mills, ball and pebble mills, and stirred mills to fit your needs Our pioneering innovations in horizontal grinding mills technology offer exceptional performance and For over 60 years, CITIC HIC has focused on providing global customers with reliable, energysaving and highefficiency mineral grinding mills, such as AG mills, SAG mills and overflow type ball millsGrinding Mills Mineral Processing Equipment CITIC HICThe Metso HIGmill™ is an advanced, energyefficient fine and ultrafine grinding solution that utilizes proven technology With the tall, narrow, vertical body arrangement, grinding media is evenly distributed and mineral particles remain HIGmill high intensity grinding mill MetsoSome of the key technical specifications include: Diameter and Length: Ball mills are typically available in diameters ranging from 06 meters to 4 meters and lengths ranging from 15 Technical specifications and selection guide for ball mills
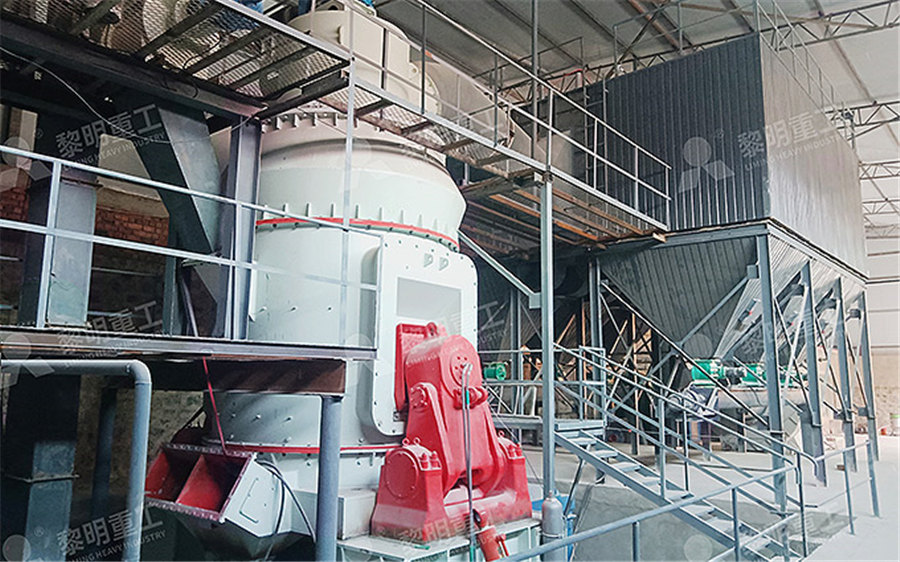
AMIT 135: Lesson 7 Ball Mills Circuits
Autogenous mills range up to 12 meters in diameter The lengthtodiameter ratios in the previous table are for normal applications For primary grinding, the ratio could vary between 1:1and 18:1 For fine regrinding in open circuit, the Customized grinding mill parts including heads, shells, trunnions and liners, main bearings, gears and pinions, and more! Metallic, PolyMet™, Megaliner™, Rubber and Orebed™ mill liners for Grinding MetsoInhouse AGMA 12 and up 6M diameter gears provide lead, profile, spacing, and bending resistance with less pitting, quieter, cooler operation, and longer gear life For most makes, models, and sizes from seals and bearings to full gear trains Mineral Processing Equipment for Mining LH Sepro Tyre Drive Grinding Mills are a reliable solution for small and medium capacity grinding applications and are suitable for ball, rod and pebble charges Sepro Grinding Mills come complete with a Variable Frequency Drive (VFD) Grinding Mills Sepro Mineral Systems
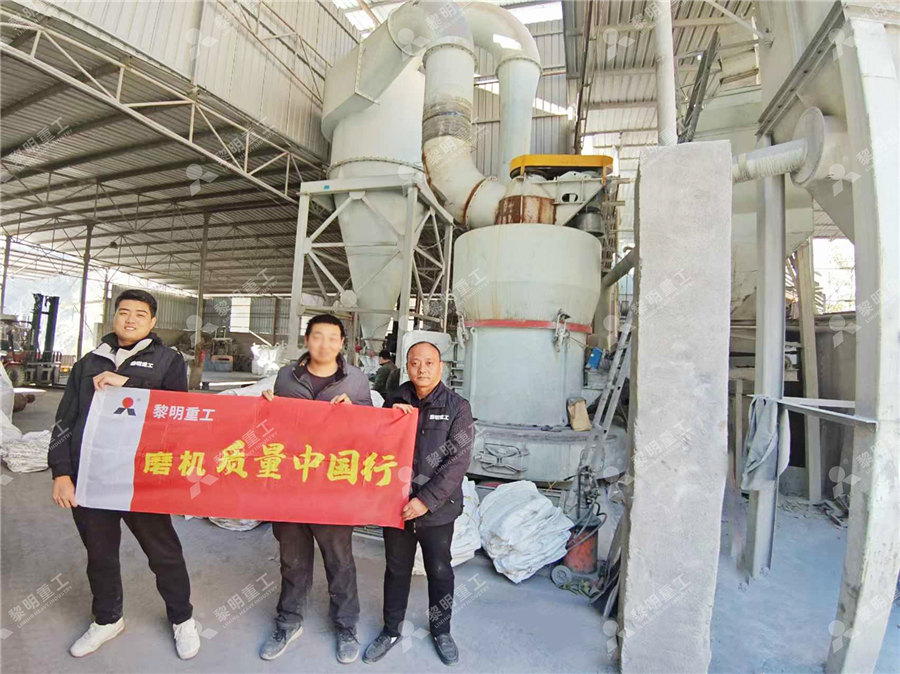
Grinding mills SKF
SKF solutions for grinding mills protect pinions and trunnions from harsh conditions Helping prevent failure for better reliability and safety with lower costs In mineral processing, grinding 2021年12月11日 In experiments done by Si et al [98] using magnetite ores to determine the effect of grinding media diameter on the mineral liberation degree, 8 different sizes of steel balls were used ie The Effect of Grinding Media on Mineral Breakage Keywords: jet mill, grinding of brittle minerals and material, ef fect of jet mill parameters, quartz, ferrosilicon Songklanakarin J Sci Technol 30 (3), 377384, May Jun 2008 1 Introduction Since recently, fine grinding and ultra fine grinding are important for Fine grinding of brittle minerals and materials by jet millWe deliver the required handson skills to those working with mineral grinding circuits so they can achieve worldclass performance from their operations Metcom’s study on ball mill coarse particle retention featured in the Nov 2021 Metcom Technologies – Expertise in mineral grinding
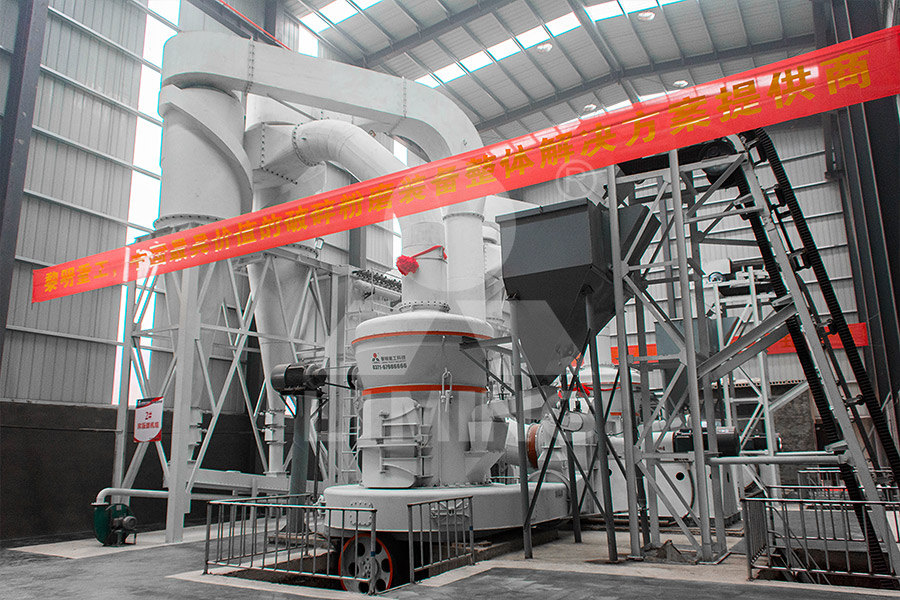
Grinding mills for mining and minerals processing Metso
When choosing your equipment we not only keep in mind mill performance, but also considering how your Premier™ or Select™ mill will optimize your minerals processing circuit Performance Metso Premier™ mills and Select™ mills are built with a robust design and components to eliminate unplanned downtime leading to high availability and reliabilityCalcium carbonate ultrafine vertical mill, integrating powder grinding, grading, conveying, secondary powder Especially in the field of ultrafine grinding of white nonmetallic minerals, it has outstanding performance It can provide highquality fillers and additives for papermaking 912: 1216: 1418: Less than 2μm=45% output (t/h) 5 Calcium Carbonate Ultrafine Vertical Mill SBM Ultrafine 2023年10月27日 The ball mill is a rotating cylindrical vessel with grinding media inside, which is responsible for breaking the ore particles Grinding media play an important role in the comminution of mineral A Review of the Grinding Media in Ball Mills for Mineral ProcessingAccording to the discharge type: overflow ball mill, grate discharge ball mill; According to the grinding conditions: wet milling, dry grinding; According to the ball mill media The Applicable Materials of Different Ball Mills Wet Grinding: Gold, chrome, tin, coltan, tantalite, silica sand, lead, pebble, and the like mining applicationBall Mill JXSC Mineral

AMIT 135: Lesson 7 Ball Mills Circuits – Mining Mill Operator
A survey of Australian processing plants revealed a maximum ball mill diameter of 524 meters and length of 884 meters (Morrell, 1996) Autogenous mills range up to 12 meters in diameter The lengthtodiameter ratios in the previous table are for normal applications For primary grinding, the ratio could vary between 1:1and 18:1Grinding: The crushed limestone small pieces are lifted to the silo and then sent to the mill evenly and quantitatively through the vibrating feeder for grinding The mill can use different types of equipment, such as an ultrafine grinding mill, which uses an advanced grinding roller and ring design to achieve higher production capacity than traditional mills with the same fineness and Limestone Grinding Mill Plant TAYMACHINERYGrinding Mills: Ball Mill Rod Mill Design PartsCommon types of grinding mills include Ball Mills and Rod Mills This includes all rotating mills with heavy grinding media loads This article focuses on ball and rod mills excluding SAG and AG mills Although their concepts are very similar, they are not discussed herePhotographs of a glass ended laboratory ball mill show Grinding Mills 911MetallurgistPDF On Jan 31, 2014, Ahmad Reza Sayadi and others published A parametric cost model for mineral grinding 0884 197e+004 112 9031 1105 1695 mineral grinding mill, and flotation A parametric cost model for mineral grinding mills
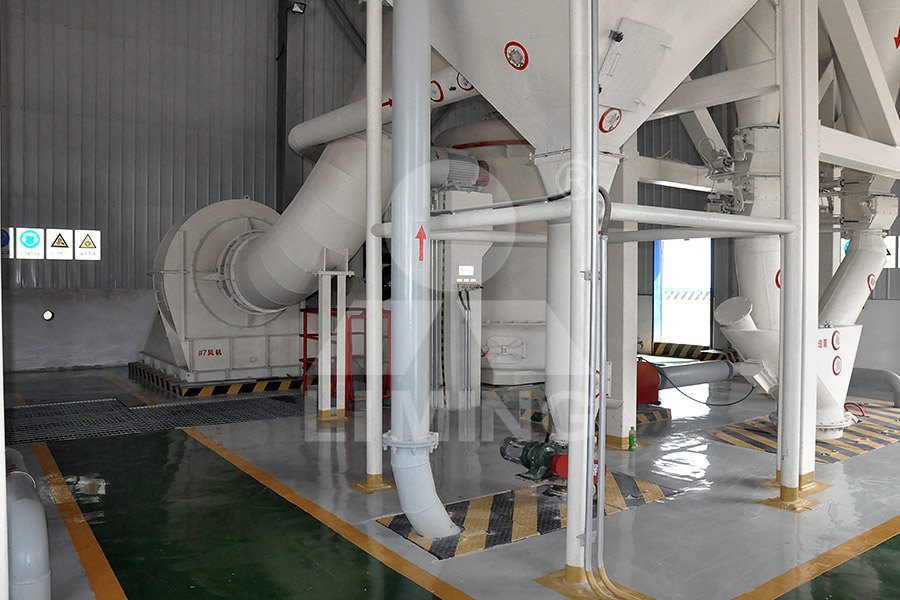
Grinding Mill Design Ball Mill Manufacturer 911Metallurgist
2017年2月20日 All Grinding Mill Ball Mill Manufacturers understand the object of the grinding process is a mechanical reduction in size of crushable material 911 Metallurgist is a trusted resource for practical insights, solutions, and support in mineral processing engineering, helping industry professionals succeed with proven expertise Grinding Mill Design Ball Mill With the grinding media evenly distributed, the ore particles remain in constant contact, significantly increasing grinding efficiency The product discharges at atmosphere at the top of the mill The combined cyclone overflow and mill discharge are the circuit product Figure 2 Optimal Grinding Conditions 21 HIGmillTM Control PhilosophyOutotec HIGmills; A Fine Grinding TechnologyIron ore dry grinding dry magnetic process of iron ore dressing mill for dry fine grinding, grinding fine reading can guarantee200 above 80%, equivalent to the common process of ball mill and screw grading machine or ball mill and cyclone grinding closed process, at the same time, iron ore dressing mill processing capacity is much higher than the ball mill, low energy consumption, News Iron ore mineral processing with standing grinding or ball 2024年7月19日 Grinding Mill equipment, such as MechProTech’s TITAN Grinding Mills and TITAN Automatic Ball Charger, can optimise grinding mills’ efficiency and performance, benefiting the process Investing in MPT equipment promises to improve your operational efficiency, with our team of experts ready to walk you through it allGrinding Mills in the Mineral Processing Industry MechProTech
.jpg)
Energy Use of Fine Grinding in Mineral Processing
2013年12月18日 Fine grinding, to P80 sizes as low as 7 μm, is becoming increasingly important as mines treat ores with smaller liberation sizes This grinding is typically done using stirred mills such as the Isamill or Stirred Media Detritor While fine grinding consumes less energy than primary grinding, it can still account for a substantial part of a mill’s energy budget Overall 2017年6月9日 As part of its mission to advance minerals technology, the Federal Bureau of Mines has conducted investigations to determine the feasibility of producing subsievesize material by an attrition grinding method The Bureaupatented technique involves the intense agitation of a slurry composed of the material to be ground, a granular grinding medium, and a Attrition Grinding Mill Design 911Metallurgist2015年10月15日 Learn how to calculate the grinding capacity of your ball mill with 911 Metallurgist This guide provides essential formulas, insights, and tips to optimize your milling process and enhance production efficiencyCalculate Ball Mill Grinding Capacity 911Metallurgist2017年10月3日 Share with Facebook; Share with Twitter; Share with Google+; Share with LinkedIn; Posted: October 3, 2017 Grinding Mills Types, Working Principle Applications The purpose of this article is to explain the usage of grinding mills in a mineral processing operation and to enable buyers to understand the best suitable grinding mill as per their specific needsGrinding Mill Types, Working Principle Applications
.jpg)
A mill power equation for SAG mills Springer
1990年2月1日 where m p is in kW; D is internal mill diameter (meters), L is internal mill length (meters); J is total fractional charge loading of the mill; J B is the fractional mill filling by balls; ε B is the effective porosity of the charge, taken as 03; ρ s and ρ b are true densities of rock and balls (tons per cubic meter), respectively; w c is the weight fraction of rock in water and rock in 2023年10月27日 The ball mill is a rotating cylindrical vessel with grinding media inside, which is responsible for breaking the ore particles Grinding media play an important role in the comminution of mineral ores in these mills This work reviews the application of balls in mineral processing as a function of the materials used to manufacture them and the mass loss, as A Review of the Grinding Media in Ball Mills for Mineral 2009年2月16日 Grinding mill circuits are the most energy and cost intensive unit processes in the mineral processing industry and therefore the study of the control systems for grinding circuits remains important (Ramasamy et al, 2005, Wills and NapierMunn, 2006)Grinding circuit control objectives range from maintaining system stability to achieving maximum economic benefitGrinding mill circuits — A survey of control and economic concernsA ball mill is a type of grinding mill used in the mineral processing Applications Mineral Processing: Grinding ores for further processing in flotation, leaching, or other mineral recovery processes Cement Production: Grinding clinker and other raw Ф24×12: 3538: 20: 62: 800: MBY710: 63: Ф24×13: 3538: 194: 69: 800: MBY710: 6 Ball Mill TAYMACHINERY
.jpg)
Grinding Mills Common Types 911Metallurgist
2016年11月7日 In Fig 13 is shown a large ball mill, designed for the dry grinding of limestone, dolomite, quartz, refractory and similar materials; this type of mill being made in a series of sizes having diameters ranging from about 26 in to 108 in, with the corresponding lengths of drum ranging from about 15 in to 55 in2017年9月1日 Fine grinding: How mill type affects particle shape characteristics and mineral liberation (12, 19, 25, 32) Mass of media: kg: 835: 1187: Media density (ceramic) kg/m 3: 383: 36: A comparison of particle bed breakage and rod mill grinding with regard to mineral liberation and particle shape effects Miner Eng, 11 Fine grinding: How mill type affects particle shape characteristics Grinding Mills Barry A Wills, James A Finch FRSC, FCIM, PEng, in Wills' Mineral Processing Technology (Eighth Edition), 2016 71 Introduction Grinding is the last stage in the comminution process where particles are reduced in size by a combination of impact and abrasion, either dry, or more commonly, in suspension in waterGrinding Mill an overview ScienceDirect Topics2017年10月26日 The following are factors that have been investigated and applied in conventional ball milling in order to maximize grinding efficiency: a) Mill Geometry and Speed – Bond (1954) observed grinding efficiency to be a function of ball mill diameter, and established empirical relationships for recommended media size and mill speed that take this factor into Factors Affecting Ball Mill Grinding Efficiency
.jpg)
IKA MF 102 Grinding Mill (Grinder) Labequip
~ Two different grinding heads can be attached to the drive ~ Heads are easily changeable Circumferential speed max: 34 m/s Feed hardness max: 6 Mohs Feed grain size max: 10 mm Material milling chamber: stainless steel 14308 Accessories: MF 102 Impact grinding head Sieve insert with hole sizes (1 of choice is included): 025 mm 050 mm 1 2023年11月24日 In order to increase the efficiency of the grinding mill, Stoimenov et al Grinding media effects Miner Eng 1999, 12, 147–163 The Effect of Grinding Media on Mineral Breakage Properties of Magnetite Ores Geofluids 2021, 2021, Grinding Media in Ball Mills for Mineral Processing2017年3月4日 Stamp mill ,Crusher , AG mill, SAG mill, Pebble m ill, Ball mill , Rod mill Rod mills are less common than ball m ills for grinding minerals The rods used in the mill, usually SIZE REDUCTION BY GRINDING METHODS ResearchGate2016年6月6日 Grinding Mill Shell Design Once the process metallurgist has thoroughly tested the ore body and determined the optimum method of mineral recovery; Some mill vendors provide 305 mm (12 in) spacing, and this SAG Mill Liner Design 911Metallurgist
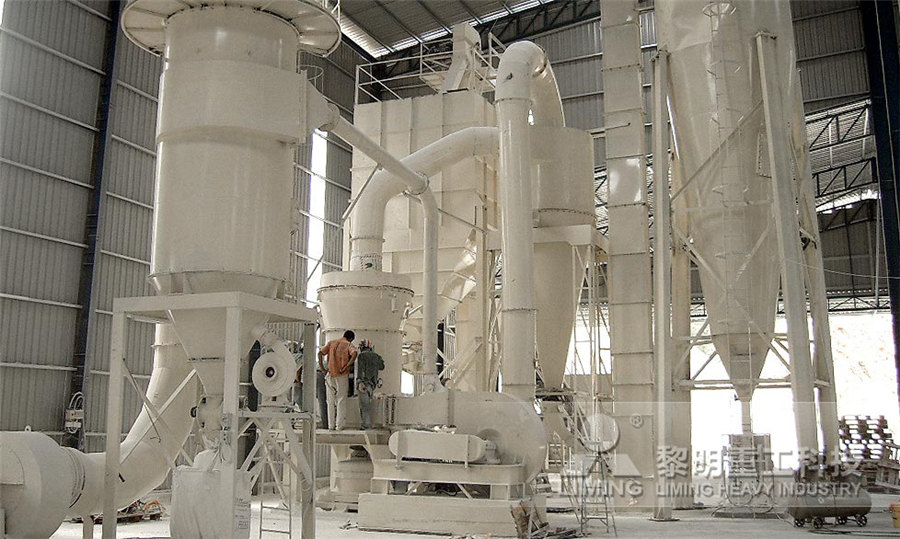
Grinding Classification Equipment JXSC Machinery
JXSC grinding classification equipment is the key equipment for crushing materials after they are crushed The ball mill can process various grinding minerals, nonferrous metal beneficiation, and new building materials It is Misunderstanding of Lubricating Oil Used in Raymond Mill As a common grinding plant, Raymond Mill can be used in fine powder making of barite, calcite, potassium feldspar, talc, marble, limestone, dolomite, fluorite, lime, activated About Us – gkmillAs of 2019, Shibang Industry and its affiliated companies have 5 advanced mining machine production bases and a production base in Xiuwu, Jiaozuo, Henan, which is under construction, with a total production area of 1,200,000 square meters, and will be able to better meet the needs of global customers in the future Stone Crushers, Mill and Grinding2017年1月17日 Grinding mills are infamous for their extremely low energy efficiency It is generally accepted that the energy required to produce new mineral surfaces is less than 1% of the electricity consumed Breaking down energy consumption in industrial grinding mills

Common Basic Formulas for Mineral Processing Calculations
2016年3月21日 Pulp Densities Pulp densities indicate by means of a tabulation the percentages of solids (or liquidtosolid ratio) in a sample of pulp This figure is valuable in two ways—directly, because for each unit process and operation in milling the optimum pulp density must be established and maintained, and indirectly, because certain important tonnage calculations are Crushing dan grinding dalam pengolahan mineral, merupakan dua tahapan utama dalam kominusi bijih untuk meningkatkan derajat liberasi mineral Metode yang digunakan meliputi penggunaan jaw crusher untuk proses crushing dan rod mill untuk grinding, dengan variasi waktu penggerusan yang 512 menitLAPORAN PRAKTIKUM PENGOLAHAN MINERAL Acara II Crushing and Grinding2003年4月1日 Netzch mill results with different media sizes: slurry feed F 80 $ 20 and 103 lm Variables Affecting the Fine Grinding of Minerals Using Stirred The Raymond mill is a versatile and reliable grinding machine, suitable for producing fine powders for a wide range of industrial applications Its efficiency, ease of maintenance, and ability to handle various materials make it a valuable asset in many industries [Introduction]: Raymond Mill has a strong performance of becoming a complete set with a production system Raymond Mill TAYMACHINERY
.jpg)
HighPressure Grinding Roller Presses for Minerals Processing
Screening at 4–12 mm Water Classi˜cation and ball mill Hydrocyclone HPGR Water Ore storage Downstream process Ore Grinding using an HPGR – Example Rule of thumb for energy savings with HPGRs The use of highpressure grinding machines in