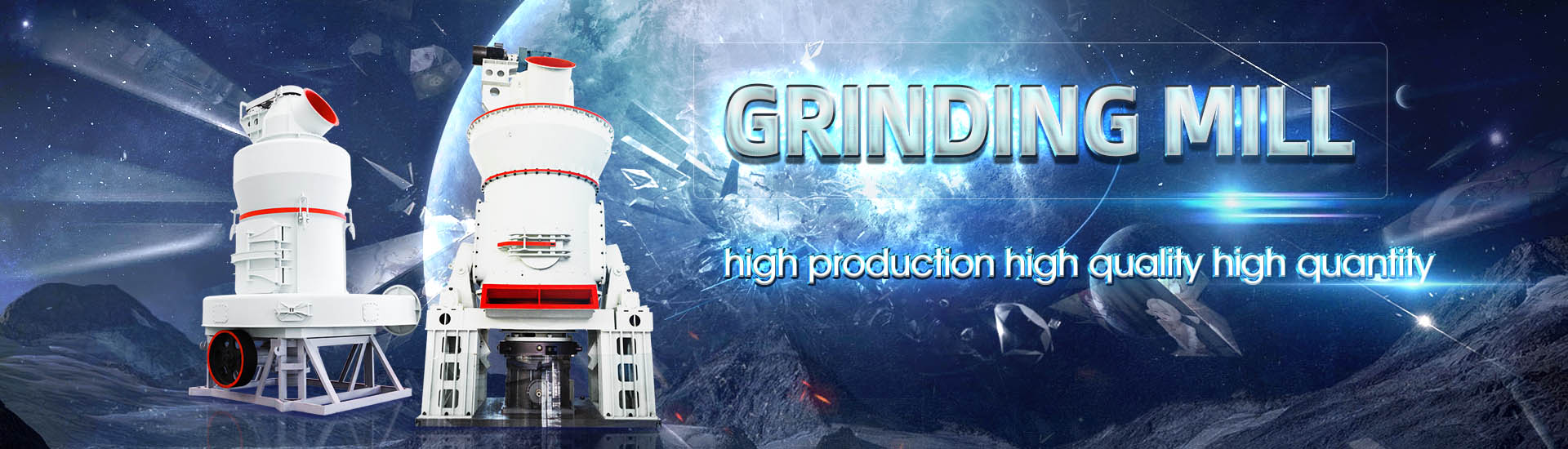
Comparison of grinding processes
.jpg)
Advances in Modeling and Simulation of Grinding Processes
2006年1月1日 This keynote paper results from a collaborative work within the STC G and gives an overview of the current state of the art in modeling and simulation of grinding processes: 2023年9月29日 Li et al [106] compared the grinding forces, grinding temperatures, surface roughness and surface quality of brazed grinding wheels, ceramic grinding wheels and Mechanical behavior and modeling of grinding force: A 19 小时之前 This paper effectively integrates Taguchi, Response Surface Methodology (RSM), and Genetic Algorithm (GA) approaches for both single and multiobjective optimization, MultiObjective Optimization of the Surface Grinding Process 1992年1月1日 This paper describes the stateoftheart in the modelling and simulation of grinding processes The kinematics of the grinding process are characterised by a series of Modelling and Simulation of Grinding Processes
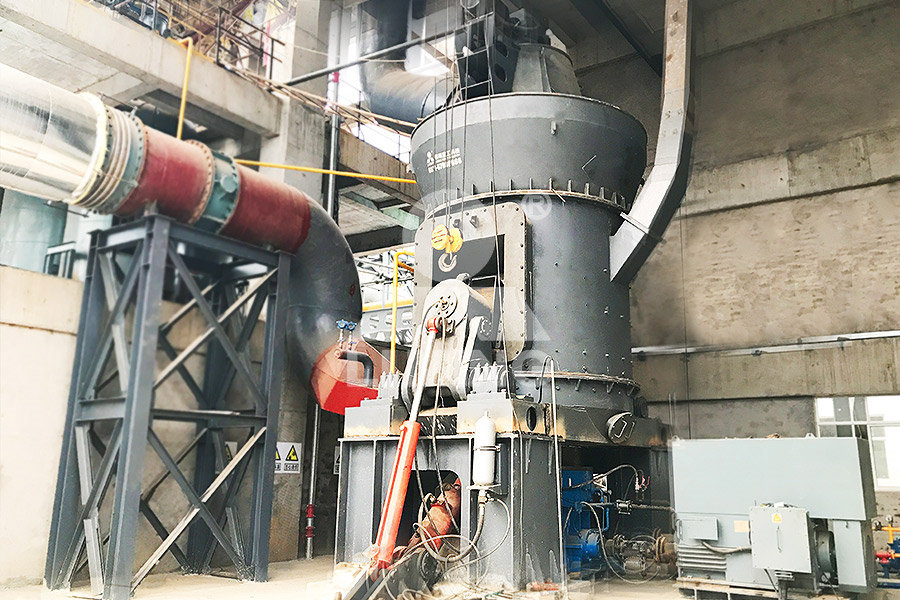
Effect of different parameters on grinding
2016年11月22日 Focusing on the core issues of grinding process, the paper presents some fundamental research findings in relation to grinding material removal mechanisms The grinding efficiency is analysed by considering the 2022年6月24日 Grinding is a manufacturing process which significantly contributes in producing high precision and durable components required in numerous applications such as aerospace, A comprehensive review on the grinding process: 2023年12月21日 Generally, the grain experiences three stages during the grinding process as it passes through the grinding zone: sliding, plowing, and microcutting The transition among the A multiscale model revealed in the grinding process and its 2015年12月30日 Grinding machines use abrasive wheels that rotate at high speed to either remove a layer of material (in rough grinding) or finish the part surface (in finish grinding) The process of grinding is much different from Grinding Processes SpringerLink
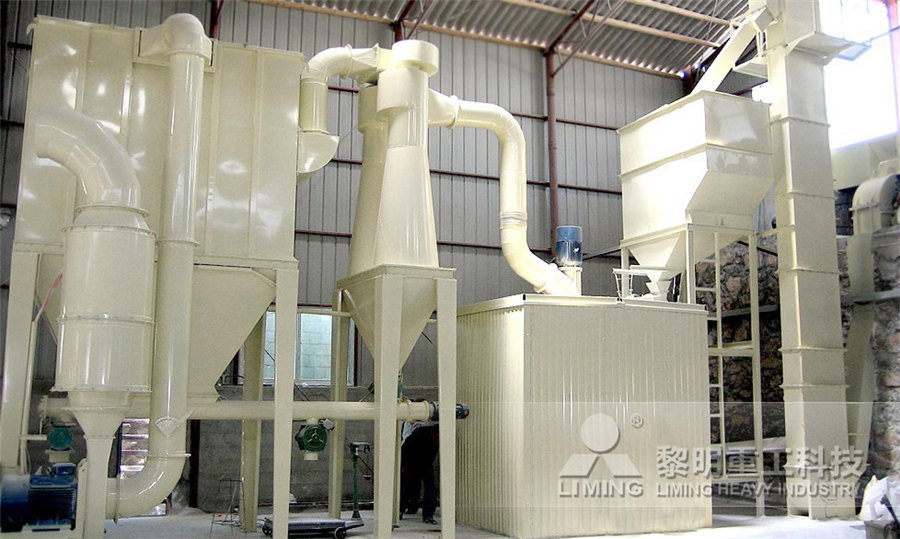
(PDF) Sustainability Versus Efficiency of Manufacturing Process
2019年1月1日 In this paper two high precision fine grinding processes are compared concerning their efficiency and ecological friendliness Therefore, Life Cycle Assessment (LCA) as well as 2024年7月12日 Grinding Process Choosing Sandpaper: Select appropriate sandpaper based on the material, surface condition, and final requirements Common grits range from 80 to 1000 and higher Comparison of Grinding Grinding vs Polishing: Differences China VMT2019年1月1日 Grinding process comparison by means of TOPSIS According to the described approach in section 43 and the datasets mentioned in secti on 32, a t otal of 6 TOPSIS analyses are (PDF) Sustainability Versus Efficiency of Manufacturing Process 2023年9月29日 Currently, scholars consider the grinding force modeling mainly from the material, grinding process, grinding wheel wear and other aspects Meng et al [3] established the grinding force model of a new type of microstructure grinding wheel based on the topography model, and found that the addition of microstructure reduced the grinding force by 496 % ~ Mechanical behavior and modeling of grinding force: A
.jpg)
A review on conventional and advanced minimum quantity
Grinding is one of the important machining processes that are widely applied in precision manufacturing In the beginning, studies mostly focused on dry machining In time, emerging technologies have led to change in the development of the machining process New techniques and tools have been developed over the last decade that has brought the process to an 2016年11月22日 Today, grinding process has been successfully applied to almost all types of material removing process with extremely high material removal rate of more than 2000 mm 3 /(mm s) and ultraprecision accuracy to nanometre level surface finish (Comley, Comparison of grinding power signals and grinding acoustic emission signals Display full sizeEffect of different parameters on grinding efficiency and its 2023年8月22日 Recently, ultrahigh strength steels have attracted an increase attention to prepare highperformance gears in helicopter transmission system to confront the complex and severe environment, owing to their superior mechanical properties (eg, high hardness and high toughness) [1, 3]Grinding as the final and crucial manufacturing processes was widely used to Study on grinding performance during ultrasonic vibration During a machining process with a trackbound cutting edge engagement, the cutting edge of the grain penetrates the workpiece upon a flat path and, after a phase of elastic deformation, triggers plastic flow of the workpiece material (Fig 3)Due to the shape of the cutting edge, the angle between the cutting edge contour and the workpiece surface is very small at the beginning of Grinding Process SpringerLink
.jpg)
A comprehensive review on the grinding process:
2022年6月24日 Grinding is a manufacturing process which significantly contributes in producing high precision and durable components required in numerous applications such as aerospace, defence and automobiles This review article is focused to uncover history, witness the present and predict the future of the grinding process2013年3月27日 The MRR achieved in the EDG process is up to 50 times higher, and the surface roughness is at least 4 times better than the EDM process The surface finish obtained by the EDG process is at least 45 times better than the conventional diamond grinding process and 3 times lower than cryogenically cooled conventional diamond grinding parison of EDG, Diamond Grinding, and EDM Processing 2006年1月1日 In the last decade the relevance of modeling and simulation of grinding processes has significantly risen which is caused by industrial needs and is indicated by the number of publications and research activities in this area Analysis and simulation of the grinding process Part III: Comparison with experiment International Journal of Advances in Modeling and Simulation of Grinding Processes2023年11月28日 Grinding is widely used for machining highprecision parts, but grinding wheel wear and grinding wheel vibration significantly impact the surface quality of the parts in the process of machining However, the effect of those two factors on the grinding surface has not been considered simultaneously in most grinding surface topography simulation studies Simulation of grinding surface topography considering
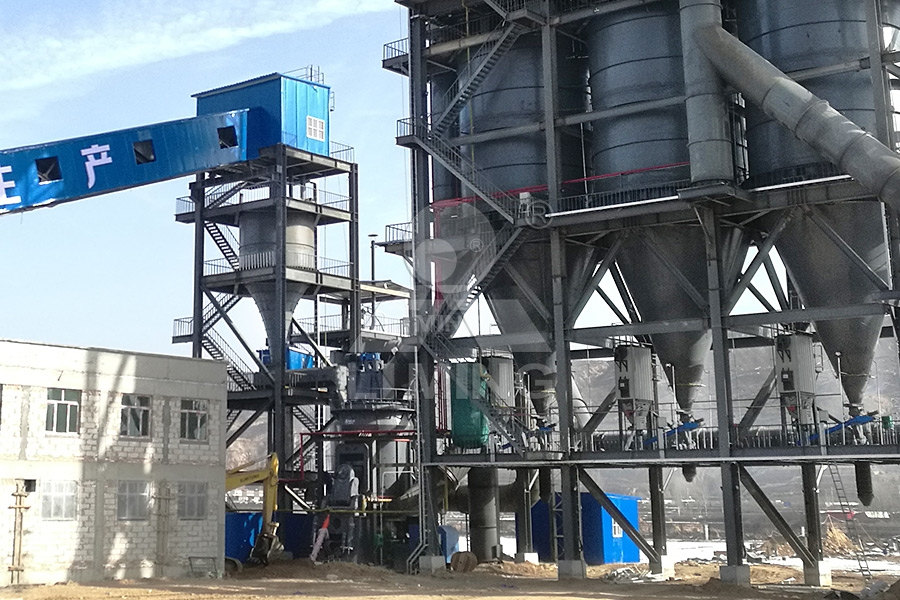
Comparison of Comminution by Impact of Particle
2006年5月1日 This article presents the innovative grinding apparatus Pulsar in which comminution is caused by impact of a particle plug on an impact plate Advantages of the Pulsar principle in comparison to other types of mills are discussed The aim of the work is to classify the Pulsar system in the field of grinding apparatus and machines in terms of energy consumption 2023年1月1日 CITIC Heavy Industries has a large installed base of grinding equipment throughout Africa in different configurations, including highpressure grinding rollers with ball mill and semiautogenous ball crusher The total installed power of CITIC’s mills exceeds 430 MW In this paper, we compare several typical grinding circuits of copper in Africa with about 15 kt/d OneMine Comparison of Typical Copper Ore Grinding Processes 2024年10月10日 The grinding process is a key link in mineral processing production and a typical complex, controlled process The steadystate model is limited by its model structure and thus difficult to applyied in a control system A hybrid modeling method driven by multisource compensation is proposed in this paper based on the mechanism model using key equipment Hybrid Modeling and Simulation of the Grinding and MDPI2023年4月23日 A comparison of the grinding media is given together with the knowledge gaps that still need to be bridged to improve the quality and performance of grinding media used in ball mills(PDF) Grinding Media in Ball MillsA Review ResearchGate
.jpg)
Sustainability Versus Efficiency of Manufacturing Process: Structured
2019年1月1日 Grinding process comparison by means of TOPSIS According to the described approach in section 43 and the datasets mentioned in section 32, a total of 6 TOPSIS analyses are carried out considering the grease and water based samples of the different products The identified process parameter relevant in each of the analyses is the minimum value 2015年12月30日 From the example it is seen that grinding is generally a high finish, high specific energy, and low power process, in comparison to turning and milling processes 44 Cylindrical Grinding Cylindrical grinding is also referred to as chuck grinding, and it involves the rotation of grinding wheel as well as the workpieceGrinding Processes SpringerLink2024年2月26日 The optimal process combination was identified under the current test parameters The findings revealed that the grinding force, grinding force ratio, and surface roughness of different crystalline planes of βGa2O3 were reduced to varied extents, enhancing surface quality in comparison to conventional grindingExperimental investigation on axial ultrasonicassisted grinding 2016年10月28日 The converter steel slag cannot be widely used in building materials for its poor grindability In this paper, the grinding characteristics of untreated and pretreated (ie, magnetic separation) steel slag were compared Additionally, the grinding property of pretreated steel slag was also studied after adding grinding aids The results show that the residues (ie, oversize Comparison of Grinding Characteristics of Converter Steel
.jpg)
Grinding Machining Process : Complete Notes Mech4study
The grinding machine provides high accuracy and fine surface finish with minimum tolerances The machining process is done by the abrasive action of the grinding wheel; the abrasives are embedded over the periphery of the rotating wheel In Grinding machine grinding wheel is work as a cutting tool and responsible for all machining processes2024年2月22日 Introduction In industrial processes, grinding balls are indispensable components in milling and grinding operations, where they play a pivotal role in reducing particle sizes and refining material textures These Ceramic vs Steel Grinding Balls: A 2016年11月1日 General comparison of experimental and numerical grinding forces with of 10 m/min, of 269 m/s and of 30, 80, and 150 µm: (a) normal and (b) tangential forces(PDF) Detailed modeling of cutting forces in 2020年12月15日 Which type of machining process is the grinding operation? (i) abrasive machining, (ii) con Kuang, W, Yang, C (2020), Comparison on grindability and surface integrity in creep feed (PDF) Machining Processes and Machines: Fundamentals
.jpg)
Temperature modeling of creepfeed grinding processes for
2023年4月1日 Thermal models of grinding processes usually rely on the moving heat source theory by Carslaw and Jaeger [11], [12]The heat source sliding over the workpiece surface is quantified by three major components: the total heat generated during the material removal, the heat partition transferred to the workpiece and the local distribution of the heat flux within the 2017年6月1日 Grinding process could be considered as a kind of most widelyused finishing operation in the manufacturing because of low cost, high machining efficiency and good finish quality [1]Grinding forces are a key element in grinding, influencing material removal rates, machined surface qualities, grinding temperature and vibrations, and further wheel wear and Detailed modeling of cutting forces in grinding process 2018年3月29日 Comparison of dry and wet grinding process in an electromagnetic mill is presented in this paper The research was conducted in a batch copper ore grinding Batch mode allows for precise parametrization and constant repetitive conditions of the experiments The following key aspects were tested: processing time, feed size, size of the grinding media, Comparison of Wet and Dry Grinding in Electromagnetic Mill MDPI2023年11月24日 The grinding media properties affect the overall performance of the grinding process, with grinding media size distribution being more significant than the density, shape, and hardness Operational parameters such as grinding media filling, pH, mill speed and wear also affect ball mill efficiency Shi, F Comparison of grinding media Grinding Media in Ball Mills for Mineral Processing
.jpg)
A Comparison of Back Grinding Processes for Bare Silicon
2011年10月1日 The optimization of grinding parameters for silicon wafers is necessary in order to reduce the likelihood of residual stresses and crack nucleation in the machined surface and improve the reliability of electronic packages This paper describes numerical simulations performed to characterize the back grinding process for bare silicon wafers and throughsilicon Grinding process involves a lot of heat generation, and sparks are produced between tool workpiece contacts Cutting fluids are employed in the grinding process to improve machining performance from ages In the industrial machining sector, the CFG technique is noteworthy compare to other highefficiency grinding and the differences are Grinding (Machining) an overview ScienceDirect Topics2010年9月6日 The particle size and shape distribution of the fi bres analysed after grinding and liberation processes are depicted in Figure 1 (Impact mill and Twinscrew extruder) The distribution curves Comparison of grinding and liberation processes for stalky 2024年7月12日 Grinding Process Choosing Sandpaper: Select appropriate sandpaper based on the material, surface condition, and final requirements Common grits range from 80 to 1000 and higher Comparison of Grinding Grinding vs Polishing: Differences China VMT
.jpg)
(PDF) Sustainability Versus Efficiency of Manufacturing Process
2019年1月1日 Grinding process comparison by means of TOPSIS According to the described approach in section 43 and the datasets mentioned in secti on 32, a t otal of 6 TOPSIS analyses are 2023年9月29日 Currently, scholars consider the grinding force modeling mainly from the material, grinding process, grinding wheel wear and other aspects Meng et al [3] established the grinding force model of a new type of microstructure grinding wheel based on the topography model, and found that the addition of microstructure reduced the grinding force by 496 % ~ Mechanical behavior and modeling of grinding force: A Grinding is one of the important machining processes that are widely applied in precision manufacturing In the beginning, studies mostly focused on dry machining In time, emerging technologies have led to change in the development of the machining process New techniques and tools have been developed over the last decade that has brought the process to an A review on conventional and advanced minimum quantity 2016年11月22日 Today, grinding process has been successfully applied to almost all types of material removing process with extremely high material removal rate of more than 2000 mm 3 /(mm s) and ultraprecision accuracy to nanometre level surface finish (Comley, Comparison of grinding power signals and grinding acoustic emission signals Display full sizeEffect of different parameters on grinding efficiency and its
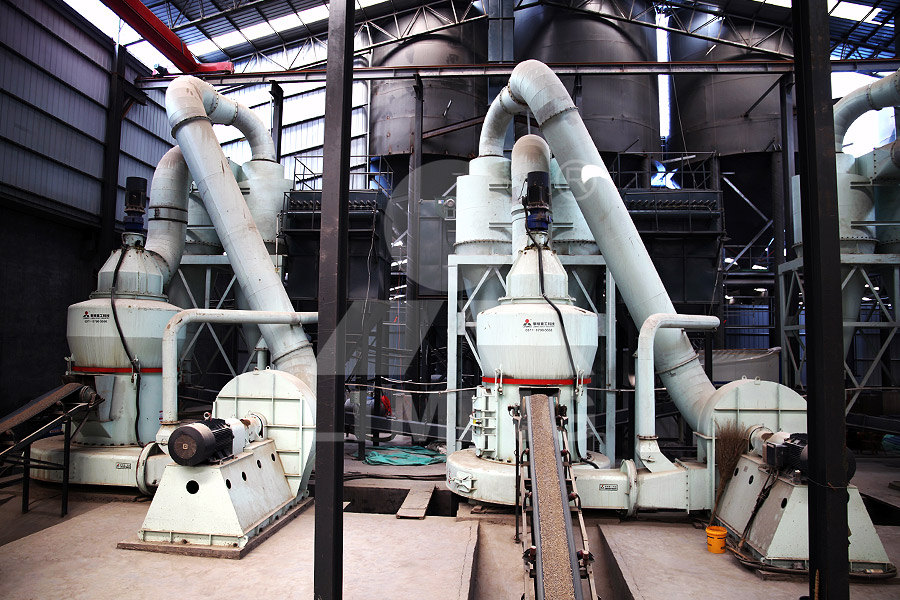
Study on grinding performance during ultrasonic vibration
2023年8月22日 Recently, ultrahigh strength steels have attracted an increase attention to prepare highperformance gears in helicopter transmission system to confront the complex and severe environment, owing to their superior mechanical properties (eg, high hardness and high toughness) [1, 3]Grinding as the final and crucial manufacturing processes was widely used to During a machining process with a trackbound cutting edge engagement, the cutting edge of the grain penetrates the workpiece upon a flat path and, after a phase of elastic deformation, triggers plastic flow of the workpiece material (Fig 3)Due to the shape of the cutting edge, the angle between the cutting edge contour and the workpiece surface is very small at the beginning of Grinding Process SpringerLink2022年6月24日 Grinding is a manufacturing process which significantly contributes in producing high precision and durable components required in numerous applications such as aerospace, defence and automobiles This review article is focused to uncover history, witness the present and predict the future of the grinding processA comprehensive review on the grinding process: 2013年3月27日 The MRR achieved in the EDG process is up to 50 times higher, and the surface roughness is at least 4 times better than the EDM process The surface finish obtained by the EDG process is at least 45 times better than the conventional diamond grinding process and 3 times lower than cryogenically cooled conventional diamond grinding parison of EDG, Diamond Grinding, and EDM Processing
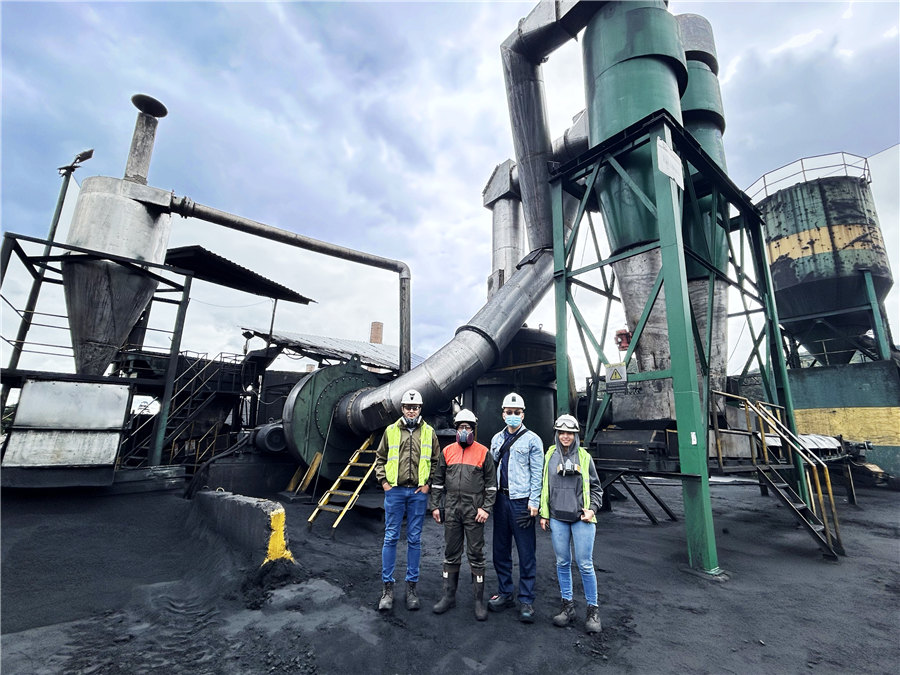
Advances in Modeling and Simulation of Grinding Processes
2006年1月1日 In the last decade the relevance of modeling and simulation of grinding processes has significantly risen which is caused by industrial needs and is indicated by the number of publications and research activities in this area Analysis and simulation of the grinding process Part III: Comparison with experiment International Journal of