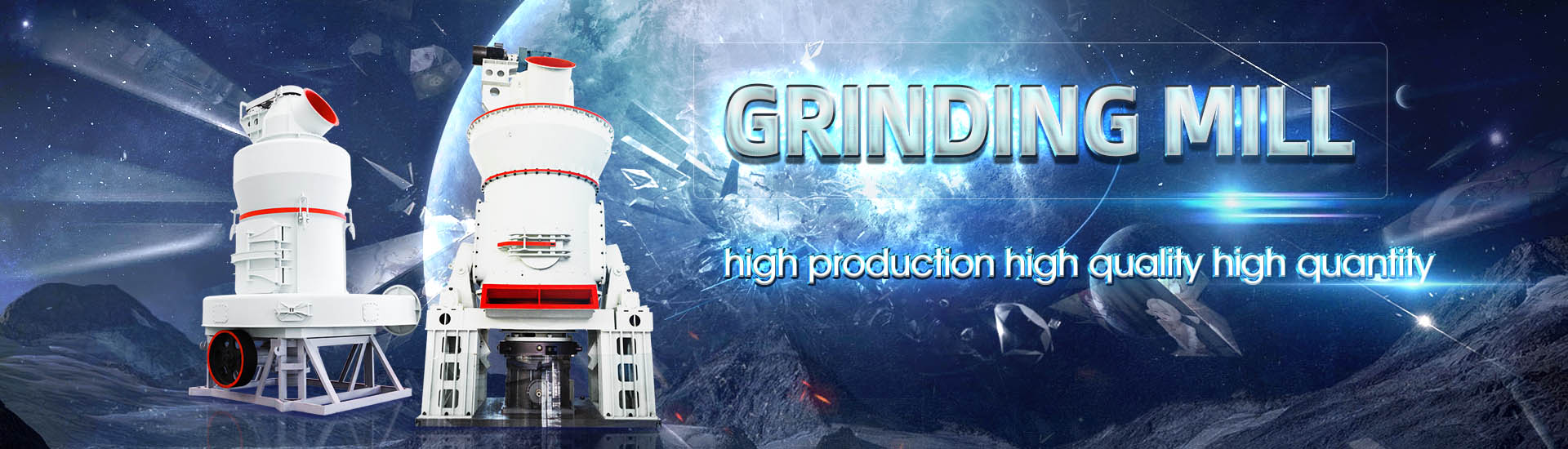
Water atomization iron oxide grinding equipment
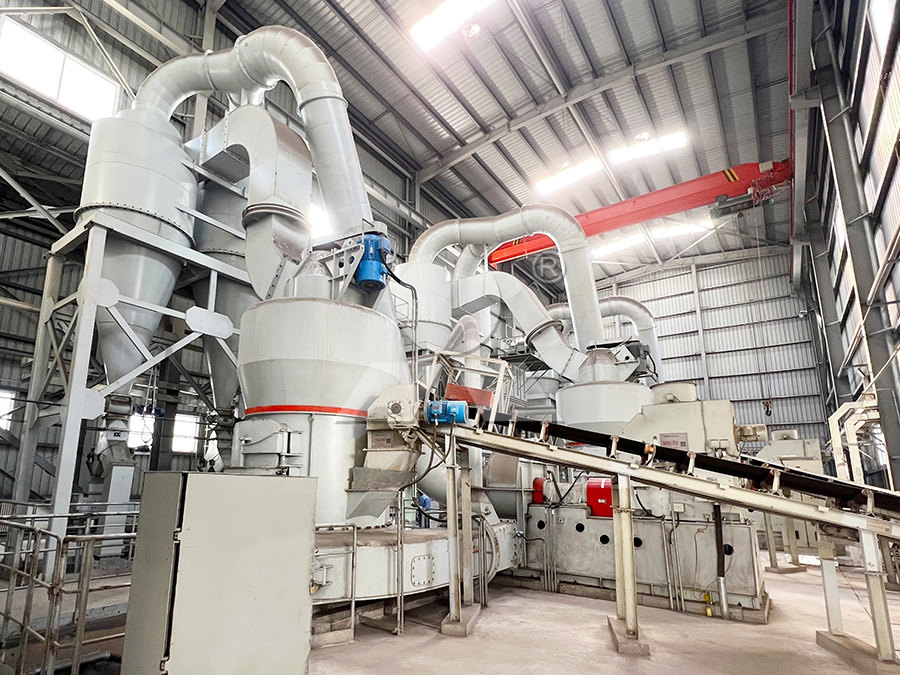
Particle morphology of water atomised iron‑carbon powders
2022年1月1日 This study will consider the cooling, solidification and collision of droplets during water atomisation of molten ironcarbon alloys and investigate the feasibility that collisions govern the particle size and shapes in water atomisation of such alloys2017年1月30日 2) Water atomization: Atomization involves the disintegration of a thin stream of molten metal through the impingement of high energy jets of a fluid Water is the most commonly used liquid in atomization Water atomized iron powders have irregular particle shape and A review of Developments in Powder Metallurgy 2019年11月1日 Hoganas and water atomization processes are currently the major iron powder production techniques in China, but both have obvious drawbacks A novel and clean iron powder production process is suggested to enhance the added value of semisteel, improve the Novel preparation process of iron powders with2020年8月4日 The effects of water spray travel distance, nozzle design, water pressure, melt superheat, and apex angle on the particle size distribution of a metal powder is studied via a laboratoryscale water atomizer; the main focus is on the first two, which are usually fixed Water atomisation of metal powders: effect of water spray configuration
.jpg)
the water atomizing process 1 Total Materia
Explore the process of atomization, a commercially popular method for producing metal powders Learn about the advantages of highpressure water atomization, its applications across various metals, and its role in the production of 2019年3月5日 Using the water atomization, the molten metal stream is disintegrated by a high velocity and pressure water jet The powder droplets solidify during the large heat exchange with the water The produced powder is collected at the bottom of the system Water atomization is Powder Production Technologies BHM Berg und Springer2022年7月1日 In the production process of metal powders by atomizing a melt with water, the melt drop interacts with the atmospheric oxygen of the spray and water (or its thermaldissociation products) during oxidation reactions at the drop surfaceOxidation Process of HighAlloy Steel Powders During Melt Atomization 2020年10月1日 Metal powder particles are covered by thin oxide layers as a result of their exposure to air or oxygencontaining atmospheres These surface layers account for up to 30–50 % of the total oxygen in typical commercial wateratomized ferrous powder grades used in the powder metallurgy (PM) industry [1], with layer thicknesses commonly reported to be in the Reduction of surface oxide layers on wateratomized iron
.jpg)
How to Make Metal Powder Additive
2023年8月31日 Based on the method of disintegration, atomization can be further classified into gas, water, plasma, centrifugal, and ultrasonic atomization Gas and water atomization are the most common types This method 2020年2月27日 DISINTERGRATED BY WATER JETS WATER VERSUS GAS ATOMIZATION WATER ATOMIZATION:MORE IRREGULAR SHAPED POWDERS MORE OXIDATION HIGHER COOLING RATE LESS SEGREGATION Water Atomization of Powders 14010202 In a simple form the relation can be written as: D = C/V sin α with V the water velocity, α the angle Aluminium Powder Metallurgy2012年8月30日 Water atomization is one of the prominent methods used in production of powders for conventional PM application Oxygen content of the powders produced by water atomization plays an important role in determining it’s as sintered properties In this work, oxide formation during various stages of water atomization and annealing wereSTUDY OF TOTAL OXYGEN CONTENT AND OXIDE 2021年8月27日 Milling equipment: The equipments are generally classified as crushers mills Crushing => for making ceramic materials such as oxides of metals; Grinding => for reactive metals such as titanium, zirconium, niobium, tantalum In conventional (gas or water) atomization, a liquid metal is produced by pouring moltenPowder metallurgy – basics applications IIT Guwahati
.jpg)
Effects of Surface Oxidation on the Magnetic Properties of
2023年8月28日 The demand for soft magnetic amorphous metal powders with high saturation magnetization values and low energy loss has increased to achieve highperformance inductors for mobile electronic devices In this study, Febased Fe923Si35B30C07P05 (wt%) amorphous metal powders were prepared using different atomization methods for controlling 2018年6月14日 Wateratomization of molten iron or alloy is a primary mechanical manufacturing method today, while chemical reduction of iron oxides is the least expensive, largescale chemical manufacturing method compared to other chemical methods However, the atomization and reduction methods create iron powders with completely different particle morphologyRoles of Iron Metal Powders in SemiMetallic Friction 2022年11月9日 A novel method of hydrogen production was proposed in a patent by Chen T et al [76]; this method differs from the conventional steamiron method in that the water vapor used in this method is oxygenated water vapor atomized by pressurizing roomtemperature water at 3–5 bar; afterward, the water is mixed with oxygen and heated using a heat Preparation of hydrogen from metals and water without CO2 ASL offers a wide range of atomisation technologies such as Water Atomisation, Gas Atomisation, Centrifugal Atomisation Oil Atomisation We have the expertise and experience to help you optimise your equipment Centrifugal 13 plants for Atomising Equipment Technologies
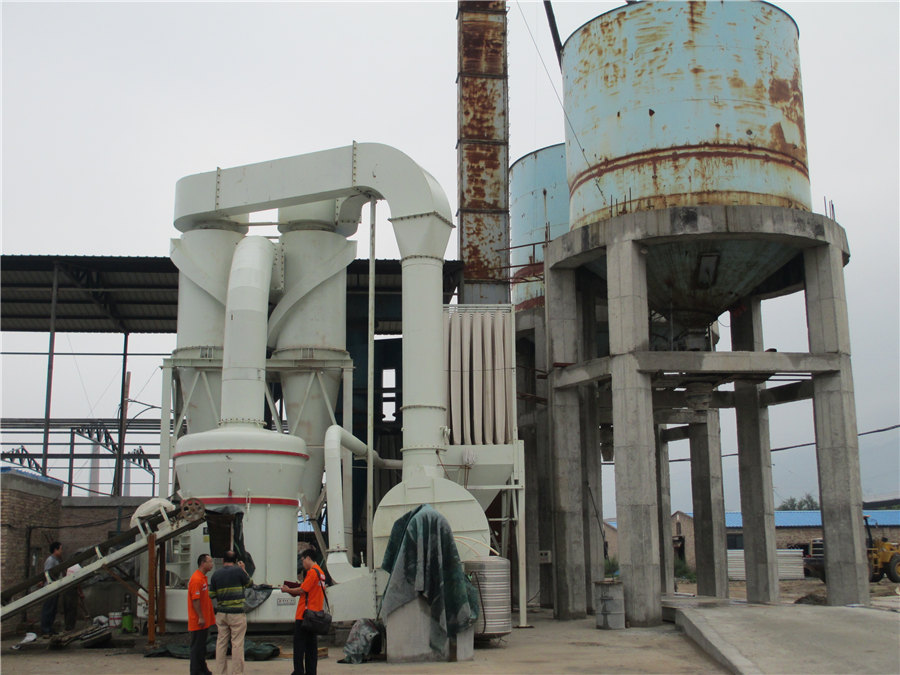
Characterization of Fine Metal Powders Produced by Hybrid by Water
2017年11月14日 Many new atomization techniques have been developed in recent years, such as ultrasonic capillary wave atomization , rotating disk atomization, swirl water jet atomization and hybrid centrifugal hydraulic atomization (CHA) with gas atomization , super highpressure water atomization [5, 6] Water atomization is the most common way for metal 2024年11月10日 The most widely used are gas atomization Equipment and water atomization Equipment In the process of atomization powder producing process, melt the metal raw materials into qualified alloy liquid (generally Metal powder water atomization equipment4 天之前 Highpressure water atomization preparation powdered material production line is featured as an equipment,an industrialized massproduction device,designed for producing powder by water atomization under morphemic Metal Alloy Powder Water Atomization Equipment3 天之前 Highpressure water atomization preparation powdered material production line is featured as an equipment,an industrialized massproduction device,designed for producing powder by water atomization under morphemic Customized Water Atomization Equipment
.jpg)
Metal Powder Water Atomization Equipment Metal3DP
2024年3月22日 Overview Metal powder water atomization is a popular technique used in the manufacturing industry to produce highquality metal powders for various applications, including additive manufacturing (3D printing), powder metallurgy, and more This process involves melting metal and forcing it through a smalldiameter nozzle, where it is atomized by highpressure 2020年6月1日 The results showed that the surface oxides consisted of a thin (~4 nm) iron oxide (Fe2O3) layer with particulate oxide phases rich in Cr, Mn, and Si, with a varying composition(PDF) Effect of atomization on surface oxide composition in 2023年9月5日 The reduction of metal oxides and salts is a widely used method for powder preparation Solid carbon can be used to reduce iron and tungsten powder, while hydrogen or decomposed ammonia is used to produce tungsten, molybdenum, iron, copper, cobalt, nickel powders Iron powder can also be produced using converted natural gas and coal gasMetal Powder Preparation Methods and Principles: A 2022年7月1日 The meltatomization method that uses water is the most economically feasible method [], which is widely used to obtain powders of iron and lowalloy steel with a branched particle shape and oxygen content after recovery annealing at the level of several tenths of percentThis content is quite acceptable for their use in traditional powder metallurgyOxidation Process of HighAlloy Steel Powders During Melt Atomization
.jpg)
Nanomaterials through Powder Metallurgy: Production, Processing
2020年7月30日 Hard steel or tungsten carbide balls are used as the grinding media, which imparts the energy through impact into the crystalline structure of the sample leading to the formation of lattice defects Arun et al investigated iron oxide (Fe 3 O 4 and αFe 2 O 3) Tallmadge JA (1978) Powder production by gas and water atomization of liquid 2020年8月13日 • The various types of atomization techniques used are, 1 Water atomization: High pressure water jets are used to bring about the disintegration of molten metal stream • Water jets are used mainly because of their higher viscosity and quenching ability • This is an inexpensive process and can be used for small or large scale productionPOWDER METALLURGY NIT 2The most common chemical powder treatments involve oxide reduction, precipitation from solutions, and thermal decomposition The powders produced can have a great variation in properties and yet have closely controlled Making Metal Powder MPIF2023年11月23日 The demand for manufacturing components with complex geometries, good mechanical properties, and material efficiency has surged across various industries, encompassing aerospace, military, nuclear, and Microstructural and mechanical characterization
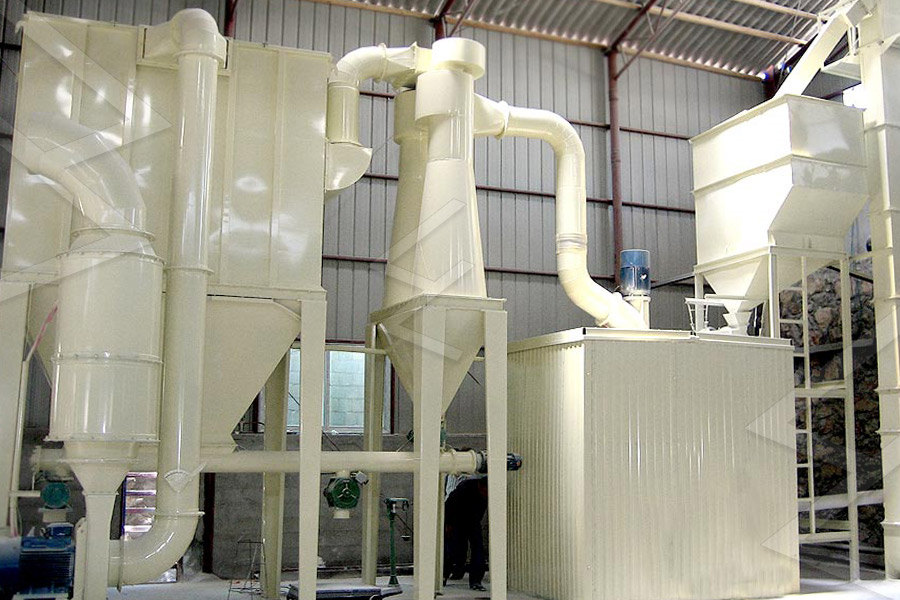
Grinding and Polishing Guide Buehler
2021年11月15日 Grinding Equipment but water is usually added to keep the specimen surface cool and to carry away the grinding debris icollidal suspension For certain materials, cerium oxide, chromium oxide, magnesium 2024年11月19日 Highpressure water atomization preparation powdered material production line is featured as an equipment,an industrialized massproduction device,designed for producing powder by water atomization under morphemic conditionIts working principle refers to the smelting of metals or metal alloys in air,in which,under the shielding made of inert Metal Copper Powder Manufacturing High Pressure Water Atomization 2024年8月30日 Iron Oxide; Complete selections of abrasive powders for grinding and polishing 180054EXTEC Equipment: Labcut 150 Variable Speed Precision Diamond Saw; Labcut 300A Advanced Bench Top Abrasive Cutting Machine; Labcut 300AF Advanced Floor Model Abrasive Cutting Machine;Iron Oxide Abrasive Powders Grinding Polishing Extec 2021年5月18日 Iron (III) oxide is a compound that appears in at least four different polymorphs: αFe 2 O 3, βFe 2 O 3, γFe 2 O 3, and εFe 2 O 3However, Fe 3+ ions are also present in another form of iron oxide: Fe 3 O 4, which is an iron crystal structure with both Fe 2+ and Fe 3+ ions And in its turn, Fe 2+ ions are also present in the FeO form of iron oxide Each of these Synthesis, Properties, and Applications of Iron Oxides
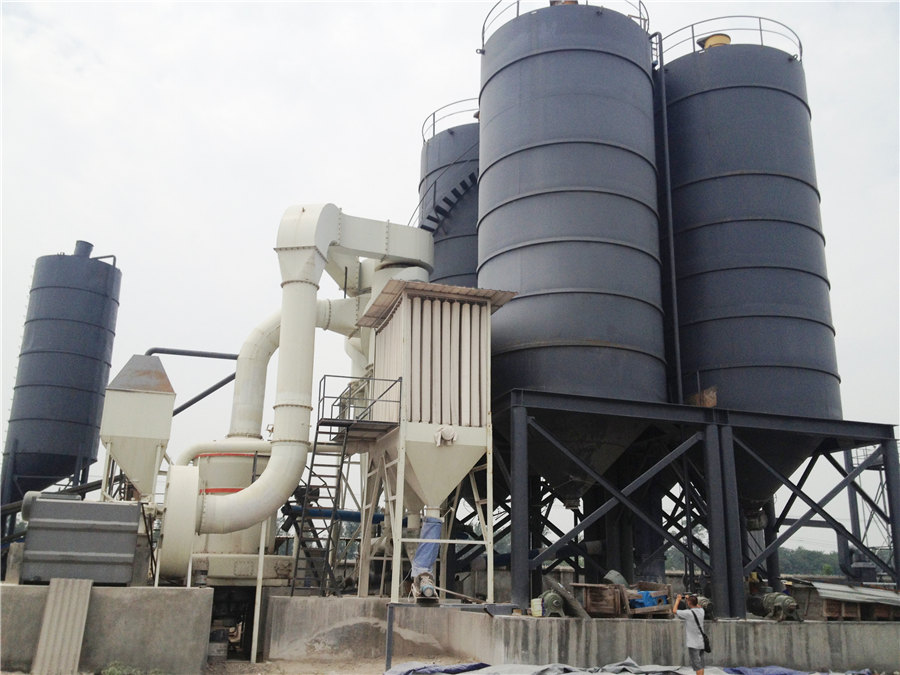
Powder Production Technologies BHM Berg und Springer
2019年3月5日 Production of metal powder has been done for decades Apart from some methods using crushers for powder production, the atomization of a molten liquid melt is the most common way to produce metal powders Therefore different melting technologies (open furnace, vacuum furnace, induction melting or plasma melting, and more) as well as atomization 2024年2月20日 Aluminum oxide grinding wheels are abrasive tools in which aluminum oxide grains are bonded together with a material to form a wheel of various shapes and sizes Safety in the operation of grinding wheels is paramount to prevent accidents and ensure the longevity of the grinding equipment To achieve safe operations, follow these guidelines Ultimate Guide to Aluminum Oxide Grinding Wheels RUISHI2024年6月5日 Presently iron and steel are also processed by atomization It is the commercial method for producing metal powders In this process, a molten metal or alloy is injected through a nozzle, where it is atomized (fragmented into small size Powder Metallurgy SpringerLink"Water Atomization Process" refers to a process that sprays and collides water at a high pressure of about 50150 MPa against a molten metal melted at a high temperature to produce fine metal powder (atomized powder) at the micron level Water Atomization Equipment STAR BURST: Wet Pulverization and Dispersion Device BiNFis: Cellulose Water Atomization Equipment SUGINO MACHINE
.jpg)
Reduction of surface oxide layers on wateratomized iron
2020年10月1日 Metal powder particles are covered by thin oxide layers as a result of their exposure to air or oxygencontaining atmospheres These surface layers account for up to 30–50 % of the total oxygen in typical commercial wateratomized ferrous powder grades used in the powder metallurgy (PM) industry [1], with layer thicknesses commonly reported to be in the 2023年8月31日 Based on the method of disintegration, atomization can be further classified into gas, water, plasma, centrifugal, and ultrasonic atomization Gas and water atomization are the most common types This method How to Make Metal Powder Additive 2020年2月27日 DISINTERGRATED BY WATER JETS WATER VERSUS GAS ATOMIZATION WATER ATOMIZATION:MORE IRREGULAR SHAPED POWDERS MORE OXIDATION HIGHER COOLING RATE LESS SEGREGATION Water Atomization of Powders 14010202 In a simple form the relation can be written as: D = C/V sin α with V the water velocity, α the angle Aluminium Powder Metallurgy2012年8月30日 Water atomization is one of the prominent methods used in production of powders for conventional PM application Oxygen content of the powders produced by water atomization plays an important role in determining it’s as sintered properties In this work, oxide formation during various stages of water atomization and annealing wereSTUDY OF TOTAL OXYGEN CONTENT AND OXIDE
.jpg)
Powder metallurgy – basics applications IIT Guwahati
2021年8月27日 Milling equipment: The equipments are generally classified as crushers mills Crushing => for making ceramic materials such as oxides of metals; Grinding => for reactive metals such as titanium, zirconium, niobium, tantalum In conventional (gas or water) atomization, a liquid metal is produced by pouring molten2023年8月28日 The demand for soft magnetic amorphous metal powders with high saturation magnetization values and low energy loss has increased to achieve highperformance inductors for mobile electronic devices In this study, Febased Fe923Si35B30C07P05 (wt%) amorphous metal powders were prepared using different atomization methods for controlling Effects of Surface Oxidation on the Magnetic Properties of 2018年6月14日 Wateratomization of molten iron or alloy is a primary mechanical manufacturing method today, while chemical reduction of iron oxides is the least expensive, largescale chemical manufacturing method compared to other chemical methods However, the atomization and reduction methods create iron powders with completely different particle morphologyRoles of Iron Metal Powders in SemiMetallic Friction 2022年11月9日 A novel method of hydrogen production was proposed in a patent by Chen T et al [76]; this method differs from the conventional steamiron method in that the water vapor used in this method is oxygenated water vapor atomized by pressurizing roomtemperature water at 3–5 bar; afterward, the water is mixed with oxygen and heated using a heat Preparation of hydrogen from metals and water without CO2
制粉项目-2023.11.17.jpg)
Atomising Equipment Technologies
ASL offers a wide range of atomisation technologies such as Water Atomisation, Gas Atomisation, Centrifugal Atomisation Oil Atomisation We have the expertise and experience to help you optimise your equipment Centrifugal 13 plants for 2017年11月14日 Many new atomization techniques have been developed in recent years, such as ultrasonic capillary wave atomization , rotating disk atomization, swirl water jet atomization and hybrid centrifugal hydraulic atomization (CHA) with gas atomization , super highpressure water atomization [5, 6] Water atomization is the most common way for metal Characterization of Fine Metal Powders Produced by Hybrid by Water