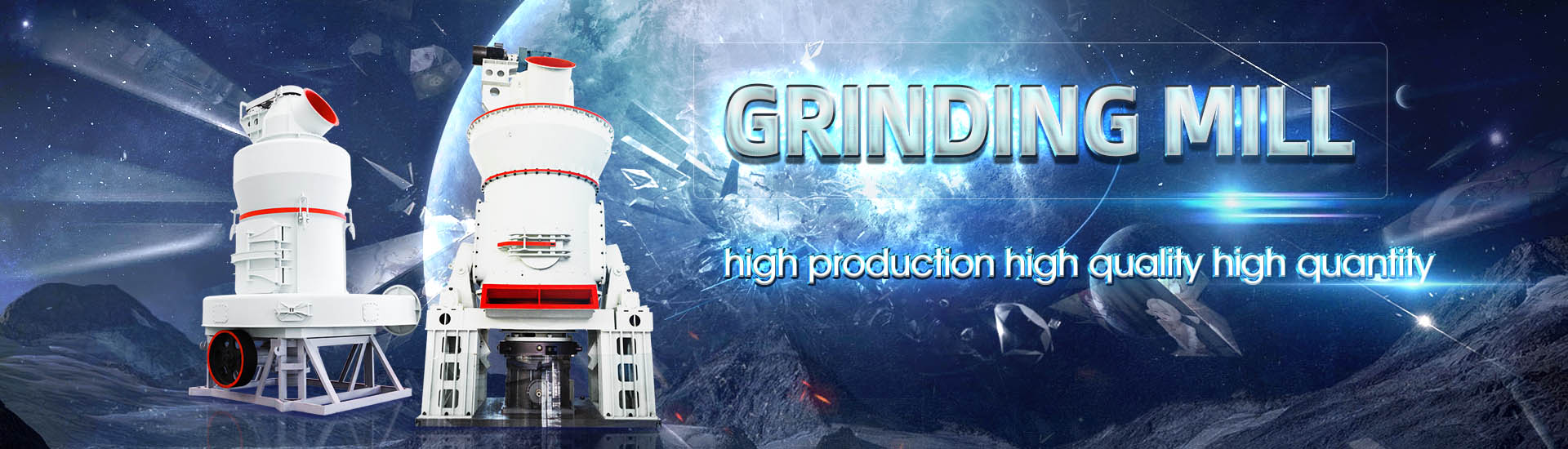
Quotation of large coal mill
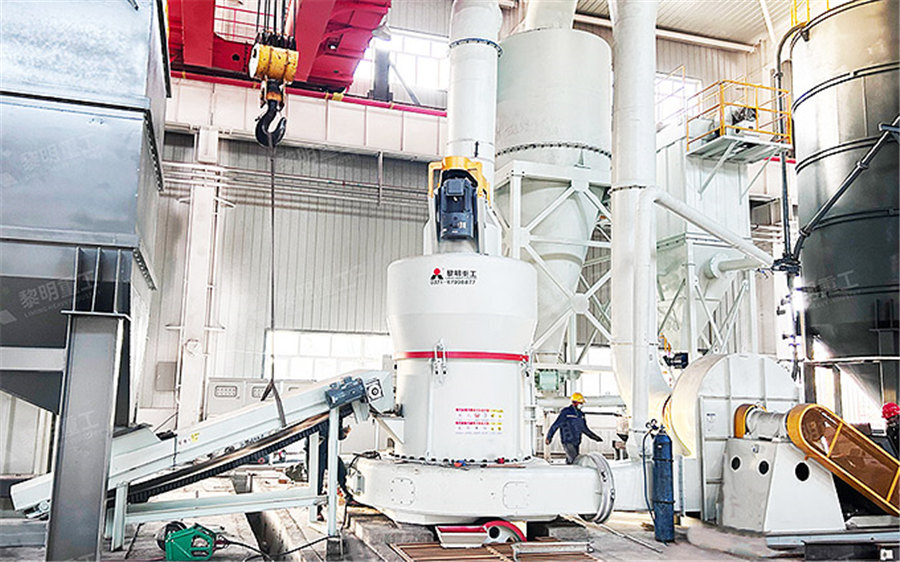
上海电气上重碾磨特装设备有限公司 Shanghai Electric
2019年12月13日 Until 2019, SHMP has produced more than 4500 sets of HP mediumspeed coal mill which were installed in almost 300 50MW100MW power generator at home and 2017年8月12日 Individual grinding mill design with a proven track record, encompassing 2, 3 and 4 rollers for fuel throughput rates up to and in excess of 200 t/h Pressure shock LOESCHEMILLSFind out all of the information about the Xinxiang Great Wall Machinery Co, Ltd product: roller mill GMRC Series coal mill Contact a supplier or the parent company directly to get a quote or to find out a price or your closest point of saleRoller mill GMRC Series coal mill Xinxiang Coal Bowl Mill, for guaranteed performance at a 500 MW capacity NTPC thermal power plant The study was conducted to assess the effective performance of the pulverizers of this 500 A Study on 500 MW Coal Fired Boiler Unit’s Bowl Mill
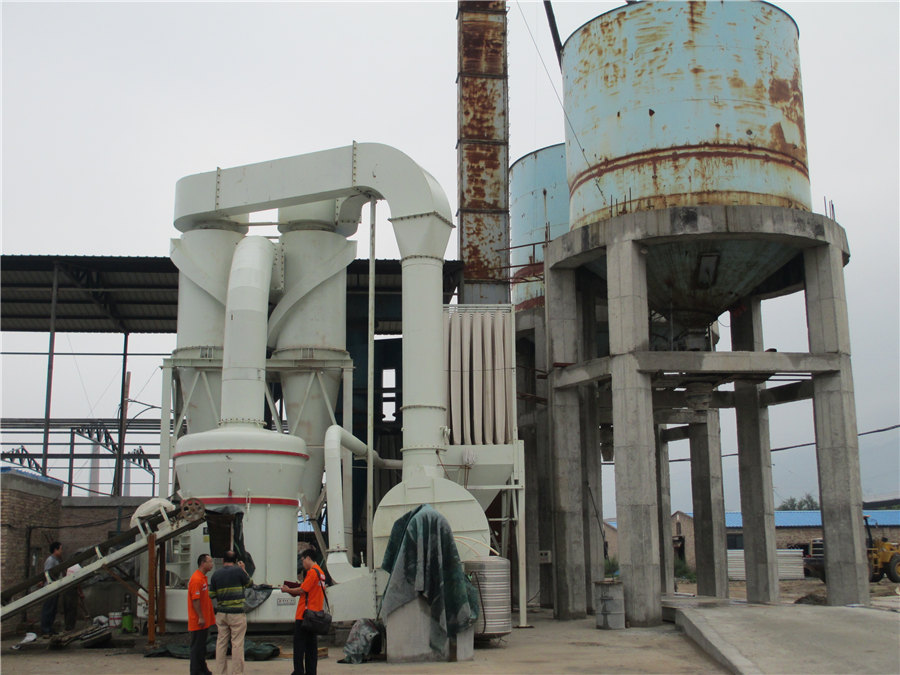
An investigation of performance characteristics
2020年8月12日 To understand the performance of a vertical roller coal mill, the real operational tests have been performed considering three different coal sources Obtained results indicate that grindingCoal mills or pulverizers play a very essential part in the coalfired power production system Coal mills grind the coal into fine powder, and the primary air entering the mill dries and drives the Coal Mill an overview ScienceDirect Topics2020年4月2日 In this paper, the findings of boiler house efficiency improvement study carried out in a large boiler house unit of a pulp and paper mill has been presentedAnalysis of the Coal Milling Operations to the 2015年11月1日 Coal mills are bottleneck in coal–fired power generation process due to difficulty in developing efficient controls and faults occurring inside the mills In this paper, a dynamic A unified thermomechanical model for coal mill operation
.jpg)
An investigation of performance characteristics and
2020年8月12日 This study shows the performance of a currently running vertical roller coal mill (VRM) in an existing coalfired power plant In a power plant, the coal mill is the critical A simple energy balance model of the coal mill is derived in (Odgaard and Mataji 2006), this model is based on a more detailed model found in (Rees and Fan 2003)In this model the coal mill is seen as one body with the mass m mThe following variables are defined: T(t) is the temperature in the coal dust flow in the mill, ṁ PA (t) is the primary air mass flow, T PA (t) is Coal Mill an overview ScienceDirect TopicsMeanwhile, the operation of coal mills also has a large influence on boiler combustion Among all the operating factors, the electricity current intensity of coal mills reflects the electricity power consumption as well as operating status of coal mills If the electricity current intensity of coal mills can be predicted by giving a set of A Modeling and Optimizing Method for Electricity Current 2014年1月1日 The emission factors of kiln end, kiln head, coal mill, crushing and cement mill was 0156 clinker g/t, 3914 clinker g/t, 1538 coal g/t, 0016 stone g/t and 0056 cement g/t respectively, the (PDF) MPS mills for coal grinding ResearchGate
.jpg)
Sectional view of MBF coal mill Download Scientific Diagram
A control oriented model was then developed by Fan (1994) and Fan and Rees (1994) In 2009, coal flow and outlet temperature of mill were modelled using mass and heat balance equations for startup 2020年4月2日 Coal mill motor power (kW) 0 4171 4548 4390 4586 4562 4410 the findings of boiler house efficiency improvement study carried out in a large boiler house unit of a pulp Analysis of the Coal Milling Operations to the Boiler Parameters2013年11月20日 Abstract: The paper presents development and validation of coal mill model (including the action of classifier) to be used for improved coal mill control The model is developed by using the mass and heat balance equations of the coal mill Genetic Algorithm is used to estimate the unknown parameters that are used in the model validationModeling and Control of Coal Mill NTNU2017年8月12日 The development of coal mills The development of Loesche coal mills began with tworoller mills and progressed to three and then to at least fourroller mills Due to the fact that the industry was asking for even higher throughputs, the company designed a LM 434 D as the world’s biggest coal mill, which successfully went intoOFTEN Loesche
.jpg)
Coal Mills SolidsWiki
2022年7月7日 Coal Mills are used to pulverize and dry to coal before it is blown into the power plant furnace Operation The coal is feed into the coal mill through a central inlet pipe where gravity is used to lead the coal to the bottom of the mill, where the grinding table and some heavy rollers pulverizes the coal to particles2020年6月19日 shut down under load, as this leaves a large amount of pulverised fuel inside a hot mill The large surface area of the pulverised coal and the high temperature inside the mill lead to rapid oxidation of the coal This results in further heat buildup and the potential for a fire If the mill is restarted without firstCOAL HANDLING SAFETY Land Instruments InternationalSection of coal bowl mill Table 1 Guaranteed coal conditions for mill performance evaluation Coal Moisture % 20 Coal HGI 55 Mill Outlet Temperarure °C 80 Mill Air Flow T/hr 102 Coal Fineness (% passing trough 200 mesh) 70% passing through 200 mesh and 90% passing through 50 mesh Differental Pressure 300 mmwc Coal Output from Mill 609 t/hrA Study on 500 MW Coal Fired Boiler Unit’s Bowl Mill Modeling and Control of Coal Mill MPC is the best choice to control a process when it is difficult to control using PID controller in systems with large time delay, large time constants, and inverse response Further, the main advantage of using MPC controller is that constraints on the input and output variables can be handled efficiently (PDF) Modeling and Control of Coal Mill Academia
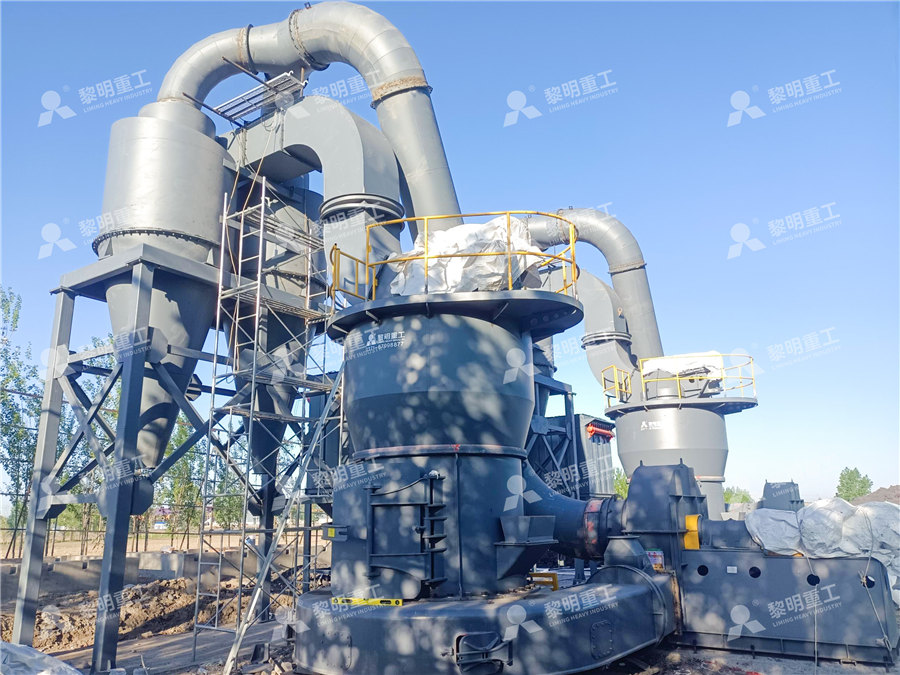
coal grinding machine CHAENG
4 天之前 Process introduction Vertical coal mill, also known as vertical roller coal mill or vertical coal grinding mill, is a mechanical equipment for crushing and grinding coal into coal powerMainly used for grinding raw coal, bituminous coal, and other fuels into coal powder, which is supplied to rotary kiln and other kilns in the cement plant and thermal power pared with the vertical roller mill, the advantages of airswept ball mill are strong adaptability to raw coal quality, simple operation and low investment cost; the disadvantages are high power consumption and high noise Vertical Roller Coal Mill in Cement Plant Vertical Roller Mill2024年10月31日 Proper Ventilation: Ensuring adequate ventilation in the coal mill area helps disperse coal dust and reduce the risk of ignition Ventilation systems must be designed to handle the specific needs of the mill Regular Maintenance: Routine maintenance of coal mills and associated equipment is vital for preventing mechanical failures This Coal Mill Safety: A Critical Aspect of Power Plant Operations Coal 2016年9月7日 additional field tests, but require suitable modelling techniques which are to be identified properly A novel coal mill modelling technique for Etype coal mill and dynamic behaviour are developed using genetic algorithms [3] Genetic Algorithms (GAs) have been successfully applied to problems in business, engineering, and scienceMeasurement and Control of Coal Pipe Temperature of
.jpg)
The layout of the coal mill with a rotary classifier
Vertical Coal Mill (VCM) is equipment for grinding and pulverizing coal into micron size Rotary kilns then use the powders as fuel burners The VCM has a housing section equipped with a lining 2021年8月1日 Yukio et al [7] proposed a model consisting of blending, grinding and classifying processes for pulverizer control Agarawal et al [8] differentiated coal powder into ten size groups, divided the bowl mill into four zones, and developed a unified model Palizban et al [9] derived nonlinear differential mass equations of raw coal, recirculation coal and suspension coal in Coal mill model considering heat transfer effect on mass 2009年9月1日 The coal mill used in the coalfired power plants is modeled in view of the controller design rather than the educational simulator The coal mass flow and the outlet temperature are modeled by reinvestigating the mass balance and heat balance models physically The archived data from a plant database are utilized to identify the model Modeling and Parameter Identification of Coal Mill2020年8月14日 the coal mill will cause large economic loss to power generation enterprises and decrease the safety and stability of the power system erefore, it is of great necessity to(PDF) Application of ModelBased Deep Learning Algorithm in Fault
.jpg)
Modeling of a medium speed coal mill Semantic Scholar
2017年8月1日 Meanwhile, the operation of coal mills also has a large influence on boiler combustion Among all Expand 1 PDF 1 Excerpt; Save A dynamic nonlinear model for a oncethrough boilerturbine unit in low load Yuguang Niu Du Ming Weichun Ge Huanhuan Luo Guiping Zhou Engineering, Environmental Science2024年8月22日 The BTM is a lowspeed mill that primarily grinds coal by impact and attrition The VRM is a medium speed mill that grinds coal by compression and, because of the low coal inventory in the mill and flat grinding surfaces, develops shearing action as well For both mills a constant centrifugal force is maintained The speedA Comparison of Three Types of Coal Pulverizers2020年8月12日 To understand the performance of a vertical roller coal mill, the real operational tests have been performed considering three different coal sources Obtained results indicate that grinding pressure, primary air (PA) temperature and mill motor current have a tendency to rise by increasing coal feeding mass flow rates for all used coal An investigation of performance characteristics and 2016年1月18日 Abstract: This paper presents the shortcomings of traditional PID method in coal mill control, such as multivariable coupling, nonlinearity and largetime delay, and give a new method to solve the problems Firstly, the principles of coal mill is presented, and a coal mill model is establishedThe Inferential predictive control method of coal mill IEEE
.jpg)
Coal Ball Mill Grinding for Different Kinds of Pulverized Coal
A highquality coal mill can effectively solve the fineness problem of coal powder and ensure uniform grinding of raw coal The fineness of pulverized coal has a great influence on the ignition temperature and burning time of the equipment In this way, the influence of bad raw coal on combustion efficiency can be well improved by coal mill2021年10月28日 From the coal yard, the coal is transfer to the mill bunkers through conveyor belt The bunkers are sized for an effective capacity of twelve (12) hours at BMCR with design coal Each mill bunker has one hopper, connected to the feeders Mills operate when the bunker coal gate valves are opened, coal is allowed to flow to the gravimetric feedersAnalysis of the Coal Milling Operations to the Boiler 2021年6月10日 54 kg/sec of coal The greatest risk of fire occurs when the mill is shut down under load, as this leaves a large amount of pulverised fuel inside a hot mill The large surface area of the pulverised coal, as well as the high temperature inside the mill, leads to rapid oxidation of the coal This results in further heat buildup and the COAL MILL Land Instruments International2020年1月1日 Coal mills have a significant influence on the reliability, efficiency, and safe operation of a coalfired power plant Coal blockage is one of the main reasons for coal mill malfunctionEarly Warning of Critical Blockage in Coal Mills Based on
.jpg)
ATOX® Coal Mill FLSmidth Cement
The ATOX® Coal Mill’s large rollers can handle up to 200mm feed lumps, reducing the need for a separate crusher Large rollers also help ensure a thick grinding bed for maximum uptime The roller segments are reversible which ensures the highly durable materials are fully utilised Our ATOX® Coal Mill can also be equipped with a water 2015年11月1日 The coal mill grinds the raw coal into fine powder and hot air entering the mill dries and carries the pulverized coal to the burners of the furnace Maffezzoni (1986 ) emphasized that coal mills are the primary cause of slow load following capability and regular plant shutdownsA unified thermomechanical model for coal mill operation2022年3月25日 Coal mills consume a huge amount of station service electricity power of a coalfired power plant Meanwhile, the operation of coal mills also has a large influence on boiler combustion(PDF) A Modeling and Optimizing Method for Electricity A simple energy balance model of the coal mill is derived in (Odgaard and Mataji 2006), this model is based on a more detailed model found in (Rees and Fan 2003)In this model the coal mill is seen as one body with the mass m mThe following variables are defined: T(t) is the temperature in the coal dust flow in the mill, ṁ PA (t) is the primary air mass flow, T PA (t) is Coal Mill an overview ScienceDirect Topics
.jpg)
A Modeling and Optimizing Method for Electricity Current
Meanwhile, the operation of coal mills also has a large influence on boiler combustion Among all the operating factors, the electricity current intensity of coal mills reflects the electricity power consumption as well as operating status of coal mills If the electricity current intensity of coal mills can be predicted by giving a set of 2014年1月1日 The emission factors of kiln end, kiln head, coal mill, crushing and cement mill was 0156 clinker g/t, 3914 clinker g/t, 1538 coal g/t, 0016 stone g/t and 0056 cement g/t respectively, the (PDF) MPS mills for coal grinding ResearchGateA control oriented model was then developed by Fan (1994) and Fan and Rees (1994) In 2009, coal flow and outlet temperature of mill were modelled using mass and heat balance equations for startup Sectional view of MBF coal mill Download Scientific Diagram2020年4月2日 Coal mill motor power (kW) 0 4171 4548 4390 4586 4562 4410 the findings of boiler house efficiency improvement study carried out in a large boiler house unit of a pulp Analysis of the Coal Milling Operations to the Boiler Parameters
.jpg)
Modeling and Control of Coal Mill NTNU
2013年11月20日 Abstract: The paper presents development and validation of coal mill model (including the action of classifier) to be used for improved coal mill control The model is developed by using the mass and heat balance equations of the coal mill Genetic Algorithm is used to estimate the unknown parameters that are used in the model validation2017年8月12日 The development of coal mills The development of Loesche coal mills began with tworoller mills and progressed to three and then to at least fourroller mills Due to the fact that the industry was asking for even higher throughputs, the company designed a LM 434 D as the world’s biggest coal mill, which successfully went intoOFTEN Loesche2022年7月7日 Coal Mills are used to pulverize and dry to coal before it is blown into the power plant furnace Operation The coal is feed into the coal mill through a central inlet pipe where gravity is used to lead the coal to the bottom of the mill, where the grinding table and some heavy rollers pulverizes the coal to particlesCoal Mills SolidsWiki2020年6月19日 shut down under load, as this leaves a large amount of pulverised fuel inside a hot mill The large surface area of the pulverised coal and the high temperature inside the mill lead to rapid oxidation of the coal This results in further heat buildup and the potential for a fire If the mill is restarted without firstCOAL HANDLING SAFETY Land Instruments International
.jpg)
A Study on 500 MW Coal Fired Boiler Unit’s Bowl Mill
Section of coal bowl mill Table 1 Guaranteed coal conditions for mill performance evaluation Coal Moisture % 20 Coal HGI 55 Mill Outlet Temperarure °C 80 Mill Air Flow T/hr 102 Coal Fineness (% passing trough 200 mesh) 70% passing through 200 mesh and 90% passing through 50 mesh Differental Pressure 300 mmwc Coal Output from Mill 609 t/hr